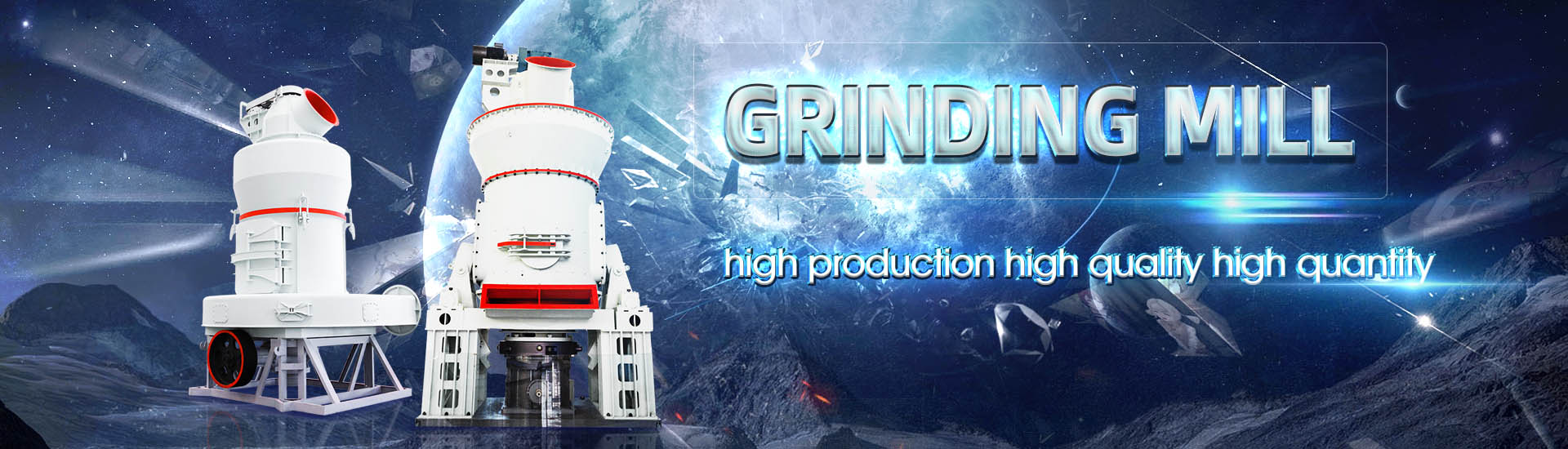
HOME→The importance of coal mill to vertical mill The importance of coal mill to vertical mill The importance of coal mill to vertical mill
The importance of coal mill to vertical mill The importance of coal mill to vertical mill The importance of coal mill to vertical mill
.jpg)
Performance optimisation of vertical spindle coal pulverisers
The effect of low calorific value coal was observed on mill’s response to match the boiler energy requirements Evaluation of the current operating pulveriser data enabled the determination of 2020年8月12日 This study shows the performance of a currently running vertical roller coal mill (VRM) in an existing coalfired power plant In a power plant, the coal mill is the critical An investigation of performance characteristics and energetic Mills are mechanical devices used to break different types of solid materials in small pieces by grinding, crushing or cutting In pulverised coalfired power plants, a pulveriser coal mill grinds Coal Mill an overview ScienceDirect TopicsThe layout of the coal mill with a rotary classifier This study shows the performance of a currently running vertical roller coal mill (VRM) in an existing coalfired power plant In aThe layout of the coal mill with a rotary classifier
.jpg)
Nonlinear coal mill modeling and its application to model
2013年3月1日 Coal mills play an important role in the overall dynamic response of coal fired power plants and there is significant potential to improve the load ramp rates of coal fired 2015年11月1日 A dynamic model of coal mill is developed, which can authentically replicate the milling operations from startup to shutdown With real time applications in mind, a composite A unified thermomechanical model for coal mill operationCoal mill is an important component of the thermal power plant It is used to grind and dry the moisturized raw coal and transport the pulverized coal – air mixture to the boiler Poor dynamic (PDF) Modeling and Control of Coal Mill Academia2013年3月1日 In these plants, pulverized coal is not stored, which makes the operation with vertical spindle mills – having very limited internal pulverized fuel storage – a just in time task Nonlinear coal mill modeling and its application to model
.jpg)
An investigation of performance characteristics and energetic
