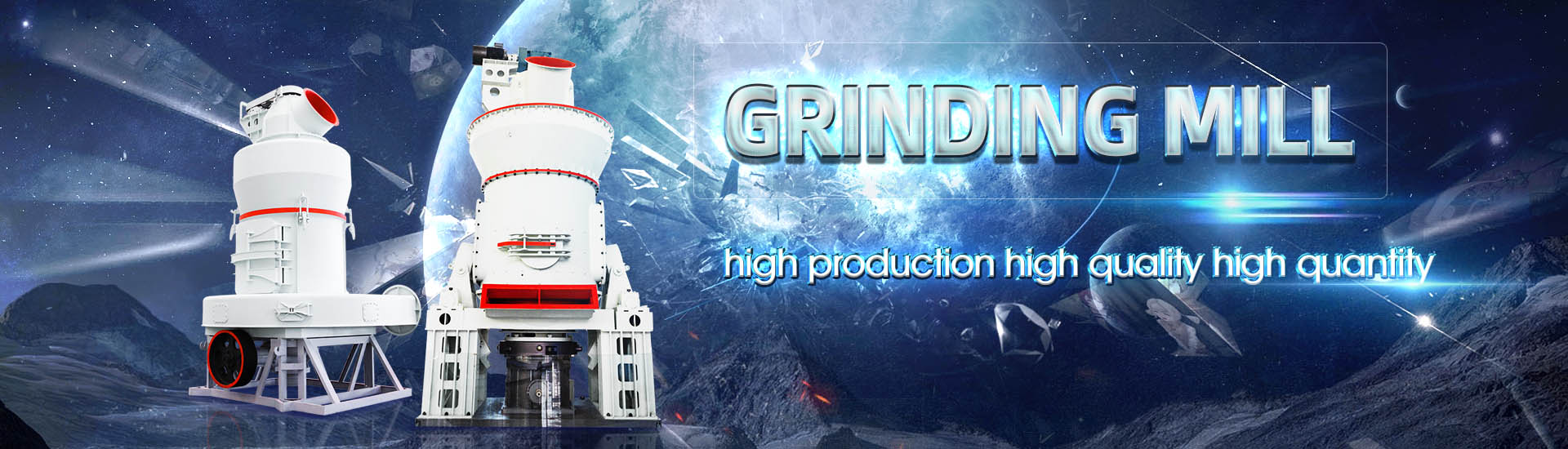
How to increase output of power plant desulfurization limestone ball mill
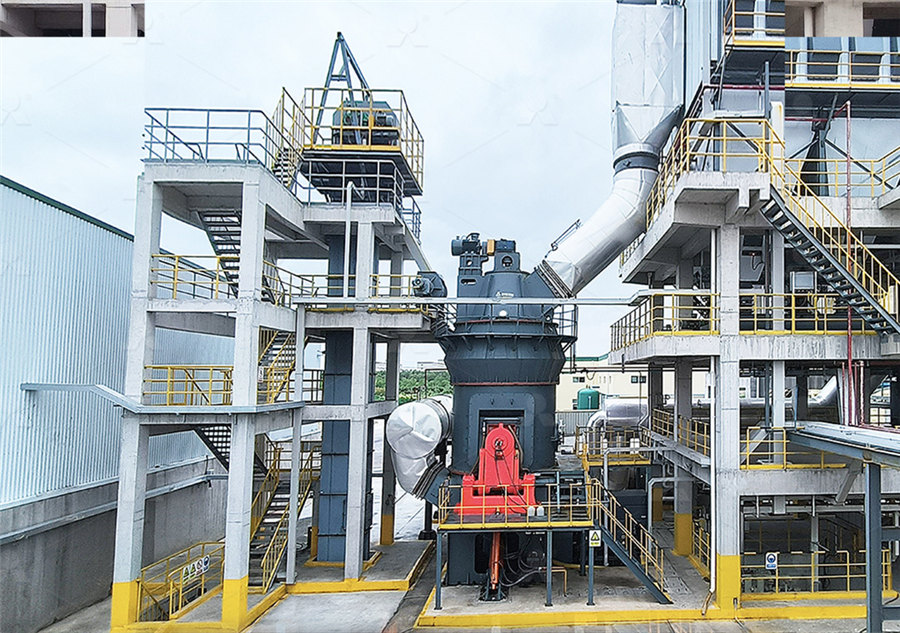
Flue Gas Desulfurization (FGD) Working Thermal
Limestone slurry in the limestone slurry storage tank of flue gas desulfurization (FGD) system will be pumped to absorber by the limestone slurry feed pumps The agitator is provided to keep the slurry solids in suspension during tank 2017年7月1日 Desulfurization tests show greater performance in terms of gypsum production SO 2 removal efficiency compared to the limestone treated with a traditional mill Multicriteria Enhancing the recovery of gypsum in limestonebased wet flue Hot gas cleaning techniques to remove sulfur and other impurities in the flue gas streams offer the key advantages to such systems This paper reviews briefly the Hot Gas Desulfurization Analytical Investigation and Design of Flue Gas Desulfurization 2017年7月1日 Desulfurization tests show greater performance in terms of gypsum production SO 2 removal efficiency compared to the limestone treated with a traditional mill Multicriteria Enhancing the recovery of gypsum in limestonebased wet flue
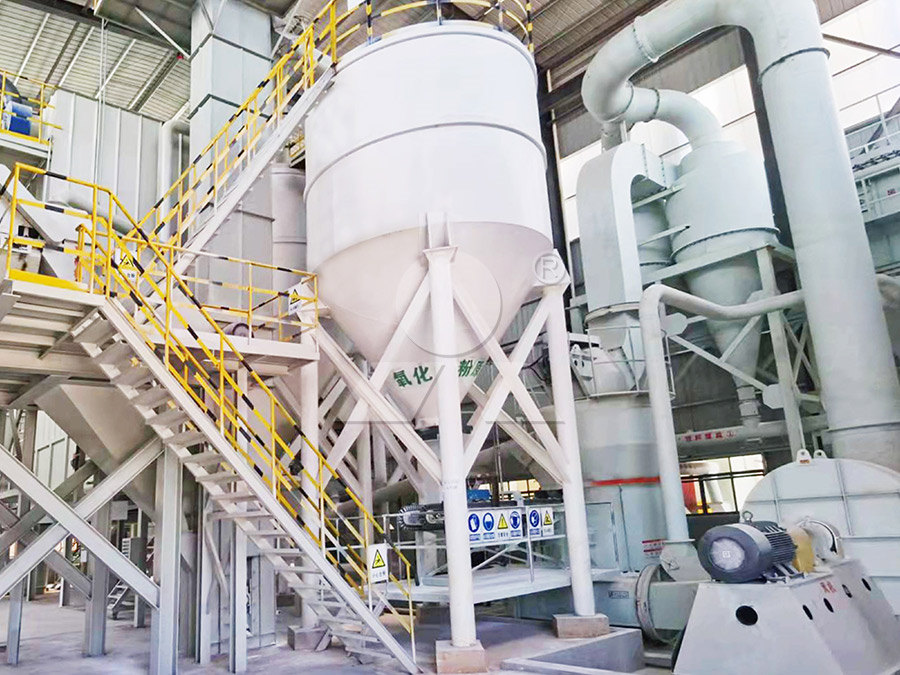
Analysis of limestone for flue gas desulfurization in a power plant
Excellent calibration curves and repeatability can be achieved with the ARL OPTIM’X to determine the suitability of limestone minerals for use in power plant scrubbers The technique is both 2021年10月13日 The viability of the VRM in this application would also enable offsite dry milling of limestone, presenting significant potential capital and operating cost benefits for a power A Technical and Economic Comparison of Ball Mill Limestone 2015年10月30日 This study investigated that status of domestic and international furnace desulfurization and desulfurization characteristics of limestone for fluidized bed use depending (PDF) A Review of Desulfurization Technology using Limestone in 2015年3月15日 The objective of this paper is to present a general review of the FGD technologies used to abate sulphur emissions from coalfired power plants, and expose the Status of Flue Gas Desulphurisation (FGD) systems from coalfired
.jpg)
A Technical and Economic Comparison of Ball Mill Limestone
