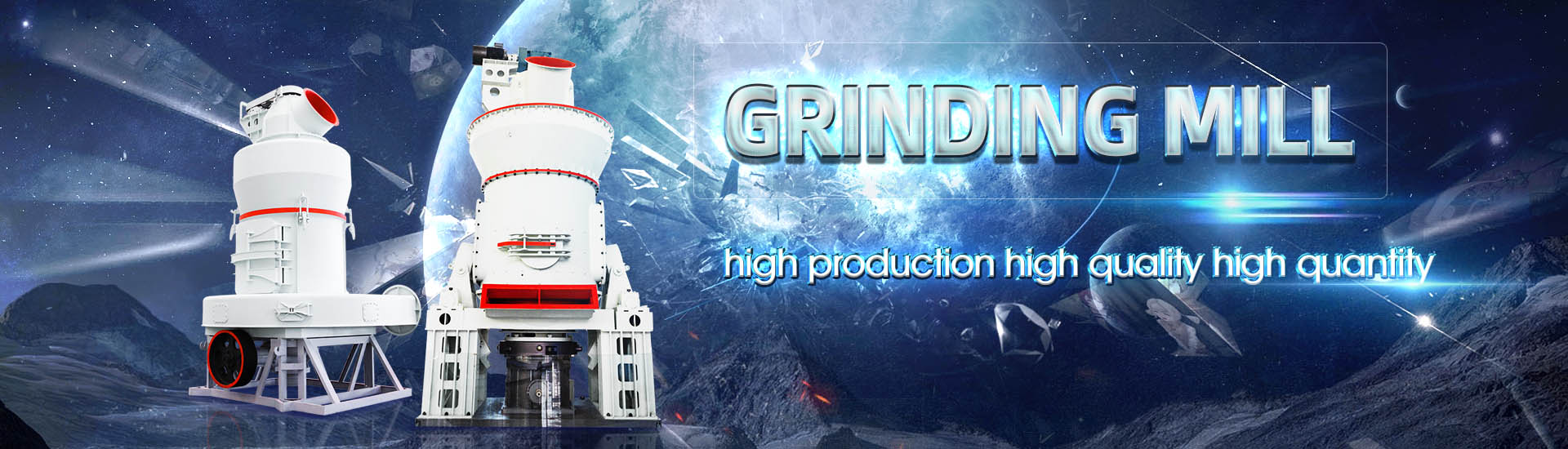
Diameter 3.2 meters by 13 meters cement mill output
.jpg)
sbm/sbm 32 multiplied by 13 m cement mill outputmd at main
Contribute to sbm2023/sbm development by creating an account on GitHubThis document contains calculations and specifications for a cement mill, including: Dimensions of the mill such as diameter, length, motor power, compartment lengths, and ratio of length to Mill Calculation: Plant: Date: Mill: Visa PDF Electric Power Scribd2015年8月1日 The material efficiency values for a raw mill, pyroprocessing tower, rotary kiln, clink cooler, and cement mill are determined to be 3669%, 3424%, 3924%, 2976%, and (PDF) Analysis of material flow and consumption in cement 2016年1月20日 In the surveyed cement plant, three balances are established between input and output material in the raw mill, clinker production, and cement grinding system 248 t, 469 t, Analysis of material flow and consumption in cement
.jpg)
sbm 32 meters cement mill production routemd
Contribute to sbm2023/sbm development by creating an account on GitHubimproving its carbon footprint (emissions per unit of output) by improving energy efficiency, increasing the use of alternative fuels, and deploying renewable energy sources With a IMPROVING THERMAL AND ELECTRIC ENERGY EFFICIENCY AT Optimization of the Cement Ball Mill Operation Optimization addresses the grinding process, maintenance and product quality The objective is to achieve a more efficient operation and OPTIMIZATION OF CEMENT GRINDING OPERATION IN BALL MILLS2020年5月1日 In this work, a cement ball mill (CBM) of a new generation cement plant is considered as a case study in order to study its efficiency based on both first and second laws Energy and exergy analyses for a cement ball mill of a new
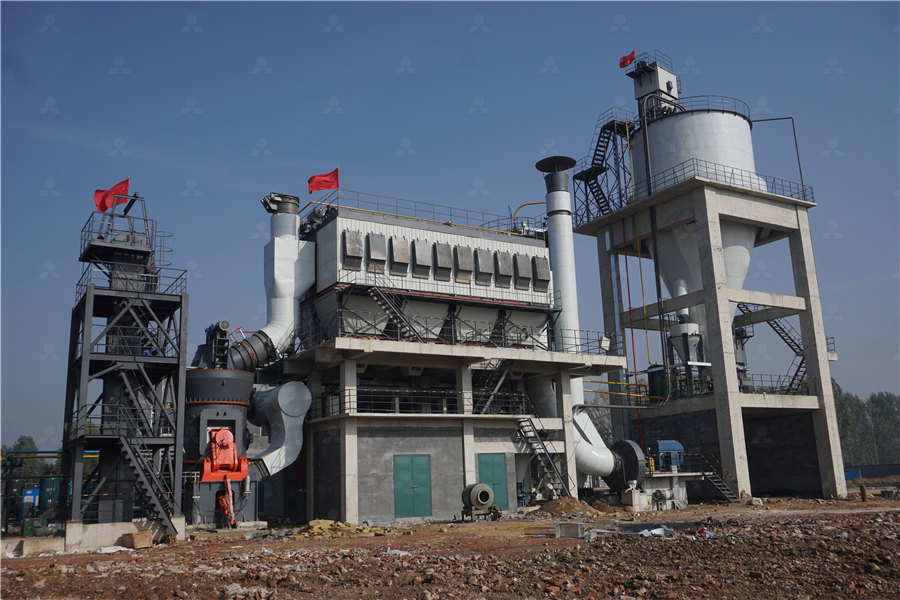
sbm/sbm 32 m cement mill capacitymd at main sbm2023/sbm
Contribute to sbm2023/sbm development by creating an account on GitHub2018年7月1日 This study aimed at optimizing both the energy efficiency and the quality of the end product by modifying the existing flowsheet of the cement grinding circuit As a general Energy and cement quality optimization of a cement grinding circuit1995年10月29日 The control system, based on a 2S4265 CNC unit, allows the milling machine to be operated in universal mode (with manual control), automatic mode (to a set program), copying