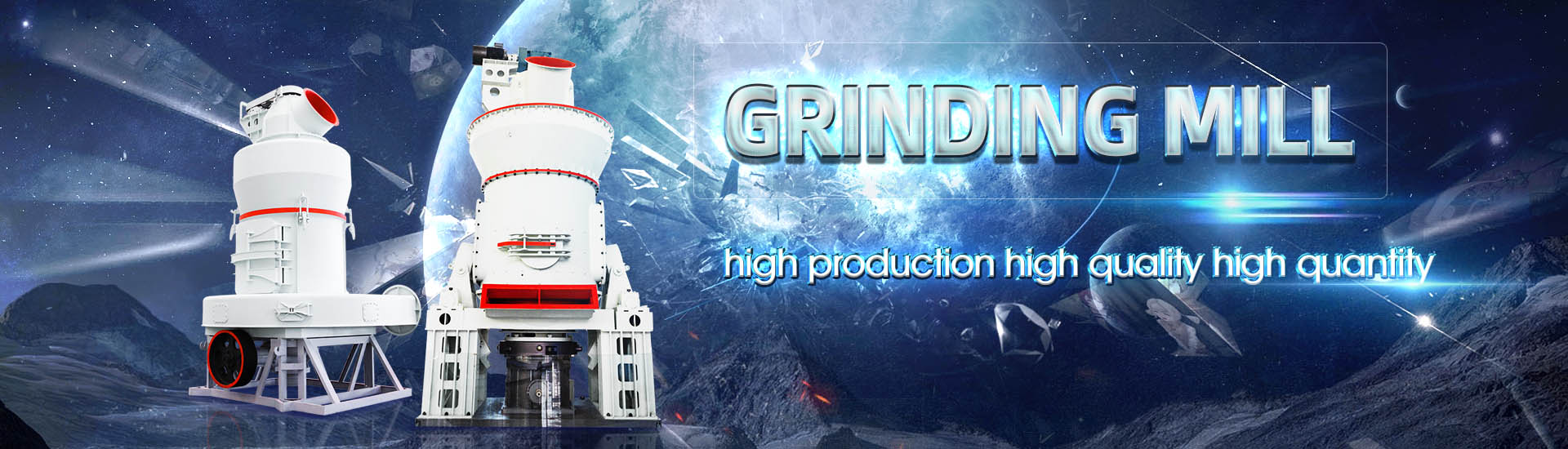
Clinker crushing and drawings
.jpg)
Process characteristics of clinker and cement production SINTEF
Purpose: Optimization of the oxyfuel clinker burning process based on process modeling verified by prototype results Oxyfuel principle: Air is replaced by recirculated CO 2 in the plant, to The process of clinkerization signifies conversion of raw meal into clinker minerals mainly consisting of C4AF (Aluminoferite), C3A (Aluminite), C2S (Belite) and C3S (Alite) phases along with small percentage of free lime CaO, MgO, Alkalies, Clinkerization Cement Plant Optimization2 Crusher and PreBlending: The material is then crushed to reduce particle sizes and blended to reduce variability in composition 3 Raw Mill and Kiln: Raw materials and additives are A practical guide to improving cement manufacturing processes Design, implementation and modernisation of clinker storage installations, customised as per requirement, achieve maximum customer benefit Adapted to the customer`s specific Clinker Storage Systems Aumund
.jpg)
The Cement Plant Operations Handbook International Cement
Nonclinker mineral additions require separate installations for storage, preblending, crushing, drying and feeding Materials such as granulated blastfurnace slag (GBS) with a high moisture In this study, the inservice performance of highMn steel hammers used in the clinker crusher environment was analyzed Microstructural and mechanical property evaluation was Inservice Performance of HighManganese Steel Clinker Crusher 2023年8月1日 Multiphased sintering technology is an innovative process that directly utilize granular steel slag to calcinate cement clinker In this study, we synthesized a type of multi Direct use of original granular steel slag to prepare multiphased They are crushed and transferred to preblending storage where other substances (such as sand, iron ore, bauxite, shale, slag, fly ash) are added to get the desired chemical compositionCement Clinker Manufacturing Process with Reactions
.jpg)
Clinker Production an overview ScienceDirect Topics
