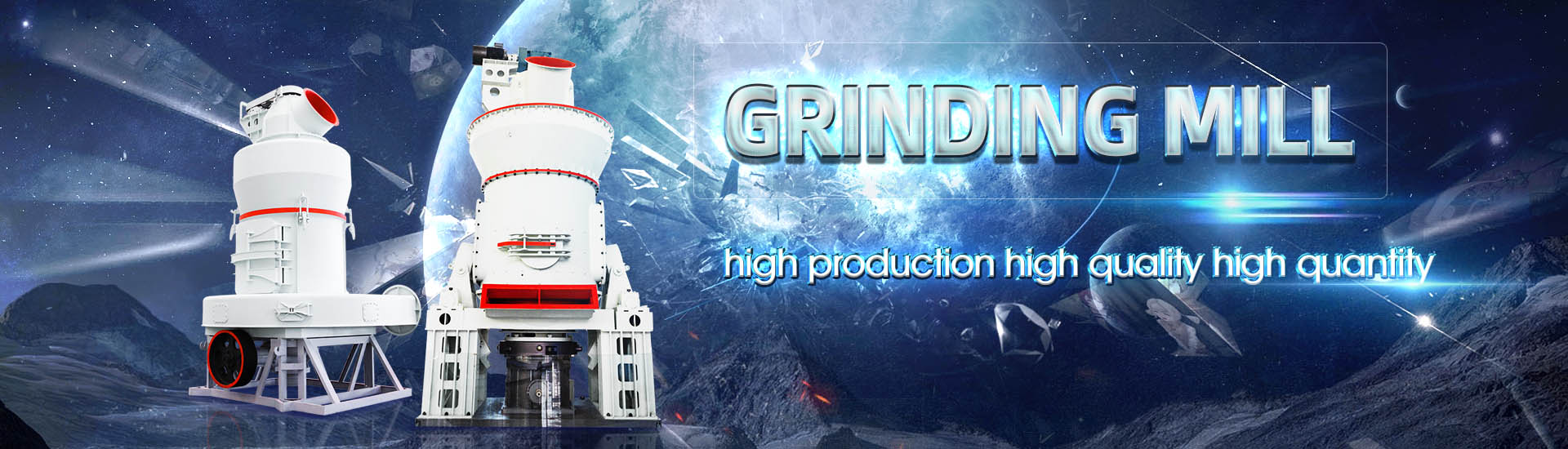
Where to use inertial ore grinding mill
.jpg)
Grinding Mills — Types, Working Principle Applications
2018年8月17日 SemiAutogenous Mills/ SAG Mills (primary grinding mill) — these mills use grinding balls with forces of attrition, impact, and abrasion between grinding balls and ore particlesIn the iron ore industry, most of the machines are found in pellet feed applications However, there are a few notable examples where HPGRs are used for coarse iron ore grinding – in High Pressure Grinding Rolls for Minerals AusIMM• Small media size, essential to increase grinding efficiency for fines • The use of inert grinding media This can deliver dramatic improvements to flotation kinetics and recovery, and Fine Grinding as Enabling Technology – The IsaMillBrowse Metso's wide offering of reliable grinding mills: AG mills, SAG mills, ball and pebble mills, and stirred mills to fit your needs Our pioneering innovations in horizontal grinding mills technology offer exceptional performance and Grinding mills for mining and minerals processing
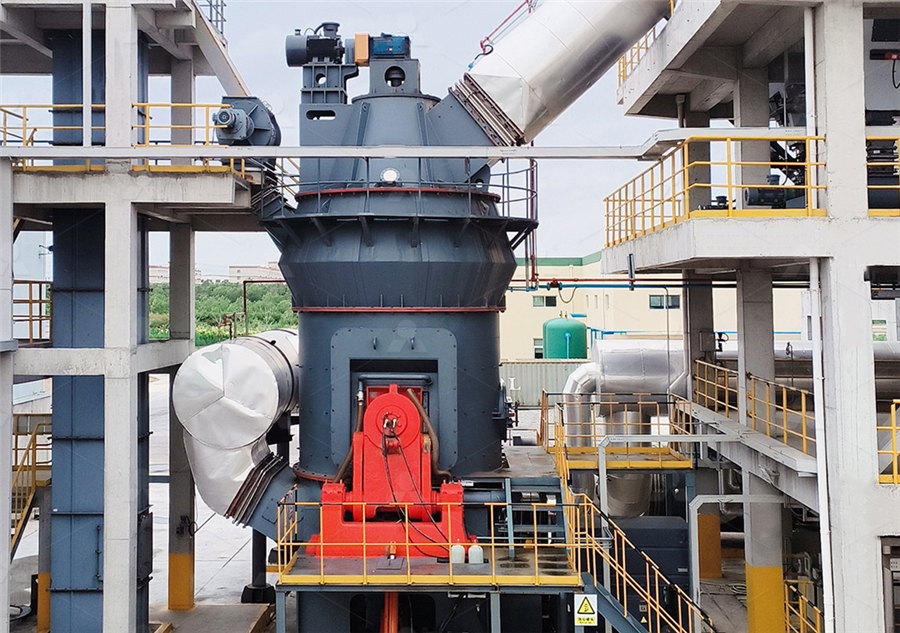
Our Dynamic HPGR Technology for Mineral Grinding
Enduron® high pressure grinding rolls (HPGR) can handle a wide variety of ores and particle sizes from fine pellet feed all the way up to coarse grinding of 75mm magnetite iron oreAccording to the ways by which motion is imparted to the charge, grinding mills are generally classified into two types: tumbling mills and stirred mills In tumbling mills, the mill shell is Grinding Mill an overview ScienceDirect TopicsTo allow quick and simple removal of the grinding chamber to expose the mill internals for maintenance purposes, the shaft is counterlevelled at the feed inlet end The grinding discs ISAMILL FINE GRINDING TECHNOLOGY AND ITS INDUSTRIAL Customized grinding mill parts including heads, shells, trunnions and liners, main bearings, gears and pinions, and more! Metallic, PolyMet™, Megaliner™, Rubber and Orebed™ mill liners for Grinding Metso
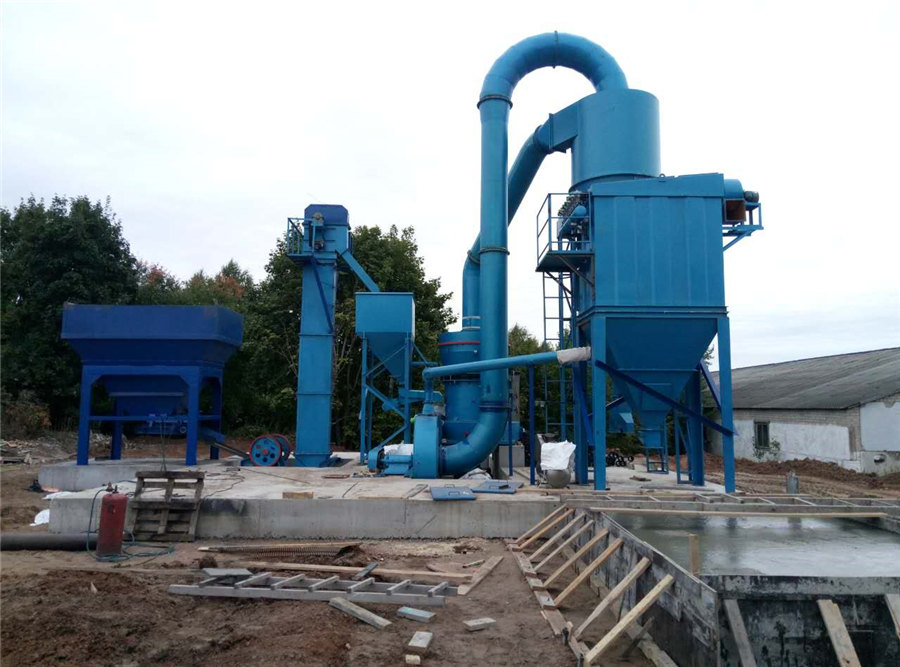
Mills for minerals and ores Loesche