mode, gauging mode (PDF) Cement mill optimization: Design parameters 2024年2月1日 Numerous noteworthy studies have been conducted on the analysis of improving the horizontal performance of a single pile through cementsoil reinforcement, including works by Rollins et al [20], Lin et al [21], Faro et al [22], and Zhang et al [23]Besides, OuYang et al [24] found through model experiments that Cementimproved soil reinforcement can effectively Performance enhancement of large diameter bored pile
.jpg)
Roller mills INFINITY FOR CEMENT EQUIPMENT
For a grinding plant designed for an output of 80 t of portland cement per hour a roller mill with a grinding bowl diameter of 41 m is required The total power consumption of the grinding plant is 265 kWh/t, cor responding to a 20 % KILN GAS is often used for the raw mill instead of the cement mill because the temperatures are higher than cooler air (typically 300 –350°C) and the raw meal is generally more moist than cement Kiln gas has high CO2 / CO content, and is therefore an explosion and safety hazard in Everything you need to know about clinker/cement GrindingCement mills are the milling machines used in cement plants to grind hard clinker into fine cement powders Cement ball mill and vertical roller mill are two most widely used cement mills in today’s cement grinding plants and are also the main types of cement mill we produce As a professional cement equipment manufacturer, AGICO has rich experience in the designing and Cement Mill for Sale Buy Cement Ball Mill Vertical Roller Mill 2024年1月26日 Cement ball mill is a well known machine to grind raw material (hard clinker) into grey powder: D = mill diameter inside liner (meter) K = proportionality constant = 335 for steel balls L = useful mill length (meters) For R = 21 m Computation of charging media for a double compartment cement ball mill
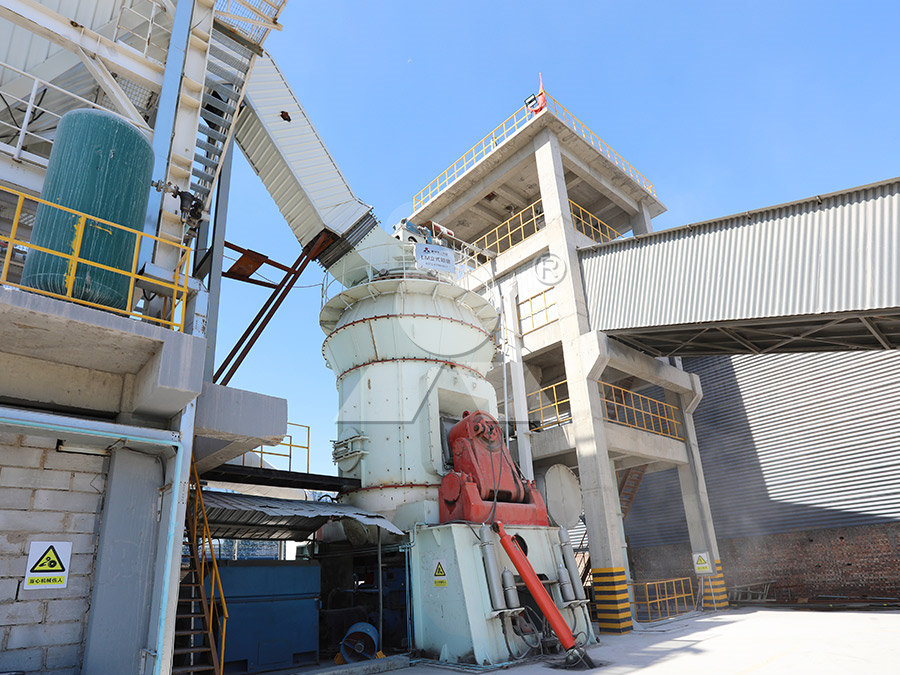
MECHANICAL ELEMENTS INFINITY FOR CEMENT EQUIPMENT
MECHANICAL ELEMENTS OF TUBE MILLS this is a part of ASEC Academy training Courses SUMMARY the mechanical elements of a tube mill could be separated into elements which have a direct function with the grinding process (ie grinding media, liners, diaphragms) and into elements which can be considered as individual units which are connected to each other to a 2015年2月14日 However, the measurement of material flow rates was not easier Costea et