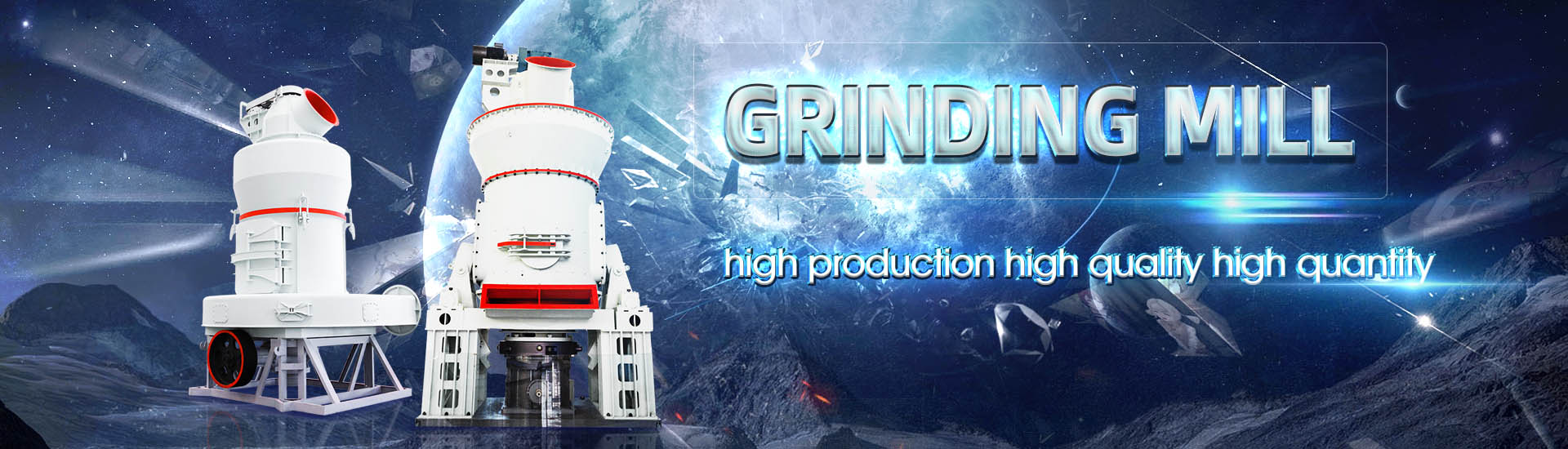
Grinding roller maintenance plan
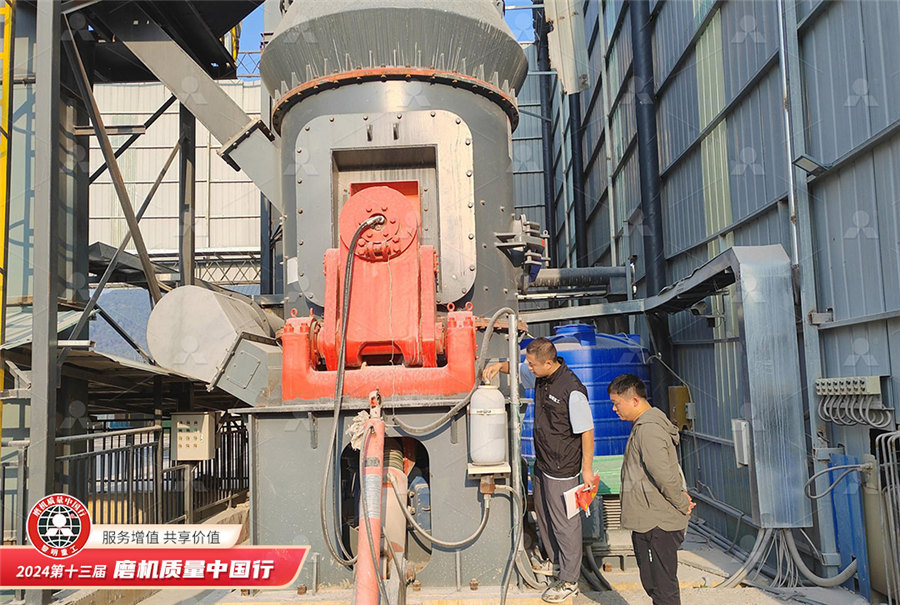
Grinder Preventative Maintenance Checklist GCH Tool
2024年1月24日 Preventative maintenance is crucial to avoid expensive repairs and possible safety hazards A welldesigned checklist should cover all aspects of a grinder’s maintenance, including preoperation checks, best practices during This document provides a list of tasks that are recommended to be completed on a daily and weekly basis to ensure the proper maintenance and performance of a Haas mill can be MILL WEEKLY MAINTENANCE CHECKLIST Haas Automation IncRoller mill maintenance can be broken down into three general areas; rolls, bearings, and drives Maintenance requirements may vary from application to application but are most directly linked CPM Roller Mill MaintenRoller mills are a very flexible piece of equipment as they can perform a variety of tasks, be it crumbling pellets, cracking, flaking grain or grinding They can also handle many different Managing Mill Maintenance Roller Mill Maintenance PDF Mill
.jpg)
How To Maintain A Rolling Mill American Steel
Proper maintenance of electrical and control systems helps ensure safe and reliable operation of the rolling mill Implement Preventive Maintenance Schedule: To streamline the maintenance process and ensure consistency, develop a 2017年12月19日 With the grinding mill critical to a plant’s throughput, it pays to ensure mills receive the necessary care and maintenance Too often mill maintenance is reactive, occurring due to a breakdown The result is higher Mill maintenance – 3 simple ways to keep your mill at a) Check wear and lubrication conditions of grinding rollers b) Check fastening conditions of wear parts on the plate c) Check wear conditions of rollers, disc, liners and other internal parts of Maintenance of vertical roller millRoll Maintenance Factors to consider which affect roll sharpness: Rolls should be fed uniformly to maximize machine efficiency Rolls being out of parallel will increase roll wear Your facility should have a program in place to regularly Roll Maintenance Grain Mill Manuals
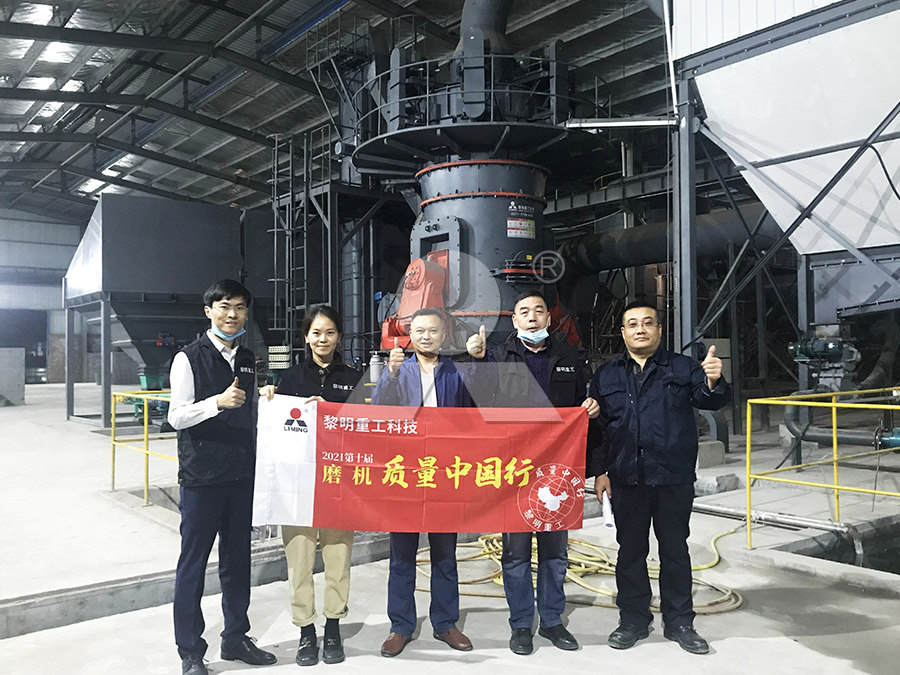
Daily use and maintenance of the grinding mill