The dry milling of ore in LOESCHE vertical roller mills has shown significant process advantages, as well as economic and ecological benefits To demonstrate these a mobile oregrinding plant the OGPmobile has been 2023年7月20日 Ore grinding is completed in the cylinder of the grinding mill With a certain amount of grinding medium in the cylinder, when the cylinder rotates, the grinding medium is Ore Grinding SpringerLink2016年6月6日 Mill operating conditions including mill speed (for circuits with variablespeed drives), density, and total mill load; The effect of feed hardness is the most significant driver for AG/SAG performance: with variations in ore SAG Mill Grinding Circuit Design 911Metallurgist2014年1月1日 Experimental and fitted breakage functions for wet grinding in 254 cm diameter mill Population balance model approach to ball mill
.jpg)
Grinding in an air classifier mill Part I: Characterisation of the
2011年7月1日 The crusher uses a more efficient method of grinding feed grain a combination of impact and cutting, in contrast to a hammer mill that grinds with a free impact of hammersManufacturing metals requires the ore grinding mill, which is unlocked at the same time as the ore mines You’ll find the ore grinding mill under Processing Buildings (the two gears icon) Place one within your industry area It’ll take a little while, but eventually the trucks from your ore mines and sand storage will start delivering ore Complete Ore Industry Area Guide for Cities: SkylinesFind your ore mill easily amongst the 42 products from the leading brands (Fritsch GmbH, Retsch, Eriez, ) on DirectIndustry, the industry specialist for your professional purchases Exhibit with us Ball mill is common used grinding plant in the industry, Ore mill, Ore grinding mill All industrial manufacturersRequest PDF On Mar 15, 2015, Mathis Reichert and others published Research of iron ore grinding in a verticalrollermill Find, read and cite all the research you need on ResearchGateResearch of iron ore grinding in a verticalrollermill
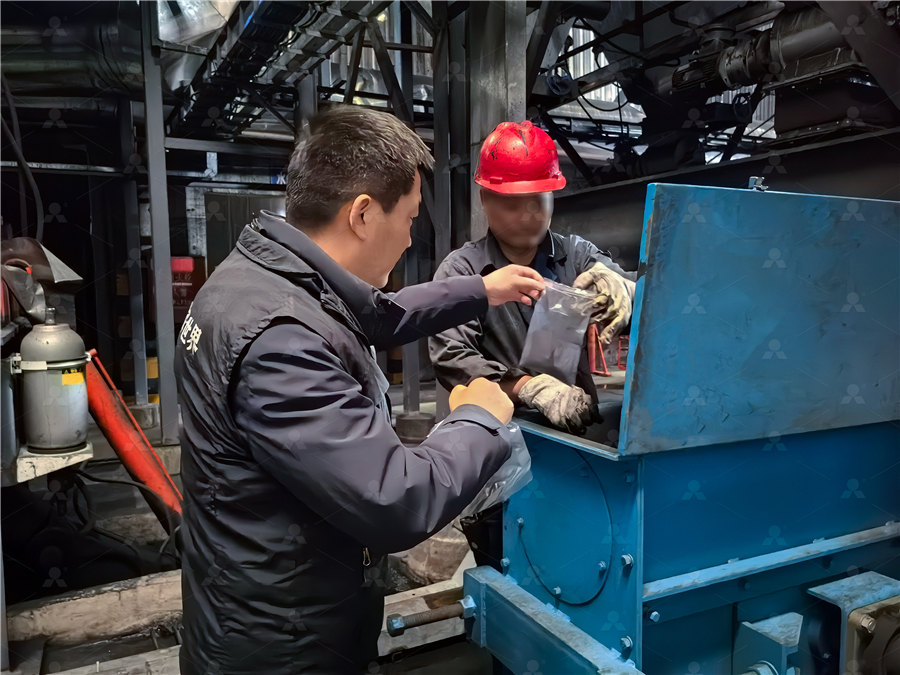
Grinding Mill Liners 911Metallurgist
2015年8月6日 There are basically two groups of Grinding Mill Liners Ones with a HIGH PROFILE and those with a LOW PROFILE The high profile liner is designed to give the The amount of unground material will slowly increase until the mill can no longer grind the bigger ore2013年8月3日 In Grinding, selecting (calculate) the correct or optimum ball size that allows for the best and optimum/ideal or target grind size to be achieved by your ball mill is an important thing for a