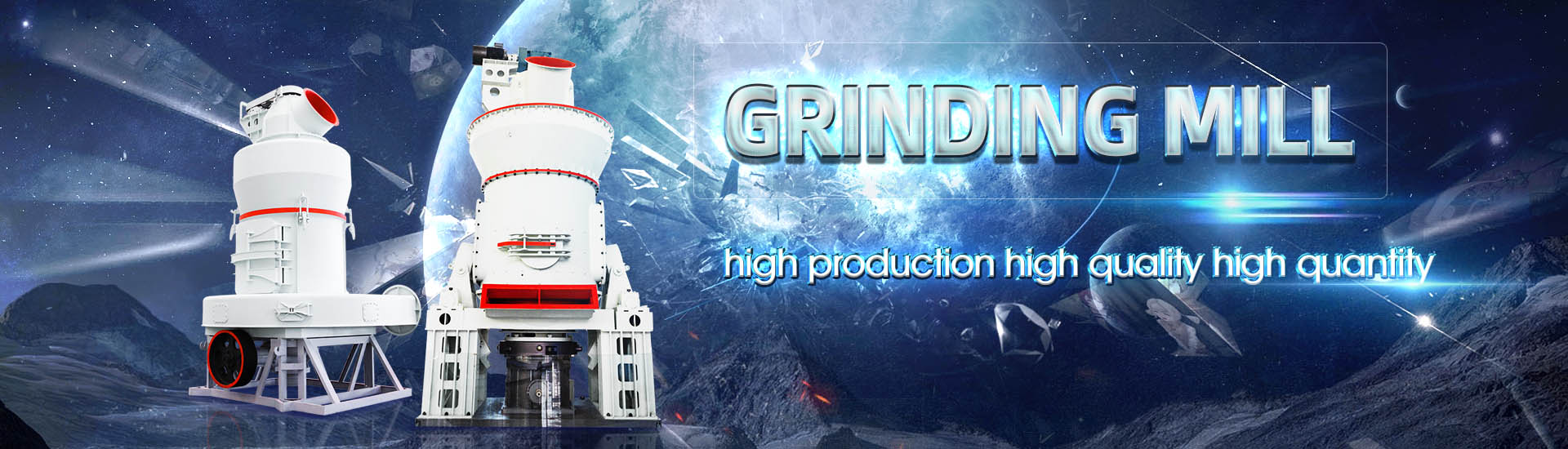
HOME→Cement grinding station process cement grinding station process cement grinding station process
Cement grinding station process cement grinding station process cement grinding station process
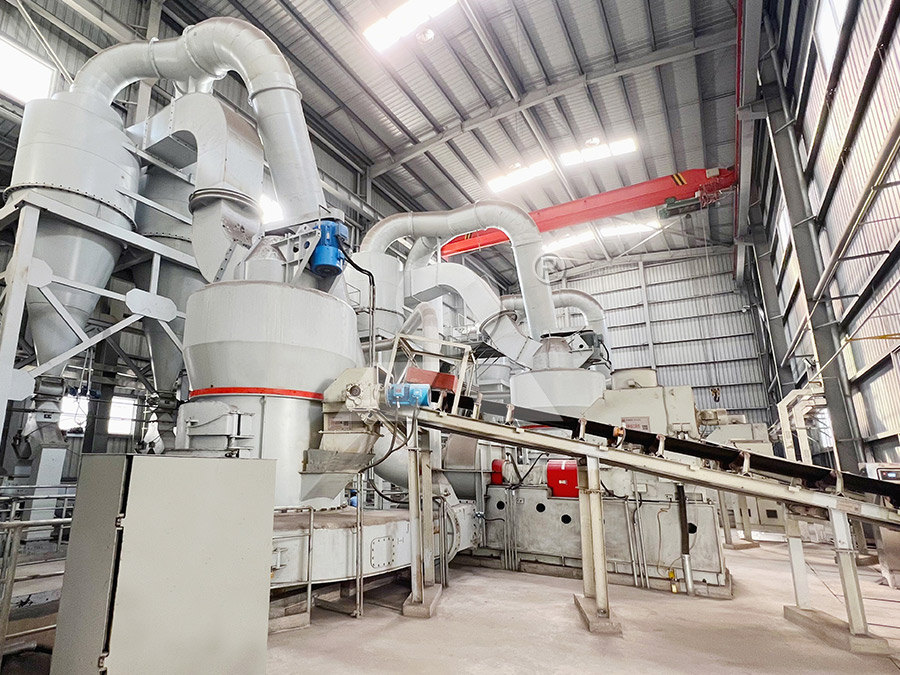
Cement Grinding Unit Process High Quality Cement
Explore Amrit Cement's stateoftheart cement grinding unit Learn about our cement grinding process and plant stages for high quality cementCement clinker grinding unit, or called cement grinding plant, cement grinding station, is an individual grinding plant in the finished cement production Cement grinding plants are primarily used to produce finished cement products by Cement Grinding Plant CHAENGWe master the construction and design schemes of various cement grinding plant systems such as vertical mill system, combined system, and ball mill system No matter what type and strength of cement you want to produce, and what Cement Grinding Plant Expert Cement Grinding Highly energy intensive unit operation of size reduction in cement industry is intended to provide a homogeneous and super fine (30004000 Blain) cement Grinding operation is monitored for Cement Grinding Cement Plant Optimization
.jpg)
Modular Mobile Grinding Plant, Portable Grinding Plant Cement
The modular mobile grinding plant developed by AGICO CEMENT is a highly flexible system capable of producing any desired types of cement for local cement producers and market Featuring all the process benefits of the classic FCB Horomill® grinding plant, the FCB FLAG™ station is Fives’ top solution for: Entering new markets; Adapting operations to market changes; Boosting production of all types of cement; The Fives Modular grinding with FCB FLAG™ stationAn evaluation of the grinding system and operation includes meaningful and critical inspection of all equipment, components and the process parameters by experts PEC Consulting can help OPTIMIZATION OF CEMENT GRINDING OPERATION IN BALL MILLS2017年5月19日 PDF Grinding is an essential operation in cement production given that it permits to obtain fine powder which reacts quickly with water, sets in few Find, read and cite all the researchOverview of cement grinding: fundamentals, additives,
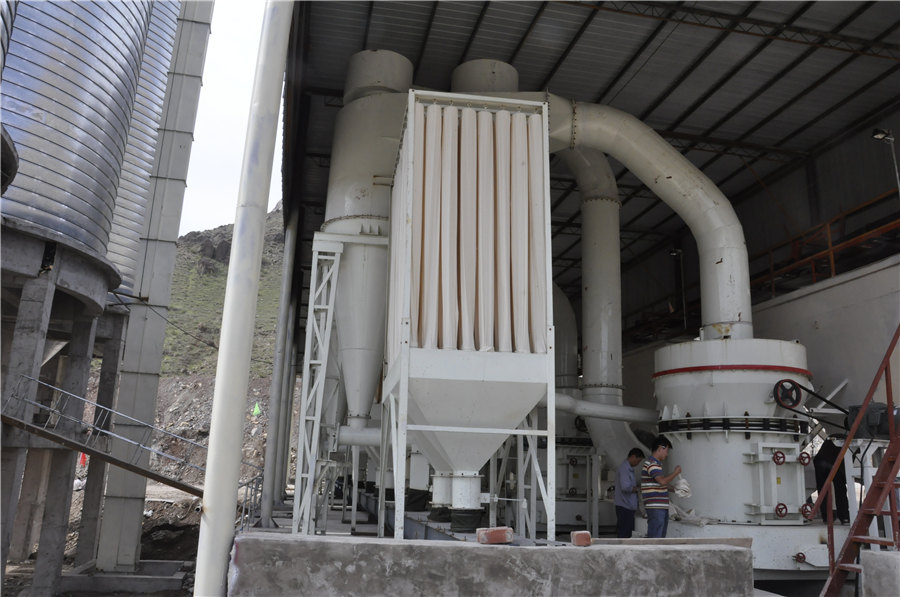
CEMENT GRINDING SYSTEMS INFINITY FOR CEMENT EQUIPMENT