2018年6月11日 Guilin Hengda is a professional grinding mill manufacturer, today brings you the standard operation and daily maintenance of the mill, hoping to solve your confusion (1) 1 Grinding roller Grinding rollers (usually 2–4) are the heart of the vertical mill, distributed on the grinding table Grinding rollers apply pressure to the material on the grinding table They are usually made of materials such as cast steel, alloy Energysaving and Efficient Vertical Roller Mill Fote 2021年12月29日 ② Regular maintenance: repair and replace the wearing parts of the grinding roller and grinding ring in a certain period of time Regularly check whether the screws on the main parts of the machine are loose, as well as the Maintenance of superfine grinding millmaintenance plan Presale service Sales service Aftersales service Tip1: The specific time arrangement depends on the actual situation Grinding roller Grinding roller is the part that grinds the material Generally, 3–6 grinding Highefficient Raymond Mill Fote Machinery
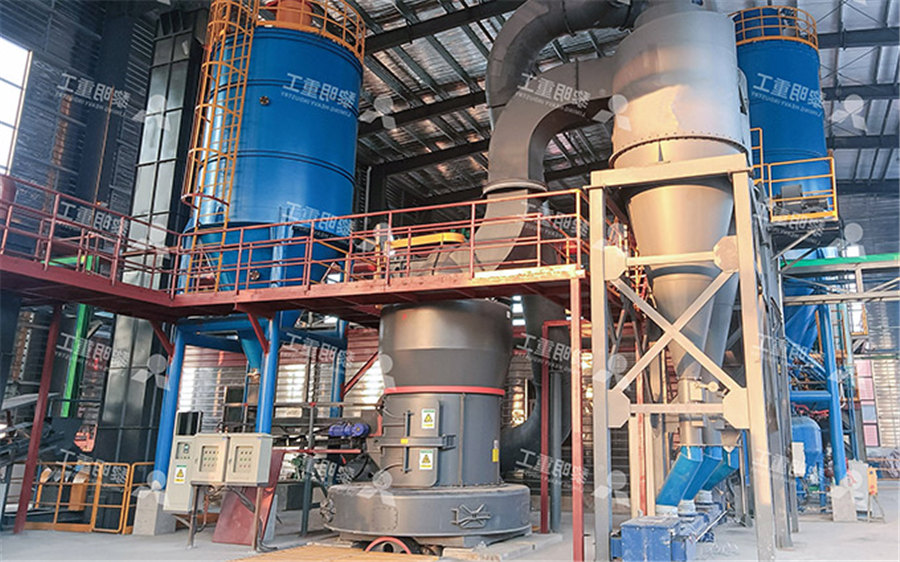
Roller Shutter Maintenance Keep Your Shutters in Top Shape
Schedule professional roller shutter maintenance: While there are maintenance tasks you can do yourself, it’s important to schedule regular professional maintenance for your roller shutters A trained technician can perform a thorough inspection, identify any potential issues, and provide expert servicing to keep your shutters in optimal conditionRoutine maintenance makes the difference 1 Put together a detailed maintenance plan 2 Record all information and activities in a log 3 Be proactive with maintenance – it always pays off 4 Kiln issues can be complex When it comes to major repairs, it’s good to get a second opinion 5Rotary Kiln Maintenance – Get the most out of your equipmentRoller presses grind thousands of tons of material, day after day, all year round Unsurprisingly, this causes progressive wear, especially of the roller surfaces In abnormal circumstances, it can also result in more significant damage to the roller itself The Roller Press Scanner detects both Current status is then automatically reported against historical data for a detailed insight into Roller Press Scanner KHD Humboldt WedagPrevious Post Next Post Contents1 KILN ALIGNMENT ROLLER GRINDING2 1 Hot kiln alignment using electronic devices21 11 Advantages of this Technique22 12 Tools and Instruments Used23 13 Measurement Procedures Using Total Station24 14 General Notes3 2 Grinding of rollers tyres31 21 Grinding Method32 22 Grinding Machine33 23 KILN ALIGNMENT ROLLER GRINDING INFINITY FOR CEMENT EQUIPMENT

