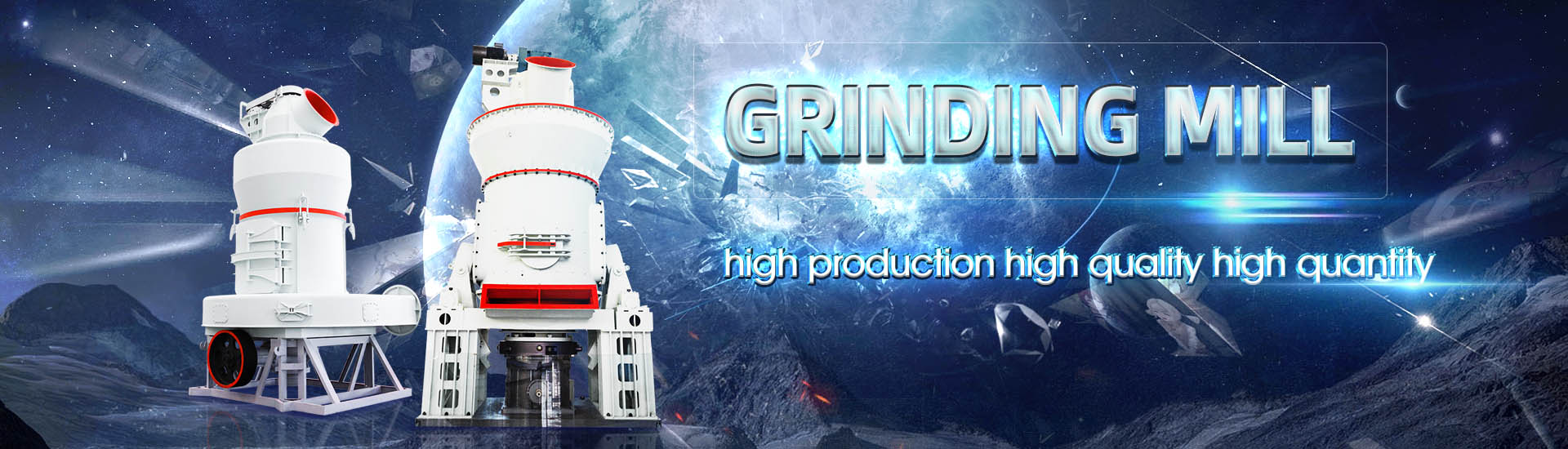
Chain talc grinder, air swept drying raw material grinding mill
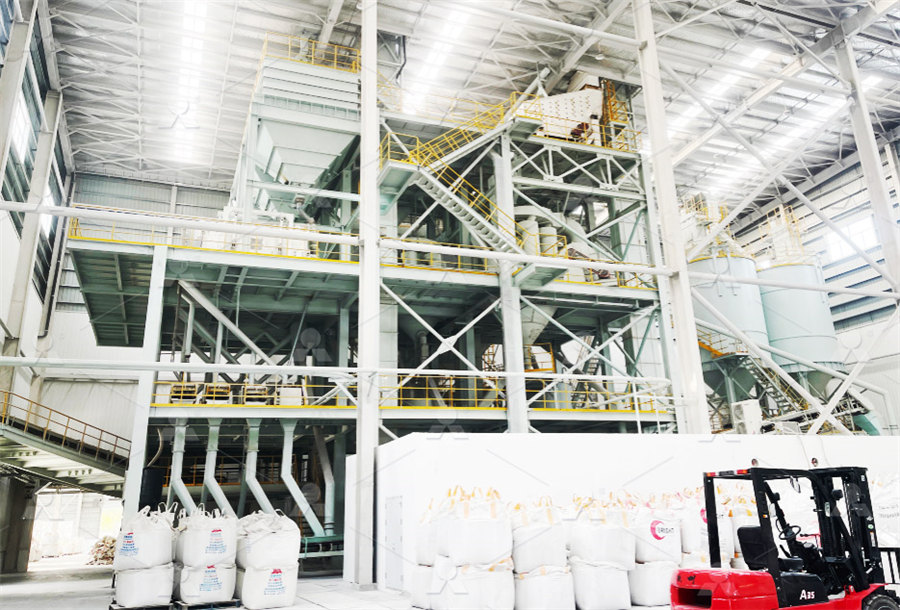
Raw Material DryingGrinding Cement Plant Optimization
Ball mills for cement raw material and coal equipped with a drying compartment adequately air swept with hot gas (2535M/sec above the ball charge), can handle moisture about 8% Fully 2015年4月1日 In this study, production capacity of a fully airswept dry grinding raw meal ball mill circuit was evaluated by modelling the mill using the perfect mixing modelling approach Optimization of a fully airswept dry grinding cement raw meal 2018年2月21日 For high moisture content of the raw material, the airswept dryinggrinding circuit as shown in Fig 412 is used The raw material is fed into a predrying duct outside the mill for primary drying, so that only predried Drying of raw materials INFINITY FOR CEMENT These mills are used to grind very moist materials that need to be dried using lowtemperature air If the relevant explosionprotection equipment is used, airswept mills are optimally suited for Industrial Solutions polysius ball mills ThyssenKrupp
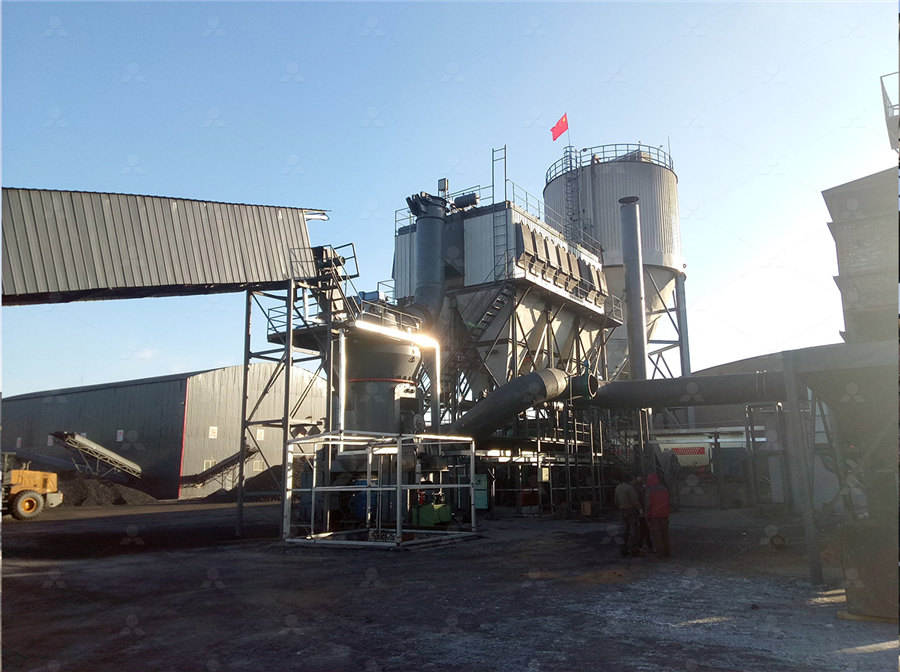
Modeling and simulation of a fully air swept ball mill in a raw
2005年2月20日 This paper is concerned with the model of a fully air swept ball mill operating in a raw material grinding circuit For simplicity, the approach assumes that different components in efficient grinding plants for its customers Loesche plants are specifically planned for the required process steps and equipped with the associated techno logy This technology comprises: • PROCESS OPTIMISATION FOR LOESCHE GRINDING PLANTSslag in roller grinding mills (vertical airswept grinding mills) is a technology introduced by Loesche The first use of a Loesche mill, with a grinding track diameter of only 11 metres, was used as 2 µm 5 µm Loesche2015年4月1日 Production capacity of a fully airswept industrial scale twocompartment KHD Humboldt Wedag® cement ball mill was optimized with the aid of simulation It was proposed Optimization of a fully airswept dry grinding cement raw meal
.jpg)
Energy and cement quality optimization of a cement grinding circuit
