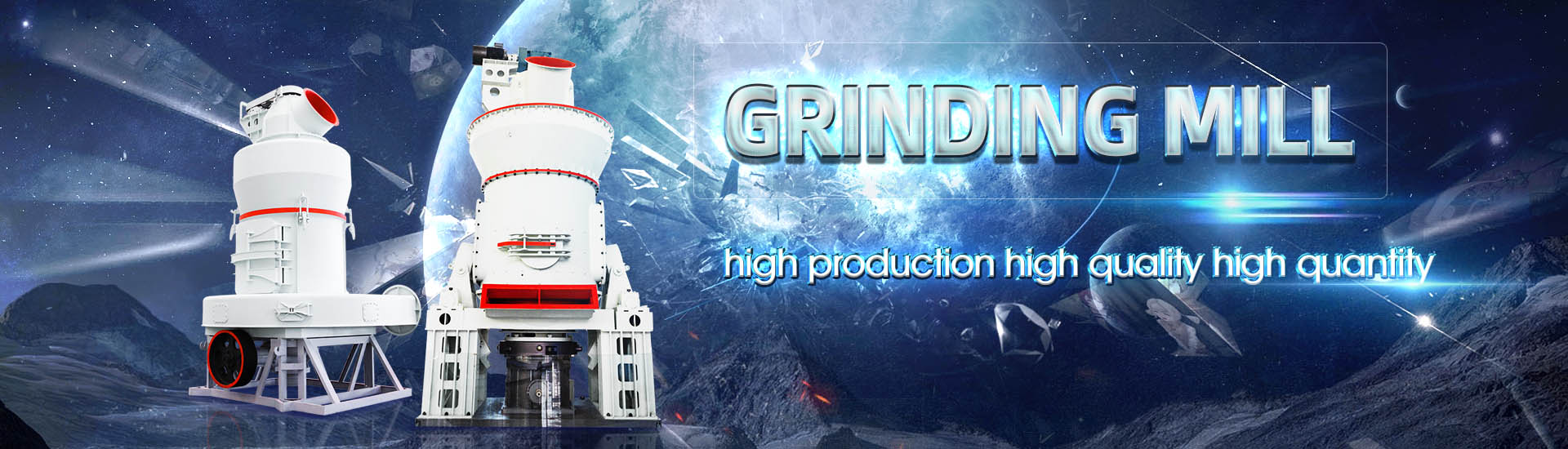
Inspection content and standards of bluestone grinding mill
.jpg)
Avoid catastrophic failures by Metso
grinding mills required an assessment to determine their actual condition Metso was mandated to conduct a visual and nondestructive inspection of the mill Results: Through the inspections, This document provides guidance on inspecting ball mills used in cement production It outlines key steps and measurements to take when inspecting the interior of a twocompartment mill Ball Mill Inspection Procedure PDF Mill (Grinding) Wear Scribd2021年1月1日 Mill filling has a dominant effect on grinding mill performance (Apelt, Asprey and Thornhill, 2001), and therefore, its accurate measurement is vital for modelling grinding mill An improved method for grinding mill filling measurement and Nowadays, conducting grindability tests requiring only a few kilos of material on several samples, is a more typical approach to grinding mill design This paper summarises the requirements SAG Mill Testing Test Procedures to Characterize Ore Grindability
.jpg)
TECHNICAL SPECIFICATION OF WET BALL MILL EQUIPMENT
This specification covers the minimum requirements for the complete design, material, manufacturing, shop inspection, testing at the manufacturer’s works, supervision of erection Schedule proper time for the grinding mill gear inspection Identify and follow the safety requirements to perform the inspection Interface with OEM to develop recommendations as Grinding mill gear inspectionThe document discusses parameters for quality finish milling including cement strength, Blaine surface area, and residue percentages It also covers inspection of ball mills including Ball Mill Operation, Inspection Optimization PDF Mill Dm›lŒ#B¡hýüôØ) V7ó䫱÷6ÃyæßæÑ;ô¶Öìå”# ë7U X ¤€;Å ˆG “÷Cõ—A Êï–?rùAq} Æ:Øœ47 Jò*ÙŒ¤f‘HÓibå sä!ÔÉ Öö½G%$‚B:È»mÿ»‰D„wwf¾Œ–j´½ ˜>$‡ û a=›Ê n† AusIMM – Leading the way for people in resources
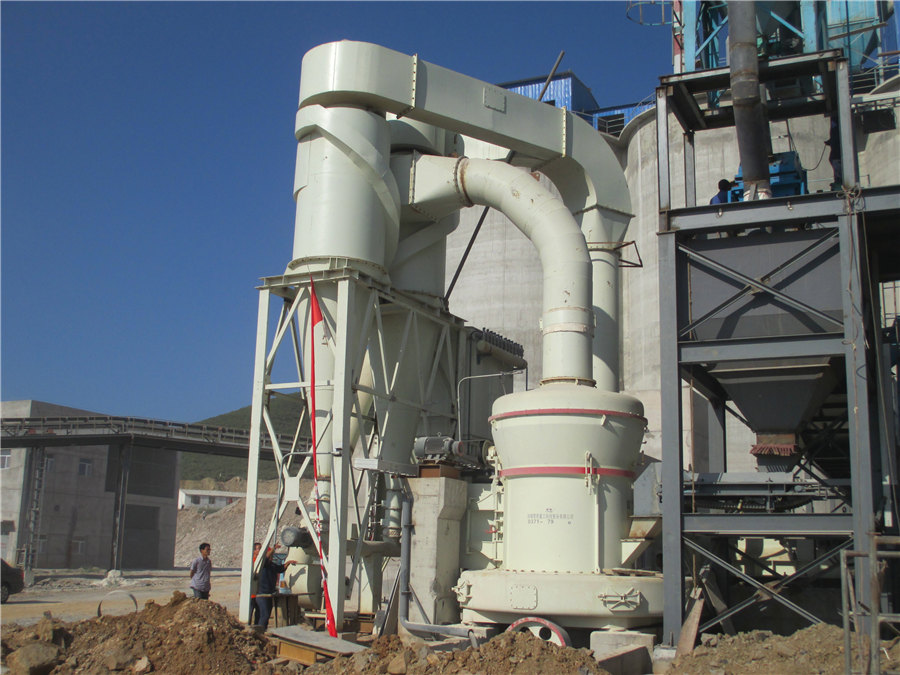
by finding problems early Metso
3 inspection packages for your horizontal grinding mill Avoid catastrophic failures by finding problems early Issues that are not caught early can lead to breakdowns and unplanned 2023年11月27日 The studies will be carried out using optical metrology methods on a Walter Helicheck inspection machine in reflected light and a number of images were stored to form