This study shows the performance of a currently running vertical roller coal mill (VRM) in an existing coalfired power plant In a power plant, the coal mill is the critical equipment,Vertical Coal Mill (VCM) is equipment for grinding and pulverizing coal into micron size Rotary kilns then use the powders as fuel burnersThe layout of the coal mill with a rotary classifierAs a leading innovator with power station technologies – and other industries that need to process coal, Magotteaux is the ideal firm to turn to when seeking cuttingedge vertical coal mill technologyOur tires and tables mean that vertical coal mills can run more efficiently than ever beforeIn many cases, there is a compromise that needs to be made between the length of Vertical Coal Mill Magotteaux137 designing alternative coal mill separators Additional plates were used to control the coal particle flow in the mill classifier system; therefore, an increase in theNUMERICAL AND EXPERIMENTAL INVESTIGATION OF A PULVERIZED COAL MILL
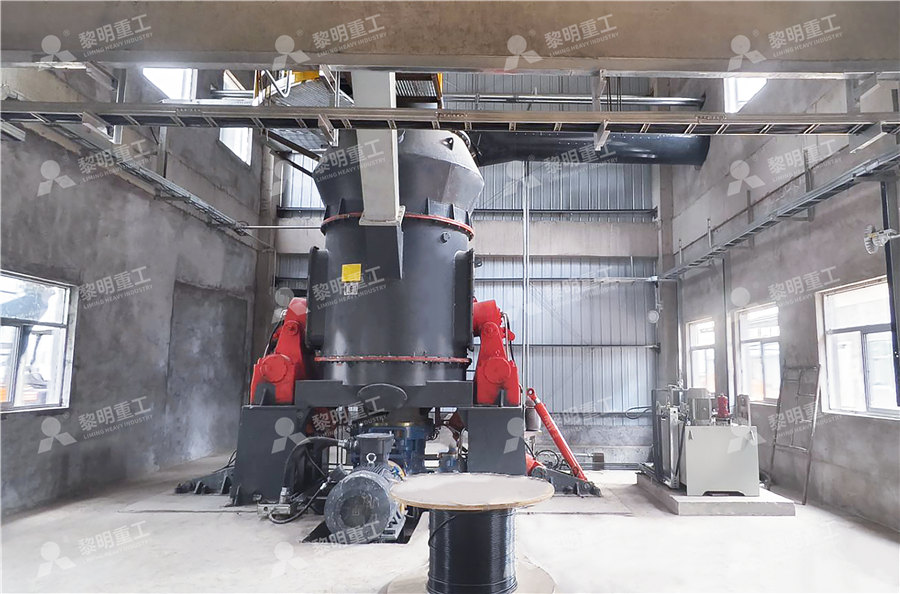
Coal Pulverizer – Power Plant Pall Corporation
Further pulverization of coal is achieved as the smaller coal particles are ground through attrition against each other and the grinding face Vertical Roller Mills This mill uses hydraulically loaded vertical rollers resembling large tires to pulverize raw coal fed down onto a rotating table: pradeebhamit@gmail, npappa@rediffmail , vasanthi@annauniv Abstract: The paper presents development and validation of coal mill model (including the action of classifier) to be used for improved coal mill control The model is developed by using the mass and heat balance equations of the coal mill(PDF) Modeling and Control of Coal Mill Academia2021年1月1日 Grinding Mill Vertical Roller Mill or Ball Mill: The reclaimed raw mix fed to Raw Mills, for drying and fine grinding of Raw meal for kiln feed: 4: Coal Grinding: Grinding Mill Vertical Roller Mill or Ball Mill: Coal is ground in Coal mill, which is a fuel for use in Kiln firing: 5: Pyro Section, Clikerization: In line calciner six stage Review on vertical roller mill in cement industry its The MPS mill also grinds, dries, calcines, and classifies gypsum without any problem, all in a single machine, for any fineness requested and considering individual requirements The MPS vertical roller mill built to last, reliable and energyefficient is the optimum solution when it comes to performing several process steps in one unitCoal mill, gypsum mill, clay mill, etc Pfeiffer MPS mills