2018年7月1日 This study aimed at optimizing both the energy efficiency and the quality of the end product by modifying the existing flowsheet of the cement grinding circuit As a general Rieco's air swept mills are versatile and efficient machines for grinding a wide range of materials Contact us today to learn more! Industries Carbon Black; Rieco's Air Swept Mill Acts as an air seal and aids in discharging material Air Swept Mills Rieco2005年2月20日 DOI: 101016/JPOWTEC200411009 Corpus ID: ; Modeling and simulation of a fully air swept ball mill in a raw material grinding circuit @article{Benzer2005ModelingAS, title={Modeling and simulation of a fully air swept ball mill in a raw material grinding circuit}, author={Hakan Benzer}, journal={Powder Technology}, Modeling and simulation of a fully air swept ball mill in a raw 2005年2月20日 1 IntroductionGrinding is a highcost operation consuming approximately 60% of the total electrical energy expenditure in a typical cement plant and 40% of this energy is for raw material grinding [1] In recent years, considerable steps have been taken to improve comminution efficiency both in the development of machines with the ability to enhance energy Modeling and simulation of a fully air swept ball mill in a raw
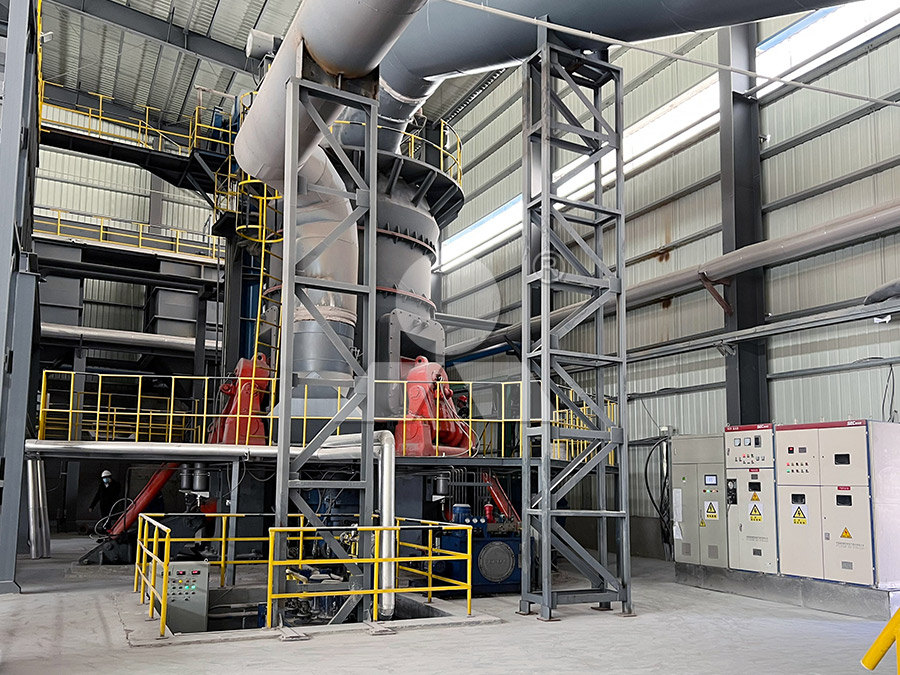
Drying of raw materials INFINITY FOR CEMENT EQUIPMENT
For high moisture content of the raw material, the airswept dryinggrinding circuit as shown in Fig 412 is used The raw material is fed into a predrying duct outside the mill for primary drying, so that only predried material enters the mill Only a small portion of the hot gases enter the mill to perform secondary drying2015年4月1日 Request PDF Optimization of a fully airswept dry grinding cement raw meal ball mill closed circuit capacity with the aid of simulation Production capacity of a fully airswept industrial Optimization of a fully airswept dry grinding cement raw meal 2015年4月9日 Some of the characteristics and requirements to be considered when selecting a grinding mill are given below Material properties – The choice of mill type is primarily dependent upon the properties of the material which is to be ground by it It is vitally important to match the mill and material characteristics properlyGrinding Mills and Their Types – IspatGuruAdvantages of air swept coal mill The feeding device of the airswept coal mill adopts a louvertype structure with oblique air intake, which enhances the heat exchange capacity of the mill and can effectively prevent material blocking at the entrance of the coal mill; optimize the support system, improve the lubrication structure, and reduce system resistanceAir Swept Coal Mill Cement Plant Machinery
