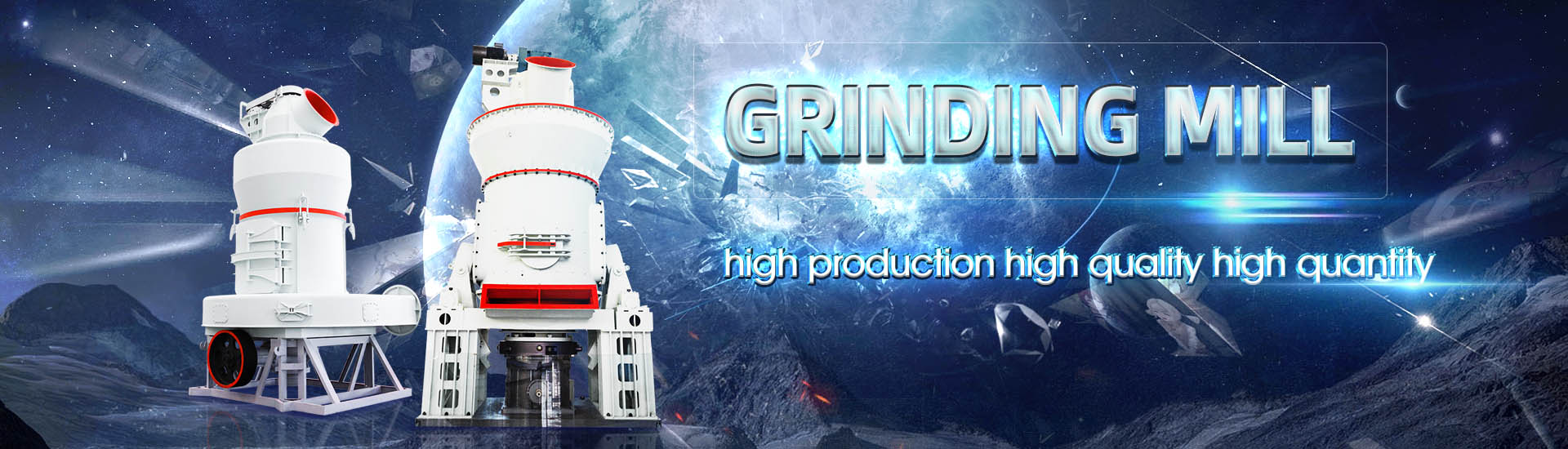
Ore grinding mill components
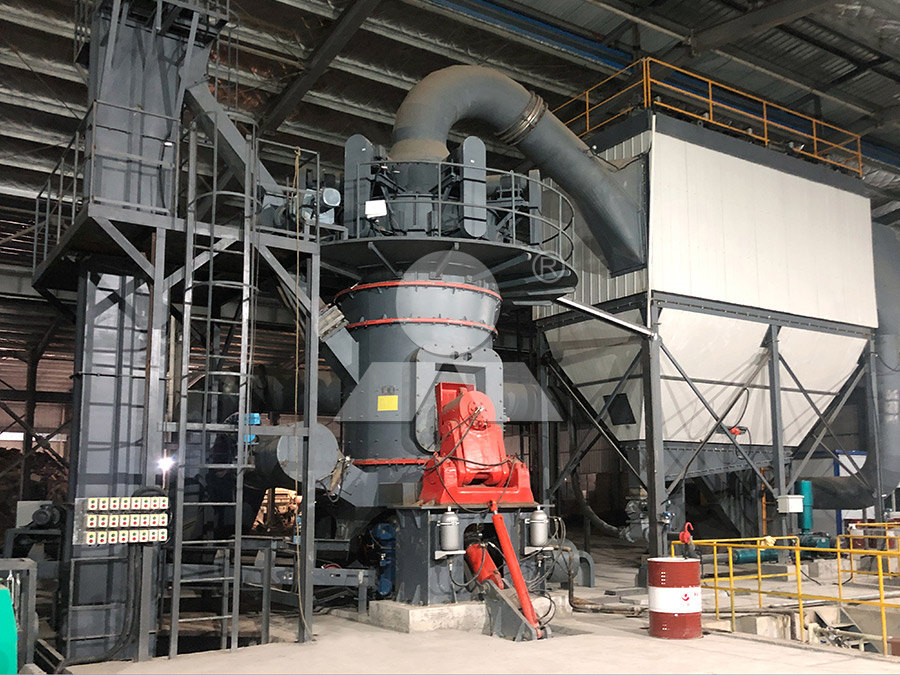
Grinding Mill Components 911Metallurgist
2015年4月29日 SAG Mill, Rod Mill or Ball Mill this is a typical grinding mill component list/assembly 911 Metallurgist is a trusted resource for practical insights, solutions, and support in mineral processing engineering, helping 2023年10月27日 Grinding media play an important role in the comminution of mineral ores in these mills This work reviews the application of balls in mineral processing as a function of the A Review of the Grinding Media in Ball Mills for Mineral Processing Customized grinding mill parts including heads, shells, trunnions and liners, main bearings, gears and pinions, and more! Metallic, PolyMet™, Megaliner™, Rubber and Orebed™ mill liners for Grinding MetsoIt is performed in cylindrical steel vessels that contain a charge of loose crushing bodies—the grinding medium—which is free to move inside the mill, thus comminuting the ore particles Grinding Mill an overview ScienceDirect Topics
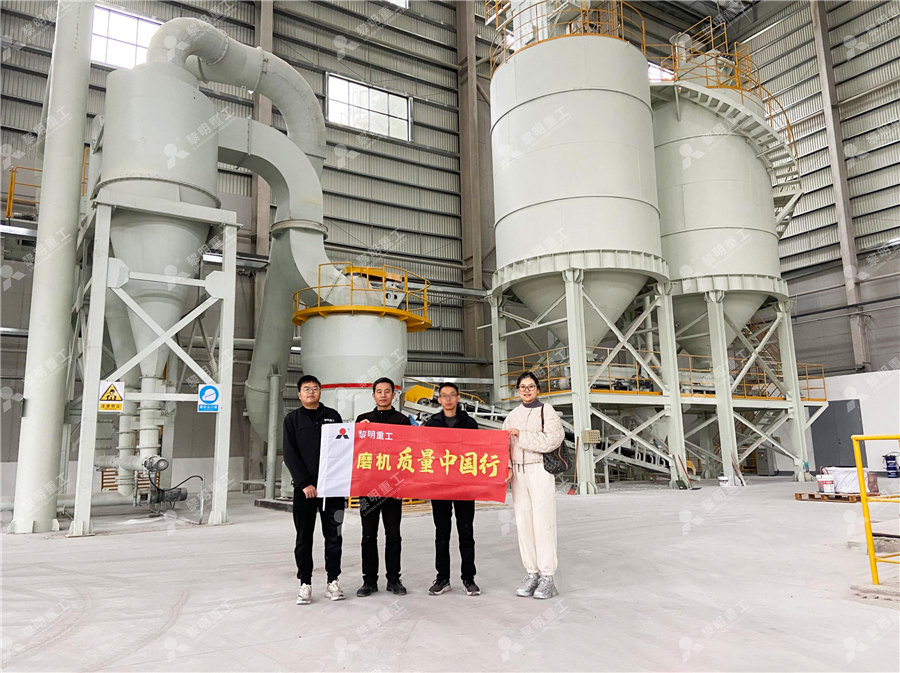
ISAMILL FINE GRINDING TECHNOLOGY AND ITS INDUSTRIAL
Fine grinding, in particular in the zinc retreatment circuit requiring a milled product P80 of 7 micron, is essential to treat the ores from the Mount Isa Mines deposits2023年7月20日 Moist grinding, a special grinding method, is used to prepare pellets for smelting According to the grinding medium features, ore grinding is mainly classified into ball grinding Ore Grinding SpringerLink2023年7月1日 For the ball milling, the breakage characteristics of a given ore were determined via dropweight tester based on the elements Then the model structure was developed by Element based ball mill and hydrocyclone modelling for a copper In a typical application, the HIG process begins with the regrinding circuit feed being pumped to a scalping cyclone upstream of the mill which classifies the target size material off from the feed Outotec HIGmills; A Fine Grinding Technology
.jpg)
Measurement and Control for Ore Grinding and Classification
