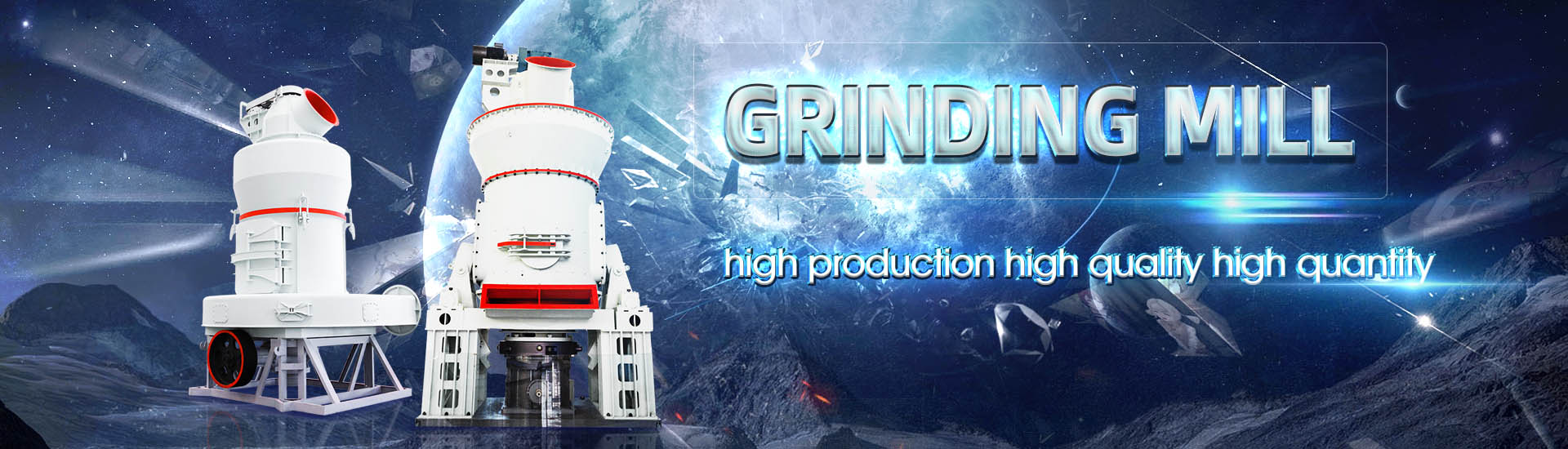
Sintered singleroll ore mill
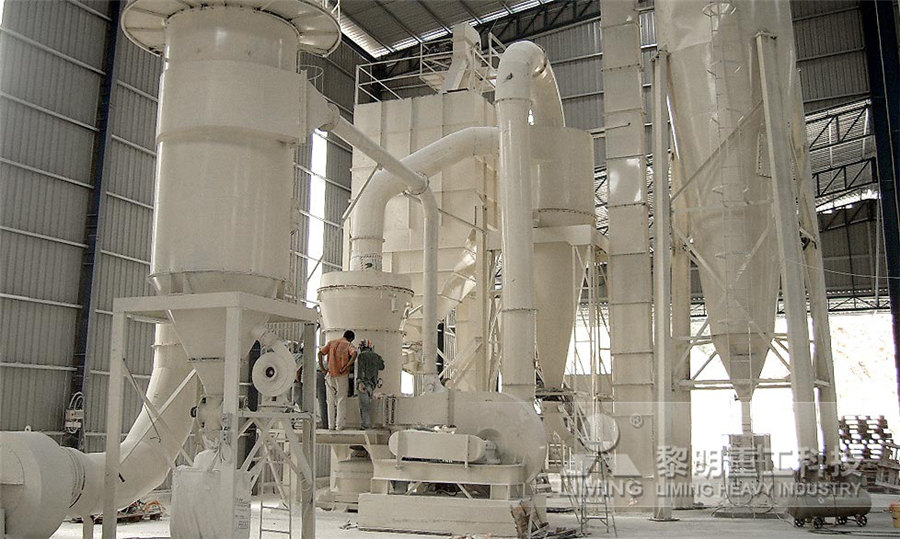
Efficient Single Roll Crusher for Sinter Crushing
The Single Roll Crusher (also referred to as Sinter Crusher or Single Roller Crusher) is a key piece of equipment in sinter production lines It is specifically designed to crush hot sintered In the Tobata No 3 Sinter Machine in Yawata Works, an SPExII line was introduced and has exhibited a high productivityenhancing effect (Fig 34))3, 4) In the line, a portion of iron ore is Improving Granulation of Sinter Materials by Using a Wet Vertical 2024年1月1日 Iron ore sintering is the iron ore powder agglomeration process that changes fine iron ore powder into the lumpy ironbearing raw material used for blast furnace ironmaking Iron Ore Sintering SpringerLink2011年2月1日 Preparation of the oiled rolling mills scale's with application of peat reduces interval between start evaporation and ignition points of the oil which favours its better Utilising of the oiled rolling mills scale in iron ore sintering
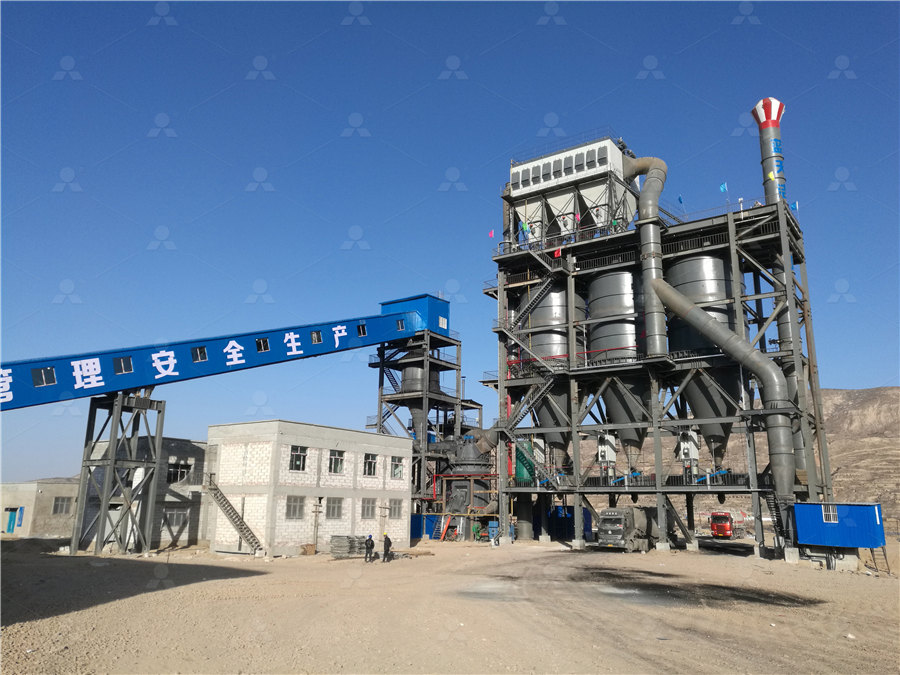
Iron Ore Sintering: Process Taylor Francis Online
2017年3月24日 Sintering is a thermal agglomeration process that is applied to a mixture of iron ore fines, recycled ironmaking products, fluxes, slagforming agents, and solid fuel (coke) The 2013年8月1日 The present work provides information on the iron ores that form part of the mineral mix which, once granulated, is loaded onto the sinter strand where it is partially melted at a temperature of(PDF) Iron ore sintering Part 1 Theory and practice of industry In recent years, with the increasing steel production and demand for sinter in China, the fluctuating iron ore quality and trade situation have brought certain challenges and potential Iron ore granulation for sinter production: Developments, the crushing process of sintered ore, and the roll tooth structure of single roll crusher is optimized based on the simulation results Firstly, the sintered ore specimens were studied by Optimization of roller teeth based on the analysis of the crushing
.jpg)
Utilising of the oiled rolling mills scale in iron ore sintering
