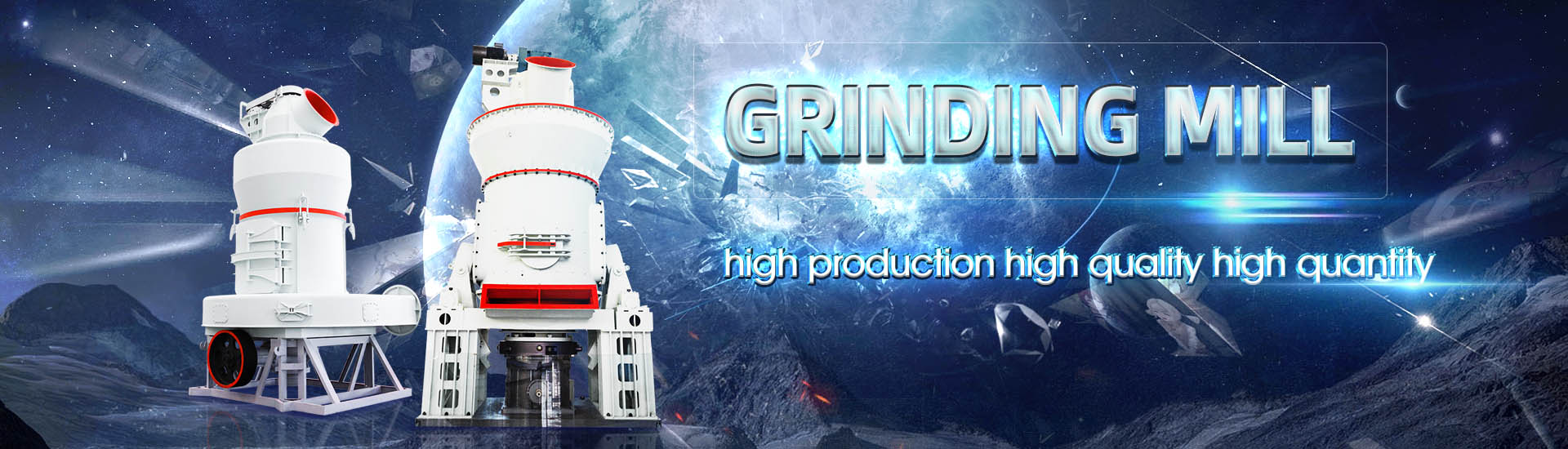
Manganese powder processing flow
.jpg)
Improvement of manganese electrolytic process and secondary
2024年6月1日 This article introduces the process flow of manganese metallurgy and provides a systematic overview of the optimisation of various aspects of the manganese electrolytic In the hydrometallurgical processing of manganese from its ore, the leach liquors often contain divalent ions such as iron, manganese, copper, nickel, cobalt and zinc along with other impurities which make manganese very difficult to separateHydrometallurgical Processing of Manganese Ores: A 2016年4月27日 The Manganese Ore Processing Plant Crushing and Sampling of Manganese Rock The flowsheet incorporates a conventional multistage Manganese Ore Processing 911Metallurgist4 天之前 However, manganese ore processing requires a complete understanding of the ore’s composition, properties, and characteristics to select the best beneficiation equipment to Optimizing Manganese Ore Process Flow and Equipment
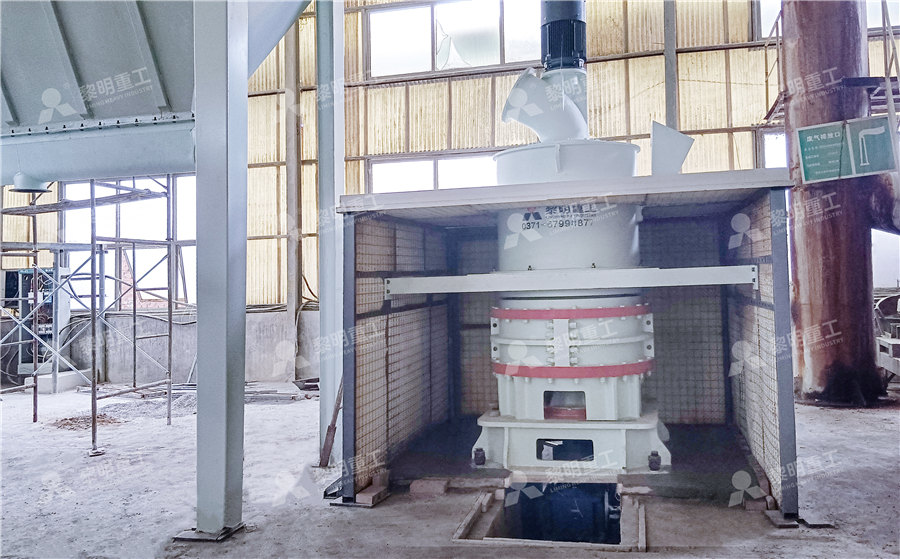
Characterization and flowability methods for metal powders
2020年12月3日 In the case of manganese powder, the gaps between the larger particles can be filled with smaller ones (possibility of increase in packing density/packing fraction)2021年9月12日 Experimental validation in the early stages of process design improves quality and allows cost estimation for plant scaleup For the investigation of the pretreatment of Process Design for the PreTreatment of Manganese Ores2023年6月27日 Manganese metallurgy is a technology for extracting metal manganese and its compounds from manganese containing mineral raw materials In 1774, the Swedish chemist Manganese Metallurgy SpringerLink2020年8月21日 As South Africa accounts for 74% of the world’s identified manganese resources and 32% of the world’s reserves,4 the paper presented here describes in more detail the From Ore Body to High Temperature Processing of Complex Ores:
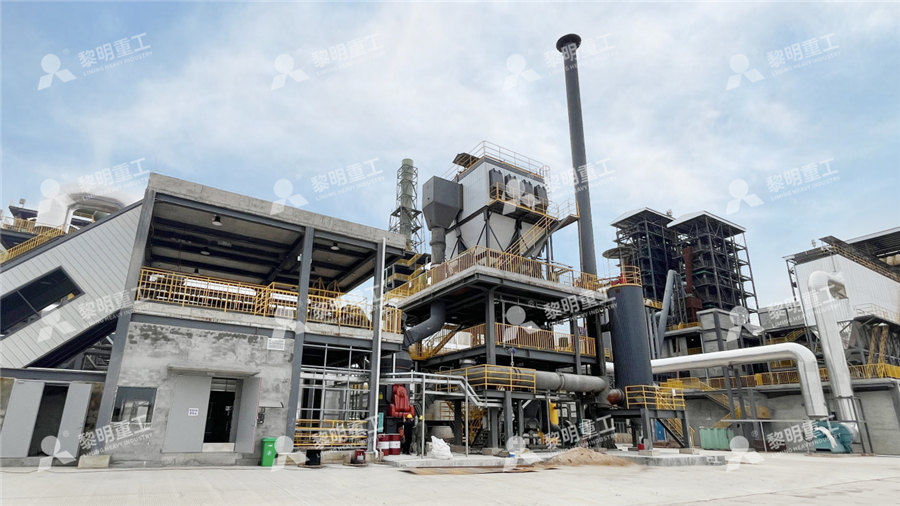
Insights into the global flow pattern of manganese
