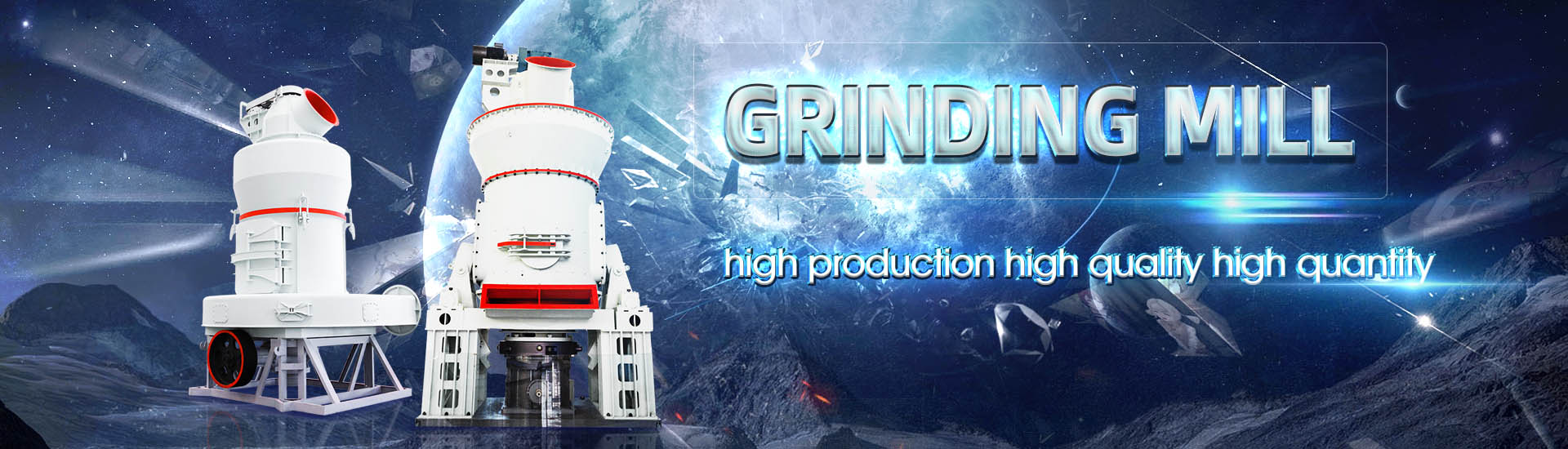
Instructions for use of highefficiency and energysaving ore grinding mill
.jpg)
Energy Use of Fine Grinding in Mineral Processing
2013年12月18日 Fine grinding, to P80 sizes as low as 7 μ m, is becoming increasingly important as mines treat ores with smaller liberation sizes This grinding is typically done using stirred mills such as the Isamill or Stirred 2022年1月1日 The results suggested that the highefficiency liberation of ore was obtained using the ceramicmedium stirred mill grinding technology, thus the efficient separation of iron and Highefficiency and energyconservation grinding technology 2022年3月30日 HPGR circuits can reduce the hard rock mining industry’s CO 2 emissions by up to 435% compared to SAG/Ball mill circuits Analysis of published data has confirmed that Helping to reduce mining industry carbon emissions: A stepby Today, it is possible to use grinding media as small as 1 mm How do they perform in industrial grinding mills? The use of small grinding media (5 12 mm), called Millpebs, in regrind mills ENERGY SAVINGS AND TECHNOLOGY COMPARISON USING
.jpg)
Metso comminution solutions Grinding
Stirred mills have proven to provide energy savings when compared with traditional grinding mills Metso engineers and manufactures both types of stirred mills, delivering industryleading 2017年11月2日 We use a review of the pertinent literature to summarize the state of the art and to determine the best practices to measure and benchmark energy efficiency This chapter EnergyEfficient Comminution: Best Practices and Future Springer2021年9月5日 This experimental work is in line with the Sustainable Development Goal of UN, SDG12: Responsible Consumption and Production and aims to improve the efficiency of ore Modeling of Bauxite Ore Wet Milling for the Improvement of 2017年1月17日 This paper analyses how properly designed control systems allow a better usage of the capacity of grinding circuits, and a reduction of the specific energy consumption even withoutBreaking down energy consumption in industrial
.jpg)
Grinding Modeling and Energy Efficiency in Ore/Raw
2022年8月31日 The main concern in ore beneficiation and processing plants is producing the desired product size with the lowest possible energy consumption It has been estimated that grinding consumes up to 4% of global electrical 2021年3月23日 New ball mill drive system with the prototype energysaving SMH motor [37] Startup of the LSPMSM SMH1732T motor with a filled ball mill after two hours of downtime: (a) active power, (b Energy Efficiency Analysis of Copper Ore Ball Mill Drive Systems2019年11月27日 In recent years, the increasing interest for energy efficiency has multiplied the number