The final manufacturing stage at a cement plant is the grinding of cement clinker from the kiln, mixed with 45% gypsum and possible additives, into the final product, cement In a modern cement plant the total consumption of electrical energy is about 100 kWh/t The cement grinding process accounts for approx 40% if this energy consumption2016年10月5日 1 Introduction Cement is an energyintensive industry in which the grinding circuits use more than 60 % of the total electrical energy consumed and account for most of the manufacturing cost []The requirements for the EnergyEfficient Technologies in Cement GrindingAGICO Cement offers EPC cement grinding station projects with more than 20 years of experience Feel free to contact us! Skip to content Blog Contact About Cases Factory CONTACT US info@cementplantequipment Modular Mobile Cement Grinding Plant For SaleThe new cement grinding process includes mixed material crushing, cement batching station, pregrinding, high fine grinding, fine powder separation, dust treatment, automatic control and other technologies, so that cement high yield, high quality, energy saving, in line with the requirements of energy saving and emission reductionCement Grinding Station Solution Ball Mill and Vertical Mill
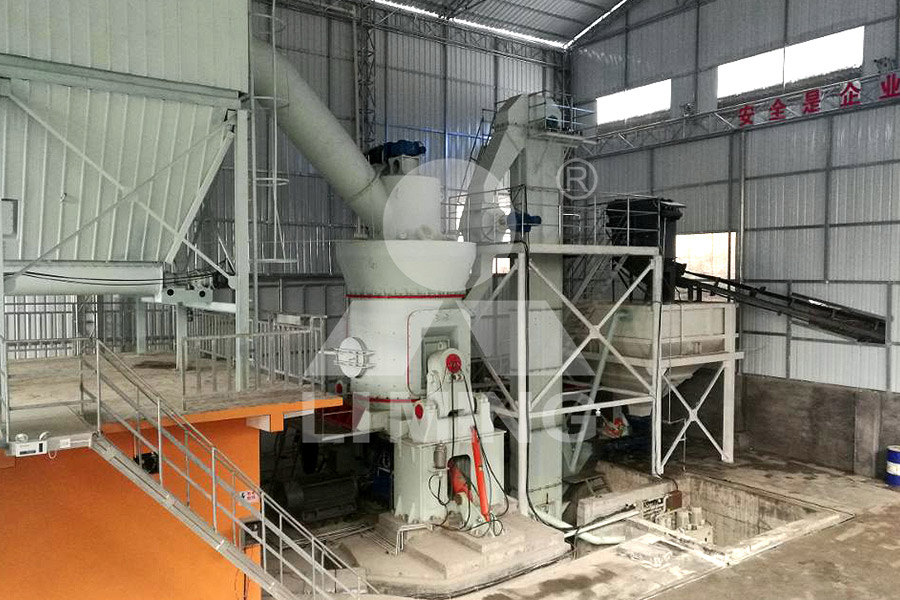
Ball Mill for Cement Grinding Process
Cement Ball Mill Structure When Ball Mill is working, raw material enters the mill cylinder through the hollow shaft of the feed The inside of the cylinder is filled with grinding media of various diameters (steel balls, steel segments, etc); when the cylinder rotates around the horizontal axis at a certain speed, Under the action of centrifugal force and friction force, the medium and the Purpose of Grinding in Cement Manufacturing The main goal of grinding in cement manufacturing is to produce a fine powder that will form the basis of the final product Grinding ensures that the raw materials are adequately prepared for the subsequent stages of the cement production process, including blending, heating, and packagingGrinding in Cement Manufacturing: Key Process, Types of Mills, Everything you need to know about clinker/cement Grinding if You read and understand this article , you will be ready to be a cement grinding area manager FEED AND