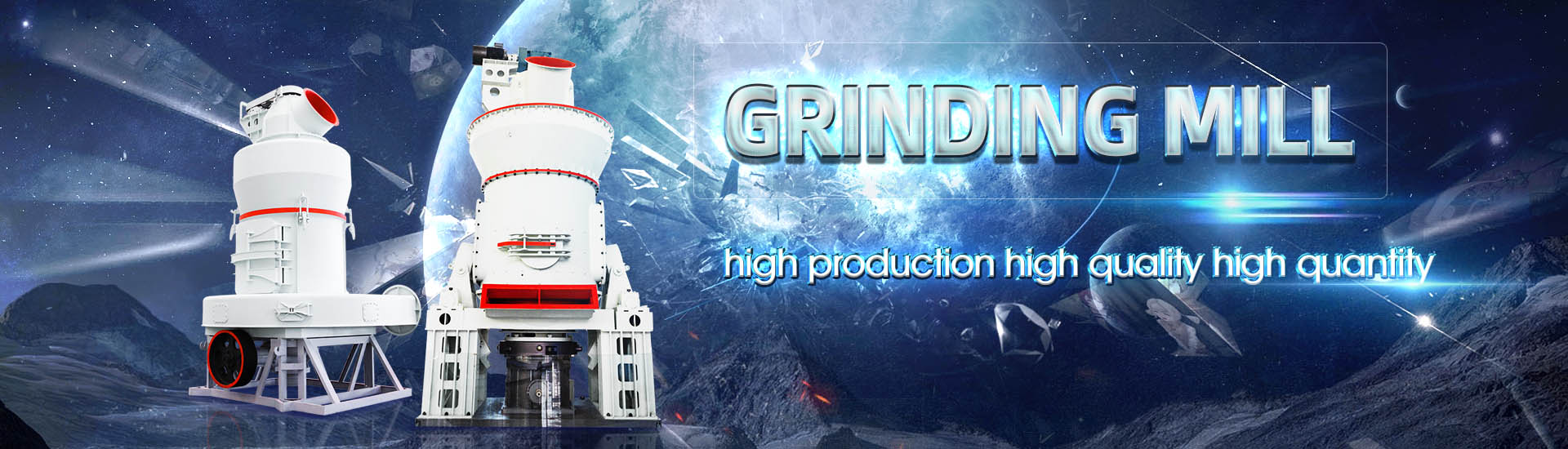
Cement grinding equipment parameters
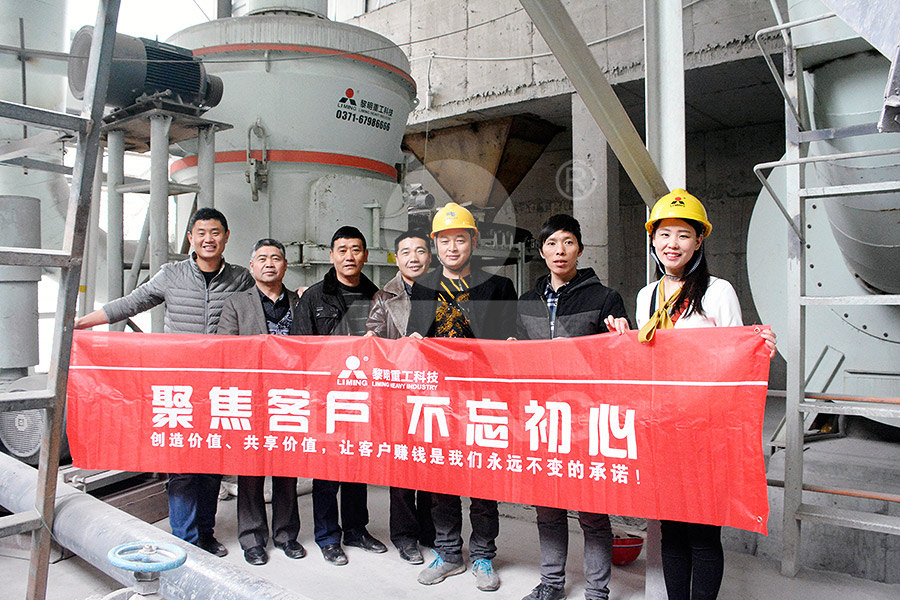
OPTIMIZATION OF CEMENT GRINDING OPERATION IN BALL MILLS
Results of the optimization can be measured by multiple parameters such as separator efficiency, specific power consumption, system throughput, and wear rate of grinding media and linersHighly energy intensive unit operation of size reduction in cement industry is intended to provide a homogeneous and super fine (30004000 Blain) cement Grinding operation is monitored for Cement Grinding Cement Plant OptimizationAs grinding accounts for a sizeable share in a cement plant’s power consumption, optimisation of grinding equipment such as ball mills can provide significant cost and CO 2BALL MILLS Ball mill optimisation Holzinger Consulting2004年11月1日 There is potential to optimise conventional cement clinker grinding circuits and in the last decade significant progress has been achieved The increasing demand for “finer Cement grinding optimisation ScienceDirect
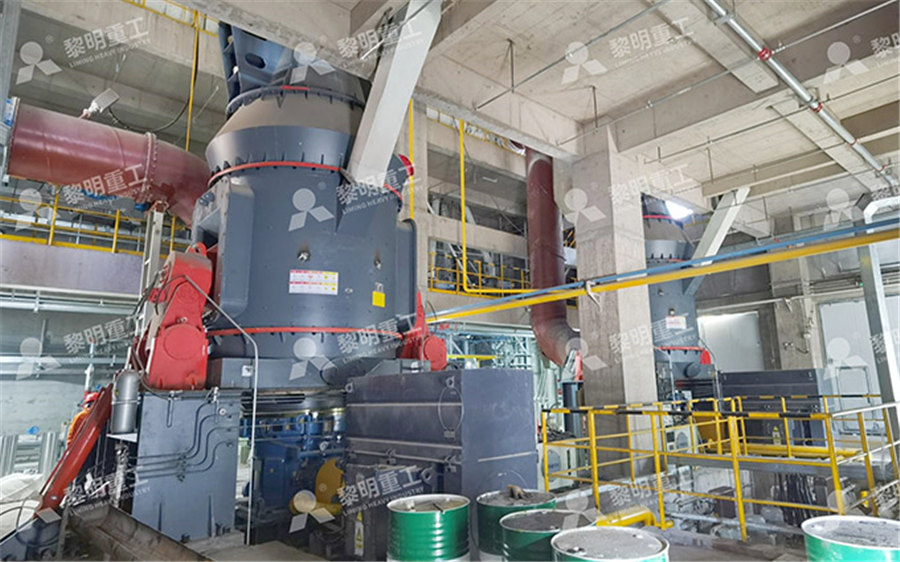
Operational parameters affecting the vertical roller mill
2017年4月1日 Vertical roller mills (VRM) have found applications mostly in cement grinding operations where they were used in raw meal and finish grinding stages and in power plants 2018年7月1日 This study aimed at improving both the energy efficiency and product quality of the end product for a given cement grinding circuit by applying an accurate sampling Energy and cement quality optimization of a cement grinding circuit2019年1月1日 The basic process parameters in grinding processes are the cutting speed v c, the feed velocity v f, the depth of cut a e, and the width of cut a p (see Fig 1, see also Denkena and Tönshoff 2011) The cutting speed is in Grinding Parameters SpringerLink2017年5月19日 The laws of solids grinding and equations to estimate the parameters of particle size distribution, which determine the properties of cement important from the practical point of view areOverview of cement grinding: fundamentals, additives,
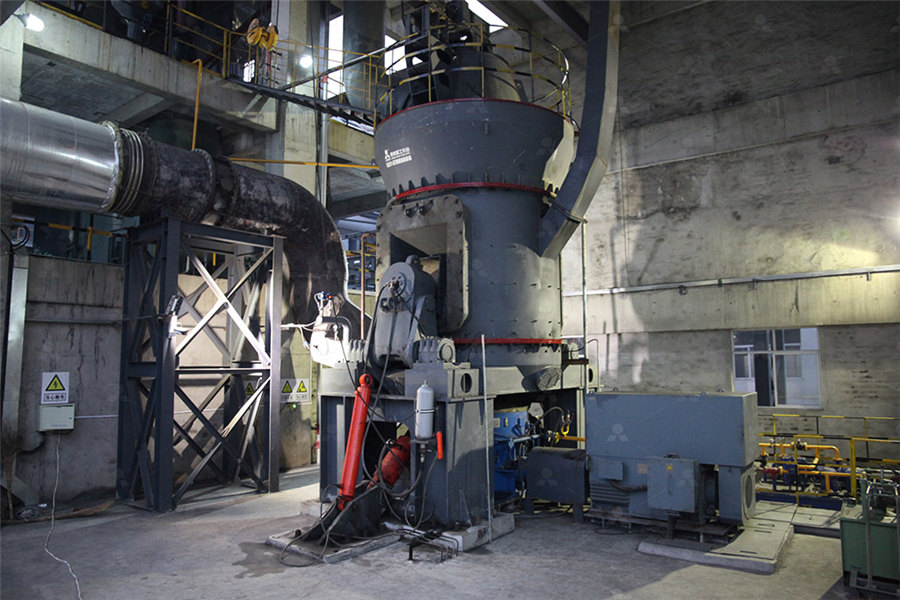