Clinker production is the most energyintensive stage in cement production, accounting for more than 90% of total industry energy use and virtually all the fuel use The main kiln type used suitable for rock crushing and sizing operations Although highMn steels have limited high temperature applicability, they have been used in clinker crusher operations as well In this study, the inservice performance of highMn steel hammers used in the clinker crusher environment was analyzed Microstructural and mechanical property evalInservice Performance of HighManganese Steel Clinkerindustry: Calcination and cement clinker burning Calcination of raw material CaCO 3 => CaO + CO 2 Process emissions of raw material: = 054 t CO 2 /t clinker Endotherm reaction at 950 °C ca 1700 MJ/t clinker ≈ 50% of energy Cement clinker burning at 1450 °C formation of hydraulic properties of clinker Thermal energy requirement:Process characteristics of clinker and cement production SINTEFCrushing: the limestone and other materials are crushed into small pieces by cement crusher, such as hammer crusher, cone crusher, jaw crusher, impact crusher, etc Mixing: according to the requirement of clinker, compound Preparation Of Cement Raw Material Cement Mill,
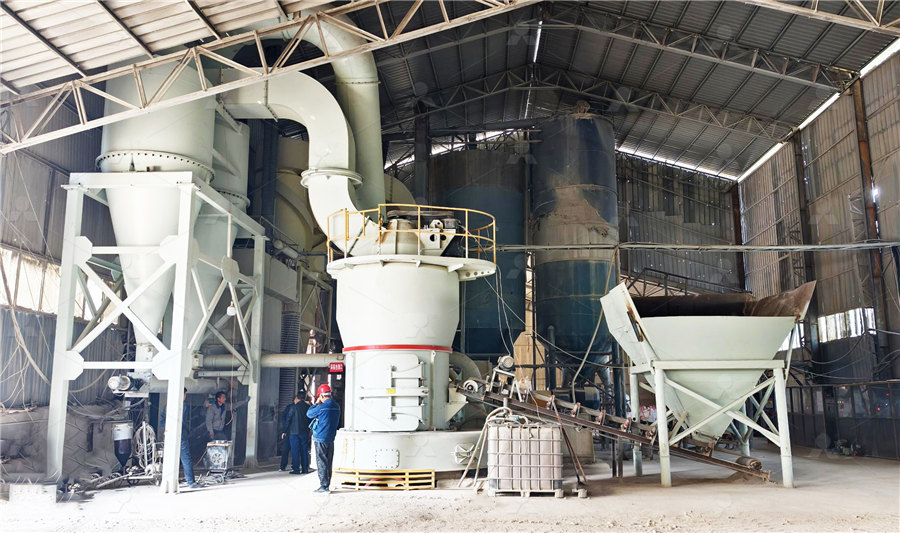
Cement Clinker Manufacturing Process with Reactions
Extraction and Preparation of Raw Materials The main raw materials (limestone, clay chalk or basalt) are quarried from natural rocks They are crushed and transferred to preblending storage where other substances (such as sand, iron ore, bauxite, shale, slag, fly ash) are added to get the desired chemical composition2022年9月21日 The cement and clinker produced by indirect mechanosynthesis (15 min of mechanical activation and heat treatment 900 C or 1200 C) were characterizedCement and Clinker Production by Indirect Mechanosynthesis Definitions the invention relates to a roll crusher for crushing hot bulk material, such as, for example, cement clinker discharged from a baking kiln, having at least two crushing rolls which are arranged in parallel, are driven in opposite directions and have a rotatably mounted supporting tube, onto which in each case a multiplicity of crushing rings to be connected to the supporting Roll Crusher for Crushing Hot Cement Clinker Google Patents2019年8月27日 The major raw materials used as a source of CaO for cement manufacturing are limestone, chalk, marl, etc These raw materials by virtue of their natural occurrence contains other mineral impurities eg, MgO, SiO 2, Al 2 O 3, Fe 2 O 3, alkali compounds, and sulfidesThese impurities play an important role to influence the cement manufacturing Cement Manufacturing and Process Control SpringerLink
