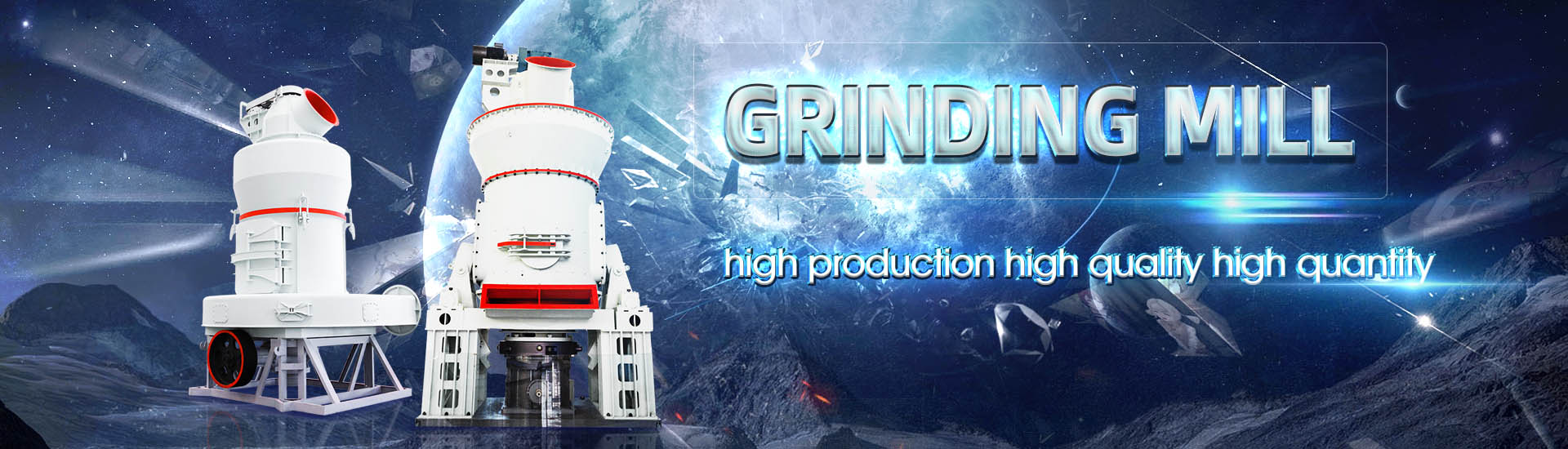
What is needed to open an ore powder making plant in Cangshan
.jpg)
Guidelines for mineral process plant development studies AusIMM
Guidelines for metallurgical testwork, process development, engineering and estimating requirements for each stage of precommitment studies are described together with those for the engineering phase The continuing rapid rise in metal prices has resulted in an unprecedented 2024年8月15日 A typical mineral processing plant is able to process various types of ores and mineral materials, including metal ores, nonmetallic ores, clay minerals, building materials and energy minerals Metallic ores: Gold ore, Mineral Processing Plants: What You Need to KnowThe first step in a mining operation typically involves removal of overburden to access the ore body for an openpit mine This overburden in then stockpiled either as waste rock or to be reused at closurePhysical Processing: Innovations in Mineral ProcessingIron Smelting: Iron smelting involves reducing iron ore, typically hematite or magnetite, in a furnace The high temperatures required (over 1500°C) posed significant challenges Early Guide to Modern Smelting Processes CED Engineering
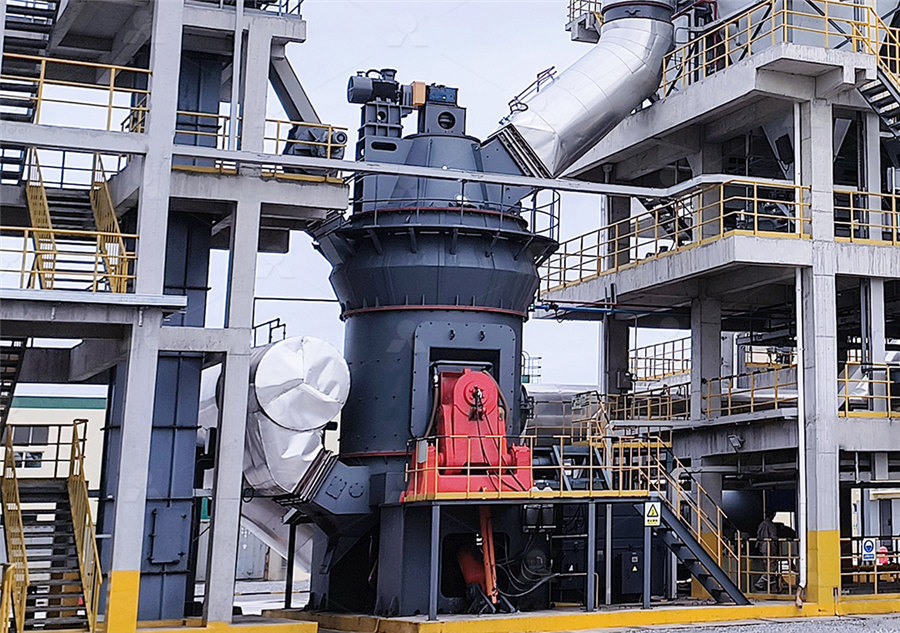
Iron Ore Pelletizing Process: An Overview IntechOpen
Ore particle shape, size, texture and capability of water retention, capillarity and cohesive strength among different particles determine the velocity of pellet growth during balling and pellet porosity Ore characteristics also influence on the 2017年10月17日 In the smelting reduction process, pelletized iron oxide ore or fine ore powders are prereduced in a fluidized bed or reduction shaft The reduced iron along with coal and lime is fed to a gasifiermelter, which From Ore to Iron with Smelting and Direct Iron The sinter plant turns iron ore into sinter, which is the optimal product for the blast furnace Sinter is made by burning a mix of iron ore powder, fluxes and recycled substances from the steel Raw materials Sinter plant ArcelorMittal2014年5月7日 Most manganese mining occurs in open pits Although there are processes in place to mine manganese nodules in the ocean floor, they cannot complete with landbased mining production Once the ore is mined, it’s Manganese Mining and Processing: Everything you
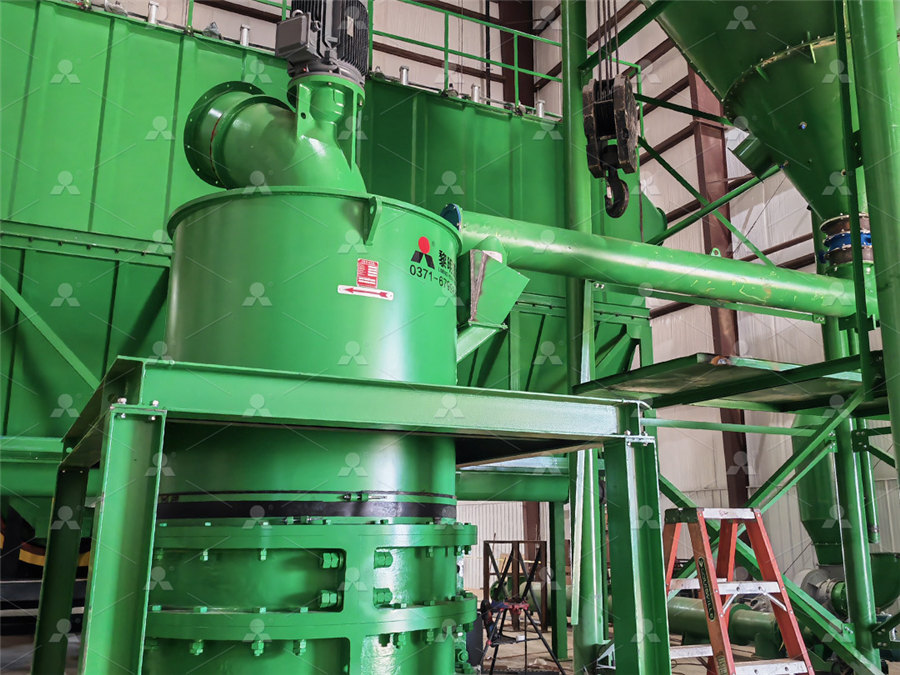
Lowcarbon production of iron and steel: Technology options,