EnergyEfficient Technologies in Cement Grinding
2016年10月5日 In this chapter an introduction of widely applied energyefficient grinding technologies in cement grinding and description of the operating principles of the related equipments and comparisons over each other in case study, in this case, a cement grinding plant The study provides a pragmatic reference model framework to practitioners that enhances maintenance decisionmaking by identifying critical Maintenance Performance Optimization for Critical Subsystems in Previous Post Next Post Contents1 Kiln Control and Operation2 1 INTRODUCTION3 1 CONTROL PARAMETERS31 11 Location of the control parameters and variables311 111 Wet kiln312 111 Lepol kiln313 111 Kiln Control and Operation INFINITY FOR CEMENT 2024年11月18日 Prof Dr A Hakan Benzer, Onur Atakay, Volkan Cebeci, Minerva Engineering, and Hakan Dündar, Hacettepe University, provide a case study showing how the application of stirred milling technology enhances cement Optimising Stirred Milling Technology World Cement
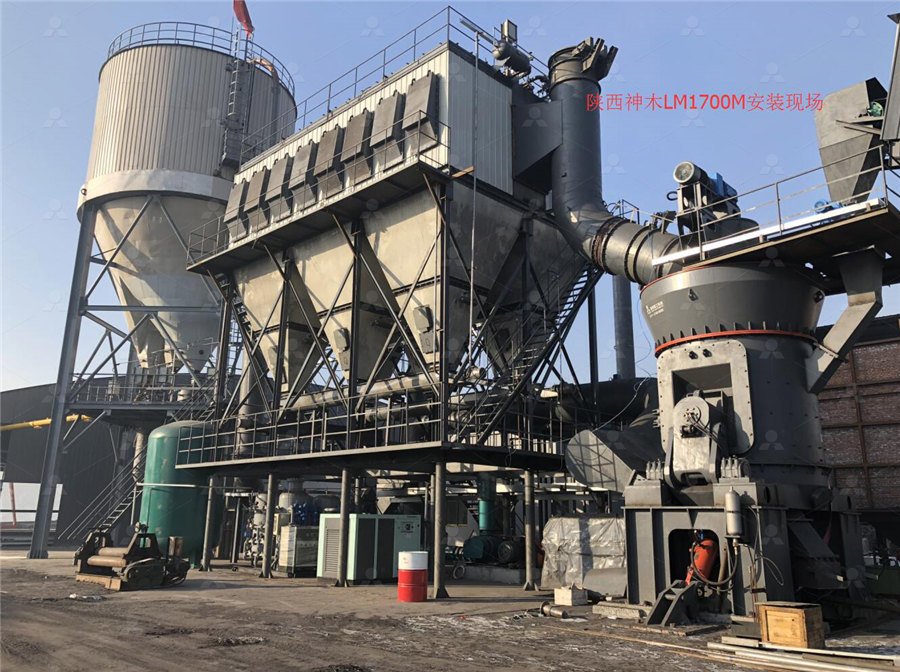
Overview of cement grinding: fundamentals,
2017年5月19日 Grinding is an essential operation in cement production given that it permits to obtain fine powder which reacts quickly with water, sets in few hours and hardens over a period of weeks i Types of Cement Kilns: Overview of wet, dry, semidry, and semiwet process kilns Components of a Cement Kiln: Detailed examination of the rotary kiln, preheater, precalciner, and cooler Kiln Operation and Optimization: Key operational parameters, energy efficiency techniques, and emission control prehensive Guide to Cement Kilns: Processes, Types, 2024年8月23日 ICR explores the details of the grinding process, which is a critical stage in cement manufacturing, which significantly impacts the final product’s quality and characteristics By finely grinding raw materials into clinker and mixing them with gypsum, cement manufacturers ensure the fineness and uniformity essential for strong and durable cement The grinding From Clinker to Cement Indian Cement ReviewEquipment: Ball Mills, Vertical Mills, Separators; Grinding process theory and fundamentals; Ball vertical mill systems and equipment components; Process design basic parameters; Control loops regulation; Process and operations troubleshooting; Key process and quality performance indicators and influencers§Process calculations; OptimizationCement Production Seminar: Grinding
