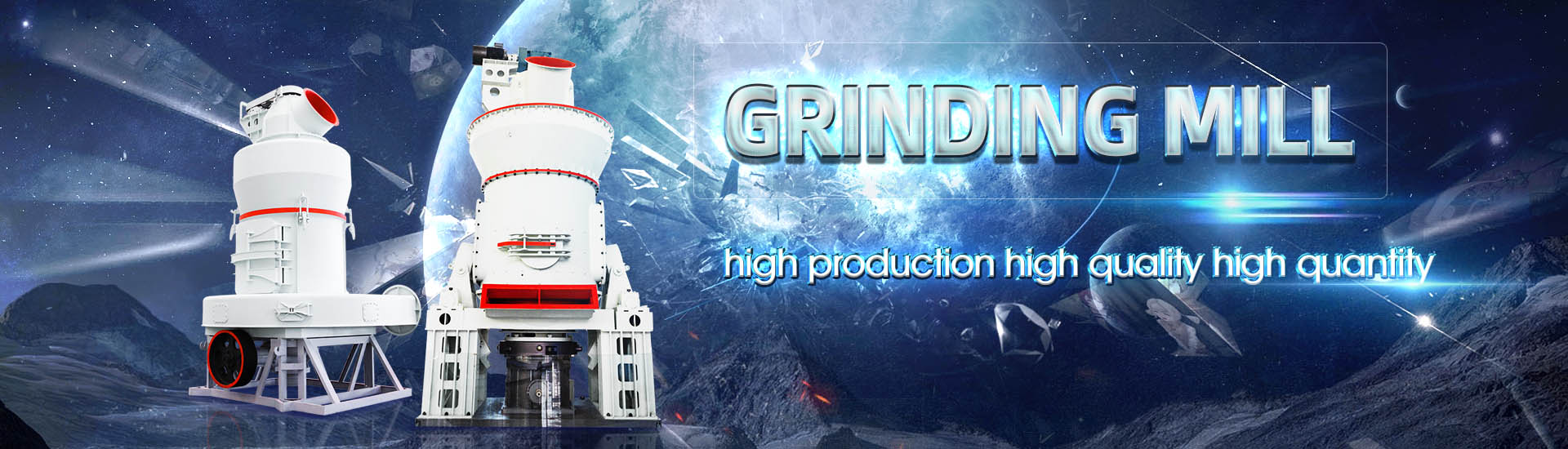
Process flow of water slag grinding
.jpg)
A new technological approach to the granulation of slag melts of
2021年11月3日 It is shown that the main advantage of the proposed HVG process is the provision of forced highspeed vortex convection of water, with the effect of vertical suction, crushing, and degassing of the threephase (water–slag granules–water vapor) heterogeneous eat orders As early as 1928, when the first Loesche mill was put on the market, the grinding principle of the vertical roller grinding mill, with a driven grinding track and springloaded rollers 2 µm 5 µm Loeschehe molten slag is poured into a special drum and cooled rapidly by sprinkling water over the slag In addition, research and development has been applied to a new process whereby molten Processing and Reusing Technologies for Steelmaking Slag2022年6月1日 We demonstrate a continuous pilotscale process to produce calcium hydroxide from iron slag The threestep process includes leaching, RO concentration, and temperature A pilotprocess for calcium hydroxide production from iron slag
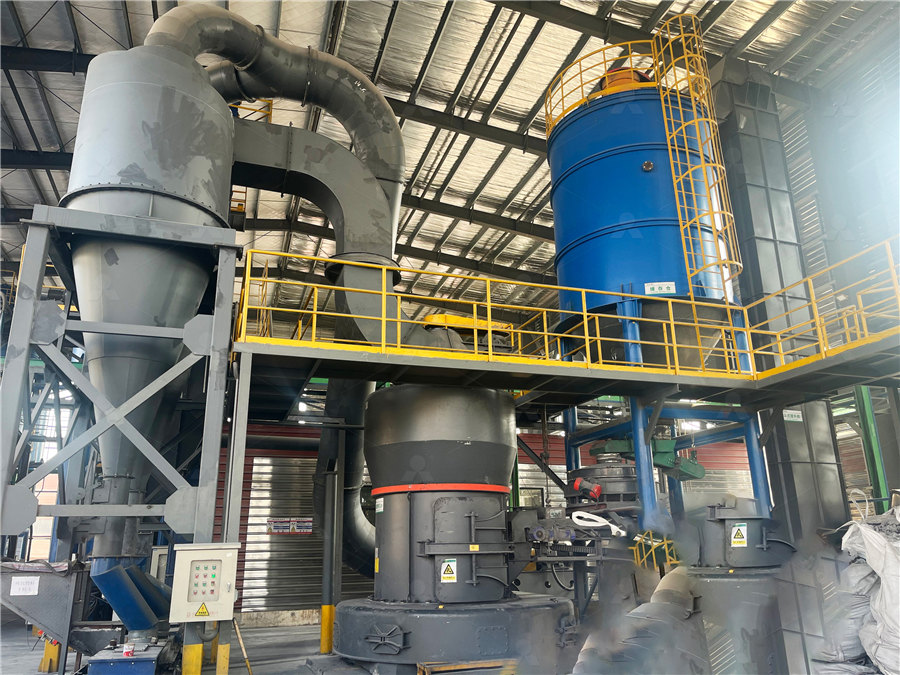
Granulation and Heat Recovery from Metallurgical Slags
2019年12月9日 The granulation processes employ mechanical impact or highpressure fluids (eg air or water) to break up the slag into small granules of typically 1–5 mm There are 2021年9月1日 In this paper, the wet extractive grinding method for efficient recovery of calcium from steelmaking slags was studied This work supports the Sustainable Development Goal of Detailed performance analysis of the wet extractive grinding 2020年5月1日 Experimental study on the calcium extraction from steel slag by combining wet grinding and extraction It is found that with the new extractive grinding method 50–60 % yield Wet extractive grinding process for efficient calcium recovery from 2021年6月24日 With the innovative approach presented in this work, it is possible to recover thermal heat from liquid slags The process concept consists of a slag tundish and four Process Concept for the Dry Recovery of Thermal Energy of Liquid
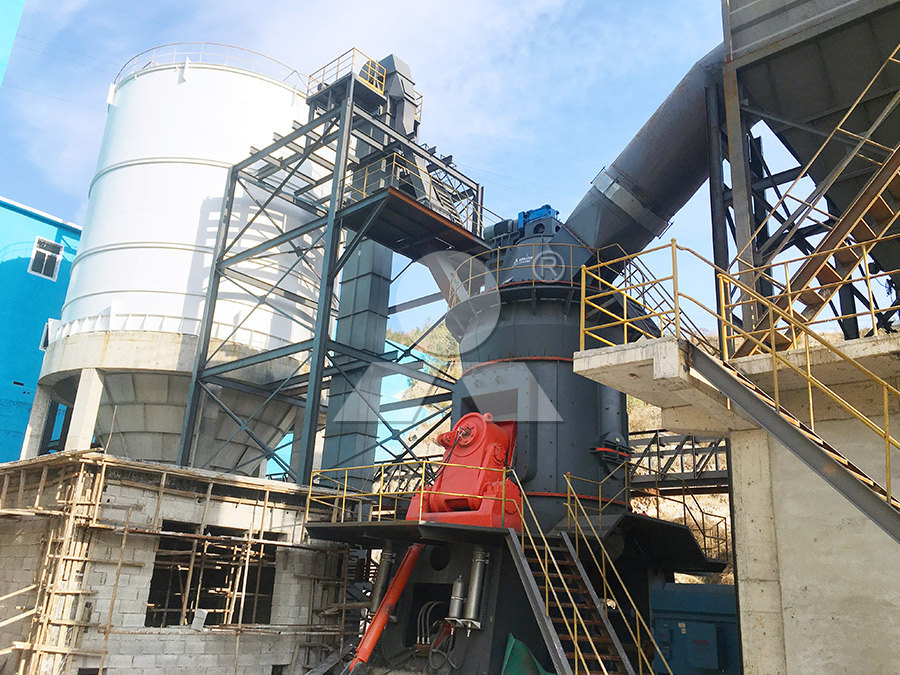
GRINDING Grinding options for slag and pozzolan PEC