Mineral Processing Engineer AKA Metallurgist to do Often, the ball used in ball mills is oversize “just in case” Well, this safety factor can cost you much in recovery and/or mill liner Calculate and Select Ball Mill Ball Size for Optimum Grinding2023年7月20日 Therefore, the rod mill is mostly used for coarse grinding of the previous period of ball mill, or grinding of brittle materials and materials against overcrushing, such as tungsten and tin ore before gravity separation; and (3) autogenous mill – it refers to the materials which themselves are collided and ground mutually to be crushed when the grinding mill rotates, and Ore Grinding SpringerLink2017年1月17日 Other process activities, such as spraying the ore with water for dust control or the fact that runofmine ore moisture is approximately 2%5% are not generally considered (Bleiwas, 2012a)Breaking down energy consumption in industrial grinding mills
.jpg)
Operating a Grinding Circuit How to Operate
2015年7月29日 Very simply put, any difficulty experienced in grinding the ore will be due to one of the following The size of the incoming feed, the work index of the ore, (if you remember this is the amount of work it takes to grind the • Small media size, essential to increase grinding efficiency for fines • The use of inert grinding media This can deliver dramatic improvements to flotation kinetics and recovery, and improved leaching leaching rates and chemistry Stirred milling was developed for fine grained ores that required an economic grind to sub 10 micron sizesFine Grinding as Enabling Technology – The IsaMill2019年8月14日 • Grid ball mill: Discharge the ore through the plaid plate When the nonsmooth ball mill liner is used, the grinding ball filling ratio is 4050%, and the grinding concentration is relatively large, the calculation result of the formula is The Ultimate Guide to Ball Mills MiningpediaIn the mill, the mixture of medium, ore, and water, known as the mill charge, Grinding uses a rotating wheel called a grinding wheel for this purpose, which has abrasive grains held by a binder (Figure 467) [54] These abrasive grains act like sharp tools that remove material from the Grinding Mill an overview ScienceDirect Topics
.jpg)
Grinding in Ball Mills: Modeling and Process Control