a statistical sample Established new indicators and criteria for grinding efficiency based on image processing of the helical groove of the end mill As a result, recommendations for the selection New indicators and standards for measuring of the end mill's Grinding mill gear inspection Recommendations revealed in inspections help mills make the right changes to maximize their production and savings Description Through this service, we conduct a basic grinding mill gear inspection of central grease, open gears and key lubrication points to seek early identification of abnormal conditionsGrinding mill gear inspectionA healthy grinding The heart of the stone mill is the millstone The size of the millstone is not decisive for the fineness of the flour However, the optimal combination of the millstone’s diameter and its speed, controlled by a threephase motor, is fundamental The combination of rotation speed and gap between stones ensures perfect milling at low temperature to avoid damaging Stone Flour Grinding Mill for Wheat, Corn, Grain, Pulses
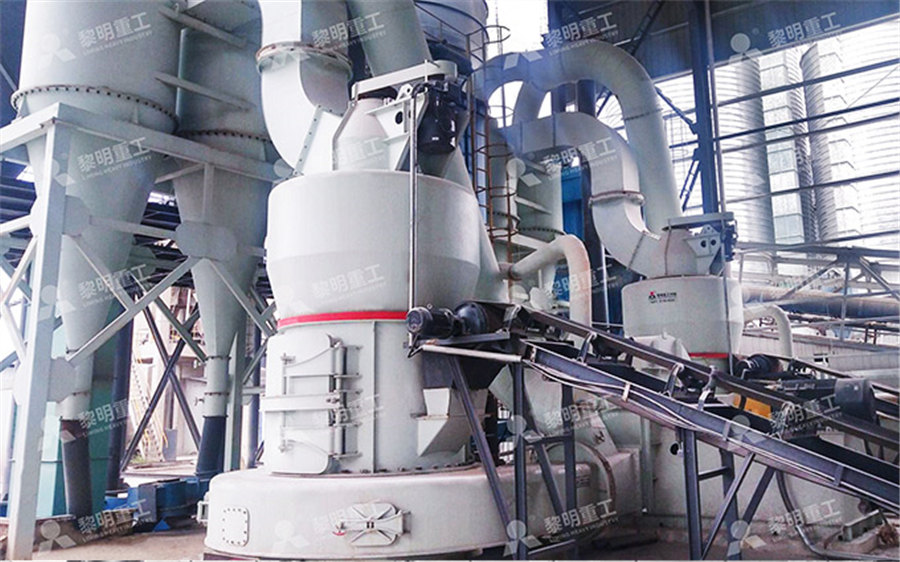
Ball Mill Inspection Procedure PDF Mill (Grinding) Wear
This document provides guidance on inspecting ball mills used in cement production It outlines key steps and measurements to take when inspecting the interior of a twocompartment mill Key areas to examine include the ball charge, material levels, wear on liners and diaphragms, sampling material at different points, and ensuring proper sizing of openings between 2018年7月19日 The detailed design procedure for a hammer mill machine is presented The system designed is a modification to the conventional hammer mill with a circular bottom casing and a semicircular screen(PDF) Design, construction and performance evaluation of a 2023年4月23日 2 and 4 wt % whereas steels contain carbon content less than 2 wt % Ball filling ratio also affects the grinding rate High mill filling reduces the grinding rate because the collision zone (PDF) Grinding Media in Ball MillsA Review ResearchGate2018年11月7日 The onthejob personnel are required to be familiar with the structure and performance of the equipment as well as the names, specifications and functions of the various components, and inspect the ball mill according to the inspection standards, time and items specified by the inspection card, and make a record3 Aspects of Ball Mill Maintenance Miningpedia