.jpg)
Talc Ultra Fine Powder Grinding Mill
2021年8月13日 Then use the cone crusher to crush the talc again until it can enter the fineness of the mill’s feed material (15mm50mm) 2 Grinding stage: The conveying and feeding system sends the small pieces of talc that meet the grinding conditions to the mill’s grinding chamber2017年6月9日 Electrical energy consumed was 274 kilowatthours per ton of raw feed Attrition Grinding of Talc (fig 25) The raw material, which contained only 105 percent minus 2 years investigated comminution of anthracite to determine the finest anthracite particle that could be produced by dry grinding in an airswept ball millAttrition Grinding Mill Design 911MetallurgistThe feeder (A) deposits raw material into the base of the Roller Mill (B) at a rate determined by pressure variations with the grinding mill Plows located ahead of each roller direct the material upward and between the grinding rolls and the Industrial Roller Mills Williams CrusherWhat Is Air Swept Coal Mill The airswept coal mill is also called a coal grinder It is the main equipment of the cement plant, used for drying and pulverizing coal powderIt mainly consists of the feeding device, main bearing, rotary part, Air Swept Coal Mill Coal Mill In Cement Plant
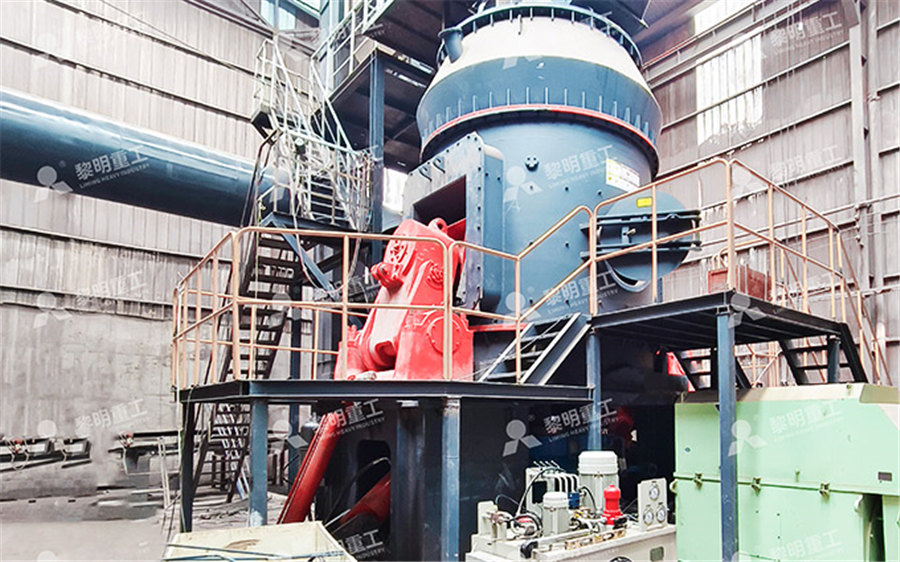
Raw Material Preparation in Cement Manufacturing
Vertical mill is a kind of air swept mill, which integrates drying, grinding and product classification It has the characteristics of less system equipment, simple process, low cost, low power consumption and low noise Beyond that, 2024年2月23日 The operation of the cement raw mill is a critical step in cement production By grinding the raw materials into a fine powder, these powders can be more easily mixed with other cement ingredients and burn more evenly during the cement clinker process Therefore, the efficient operation of the cement raw mill directly impacts the production efficiency and quality How Does a Raw Mill Work in a Cement Industry2017年5月25日 In “wet” grinding the material to be ground is fed to the mill in the form of a “pulp” containing, perhaps, 50% by