2020年3月1日 One thing to be aware of is that we did not consider the processing losses (eg, slags) in the manganese flow system According to previous studies, the ratio of manganese losses in slag to the total manganese input could reach 20%–40% in Fe–Mn and Si–Mn production ( Dashevskiy et al, 2013 ; Kim et al, 2011 ; Westfall et al, 2015 ), and 10%–45% 2014年5月7日 The Basics of Manganese Mining and Processing While exposure to manganese fumes, dust and compounds should be avoided, in safe formulas manganese is used by most everyone The fact that manganese is Manganese Mining and Processing: Everything you 2024年2月26日 Chongqing Chengkou manganese deposit is a large carbonatetype manganese deposit in the upper reaches of the Yangtze River, located in Gaoyan Town, Chengkou County, Chongqing In order to improve the Comprehensive Study on Mineral Processing Methods 2020年12月3日 In the case of manganese powder, Allesø, M, Garnaes, J Rantanen, J Evaluation of ring shear testing as a characterization method for powder flow in smallscale powder processing equipmentCharacterization and flowability methods for metal powders
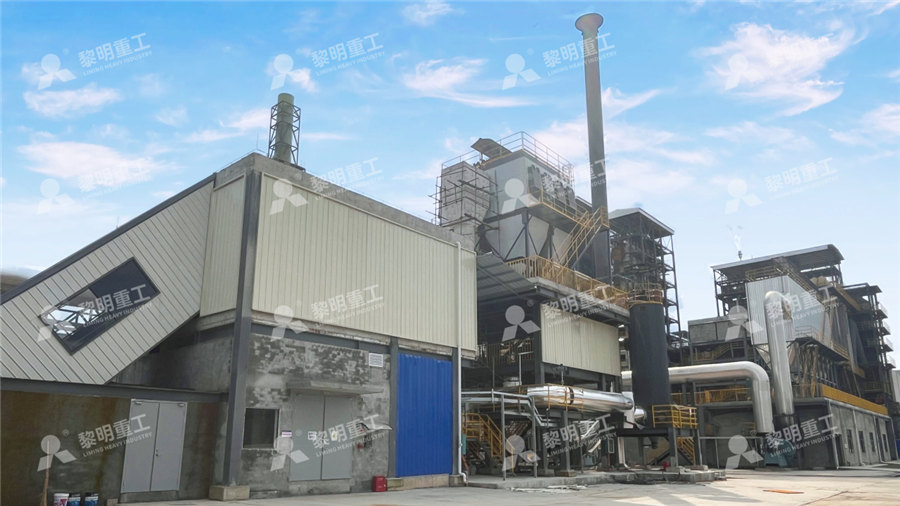
Typical Manganese Beneficiation Flow Sheet Multotec
Typical Manganese Beneficiation Flow Sheet Multotec specialises in manganese beneficiation equipment with over 50 years of global experience and leading technology Our team of metallurgists and engineers will partner with you to customise your equipment, helping your process run more efficiently while lowering your overall cost per ton2023年3月8日 Increasing demand for manganese and rapid depletion of highgrade manganese ores grow attention to other resources However, environmental impacts and technoeconomic issues are the main challenges regarding manganese extraction from lowgrade ores This study investigated the environmental impacts of manganese recovery from lowgrade ores and the Assessing the environmental footprints of the manganese 10TPH Manganese Ore Processing Plant flow This is a complete and