2021年4月21日 From a technical perspective, the challenge of decarbonization involves two processes: chemical reduction for iron ore refining (process emission), commonly with The first step in the overall powder metallurgy (PM) process is making metal powders There are four main processes used in powder production: solidstate reduction, atomization, electrolysis, and chemical SolidState Reduction In Making Metal Powder MPIFKeywords: Mineral process plant, Metallurgical testwork, Engineering and cost studies, Feasibility studies This paper is part of a special issue on Metallurgical Plant Design and Operating Strategies Introduction The continuing rapid rise in metal prices has resulted in an unprecedented global increase in the number of mineral project developmentsGuidelines for mineral process plant development studies AusIMM2016年3月21日 w = weight of dry ore (grams) in one liter of pulp, K = the solids constant, Assume the specific gravity of the water in the pulp to be unity Formula (5) is used in making tabulations for mill use As used in these formulas the Common Basic Formulas for Mineral Processing
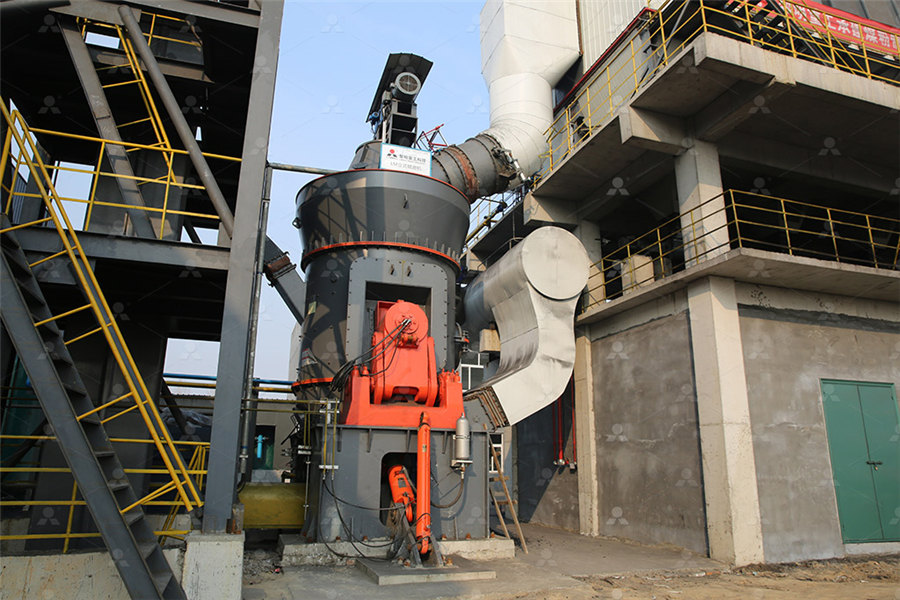
Iron Ore Pelletizing Process: An Overview
PDF On Jul 11, 2018, Sandra Lúcia de Moraes and others published Iron Ore Pelletizing Process: An Overview Find, read and cite all the research you need on ResearchGate2019年11月30日 The iron ore mine currently has an abundance of OFF grade ore stockpiles due to the prioritising of ON grade ore at the plant Stockpiling is included in the fiveyear and 12month rolling plans If the ore that is mined is more than what the plant can process, it is then sent to the stockpilesMine Planning and Optimisation Techniques Applied in an Iron Ore Our community came together to smelt twentyfive pounds of iron Every aspect of the smelt was a team effort, from collecting magnetite sand from a local beach, to building the bloomery furnaceHow to Smelt Iron: The 6 Steps to Iron Smelting The Crucible2016年3月30日 In book: Encyclopedia of Iron, Steel, and Their Alloys (pppp 10821108) Chapter: i) Direct Reduced Iron: Production; Publisher: CRC Press, Taylor and Francis Group, New York(PDF) i) Direct Reduced Iron: Production ResearchGate
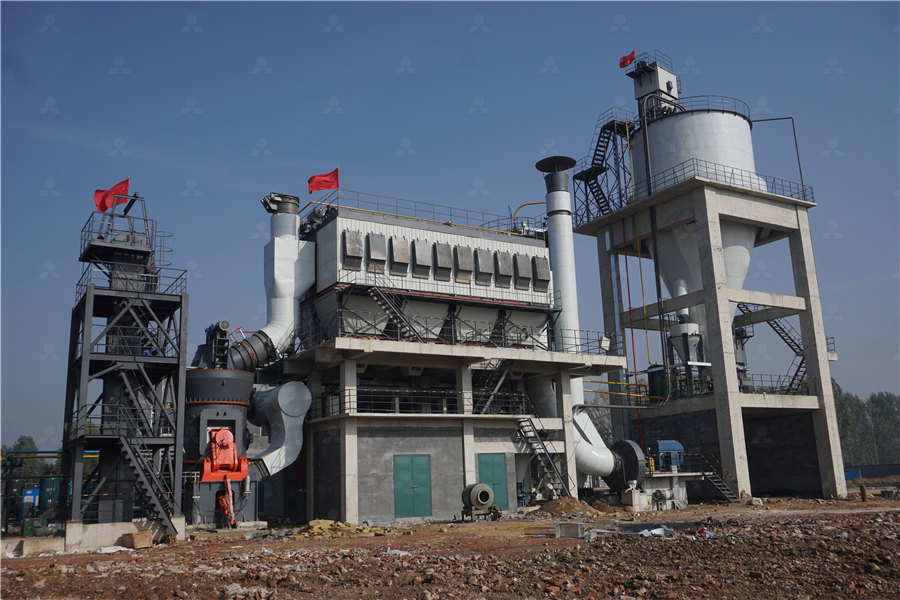
Copper Mining and Processing: Processing Copper Ores