al [13] developeda fuzzy logicbased control architecture in which the ball mill grinding process was considered as a Control System Architecture for a Cement Mill Based on Fuzzy Contribute to sbm2023/sbm development by creating an account on GitHubsbm 32 meters cement mill production routemd2017年3月24日 These findings demonstrate the functional mechanism of the fiber diameter on the road performance of cementstabilized the readings from the two meters a t each end [13] [14] [15][16][17 (PDF) Impact of Fiber Diameter OnRoad Performance
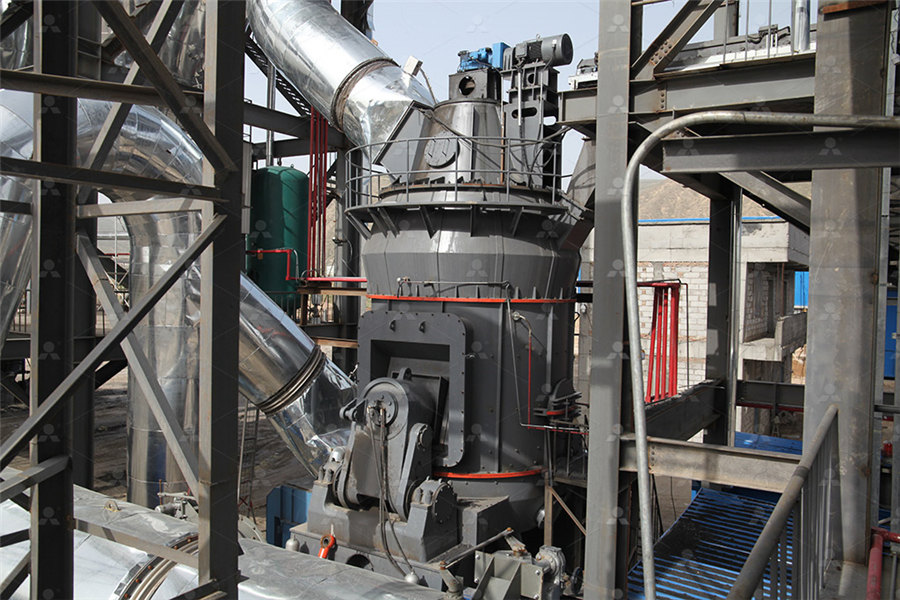
Optimization of ball mill operating parameters for their effect on mill
2014年1月1日 Download Citation Optimization of ball mill operating parameters for their effect on mill output and cement fineness by using RSM method 13403 μm and 17344 μm, respectively, Advantages of cement ball mill Less investment: cement ball mill with advantages of a perfect motor system, low energy consumption and power consumption, and ultralow operating cost, which can save a lot of cost input; Cement Ball Mill Ball Mill For Sale Cement Mill 15 2019年10月18日 One of the advantages of cement and the cement concrete industry in sustainability is the ability to utilize large amounts of industrial solid wastes such as fly ash and ground granulated blast Utilization of tailings in cement and concrete: A review2013年6月14日 Increments of production output were 135%, 125%, an d 105% for projects II, III, (113) 29 (53) 65 (90) In cement mill, Production yield, fineness and strength of cement as
.jpg)
The Ultimate Concrete Calculator (Cubic Meters/Yards Bags)
Hence, the calculator presents the volume of concrete as 13440 cubic meters However, this value represents the exact volume without taking into account any wastage, substrate and surface flatness, and other factors Thereby, in this example, we will consider ordering 14 cubic meters, The company’s cement ball mill has 31 specifications and models with a cylinder diameter ranging from 22m to 42m, and the supporting motor is 380KW to 3530KW A single cement ball mill can meet the grinding of 1187t cement products per hour, such as with a roller press Combined use, the production capacity will be greatly improvedBall Mill In Cement Plant Selling Various Types Of Cement Mill2016年4月25日 In cement industry about 110 kWh of electrical energy is consumed to produce one ton of