sents extra challenges to the grinding process A careful assessment of grinding options a anulated blastfurnace slag (GBS) and pozzolans However, these materials present high 2019年5月23日 The water quenching method includes furnacefront water quenching and outdoor water quenching Furnacefront water quenching means pouring hightemperature Comprehensive Utilization Technology of Steel Slag2022年6月24日 PDF Grinding is a manufacturing process which significantly contributes in producing high precision and durable components required in numerous A heavy stream of water was applied to the(PDF) A comprehensive review on the grinding process: 2023年11月20日 Mineral process wastes, such as metallurgical slags nowadays, are of significant metals and materials resources in the circular economy The usability of ironmaking slag is well established; however, steel A Review on Environmental Concerns and
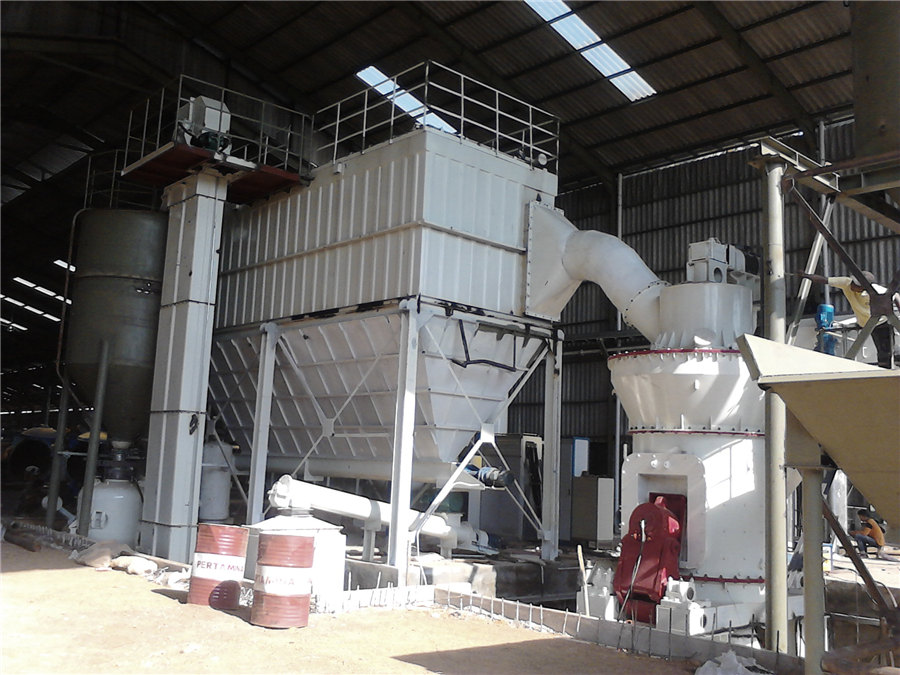
PROCESS OPTIMISATION FOR LOESCHE GRINDING PLANTS
vertical roller grinding mills for grinding: • Coal • Cement raw material • Clinker / granulated slag • Industrial minerals, and • Ores The core elements of these plants are the Loesche vertical mills for drygrinding the abovementioned grinding stock Loesche has 2022年2月2日 Yang and Yu used a multistage grinding, subsequent roasting, and flotation method to recover iron from copper slag The process flow chart is shown in Fig 4 When the copper slag grinding fineness was 0074 mm, the roasting temperature was 1000 °C, the roasting time was 1 h, and the final iron ore concentrate was obtainedA Review of Comprehensive Utilization of Copper Slag of ChinaWater quenching blast furnace slag (WQBFS) is widely produced in the blast furnace iron making process It is mainly composed of CaO, MgO, Al2O3, and SiO2 with low contents of other metal elements Treatment procedure of water quenching blast furnace slagProcess flow diagram (wet process): Wet process: The dryprocess steel slag production process does not need to consume precious water resources After the steel slag is crushed, rod milled, and magnetically separated, the slag steel can be selfgrinding to obtain grade A and B scrap steel The iron content of the slag powder can reach more Steel slag recycling crushing and grinding production line
.jpg)
Comprehensive utilisation of blast furnace slag Taylor Francis