high quality manganese ore processing plant According to the customer’s requirements, we designed two crushing processes to achieve the appropriate particle size before entering the gravity separation10TPH Manganese Ore Processing Plant In South Africa2023年3月15日 1 Introduction Lithiumion batteries have been widely used in energy storage for mobile electronic equipment, power vehicles and other fields due to its excellent characteristics such as high energy density, long cycle life, low selfdischarge rate and no memory effect [1]In recent years, under the influence of multiple factors such as energy, environment, science and Efficient separation and recovery of lithium and manganese from
.jpg)
Manganese Ore Processing Plant Luoyang Dahua
The manganese powers which meet the beneficiation requirement will be sent to magnetic separator to remove sundries The finial powders send to dryer to get high grade manganese powder Equipment Configuration: 1 The crushing machine for manganese ore: jaw crusher, hydraulic cone crusher 22012年6月6日 Manganese ferrite nanoparticles were synthesized using a HighEnergy BallMilling mechanochemical method After 1 h of milling, the process produces a material consisting of single crystalline domain nanoparticles having a diameter of about 8 nm Chemical properties of the synthesized powders allow an easy functionalization with citric acid Both asobtained and Manganese iron oxide superparamagnetic powder by 2024年1月13日 The shape of powder particles plays a pivotal role in determining their Powder Processing flow characteristics Irregularly shaped particles, common in many powders, contribute to interlocking and reduced Powder Processing Challenges: Mastering force and 2022年11月16日 Abstract— A hydrometallurgical method for the extraction and separation of Li(I), Mn(II), Al(III), and Fe(III) from the cathode material of a lithium–manganese battery is proposed for the first time; the method is based on a combination of leaching and liquid extraction using a deep eutectic solvent The extraction system based on Aliquat 336/menthol (1 : 1) is A FlowChart for Processing of a LithiumManganese Battery