cement and about 26% of the total electrical power is used during farine productionDetermination of correlation between specific energy consumption 2020年5月1日 Cement industry consumes a huge amount of electrical energy that is about 100 kWh/t (kWh per ton (10 3 kg) of cement) [16]In a cement plant, about twothirds of the total electrical energy is used for particle size reduction of raw materials and clinker [17]There is a diverse range of options to decrease the production expenses as well as CO 2 emissions that Energy and exergy analyses for a cement ball mill of a new
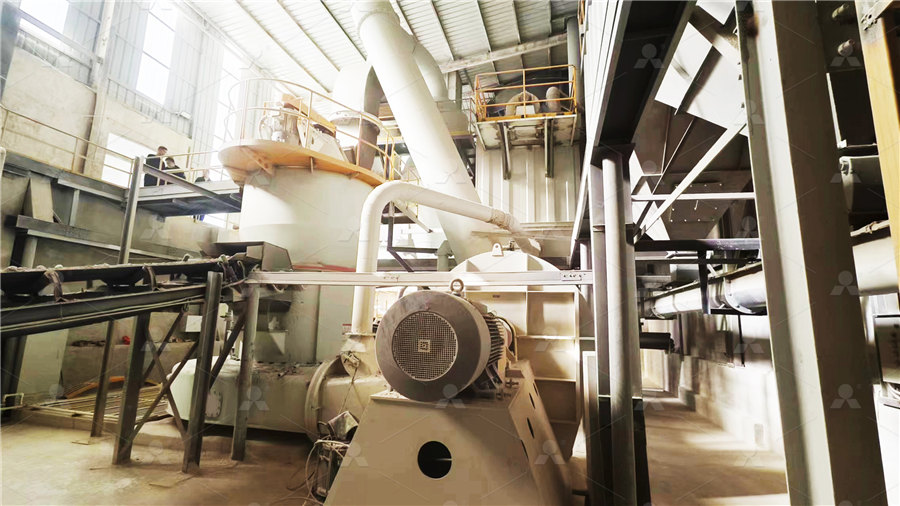
Ventilation Prediction for an Industrial Cement Raw Ball Mill
2021年6月10日 In cement mills, ventilation is a critical key for maintaining temperature and material transportation However, relationships between operational variables and ventilation factors for an industrial cement ball mill were not addressed until today This investigation is going to fill this gap based on a newly developed concept named “conscious laboratory (CL)” For level, coal mill output level also required to be increased Reduction in particle size coal mill internal diameter helped optimizing output at required Reduction in 90 micron residue 20 15 10 8 5 0 Before After MOTOR MOTOR BEFORE AFTER 20 15 10 5 0 Before After % Residue Coal Mill Output (Ton per hour) 142 132 COAL MILL COAL MILLUse of 100% Unconventional Fuel in Cement Kiln A Case Study(LOESCHE mill) e raw vertical roller mill has four rollers, 3000 KW main drive, 48 m table diameter, 216 m roller diameter with 330 t/h capacity (made by LOESCHE Company from Germany) e table Modeling of energy consumption factors for an industrial cement 2014年3月1日 M s belonging to the interval [13, 25] and with a stepwise increase of 01, the (k p , k i , k d ) sets are com puted for each cement type using t he average orOptimizing the control system of cement milling:
.jpg)
(PDF) Analysis of material flow and consumption in cement production
2015年8月1日 mill, pyroprocessing tower, rotary kiln, clink cooler, and cement mill are determined to be 3669%, 3424%, The kiln is 4 m in diameter and 60 m in and 1340% of the total output 3 Factors affecting ball mill performance 4 Ball mill improvements case examples 5 Conclusions question time Introduction Cement manufacture is energy intensive o Cement manufacture consumes typically 3,100 – 3,400 