after the blast furnace slag has been water quenched in front of the furnace, the slagwater mixture is concentrated, filtered and dewatered, and then the filtered water is reused through a settling tank The method has a strong processing ability and good quality of water quenched slag into slag, but due to its complex2007年5月1日 Slag Atomising Technology (SAT) Slag Atomising Technology is a process that converts molten slag (13001350ºC) into small spherical balls with a diameter range of 01 to 45mm The process consists of a high speed air blowing system with catalyst and water exposed to the stream of falling molten slag out of a tundish into the yardSlag Atomising Technology (SAT): Strategic management of 2023年8月22日 Grinding is usually used to increase the specific surface area of steel slag to improve its activity However, due to the large amount of hardtogrind minerals in steel slag, a large amount of energy is wasted in the grinding process Therefore, the current investigation aims to remove the hardtogrind minerals in steel slag as much as possible to explore the The Effect of Removing HardtoGrind Minerals from Steel Slag on 2024年1月31日 Kang W, Xiaoli L, Chao J, et al Optimal tracking control for slag grinding process based on adaptive dynamic programming Acta Automatica Sinica 2016; 42: 1542 Yan L Progress in research on mixing techniques for transverse injection flow fields in supersonic crossflows Journal of Zhejiang UniversitySCIENCE A 2013; 14: 554 Intelligent process control system for predicting operating

Comprehensive utilization of steel slag: A review ScienceDirect
2023年5月15日 Steel slag is the main solid waste generated in the steelmaking process, accounting for 15 to 20% of crude steel output [1]China's crude steel output in 2021 was 1035 billion tons [2], more than half of the global crude steel output (19505 billion tons) [3], and the steel slag output exceeded 120 million tonsIn contrast, the comprehensive utilization rate of Download scientific diagram Process flow sheet for Pelletization using wet grinding process from publication: Iron Ore Pelletization Technology and its Environmental Impact Assessment in Eastern Process flow sheet for Pelletization using wet 2023年7月21日 112 The Lhasa method (RASA) The Lhasa method (RASA) water granulated slag treatment system was developed by Nippon Steel Pipe and the British trading company RASA and was first applied on blast furnace No 1 at Fukuyama Steel Works in Japan [Citation 4]The principle of the RASA method is that after the blast furnace slag has been water Comprehensive utilisation of blast furnace slag Taylor Francis The main challenge of the steel industry for the next decade is the