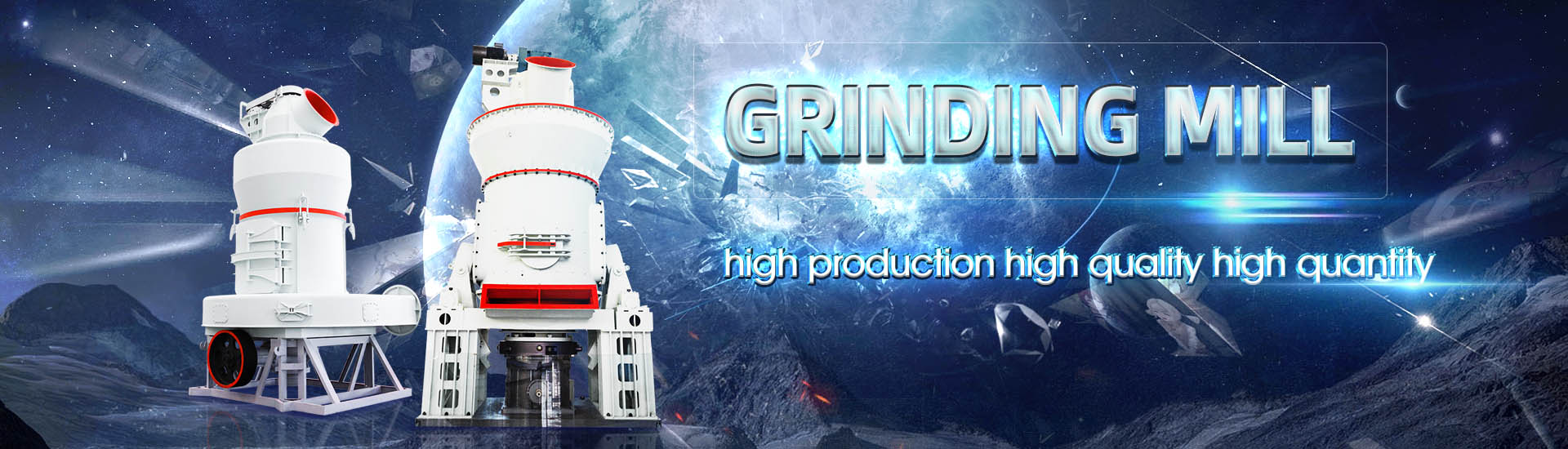
Calcite ore grinding ball consumption
.jpg)
Wet Grindability of Calcite to UltraFine Sizes in Conventional Ball
2015年7月29日 The influence of operating parameters such as operation speed (% of critical speed), ball filling ratio, calcite filling ratio, pulp density, ball size distribution, and grinding time on the grindability of calcite ore was systematically examined Experimental results were This study focused on ultrafine grinding of calcite powder (CaCO 3) using a vertical stirred ball mill The influences of various operating parameters such as stirrer speed (rpm), ball filling Optimization of Wet Grinding Parameters of Calcite Ore in Stirred 2015年7月4日 An experimental practice on the ultrafine wet grinding of calcite ore in a conventional batch ball mill is reported In this study, the effect of wet grinding conditions on the production of fine particles was researched The influence of operating parameters such as operation speed (% of critical speed), ball filling ratio, calcite filling ratio, pulp density, ball size Wet Grindability of Calcite to UltraFine Sizes in Conventional Ball 2013年12月18日 Fine grinding, to P80 sizes as low as 7 μm, is becoming increasingly important as mines treat ores with smaller liberation sizes This grinding is typically done using stirred mills such as the Isamill or Stirred Energy Use of Fine Grinding in Mineral Processing
.jpg)
Grinding Media in Ball MillsA Review [v1] Preprints
2023年4月24日 Grinding is the final stage of comminution, which reduces particle size to micron size level The size reduction is achieved by attrition, abrasion, and impact between the ore itself and between the ore particles and grinding media []According to Swart et al [], ball mills are mostly used because of their very high size reduction ratio, although they have a very low 2010年1月31日 Request PDF Effect of grinding aids on the grinding energy consumed during grinding of calcite in a stirred ball mill A series of wetgrinding experiments has been carried out on inorganic Effect of grinding aids on the grinding energy consumed during grinding 2021年4月21日 The purpose of this study was to investigate the dry grindability of calcite powders in a vertically and horizontally orientable laboratory batch type stirred mill The experimental results were evaluated using stress