MJ of fuel/t clinker 90 130 kWh / t cement in a modern plant, more for older or less efficient plants;Improvements in New Existing Cement Grinding Mills by Tim 2019年7月31日 The kiln, which is a rotating steel tubular furnace measuring 60 to 90 meters in length and 6 meters in diameter, is lined with large heatresistant bricksEnvironmental Pollution by Cement Industry ResearchGateAGICO Cement provides vertical cement mill, vertical roller mill used for cement manufacturing, powerful grinding and homogenization, customdesign cement mill, onschedule delivery Skip to content +86 Vertical Cement Mill
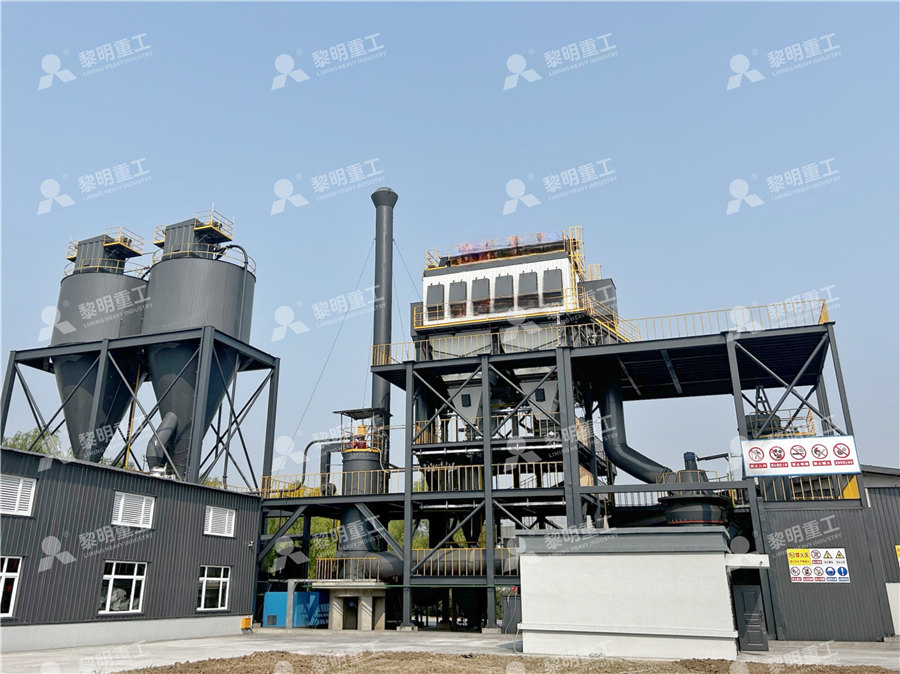
Selection of AC Induction Motors for Cement Plant Applications
The altitude at the site can also affect the motor selection when installation elevations exceed 1000 meters The lower density of air at higher altitudes results in a decreased cooling media for the motor The derate factor is 11% of the specified temperature rise for each 100 meters of altitude in excess of 1000 metersA 10 MW cement mill, output 270 tonnes per hour A cement mill (or finish mill in North American usage [1]) is the equipment used to grind the hard, nodular clinker from the cement kiln into the fine grey powder that is cementMost cement is currently ground in ball mills and also vertical roller mills which are more effective than ball millsCement mill Wikipedia2015年4月1日 1 Introduction Airswept raw meal ball mills introduced by the cement mill manufacturers FLSmidth ® (Smidth, 2002), Polysius ® (Polysius, 2002) and KHD Humboldt Wedag® are the most commonly used onesKHD Humboldt Wedag® manufactured fully airswept raw meal mills which have two compartments used for drying and grinding processesOptimization of a fully airswept dry grinding cement raw meal 2017年8月1日 Supposing that the maximum velocity of a ball is its terminal velocity when it falls from rest to the bottom of the mill, ie v r = 2 gh = 1066 m/s, where h is equal to the diameter of the mill, we can determine its maximum overlap percentage (with respect to the diameter) of a 70 mm diameter ball (Section 322)A generic wear prediction procedure based on the discrete
.jpg)
Cement mill, Cement grinding mill All industrial