2023年6月1日 The main parameters of grinding and classification process include measurement of millfeeding quantity, mill load measurement, measurement of ore slurry density, Online 2017年9月1日 The objective of this work is to assess the influence of fine grinding in ball mills and stirred mills on valuable mineral liberation and particle shape characteristics of UG2 ore, a Fine grinding: How mill type affects particle shape characteristics 2023年7月1日 The simplified flowsheet of the copper ore grinding circuit on which the water added points and sampling locations are seen is depicted in Fig 1 In this regard, product size distributions of Ball mill1 and Ball mill2 were predicted for each componentElement based ball mill and hydrocyclone modelling for a copper ore 2023年7月20日 Therefore, the rod mill is mostly used for coarse grinding of the previous period of ball mill, or grinding of brittle materials and materials against overcrushing, such as tungsten and tin ore before gravity separation; and (3) autogenous mill – it refers to the materials which themselves are collided and ground mutually to be crushed when the grinding mill rotates, and Ore Grinding SpringerLink
.jpg)
Mineral processing Wikipedia
Crushing, a form of comminution, one of the unit operations of mineral processing Mineral processing is the process of separating commercially valuable minerals from their ores in the field of extractive metallurgy [1] Depending on the processes used in each instance, it is often referred to as ore dressing or ore milling Beneficiation is any process that improves (benefits) the HGM ultrafine grinding mill can process nonmetallic ores with Mohs hardness less than 7 The equipment has stable operation, simple operation, long service life, low carbon and environmental protection There are 5 models of HGM ultrafine grinding mill, SBM Ore Ultrafine Grinding Mill2022年8月31日 The grinding speed of ore and its component minerals decreased exponentially with the grinding time, and the instantaneous grinding speed of 0 min was negatively correlated with the feed sizes The rapidly decreasing trend of the grinding speed reached the threshold when the grinding time reached 4 minGrinding Modeling and Energy Efficiency in Ore/Raw Material SAG MILL TESTING AN OVERVIEW OF THE TEST PROCEDURES AVAILABLE TO CHARACTERIZE ORE GRINDABILITY AUTHOR: FO VERRET, G CHIASSON AND A MCKEN SGS KEYWORDS Comminution, grindability, grinding, SAG mill, AG mill, milling, HPGR, work index, pilot plant INTRODUCTION The resistance of ore samples to breakage (or hardness) is SAG Mill Testing Test Procedures to Characterize Ore
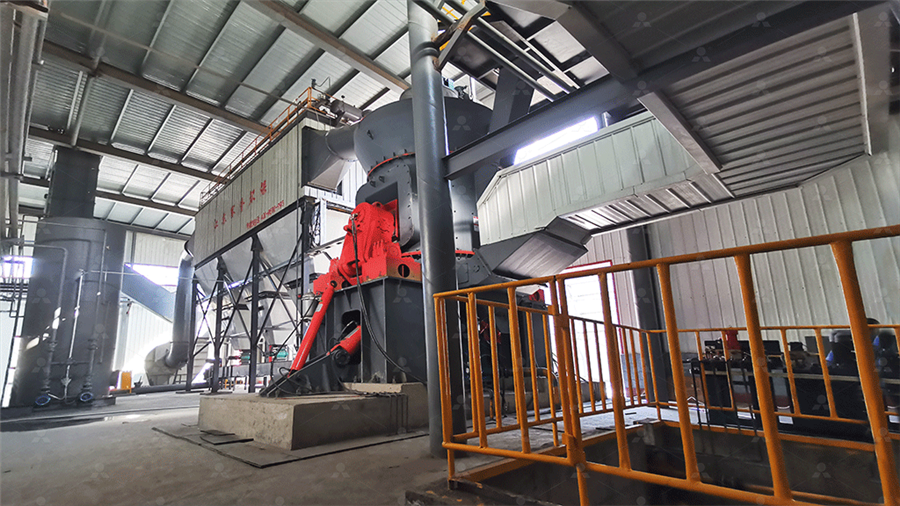
Grinding Mill Liners: Protecting Your Investment and WALKSON