High Pressure Grinding Roller (HPGR) LEE JUN
3000mm: 14002200 mm: 43007200 t/h: ≤75 mm: 2x35502x6300 kW * The above technical parameters are obtained by taking the iron ore (true density of 33 t/m³, and medium hardness) as an example, only for reference for model selection The specific selection parameters shall be based on the experimental data, and will be provided after design of the process planThe document provides installation and operation instructions for the HRM1700M Vertical Roller Coal Mill It describes the mill's technical parameters, components, structure, working principles, and installation process Key aspects include grinding rollers that can be removed for maintenance, a hydraulic system that controls grinding pressure, and a separator that Operation Manual: HRM1700M Vertical Roller Coal Mill2023年6月22日 This article describes the critical parameters and basic maintenance items for these common size reduction machines Fundamentals of hammermill grinding A typical hammermill, as shown in Figure 1, consists of a rotor enclosed in a cylindrical grinding chamber that is encircled by screensHammermill and roll crusher maintenance and operation2024年4月11日 Learn how to address common issues and implement an effective conveyor maintenance plan Routine conveyor maintenance is import Learn how to address common issues and implement an effective conveyor The Basics of Conveyor Maintenance Limble CMMS
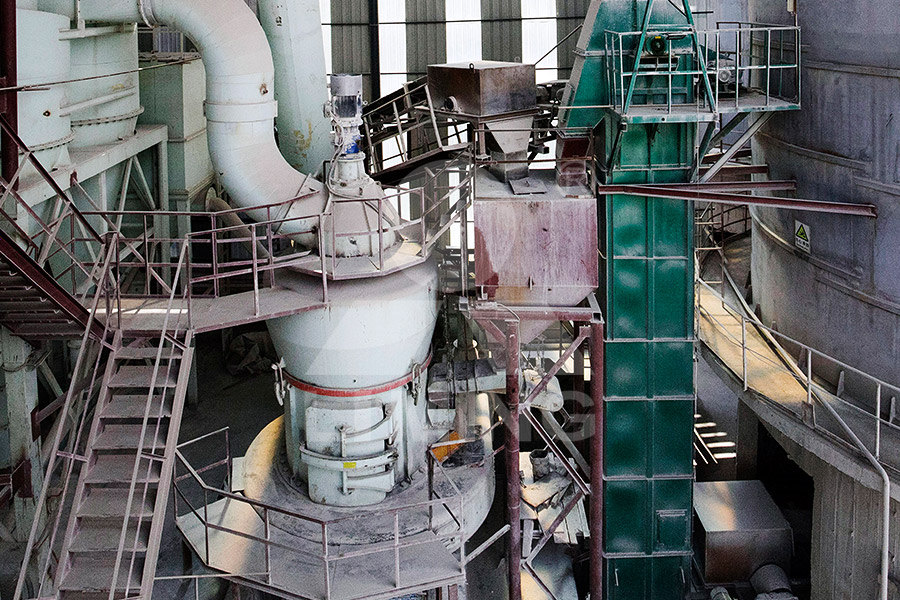
Roller Mill Springer
R Roller Mill Xiao Xiao1, Huang Lilong2 and Xu Kuangdi3 1Changsha Research Institute of Mining and Metallurgy, Changsha, China 2Changsha Research Institute of Mining and Metallurgy, Changsha, China 3Chinese Academy of Engineering, Beijing, China Roller mill is a type of grinding equipment for crushing materials by pressure between two orWhile occasionally overlooked, roller balancing can be an important part of scheduled roller maintenance Depending on the machinery speed and exacting tolerances required, whenever recovering