of players and the issuing of legislative documents, so the very notion of “efficiency” has taken different meanings in a more or less Efficiency, Energy Saving, and Rational Use of 2023年7月20日 Ore grinding process falls into opencircuit and closedcircuit grinding The grinding products of the former are directly processed in the next processing procedure without returning to the grinding mill After the grinding products of the latter are classified, the coarse particles are returned to the grinding mill for regrindingOre Grinding SpringerLink
.jpg)
Comparison of energy efficiency between ball mills and stirred
2009年6月1日 Request PDF Comparison of energy efficiency between ball mills and stirred mills in coarse grinding Stirred mills are primarily used for fine and ultrafine grinding They dominate these 2018年7月1日 Among the industries, the nonmetallic industry was reported as the third largest energy user and accounted for about 12% of the global energy use [1]Within this portion, cement industry had the majority of the utilization with 85–12% [1], [2]US Energy Information Administration (EIA) [7] named cement industry as the most energy intensive among the Energy and cement quality optimization of a cement grinding circuitLearn how homeowners can make energy saving changes and take advantage of rebates and incentives Learn More about Home Upgrades November 23, 2024 The Energy Savers' DoItYourself (DIY) Projects offer easy, stepbystep instructions to home energy efficiency improvements that will save you energy and money June 24, 2024 Have more questions?Energy Savings Hub Department of Energy2021年11月1日 A pilotscale grinding technology of ceramic medium stirred mill was proposed in this study Based on the specific productivity and grinding efficiency, the appropriate grinding parameters were Highefficiency and energyconservation grinding technology
.jpg)
ENERGY SAVINGS AND TECHNOLOGY COMPARISON USING SMALL GRINDING
In ball mills, energy savings vary from 10 per cent to 40 per cent compared to 25 mm media A regrind ball mill with a mix of small grinding media can be as energy effi cient as an Isa Mill charged with 25 and 35 mm beads In vertical stirred 2021年9月5日 Size reduction is a necessary operation in mineral processing plants and provides the desired size for separation operations and the liberation of the valuable minerals present in ores Estimations on energy consumption indicate that milling consumes more than 50 % of the total energy used in mining operations Despite the fact that ball milling is an efficient Modeling of Bauxite Ore Wet Milling for the Improvement of 2024年5月31日 This paper presents an industrial verification test, adding a high pressure grinding