2021年10月13日 The viability of the VRM in this application would also enable offsite dry milling of limestone, presenting significant potential capital and operating cost benefits for a power 2021年10月13日 Wet flue gas desulfurization (WFGD), using limestone with forced oxidation (LSFO), is a common Flue gas desulfurization (FGD) process where limestone reacts with SO2 to produce gypsum (CaSO42H2O)A Technical and Economic Comparison of Ball Mill Limestone About 90% thermal power plants in Japan, Germany, and the United States adopted this technology for the flue gas desulfurization Part2 2 Working Principle Limestone is used as the desulfurization absorbent Limestone is crushed and ground into powder Limestone powder is mixed with water to form the absorption slurryLimestoneGypsum FGD Wet DesulphurizationIndex Terms—wet desulfurization of gypsum, PID control, multistep feed forward predictive control, long and short term memory network I INTRODUCTION ITH the development of the power industry, the content of SO2 produced by coalfired power plants in China has been increasing in the proportion of SO2 emissionsFeed Forward Cascade PID Based Predictive Control of the PH
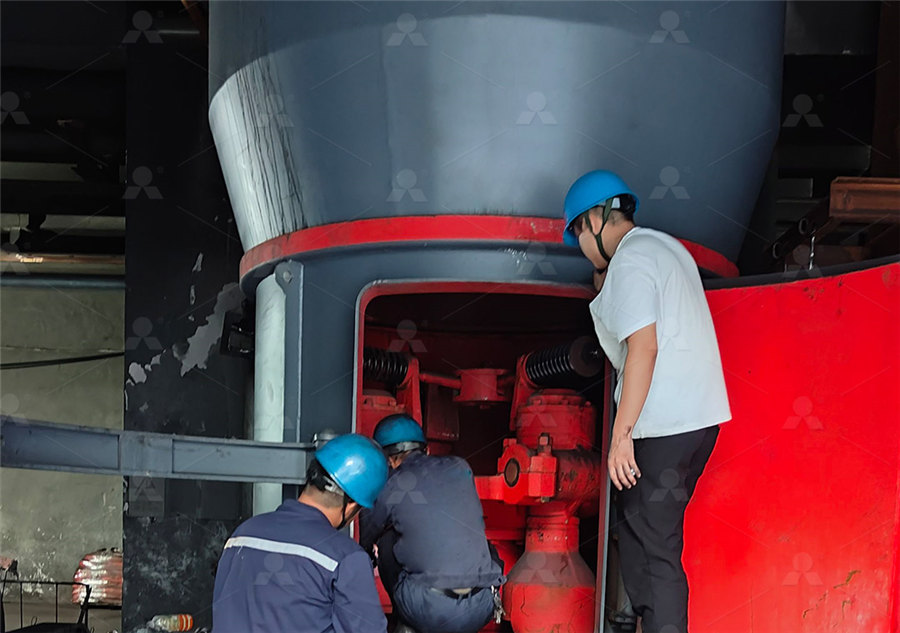
Factors Affect The Output and Quality of Ball Mills And How to
2023年12月28日 If the balltomaterial ratio is too large, it will increase the wasted work loss due to impact friction between the grinding body and the lining plate, increase power consumption, and reduce output Choosing the ball loading amount and the balltomaterial ratio of the ball mill is the most common problem in actual production2022年1月15日 In the industrial production of China, the processing of phosphate rock, volcanic eruptions, kerosene combustion and aluminum smelting will lead to flue gas emissions containing a large amount of SO 2SO 2 is a highly irritating gas Because SO 2 is freely soluble in water and enters the respiratory tract, it can generate corrosive sulfurous acid, sulfuric acid, and sulfate Summary of research progress on industrial flue gas desulfurization 2017年10月25日 This has been termed the ball mill circuit functional performance equation (McIvor, 1989) It states that the output of new product size material of a ball mill circuit with a given feed size is determined by: a the total mill power draw;How to Improve Ball Mill Performance 911MetallurgistABSTRACT Wet flue gas desulfurization (WFGD), using limestone with forced oxidation (LSFO), is a common Flue gas desulfurization (FGD) process where limestone reacts with SO2 to produce gypsum (CaSO42H2O) In South Africa, Eskom’s Kusile Power Station utilizes conventional wet ball milling to grind highgrade limestone (96% CaCO3) to 95% passing 45 µm prior to use in A Technical and Economic Comparison of Ball Mill Limestone