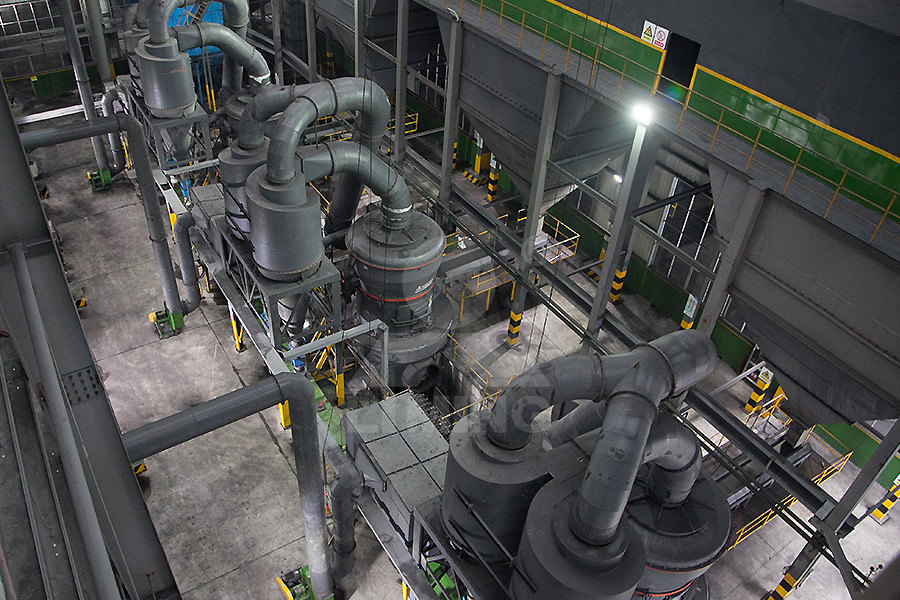
Cement Euipment Overview Cement Making Machines Cement
2019年9月27日 Clinker cooler and dryer Clinker cooler and dryer are two necessary parts of cement clinker production The dryer produced by AGICO can apply for various raw materials and easy to adjust During the operation, the dryer supplies heat stably, ensures the drying quality and cement quality The cement cooler is also used for clinker productionWith over 800 clinker coolers commissioned around the world, Claudius Peters represents a leading role in the clinker cooling technology Starting in the 1950’s, Claudius Peters has gained almost 70 years of experience and has been responsible for many of the innovative milestones reached in the past decades that are considered today as state of the art in the cement industryClinker Cooling Claudius Peters2022年1月23日 The first crushing of the bauxite may often take place at the mine before transport to the alumina refinery if located nearby, or to the shipping port for export At the refinery further crushing and/or washing may take place before the crushed bauxite is subjected to a grinding operation for final sizing before digestionPhysical Bauxite Processing: Crushing and Grinding of BauxiteCement Clinker Cooler Grate Plates AGICO Cement Plant Spare Parts and Steel Castings AGICO Cement has the ability to produce and process various steel castings, and can manufacture full range of cement plant spare parts according to the drawings, including clinker cooler spare parts, crusher spare parts, ball mill spare parts, kiln spare parts,vertical roller mill Clinker Crusher And Drawings
.jpg)
Clinker Crusher Hammers > Crusher Parts > Products
DSMAC has successfully designed and manufactured SANDWICH® Super High Chrome hammerhead, which is used for clinker crushing equipment Designed with incomparable high technology, and we accept processing with supplied Keeps crushing, and crushing, and crushing and 2 An optimal crusher solution can help keep a kiln and cooler operating at peak