Copper processing is a complicated process that begins with mining of the ore (less than 1% copper) and ends with sheets of 9999% pure copper called cathodes, which will ultimately be made into products for everyday useThe most common types of ore, copper oxide and copper sulfide, undergo two different processes, hydrometallurgy and pyrometallurgy, respectively, The sinter plant turns iron ore into sinter, which is the optimal product for the blast furnace Sinter is made by burning a mix of iron ore powder, fluxes and recycled substances from the steel plant to create an opengrained, consistent substance The sinter is then crushed, cooled and screened for dust Sometimes, iron ore is supplied in the form of iron ore pellets These need no further Raw materials Sinter plant ArcelorMittal2018年2月21日 About 80% of the worlds’ reserves for platinum group metals (PGMs) are in South Africa’s Bushveld Igneous Complex Processing of PGM involves comminution, flotation, smelting, converting, base metals refinery and precious metals refinery Due to increasing chrome content in the feed and the challenges associated with operating high chrome feed, alternative Extraction of Platinum Group Metals IntechOpen2015年3月15日 Understanding Sinter and Sinter Plant Operations satyendra; March 15, 2015; 8 Comments ; fluxes, Iron ore fines, SCFA, sinter, sinter plant basic sinter, sintering machine,; Understanding Sinter and Sinter Plant Operations Sintering is a process of agglomeration of fine mineral particles into a porous and lumpy mass by incipient fusion caused by heat produced Understanding Sinter and Sinter Plant Operations IspatGuru
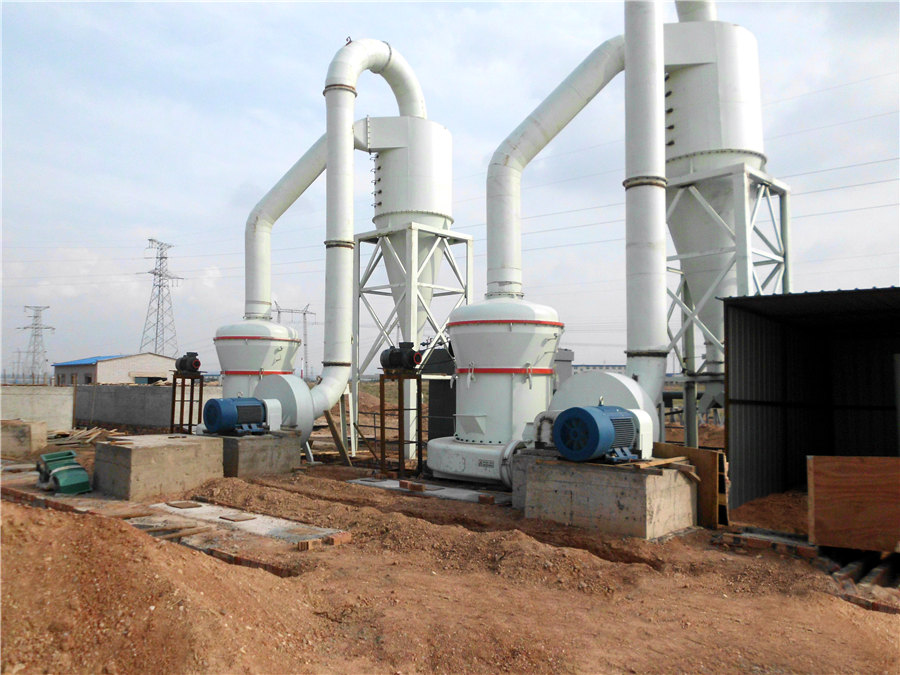
From Ore to Iron with Smelting and Direct Iron
2017年10月17日 Smelting Reduction Figure 2: The smelt reduction vessel (SRV) is the core technology component of the Hismelt process Source: RioTinto While years of ironmaking technology innovations have optimized blast The sinter plant turns iron ore into sinter, which is the optimal product for the blast furnace Sinter is made by burning a mix of iron ore powder, fluxes and recycled substances from the steel plant to create an opengrained, consistent substance The sinter is then crushed, cooled and screened for dust Sometimes, iron ore is supplied in the form of iron ore pellets These need no further Raw materials Sinter plant ArcelorMittalWhen most people think of the metalmaking process, they picture a stream of molten metal pouring into a mold it makes a