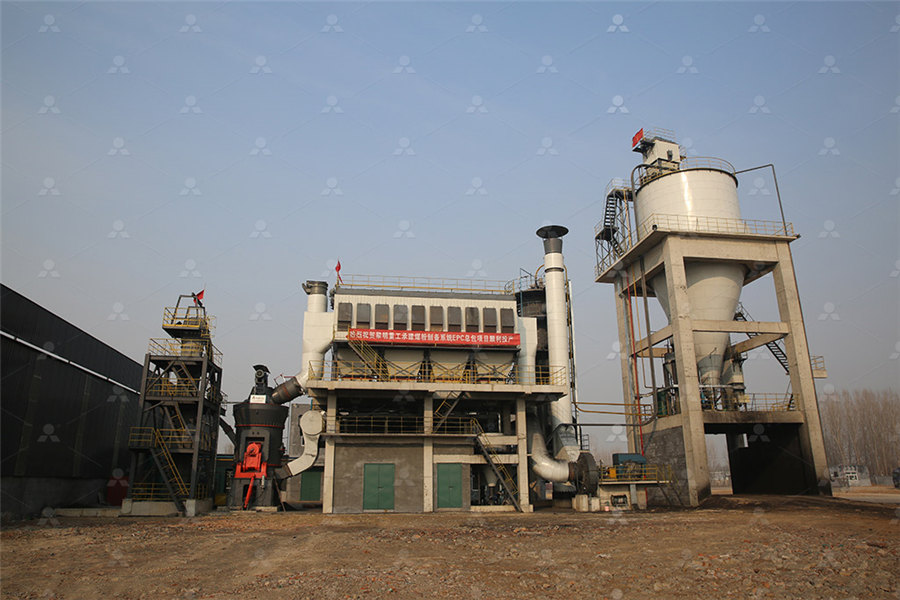
Calculate and Select Ball Mill Ball Size for Optimum Grinding
2013年8月3日 In Grinding, selecting (calculate) the correct or optimum ball size that allows for the best and optimum/ideal or target grind size to be achieved by your ball mill is an important thing for a Mineral Processing Engineer AKA Metallurgist to do Often, the ball used in ball mills is oversize “just in case” Well, this safety factor can cost you much in recovery and/or mill liner where he screens for pebbles (that could damage the mill) with his fingers, while the mill is operating Meanwhile the customer ties her sack to the end of the discharge pipe to collect the meal If the customer has brought more than one tin of grain, the miller fills the hopper as needed The mill is run continuously as much as possibleSMALL SCALE MILL FORTIFICATION MANUALThis document outlines inspection procedures for the ball mill at Arish Cement Company's production department It details checking various parts of the mill like the inlet, feeders, liners, ball charge, and diaphragms Measurements are taken to monitor wear, ensure proper material flow, and maintain grinding efficiency The goal is to prevent issues that could reduce Ball Mill Inspection Procedure PDF PDF Mill (Grinding) ScribdBall Mill Grinding Process Handbook Free download as PDF File (pdf), Text File (txt) or read online for free This document provides guidance on ball mill grinding processes It covers topics such as ball mill design including length to Ball Mill Grinding Process Handbook
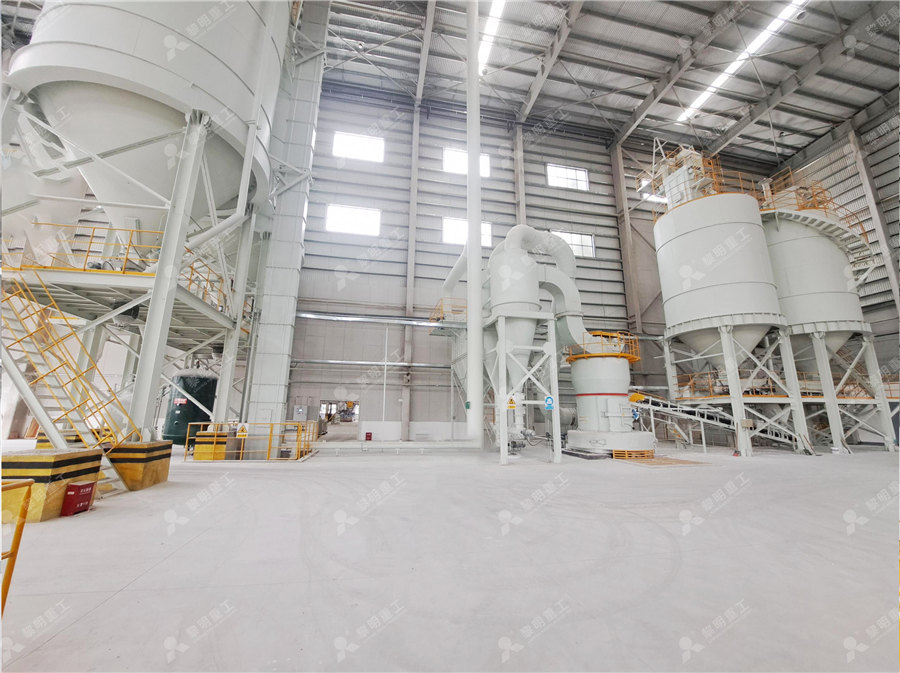
Pipe Mill Surveillance and Steel Mill Inspection
Our steel mill inspection services bring extensive experience in surveying and inspecting coils, billets, slabs and platemanufacturing processes Applus+ has a full range of assessed and approved platemill, pipemill, bendshop and coatingmill resources, closely located to the major mill facilities across the globe2021年8月9日 Bluestone Bluestone is also known as limestoneBluestone is a gray or whitish sedimentary rock (about 15% of the lithosphere) generated in the crust marine lake basin, with a water absorption rate of 075% or less, a flexural strength of 100 MPa or more and a gloss of about 60 for the blue stoneBluestone Crushers and Grinding MillsBluestone Processing 2015年7月18日 