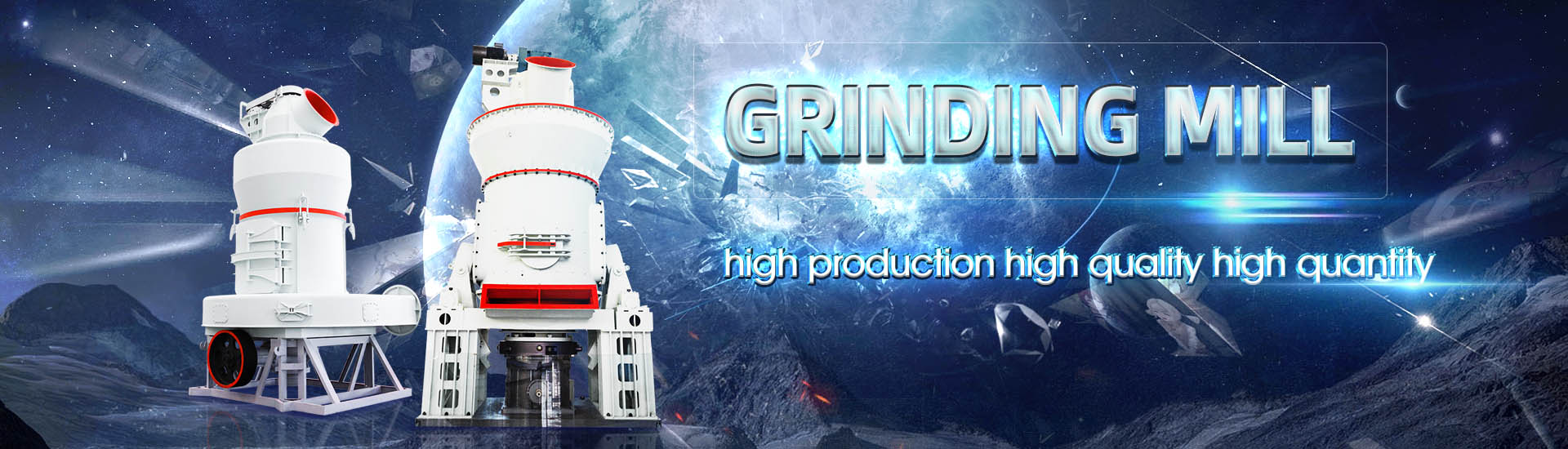
1616 single forged ore grinding mill
.jpg)
A Review of the Grinding Media in Ball Mills for Mineral Processing
2023年10月27日 Grinding media play an important role in the comminution of mineral ores in these mills This work reviews the application of balls in mineral processing as a function of the Grinding in ball mills is an important technological process applied to reduce the size of particles which may have different nature and a wide diversity of physical, mechanical and chemical Grinding in Ball Mills: Modeling and Process Control SciendoIntegrated with a classification tower and feed/discharge conveyor system, the mill can be setup to facilitate open circuit, single stage closed circuit, AG/SAG and ball mill circuit (SAB), and SAG milling grinding pilot plants alsglobal2023年7月20日 Moist grinding, a special grinding method, is used to prepare pellets for smelting According to the grinding medium features, ore grinding is mainly classified into ball grinding Ore Grinding SpringerLink
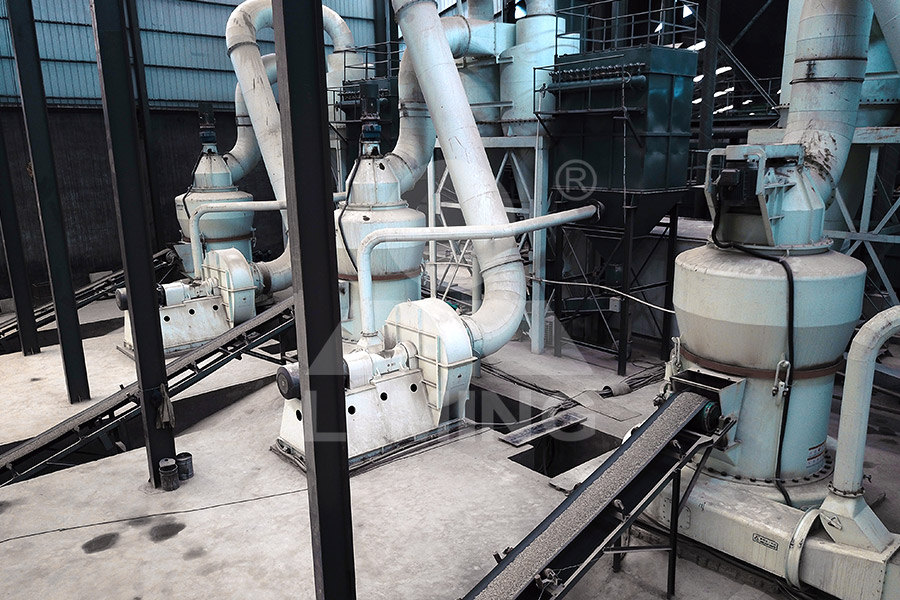
TECHNICAL NOTES 8 GRINDING R P King
Mills usually operate in the range 65 82% of critical but values as high as 90% are sometimes used A crucial parameter that defines the performance of a mill is the energy consumption 2012年1月1日 The Gold Mill was commissioned in March 2008 with a 32’ x 32’ EGL, 165MW single stage SAG mill, to process 5 million tonnes per annum high grade oxide Au/Ag ore Yanacocha Gold Single Stage SAG Mill Design, Operation, and 2012年6月1日 The paper presents an overview of the current methodology and practice in modeling and control of the grinding process in industrial ball mills Basic kinetic and energy Grinding in Ball Mills: Modeling and Process Control ResearchGategrinding environments in which grinding media are used These include semiautogenous (SAG) mills, rod mills, conventional ball mills, and tower mills The different types ofgrinding media Wear ofgrinding media in the mineral processing industry: An
.jpg)
Ball Grinding Process SpringerLink