2011年2月1日 Industrial trials demonstrate possibility to increase the oil combustion degree at sintering 27 times as much Consumption of the oiled scale was increased from zero to 2016年8月24日 Sintering is the most economic and widely used agglomeration process to prepare iron ore fines for blast furnace use Owing to the depleting reserves of traditional high grade iron ore, there have been considerable Recent advances in iron ore sintering Taylor Francis EFFECTS OF MILL ROTATIONAL SPEED ON THE BATCH GRINDING KINETICS OF A UG2 PLATINUM ORE By DINEO MOKGANYETJI MAKGOALE Submitted in accordance with the requirements for the degree of MAGISTER TECHNOLOGIAE in the subject ENGINEERING: CHEMICAL at the UNIVERSITY OF SOUTH AFRICA SUPERVISOR: Prof FRANCOIS EFFECTS OF MILL ROTATIONAL SPEED ON THE BATCH GRINDING KINETICS OF 2011年9月13日 In this contribution results from physical and technological testing of different sintered microcrystalline aluminum oxide abrasive grains are presented For the physical testing an innovative test stand based on a grain mill was used Significant differences of the measured friction forces were obtained for two different sintered microcrystalline abrasive grain types In Grain mill test for sintered microcrystalline aluminum oxide abrasive
.jpg)
Effect of Addition of Mill Scale on Sintering of Iron Ores
2016年6月30日 Ironrich (65 to 70 pct total Fe) mill scale generated during processing by steel mills can be recycled by using it as a ferrous raw material in the sintering process The effect of mill scale addition on the phase formation of sintered specimens from an industrial sinter blend containing 0 to 15 wt pct mill scale was examined, and the mineral phases formed during 2022年1月1日 Due to mechanical stress during transport, iron ore sinter partly degrades and fines are produced, which have to be resintered causing high costs and emissionsDevelopment of an automated single particle impact tester for iron ore 2015年11月21日 CRUSH, GRIND and CLASSIFY in a single pass! YOU Will save time, money and labor with the Gibson combination Elliptic Roll and Ball Mill• It is the first successful mill put on the market that will take the mine run of ore Crush grind and classify in a single pass • Horsepower consumption over one third less than ordinary ball millsGibson Roll Ball Mill 911Metallurgist2001年8月1日 The selfexcited horizon vibration of singleroll driving mill is analyzed The nonlinear equation of the horizon motion is derived base on analyzing the relationship between relative velocity and Qualitive analysis of selfexcited horizon vibration in singleroll
.jpg)
Roll reducing mill CSM MACHINERY