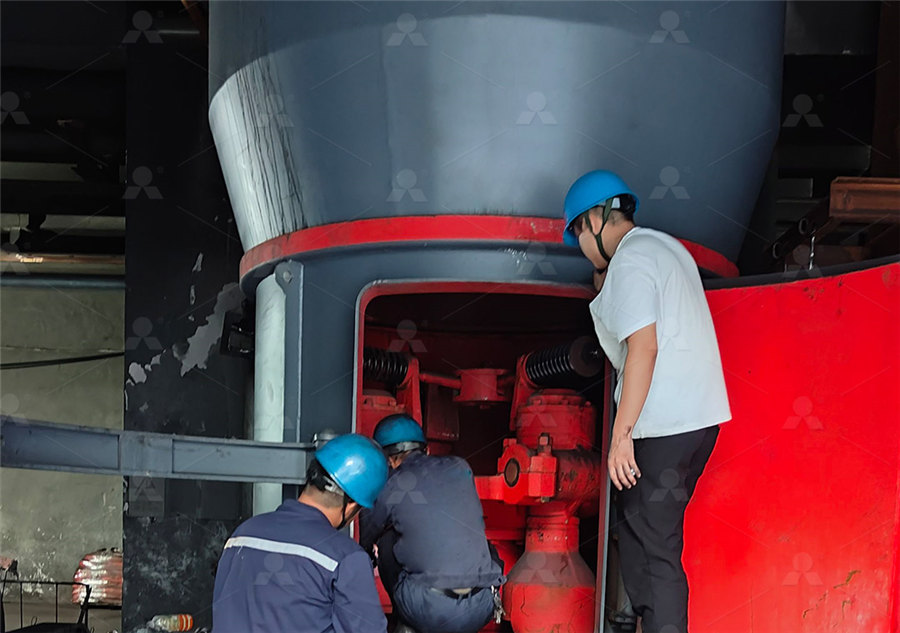
BALL MILLS Ball mill optimisation Holzinger Consulting
process Together with ball charge composition, both tools – liners and media – can be optimally adjusted for the application They can then fulfil the Figure 2: ball mill tools and comminution process Figure 1: ball mill communition process chain Ball charge management grinding Ventilation and cooling Operation and control2006年1月20日 An experimental study was performed on a countercurrent pilotscale packed scrubber for wet flue gas desulfurization (FGD) The flow rate of the treated flue gas was around 300 Nm3/h, so the pilot PilotPlant Technical Assessment of Wet Flue Gas Desulfurization Procurement of desulfurization machinery for power plants, environmentally friendly limestone grinding machines to create clean emissions Power plants are essential in providing electricity to homes and businesses, but they often produce harmful emissions that contribute to air pollution This is where desulfurization machinery comes into playProcurement of desulfurization machinery for power plants A Limestone Grinding Mill Plant is a facility designed to process limestone into fine powder for various applications Limestone is a sedimentary rock primarily composed of calcium carbonate (CaCO₃) and is widely used in industries such as construction, agriculture, and manufacturingLimestone Grinding Mill Plant TAYMACHINERY
.jpg)
(PDF) Performance optimization of an industrial ball
2017年1月1日 An increase of over 10% in mill throughput was achieved by removing the ball scats from a single stage SAG mill These scats are non spherical ball fragments resulting from uneven wear of balls Operation of Ball Mill Pulveriser The Ball mill pulveriser is basically horizontal cylindrical tube rotating at low speed on its axis, whose length is slightly more to its diameter The inside of the Cylinder shell is fitted with heavy cast liners and Pulveriser in Thermal Power Plant Bowl Mill Ball 2002年1月1日 Coalfired electricitygenerating plants may use SO2 scrubbers to meet the requirements of Phase II of the Acid Rain SO2 