efficiency The HRB MF (heavyduty roll breaker modular frame) sets the standard in clinker breakers and is FLSmidth’s standard recommendation for the important task of crushing clinker at busy cement plantsFLSmidth CrossBar Cooler Brochure DirectIndustry2016年2月29日 Any multistage crushing plant will have a “bottleneck” stage, and it is this stage which establishes the production rate of the entire plant; therefore, inasmuch as it consists of drawing off an intermediate size, or sizes, of product the amount of which, at any time, runs in excess of the capacity of the reduction crushersCrushing Plant: Surge Bins VS Stockpiles 911MetallurgistThe clinker crushing apparatus of the bottom ash processing facility according to an embodiment of the present invention includes a base frame, a left and right support rotatably coupled to the base frame, and a horizontal rotation axis orthogonal to the rotation axis of the left and right rotation support so as to be rotatable An intermediate support frame coupled up and down KRB1 Apparatus for breaking clinker in a dry bottom
.jpg)
Cement Extraction, Processing, Manufacturing Britannica
2024年11月23日 There are four stages in the manufacture of portland cement: (1) crushing and grinding the raw materials, (2) blending the materials in the correct proportions, (3) burning the prepared mix in a kiln, and (4) grinding the burned product, known as “ clinker,” together with some 5 percent of gypsum (to control the time of set of the cement)Hammer crusher is the hammer mill machine used in the cement production line The industrial hammer crusher produced by AGICO has a large crushing ratio, high production capacity, low energy consumption, and simple structureHammer Crusher Hammer Mill Machine AGICO Hammer Mill Definitions the invention relates to a roll crusher for crushing hot bulk material, such as, for example, cement clinker discharged from a baking kiln, having at least two crushing rolls which are arranged in parallel, are driven in opposite directions and have a rotatably mounted supporting tube, onto which in each case a multiplicity of crushing rings to be connected to the supporting Method for crushing hot cement clinker Google Patentsits crushing process Whereas most other types of crusher use metallic parts to crush rock, the Kinglink VSI uses the rock fed into the machine to crush itself This autogenous crushing process produces the bestshaped aggregate on the market today The high velocity impact crushing achieved in a Kinglink KLSeries VSI improvesVertical Shaft Impact Crusher