intensity analysis The performance was also compared in terms of mill orientation The results showed that the d50 values decreased with The Influence of Stirred Mill Orientation on Calcite Grinding2024年6月29日 Grinding media influence the energy consumption and efficiency of the grinding process during the calculation of the Bond Work index (BWi), a wellknown method for selecting comminution equipment, evaluating milling efficiency, and calculating required milling power Traditional grinding tests often choose steel balls as the grinding media, but ceramic balls are A New Approach to the Calculation of Bond Work Index with
.jpg)
Effect of grinding aids on the grinding energy consumed during grinding
DOI: 101016/JMINENG200909011 Corpus ID: ; Effect of grinding aids on the grinding energy consumed during grinding of calcite in a stirred ball mill @article{Choi2010EffectOG, title={Effect of grinding aids on the grinding energy consumed during grinding of calcite in a stirred ball mill}, author={H I Choi and W Lee and D Kim and 2013年8月3日 In Grinding, selecting (calculate) the correct or optimum ball size that allows for the best and optimum/ideal or target grind size to be achieved by your ball mill is an important thing for a Mineral Processing Engineer AKA Metallurgist to do Often, the ball used in ball mills is oversize “just in case” Well, this safety factor can cost you much in recovery and/or mill liner Calculate and Select Ball Mill Ball Size for Optimum Grindinging ball millsTumbling ball mills, which are often utilizedin wet and dry ultrafine grinding practices, have a relatively small power density due to limiting the power consumption by the number of revolutions of grinding media which are centrifugedatthechamberwallThus,inordertoproducefine andultrafinematerial,averylonggrindingtimeisneeded[1]The Influence of Stirred Mill Orientation on Calcite GrindingReducing Grinding Energy and Cost Magnetite Iron Ore Design Case Study A Jankovic and W Valery Metso Process Technology Innovation, PO Box 1028, Eagle Farm Qld, 4009, AustraliaReducing Grinding Energy and Cost Magnetite Iron Ore
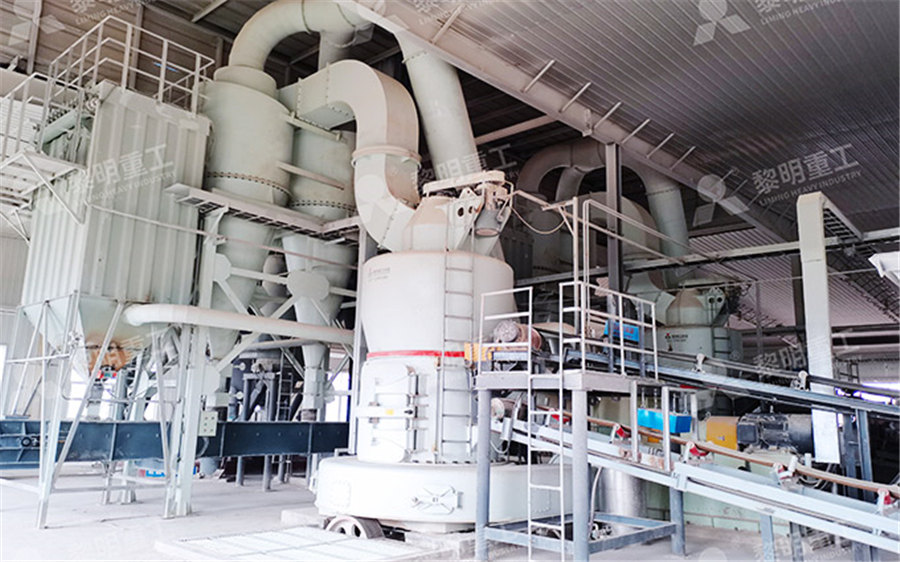
Grinding Media in Ball MillsA Review ResearchGate