2012年6月1日 is charged with the starting material (ore, rock, etc) and the grinding media (balls), 52 approach is most frequently used in ball mill grinding circuits The main advantage 2013年4月1日 A simple and novel nonlinear model of a runofmine ore grinding mill circuit, developed for process control and estimation purposes, is validatedAnalysis and validation of a runofmine ore grinding mill circuit 2024年5月17日 A SAG (SemiAutogenous Grinding) mill is a giant rotating cylinder filled with grinding media and the ore being reduced As the mill rotates, the grinding media lifts and the impact crushes the feed material SAG mill control refers to the practice of managing the mill load, which is the amount of material inside the mill at any given timeA guide to SAG Mill managementFigure 2 compares the power consumption of a laboratory ball mill to a UFG mill in grinding KCGM concentrate Figure 2 Comparison of Grind Product Sizes The use of UFG grinding in the minerals processing industry is a relatively new development being based on the smaller low mass, batch UFG mills being used by other industries for high value Ultra Fine Grinding A Practical Alternative to Oxidative
.jpg)
MeasurementBased Modelling of Material Moisture and
2021年1月19日 The experimental setup involves an inertialimpingement classifier and cyclone being part of dry grinding circuit with electromagnetic mill and recycle of coarse particles The tested granular material is copper ore of particle size 0–125 mm and relative moisture content 05–5%, fed to the installation at various rates2023年4月23日 grinding media in a grinding mill with about 2630 wt% chrome by Chen et al [37] using a phosphate ore in a modified ball laboratory ball mill whose electrochemical potential could be controlled(PDF) Grinding Media in Ball MillsA Review ResearchGate1 Population balance model approach to ball mill optimization in iron ore grinding Patricia M C Faria1,2, Luís Marcelo Tavares2 and Raj K Rajamani3 1 Vale SA, Brazil 2 Department of Population balance model approach to ball mill optimization in iron ore 2017年7月20日 Where in conventional rod and ball mill plants there are usually 3 to 4 stages of crushing followed by 1 to 3 stages of grinding, depending on ore fineness and hardness, primary autogenous plants require only one stage of Autogenous Grinding Semi Autogenous Grinding
.jpg)
How to choose a suitable ore powder grinding mill?