nice visual for films and commercials But when you consider making parts with powder metal, it may How Metal Powder Is Made: Step 1 of the Powder When the ore is mined in forested areas, an average of 80 percent of the land is returned to its native ecosystem Production and reserves Tens of millions of metric tons of bauxite to reestablish the equivalent level of plant species richness in rehabilitated areas equal to the unmined Jarrah forest (A Jarrah forest is tall open forestBauxite 101 The Aluminum Association
.jpg)
Cement Manufacturing Process INFINITY FOR CEMENT EQUIPMENT
IF YOU NEED THIS GUIDE AND ALL OTHER USEFUL EXCEL SHEETS WHICH WILL MAKE YOU MASTER THE PRODUCTION , PROCESS , MAINTENANCE ACTIVITY IN YOUR CEMENT PLANT KINDLY CLICK HERE Raw Material Preparation and Raw Meal Design Part One: Raw Material Preparation General; The production of cement is started from quarrying Figure \(\PageIndex{2}\): Three Common Ores (left) Iron ore, (middle) Manganese ore – psilomelane, and (right) Lead ore – galena and anglesite Most metals are found as types of rock in the Earth's crust These ores contain sufficient minerals with important elements including metals that can be economically extracted from the rock232: Principles of Extractive Metallurgy Chemistry LibreTexts2024年4月26日 OpenPit Mining: Openpit mining is employed when the iron ore deposit is close to the surface or forms a large, easily accessible ore body In this method, largescale excavation machinery, such as excavators and haul trucks, is used to remove the overburden (surface material) and expose the ore depositIron Ore Processing: From Extraction to ManufacturingFrom its original home buried underground in a mine to its use in a finished product such as wire or pipe, copper passes through a number of stages When it is recycled it can pass through some over and over againFrom Ore to Finished Product Copper
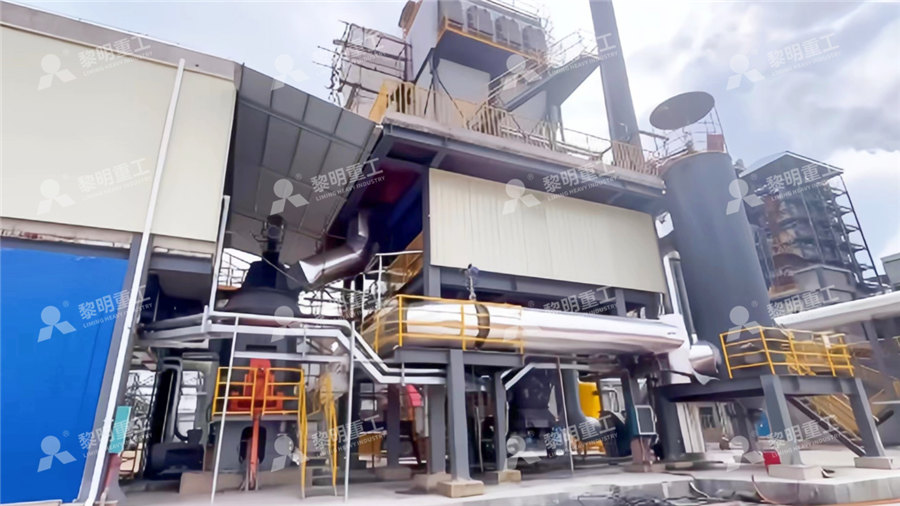
How Is Iron Ore Processed into Pellets? Sree Metaliks
2023年9月1日 Let’s understand more about these little but integral materials due to which steel making has reached its zenith What are Iron Ore Pellets? The term Pellet means a small, rounded substance Iron Ore Pellets are small balls of iron ores These Pellets use the powder that is derived from extracting ore as a raw materialRocks with large concentrations of minerals, are called ores Mining depends on finding good