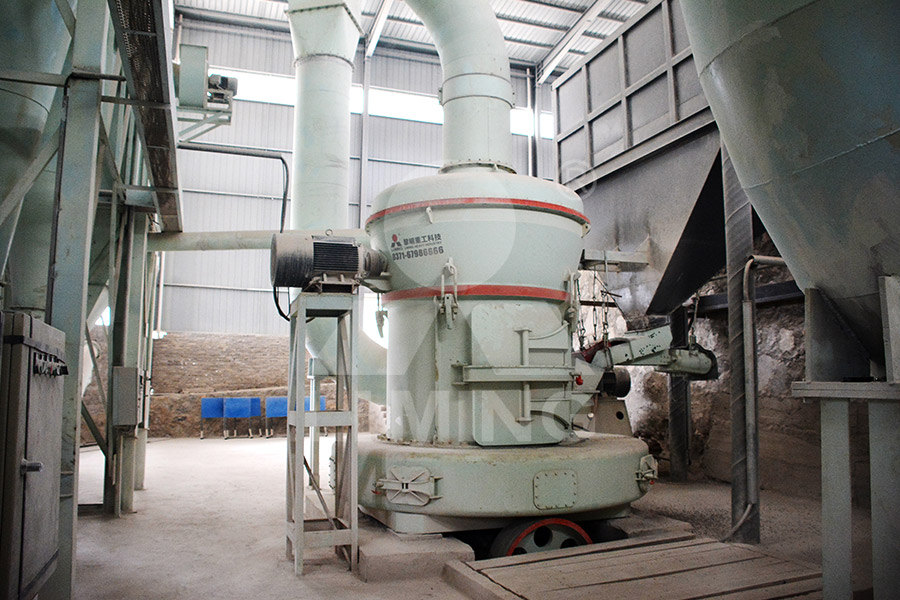
A concise summary of powder processing methodologies for flow
2023年6月1日 The Powder Flow Tester evaluates powder flow properties in industrial processing equipment rapidly and efficiently [40, 41] Flow Function, Wall Friction, Bulk Density and Time Consolidation Test with Flow Function, Arching diameter, Rathole Dimension, Hopper Half Angle, etc be determined and calculated with the help of simple function in powder flow 2019年8月23日 Strong magnetic separation Manganese mineral is a weak magnetic mineral ( the specifical magnetization coefficient x=10×106~600×106cm3/g ), and it can be recovered in a strong magnetic field magnetic separator with a magnetic field strength Ho=800~1600kA/m (10000~20000oe), the manganese grade is increased by 4% to 10%Manganese Processing Equipment, Process Flow, Cases JXSC2021年8月4日 Manganese ore process flow: Manganese Ore Processing Atairac; ; Home Material Processing The finial powders send to dryer to get high grade manganese powder Equipment Configuration: 1 The crushing machine for manganese ore: jaw crusher, hydraulic cone crusher 2Manganese Ore Processing – ATAIRAC ENGINEERED PRODUCTS Download scientific diagram Schematic flow diagram of the leaching and separation of manganese sulfate from pyrolusite ore from publication: Recovery of pure MnSO 4∙H 2O by reductive leaching Schematic flow diagram of the leaching and separation of manganese
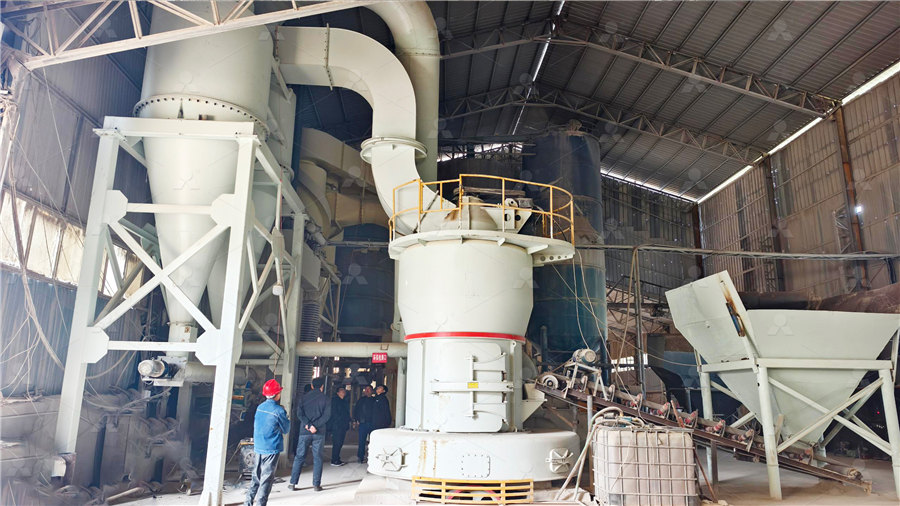
From Ore Body to High Temperature Processing of Complex Ores: Manganese
2020年8月21日 Manganese is considered a relatively rare metal as concentrations of it in ore of commercial importance are geographically limited In nature, manganese is found in the form of oxides, carbonates, and silicates Manganese ores are complex in the sense that they not only consist of a complex oxide mineral assemblage but these minerals are also very finely inter Introduce how to crush