Rolls are manufactured of hardened alloyed steel or of steel with sintered carbide rings Sintered carbide rolls offer up to 4 times longer service than steel rolls Consequently, it is advisable to order sintered carbide rolls for frequently occurring tube sizes Silent operation; Low noiselevel of the machine Quality; Straighter elementsIn this 18roll stand, the very thin rolls are supported against lateral buckling With the 18HS mill design, highstrength and stainless steel grades can be produced more efficiently Integrated in a continuous tandem cold mill, our 18HS allows you to set up a Cold rolling mills for stainless steel SMS group GmbHRequest PDF On Mar 15, 2015, Mathis Reichert and others published Research of iron ore grinding in a verticalrollermill Find, read and cite all the research you need on ResearchGateResearch of iron ore grinding in a verticalrollermill1993年9月1日 Semantic Scholar extracted view of "Comminution of single particles in a rigidlymounted roll mill part 2: product size distribution and energy utilization" by O Gutsche et minution of single particles in a rigidlymounted roll mill
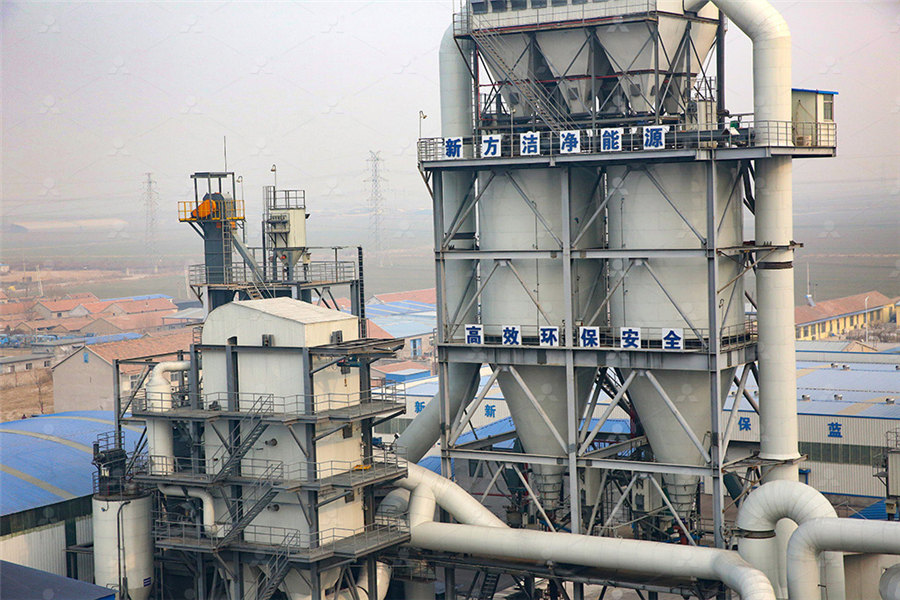
Sintering: Most Efficient Technologies for Greenhouse Emissions
2019年7月19日 So, the sintering process main objectives are to increase the size of ore additives to a level acceptable to the blast furnace for improving permeability of burden inside the BF; to form a strong agglomerate with high bulk reducibility; to remove volatile matter like CO 2 from carbonates, H 2 O from hydroxides, and sulfur from sulfide type of ore fines along with 2022年9月21日 The most effective approximation to date for expressing the behavior of softened sintered ore has been the elastic bodybased model By adopting the DEM, which expresses each sintered ore particle as a single spherical particle, and by associating the interparticle contact force according to Heltz’s elastic contact theory with Young’s modulus, it is possible to express Dynamic Model of HighTemperature Sintered Iron Ore PlasticSingleroller mill With the singleroller mills, brittle, soft to mediumhard materials can be reduced in size with a reduction ratio of approx 1:5 to 1:5 The stepped arrangement of the crushing jaws on the crushing wall enables any material Roller Mills by SIEBTECHNIK TEMA Crushing milling Download Citation On May 23, 2023, Bo Dai and others published Optimization of roller teeth based on the analysis of the crushing mechanism of sintered ore Find, read and cite all the research Optimization of roller teeth based on the analysis of the crushing
.jpg)
Sintered Ore an overview ScienceDirect Topics