In the world of mineral processing and ore grinding, the durability and efficiency of grinding mill liners are critical factors These unassuming components play a pivotal role in ensuring the continuous operation of grinding mills, which are essential in various industriesIn the mill, the mixture of medium, ore, and water, known as the mill charge, is intimately mixed, the medium comminuting the particles by any of the above methods Apart from laboratory testing, grinding in mineral processing is a continuous process, material being fed at a controlled rate into one end of the mill and discharging at the other end after a suitable dwell (residence) timeGrinding Mill an overview ScienceDirect Topicsloading spout, 4 armor, 5 grinding unit, 6 commercial component, 7 unloading spout A fragment of armor with riffles and grinding unit (ball), B fragment of riffle with commercial component The mode of the mill is as follows Water and ore are fed into the mill operating cavity through a loading spoutDevelopment of a new lining ball mill model for commercial component 2024年1月12日 How Overflow Type Ball Mill Works Material Feed: The raw material is fed into the mill at one end and travels through the mill by rotation The feed enters the mill at a specific rate, ensuring a controlled grinding process; Grinding Process: As the mill rotates, the grinding media crushes and grinds the material into a fine powder The wet conditions enhance the Wet Overflow Type Ball Mill and Applications
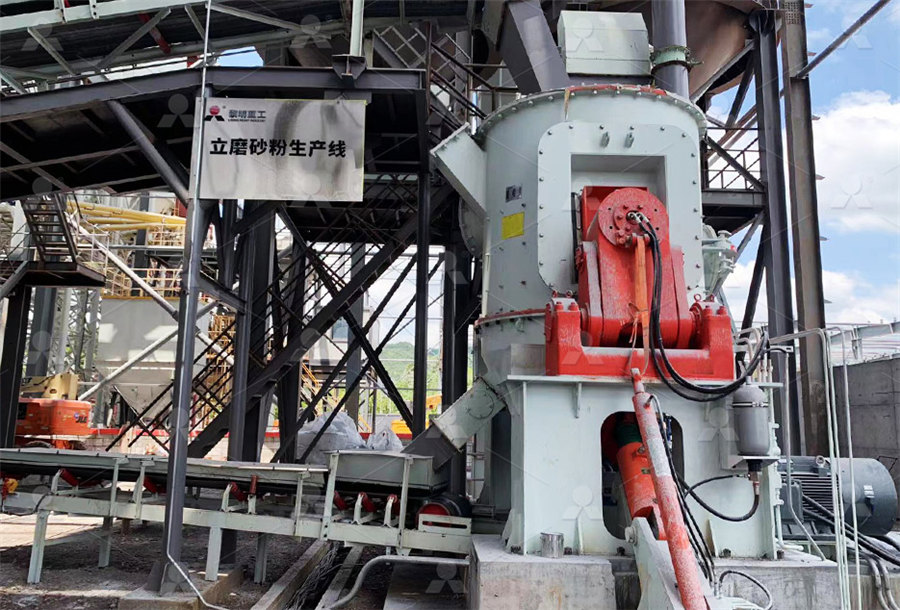
Grinding Metso
Metso has experience with over 8,000 grinding mill installations globally, including manufacturing and delivering the largest SAG/AG mills in the world Global expertise, local presence +100 years of experience in minerals processing Professionals in over 50 countries around the worldmineral processing, art of treating crude ores and mineral products in order to separate the valuable minerals from the waste rock, or gangue It is the first process that most ores undergo after mining in order to provide a more Mineral processing Metallurgy, Crushing Grinding ore grinding mill circuit A continuoustime grinding mill circuit model is presented with a hydrocyclone cluster as the primary classi er The discretetime component is the switching of hydrocyclones in the hydrocyclone cluster The resulting model is a hybrid nonlinear model with both continuous and discrete dynamicsHybrid nonlinear model predictive control of a runofmine ore Metso Premier™ mills and Select™ mills are built with a robust design and components to eliminate unplanned downtime leading to high availability and reliability Our grinding mill inspection packages can help you save thousands of Euros per day Gear and pinion services A complete range of gear and pinion sets, inspections, Grinding mills for mining and minerals processing Metso