or repairing rollers, balancing of Industrial Roller Balancing Services Offered by The 2018年1月1日 PDF Operational experiences with High Pressure Grinding Rolls (HPGR) have shown that the rollers do not wear at the same rate This differential wear Find, read and cite all the research (PDF) Roller life extension of high pressure grinding rolls with During the operation of the vertical roller mill product, the contact surface is subjected to multiple grinding and grinding, which will cause the overall product quality of the vertical roller mill to be damaged The timely maintenance and protection of the vertical roller mill plays a key role in prolonging the life of the vertical roller millHow to maintain and protect the vertical roller mill
.jpg)
Construction, Working and Maintenance of Crushers for Crushing
1 Construction, Working and Maintenance of Crushers for Crushing Bulk Materials practicalmaintenance Construction, Working and Maintenance of Crushers for Crushing Bulk Materials By K P Shah : kpshah123[at]gmail (Please replace [at] with @) Committed to improve the Quality of Lifedirect contact with the rollers This reduces the wear of the grinding tools in comparison to conventional grinding methods such as ball or SAG mills Additionally, all the material passes through the relatively small but highly intensive grinding zone between the two rollers, leaving no grinding volume unused in contrast to ball millsHighPressure Grinding Roller Presses for Minerals ProcessingThe process of hardfacing grinding roller is complex, and the manufacturing time is long During the manufacturing process, it requires multiple surfacing, and the welding wire consumption and maintenance costs are high Ceramic Grinding Roller This kind of grinding roller mainly adopts metal matrix composite ceramicsVertical Roller Mill Grinding Roller AGICO Cement PlantThe grinding rollers’ quality directly affects the finished cement’s fineness and the stability of the grinding mills It wears as the vertical grinding mill’s longtime operation Generally speaking, the lifetime of a grinding roller is about 500 hours This number decreases when the grinding materials have higher hardnessGrinding Roller For Vertical Roller Mill High Strength, Long
.jpg)
AusIMM – Leading the way for people in resources