FEED SYSTEM Mill type: cement mill, dry process raw mill, wet process raw mill Diaphragm location: Raw mill: transfer diaphragm at the drying chamber outlet, intermediate, Everything you need to know about clinker/cement GrindingThe Effect on the Performance of Cement Grinding Aid Components GUO Yanmei1,a, SUN Shaofei2,b,* 1 Hohhot Construction Engineering Quality Supervision Station ,Hohhot ,China 2 Inner Mongolia University of Science Technology ,Baotou ,China aTel,b:@ 223 Cement Grinding Aid Compound The Effect on the Performance of Cement Grinding Aid Components
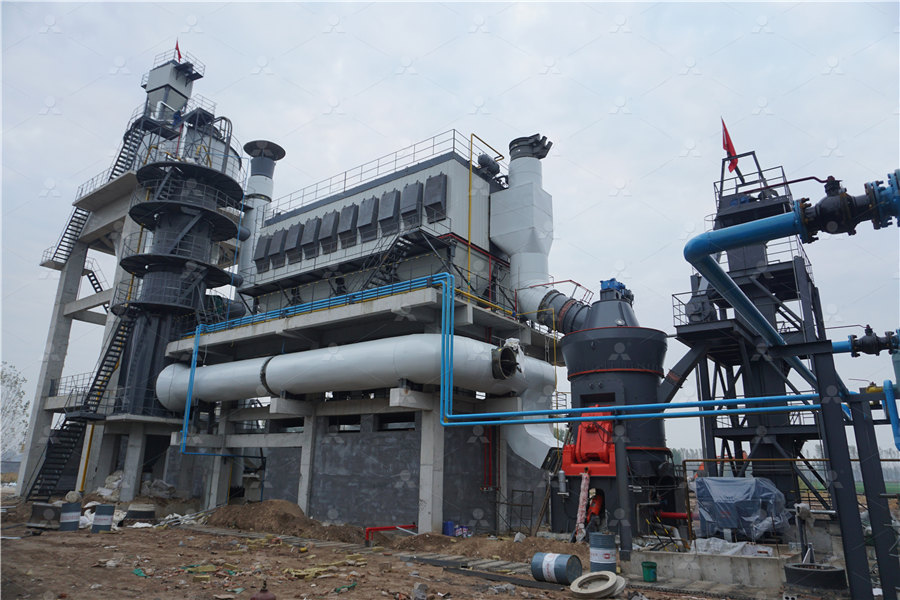
Cement Production Process Cement Manufacturing Process AGICO CEMENT
2020年8月25日 A full cement production process includes the cement crushing process, raw mill process, clinker process, and cement grinding process, cement packing process, and related process Find more! Skip to content +86 s about blog contact EN ES Menu Menu Home;2014年6月10日 Evolution of the cement Process • Wet process easiest to control chemistry better for moist raw materials • Wet process high fuel requirements fuel needed to evaporate 30+% slurry water • Dry process kilns less fuel requirements • Preheater/Precalciner further enhance fuel efficiency allow for high production ratesCement manufacturing process PPT Free Download SlideShare2023年7月19日 Grinding aids, primarily amine group chemicals, are used to reduce agglomeration and increase concrete strength in order to ensure an efficient comminution process in the modern cement industryIntensifying the cement grinding processNowadays, the dry process is the most popular cement making process which is widely adopted by cement plants all over the world for its great advantages in energy saving and environmental protection Cement Making Process The How Is Cement Produced in Cement Plants Cement
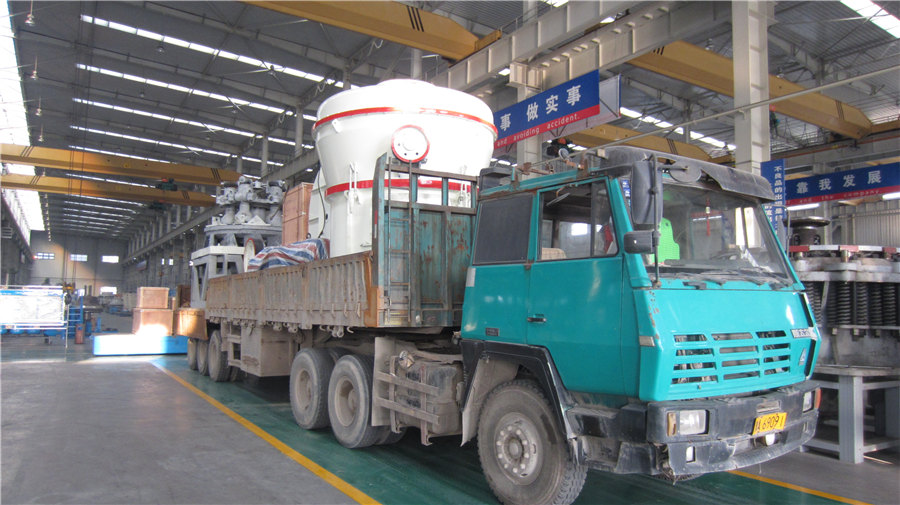
Modular Grinding Plant AGICO Cement Machinery
There are two types of mills commonly used in the modular mobile grinding station: ball mill and vertical roller mill (VRM) We will select the appropriate mill module according to the specific needs of customers The mill is the core The power ingesting of a grinding process is 5060% in the cement production power consumption The Vertical Roller Mill (VRM) reduces the power consumption