.jpg)
Exploring the components and functionality of a ball mill section
Liners are essential components that line the inner surface of the ball mill drum, protecting the drum from wear and tear caused by the grinding media and ore They are typically made of highquality cast steels or rubber materials, depending on the application and desired wear resistance2023年10月27日 The ball mill is a rotating cylindrical vessel with grinding media inside, which is responsible for breaking the ore particles Grinding media play an important role in the comminution of mineral ores in these mills This work reviews the application of balls in mineral processing as a function of the materials used to manufacture them and the mass loss, as A Review of the Grinding Media in Ball Mills for Mineral 2015年3月10日 DOI: 101016/JMINPRO201410002 Corpus ID: ; Copper ore grinding in a mobile vertical roller mill pilot plant @article{Altun2015CopperOG, title={Copper ore grinding in a mobile vertical roller mill pilot plant}, author={Deniz Altun and Carsten Gerold and Hakan Benzer and Okay Altun and Namık A Aydogan}, journal={International Journal of Copper ore grinding in a mobile vertical roller mill pilot plant2024年7月19日 Grinding Mill equipment, such as MechProTech’s TITAN Grinding Mills and TITAN Automatic Ball Charger, can optimise grinding mills’ efficiency and performance, benefiting the process Investing in MPT equipment promises to improve your operational efficiency, with our team of experts ready to walk you through it allGrinding Mills in the Mineral Processing Industry MechProTech
.jpg)
Mechanistic modeling and simulation of multicomponent batch
2022年6月29日 Keywords: ball milling, multicomponent, iron ore In order to supply de demand of metals in a scenario of depletion of the richest ore deposits around the world, the most part of mining companies 2020年6月3日 Grinding mills are some of the most important equipment in mines, processing over a few thousand tons of ore every hour It is not uncommon to see these days that a single line of a grinding circuit consisting of a Semi