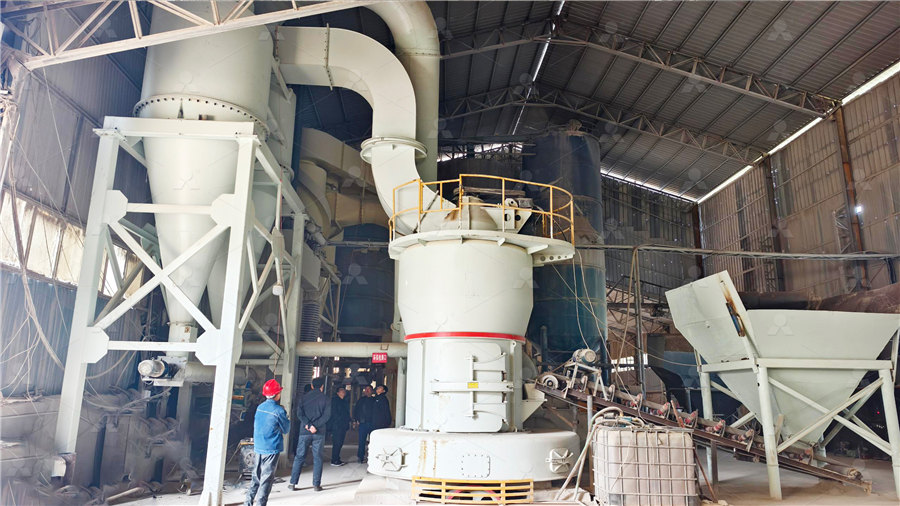
Innovation and optimisation in cement grinding
• Cement grinding 38 % • Conveying, packing, loading 5 % 100 % total demand ~ 110 kWh/tcement more than 60 % for grinding processes! *all* Grinding and its impact on quality Cement grinding as an example: quality parameters: • workability • water demand • strength • durability of concrete2021年4月19日 Grinding of finished cement is performed in a single stage, intergrinding materials with very different grindabilities This intergrinding process has many different interactions among the different components of the finished cement In a context of developing more sustainable and less energy intensive processes, it is important to understand the Resistance to Grinding and Cement Paste Performance of Blends Previous Post Next Post Contents1 Ball charge optimization2 1 How to use the BP21 2 Description of the main indicators used in this BP2101 The residue on 2mm/4mm before partition wall2102 Material filling level and ball charge expansion211 Cement mill specific power 1st compartment 212 Raw mill specific power 1st compartment Ball charge Ball charge optimization INFINITY FOR CEMENT EQUIPMENT2023年12月26日 As we all know, the dryprocess cement production line is commonly used in the cement industry The new type of dryprocess cement production process includes four main sections: Prehomogenization of raw materials, homogenization of raw materials, clinker firing, cement grinding, etc Raw material conveying system The raw material, including limestone, 6 Cement Equipment For Dryprocess Cement Production Line

Cement Seperator for Cement Grinding System