%PDF16 %âãÏÓ 4215 0 obj > endobj 4235 0 obj >/Encrypt 4216 0 R/Filter/FlateDecode/ID[87C03FABF6FB2246BC4F9AB649B4B217>]/Index[4215 26]/Info 4214 0 R/Length 101 2020年11月3日 The customer agreed to a threeyear preventative maintenance plan: Downtimes decreased to 22 hours in 2018, none in 2019 and eight in the first five months of 2020 Preventive maintenance is an inspection that covers parts and processes – a thorough quality control that ensures uptime and efficiency and extends the life of the machineWhat Preventative Maintenance of Grinding Machines Can mills for drygrinding the abovementioned grinding stock Loesche has developed and built the largest and most efficient grinding plants for its customers Loesche plants are specifically planned for the required process steps and equipped with the associated techno logy This technology comprises: • Processing plants and material storagePROCESS OPTIMISATION FOR LOESCHE GRINDING PLANTSraw material grinding, a modular vertical roller mill with 5 m table diameter and 4 rollers was added The existing kiln systems were partly modernized, one kiln system was replaced by new system Grinding Process Optimization Featuring Case Studies and
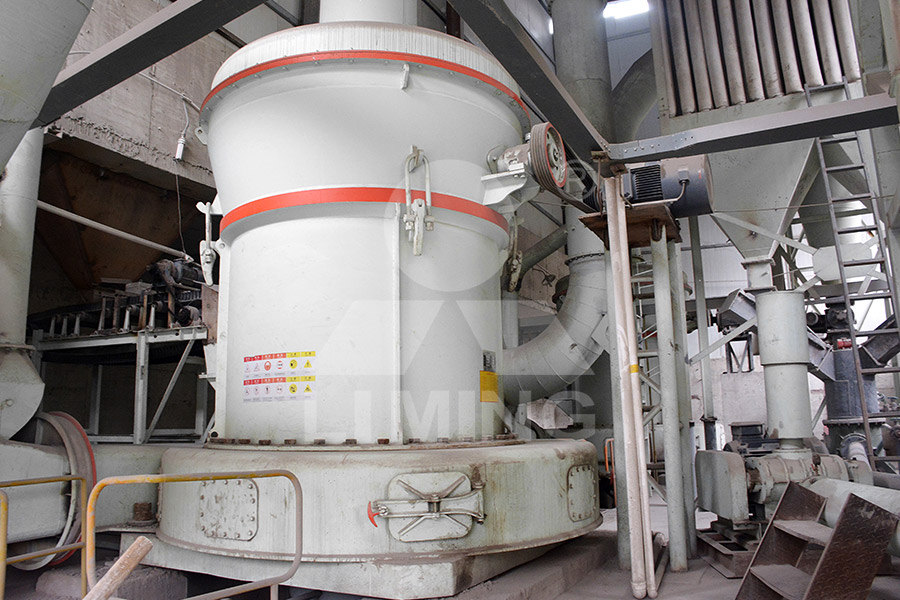
Enduron® High Pressure Grinding Rolls (HPGR) Weir
With low energy consumption, low maintenance requirements, excellent throughput capacity and high availability, Enduron® high pressure grinding rolls (HPGR) are a proven way to improve the efficiency of mineral grinding circuits and industrial mineral applications Setting the benchmark for energy efficient grinding, they use dynamic skewing to provide bestinclass size reduction Hannecard Roller Coatings, Inc 1031 Lambert Street, Barberton 44203 Ohio USA +1 3307538458 ohio@hannecardPrecision roller grinding Hannecard Rollercoatings2017年6月19日 As a worldwide leader in grinding solutions for the cement industry and understanding the changing needs of cement producers and how to tailor solutions to meet those needs Optimizing output, improving efficiency, and reducing CO2 emissions while keeping investment costs to a minimum are common challenges that the modular vertical roller mill Grinding process optimization IEEE Xploregrinding using standard bond grinding calculations based on population balance models is successfully applied [4, 38] Various grinding laws, energy relationships, control factors and controller design for cement grinding are discussed in [37] Figure1 Vertical roller mill for cement grinding [13] VRM shown in Figure1 uses hydraulically hardPROCESS CONTROL FOR CEMENT GRINDING IN VERTICAL ROLLER