Table 1 Chemical composition of typical grinding media (% wt) Adapted from [24] 211 Cast Iron Cast iron can be grey cast iron or white cast iron, but white cast irons are commonly used in Grinding capacity was maintained over the range 030% pebbles , by volume, with savings in energy and ball consumption increasing progressively 20 mm (40%), 32 mm (10%), and 40 mm (10%) for dry finegrinding of calcite ore Finer ball loads were unable to break coarser particles nipped in the feed Breakage rate is dependent on feed (PDF) A Review of the Grinding Media in Ball Mills for Mineral 2010年1月1日 Stirred ball mills have been used in recent years for grinding particles to submicron sizes due to their easier operation, simpler construction, higher grinding rate and lower energy consumption compared with other fine grinding machines (Choi, 1996, Bernhart et al, 1999, Shinohara et al, 1999, Choi and Wang, 2007, Choi et al, 2007, Shi et al, 2009, Effect of grinding aids on the grinding energy consumed during grinding 2014年10月27日 An experimental practice on the ultrafine wet grinding of calcite ore in a conventional batch ball mill is reported In this study, the effect of wet grinding conditions on the production of fine Wet Grindability of Calcite to UltraFine Sizes in Conventional Ball
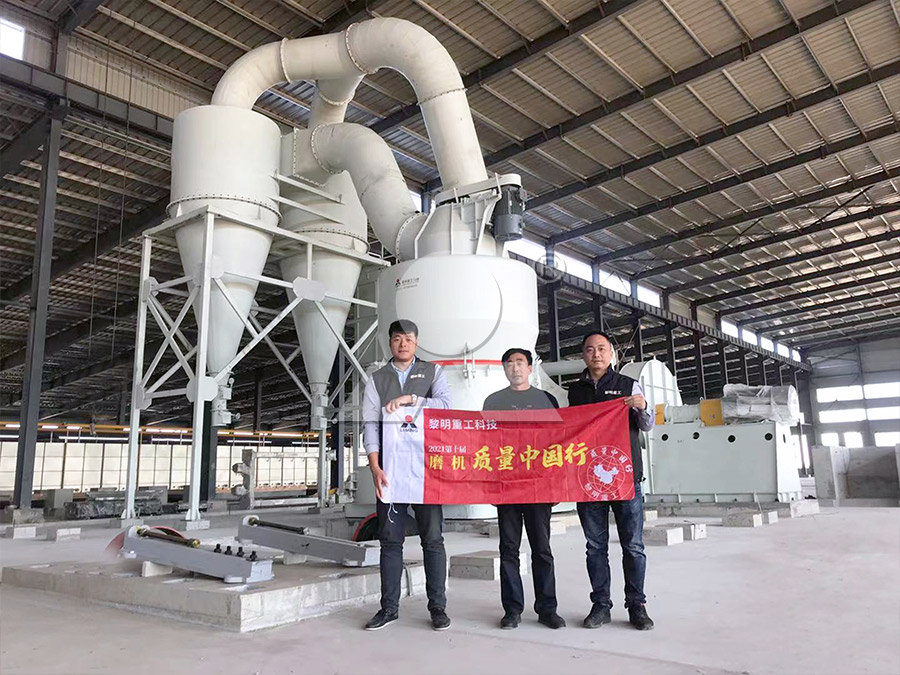
Consumption of steel grinding media in mills – A review
2013年8月1日 Apart from these cost factors, one of the major unsolved problems in the optimal design of ball mills concerns the equilibrium media size distribution in the mill, which is determined by the rate at which makeup media is added to the mill, as well as the rate at which these grinding media are consumed (Austin and Klimpel, 1985)Reliable prediction of grinding media 2023年7月20日 (2) Various working parameters of grinding mill, including fraction of critical speed for grinding mill, filling rate for grinding mill, grinding concentration, grinding cycle load, etc (3) And grinding material properties, including ore grindability, feeding particle size, etc Huge energy and steel consumption in ore grinding process greatly affect the subsequent separation Ore Grinding SpringerLink2024年11月11日 In evaluating ore grinding energy consumption using the Bond ball mill work index, discrepancies were identified As a result, an investigation into the determination method of Hou Ying (HY) wet ball milling work index (WHY) for Gongchangling magnetite ore was conducted to determine the correlation between