Application: In cement industry production, in order to improve the efficiency of the grinding system and reduce the energy consumption of the product, a circulating grinding system is now widely used As an important part of the Fine Grinding and Mill Cooling PROBLEM Insufficient mill cooling lead to material agglomeration on balls and liners The grinding is not any more done by balls against material but by material against material SOLUTION Adapted EVERY COMPONENT OF BALL MILL DETAILEDVertical roller mills and ball mills represent two clearly distinct technologies However, with proper adjustments to the operational parameters of the vertical roller mill almost identical cement properties can be achieved by the two mills Cement grinding Vertical roller mills VS ball mills2013年5月1日 Grinding, a complicated machining process which has been extensively studied and documented in order to understand the subtleties of the operation being performed in different methodologies and Influence of Process Parameters on Grinding A Review
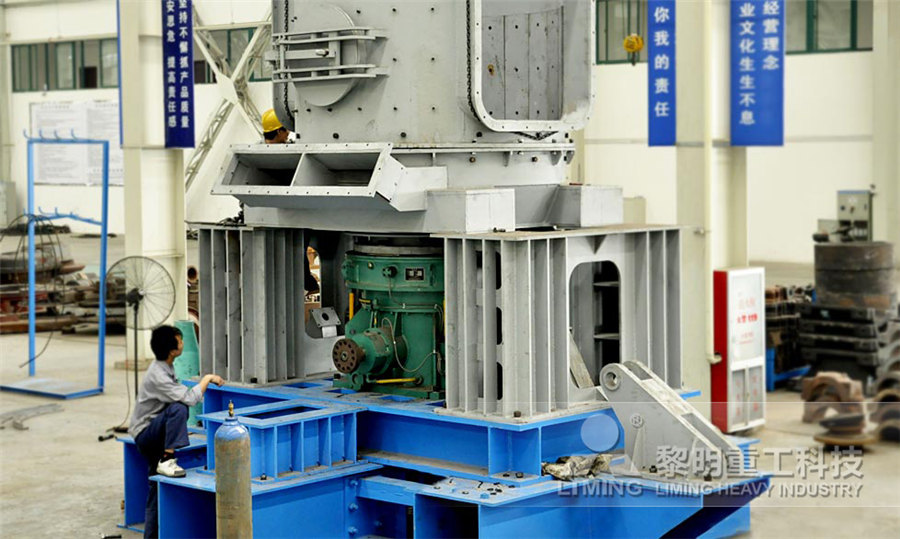
Parameters for the Grinding Process in Vertical Mills Using Gob
the cement grinding process, in order to obtain better efficiency with the lowest consumption of electrical energy, in addition, it is necessary to take into account certain operating parameters to guarantee a quality product Most of the works related to energy consumption vary a single parameter at a time, propose models, makeThe vertical roller mill (VRM) is a type of grinding machine for raw material processing and cement grinding in the cement manufacturing processIn recent years, the VRM cement mill has been equipped in more and more cement plants around the world because of its features like high energy efficiency, low pollutant generation, small floor area, etc The VRM cement mill has a Vertical Roller Mill Operation in Cement Plant2016年10月5日 In this chapter an introduction of widely applied energyefficient grinding technologies in cement grinding and description of the operating principles of the related equip‐ ments and comparisons over each other in terms of grinding efficiency, specific energy consumption, production capacity and cement quality are given A case study per‐ formed on a EnergyEfficient Technologies in Cement GrindingAGICO CLM Series high pressure grinding rolls (HPGR) are efficient and energysaving crushing equipment that can be widely used in crushing and grinding operations in cement, chemical, mining, metallurgy, and other industriesAGICO High Pressure Grinding Roll (HPGR) AGICO Cement Plant
