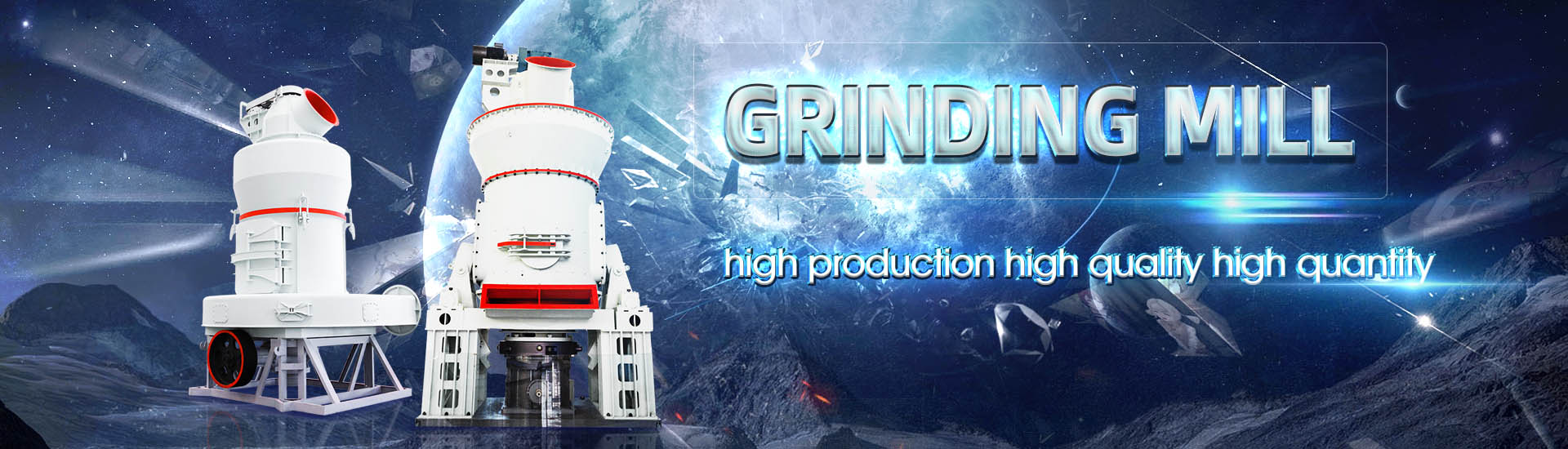
Low speed grinding steel ball ratio
.jpg)
Investigating the Influence of Medium Size and Ratio
2024年8月27日 This study explores the effect of steel ball size and proportion on mineral grinding characteristics using Discrete Element Method (DEM) simulations Based on batch grinding kinetics, this paper analyzes the contact 2023年10月27日 Chenje et al compared five types of grinding media balls (eutectoid steel, lowalloy steel, mediumchromium cast iron, cast semisteel and unalloyed white cast iron) and A Review of the Grinding Media in Ball Mills for Mineral Processing Steel and other metal balls are the most frequently used grinding media with sizes of the balls ranging from 10 to 150 mm in diameter [30] Cylpebs are slightly tapered cylindrical grinding Grinding in Ball Mills: Modeling and Process Control Sciendo2020年5月1日 Too small a material ball ratio increases the probability of ballball collision, which not only reduces the processing capacity of the mill but also increases direct impact, ballto Enhancing the capacity of largescale ball mill through process
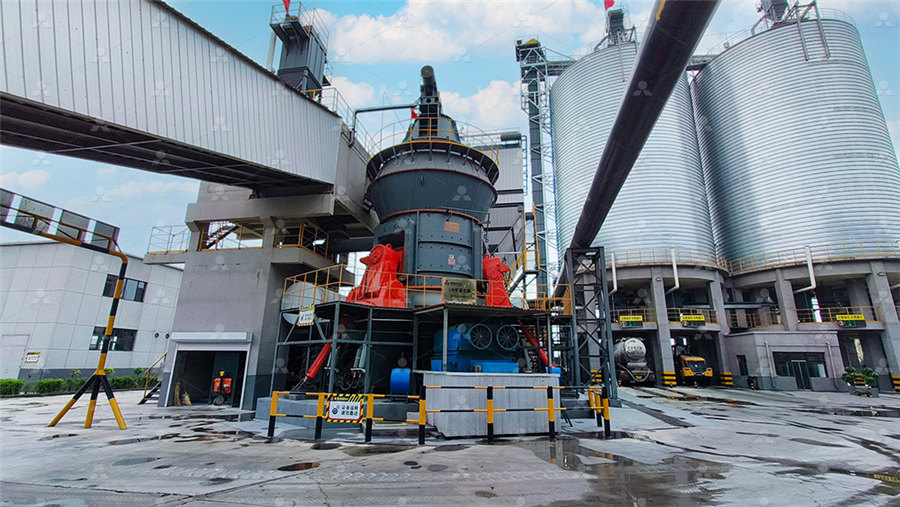
Effect of Ball Milling Mechanism on the Density and Hardness of Al
2022年9月13日 Present work aims to improve density and hardness of Al matrix by changing rotational speed and milling time Two mechanisms, lowspeed ball milling (LSBM) and dual 2023年9月29日 Section 4 summarizes the behavioral change phenomenon and grindability considering speed effect, size effect, tribological and thermal impact These three stages of Mechanical behavior and modeling of grinding force: A 2021年2月19日 Optimization results confirmed that the balls to powder weight ratio were the most influential process parameter The optimum process parameters setting concluded that Comparative Study on Improving the Ball Mill Process Parameters 2021年10月1日 Grinding is a process where the particle size of the material is reduced under the combined effects of the impact action and the abrasion action of steel balls (grinding medium) Research on the characteristics of particles size for grinding
7TOCS.jpg)
Highspeed grinding: from mechanism to machine tool