Autogenous Grinding (SAG) mill followed typically by two ball mills generating over USD $1 million of revenues per dayHow grinding mill design changed over the last 30 years2018年8月17日 Further, the grinding mills can be categorized into three major types — rod mills, ball mills, and SAG mills So, which one is for you? Well, the answer essentially lies in the feed size and the Grinding Mills — Types, Working Principle 2022年10月13日 Grinding plays an important role in mining, construction, metallurgy, chemical, coal and other basic industries In terms of beneficiation, grinding is the most energy consuming operation So, reasonable grinding Research on Grinding Law and Grinding Parameters
.jpg)
SAG Mill Grinding Circuit Design 911Metallurgist
2016年6月6日 B Mill Power Mill Speed: Percent Critical/Peripheral; Direction of Rotation; Power Draft Design Drive Power C Total Feed Conditions, including total mill volumetric flow rate; recirculating load Feed Chute Design 2017年11月6日 Grinding balls are essential mechanical components in ball and semiautogenous (SAG) mills Their function is crushing and grinding ore rocks weighing up to 45 kg (100 lb) preparatory to recovery of valuable minerals, from lead through rare earth elements, which are essential to the approaching 21st century technological societyGrinding Ball Design 911Metallurgist2012年6月1日 As the cylinder starts to rotate, the grinding balls inside the cylinder crush and grind the feed material, generating mechanical energy that aids in breaking bonds, activating the catalyst, and Grinding in Ball Mills: Modeling and Process ControlThe rock and grinding media are placed in the mill and rotated, causing the grinding media to tumble and crush the rock into smaller pieces The mill operates in a closed circuit with screens that size the ore and send it back to the mill for further grinding The product from the mill is then sent to a cyclone for separation of the desired A Comprehensive Guide to SAG Mill Operation ball mills supplier
.jpg)
A guide to SAG Mill management
2024年5月17日 A SAG (SemiAutogenous Grinding) mill is a giant rotating cylinder filled with grinding media and the ore being reduced As the mill rotates, the grinding media lifts and the impact crushes the feed material SAG mill control refers to the practice of managing the mill load, which is the amount of material inside the mill at any given timeBall Mill Grinding Machines: Exploring the Working