for cement grinding approximately 3040% associated with other grinding mills The process variables in cement grinding process using VRM are strongly nonlinear and having large timePROCESS CONTROL FOR CEMENT GRINDING IN VERTICAL 2016年10月23日 The principle of Grate Discharge grinding is nearly universally adapted in the cement grinding industry Grate Discharge Ball Mills are the rule rather than 911 Metallurgist is Only close economic study can determine which process should be used CLINKER GRINDING Clinker, the discharge product from the kiln, is partially cooled Cement Grinding 911MetallurgistCement Clinker Grinding Station can make full use of Industrial waste such as the slag , fly ash, furnace slag and coal gangue around the city, so it is an environmental protection industry FTM cement mill station is featured with relatively simple process, easy operation, less investment in process equipment, energy saving, and environmental protectionCement Grinding stationcement ball millGrinding mill stationGrinding
.jpg)
EnergyEfficient Technologies in Cement Grinding
2016年10月5日 In this chapter an introduction of widely applied energyefficient grinding technologies in cement grinding and description of the operating principles of the related equip‐ ments and comparisons over each other in terms of grinding efficiency, specific energy consumption, production capacity and cement quality are given A case study per‐ formed on a Therefore, a cement grinding station is more suitable for the actual development of the local area Because it needs a smaller area and has no requirements for mine resources Cement grinding process Cement grinding is the last step of cement making The main grinding equipment cement mills grind the clinker to finished cement powdersCement Grinding Units Cement Plant Equipment CNBMSINOMA2023年8月21日 ICR looks at the inner workings of grinding mills in the cement industry to understand the technological advancements that are reshaping the landscape against the foreground of sustainability Innovations to enhance the grinding processes are aimed at minimising their environmental footprint while increasing efficiency and performance In CuttingEdge Grinding Solutions Indian Cement ReviewCHAENG can provide the complete solutions of 15100t/h cement grinding station for you Please send to for the quotation HOME; CONTACT:+86 / +86 Providing professional cement grinding process for clientscement grinding station