Reduction Program Additionally, the use of scrubbers can result in Flue Gas Desulfurization: The State of the Art [J] ResearchGate2019年7月22日 The reduction of wet desulfurization wastewater is one of the important tasks of coalfired power plants, and it is important for achieving “zero emissions” Evaporation and concentration (EC) with waste heat is an effective way to reduce wastewater Here, two typical types of industrial desulfurization wastewater are used to study the change rule of pH and total Evaporation and concentration of desulfurization wastewater with
.jpg)
Enhancing the recovery of gypsum in limestonebased wet flue
2017年7月1日 The most common types of FGD system are based on the contact between the flue gases and an alkaline sorbent such as lime or limestone (Wang et al, 2005)Furthermore, the major types of largescale power plant FGD systems include (i) spray towers, (ii) spray dryers and (iii) dry sorbent injection systems (Song et al, 2012)These FGD systems can achieve about Neither lime nor limestone dissolves well in water and therefore, both are pumped in slurry form to the scrubber tower Lime slurry is more alkaline, having a pH of 125 while limestone slurry is roughly neutral A lime based system will therefore add more lime when pH drops below 12 and a limestone based system will be controlled around 6 UnlessLime / Limestone Wet Scrubbing System for Flue Gas DesulfurizationKeywords: Flue Gas Desulfurization, FGD sytem design, SO 2 removal, limestone scrubbing, flue gases 1 Introduction 1The term flue gas desulfurization has traditionally referred to wet scrubbers that remove sulphur dioxide (SO 2) emissions from large boilers (mainly coal and oil fired combustion) However, because of theAnalytical Investigation and Design of Flue Gas Desulfurization ABSTRACT: In 1927, the limestone desulfurization process was first applied in the Barthes and Bansside Power Plants (total 120MW) beside the Thames River in UK to protect highrise building in LondonApplication and Development Trend of Flue Gas Desulfurization

HOW DIGITAL STRATEGIES IMPROVE STEAM POWER PLANT