weight of water In dry grinding, however, the granular material is fed into the mill in a sensibly dry condition; the only moisture present being the few percent normally held by the powderAir Swept Mill 911Metallurgist2016年11月7日 The rod mill, however, differs in principle in that the grinding bodies are rods instead of spheres whilst a pebble mill is a ball mill in which the grinding bodies are of natural stone or of ceramic material The types of mill normally encountered can further be classified according to the method of feeding the raw material to, and the removal Grinding Mills Common Types 911Metallurgist
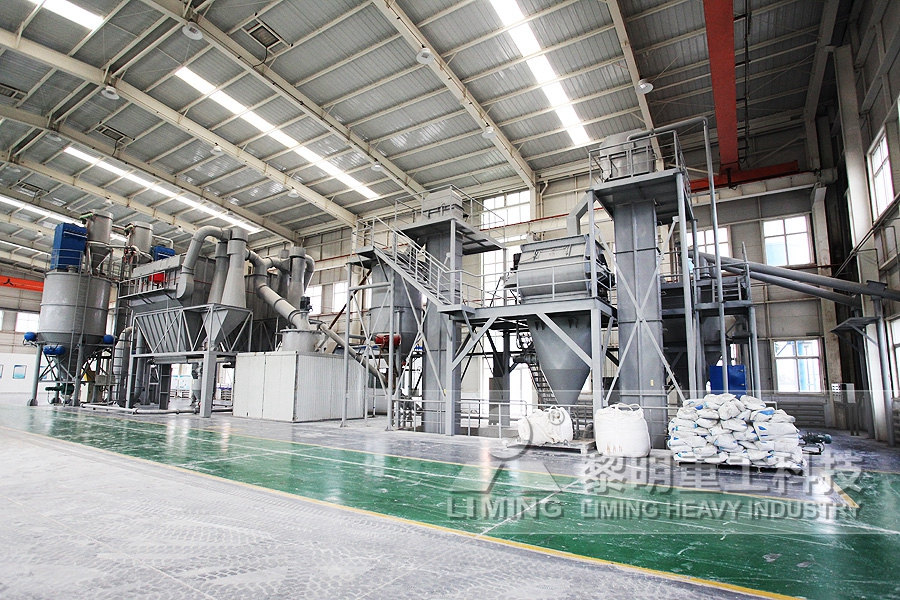
Limestone Powder Ultrafine Vertical Roller Mill
Limestone Powder Ultrafine Vertical Roller Mill Modle : CLUM Series Finished Size: 4003000 mesh Processing Ability: 3 – 45t/h Max Feeding Size: 10 mm M 1 Set Price: $ Range Of Application: Limestone, Calcium Carbonate, Talc, AGICO Cement Vertical Mill AGICO Cement Ball Mill Cement Vertical Mill Grinding System Cement vertical mill, also called roller mill, is another raw mill commonly used in cement pared with the cement ball mill, it has a great difference in structure, grinding principle, process layout, automatic control, and energy consumption, which play an important role in the Raw Mill – Raw Mill In Cement Plant AGICO Cement Raw MillThe ball mill is a traditional coal pulverizer machine, which has been widely used since it was invented In the cement plant, the new dry process cement manufacturing requires the moisture content of coal powder to be 05% ~ 15%, while that of raw coal is 15% ~ 40%Coal Mill in Cement Plant Vertical Roller Mill AirSwept Ball MillFinal grain size: 1 µm 500 µm Rotational speed: 12,000 rpm 18,000 rpm Output: 5 kg/h The Universal Laboratory Mill (FNG00) is the smallest crushers of the FNG range Manufactured in the mass and built steel stainless 316L welded mechanic, it is intended for the small installations of grinding in laboratory Powder mill, Powder grinding mill All industrial manufacturers
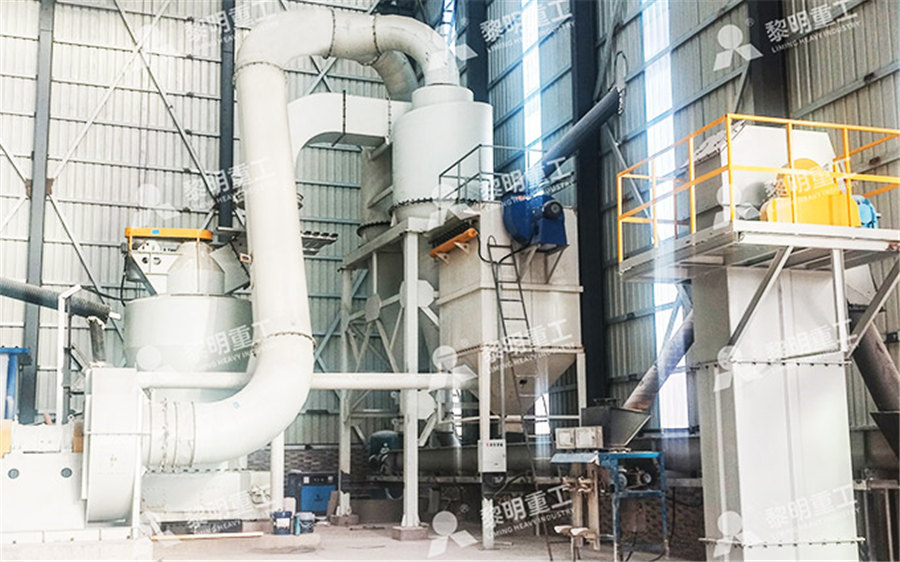
Performance analysis, modelling and simulation of dry