quality ore, preferably within a small area The next step is to get the rocks which contain the mineral out of the ground Once the ore is on the surface, the process of getting the mineral you want out of the rock can start251 Exploration: Finding minerals Mining of mineral resources2013年1月1日 For banded iron formationhosted deposits accurate boundary modelling is critical to oregrade estimation Key to estimation fidelity is the accurate separation of the different domains within the (PDF) Planning an Iron Ore Mine: From Exploration 2018年11月19日 PDF The aim of mineral processing is to get the mineral from rock or Ore that has good economic value in the market Generally, the ability of Find, read and cite all the research you need (PDF) Comminution in mineral processing
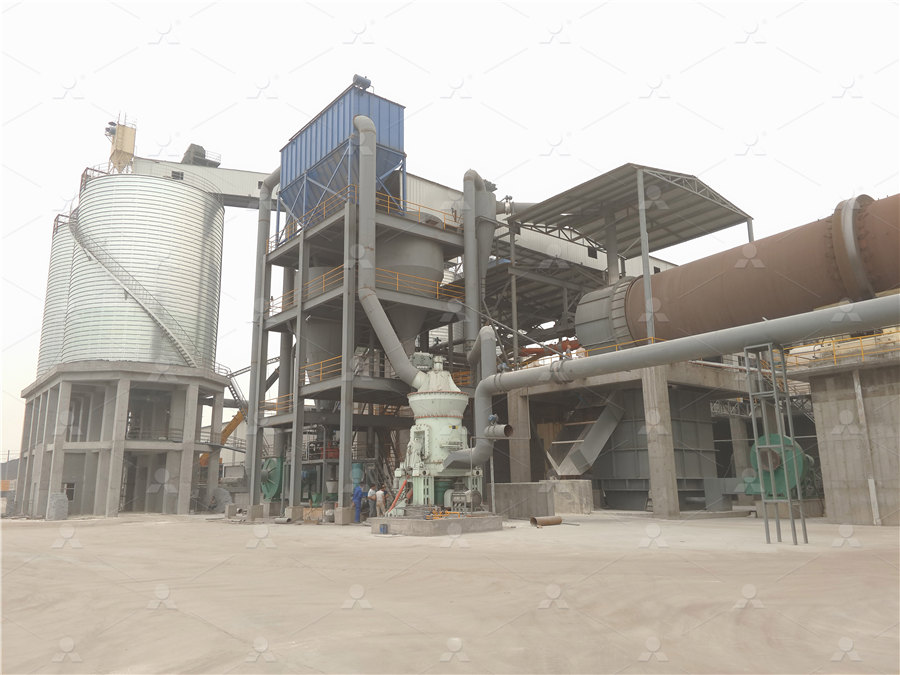
Iron ore beneficiation: an overview ScienceDirect
2023年1月1日 The iron ore industries of India are expected to bring new technologies to cater to the need of the increasing demand of quality ores for steel making This chapter briefly discusses the current scenario of the iron ore resources in India, iron ore mining methodology, beneficiation technique, and the current operating practices for achieving sustainable growth in the iron and ore pelletizing plant The idea of rolling moist fine ore in a drum to form balls and then drying and firing it was first patented by A G Andersson in Sweden in 1912 Further development was performed to bring the idea to reality In 1943, E W Davies and coworkers demonstrated the process using an experimental shaft furnaceIron Ore Pelletizing Process: An Overview IntechOpen2017年7月7日 Several different types of kilns are used for the calcination process These kilns can be rotary kilns or shaft kilns The type of the kiln to be selected strongly depend on the characteristics of the limestone, anticipated production rate, cost of fuel, investment costs, available fuel, local conditions, infrastructure and other thingsIts Processing and Application in Iron and Steel Industryfrom their naturally existing ores or mineral compounds It is a process conducted at elevated temperatures that utilizes heat and chemical reactions to convert raw materials into purified metal products The main goal of smelting is to segregate the targeted metal from impurities and other nonmetallic elements found in the oreGuide to Modern Smelting Processes CED Engineering