.jpg)
Clinker Grinding Techniques in Cement Manufacturing JM
2023年10月19日 They are used less frequently than other grinding equipment in the cement industry AirSwept Mills: Adjust grinding parameters as needed to compensate for these variations Blend Clinkers: If possible, blend different clinker sources to achieve a more consistent feed to the grinding processFor company control matters and for the training of the operators it is helpful to note down the process parameters in a log book every hour Beside start – stop time and any problems in the grinding plant the following parameters are recommended for being entered the log sheet:feed rate to the mill, production rate (t/h]PROCESS TRAINING for operators of Vertical RAW Mills2023年8月21日 Tushar Khandhadia, General Manager – Production, Udaipur Cement Works, discusses the role of grinding in ensuring optimised cement production and a high quality end product How does the grinding process Grinding process is a critical stage in cement productionSurvey of compound and closed circuit mills Virtually all the cement produced in the United States is ground in closed circuit grinding mills; ie finished cement grinding mills with a yearly produc tion capacity in 1982 of approximately 104 Grinding in closed circuit INFINITY FOR CEMENT
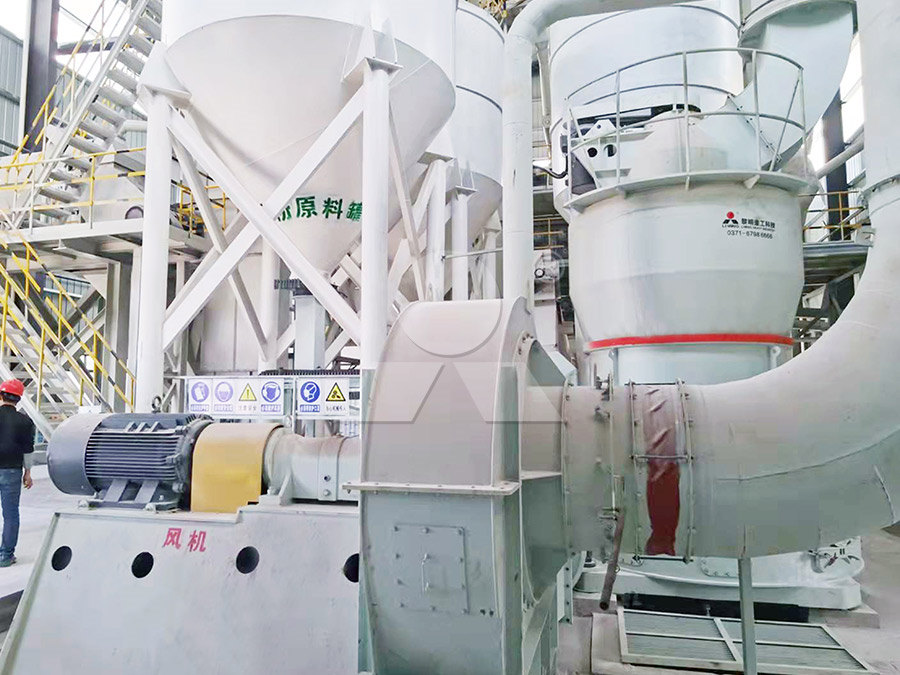
VRM In Cement Plant Maximize Energy Saving CNBMSINOMA
Vertical roller mill manufacturers Vertical roller mill or VRM is a largescale grinding equipment designed for pulverizing cement raw meal, cement clinker, slag, coal, fly ash, limestone, and other hard grinding materialIt integrates grinding, drying, separation, and conveying in one machine The equipment is widely used in many industries such as cement, electric power, metallurgy Adjusting mill parameters: Finetuning mill parameters such as mill speed, ball charge, filling ratio, and