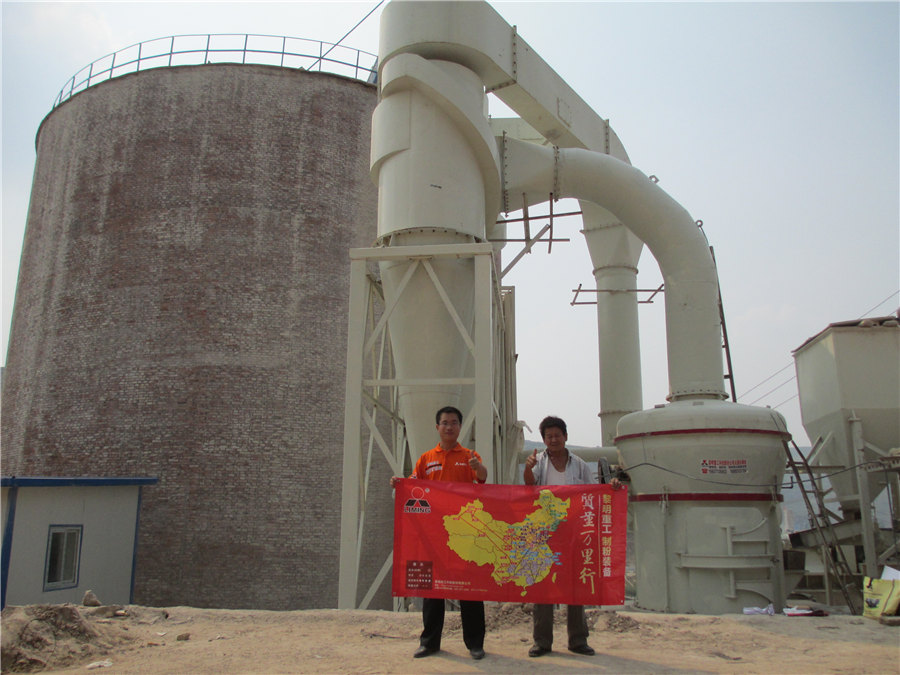
Hopper Discharge Systems Aumund
and cement clinker The pan profile provides a high resistance against buckling and consequently accepts considerable hopper loads Where adequate, the plate edges may be fitted with wearresistant protective caps The traction force required to reclaim the material from the hopper is calculated on the basis of the hopper geometry Chains featuring2021年8月26日 This research aimed to investigate the environmental, economic, and functional performances of ordinary portland cement (OPC) In short, we discussed the definition, the chemical composition and Study and Review of Ordinary Portland CementSuperior's Cemco VSI boasts global usage, persistently processing a wide range of materials in diverse industries The Cemco Vertical Shaft Impactor creates cubical aggregates, manufactured sands, and eliminates unsound materialCemco® Vertical Shaft Impactor (VSI) Superior IndustriesStep 3: clinker cooling Clinker cooling is the final step in clinker production This process aims to recycle heat, preheat the secondary air, and improve the quality and grindability of the clinker Besides, the rapid cooling of the clinker in this process is convenient for cement storage and transportation Clinker CoolerClinker Production Clinker Manufacturing Cement
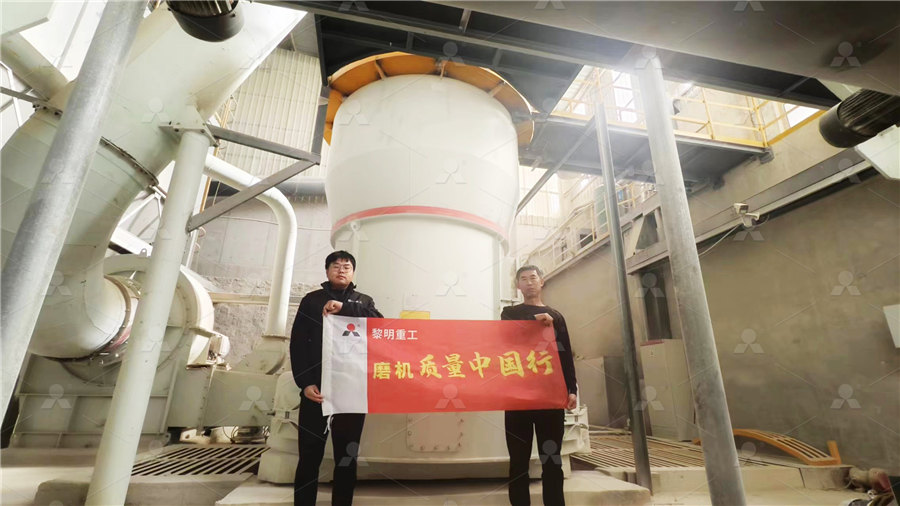
PROCESS ENGINEERING FOR THE CEMENT LIME INDUSTRIES
PROJECT: CLINKER COOLER STACK SAXUM scope of work: Complete basic and detailed mechanical and structural engineering, drawing sign off and stamping, for the new clinker cooler stack to be installed in the St Mary’s Cement plant as part of the plant upgrade project Votorantim North America St Mary´s CementHSC550 Jaw Crusher – a proven troublefree performer, this crusher reliably delivers consistent crushing results across materials including raw meal, clinker, cement, slag, ores, oxidic material and ferroalloys, with a feed size up to 50 mmFine Jaw Crushers FLSmidth• Impact crushing on anvils