2023年7月27日 Ball grinding can be carried out in either dryoperation or wetoperation The former is widely used in coalfired power plants and cement industry, and the latter is widely In the present state of technological development for primary grinding mills, there is a wide choice of acceptable options with respect to type and size, grinding flowsheet and grinding mediaPrimary Grinding Mills: Selection, Sizing And Current PracticesSavona Equipment is your source for mill components and accessories for large primary ore process concentrating through secondary and tertiary fine material as well as complete ore processing facilities All our reconditioned mill components will be supplied ready for service We can supply SAG mill parts and Ball mill wearparts including ball mill liners and shell liners Our Grinding Mill Parts for Sale Ball Mill Parts SAG Mill Parts2016年10月21日 This page is devoted to the subject “From the Comminution Theory to Practice by selection of the correct Process Equipment” by taking you step by step through some of the variables encountered in the specific part of Comminution Theory Process Equipment
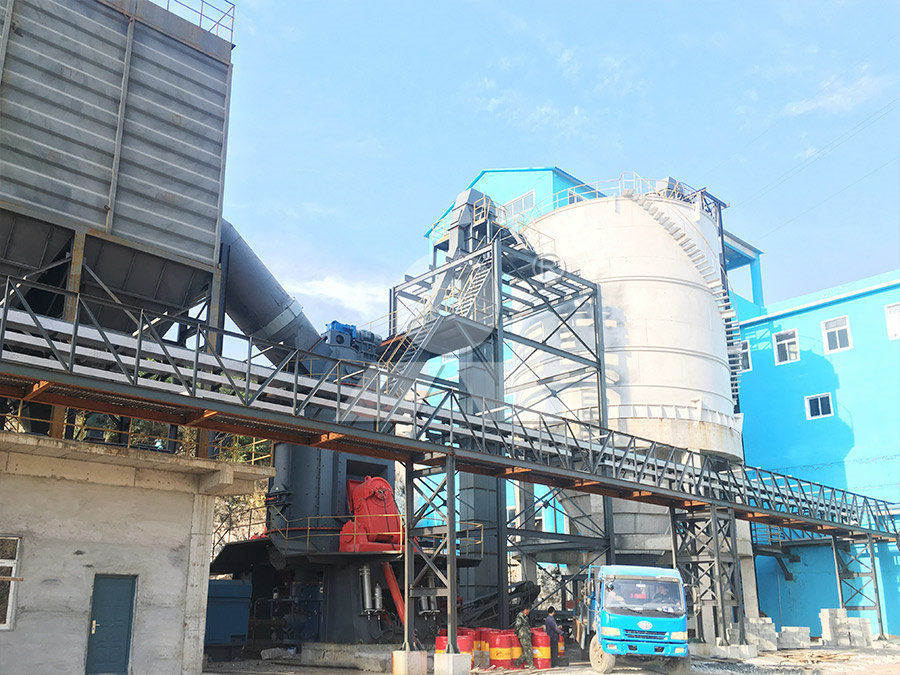
Grinding Mill Design Ball Mill Manufacturer 911Metallurgist
2017年2月20日 The grinding charge in a ball mill consist of cast or forged steel balls These balls are fed together with the feed and consequently ball mills can be in operation for months without stopping The ball size is often in the diameter range of 2075 mm The biggest size is chosen when the mill is used as a primary grinding millThe Autogenous Mill, also known as AG Mill, is a type of grinding mill used in the mining industry This machine uses ore and rock itself as grinding media to perform its job Unlike other types of mills that use steel balls or rods for grinding materials, the Autogenous Mill relies on the material being ground to break itself into smaller piecesUnderstanding the SAG Mill in Copper Ore Mining ProcessBall Mill Forged Grinding Steel Ball From Chinese Manufacturer US$ 650680 / Ton 25 Product Description High Hardness Good Price 