Principle, Types, Parts, Applications, Advantages, and Recent Developments Ball mill grinding machines are widely used in various industries for the comminution of materials into fine powders They are versatile tools that offer efficient and reliable grinding and mixing capabilitiesBall Mill Grinding Machines: Working Principle, Types, Parts GMDs are the grinding solution of choice in challenging environments like high altitudes or varied climates in remote locations By eliminating bolton mechanical components such as ringgears, pinions, couplings and gearboxes, GMDs offer ore producers unrivalled availability, efficiency and durability, while reducing operating expenditureMaking remote mines and low ore grades economical and shifting This work relates to a wear test for mill components after the occurrence of a failure in an iron ore pelletizing plant at Vale’s (1985) 253 261 CORROSIVE AND ABRASIVE WEAR IN ORE GRINDING* I IW ASAKI, S C RIEM ER and J N ORLICH M ineral Resources Research Center, University of M innesota, M inneapolis, MN 55455 (USA Corrosive and abrasive wear in ore grinding Academia
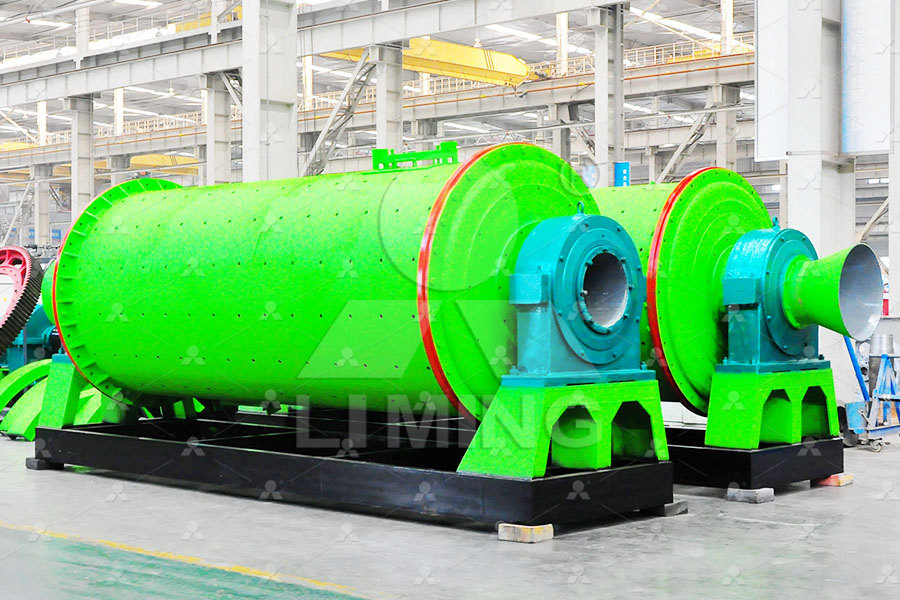
AG Autogenous Grinding 911Metallurgist
2015年8月6日 In conventional milling, the ore is crushed to, plus or minus, 3/8 of an inch, before it is put into a mill for grinding In a autogenous mill the ore is fed directly into the mill from either the primary crusher or the mine itself The size 2022年8月24日 The method allows capturing variations in mill filling and mill speed, whereas effects such as ball size distribution and solids concentrations require conducting batch tests incorporating their Multicomponent modeling and simulation of the Minas Rio iron ore Here, we delve into the key components and technologies that make up the modern ore powder production process Key Components of Ore Powder Production Equipment: 1 Vertical Roller Mill: Offers a compact design and is efficient in grinding ore to fine powder Raymond Mill: Advancements in ore powder production process equipment: The control of AG mills, fed by ores with hard and soft components, can also be challenging, due to the sensitivity of the mill to the ratio of hard to soft components In this paper, a multicomponent modelling approach was used to demonstrate that the harder component should be used as grinding media, and its use should be kept to a minimum to avoid reduction in the mill How to Use Hard Ore Components as Grinding Media