roll and magnetic separation operation after the thirdstage fine crushing operation to reduce the particle size of ball mill feed and improve the processing capacity of grinding operation The optimal process parameters of high pressure grinding roll and magnetic separation were High Pressure Grinding Roll and Magnetic Separation for Energy Saving PDF On Aug 1, 2013, Ernst Worrell and others published Energy Efficiency Improvement and Cost Saving Opportunities for Cement Making An ENERGY STAR® Guide for Energy and Plant Managers Find (PDF) Energy Efficiency Improvement and Cost
.jpg)
EnergyEfficient Advanced Ultrafine Grinding of
2023年7月10日 The present literature review explores the energyefficient ultrafine grinding of particles using stirred mills The review provides an overview of the different techniques for size reduction and the impact of energy 2010年10月1日 Download Citation Applications of Efficient EnergySaving Cement Grinding Technology and Equipment Joint grinding system is the preferred cement grinding system of current cement process Applications of Efficient EnergySaving Cement Grinding2009年6月1日 At product sizes finer than 80% passing 75 μm, the efficiency of ball mill grinding rapidly decreasesThe practical limit to ball mill product fineness is considered to be 40–45 μm (Gao and Weller, 1994)Although ball mills can still be found in the regrind circuits in a number of mineral processing plants, their energy consumption is high, and size reduction efficiency is parison of energy efficiency between ball mills and stirred For the Bond ball mill, the net energy consumptions were determined from the mill revolution data at which the Bond tests Table 2 Comparison of the measured energy consumptions of Bond ball mill with vertical shaft stirred mill in coarse grinding duty Ore GC2 Mill type Ball mill Stirred mill Ball mill GHB Stirred mill SMT Ball mill Stirred (PDF) Comparison of energy efficiency between ball mills and

(PDF) Grinding Media in Ball MillsA Review ResearchGate
2023年4月23日 It consumes most of the energy used in mineral processing plants with grinding using up to 50% of the provided energy Tumbling mills are an old technology that is still commonly used for grinding2024年2月5日 Energysaving grid ball mill is a kind of grinding equipment widely used in industrial production It has the advantages of energy saving, high efficiency, and environmental protection However, inHow to Improve Working Efficiency of EnergySaving Grid Ball 2002年11月1日 Average ore loss in mining 19%;average ore loss in mineral processing 10% Energy wastage in Mining and Mineral Processing A vast amount of energy is consumed in mining industry, eg, in the USA The energy