20150mm Steel Forged and Casting Iron Ore Grinding Media Ball for Ball Mill Machine Factory for Cement Plant Mine Send us the drawings and we'll give you our best offer within 2 hours,click here contact us Forged Grinding Ball China grinding media ball, forged steel grinding 2017年8月26日 One of the most difficult tasks is the direct establishment of contribution of corrosion wear An indirect method of measuring corrosion contribution is to compare steel wear in wet and dry grinding Metal loss per ton of ore ground is higher in wet grinding than in dry grinding for a typical ore of average work index 13 kWh/tHow to Reduce Steel Consumption in Grinding Mills
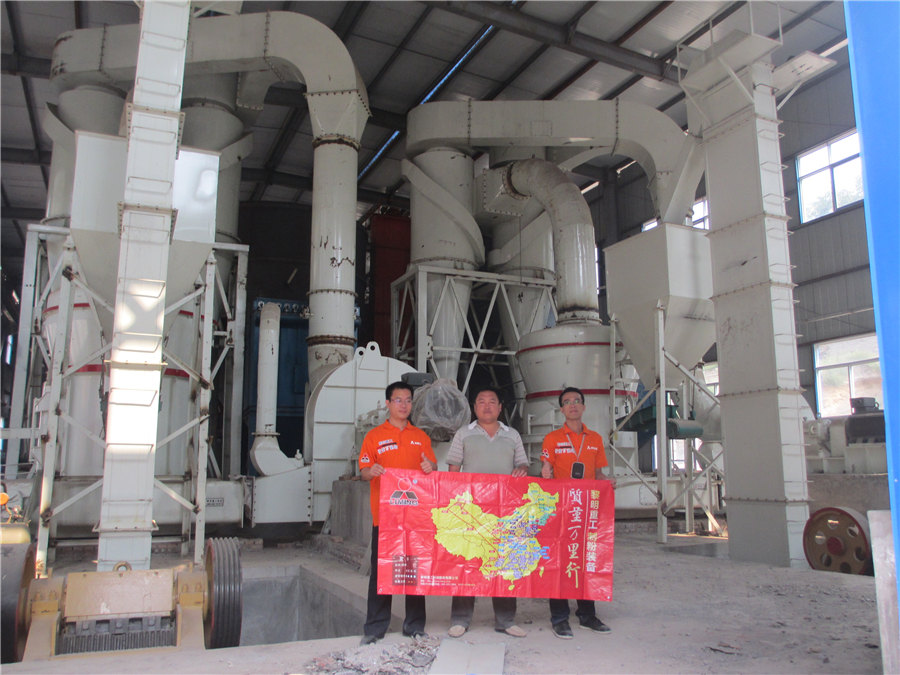
INVESTIGATION ON FLOTATION BEHAVIOR OF A COPPER SULFIDE ORE
Compressive grinding, Dry grinding, Flotation of copper sulfide ore, Mineral liberation, Vertical roller mill INTRODUCTION Copper production is mainly connected to porphyry copper deposits as main 2024年5月7日 Forged steel grinding balls are essential components used in various grinding and milling applications across industries such as mining, cement, and chemical processing These balls, crafted through the process of forging, are renowned for their robustness and ability to perform under rigorous conditions, making them a preferred choice for heavyduty grinding tasksForged Steel Grinding Balls by ENERGOSTEEL1985年6月1日 The relative significance of corrosive and abrasive wear in ore grinding is discussed Laboratory marked ball wear tests were carried out with magnetic taconite and quartzite under different (PDF) Corrosive and abrasive wear in ore grinding ResearchGate2016年7月14日 HPGR test results published by Grier (1992) on gold ores from the Mt Todd project showed significant energy savings for a HPGR/Ball Mill circuit as compared to a SAG/Ball Mill plant By adding a Polycom highpressure grinding roll, the throughput of existing plants can be increased by as much as 150% while simultaneously reducing the power consumption by HPGR 911Metallurgist
.jpg)
How to choose a suitable ore powder grinding mill?