WHY and grinding energy consumption at varying Exploring the Link between HY Wet Ball Mill Work Index and Grinding Grinding capacity was maintained over the range 030% pebbles , by volume, with savings in energy and ball consumption increasing progressively (40%), 20 mm (40%), 32 mm (10%), and 40 mm (10%) for dry finegrinding of calcite ore Finer ball loads were unable to break coarser particles nipped in the feed [68] 65 and 127 mm Breakage Grinding Media in Ball MillsA Review Academia
.jpg)
THE IMPACTS OF GRINDING BALL SIZE DISTRIBUTION ON ENERGY CONSUMPTION
THE IMPACTS OF GRINDING BALL SIZE DISTRIBUTION ON ENERGY CONSUMPTION, PRODUCT SIZE AND MEDIA WEAR WITHIN THE DRY STIRRED MILL Tolga SERT Master of Science, Mining Engineering Supervisor: Assoc Prof Okay ALTUN (January, 2021, 89 pages) In today's conditions, it is desired to use water resources more efficiently due to environmental 2017年1月17日 Other process activities, such as spraying the ore with water for dust control or the fact that runofmine ore moisture is approximately 2%5% are not generally considered (Bleiwas, 2012a)Breaking down energy consumption in industrial grinding mills2018年11月13日 The particle size distribution and energy consumption during grinding of the ground product were For tungsten ore grinding, /calcite mixture of 28–2 mm in the ballandrace mill is Breakage Characterization of Grinding Media Based on Energy Consumption 2009年7月1日 Request PDF Effect of grinding aids on the kinetics of fine grinding energy consumed of calcite powders by a stirred ball mill a b s t r a c t An experimental investigation was carried out on Effect of grinding aids on the kinetics of fine grinding energy
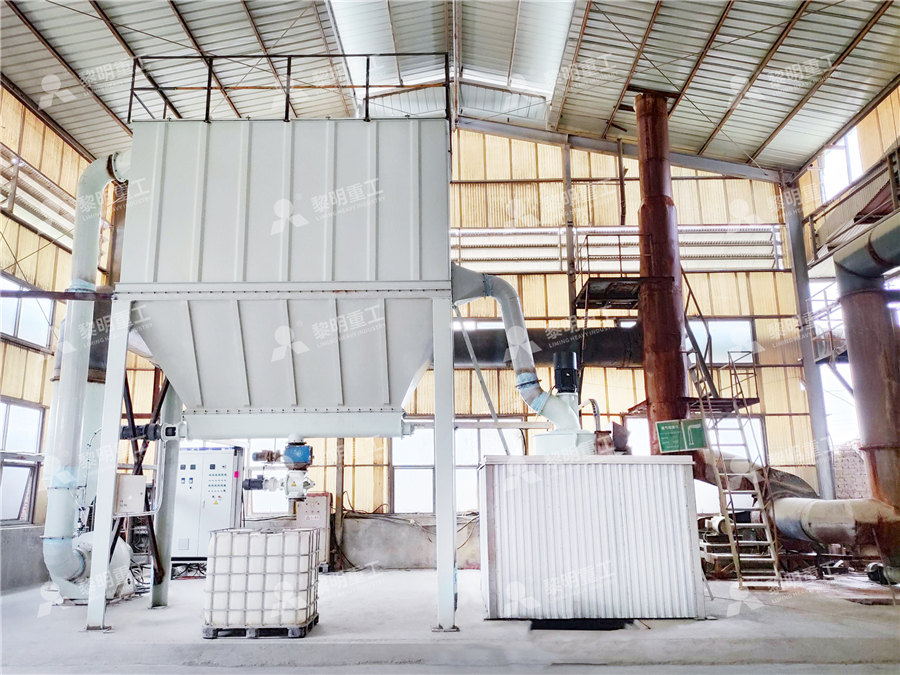
A Review of the Grinding Media in Ball Mills for
2023年10月27日 The ball mill is a rotating cylindrical vessel with grinding media inside, which is responsible for breaking the ore particles Grinding media play an important role in the comminution of mineral 2023年10月17日 3 Ultrafine Powder Grinding Mill Ultrafine powder mill (threering / fourring mediumspeed micropowder mill) feed particle size ≤25 mm, production capacity 0545 t/h, production fineness 1503500 mesh,it is a highefficiency and lowconsumption ultrafine powder processing equipment that successfully replaces the traditional jet mill and complex process How to