.jpg)
Technical specifications of vertical roller coal mill
Vertical Coal Mill (VCM) is equipment for grinding and pulverizing coal into micron size Rotary kilns then use the powders as fuel burners The VCM has a housing section equipped with a lining 2016年1月18日 Next, the paper estimates the coal outlet mass flow of the coal mill by using extended Kalman filter (EKF), and the result is compared with the coal flow instruction Finally, we take the estimation of coal outlet mass flow as the new controlled variable and use inferential predictive control method to solve the coal mill control problemsThe Inferential predictive control method of coal mill IEEE Since the first application using an MPS mill to process pulverized coal in Germany in the mid 1960s, there have been over 2,000 different MPS mill installations operating in coalfired power plants worldwide As one of the most popular coal pulverizers in the utility industry, the MPS mill was first introduced into the US in the early 1970sCoal Pulverizer Design Upgrades to Meet the Demands of Low Coal and Electricity Generation Worldwide In 2019, coal comprised 27% of the world’s primary energy consumption and 364% of the all electricity generated in the world 7 See figure below Alleviating Energy Poverty – Coal Is Part of the Coal's Importance to the World Society for Mining,
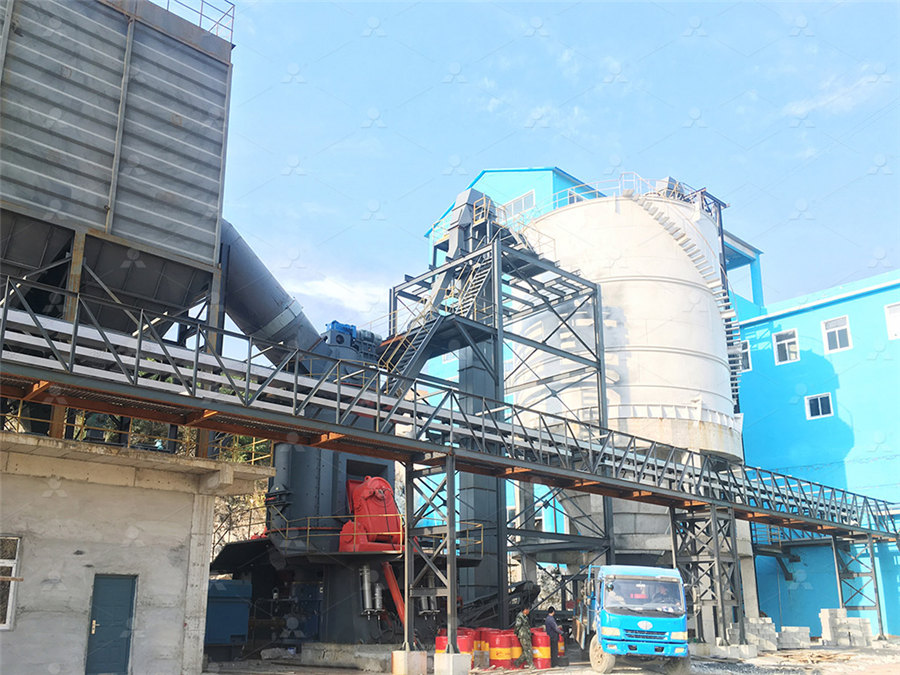
vertical roller mill, vertical coal mill, vertical slag mill, superfine
Vertical roller mills are mainly engaged in three major fields of slag, coal powder, and nonmetallic ore Divided into: vertical roller mill, vertical slag mill, vertical coal mill, and ultrafine vertical mill2016年9月1日 Furthermore, VRM separator speed (rpm) is one of the key operational parameters that determines product particle size Increasing the classi er rotor speed from 60 to 80 rpm decreases the particle Operational parameters affecting the vertical roller mill 2022年11月1日 Vertical Coal Mill (VCM) is equipment for grinding and pulverizing coal into micron size Rotary kilns then use the powders as fuel burners The VCM has a housing section equipped with a lining WEAR ANALYSIS OF VERTICAL COAL MILL PLATE ResearchGate2020年4月7日 The main task of a coal mill system is to prov ide qualified fuel for the pulverized coal boiler In As early as in 1998, a n improved dynamic model of vertical spindle roll Modeling of Coal Mill System Used for Fault Simulation