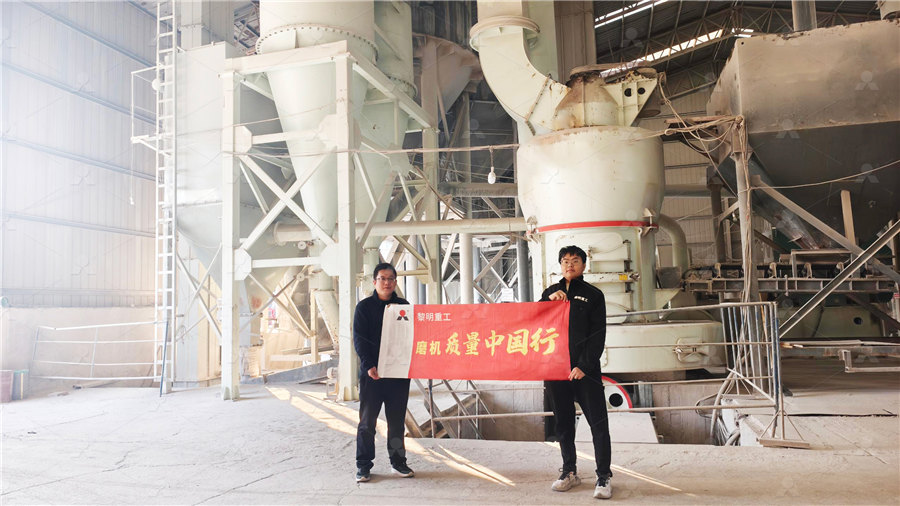
Overview of cement grinding: fundamentals,
2017年5月19日 The main factors affecting energy consumption in grinding cement are considered Cuttingedge additives technology impacts on cement process, performance and handling2022年8月10日 Grinding in the cement manufacturing process takes place at three stages: raw meal grinding, cement grinding, Cement grinding station can greatly digest the slag, fly ash, slag, coal gangue and other industrial waste Grinding: Smarter Solutions Indian Cement ReviewCost Savings: While there may be initial investments in setting up a cement grinding station, the longterm benefits include reduced energy costs, increased production efficiency, and potential savings on raw material usage Cement Grinding Plants Cement Grinding UnitCement grinding station is an individual independent cement finished products production units of the formation of finally finished stage of cement production line Grinding is an essential process in the cement industry ; Zhongke in Cement Grinding StationHenan Zhongke Engineering
.jpg)
How Cement is Made Cement Manufacturing Process
Stage 2: Grinding, Proportioning, and Blending The crushed raw ingredients are made ready for the cementmaking process in the kiln by combining them with additives and grinding them to ensure a fine homogenous mixture The composition of cement is proportioned here depending on the desired properties of the cement Generally, limestone is 80%, and the remaining 20% The whole system of cement grinding station mainly includes cement grinding, cement homogenization and batching, cement packaging and bulk loading And the system is composed of cement mill, OSEPA highefficiency separator, elevator, packing machine and so on In order to meet the customers' requirements on different granularity of auxiliary materials, it can be Clinker Grinding Unit CHAENGCement Grinding Unit EPC Solution With a strong RD team, experienced engineers, and firstclass technical services, we aim to provide users with the most advanced and optimized cement production solutions The main task of the cement grinding plant is to grind the cement clinker into particles