2008年6月1日 In this study, performance evaluation, modelling and simulation of airswept coal ball mill grinding circuit is presented Ball mill in the circuit was modelled based on the Whiten's (1972 2015年4月1日 Airswept raw meal ball mills introduced by the cement mill manufacturers FLSmidth ® (Smidth, 2002), Polysius ® (Polysius, 2002) and KHD Humboldt Wedag® are the most commonly used ones KHD Humboldt Wedag® manufactured fully airswept raw meal mills which have two compartments used for drying and grinding processesOptimization of a fully airswept dry grinding cement raw meal vertical roller mill Application process Raw material process Background In the vertical roller mill which is widely used in the raw material grinding process, raw materials input grinding table are crushed and pulverized on it and transported to separator by kiln exit gas introduced into the mill as drying, transporting and separating purposeVertical roller mill for raw Application p rocess materialsRaw mill is generally called cement raw mill, raw mill in cement plant, it refers to a common type of cement equipment in the cement plantIn the cement manufacturing process, raw mill in cement plant grind cement raw materials into the raw mix, and the raw mix is sent to the cement kiln to make cement clinker, next, clinker and other admixtures will be ground into finished cement by Raw mill Cement Plant
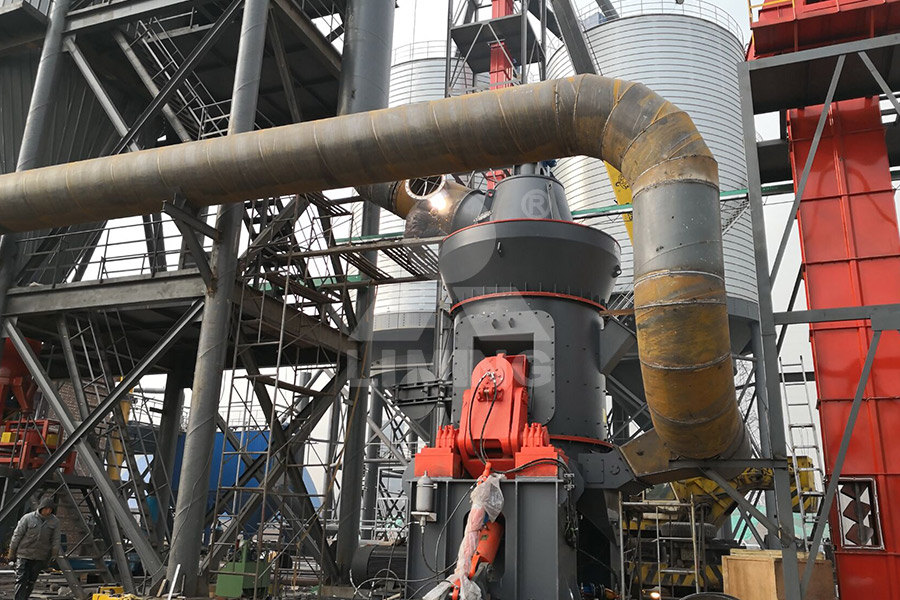
Energy and cement quality optimization of a cement grinding circuit
2018年7月1日 Among the industries, the nonmetallic industry was reported as the third largest energy user and accounted for about 12% of the global energy use [1]Within this portion, cement industry had the majority of the utilization with 85–12% [1], [2]US Energy Information Administration (EIA) [7] named cement industry as the most energy intensive among the Ball mill is one of the most variable and effective grinding machines which is mainly applied for further grinding the crushed materials Compared with other grinding mills, the variety of grinding modes, available grinding tool materials, and flexible production capacity make ball mill grinders the perfect match for a vast range of applications, such as cement industry, new building Ball Mill Grinder Ball Grinding Mill For Sale Different Ball Mill 1996年3月1日 The grate discharge mill could hardly produce such a fine material because the fine particles coated the grinding media and the lining of the mill The internal classification in the airswept Ultrafine grinding in an