steel production transformation process, starting in Europe The CO 2 intensive blast furnace/basic oxygen furnace (BOF) route will be substituted by a combination of Direct Reduced Iron (DRI), based on natural gas, later on “green” hydrogen, with an Electric Arc Furnace (EAF) or a Submerged Arc Furnace (SAF), The steel production transformation process in Europe: New slag
.jpg)
Comparison of Grinding Characteristics of Converter Steel Slag
2016年10月28日 The converter steel slag cannot be widely used in building materials for its poor grindability In this paper, the grinding characteristics of untreated and pretreated (ie, magnetic separation) steel slag were compared Additionally, the grinding property of pretreated steel slag was also studied after adding grinding aids The results show that the residues (ie, oversize 2023年11月8日 Grinding and magnetic separation of titanium slag; Desulfurization, Process flow diagram of titanium slag smelting process From loading hoppers, ilmenite concentrate and reductant are separately fed to dosing hoppers (position 24) through a system of belt conveyors circulating process water;Titanium Slag Production Process: Technologies To Improve 2023年2月15日 Slag bricks Slag brick production process Slag brick is made by mixing, watering, grinding and pressing slag and limestone In the production process of slag brick, the particle size of the slag is generally smaller than 8 mm, and the steam temperature injected into the kiln is about 80 ℃ to 100 ℃, the maintaining time is about 12 hoursHow to Process Slags (with detailed process)? Fote MachineryMixed GGBS and water into a wetgrinding tank, and ground at a speed of 400 r/min for 30 min and 60 min to prepare GGBS slurries (WT1 which is accompanied by a simultaneous reduction in hydration heat flow Utilization of lithium slag by wetgrinding process to improve the early strength of sulphoaluminate cement paste J Clean Effect of ground granulated blastfurnace slag slurries by wetgrinding
.jpg)
Manufacture Of Portland Cement Process Flow chart civil
2019年11月30日 Significant advancements have been made in raw material grinding, preheating, controlled clinker cooling, cement grinding, and packing technologies with advanced process control and instrumentation system in recent yearsThe open circuit grinding process is the earliest slag powder grinding technology It has the advantages of simple process, low technical