with a certain fineness to make it into finished Cement Grinding Plant Expert Cement Grinding Solutions from The power ingesting of a grinding process is 5060% in the cement production power consumption The Vertical Roller Mill (VRM) reduces the power consumption for cement grinding approximately 3040% associated with other grinding mills The process variables in cement grinding process using VRM are strongly nonlinear and having large timePROCESS CONTROL FOR CEMENT GRINDING IN VERTICAL
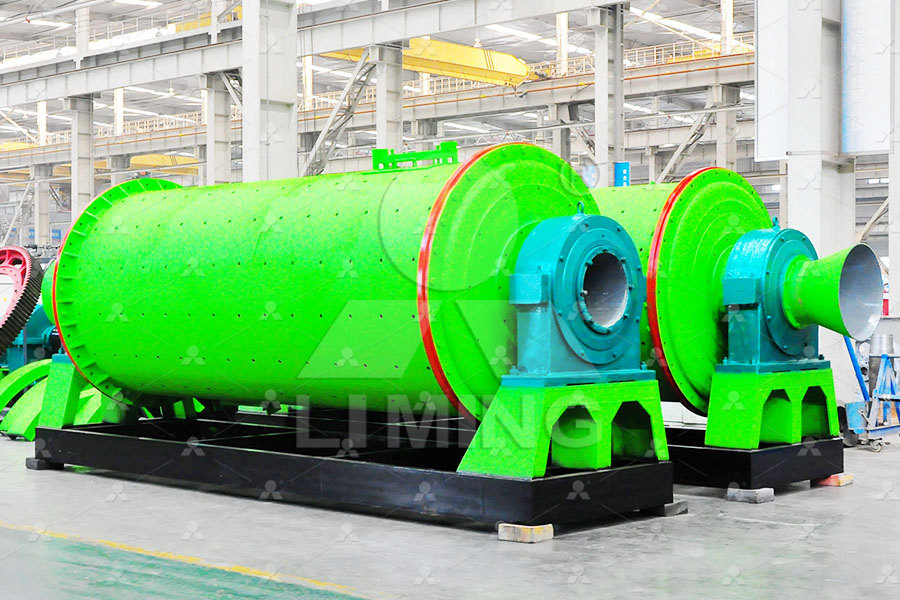
Cement Grinding Technology In Cement Production Process
2022年8月15日 Cement Grinding Technology in Cement Production Process English VersionIn this session I will explain about Cement Grinding Technology for cement productioCement grinding and packing process The clinker is ground with an amount of gypsum to a fine powder in order to regulate the setting time of cement and to gain the most important property of cement, which is compressive strength To produce different types of cement Cement grinding and packing process Al badia cement2022年10月13日 A proper amount of gypsum is added to the clinker, and sometimes some mixed materials are added They are ground together to form cement cement grinding plant manufacturing process The manufacturing Differences Between Grinding Plant Cement Plant2024年9月10日 Cement Manufacturing Process Cement manufacturing is an intricate process involving the extraction and grinding of raw materials, followed by blending and heating in a kiln to produce clinker This clinker is then ground Cement Manufacturing Process: Know Extraction,
.jpg)
Resistance to Grinding and Cement Paste Performance of Blends
2021年4月19日 Grinding of finished cement is performed in a single stage, intergrinding materials with very different grindabilities This intergrinding process has many different interactions among the different components of the finished cement In a context of developing more sustainable and less energy intensive processes, it is important to understand the Chemical process industries are running under severe constraints, and it is essential to maintain the endproduct quality under disturbances Maintaining the product quality in the cement grinding process in the presence of clinker heterogeneity is a challenging task The model