manganese, whole manganese ore processing plant flow layout (with photo), and related rock crusher machine Contact us to do free flow design Skip to content The finely ground manganese ore powder needs to go through a magnetic separator for strong magnetic separation and impurity removal, Manganese Ore Processing Solution Eastman Rock Crushera hydrochloricacid solution for cathode leaching The proposed flowchart for processing of the lithium– manganese battery allows one to carry out sufficiently complete separation of Li, Mn, Al, and Fe Keywords: deep eutectic solvent, metal ions, leaching, solvent extraction, separation flow chart DOI: 101134/S50268 INTRODUCTIONA FlowChart for Processing of a LithiumManganese Battery 2023年8月7日 Manganese is a type of common metal mineral in nature More than 150 types of manganese minerals have been discovered so far, but only a small portion of manganese ore with mining and utilization value, mainly including pyrolusite, psilomelane, bog manganese ore, etc Manganese has become an essential strategic mineral resource among countries and apply in Five Common Types Of Manganese Ore Processing Solutions
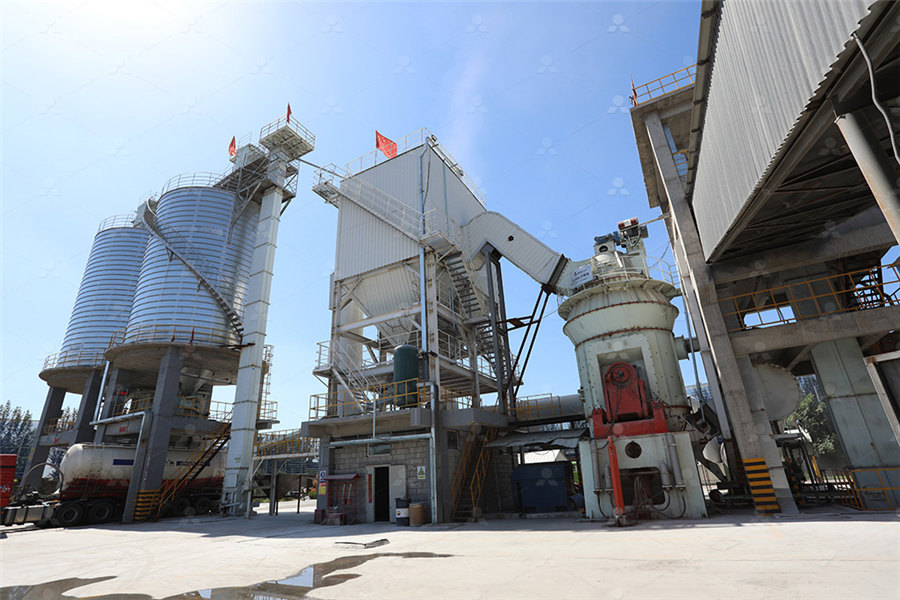
Manganese Ore Crusher/ Manganese Ore Processing
Manganese Ore Processing Plant Flow Manganese ore processing plant mainly consists of crushing, grinding and beneficiation The First Stage: Crushing and Screening Send the screened 012mm manganese powder into ball mill for Abstract: Beneficiation studies on manganese ore fines of Ramakolla and Kanavehalli mines, Sandur, Karnataka Recent years, there is an increasing demand on manganese consumption which stems from the important role of manganese in carbon steel production The growing need for manganese ores makes the beneficiation of lowgradeStudies on the Gravity Processing of Low Grade Manganese Ore The Powder Flow Tester evaluates powder flow properties in industrial processing equipment rapidly and efficiently [40,41] Flow Function, Wall Friction, Bulk Density and Time Consolidation Test with