and also autogenous crushing between material springing back from anvils and material thrown from rotor occurs at the same time • This type of crushing is recommended for low and medium abrasive materials such as gravel, limestone, dolomite, diabase, bricks, cement clinker etcVERTICAL SHAFT IMPACT CRUSHERSThe grate cooler is a quenching type cement cooler applied for the cement manufacturing plant According to the movement mode of the grate, the grate cooler can be divided into three types, rotary type, vibrating type, and pushtype grate cooler, with the development of cooler technology, pushtype grate cooler is considered the most common clinker cooler in the cement production Grate Cooler In Cement Plant Clinker Cooler, Cement Cooler
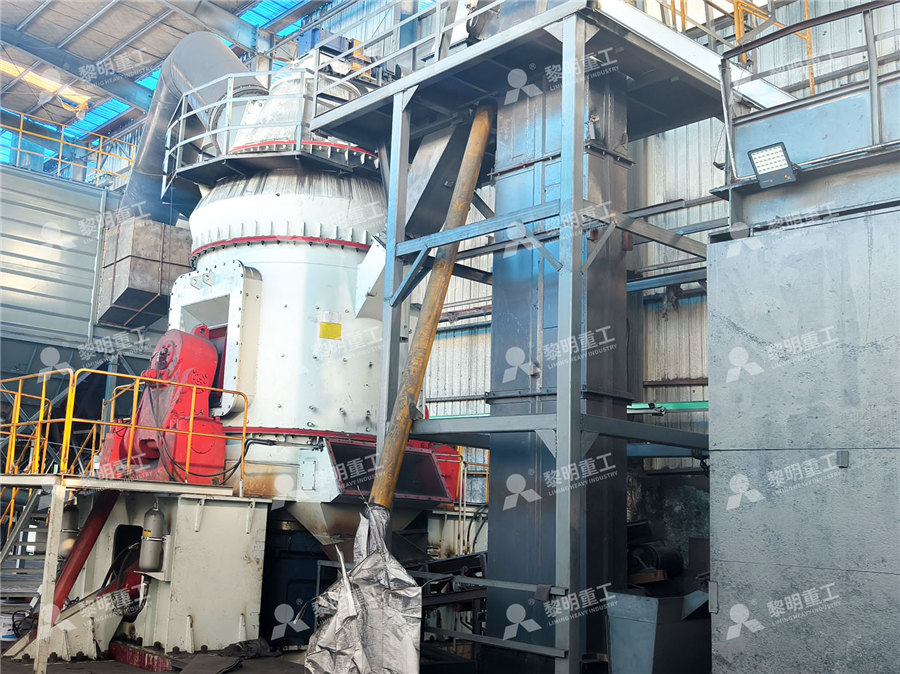
Modelling the cement process and cement clinker
2013年1月1日 In the clinker, increased Cl1 decreased the proportion of Pb and Cd, moreover, Pb and Cd increased in kiln dust with Cl1 increased; Calculations using a kiln dust recycle model showed that, and heated into clinker 4 Clinker Analysis: The cooled clinker elemental composition is determined, then ground into fine particles There are 4 stages of cement production that help maintain consistent raw material quality with minimal chemistry deviation, from quarry to silo to customer Request quote or infoA practical guide to improving cement manufacturing processes After crushing, the crushed limestone is piled longitudinally by an equipment called stacker / reclaimer The hot clinker from kiln discharge is cooled very quickly/ quenched in air with the help of efficient coolers The temperature of clinker is brought to 50oC from 1400oCKnow all about cement manufacturing process in india mycem 2022年1月22日 Cone crusher is advanced crushing equipment in the mining field Its outstanding advantages are a high degree of automation, wide particle size adjustment range, and stable operation In the process of cement clinker processing, a high degree of automation means that the operation process and steps of the equipment can be further simplified, which What Are The Cement Clinker Crushing Equipment?
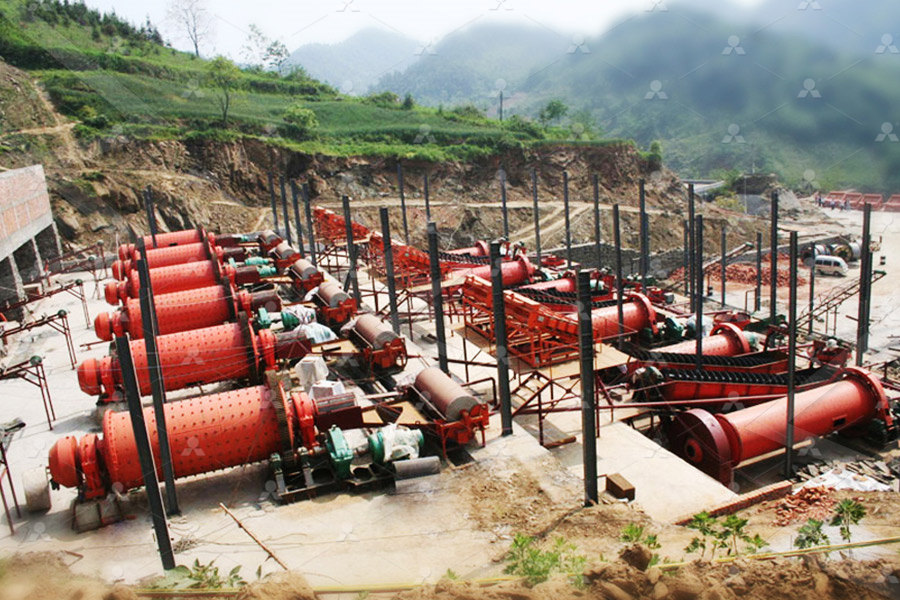
Cement Manufacturing—Technology, Practice, and Development