digital power plant initiative, Mitsubishi Power is developing new AIbased control systems to enhance performance, efficiency and flexibility for power plants Analyzing large volumes of data acquired during plant operations allows advanced analytics to provide a range of functions, including cost optimization and early detection of anomalies2024年2月29日 22 Process Simulation Figure 2 presents the process simulation of the pyrolysisbased cofiring system The coal and biomass grinding processes in the fuel conversion unit are simulated by Crusher model The biomass needs to be dried after grinding since the water content of the biomass entering the pyrolysis reactor is high, which could lead to a Technoeconomic Analysis of Supercritical CoalFired Power Plant The limestone desulfurization grinding production line includes electromagnetic vibrating feeder, jaw crusher, European type trapezium mill, bucket elevator, belt conveyor, adjustable silo, electronic control system, etc The main equipment is patented product MTW175 European type trapezium mill with output of 15T/H Customer evaluation:20T/H limestone desulfurization grinding production line 2017年7月26日 The finer you crush, the higher your ball mill tonnage and capacity will be The effect of ball mill feed size and how it affects circuit throughput can be hard to estimate Here we described a method of designing a crushing plant using power drawn and power rate to define reduction ratios in each stage of crushingHow Ball Mill Ore Feed Size Affects Tonnage Capacity
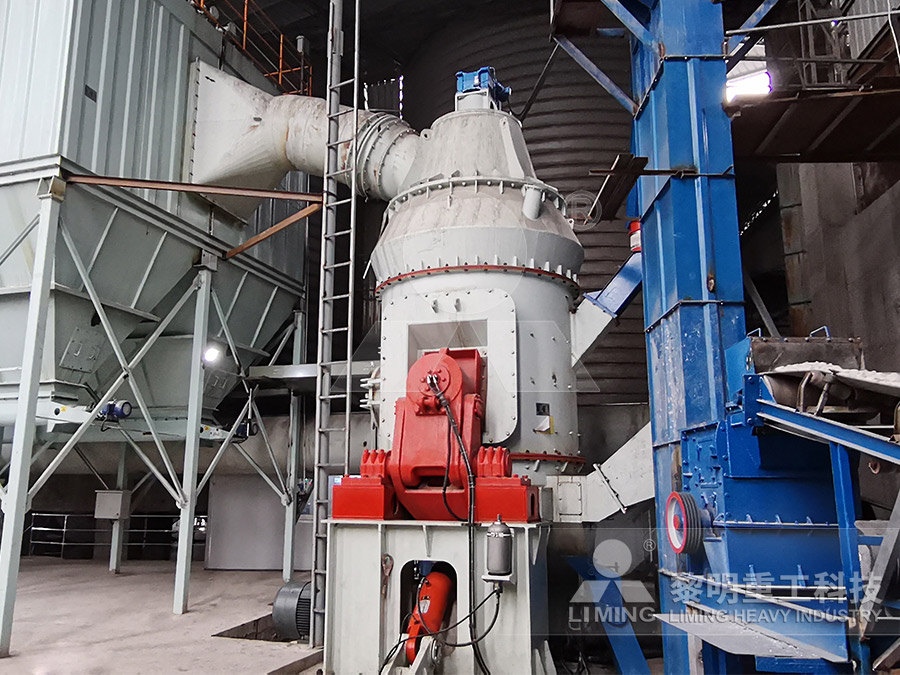
5 Ways to Improve the Ball Mill Efficiency FTM
2020年1月11日 Here the structure means the ratio of ball mill length to its diameter According to the industrial tests, the capacity varies with the ball mill types; Even from the same type of ball mill, the energy consumption and milling efficiency are different One of the factors is the function of the diameter and ponents of power plant: ball mill of FGD (Flue gas desulfurization) Components of power plant: Fluegas desulfurization FGD plant for removing SOx, big blue tank is absorber tank and other important component is GGH ie Gas to Gas heater its called wet FGD ball mill it can make 20 mm limestone into micron particlesComponents of Power Plant: Ball Mill of FGD (Flue Gas Desulfurization SO 2 emission from lean waste gases in stationary sources (eg, power plants) can be treated by wet and dry fluegas desulfurization (FGD), while the stationary source like oresmelting plants produces rich gases containing SO 2 of much higher concentration that Desulphurisation an overview ScienceDirect Topics2002年4月1日 The average station service power consumption rate of desulfurization facilities increased from 112 to 129% following retrofitting, while limestone usage increased from 1126 to 1555 kg/(10 ⁴ Optimum Values of Process Parameters of the “Wet Limestone