choose a suitable ore powder grinding mill?DOI: 101016/JMINENG201603029 Corpus ID: ; An analysis of the energy split for grinding coal/calcite mixture in a ballandrace mill @article{Xie2016AnAO, title={An analysis of the energy split for grinding coal/calcite mixture in a ballandrace mill}, author={Weining Xie and Yaqun He and Zhenzhou Ge and Fengnian Shi and Yong Yang and Hong Li and Shuai Wang An analysis of the energy split for grinding coal/calcite mixture in 2018年6月18日 Ore pretreatment methods for grinding: journey and prospects, Mineral Processing and Extractive Metallurgy Review, DOI: 101080/2018 To link to this article: https://doior g/10 Ore Pretreatment Methods for Grinding: Journey and Prospects
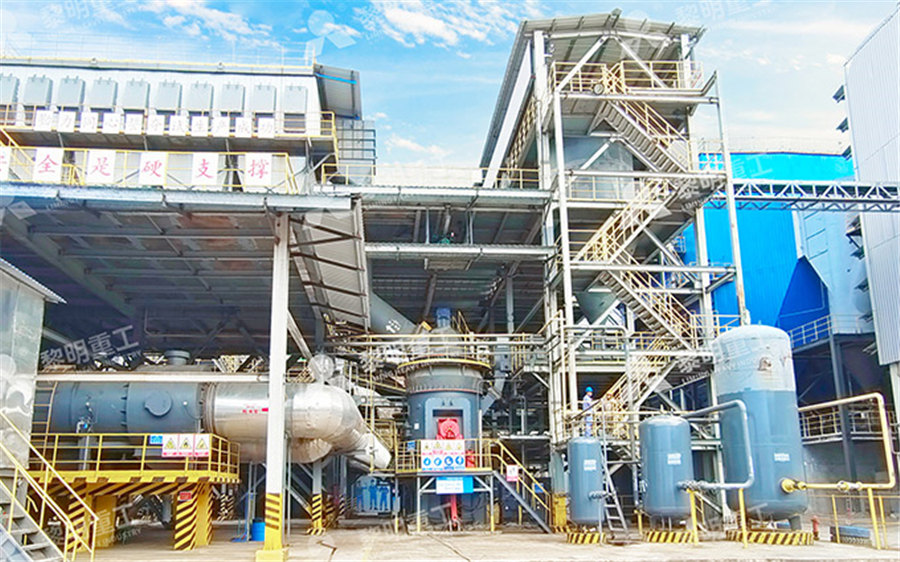
(PDF) Effect of wet ball milling on copper ore flotation by fractal
2023年3月15日 The examined parameters include grinding time, ball load, and solid weight percentage The collected fractal dimensions for particles ranged from 1 to 2, which is according to the principle of 2021年11月1日 A mineralogy, rheology, and energy consumptionbased experimental characterization of chalcopyrite ball mill grinding processes, in both batch and continuous flow processing modes, is carried out Experimental characterization of chalcopyrite ball mill grinding The energy consumption of grinding is the subject of many studies, especially in the case of ball mills for grinding clinkers [8,9], fuels [10], iron ore [11], hematite ore [12], sulfide ore [13 Effect of grinding concentration on the M (Pb) ResearchGate2021年12月11日 In experiments done by Si et al [98] using magnetite ores to determine the effect of grinding media diameter on the mineral liberation degree, 8 different sizes of steel balls were used ie The Effect of Grinding Media on Mineral Breakage Properties of
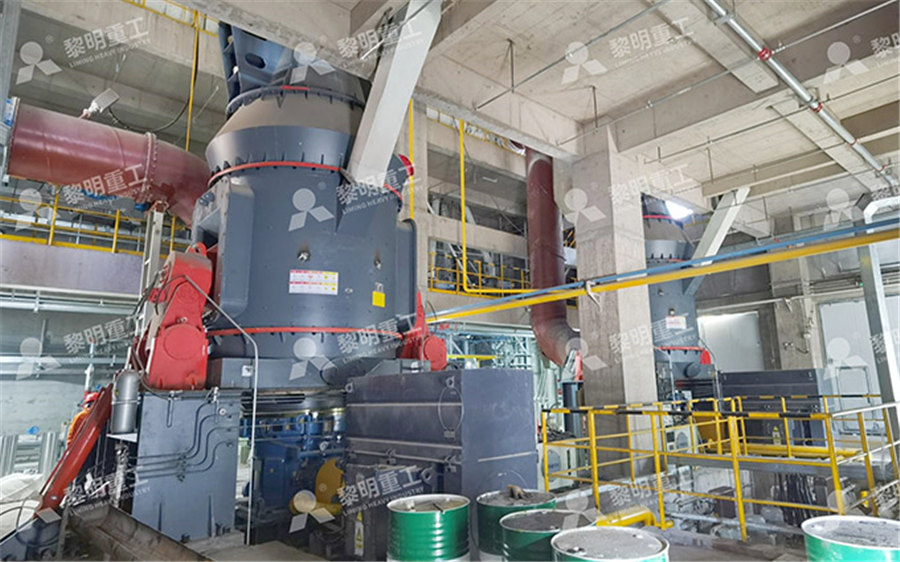
Jhamarkotra phosphate ore processing plant Nature
further reduction of power consumption to 32 kWh per metric ton of ore treated INTRODUCTION Beneficiation of phosphate ores containing carbonate gangue minerals such as calcite2023年1月8日 Particle size distributions of feed for calcite grinding by the stirred mill and ball mill (modified from [39,40] Mills used in this study (a) stirred mill [39], (b) ball mill [40] Figure 4(PDF) Comparison of Particle Shape, Surface Area, and 2017年4月4日 Grinding