Observing the requirements and seeing the importance of the aspects involving safety and feed quality, the objective of this work was to evaluate the quality of the process, products and EVALUATION OF THE PROCESS, PRODUCTS AND INSTALLATIONS OF A FEED MILL2022年1月1日 The present research is focused in the developing an analytical outcome that can give a glimpse into the stone crushing ball mill gear box Further there is a lot of scope available in the field of stone crushing ball mills as the country’s growth depends on the infrastructure and roads in this stone makes a very crucial roleDesign and simulation of gear box for stone crushing ball mill
.jpg)
The Selection and Design of Mill Liners 911 Metallurgist
The second primary function of a liner is to transfer rotary motion of the mill to the grinding media and charge After all, it is the interface between the mill and the grinding charge Although work on the grinding action in mills was published 100 years ago (White 1905 and Davis 1919), the firstGrinding Mills: Ball Mill Rod Mill Design PartsCommon types of grinding mills include Ball Mills and Rod Mills This includes all rotating mills with heavy grinding media loads This article focuses on ball and rod mills excluding SAG and AG mills Although their concepts are very similar, they are not discussed herePhotographs of a glass ended laboratory ball mill show Grinding Mills 911Metallurgist2016年1月1日 The wear of balls used during a grinding process is considered one of the losses that cause an increase in the operating cost allocated to the ball mill [21]A comparison of wear rates of ball mill grinding mediaThe studies will be carried out using optical metrology methods on a Walter Helicheck inspection machine in reflected light and a number of images were stored to form a statistical sample Established new indicators and criteria for grinding efficiency based on image processing of the helical groove of the end mill As a result, recommendations for the selection of optical control New indicators and standards for measuring of the end mill's
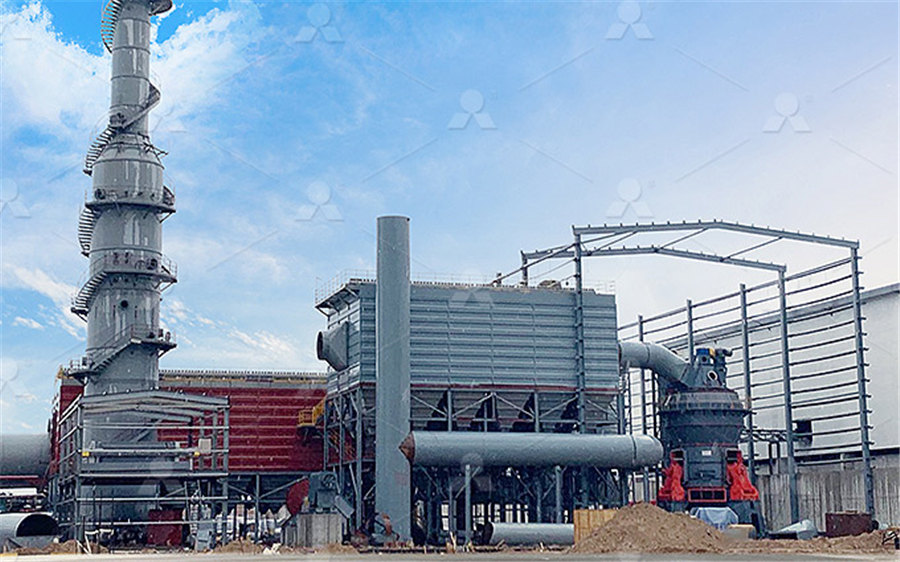
BALL MILL INSPECTION PROCEDURE The Cement Grinding Office