efficiency of ball milling in comminution2021年2月26日 Milling is among the most energyconsuming technological stages of copper ore processing It is performed in mills, which are machines of high rotational masses The start of a mill filled to capacity requires appropriate solutions that mitigate the overloading One method for increasing the energy efficiency of ball mills is to optimize their drive systems This article Energy Efficiency Analysis of Copper Ore Ball Mill Drive
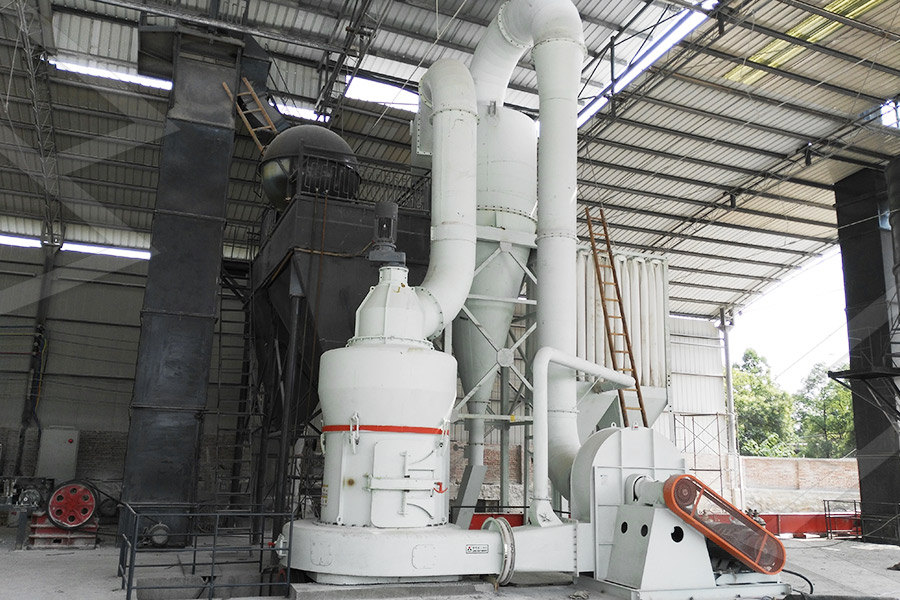
Grinding Modeling and Energy Efficiency in Ore/Raw Material
2022年8月31日 Therefore, any research effort that has the potential to reduce energy consumption while maximizing grinding efficiency is of great importance This Special Issue welcomes papers that highlight innovations and future trends in modeling grinding and technological ways to improve the grinding efficiency in ore/raw material beneficiation2022年1月1日 A pilotscale grinding technology of ceramic medium stirred mill was proposed in this study Based on the specific productivity and grinding efficiency, the appropriate grinding parameters were ascertained as follows: material ball ratio of 07, ceramic ball medium size ratio (10 mm: 15 mm: 20 mm = 3:2:5), stirring speed of 110 rpm, grinding concentration of 50%, Highefficiency and energyconservation grinding technology using 2022年3月1日 High Pressure Grinding Rolls (HPGR) circuits have the potential to reduce the Mining Industry’s CO2 emissions by up to 345 megatonnes/year, or 435% when compared to the established Autogenous Helping to reduce mining industry carbon emissions: A small grinding media represents the best potential to improve grinding efficiency How do the small grinding media perform in industrial grinding mills? The use of small grinding media in regrind mills proved that finer grinding can be achieved at lower energy consumption In ball mills, smaller grinding media versus 25 mm media generate aEnergy Savings and Improved Recovery with Small Grinding Media
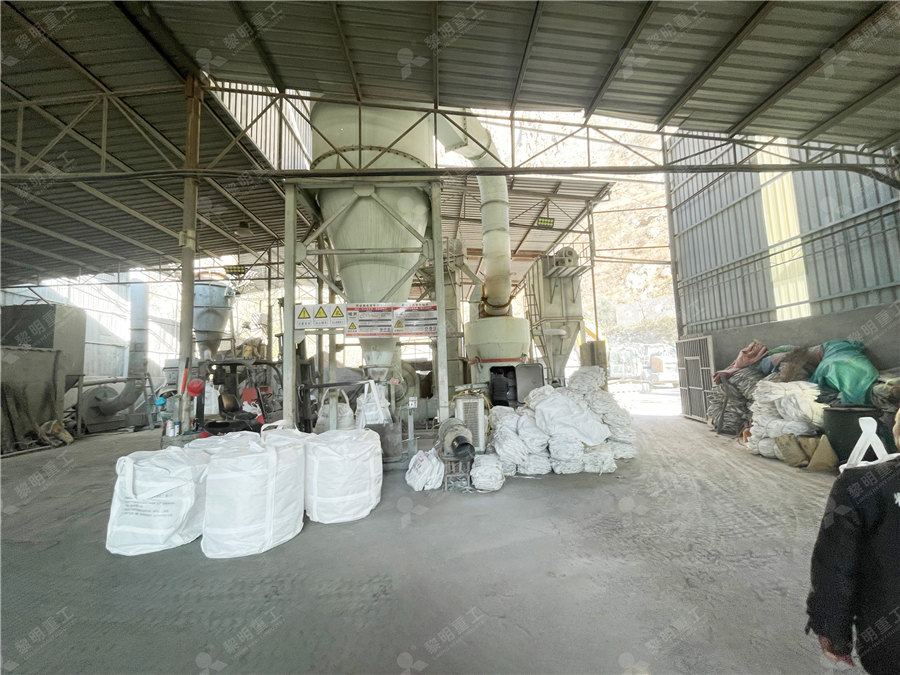
(PDF) Energy efficiency of highrise buildings ResearchGate
2018年3月6日 This helps to identify the main techniques used for the construction of energyefficient residential buildings a compact planning solution, highly efficient building insulation, “intelligent 2021年4月29日 The ball mill is a rotating cylindrical vessel with grinding media inside, which is responsible for breaking the ore particles Grinding media play an important role in the comminution of mineral A Comparative Study of Energy Efficiency in Tumbling Mills with the Use Energies 2021, 14, 1786 3 of 14 ring gear is engaged with a pinion gear In versions with lowspeed motors, the pinion