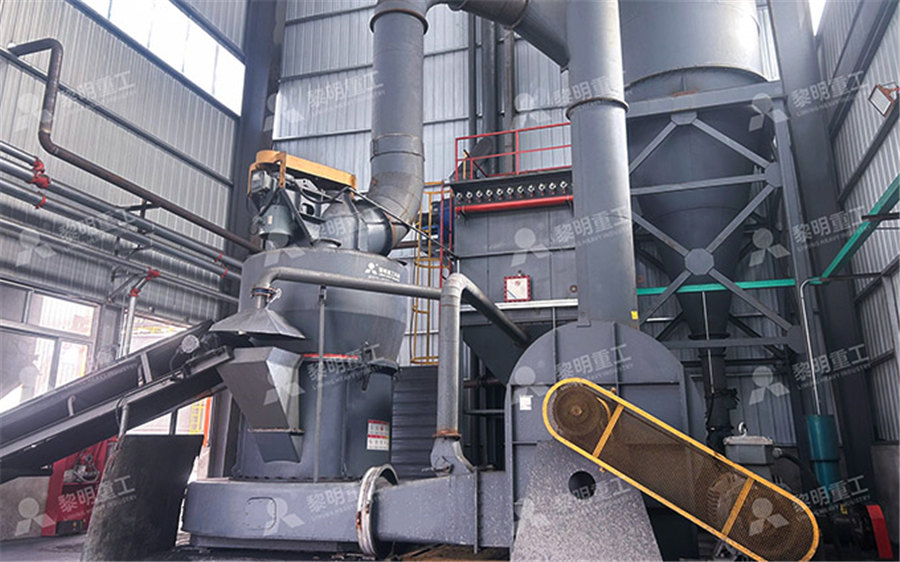
Nonlinear coal mill modeling and its application to model
2013年3月1日 Therefore, for coal mill control the application of NMPC is a recommended solution 8 Conclusions In the present paper, the modeling of a vertical roller pressure coal mill was addressed As a result, a nonlinear model has been developed and validated to predict the coal mill behavior during start up and normal operationWhen selecting a vertical mill for a 200 mesh coal powder preparation system, several factors should be considered: Material Properties: The hardness and moisture content of the coal will influence the choice of vertical mill Production Capacity: The desired production volume will determine the size and capacity of the vertical mill neededChoosing the right vertical mill for 200 mesh coal powder Vertical Coal Mill, also known as coal mill, for superfine grinding of raw coal, soft coal specifically for cement, power plant, steel mill and other fields Its special design structure and production process creates the higher production efficiency with lower energy consumption, less dust, lower noise than ball mill, which meets national standard of energy saving industryVertical Coal Mill Great WallPart of what marks Magotteaux out as a leader in vertical coal mill technology is our ongoing commitment to making things better for power station managers and other users of milled coal today After all, our impressive Expand range of wear parts for vertical mills did not simply come about by accident, we identified an area we thought we could bring technological Vertical Coal Mill Magotteaux
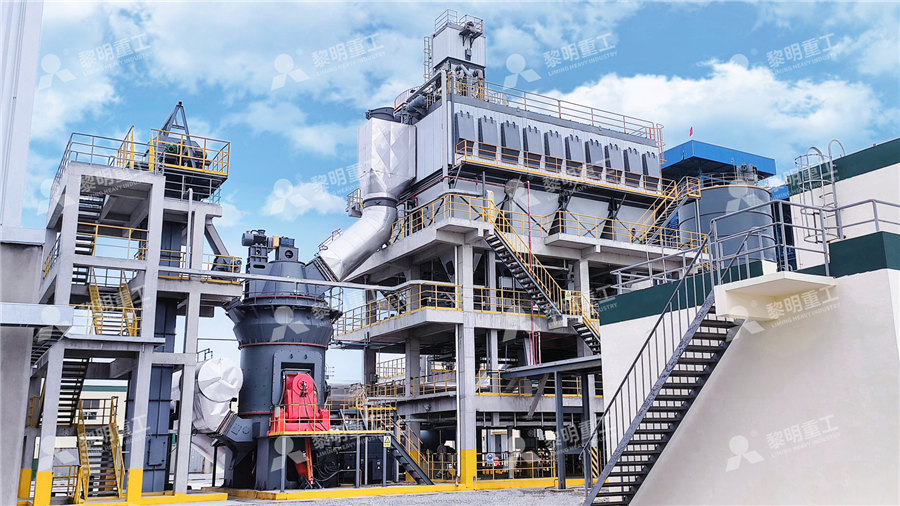
The importance of vertical roller mill in limestone grinding