2023年10月17日 3 Ultrafine Powder Grinding Mill Ultrafine powder mill (threering / fourring mediumspeed micropowder mill) feed particle size ≤25 mm, production capacity 0545 t/h, production fineness 1503500 mesh,it is a high 2017年1月17日 Other process activities, such as spraying the ore with water for dust control or the fact that runofmine ore moisture is approximately 2%5% are not generally considered (Bleiwas, 2012a)Breaking down energy consumption in industrial 2017年10月26日 The following are factors that have been investigated and applied in conventional ball milling in order to maximize grinding efficiency: a) Mill Geometry and Speed – Bond (1954) observed grinding efficiency to be a Factors Affecting Ball Mill Grinding EfficiencyOverall, ball size and shape are important factors to consider when choosing a mill for ore grinding However, Singlestage ball mills are designed for grinding small quantities of a particular material They have one grinding chamber that holds the material to be ground and a rotating drum that does the grindingFactors affecting ores grinding performance in ball mills
.jpg)
Grinding Fundamentals PDF Mill (Grinding) Bearing
Grinding Fundamentals Free download as PDF File (pdf), Text File (txt) or read online for free Outokumpu is an expert in grinding mill design and technology, having supplied nearly 1000 mills globally over several decades They offer various mill types including rod, ball, pebble, and autogenous/semiautogenous mills Their designs focus on reliability and process optimizationBond Lowenergy Impact N/A 762 PQ/HQ N/A 25 10 Single Particle N Y Media Competency 183 165 N/A 750 300 Batch N Y MacPherson Autogenous 046 32 NQ 118 175 100 Continuous Y Y JK Dropweight N/A 63 PQ/HQ N/A 75 25 Single Particle N Y SMC Test® N/A 315 Any N/A 204 54 Single Particle N Y JK Rotary Breakage Test® 0455 53 HQ N/A 75 15 Single SAG Mill Testing Test Procedures to Characterize Ore Grindability2012年6月1日 As the cylinder starts to rotate, the grinding balls inside the cylinder crush and grind the feed material, generating mechanical energy that aids in breaking bonds, activating the catalyst, and Grinding in Ball Mills: Modeling and Process ControlGrinding steel balls are the grinding media and the core components of a ball mill They can directly affect the grinding efficiency of the whole ore processing plant and the final product quality During the grinding process, grinding steel balls are used for mixing and milling materials (such as minerals, paints, and chemicals) into fine powdersChoose the Best Grinding Steel Balls for Your Ball Mill Fote
.jpg)
Chemical composition of selected grinding media (wt%)