grinding media size can have a substantial impact on the grinding efficiency of the mill For example, a 10% increase in mill speed can result in up to 10% higher production rate, while optimizing the ball charge can lead to a 510% reduction in energy consumptionCement Mill Optimization: Practical Strategies for Enhanced 4 Comments / CEMENT GRINDING / By admin Previous Post Next Post Contents BALL MILL INSPECTION PROCEDURES CLICK HERE NOW TO DOWNLOAD MOST IMPORTANT BOOKS IN CEMENT INDUSTRY + PRACTICAL EXCEL SHEETS TO HELP YOU IN YOUR DAILY WORK – Actual operation parameter of the main equipment BALL MILL INSPECTION PROCEDURES INFINITY FOR CEMENT EQUIPMENTBall mill is the cement crushing equipment in the cement plant Compared with open circuit ball mill, the closedcircuit ball mill has high efficiency, high output, low cement temperature, and good comprehensive benefit It is the best choice for a cement plantBall Mill In Cement Plant Cement Ball Mill AGICO Cement
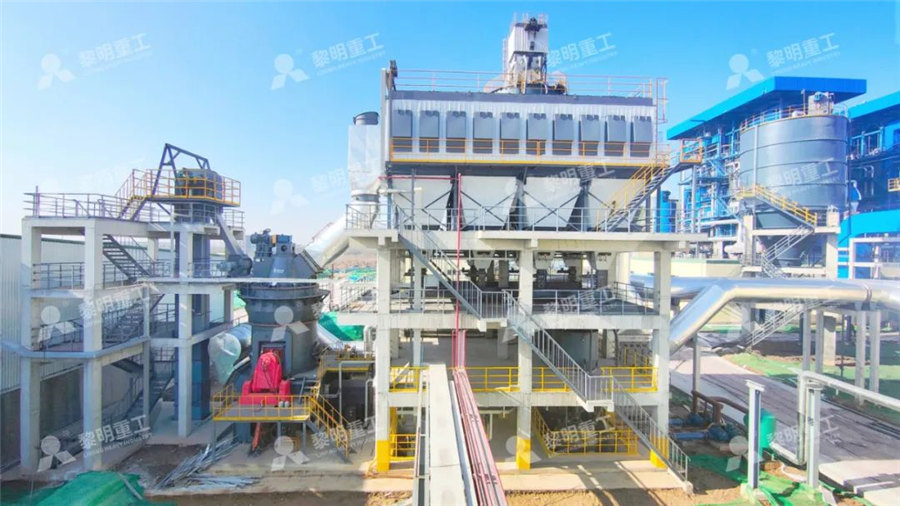
Hydraulic Roller Press in Cement Plants AGICO Cement Equipment
The cement roller press is a type of material crushing machine which is often used in cement plants It usually works together with a ball mill to form a pregrinding or finalgrinding system for the grinding of raw materials, coal, and clinker Compared with the traditional tube mill and ball mill, the roller press has lower energy consumption and higher production efficiency, Cement Ball Mill Structure When Ball Mill is working, raw material enters the mill cylinder through the hollow shaft of the feed The inside of the cylinder is filled with grinding media of various diameters (steel balls, steel segments, etc); when the cylinder rotates around the horizontal axis at a certain speed, Under the action of centrifugal force and friction force, the medium and the Ball Mill for Cement Grinding ProcessComminution of cement raw materials cannot be completely performed by autogenous grinding Therefore grinding media are employed in an amount comprising approximately 612 % of the mill volume With the auxiliary charge of grinding media, a better reduction by