Flow Function, Arching diameter, Rathole Dimension, Hopper Half Angle, etc be determined and calculated with the help of simple function in powder flow tester [ 24 , 42 ]A concise summary of powder processing methodologies for flow 2017年2月1日 Spent Zn–MnO 2 battery electrode powder, containing 301% of Mn and 256% Zn was was treated via reductive leaching by H 2 SO 4 and selective precipitation by NaOH at pH 13 for Mn(OH) 2 and then pH 10 for Zn(OH) 2, and the hydroxides converted respectively to MnO 2 and ZnO by calcination The effects of H 2 SO 4 concentration, leaching time, solidliquid Recovery Zinc and Manganese from Spent Battery Powder by
.jpg)
Improvement of manganese electrolytic process and secondary
2024年6月1日 Manganese (Mn) is a metallic element in transitional group located in the fourth cycle and group VIIB of the periodic table Mn is hard but fragile and has a melting point of 1246 °C (Sun et al, 2020)In terms of chemical properties, the monomers of Mn are reflected that Mn readily is oxidized by oxygen under heating conditions, and are dissolved in dilute sulfuric acid2024年11月21日 Manganese ore processing plants typically include crushers, ball mills, where the manganese ore is refined into a fine powder using specialized equipment such as ball mills or vertical roller mills To achieve this, various crushing equipment Challenges Process Flow of Chromium Ore Dressing Technology Equipment Required To Build A Manganese Ore Processing PlantManganese Ore Processing EquipmentMining manganese ore involves several steps and methods For grinding the ore into a fine powder Gravity Separation Equipment Such as: mine site early stage exploration, mineral ore analysis test, trial ore processing test, complete process flow sheet design, full line of mining equipments, after Manganese ore processing plant Hengcheng Mining Equipment Co,ltdIMPC 2016: XXVIII International Mineral Processing Congress Proceedings ISBN: 9781292 BENEFICIATION OF LOW GRADE MANGANESE ORE BY JIGGING IN A SPECIALLY DESIGNED ORE DRESSING UNIT Malo Rousseau1, Simon B Blancher1, Renato Contessotto2, Thomas Wallmach1 1: ERAMET Research, 1 av Albert Einstein 78190 (PDF) Beneficiation of low grade manganese ore by jigging in a