2012年12月25日 BALL MILL INSPECTION PROCEDURE the content will be optimally indexed by Google via AI and sorted into the right category for over 500 million ePaper readers on YUMPU On a process point of view, a mill inspection is only representative if the grinding mill circuit is in a steady working condition with a representative cement 2024年2月12日 Factor Description; Type of Mill: Manual: Requires handcranking, laborintensive, no power consumption Electric: Uses a motor, more convenient, faster grinding: Grinding Mechanism: Stone Grinding: Produces How to pick the best home grain mill: A buyer's guide The document provides instructions for conducting a mill crash stop inspection The key steps include: 1) Stopping the entire circuit at once to avoid distorting mill granulometry measurements 2) Checking material levels and volumes to How To Do A Mill Crash Stop Inspection: Grinding5 VERTICAL ROLLER MILL KTM Main data Type Min motor power Max motor power Min capacity Max capacity [kW] [kW] [t/h] [t/h] KTM 400 11 18,5 0,1 0,8 KTM 800 37 55 2 5 KTM 1000 55 90 4 8 KTM 1200 90 132 6 12 KTM 1400 132 200 9 18 KTM 1600 200 315 12 24 KTM 1800 315 400 20 38 KTM 2000 400 500 29 50 KTM 2200 500 630 39 64 KTM 2400 630 800 GRINDING AND SEPARATING TECHNOLOGY SYSTEMS
.jpg)
Three factors that determine the wear life and performance of mill
Choice of mill lining A mill lining should be optimized to suit each specific mill Choosing an appropriate type of lining and design in terms of lining material, thickness and profile is vital for optimizing mill throughput and total grinding costs Choosing the correct liner material and design ensures that the mill itself is well protectedPaglierani and Ocrim are the manufacturers of BioStoneMill, the Commercial Electric Stone Mill available in two models (BioStoneMill 700 and 1500) +39 0541 info@paglierani EnglishCommercial Electric Stone Grain Mill by Paglierani and Ocrim2015年1月1日 Flour milling is a technology which combines food science and engineering with the art of the practical miller This chapter aims to help define the science and the art of a process which produces one of the most versatile of bakery raw materials and aims to provide a background to the link between wheat, the milling process and the properties of the final flourWheat Milling and Flour Testing SpringerLink2021年1月1日 Mill filling has a dominant effect on grinding mill performance (Apelt, Asprey and Thornhill, 2001), and therefore, its accurate measurement is vital for modelling grinding mill performanceMeasuring filling is also necessary to estimate the composition of the load for mill modelling: rock and slurry for AG mills; rock, balls and slurry for SAG mills; or balls and slurry An improved method for grinding mill filling measurement and