impact can be achieved The grinding balls used are of 100130 mm diameterDrying of raw materials INFINITY FOR CEMENT EQUIPMENTSubsystems in Cement PreGrinding Section: A Case Study Approach 1 Introduction Today’s cement manufacturing firms face unin tended machine downtimes and high maintenance costs, landing to a struggle to sustain their market shares The quality and output of grinding and milling operations greatly depend on the availability andMaintenance Performance Optimization for Critical Subsystems in Cement
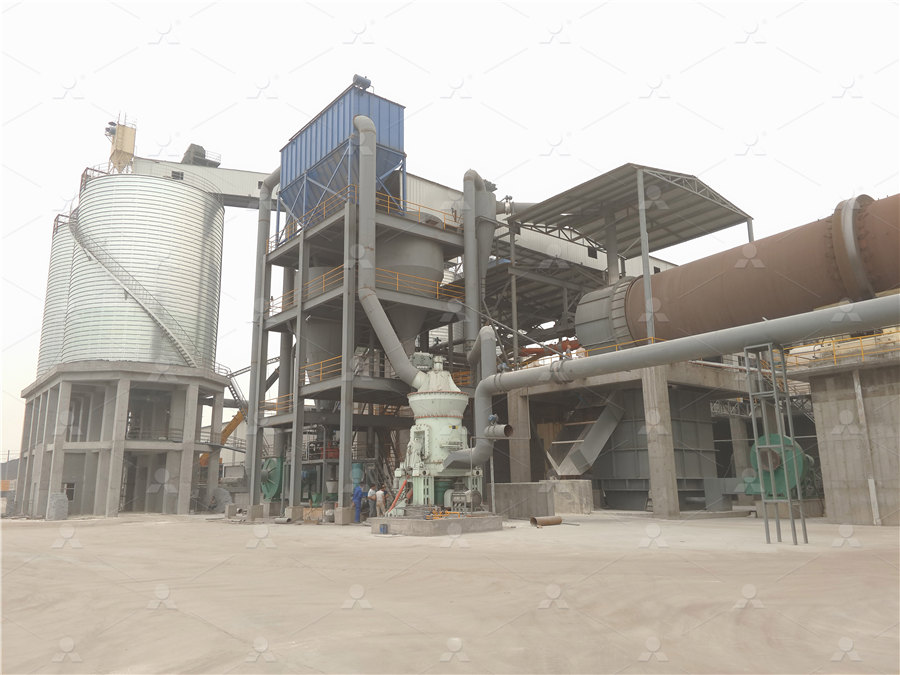
CRUSHING AND GRINDING SEMINAR The Cement
The purpose of the training is to Identify and understands necessary known and unknown information towards the completed cycle of the crushing and grinding system Throughout the course the lectures are supplemented with exercises Previous Post Next Post AIR SEPARATORS 40 AIR SEPARATORS 41 Introduction Separators are utilized in a closed circuit grinding system for the purpose of separating (classifying) the fine and coarse particles of the feed The fine particles are passed through the separator to become finished product while the coarse particles are returned to the AIR SEPARATORS INFINITY FOR CEMENT EQUIPMENT2022年1月23日 This work concentrates on the energy consumption and grinding energy efficiency of a laboratory vertical roller mill (VRM) under various operating parameters For design of experiments (DOE), the response surface method Analysis and Optimization of Grinding Performance of 2023年11月21日 Sensors and data acquisition devices will be widely used in production lines to monitor realtime parameters during the production process to Innovation of grinding equipment Efficient and energysaving new grinding equipment such as vertical cement mills and cement roller presses will become more popular to reduce energy Trend Analysis Of Cement Production Line Design Cement Equipment
.jpg)
Grinding Solutions Indian Cement Review