4 Dust emission ≤10mg/Nm3, in line with environmental protection requirements; 5 With composite separator, the fineness of the product can be adjusted freely to meet the needs of customers producing different products2012年11月17日 20 131Fineness Fineness is an indicator of the quality of the pulverizer action Specifically, fineness is a measurement of the percentage of a coal sample that passes through a set of test sieves usually designated at 50, Coal mill pulverizer in thermal power plants PPT2014年10月1日 To investigate the effect of size and density on the segregation of particles in the static classifier of vertical spindle mill, classification tests of coal were conducted in a labscale Numerical and experimental analysis of pulverized coal mill Magotteaux: The global leader in wear parts for Vertical Mill grinding circuits Magotteaux has established itself as a global leader in wear parts for vertical mill grinding circuits by consistently delivering innovative solutions that address the complex requirements of multiple industries Our commitment to innovation, quality, and customer satisfaction has earned us the trust and Vertical Mill Mining Magotteaux
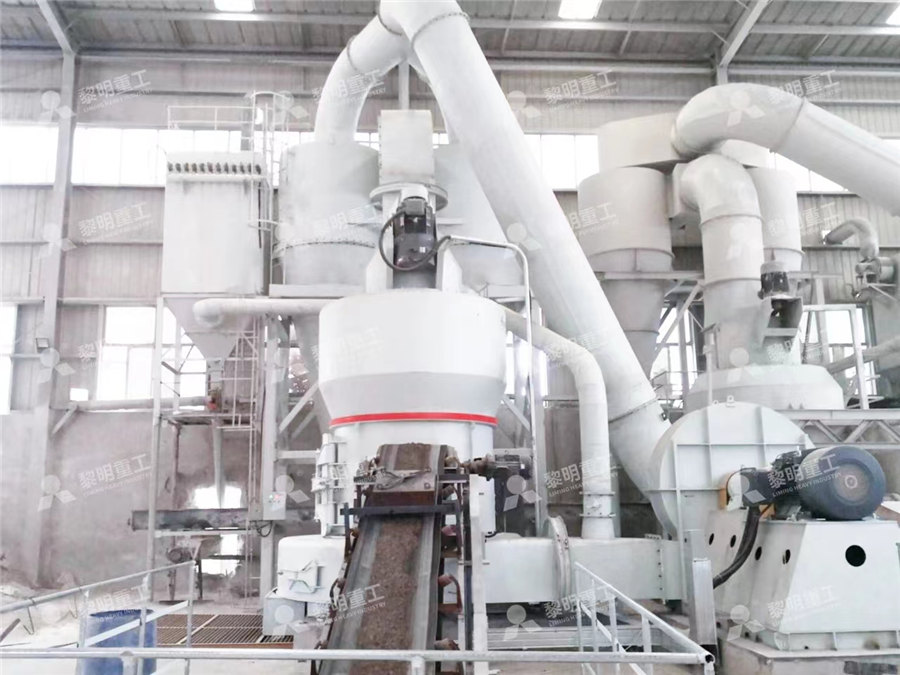
Detection of Malfunctions and Abnormal Working Conditions of a Coal Mill
2018年5月2日 Coal mill malfunctions are some of the most common causes of failing to keep the power plant crucial operating parameters or even unplanned power plant shutdowns Therefore, an algorithm has been developed that enable online detection of abnormal conditions and malfunctions of an operating mill Based on calculated diagnostic signals and defined From the coal yard, the coal is transfer to the mill bunkers through conveyor belt The bunkers are sized for an effective capacity of twelve (12) hours at BMCR with design coal Each mill bunker has one hopper, connected to the feeders Mills operate when the bunker coal gate valves are opened, coal is allowed to flow to the gravimetric feedersAnalysis of the Coal Milling Operations to the Boiler Parameters2015年11月1日 As presented by Andersen et al (2009) and Odgaard, Stoustrup, and Mataji (2007), coal moisture imposes limit on the maximum load at which a coal mill can be operated and the load gradient (how fast the mill may change its operating point), if it is desired that the pulverized coal entering the furnace has moisture content less than or equal to a certain value A unified thermomechanical model for coal mill operation2011年10月1日 As an example of the importance of effective fuel classification, a typical classifier for a vertical air swept pulverizer which have been limited to the upper portion of the pulverizer is Improved Coal Fineness Improves Performance, Reduces Emissions