To work under wet grinding condition, the alloys used for ball mill liners were considered to be phase structures with high hardness, toughness and corrosion resistance [11, 26,27]2017年7月20日 Where in conventional rod and ball mill plants there are usually 3 to 4 stages of crushing followed by 1 to 3 stages of grinding, depending on ore fineness and hardness, primary autogenous plants require only one stage of crushing followed by 1 to 2 stages of grindingAutogenous Grinding Semi Autogenous Grinding Circuits2014年10月1日 In a test performed in the Loesche test center in Germany, copper slag grinding saved 229% energy in an airswept model and 344% energy in an overflow model [13,14]Copper Ore Grinding in a Mobile Vertical Roller Mill Pilot PlantRequest PDF On Mar 15, 2015, Mathis Reichert and others published Research of iron ore grinding in a verticalrollermill Find, read and cite all the research you need on ResearchGateResearch of iron ore grinding in a verticalrollermill
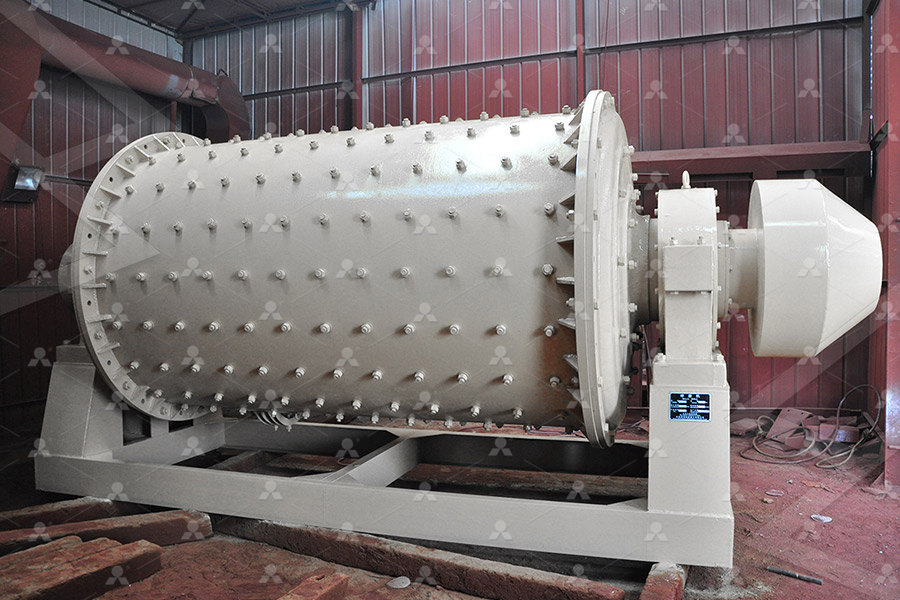
Ore Grinding SpringerLink
2023年7月20日 Therefore, the rod mill is mostly used for coarse grinding of the previous period of ball mill, or grinding of brittle materials and materials against overcrushing, such as tungsten and tin ore before gravity separation; and (3) autogenous mill – it refers to the materials which themselves are collided and ground mutually to be crushed when the grinding mill rotates, and 2022年1月1日 The size of grinding media is the primary factor that affects the overall milling efficiency of a ball mill (eg power consumption and particle size breakage)Effect of grinding media on the milling efficiency of a ball mill2012年4月17日 Effect of Slurry Density on Load Dynamic and Milling Performances in an Iron Ore Ball Mill On for grinding the iron ore in a ball mill a single lifter as it passes through the mill (PDF) Effect of Slurry Density on Load Dynamic and ResearchGate2021年11月1日 High chromium balls are recognized as better grinding media in terms of wear rates than forged steel balls, which are conventional grinding media in the milling process of iron ore(PDF) Morphology and wear of high chromium and
.jpg)
Population balance model approach to ball mill optimization in iron ore
2014年1月1日 Population balance model approach to ball mill optimization in iron ore grinding January 2014; The present work analyzes the application of recent singleparticle testing methods that are Latest news Overview of cast grinding media balls and production line operations 23 10 月, 2024 5:34 上午; Optimizing Efficiency: Exporting CuttingEdge Grinding Balls Production Lines 10 10 月, 2024 10:30 上午; Technological progress and application prospects of grinding ball production lines 26 9 月, 2024 7:36 上午; Future Manufacturing: Revealing the Innovative Comparison of casting grinding media balls forged steel balls2023年12月12日 Ore can have various properties, such as hardness, density, moisture content, etc, which can affect the ore’s productivity and grinding efficiency Discover the world's research 25+ million members(PDF) Control of ball mill operation depending on ball load and ore 2016年6月3日 The principal method of grinding in a Tower mill is attrition (scrubbing of particles off material being ground), with the possibility of some shearing and 911 Metallurgist is a trusted resource for practical insights, Tower Mill Operating Work Index 911Metallurgist