.jpg)
BALL MILL MAINTENANCE The Cement Institute
2024年10月28日 The Ball Mill Maintenance course is designed to engage in the effective use of handson learning methodology as a unique combination of theory and practical work section applied to the ball mill system’s maintenance inspection Major components like the grinding tool, grinding roller, and grinding ring are prone to wear• Maintenancefree grinding device • CE conformity Technical data Motor rating 009 kW Supply voltage 230 V, 50/60 Hz, 1 phase Grinding roller speed 800 RPM Weight without drive 28 kg Product details 4 Flat equalizing/grinding Graf Service carding and nonwovenService Carding and NonwovenHannecard Roller Coatings, Inc 1031 Lambert Street, Barberton 44203 Ohio USA +1 3307538458 ohio@hannecardRoller maintenance repair Hannecard RollercoatingsGrinding urethane rollers is not an easy task, Plan Tech has build custom one off machines capable of performing such precision We use special grinding wheels and also a custom blend of special coolants that we use while grinding Grinding Urethane Rollers – Grinding Polyurethane
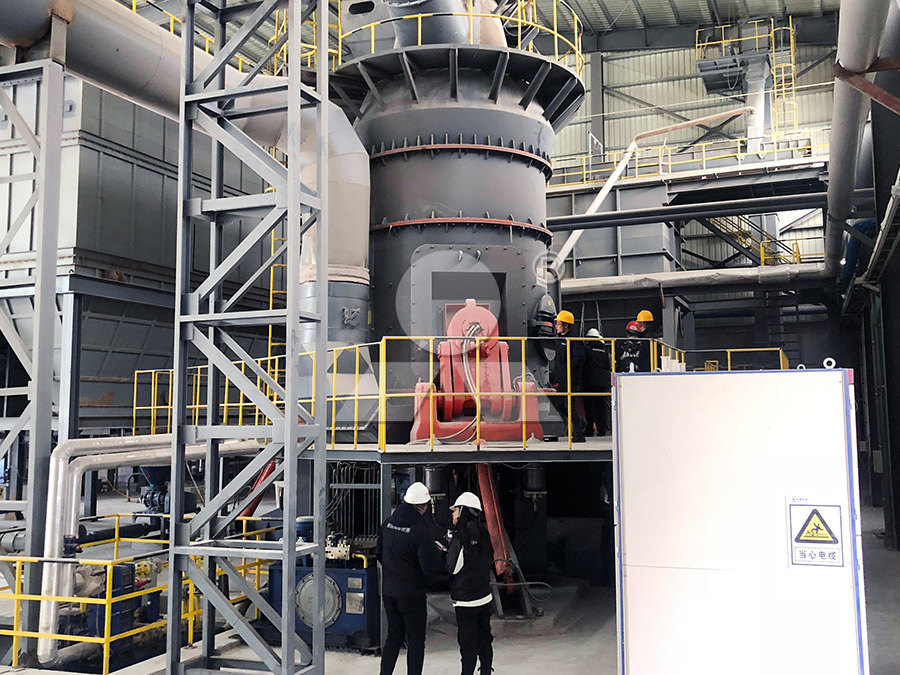
Roller Mill SpringerLink
2023年7月4日 The combination forms of the grinding roller and the grinding table include tapered rollerflat type, tapered rollerbowl type, drum rollerbowl type, The vertical roller mill has the advantages of low energy consumption, high output, easy maintenance, etc, and has been widely applied in cement, steel and power industry, The specially designed honeycomb structure enables the grinding curve of the grinding roller and lining plate to maintain a sufficient grinding area, reducing the mills power consumption by about 7% Ceramic Grinding Rollers VS Hardfacing Grinding Rollers Ceramic Grinding Roller Hardfacing Grinding Roller 1 set of ≈ 3X Hardfacing Cost MaintenanceCeramic Grinding Roller Qiming Casting13 Develop a maintenance plan The Importance of Regular Maintenance Regular maintenance is