2019年12月24日 Energy Resources, Its Role and Use in Metallurgical Industries RC Gupta, in Treatise on Process Metallurgy: Industrial Processes, 2014 423132 Sinter Making The iron ore fines (− 10 mm) are agglomerated using Dwight Lloyed sintering machine The iron ore fines and coke breeze fines mix with moisture is fed on the sinter bed which is ignited by a gas 2024年11月1日 In this paper, the adaptability between H 2rich gas injection and sintered ore performance with different raw material ratios was systematically analyzedFirst, the sintering indexes before and after H 2rich gas injection were compared to evaluate the impact of H 2rich gas injection on the yield and quality of sintered ore with different fine ratios and basicityAdaptability analysis of H2rich gas injection and sintered ore Rolling mill consisting of four rolls or known as a 4 High rolling mill is used for reducing material to extremely small thicknesses Through the use of larger backup rolls, the issues of roll deflection can be avoided and smaller work rolls can be used This reduction in work roll diameter: Reduces overall separating force required for reductions4 High Rolling Mill Element Machinery2023年5月23日 The JH2 constitutive model of sintered ore was obtained based on relevant tests and theoretical derivation, and used finite element method to reveal the crushing mechanism of sintered ore, and found that the maximum stress was Optimization of roller teeth based on the analysis of the crushing
.jpg)
Rolling Mills Rolls – IspatGuru
2013年12月8日 Based on the microstructure of the roll materials , the rolls are classified as (i) hypo eutectoid steel rolls, (ii) hyper eutectoid steel or ‘Adamite’ rolls, (iii) graphitic hyper eutectoid steel rolls, (iv) high alloyed steel rolls, (v) spheroidal graphite iron rolls, (vi) indefinite chill cast iron rolls, and (vii) Special materials such as sintered carbide and ceramic rolls2016年6月30日 Secondly, any Fe 2 O 3 which forms through oxidation of the FeO and Fe 3 O 4 in the mill scale only begins to convert to Fe 3 O 4 above ∼1150°C (see Figures 1 and 2) and so no appreciable Effect of Addition of Mill Scale on Sintering of Iron Ores2019年8月14日 Secondary crushing of the ore before the Single Stage SAG mill The most cost effective option to achieve the obje ctive of 10% increase in throughput in a moreOptimisation of secondary crushing stage before 2017年12月20日 Until the 1950s of the last century, the oxidized iron ores that were loaded into the blast furnace had granulometries within 10 and 120 mm However, the depletion of highgrade iron ore sources has made necessary Iron Ore Agglomeration Technologies IntechOpen
.jpg)
Desiliconisation and Dephosphorisation Behaviours of Various