.jpg)
Mill liner wear and performance monitoring Metso
Unique in the industry, Metso MillMapper™ liner wear monitoring allows your maintenance and operational personnel to extend liner life cycles, optimize liner design, prevent liner failures, optimize throughput, and improve the performance of your mill Benefits: Improves safety; Minimizes inspection shutdown times; Captures wear data on the 2023年10月27日 The ball mill is a rotating cylindrical vessel with grinding media inside, which is responsible for breaking the ore particles Grinding media play an important role in the comminution of mineral ores in these mills This work reviews the application of balls in mineral processing as a function of the materials used to manufacture them and the mass loss, as A Review of the Grinding Media in Ball Mills for Mineral American Journal of Engineering Research (AJER) 2017 w w w a j e r o r g Page 143 Figure 3; Hammer Mill, Front view Figure 4; Hammer Mill, Top view Figure 5a; Hammer Mill Figure 5b; Hammer Mill III RESULTS AND DISCUSSIONS Table I: Results Obtained from the Calculation S/No PARAMETERS SYMBOL VALUE UNITImprovement on the Design,Construction and Testing of Hammer Mill2016年8月31日 Thus, the company “Energosteel” has the ability to manufacture and supply of steel grinding balls by the old DSTU 349997 and by the new DSTU 8538: 2015, depending of customers needs, because the production QUALITY STANDARDS OF STEEL GRINDING BALLS
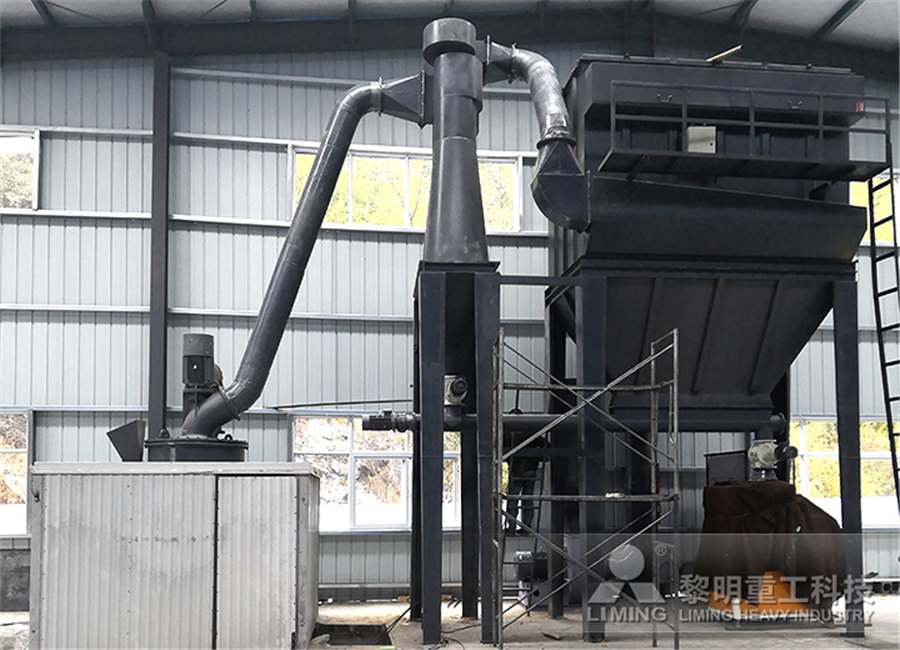
Grinding in Ball Mills: Modeling and Process Control
2012年6月1日 lifters which help to raise the content of the mill to greater heights before it drops and cascades down [36] There are three types of grinding media that are commonly used in ball mills:Grinding Mill RPM 480 300 Kg/h fine/coars 150 400 250 800 % of flour, grain size below 260 my (micron) 76 35 70 28 % of flour, grain size above 260 my (micron) 16 25 20 22 % bran, grain size above 600 my (micron) 8 30 10 50 Above values are average values for fine + INDUSTRIAL HORIZONTAL STONE GRINDING MILLS (WMODEL)The Tabletop Mill EM 25/250 is a specially developed tabletop type and may be characterized as a minisize grinding