.jpg)
A Study on 500 MW Coal Fired Boiler Unit’s Bowl Mill
Section of coal bowl mill Table 1 Guaranteed coal conditions for mill performance evaluation Coal Moisture % 20 Coal HGI 55 Mill Outlet Temperarure °C 80 Mill Air Flow T/hr 102 Coal Fineness (% passing trough 200 mesh) 70% passing through 200 mesh and 90% passing through 50 mesh Differental Pressure 300 mmwc Coal Output from Mill 609 t/hr2009年9月20日 A control oriented model was then developed by Fan (1994) and Fan and Rees (1994) In 2009, coal flow and outlet temperature of mill were modelled using mass and heat balance equations for startup Modeling and Parameter Identification of Coal Mill3 Precise Control and Automation: Bellian Machinery's coal mills feature advanced control systems that enable precise control over various operational parameters Operators can adjust grinding variables, such as coal flow and mill rotation speed, in realtime to achieve the desired coal fineness and optimize mill performanceCoal Mill in Thermal Power Plant: Enhancing Efficiency and 2020年4月2日 The different mill has different PC pipe corners, The mill design in the power plant is a vertical bowl Coal mill motor power (kW) 0 4171 4548 4390 4586 Analysis of the Coal Milling Operations to the Boiler
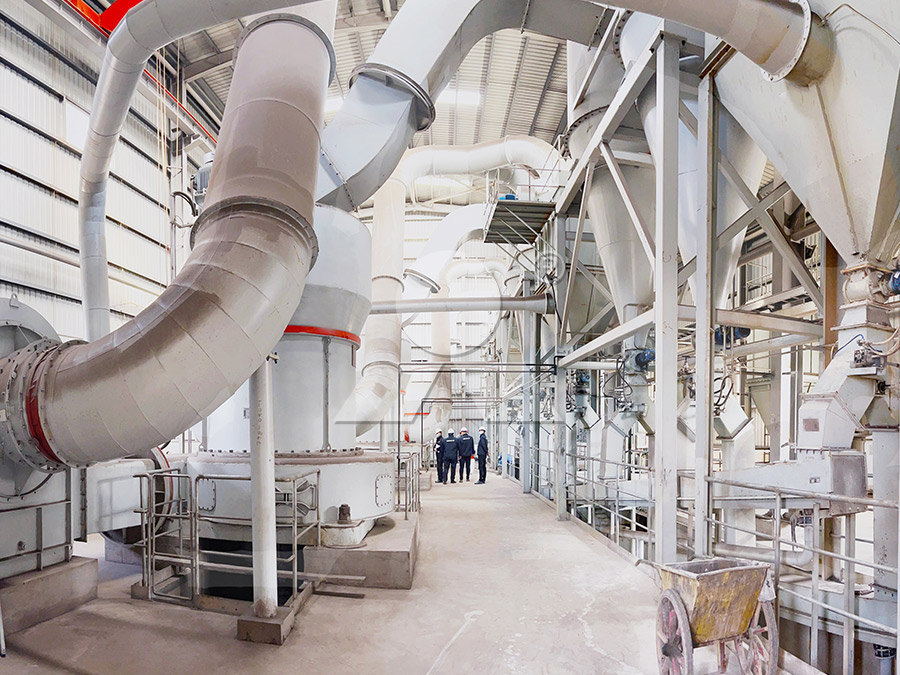
COAL VERTICAL MILL Xinxiang Great Wall Machinery Co, Ltd
Process introduction GRMC coal vertical mill produced by CHAENG adopts a special structure design and production technology, and the quality is up to the leading level in China It is the first choice equipment for grinding raw coal and bituminous coal 1 The raw coal is screened from the raw coal storage yard and then dropped onto the belt conveyor through the grid screen2024年1月15日 An industrialscale vertical roller mill (M600) was analysed for air flow in this study This led to proposed modifications, which were implemented in a new mill design (M350) The M600 mill can operate under continuous mode and is used for fine grinding of materials The design of this mill is depicted in Fig 1Optimisation of the performance of a new vertical roller mill by Our ATOX® Coal Mill is a compact vertical roller mill that can grind almost any type of raw coal The coal mill utilises compression and shear force generated