requirements for operators, and low investment cost The unit power consumption of this system is about 100kWh/t per grinding slag with a specific surface area of 450m 2 /kgGGBS Production Line Slag Mill for Slag Powder Grinding AGICO2024年4月15日 Therefore, in this study, the process of “roasting–grinding–magnetic separation” was selected to recover iron and other valuable metals from lead slag The principle flow is shown in Fig 3 (2)Iron recovery from lead smelting waterquenching slag by 2024年8月15日 The gravity separation of metallic copper from CSS is significantly influenced by the grinding time and backwash water flow rate Therefore, a detailed investigation the gravity and flotation separation process doesn't produce any waste slag or water, and the combined process can remarkably increase the copper recovery and reduce Efficient recovery of copper from copper smelting slag by gravity
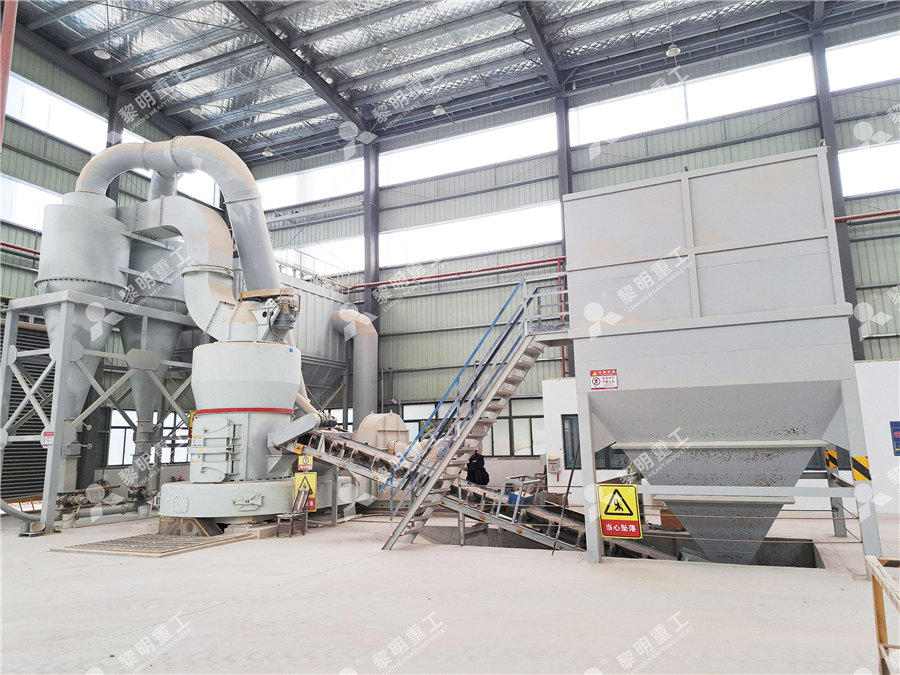
The technical flow process of recycling ironrich
Download scientific diagram The technical flow process of recycling ironrich phases in steel slag from publication: Comparison of Grinding Characteristics of Converter Steel Slag with and 2019年9月10日 With prolonging of carbide slag grinding time, the slump flow increased from 190 mm to 210 mm, whether using mix or divide grinding process, slurry slump flow gradually decreased with the extension of grinding time which increased the adsorption water on particles surface and relatively reduced free water for liquidityThe slurry and physicalmechanical performance of autoclaved aerated 2022年2月3日 However, we did not show a continuous integrated process, a key step towards process intensification In addition, the proposed process could have a large water footprint, requiring 5400 L of water per kg of Ca (OH)2 produced Thus, implementing water recirculation is essential to demonstrate that this technology is technically viableA pilotprocess for calcium hydroxide production from iron slag where m j is the mass flow rate of the carbonated slag and entrained water, C p j is the specific heat capacity of the carbonated slag and water, m 0 is the mass of the removed water, \(\triangle H{evp}\) is the heat of vapourization for water, \(\eta{heat}\) is the thermal efficiency of drier, with a selected value of 085, and ∆T i is the temperature difference in the drying process Carbon Dioxide Sequestration via Steelmaking Slag Carbonation