mill It is our smallest stone mill and wellsuited for big households or small farm shopsGrinding mills A century of milling experience Contact us2016年2月26日 The hammer mill is the best known and by far the most widely used crushing device employing the impact principle of breaking and grinding stone Thus far we have described machines which do a portion of their work by impact, but the only machine described in which this action plays an important role was the sledging roll type and particularly the Edison roll crusher Hammer Mill Crusher Grinder 911Metallurgist
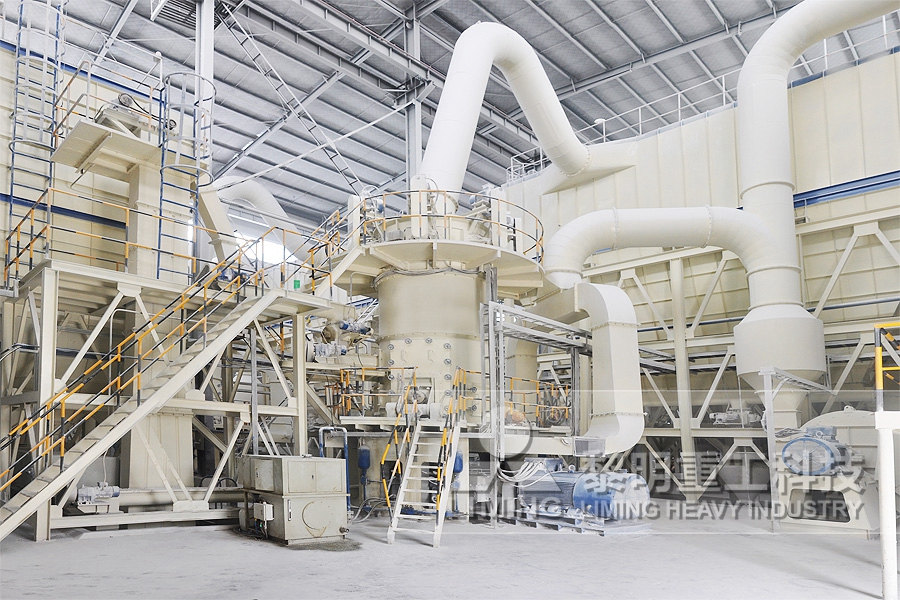
Grinding in Ball Mills: Modeling and Process Control Sciendo
55 known as the distribution function [45, 46]) describes the distribution of fragment sizes obtained after a breakage of particles of size xjThus, b1j, b2j, , bnj are the mass fractions of particles in size classes 1, 2, , n after a breakage of particles in size class j The mechanism of breakage is illustrated in [23] by a diagram shown in Fig 3Bluestone Grinding Tile Cleaners® provide Australia's leading commercial and residential bluestone grinding solutions Call 1300 771 201 for a free quote or use our quick enquiry formBLUESTONE GRINDING EXPERTS SYDNEY / MELBOURNE / Ball Mill Inspection Procedure Free download as PDF File (pdf), Text File (txt) or view presentation slides online "Doctor" is required for: 1) implementation of "Health checks" I Regular action 2) urgent investigations of actual process problems I Nonregular action This presentation focuses on the regular "health check" procedureBall Mill Inspection Procedure PDF Mill (Grinding) CalibrationEach mill system shall be supplied by separate distribution box such that it can feed back to ball mill, HP LP trunnion pumps, Agitators pumps separately The scope of supply for Limestone Grinding System shall include but not limited to the following: Sl no Item Description Qty/Mill Vendor to confirm 1TECHNICAL SPECIFICATION FOR LIMESTONE GRINDING SYSTEM
.jpg)
Cold rolling mill inspection and defect detection AMETEK
grinding problems such as incorrect speed, spindle bearing failure, coolant contamina tion, and grinding wheel issues This automatic surface inspection is a complementary technology to eddycurrent testing or ultrasonic testing to assure that the rolls are suitable for the rolling process A modular inspection solution