is an important operation with various industrial applications Literature studies indicate that grinding has an immense economic effect on the industry due to its high energy consumption, where approximately 5 to 6 % of the world electricity is consumed in mineral processing plants by using 80 % of this energy for crushing and grinding of raw materials In Rationalization of energy consumption in the grinding of some ores 2021年11月8日 Illite ore industrial grinding mill machine can grind illite into powder up to 3000 mesh, such as calcium carbonate, dolomite, calcite, marble, and so on Highpressure Suspension Roller Mill 80325 mesh HGM Ultrafine Grinding Mill 1503000 mesh CLUM Low consumption of grinding media, nonpolluting The temperature is low Illite Ore Industrial Grinding Mill Machine SBM Ultrafine
.jpg)
Grinding Kinetics Study of Tungsten Ore ResearchGate
2020年12月31日 As a result of this study, optimum grinding test conditions determined to be 70% of Nc, J=035 for ball filling ratio, 40 mm (10%), 32 mm (10%), 20 mm (40%), 12 mm (40%) for ball size distribution 2018年9月30日 Abstract This study focused on ultrafine grinding of calcite powder (CaCO3) using a vertical stirred ball mill The influences of various operating parameters such as stirrer speed (rpm), ball filling ratio (J), powder filling ratio (fc), solid ratio (wt%) and grinding time were studied under wet conditionsOptimization of Wet Grinding Parameters of Calcite Ore in Stirred Ball % 98824 0489 0388 0100 0065 0052 0022 0025 0020 0015 Grinding tests were carried out in a dry stirred ball mill both vertical and horizontal orientations with varyingThe Effect of Stirred Mill Orientation on Calcite Grinding2015年7月29日 The influence of operating parameters such as operation speed (% of critical speed), ball filling ratio, calcite filling ratio, pulp density, ball size distribution, and grinding time on the grindability of calcite ore was systematically examined Experimental results were evaluated on the basis of d 80 product sizeWet Grindability of Calcite to UltraFine Sizes in Conventional Ball
.jpg)
A specific energybased ball mill model: From batch grinding to
2016年2月1日 For instance, the power consumption of ball mill for grinding ceramic raw material is less than 80 kW [9] while a 5 m diameter and 84 m length ball mill consumes 39 MW of power for gold ore