.jpg)
Copper Mining Processing: Everything You Need to Know
2014年7月17日 After the ore is crushed, it undergoes concentration This isn’t necessary for some types of ore, such as oxide ores, as crushing and grinding are enough to separate the waste rock from minerals However, concentration methods such as froth floatation separate the copper minerals from the waste rock for more tricky ores, such as sulfide oresOpen Cut/Pit A mine worked at and from the surface Also called surface mine Orebody A natural concentration of valuable minerals that can be economically extracted Ore Loss The loss of ore to the waste mining stream during blasting or mining Overburden Layers of soil and/or rock covering an orebody OverbreakBlasting PrinciplesSteelmaking process can generally be classified into four main different routes including blast furnace/basic oxygen furnace (BFBOF), direct reduction/electric arc furnace (DRIEAF), smelting reduction/basic oxygen furnace (SRBOF) and melting of scarp in electric arc furnace (EAF) Fig 1 shows the various steel production routes from the raw materials to the crude steel Steelmaking Process an overview ScienceDirect TopicsThis process helps to increase the surface area of the ore, making it more accessible for subsequent grinding Grinding, on the other hand, involves further reducing the size of the crushed ore into a fine powder The crushed ore is transferred to a grinding mill, which contains heavyduty steel balls or rodsGold Refinery Process: From Raw Material to Pure Gold
.jpg)
Ore National Geographic Society
2024年10月30日 Ore is a deposit in Earth’s crust of one or more valuable mineralsThe most valuable ore deposits contain metals crucial to industry and trade, like copper, gold, and iron Copper ore is mined for a variety of 2018年1月1日 Mining is a complex, expensive, yet lucrative business Today’s openpit mines are huge projects in Australia To keep the projects profitable, planners and schedulers are under constant OpenPit Mine Production Planning and 2024年1月7日 It’s like a metamorphosis, where the ore sheds its rough exterior to reveal the valuable tungsten inside The Transformation: The first step in this transformation is crushing and grinding the ore into a fine powder This How is Tungsten made: From Ore to HighTech MetalWhile each cement plant may differ in layout, equipment, and appearance, the general process of manufacturing portland cement is the same: crushed limestone and sand are mixed with ground clay, shale, iron ore, fly ash and alternative raw materialsHow Cement is Made Portland Cement Association