2019年2月20日 Three types of solid oxygen materials (sintered return ore, scale briquette and fine mill scale) were carefully investigated as hot metal pretreatment agents, evaluating their desiliconisation 2017年7月26日 We will consider an ore with a ball mill work index varying between 16 and 13, feeding into a single stage ball mill operation with one million kilowatts per day consumed power For the particular mill configuration, a performance graph, Fig (21), has been constructed according to Bond’s methodsHow Ball Mill Ore Feed Size Affects Tonnage Capacity24 dia X 18 in long Scoop feed Grate discharge Will take the mine run of ore, crush grind and classify in a single pass WW Gibson Combination Elliptic Roll and Ball Mill ID: 24 dia X 18 in long Scoop feed; 5000 TPD Ore Processing and Recovery Plant Siemens 100 HP Electric MotorsWW Gibson Combination Elliptic Roll and Ball Mill Savona 2024年1月1日 Iron ore sintering is the iron ore powder agglomeration process that changes fine iron ore powder into the lumpy ironbearing raw material used for blast furnace Hot crushing is done by singleroll crusher Granulation of the cooled sinter cake will separate the product sinter, bedding material, and return ore based on their Iron Ore Sintering SpringerLink
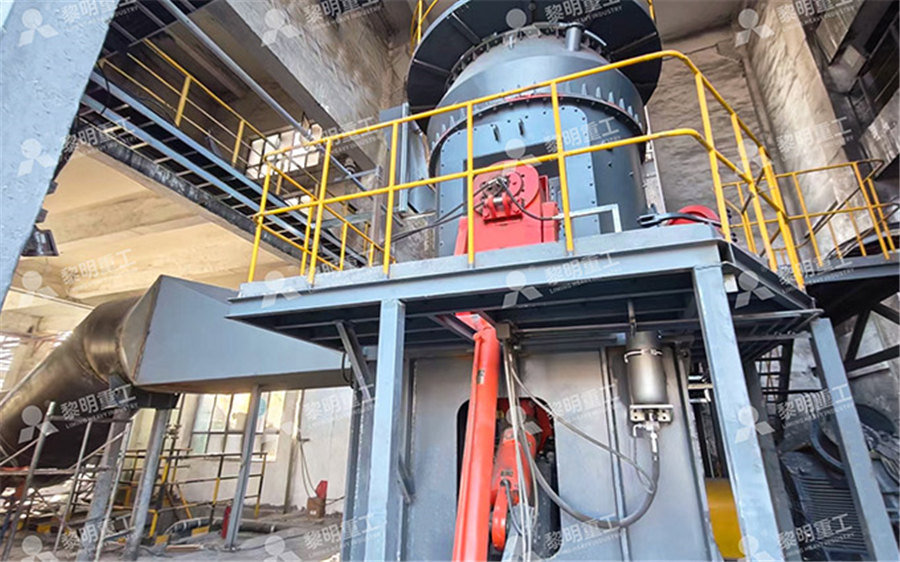
Sintering: A Step Between Mining Iron Ore and Steelmaking
2019年6月11日 World resources are estimated to be greater than 800 billion tons of crude ore containing more than 230 billion tons of iron The only source of primary iron is iron ore, but before all that iron ore can be turned into steel, it must go through the sintering process Sinter is the primary feed material for making iron and steel in a blast furnace2023年3月10日 sintered and whose grain size is below the minimum of 63 mm (sometimes 5 mm), and therefore, has to be resintered 3040 % of the total sinter mass flow is screened out as return fines at hot A Breakage Model for Discrete Element Simulations Applied to Iron Ore 2021年5月3日 Gold is extracted from gold ores According to the World Gold Council, approximately 190,000 tons of gold has been mined since 1950 The highquality ores have been gradually depleted since then [1]However, the demand for gold for industrial use has increased owing to the growing demand for electronic products, such as computers and smartphones [2], Utilizing gold mine tailings to produce sintered bricks2013年5月30日 Fig 4 Roll configurations in rolling mills Twohigh mill roll configuration – This is the most commonly used rolling mill configuration In this configuration, there are two horizontally mounted rolls The rolling mill motor Basics of Rolling and Rolling Mills – IspatGuru