airswept ball mill circuit ResearchGateThe raw material will be fed into the feeding device of the coal mill by the feeder And at the same time, the hot air with a temperature of 300℃ enters the feeding device through the airline The lifting blade lifts the raw material and the raw material will Air Swept Coal Mill Cement Plant Equipment Coal Grinding Mill
.jpg)
(PDF) Grinding in an air classifier mill Academia
The fine particles leave the mill together with the main air through the classifier, while the coarse material is rejected and transported by the internal circulation back to the grinding zone Starting from the air flow visualisation measurements by Particle Image Velocimetry (PIV), the influence of the operating conditions on the flow pattern within the mill is described4 The process chain at a glance xCrushing: crushers break up the raw material delivered from the quarry and provide the raw mill with the feed size range it requires Crushers xRaw material analysis:the POLAB® CNA online analyser provides the first data regarding the chemical contents and/or homogeneity of the raw materialRaw material preparation From the quarry to raw mealDRYING: For processes that utilize high moisture feed materials, the conveying air stream can be heated for fluid bed drying of ground material Hot air is introduced into the grinding zone of the mill to fluidize and dry ground particles for easier flow through the airswept systemAirswept Roller Mills Bradley Pulverizer CompanyFinal grain size: 74 µm 400 µm Rotational speed: 21 rpm Output: 16 t/h 50 t/h Ball mill is common used grinding plant in the industry, and it is key equipment used for milling after materials are crushed This machine can be can grind all kinds of ores and other materials, which is widely used Mill, Grinding mill All industrial manufacturers
.jpg)
Everything you need to know about cement Materials
In the subsequent period, ball mills known as “airswept tube mill” and “tube mill with bucket elevators” were developed to carry out both drying and grinding of moist materials They worked in closecircuit, the object of which was to Drying and grinding are generally being done in either air swept ball mill or a vertical mill The selection of mill system will depend mostly on the factors like initial capital cost, drying and grinding capacity required, cost