predictive controller (MPC) poses a viable solution to handle the variability This paper addresses the Predictive Controller Design for a Cement Ball Mill Grinding Process The production process of Portland cement is representative in cement production It uses limestone and clay as the main raw materials, which are crushed, Cement grinding station is an industry with green benefits Types of cement you need to know about Commonly used raw materials for cement grinding stations 1Cement Grinding StationHongji Mining Machinery2018年8月28日 cement manufacturing process phase ii: proportioning, blending grinding; cement manufacturing process phase iii: preheating raw material; cement manufacturing process phase iv: kiln phase; cement manufacturing process phase v: cooling and final grinding; cement manufacturing process phase vi: packing and shipping; cement manufacturing Cement Manufacturing Process The Engineering Community
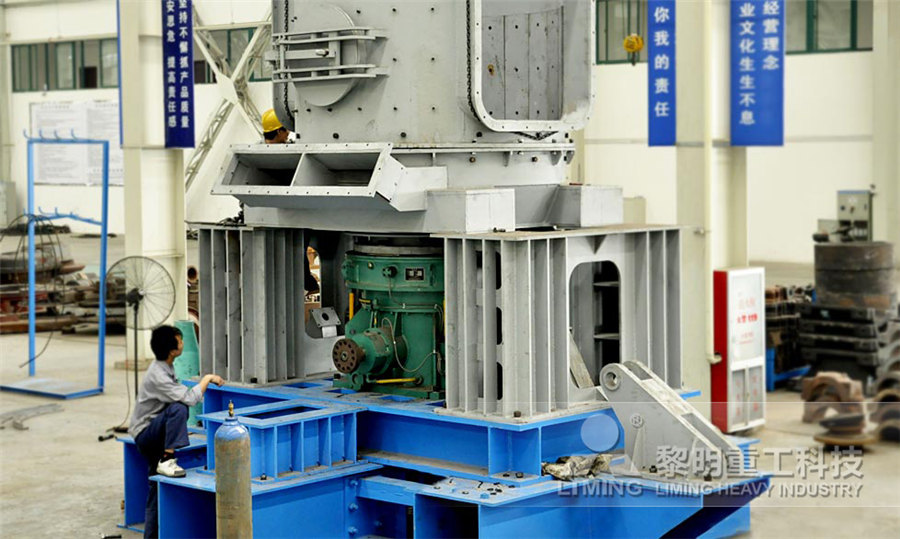
PROCESS CONTROL FOR CEMENT GRINDING IN VERTICAL ROLLER MILL
The power ingesting of a grinding process is 5060% in the cement production power consumption The Vertical Roller Mill (VRM) reduces the power consumption for cement grinding approximately 3040% associated with other grinding mills The process variables in cement grinding process using VRM are strongly nonlinear and having large time delay characteristics 2016年1月1日 A Review Article on Manufacturing Process of Cement, Environmental Attributes, Topography and Climatological Data Station: IMD, Sidhi MP(PDF) A Review Article on Manufacturing Process of Cement The grinding process consumes the most energy in cement production, its energy consumption accounts for more than 70% of the total power consumption in the whole process of cement production There are three main grinding processes in cement production: raw meal grinding, cement grinding, and raw coal grindingBall Mill Roller Press for Cement Grinding ProcessIn container number #3 we have included the dynamic separator, the bag filter and the process fan 1 This 3rd generation dynamic separator allows you to produce high Blaine cements with full guarantees, low bypass and energy saving 2 This 2m bags filter will collect the cement and precipitate it into the siloModular and portable grinding station Plug and Grind classic