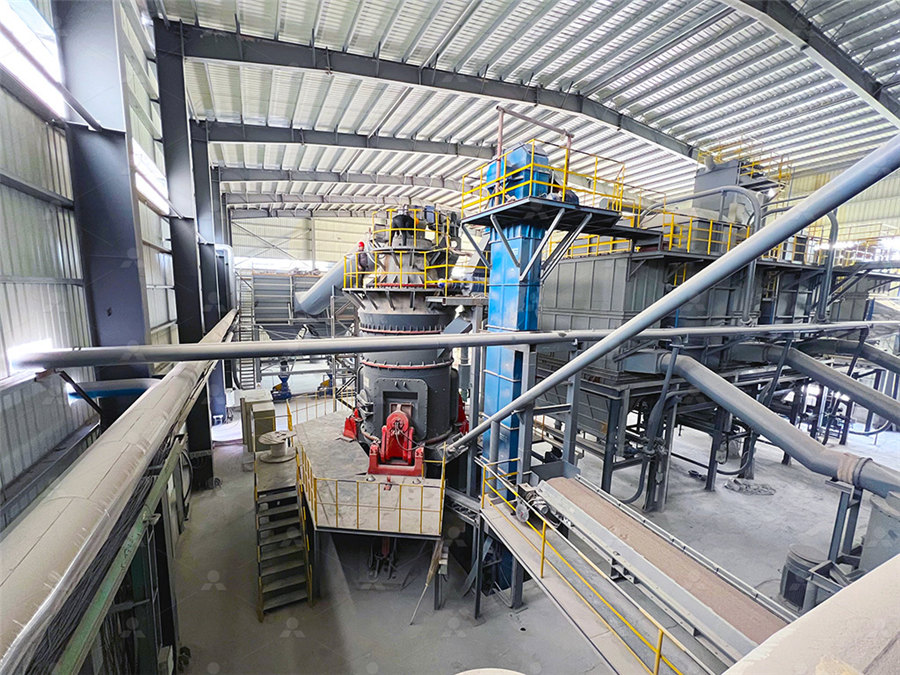
HPGR 911Metallurgist
2016年7月14日 HPGR test results published by Grier (1992) on gold ores from the Mt Todd project showed significant energy savings for a HPGR/Ball Mill circuit as compared to a SAG/Ball Mill plant By adding a Polycom high Variety of reliable mills based on UCMILL principle Singlestand Reversing Cold Mill A singlestand cold rolling mill is capable of producing 100,000 to 400,000 t/a depending on product mix Rolling schedules can be carried out with an even Advanced Reversing Cold Mills by Primetals Butech Bliss pioneered the “Tandem Piston” Roll Force Cylinder which paved the way for many single and multistand mill modernizations over the years This commitment to roll force cylinder design also makes us the perfect supplier for roll force cylinder test and repair servicesHot Cold Rolling Mill Equipment Manufacturer Mill Upgrades2021年9月8日 PDF Rolltoroll (R2R) Sintered CdTe Nanocrystal Photovoltaics The R2Rfriendly techniques were then combined into a single, integrated process, RollToRoll Friendly SolutionProcessing of Ultrathin, Sintered

Sinter plant Global Energy Monitor
A sinter plant is used to agglomerate iron ore to produce sinter, a product that can be used in a blast furnace[1] According to the US Environmental Protection Agency, the sintering process converts finesized raw materials, including iron ore, coke breeze, limestone, mill scale, and flue dust, into an agglomerated product, sinter, of suitable size for charging into the blast The sintered part is carefully cooled to room temperature while maintaining a controlled atmosphere in the last zone This prevents air ingress and oxidation, ensuring that the final part’s properties are preserved Carefully managing these zones can help achieve the desired mechanical and material characteristicsGuide to Sintered Metal Products Allied Sinterings, Inc12×30 Single Pair Mill RMS’s single pair mills are ideal for applications where a coarse grind consistency is required Typical micron targets for a single pair mill range from 3,000 to 1,200 micronsSingle Pair Mills RMS RollerGrinder2017年9月1日 Request PDF Fine grinding: How mill type affects particle shape characteristics and mineral liberation In minerals beneficiation applications, the main function of comminution circuits is to Fine grinding: How mill type affects particle shape ResearchGate