2021年11月17日 Clinker Manufacturing Process Cement grinding Cement dispatch All these steps are described in detail in the next sections crushing, blending, and drying Subsequently, it is used for feeding to the cement mill Commonly used materials include volcanic rocks, limestone or calcined clay, granulated blastfurnace slag, The stacker and reclaimer is the prehomogenization system in the cement plantAs a necessary part of the cement production line, it can concurrently or respectively complete the stacking and reclaiming The stacker and reclaimer play a vital role in the limestone prehomogenization, stabilize the condition of cement kiln, ensure the clinker qualityStacker And Reclaimer Cement Plant PartsWe supply raw cast and machined parts according to drawings for the main manufacturers in the sector, for both trains and infrastructures Cement Since its inception, ESTANDA has had an important presence in the cement sector, becoming a prestigious international benchmark in the supply of cast parts for different phases of the cement manufacturing processHOME Fundiciones EstandaCrushing ability: the tray is equipped with moving jaw plates to enhance the crushing ability The heat consumption of clinker in modern shaft kiln can be controlled within (600 ~ 700) For spare parts: size and dimensions, material and weight, and your drawings with details, you can send the drawing to Kiln, Vertical Shaft Kiln, Vertical Kiln Cement Plant
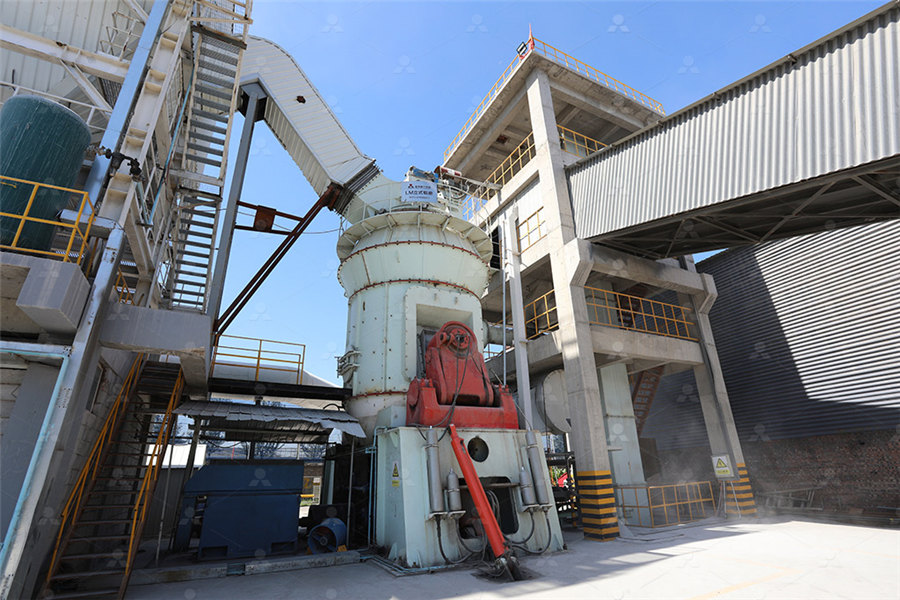
Clinker Crusher Hammer Manufacturer EB Castworld
Clinker Crusher Hammer Manufacturer Clinker Crusher Hammer Head are the most important wear parts of crusher, They are the wearresisting materials that are mainly used in metallurgy,mining and crushing equipment, including ordinary high manganese steel, modified high manganese steel, superhigh manganese steel, multicomponent alloy intensely Rotary cooler is one kind of cement cooler applied for cement manufacturing plantsAs an essential part of the cement kiln system, a rotary cooler is used to cool the clinker discharged from the cement rotary kilnThe rotary cooler also helps air to absorb the large amounts of heat carried by clinker, heating the combustion air up to the high temperature, strengthen the calcination, Rotary Cooler Clinker Cooler In Cement Plant AGICO CEMENT