.jpg)
Manganese ore processing production line
2022年8月25日 The unqualified manganese powder is sent to the ball mill for grinding Stage 3: mineral processing The manganese powder meeting the ore dressing requirements is sent to the magnetic separator for strong magnetic separation to remove impurities, and the obtained manganese powder is sent to the dryer for drying to obtain manganese refined powder2021年6月23日 Introduction of manganese ore process flow: In the first step of the manganese ore processing process, the raw manganese ore is crushed at the manganese ore production line site The bulk manganese ore will be transported to the silo through the loading equipment, and then evenly sent to the jaw crusher by the vibrating feeder for primary brokenManganese Ore Processing Plantmanganese ore production Manganese (Mn) is the twelfth most abundant element in the Earth’s crust Amongst some 300 minerals containing manganese, only about a dozen are of economic significance Manganese is a silverygray metal that resembles iron Manganese Ore Process Plant JXSC Mineral2020年7月30日 The mechanism of droplet formation from the molten metal depends on the powder characteristics: size, shape, and structure; process parameters: molten metal properties (composition, viscosity, and surface Nanomaterials through Powder Metallurgy:
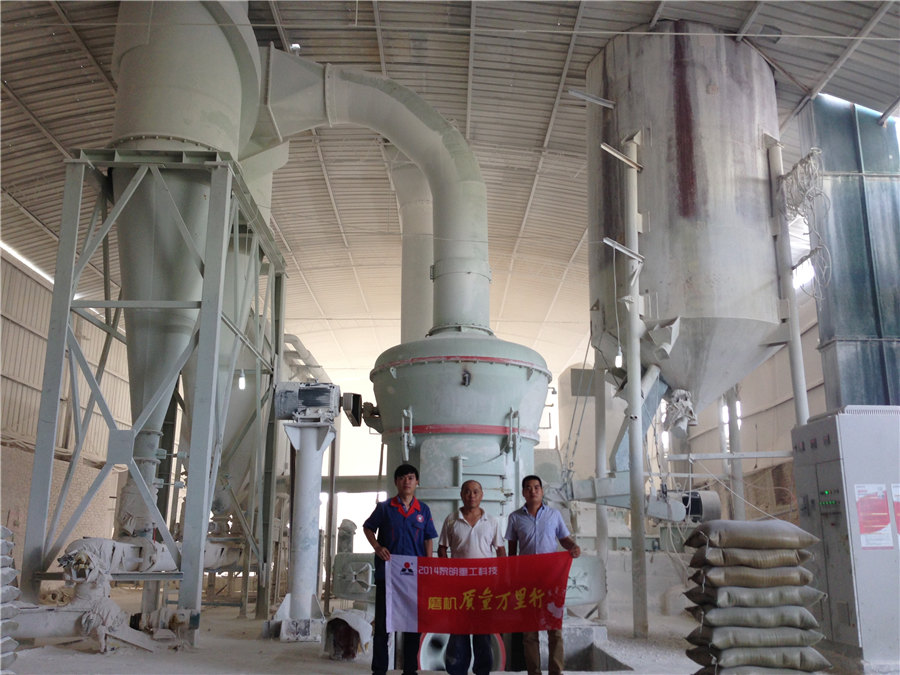
A Review of Low Grade Manganese Ore Upgradation Processes
2019年7月29日 A 9743% leaching ratio of manganese was obtained from the roasted ore, which was leached by a 15 mol/L concentration of sulfuric acid at a 50°C leaching temperature, 50 rpm stirring speed and a 2018年7月28日 The hot compressive deformation behaviors of ZHMn34221 manganese brass are investigated on ThermecmastorZ thermal simulator over wide processing domain of temperatures (923–1073 K) and strain rates (001–10 s–1) The true