between the large rollers and the rotating table to crush and grind raw coal, removing the need for a ATOX® Coal Mill FLSmidth CementA control oriented model was then developed by Fan (1994) and Fan and Rees (1994) In 2009, coal flow and outlet temperature of mill were modelled using mass and heat balance equations for startup Sectional view of MBF coal mill Download Scientific Diagram
.jpg)
Coal Grinding Cement Plant Optimization
Mill Feeders: Feeders for coal mill are generally installed directly under hoppers with rod gate in between The feeders are generally 2 to 3 m long and discharge on to conveyor or feeding chute to mill For coal mill feeding, table feeders, belt feeders, When it comes to the operation of a ball mill, it’s important to have a clear understanding of how the machine works One key component of the ball mill is the feeder, which is responsible for accurately dispensing the grinding media into the mill The importance of ball mill feeders in the grinding process cannot be overstated, as they play a critical role in ensuring that the entire The Importance of Ball Mill Feeders in the Grinding Processin the mining or coal processing operations Fig3 Mill fuel piping connections to furnace II COAL MILL SPECIFICATIONS PERFORMANCE ANALYSIS Typical Coal Pulveriser Mill Details in 660 MW SuperCritical [3] Unit is as given in table Table No 1 Table1 Coal mill Type Bowl Type Mediumspeed Coal mill Number of Mills 6set/ boilerPulveriser Mill Performance Analysis Optimisation in Super2013年3月1日 In the present paper, the modeling of a vertical roller pressure coal mill was addressed As a result, a nonlinear model has been developed and validated to predict the coal mill behavior during start up and normal operation The parameter optimization and the model validation have been conducted with real coal mill measurementsNonlinear coal mill modeling and its application to model predictive
.jpg)
Research on fault diagnosis of coal mill system based on the
2020年9月1日 In the second set of test, the actual operation data of the coal mill was used for testing based on the trained model in the first set of test During the test, the actual operation data of a coal mill for 5000 s was selected as the data samples, which contained the conditions of multiple coal interruption The results are shown in Fig 14