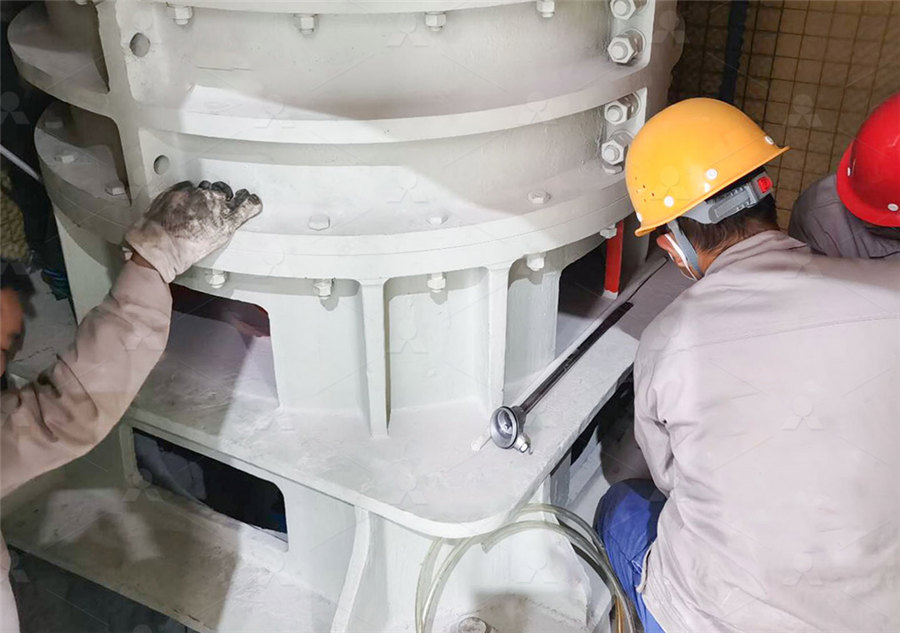
Grinding Mills 911Metallurgist
Grinding Mills: Ball Mill Rod Mill Design PartsCommon types of grinding mills include Ball Mills and Rod Mills This includes all rotating mills with heavy grinding media loads This article focuses on ball and rod mills excluding SAG and AG mills Although their concepts are very similar, they are not discussed herePhotographs of a glass ended laboratory ball mill show Ore grinding machines can be divided into many types according to different classification methods, each with significant characteristics The following is a general introduction to the types of oregrinding machines and their characteristics According to the different media of the mill, the grinding machines are divided into: If the medium is steel balls, it is called a ball mill;Ore Grinding Machines: Ball Mill, Rod Mil Grinding Media2023年7月4日 Roller mill is a type of grinding equipment for crushing materials by pressure between two or more rolling surfaces or between rolling grinding bodies (balls, rollers) and a track (plane, ring, and table) The roller mill with several grinding rollers as working components rolls along the manganese ore fine grinding Roller Mill SpringerLinkThe typical grinding mill includes the ball mill, rod mill, SAG mill, Raymond grinding mill, AG mill, vertical mill, etc, Due to the work impact, the quality of the grinding mill parts and components directly determines the service life of the grinder JXSC Machine mainly supplies customized mill parts and components that aim to improve the reliability of your machineGrinding Mill Parts JXSC Machine
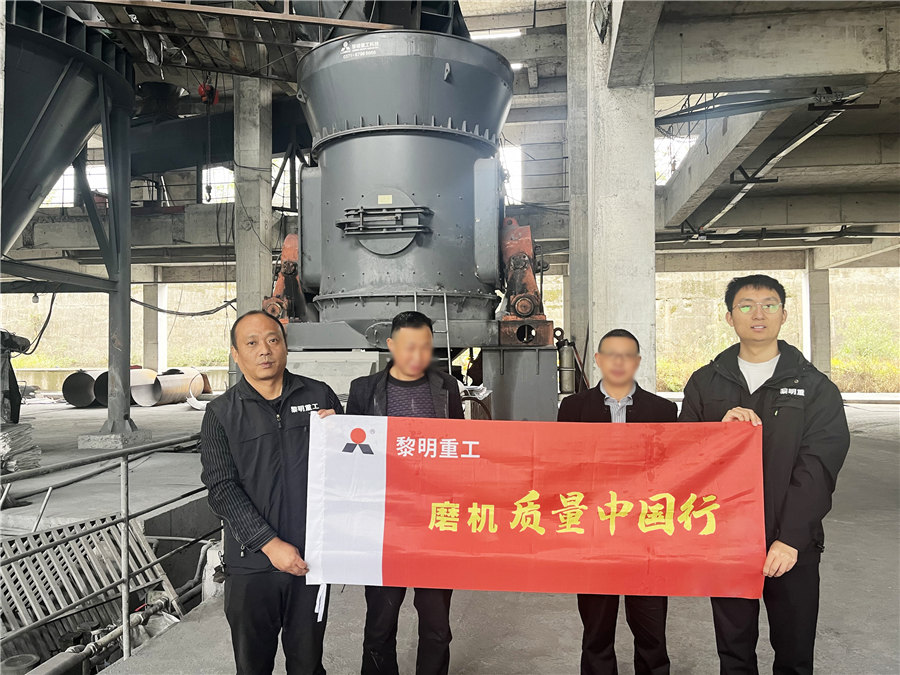
Understanding Ball Mill Parts: Essential Components for Effective Grinding
2024年5月17日 The efficiency and performance of a ball mill depend significantly on the quality and condition of its parts This comprehensive article explores the essential components of a ball mill, their functions, and the critical aspects of their maintenance Key Components of 2019年12月15日 429 VertiMills Vertical mills were first designed in the 1950s for applications in fine and ultrafine grinding in Japan Lately, the vertical mill is making progress toward primary grind application and shown promise in energy reduction relative to ball mills, typical to what is normally seen in regrinding applications (Mazzinghy et al 2014)Beneficiation of Gold and Silver Ores SpringerLink