.jpg)
INVESTIGATION ON FLOTATION BEHAVIOR OF A COPPER SULFIDE ORE
2019年8月1日 Furthermore, all deposits mentioned above are located in arid regions, which restricts the application of wet processing methods An option to simultaneously limit overgrinding and save water 2018年8月8日 One of the most effective methods of grinding Portland cement is the use of an electromagnetic mill, which has proven its advantage in creating clinkerless binders [2], regulating the kinetics of (PDF) Grinding Kinetics Adjustment of Copper Ore 2013年8月1日 For example, Leppinen et al (1998) found, that depending on ore type, the potential difference (after milling) for complex sulphide ores between grinding in normal steel and stainless steel mills was about 100–250 mV, while Kelebek et al (1995) have reported differences of 500–600 mV for pyrrhotiterich coppernickel sulphide ores in the initial stages of grindingConsumption of steel grinding media in mills – A review2013年8月3日 In Grinding, selecting (calculate) the correct or optimum ball size that allows for the best and optimum/ideal or target grind size to be achieved by your ball mill is an important thing for a Mineral Processing Engineer AKA Metallurgist to do Often, the ball used in ball mills is oversize “just in case” Well, this safety factor can cost you much in recovery and/or mill liner Calculate and Select Ball Mill Ball Size for Optimum Grinding
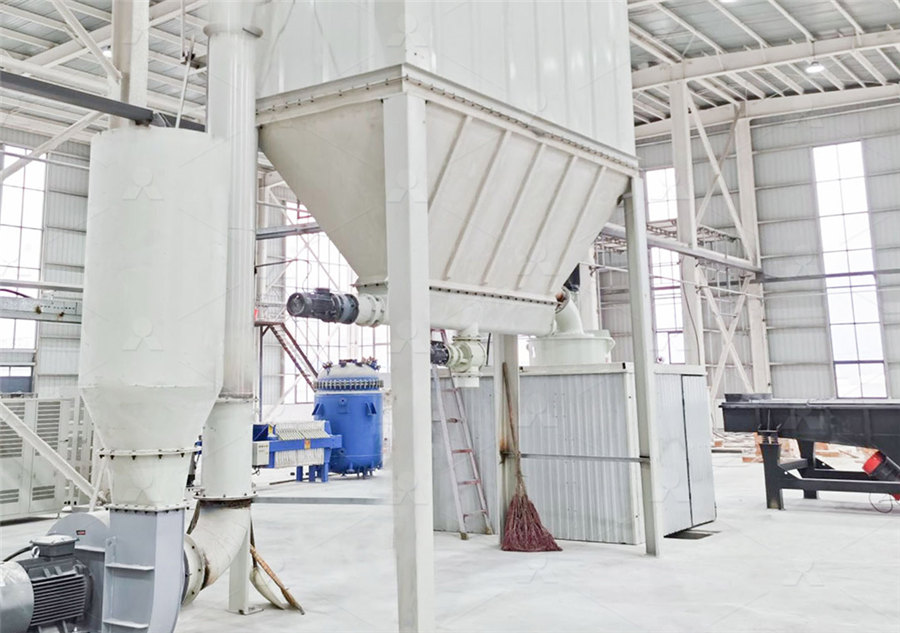
Grinding Ball Wear Breakage by Impact Abrasion Tests
2017年10月18日 The balls included forged steel, cast steel, Flaking and pitting modes do not develop normally during grinding of ore in a ball mill because abrasive wear proceeds at a faster rate Steel balls abrasion The abrasive wear of the steel balls determined from the pinon drum wear test ranged from 0577 to 1094 mm³/m2015年12月1日 Öksüzoglu and Uçurum [27] studied the ultrafine grinding of gypsum ore in a dry ball mill In their grinding tests, the mill speed was varied from 50 to 90% of the critical speed for gypsum oreAn experimental study on the ultrafine grinding of gypsum ore 4 天之前 Additionally, the ball mill’s versatility allows parameters such as speed, feed rate and material composition to be adjusted, making it adaptable to different types of lithium ore This flexibility is essential to optimize the grinding process for each specific ore type, thereby increasing cost efficiency and resource sustainabilityBall Mill Is The Key To Grinding Lithium Ore JXSC Machinery2020年7月24日 This paper presents results regarding the grinding behaviour of two batches of material (clinker) in a ball mill with its own twostep grinding process: the first one with a ball load, the second Determination of granulometrical composition of the clinker by grinding
.jpg)
Understanding the Science Art of Grinding Media Selection in
2023年10月16日 Replenishing the grinding media can be done with either singlesize media or with a balanced ball charge consisting of various sizes, corresponding to the particle size distribution of the mill