.jpg)
Application of deep learning in iron ore sintering process: a review
2024年3月16日 In the wake of the era of big data, the techniques of deep learning have become an essential research direction in the machine learning field and are beginning to be applied in the steel industry The sintering process is an extremely complex industrial scene As the main process of the blast furnace ironmaking industry, it has great economic value and 2017年10月6日 RelatedStart Soap Making Business 2 Formula of Washing Powder The manufacturing of detergent powder is not so complicated and involves mixing of different ingredients in the right proportions Each detergent making company has its own customized formula that can be crafted keeping in mind your target marketHow to Start a Detergent/Washing Powder Business2010年6月30日 Wet beneficiation of minerals necessarily requires removal of large amounts of water—typically contaminated—before further processing of the concentrated ores can be carried outDewatering and Drying in Mineral Processing Industry: Potential for 2018年6月1日 Topics include powder manufacturing processes, sphericity, chemistry and measurement technologies, as well as considerations in relation to heats, lots and batches As such, it is hoped that this review will allow for a clearer understanding of powder properties and reduce confusion among endusersAn introduction to metal powders for Additive Manufacturing
.jpg)
How Electric Car Batteries Are Made: From Mining To Driving
2019年1月24日 Materials Within A Battery Cell In general, a battery cell is made up of an anode, cathode, separator and electrolyte which are packaged into an aluminium case The positive anode tends to be made up of graphite which is then coated in copper foil giving the distinctive reddishbrown color The negative cathode has sometimes used aluminium in the 2024年3月17日 Steel making is a sophisticated process that turns iron ore into steel, involving methods like the Blast Furnace and Electric Arc Furnace to produce various grades of steel The industry emphasizes sustainability by using additives and recycled materials while ensuring quality through rigorous testing for diverse applicationsA Visual Guide: Steel Making Process Chart Cabaro Group