2023年10月17日 Factors for choosing a suitable ore powder grinding mill 1 Raw material characteristics: Different raw materials have different hardness, humidity and grinding and crushing properties, and the corresponding ore 2013年12月31日 Some of them use the standard mill, while others are based on a nonstandard mill or computation techniques The grinding of ore is a highly energyintensive process [1] [2][3][4]A developed approach based on grinding time to determine ore 2015年3月10日 Vertical roller mills (VRM) have been used extensively for comminuting both cement raw materials and minerals like limestone, clinker, phosphate, manganese, magnesite, feldspar and titanium These mills combine crushing, grinding, classification and drying operations in one unit and have advantages over conventional machines and literature reports that 15% Copper ore grinding in a mobile vertical roller mill pilot plantKeywords—electromagnetic mill, grinding process, hierarchical control, process optimization I Technology: 1 – electromagnetic mill, 2 – inertial separator, 3 – cyclone Fig 3 General structure of the hierarchical control system presents example of cumulative grain content of copper ore being grinded in electromagnetic millPower optimizing control of grinding process in electromagnetic mill
.jpg)
Ore Grinding mill doesnt have resources even though its right
You might be producing more ore than you sand storage fits when set to balance Build another sand storage nearby/next to your grinding mill and set this one to fill That way your new sand storage won’t run out of trucks and should be ready to deliver when your mills need it2013年12月18日 Fine grinding, to P80 sizes as low as 7 μm, is becoming increasingly important as mines treat ores with smaller liberation sizes This grinding is typically done using stirred mills such as the Isamill or Stirred Media Detritor While fine grinding consumes less energy than primary grinding, it can still account for a substantial part of a mill’s energy budget Overall Energy Use of Fine Grinding in Mineral ProcessingOne contribution to minimise the increase is to use more efficient comminution equipment Verticalrollermills (VRM) are an energyefficient alternative to conventional grinding technology One reason is the dry inbed grinding principle Results of extensive test works with two types of magnetite iron ores in a Loesche VRM are presented hereResearch of iron ore grinding in a verticalrollermill2022年9月1日 The use of chemical additives is one of the most common ways of pretreating ore before grinding (Chipakwe et al, 2020, Prziwara et al, 2019) The energy required for dry grinding can be reduced using surface active compounds such as grinding aids, which are widely used in industrial dry fine grinding processes, such as by the cement sectorTowards waterless operations from mine to mill ScienceDirect
.jpg)
Effect of Water Density on Grinding Mill 911Metallurgist
2015年7月29日 The more water that is added, the faster the ore will go through the mill This means the time it has to be ground will be reduced and a poor grind will result At the other extreme, if not enough water is used, the ore will not be able to flow through the mill The result is the ore will not be able to move into the rod load Because there isn 2020年6月3日 The design of such grinding mills is extremely critical, requiring sophisticated software tools, proprietary calculation worksheets, and experienced technical engineers and drafters This blog will review how the mill design How grinding mill design changed over the last 30 yearsThis paper looks at the past, present and not too distant future of grinding mill reliningSince the adoption of autogenous grinding (AG) mills and semiautogenous grinding (SAG) mills as the primary ore reducing devices in the comminution circuit, plant shutdown frequency and duration has largely been driven by the liner maintenance requirements of these millsThe past 30 14th AusIMM Mill Operators' Conference 2018Dry grinding in electromagnetic mill: 1 – Feed stream, 2 – Vertically aligned working chamber, 3 – Workspace with grinding media, 4 – Main stream of gaseous medium, 5 – Final product, 6 Assessment of classification with variable air flow for inertial
.jpg)
Research of iron ore grinding in a verticalrollermill
2015年3月15日 For the grinding tests, a Loesche mill LM45 (table diameter 045 m) is used (Fig 2a) This pilot scale mill is a special development for ore grinding, which is reflected by several features The mill has four rollers, which are able to stress the particle bed with grinding pressures of up to 5000 kN/m 22016年4月22日 In all ore dressing and milling processes, including flotation, cyanidation, gravity concentration, and amalgamation, it is necessary to crush and grind, often with rob mill ball mills, the ore in order to liberate the minerals In the chemical and process industries, grinding is an important step in preparing raw materials for subsequent treatmentBall Mill Rod Mill Design 911Metallurgist2017年8月26日 One of the most difficult tasks is the direct establishment of contribution of corrosion wear An indirect method of measuring corrosion contribution is to compare steel wear in wet and dry grinding Metal loss per ton of ore ground is higher in wet grinding than in dry grinding for a typical ore of average work index 13 kWh/tHow to Reduce Steel Consumption in Grinding Mills2018年8月17日 Extreme temperatures, impact velocity, mill load, grinding media, ore types, and applications are some of the factors to be considered while installing new linersGrinding Mills — Types, Working Principle Applications
.jpg)
Grinding Modeling and Energy Efficiency in Ore/Raw Material
2022年8月31日 The order of influencing factors of the two ores is as follows: grinding time > filling ratio > grinding concentration For Tongkeng ore, the optimized grinding conditions are grinding time 54 min, grinding concentration 67% and filling ratio 35% For Gaofeng ore, the optimized grinding conditions are grinding time 38 min, grinding When iron ore is extracted from a mine, it must undergo several processing stages Six steps to process iron ore 1 Screening We recommend that you begin by screening the iron ore to separate fine particles below the crusher’s CSS before the crushing stage A static screen is used to divert the fine particles for crushingThe six main steps of iron ore processing Multotec