crucial for preventing common conveyor problems and ensuring the efficiency and longevity of the system By implementing routine maintenance tasks and identifying potential problems early on, you can save time and money in the long run Key TakeawaysTroubleshooting Conveyors: Maintenance and Repair GuideCite this article: LI Yongqiang Application and Maintenance of Grinding Roller Lubrication System of ATOX Roller Mill[J] Cement Technology, 2021, 1(2): 3740Application and Maintenance of Grinding Roller Lubrication
.jpg)
BALL MILLS Ball mill optimisation Holzinger Consulting
and cement Roller presses are used mainly in combination with a ball mill for cement grinding applications and as finished product grinding units, as well as raw ingredient grinding equipment in mineral applications This paper will focus on the ball mill grinding process, its tools and optimisation possibilities (see Figure 1) The ball millRoller Mill Maintenance Mark Heimann Roskamp Champion 2975 Airline Circle Waterloo, Iowa USA 50703 Tel 319 232 8444 Fax 319 236 0481 sales@cpmroskamp crumbling pellets, cracking corn, dry rolling and steam flaking grain, and grinding corn, wheat, or milo for mash and pelleted feeds While each application has some unique aspects, CPM Roller Mill MaintenVertical roller mills became increasingly dominant for grinding raw materials mainly for the cement industry due to their high energy efficiency and excellent drying capacity With the experience gained from repairs worldwide, Castolin Eutectic has developed its own specialized Vertical Roller Mill program Preventive maintenance on VRMs can extend the lifetime by as much as 100%, Vertical Roller Mill Repair: Enduring Performance PDF Mill grinding using standard bond grinding calculations based on population balance models is successfully applied [4, 38] Various grinding laws, energy relationships, control factors and controller design for cement grinding are discussed in [37] Figure1 Vertical roller mill for cement grinding [13] VRM shown in Figure1 uses hydraulically hardPROCESS CONTROL FOR CEMENT GRINDING IN VERTICAL ROLLER
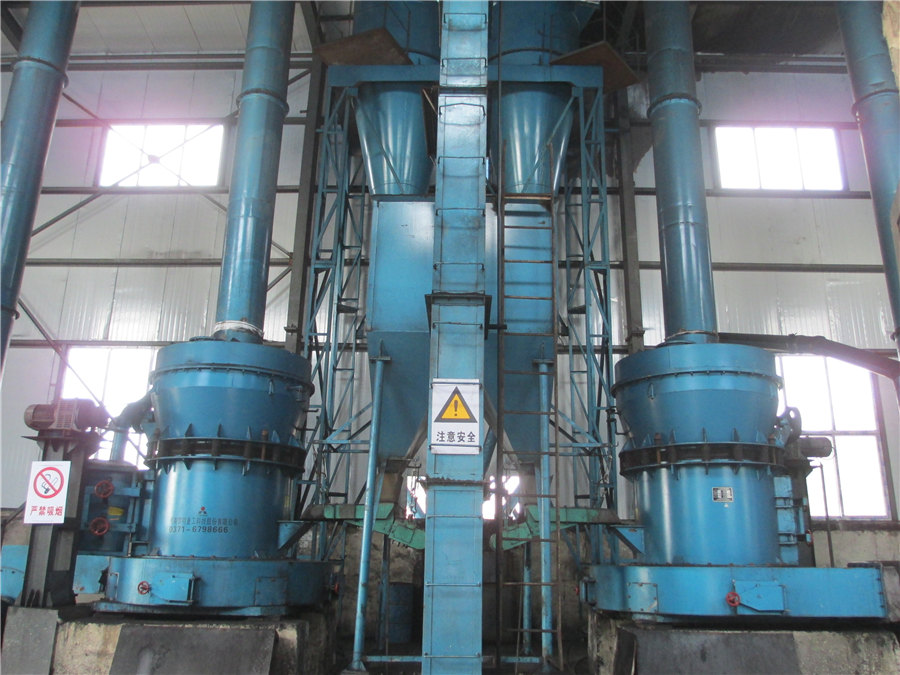
Grinding Grooving Services Pinnacle Roller
©2016 Pinnacle Roller Co 2147 Spring Grove Ave Cincinnati, OH 45214 Telephone: 5133694830 Fax: 5132413361