is set on a shaft directly connected to the motor, and in versions with highspeed motors theEnergy Efficiency Analysis of Copper Ore Ball Mill Drive Systems2017年7月1日 It is also worth mentioning that the omnipresent conven tional grinding mill is infamous for being a very energy inefficient process, regardless of the reference used, ie: • minimum energy for generating new mineral surfaces: 1 to 2 % (Fuerstenau and Abouzeid, 2002; Tromans and Meech, 2004); • energy for producing new surface area by the com pression Reducing the energy footprint of grinding circuits: the process
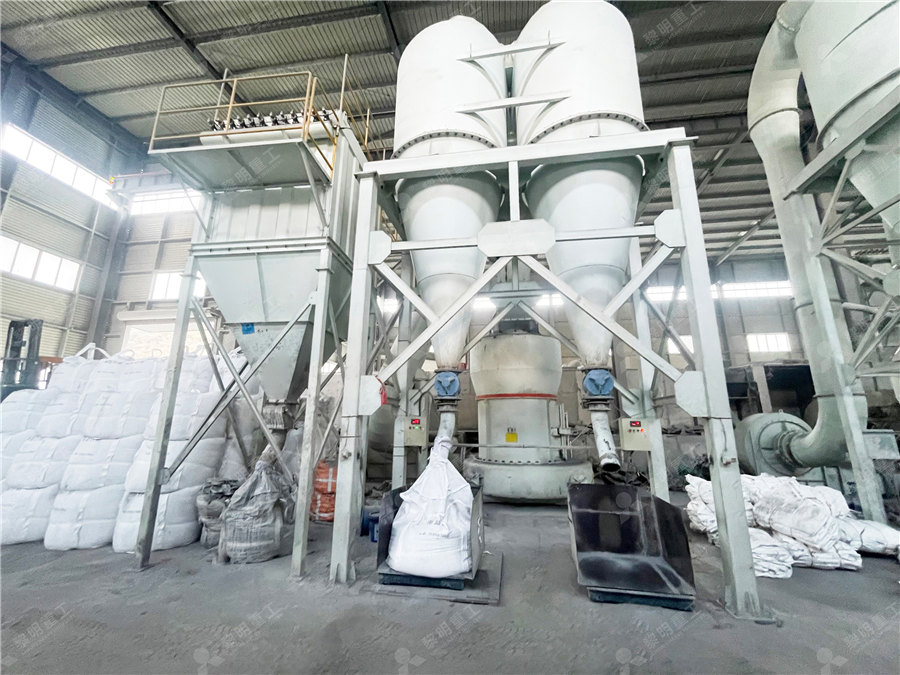
ENERGY SAVINGS AND TECHNOLOGY COMPARISON USING SMALL GRINDING
In ball mills, energy savings vary from 10 per cent to 40 per cent compared to 25 mm media A regrind ball mill with a mix of small grinding media can be as energy effi cient as an Isa Mill charged with 25 and 35 mm beads In vertical stirred 2023年11月1日 Grinding operation is the last preparation stage before beneficiation In this stage, the material undergoes the combined action of impact and grinding, so that the ore particle size is diminished and the qualified materials is provided for succeeding beneficiation operations [1, 2]Generally, the quality of the grinding product is also an important factor to determine the Energy conservation and consumption reduction in grinding 2022年3月30日 All industries are facing increasing pressure to ensure that carbon emissions are reduced to help achieve the socalled 15 °C future This has led to most of the major mining companies committing to significant reductions in their operational carbon footprint – in many cases by up to 30–40% in the next 10–15 years and to place themselves in a netzero scope Helping to reduce mining industry carbon emissions: A stepby 2023年2月26日 Grinding has been extensively applied to meet the urgent need for tight tolerance and high productivity in manufacturing industries However, grinding parameter settings and process control still depend on skilled workers’ engineering experience The process stability in complicated nonuniform wear can't be guaranteed Moreover, it is impossible to obtain Development of grinding intelligent monitoring and big data
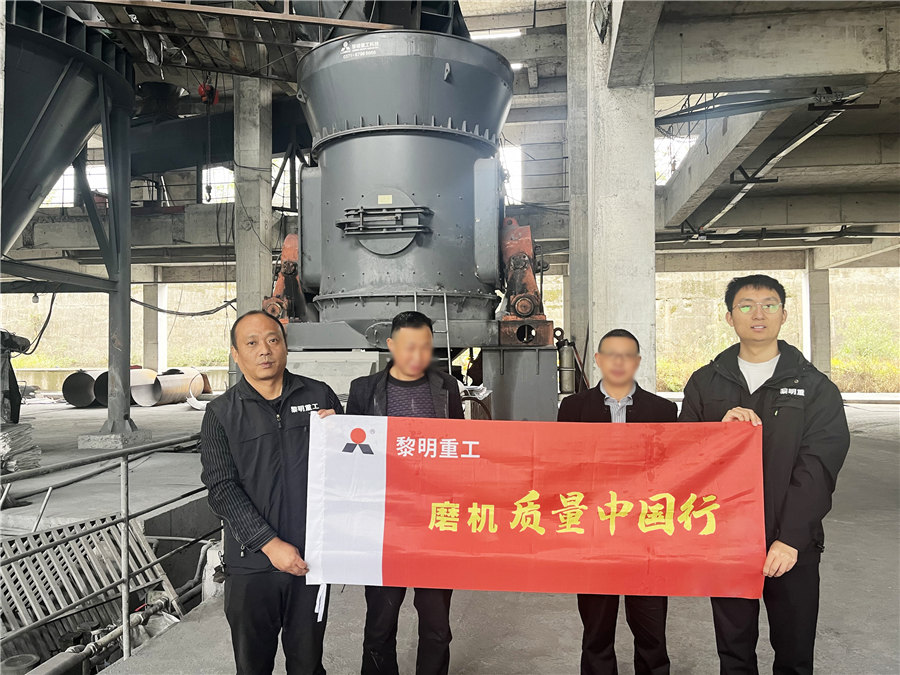
3 Implement energy savings energygovau