Find your cement mill easily amongst the 28 products from the leading brands (Fritsch GmbH, Retsch, Bühler, Output: 50 kg/h The fast mill for all tasks With a freely adjustable rotor speed of 2,000 horizontal glass for ceramics disc 2022年11月1日 With a steadystate population balance model (PBM), their simulation results (Genc, 2016) suggested that for a given cement product fineness, the twocompartment mill yielded approximately 10 % higher mill capacity compared to the threecompartment mill, which contradicts the traditional design in the cement industry of operating threecompartment ball Impact of ball size distribution, compartment configuration, and One of the advantages of cement and the cement concrete industry in sustainability is the ability to utilize large amounts of industrial solid wastes such as fly ash and ground granulated blast furnace slag Tailings are solid wastes of the ore beneficiation process in the extractive industry and are available in huge amounts in some countries This paper reviews the potential Utilization of tailings in cement and concrete: A review De PDF On Oct 1, 2015, Mohan Singh Panwar and others published INCREASING OUTPUT OF CEMENT GRINDING IN BALL MILL CASE STUDY Student, 2 Guide, 3 External Guide Find, read and cite all the (PDF) INCREASING OUTPUT OF CEMENT GRINDING IN BALL MILL
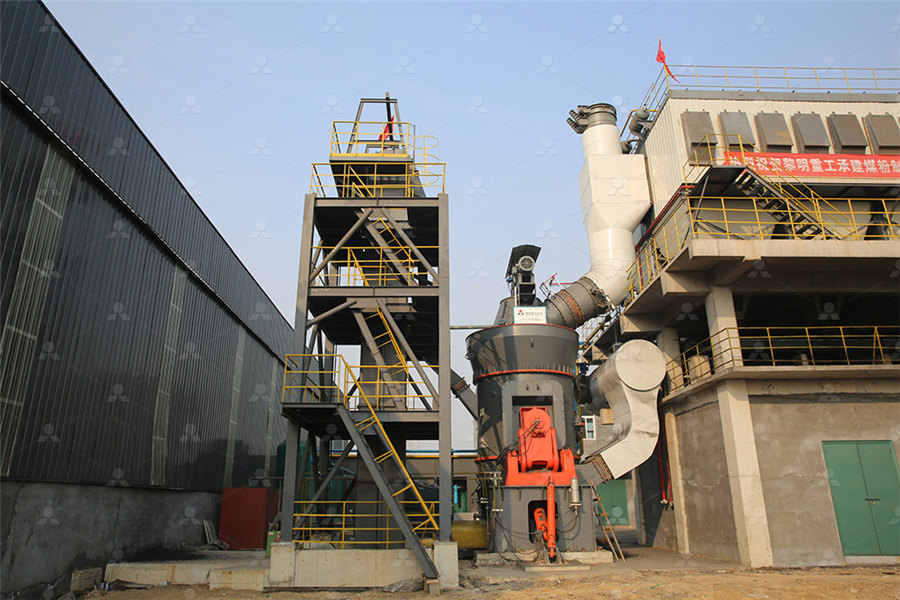
sbm 32 meters cement mill production routemd
Contribute to sbm2023/sbm development by creating an account on GitHubRaw mill is also known as cement raw mill, AGICO has a large area of the workshop of 30,000 square meters, High output: large crushing ratio and strong production capacity effectively improve the grinding fineness, and the processing capacity is increased by about 15%Raw mill Cement Plantcement, slag and blended cements Figure 1 OK 42 cement mill The OK mill was originally designed by Onoda Cement and Kobe Steel in the early 1980s From the early 1990s till today, the OK mill has since been successfully developed and manufactured by FLSmidth By combining product leadership with customer intimacy, we have improvedOK Mill: The 3: Mechanical optimized and 31: Grinding concept 2015年6月23日 3 ~ Nael Shabana 20103~ 60 Ventilation 70 Grinding and Generation of Heat 71 Heat Generation in Tube Mills 72 Cooling Procedures During Finish Grinding 73 Heat Balance for Mill Cooling 80 Cement Mill Specific Power Consumption 81 Calculation of Cement Mill Power Consumption 82 Calculation of the Specific Consumption of Energy per Ton of cementmill PDF Free Download SlideShare