of energy (power) etc Coal Fineness: It is understood generally that the finer we grind, the easy it is for burningCoal Grinding Cement Plant OptimizationGrinding of cement raw material – material separation in cyclones The cement raw material mixtures are ground, dried, and classified in the Pfeiffer vertical roller mill For drying the material, hot gases are directed into the mill Product fineness can be Raw mills for all requirements Gebr PfeifferOperating in the medium to fine particle size reduction range the Air Classifier Mill delivers guaranteed, accurate particle size +44 (0)1928 Suitable for combined grinding and drying; Size reduction of the raw material happens effortlessly as the materials impact against the grinding rotor and fixed liner at high speed and ACM Air Classifier Mill Hosokawa Micron Ltd
.jpg)
Air Classifying Mill ACM Air Classifier Mill Manufacturer Rieco
Rieco is a trusted manufacturer of Air Classifying Mill ACM, specializing in highquality air classifier mill solutions Our ACM mills are designed for precise and efficient grinding, offering excellent particle size reduction capabilities Contact us for topnotch air classifier mill equipment and reliable powder processing solutionscement mills with a drying chamber see raw mills Mill working conditions: ventilation air speed through the mill Bigger or smaller than 12 [m/s] Material abrasivity The [%] of slag or pouzzolana content on the fresh mill feed for cement grinding The [%] of free silica at mill feed for raw material grinding Moisture content of the mill Everything you need to know about clinker/cement GrindingThe Raymond Roller Mill is an airswept vertical ringroll mill with an integral Raymond Roller Mills are available with grinding ring diameters ranging from 30120 in / 7603050mm These sizes are capable of producing a wide range of product fineness from a wide variety of material Typical material processed Clay, Fire Clay Raymond Roller Mill airswept vertical ringrollGambar 2 Raw Grinding Mill TINJAUAN TENTANG RAW GRINDING MILL bagian Raw Grinding Mill Roller mill secara umum tersusun dari shell, kerangka utama, stand, table, roller arm, gear reducer, rollerpressing unit dan separator Secara umum detail dari bagianbagian Raw Grinding Mill diberikan dibawah ini : PENAMBANGANANALISIS EFISIENSI RAW GRIDING MILL PADA PROSES