.jpg)
Selecting the right model of grinding mill for limestone
Selecting the right model of grinding mill for limestone desulfurization powder technical upgrade project Limestone desulfurization is a widely adopted method for reducing sulfur dioxide emissions from industrial processes, particularly in power plants and steel mills2018年12月19日 Images of limestone and CFBC flyash samples (a) and (b) is limestone particle and crystalline structure; (c) fly ash of Samcheok green power Co; and (d) fly ash of Yeosu Coal Power CoUtilization of CFBC Fly Ash as a Binder to Produce InFurnace 1 Introduction Wet limestone flue gas desulfurization is the most widespread technology to control SO2 emission in coalfired power stations In the wet limestone desulfurization process the flue gas is scrubbed with slurry containing limestone particles (CaCO3)Controllability Analysis and Decentralized Control of a Wet Limestone 2013年9月1日 In this paper, the output can not meet the operating requirements problems of power plant desulfurization device wet mill system operation, site of the optimization test of wet mill system Experimental Study on Optimization of Wet Desulfurization of Wet Ball
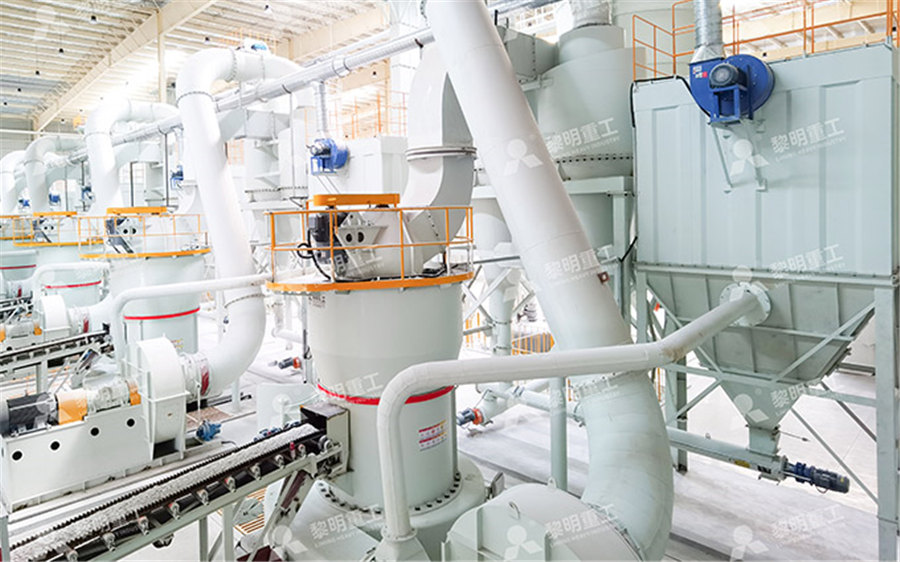
Flue Gas Desulfurization: Detailed Process Overview
2024年8月13日 This blog post is the third in a threepart series that discusses flue gas desulfurization (FGD) The first post provides overviews of sulfur dioxide (SO 2) and emissions regulations, the FGD industry, and global FGD market trendsThe second post provides highlevel overviews of wet, semidry, and dry FGD technologies with respect to SO 2 capture 2022年7月25日 In this study, a pilotscale evaporation tower system was built to treat the desulfurization wastewater by spray evaporation The distribution characteristics of Cl− in the wastewater evaporation process were investigated Besides, the morphology and physicochemical property of solid evaporation products from desulfurization wastewater were Experimental study on the treatment of desulfurization SpringerComparing Lime and Limestone SO 2 Wet Scrubbing Processes More than ninety percent of US flue gas desulfurization (FGD) system