stress–strain curves exhibit a single peak stress, after which the stress monotonously decreases until a steady state stress Constitutive modeling for high temperature flow behavior of a Rich in mineral salts Process flow chart for jaggery powder preparation is shown below [17] (Figure 1 manganese 0205mg, or 1020% of the RDI Process flow chart for jaggery powder preparation2024年9月2日 Manganese ores were collected from the Koira mines in the Sundargarh district of Odisha The process flow sheet for the present study is shown in figure 1The collected samples were in the form of lump ores which were first subjected to ball milling for ½ hr to produce ore fines of size −150 mesh sizesPyrometallurgical processing of manganese ore IOPscience
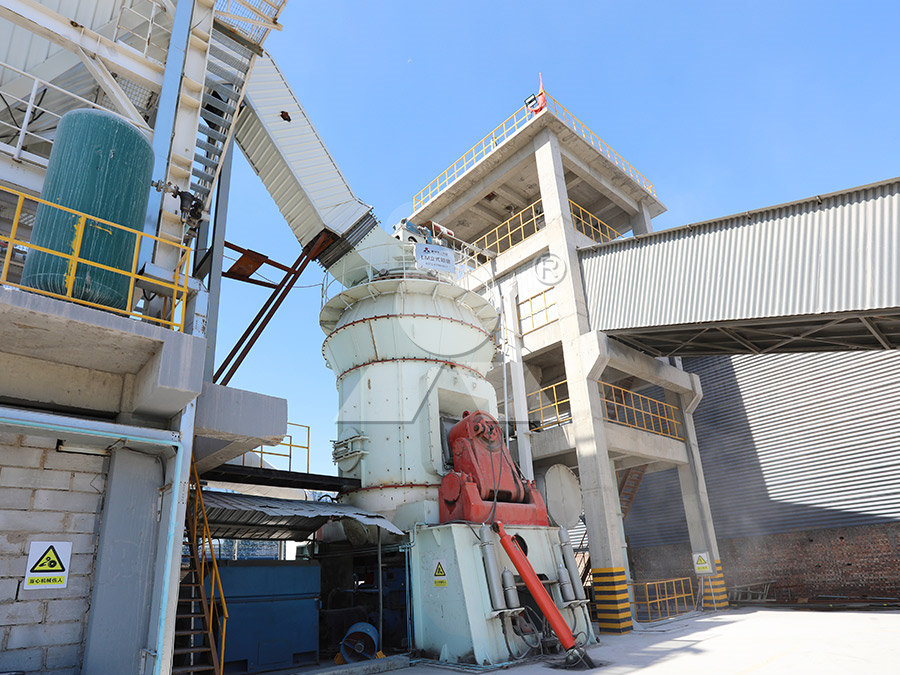
Nanomaterials through Powder Metallurgy: Production, Processing
2020年7月30日 Nanomaterials through Powder Metallurgy: Production, Processing, and Potential Applications toward Energy and Environment July 2020 DOI: 101007/978303011155712712015年7月25日 Over the full range of slag fractions, turbulent flow was obtained as a result of overall lower mixture viscosities and higher flow rates for lower slag fractions, compared to using the viscosity model from Pal A volumetric flow rate of 0032 m 3 s −1 was estimated when tapping only metal (SR = 0), decreasing to 0022 m 3 s −1 at a slag fraction of 05Modeling of Manganese Ferroalloy Slag Properties and Flow 2017年2月1日 PDF Spent Zn–MnO2 battery electrode powder, containing 301% of Mn and 256% Zn was was treated via reductive leaching by H2SO4 and selective Find, read and cite all the research you need Recovery Zinc and Manganese from Spent Battery Powder by It mainly beneficiates manganese ores containing nonmetallic impurities such as silicates The actual process flow may vary depending on the composition and characteristics of the ore Usually, the combined beneficiation process is used for manganese ore processing plant to maximize the mineral grade and recovery rateManganese Ore processing JXSC Machinery