.jpg)
Process Concept for the Dry Recovery of Thermal Energy of Liquid
2021年6月24日 Industrialscale applications incorporating the recycling of those byproducts are common since many decades and include examples like (1) the grinding of waterquenched blast furnace slag (GGBFS) to receive hydraulic properties for their use in cement, (2) using stabilized slags as aggregates in roads and civil installations, (3) using freelime and phosphorous 2021年7月12日 The physical or empirical modeling of the grinding process and the effects of its parameters on the workpiece quality is sophisticated This is due to the extreme complexity of the process So far, no remarkable success could be made by the proposed models to achieve a reliable and effective design and control of the process This article introduces an expert Development of an expert system for optimal design of the grinding processof granulated blastfurnace slag and pozzolans presents extra challenges to the grinding process A careful assessment of grinding options available is key to efficient grinding operations n by Frank Benavides and Russell Reimer, PEC Consulting Group LLC, USA GRINDING 1 SEPTEMBER 2022 INTERNATIONAL CEMENT REVIEW T he increasing pressure to useGRINDING Grinding options for slag and pozzolan PEC 2012年3月1日 This article describes the results when grinding cement and granulated blastfurnace slag and discusses t h em with regard to factors that affect the engineering process When using grinding aids Operating experience with a vertical roller mill for grinding
.jpg)
Steel slag in China: Treatment, recycling, and management
2018年8月1日 Slag aging also is used to stabilize freeCaO and freeMgO into calcium or magnesia hydroxide (Nishinohara et al, 2013) This process involves spraying steel slag with water steam and then covering it with tent sheets in a yard The duration of the entire process takes about six daysThe blast furnace slag ball mill can effectively process the slag and obtain the ground blast furnace slag with the particle size of 0074089mm, which are used for grinding watergranulated blast furnace slag and steel slag Blast Furnace Slag Ball Mill2020年11月19日 As the titanium industry rapidly develops, lowgrade ilmenite resources are drawing global attention The direct use of lowgrade ilmenite can result in low production efficiency and heavy pollution In addition, the production of hightitanium slag