capacity uses lime or limestone This trend will likely continue into the next phase of federally mandated SO 2 Flue Gas Desulfurization LimeMax Capacity 1,050 MW Max Inlet SO 2 Concentration 80,000 mg/Nm 3 (Coal fired) Max SO 2 Removal Efficiency 99% High Reliability The flue gas desulfurization (FGD) plant removes sulfur dioxides (SO 2) from flue gas produced by boilers, furnaces, and other sourcesMitsubishi Power effectively contributes to the prevention of air pollution through its wet limestone Mitsubishi Power Flue Gas Desulfurization (FGD) Plants
.jpg)
Enhancing the recovery of gypsum in limestonebased wet flue
2017年4月6日 Additionally, the size distribution of limestone which has been reported to have an effect on gypsum production and SO2 removal, would also influence the particle yields in WFGD system2006年7月1日 With approximately 140 new coal fired power plants on the drawing boards for the US alone, the concern for meeting clean air regulations here and around the world is leading new and existing Selecting the Right Pumps and Valves for Flue Gas Desulfurization2019年3月13日 More than 80% of the power plants in China are using WFGD as their main method for desulfurization (Wang and Hao Citation 2012) In the flue gas treatment systems in coalfired power plants, WFGD systems are commonly installed downstream of the electrostatic precipitators (Sui et al Citation 2016 ) and the pressure charging fans, operating at positive Full article: Modeling and optimization of wet flue gas desulfurization 2020年5月1日 Fossil fuel combustion accounts for the primary portion of the world's power generation, in which coalfired power generation still contributes to around 40% of global electricity supply [1, 2]Especially in China, the total installed capacity of the power blocks exceeded 177 billion kilowatts leading the world by 2017, more than 60% of which is supplied Operation strategy optimization of desulfurization system based
.jpg)
why is limestone used in coal power plants Welcome to Tables
Power plant emissions of sulfur dioxide and nitrogen Feb 27, 2013 Emissionsof sulfur dioxide (SO 2) and nitrogen oxides (NO x) from the electric power sector in 2012 declined to their lowest level since the passage of the Clean Air Act Amendments of 1990The decline in emissions is due primarily to an increasing number of coalfired units retrofitted with fluegas desulfurization