2015年1月31日 From hubandspoke model to split grinding; from singlegrinding solution to a combination of system solutions; and from energyintensive traditional ball mill to upgraded versions and use of pregrinders, the cement industry is shifting towards more energyefficient grinding solutions ICR trains its spotlight on the current technology trends The cement 2018年7月1日 Among the industries, the nonmetallic industry was reported as the third largest energy user and accounted for about 12% of the global energy use [1]Within this portion, cement industry had the majority of the utilization with 85–12% [1], [2]US Energy Information Administration (EIA) [7] named cement industry as the most energy intensive among the Energy and cement quality optimization of a cement grinding circuitEquipment: Preheaters, Kilns, Burners, Clinker Coolers§Process theory and fundamentals; Pyroprocess systems and equipment components; Equipment and process design basic parameters; Key process concerns, process and operations troubleshooting; Key process and quality performance indicators and influencers; OptimizationCement Production Seminar: Pyroprocess2004年11月1日 The current world consumption of cement is about 15 billion tonnes per annum and it is increasing at about 1% per annum The electrical energy consumed in cement production is approximately 110 kWh/tonne, and around 40% of this energy is consumed for clinker grindingThere is potential to optimise conventional cement clinker grinding circuits and in the Cement grinding optimisation ScienceDirect
.jpg)
StepbyStep Guide to Cement Ball Mill Maintenance
Maintaining a cement ball mill is crucial for ensuring optimal performance and longevity of the equipment Regular maintenance helps prevent costly breakdowns and ensures smooth operation This practical guide provides detailed steps, tools required, manpower needed, and recommended schedules for maintaining a cement ball milland cement Roller presses are used mainly in combination with a ball mill for cement grinding applications and as finished product grinding units, as well as raw ingredient grinding equipment in mineral applications This paper will focus on the ball mill grinding process, its tools and optimisation possibilities (see Figure 1) The ball millBALL MILLS Ball mill optimisation Holzinger Consulting