Doors not properly sealed are the most common energy drain for fridges Use timers on equipment A single computer and monitor left on 24 hours a day can cost over $200 a year Set computers and other equipment to automatically turn off at the end of the day and use ‘energysaving’ modes for photocopiers and printers2023年2月23日 Replacing outdated motors on feed processing equipment with highefficiency motors and variable speed drives (VSD), which match input power to the operational requirements, holds vast potential for feed millers “Too 3 ways to improve feed mill energy efficiency2024年1月31日 Ceramic ball milling has demonstrated remarkable energysaving efficiency in industrial applications However, there is a pressing need to enhance the grinding efficiency for coarse particles This paper introduces a novel method of combining media primarily using ceramic balls supplemented with an appropriate proportion of steel balls Three grinding media Enhancing the Grinding Efficiency of a Magnetite SecondStage Mill Grinding efficiency is the unit energy consumption rate of the mill, which represents the amount of material with a particle size of 0043 mm newly generated for every 1 kW•h of energy consumed Energy conservation and consumption reduction in grinding
.jpg)
Metso comminution solutions Grinding
and ultrafine grinding efficiency The SMD utilizes the rotational energy of impeller arms to impart a highenergy motion to the mixture inside the mill With its simplistic design and long maintenance intervals, SMD series provides the highest level of availability in the market Up to 40% higher energy efficiency Up to 250 microns feed sizeEnergy savings are at the heart of the multiple benefits of energy efficiency and link to many other economic, social and environmental benefits Energy efficiency reduces energy use worldwide Globally, energy efficiency improved by an estimated 13% between 2000 and 2017Energy savings – Multiple Benefits of Energy Efficiency – 2022年3月29日 Abstract The results of industrial comparative tests of batches of grinding balls with a diameter of 40, 60, and 80 mm from chromium–molybdenum steel of the nominal grade ShKhM and balls of the current manufacture from rail steel in the first chambers of drum mills while grinding of cement are presented As the test results showed, total specific consumption Efficiency of the Use of HighQuality Grinding Balls from Chrome 2019年6月21日 They use rotational energy created by impeller arms to impart a highenergy motion to the media/slurry mixture inside the mill This results in particletoparticle shear and compressive forces Grinding down energy consumption in comminution
.jpg)
Flowsheet considerations for optimal use of high pressure grinding
2010年8月1日 Also, the possibility of fine grinding at a relatively low energy input and high capacity, such as in iron ore pellet feed preparation, further expands the use of the technology Finally, the additional advantages to the downstream process, such as a reduced ball mill work index for subsequent grinding or enhanced leaching performance in gold treatment, makes the