via electric furnace melting consumes significant energy and possesses low production efficiency Therefore, a HighTitanium Slag Preparation Process by Carbothermic2022年9月25日 The factors affecting the flotation index of copper minerals include slag cooling process, slag properties, flotation process conditions, etc (Stanojlović and Sokolović, 2014; Roy et al, 2015; Linsong et al, 2022) The slag cooling mode is an important factor including slow cooling and water quenchedExtraction and separation of copper and iron from copper smelting slag
.jpg)
Process flow sheet for Pelletization using dry grinding process
Download scientific diagram Process flow sheet for Pelletization using dry grinding process from publication: Iron Ore Pelletization Technology and its Environmental Impact Assessment in Eastern 2017年2月8日 Based on the mineralogical analyses of slag, the tested copper smelting slag was composed of fine particles with complex association and dissemination, in which bornite was the main copperbearing mineral Under the condition of the grinding fineness of −0074 mm and the proportion of 80%, flotation exhibited highest efficiencyThe Recovery of Copper from Smelting Slag by Flotation Process2018年1月1日 It was found that grinding of titanium slag particles to 40 μm contributes to more complete In the water leaching process, the Na(+) was exchanged a flow sheet was Study of soda effect on the sintering process of low titanium slag2012年6月1日 The process input variables in the figure are: u 1 − mill feed water flow rate, u 2 − fresh ore feed rate, u 3 − mill critical speed fraction, u 4 − sump dilution water flow rate and u 5 Grinding in Ball Mills: Modeling and Process Control
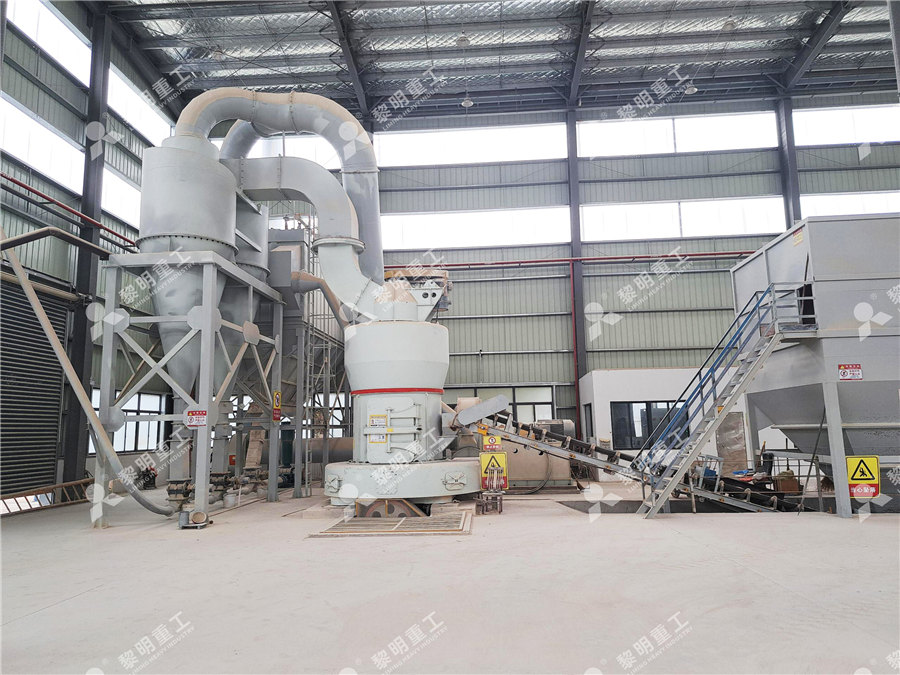
Analysis and multiobjective optimization of slag powder process
2020年11月1日 The entire slag powder process is shown in Fig 2 Firstly raw slag materials are transported into the vertical mill through the conveyor belt after iron removement and drying process The raw slag is ground under the pressure of the grinding roller and the millstone The slag powder is blown to the upper part of the vertical mill by the hot gas2018年6月1日 Moisture content is also a critical parameter in the grinding process as it significantly impacts various aspects, including grinding time, particle size, and power requirements (Jung et al, 2018)Effect of Moisture Content on the Grinding Process and Powder