2024年10月5日 Highspeed grinding (HSG) is an advanced technology for precision machining of difficulttocut materials in aerospace and other fields, which could solve surface burns, defects and improve surface integrity by increasing the linear speed of the grinding wheel The advantages of HSG have been preliminarily confirmed and the equipment has been built for 2024年8月27日 This study explores the effect of steel ball size and proportion on mineral grinding characteristics using Discrete Element Method (DEM) simulations Based on batch grinding kinetics, this paper analyzes the contact Investigating the Influence of Medium Size and Ratio quartz are subjected to lowspeed grinding using the ball mill technique where reveals that when D (size of steel ball) = 25 mm and n (rotation speed of mill) ≤ 1234 rpm, the steel balls inside the mill attain the of the two minerals is defined as the ratio between the new yields of two minerals at the 0074 mm size per unit time PAPER OPEN ACCESS You may also like IOPscienceTo really choose, I guess it depends on the material and your mill (vial, RPM, media, filling volume) Ie Si80Ge20 is easily alloyed in the high energy SPEX millBest way to determine the balltopowder ratio in ballmilling?
.jpg)
The Ultimate Guide to Ball Mills Miningpedia
2019年8月14日 Common steel ball materials Specific 1 Low chromium cast ball Assuming the rotation speed of the ball mill is fixed, When the nonsmooth ball mill liner is used, the grinding ball filling ratio is 4050%, and the grinding concentration is relatively large, 2002年7月1日 For example, the MBroseghini et al [21] claimed that the movement of the ball in favor of grinding was cataracting regime and the reasonable value of the rotational speed ratio of the supporting Effects of rotational direction and rotationtorevolution speed ratio 2022年10月13日 The friction coefficient is one of the key parameters in the tribological performance of mechanical systems In the condition of light normal load and low rotation speed, the friction coefficients of ballondisc with rough surface in dry sliding contact are experimentally investigated Friction tests are carried out under normal load 2–9 N, rotation speed 20–48 rpm Experimental Investigation into the Friction Coefficient of Ballon 2018年6月4日 Table 3 shows the recommended speed Ratios for various grinding wheel specifications Hard wheel specifications, like diamond vitrified and metalbond wheels, are typically dressed at a negative speed ratio where the dressing forces are lowest to help improve dresser tool life Table 2 – Speed ratio impact on grinding processOptimizing grinding and dressing with 'dressing speed ratio'
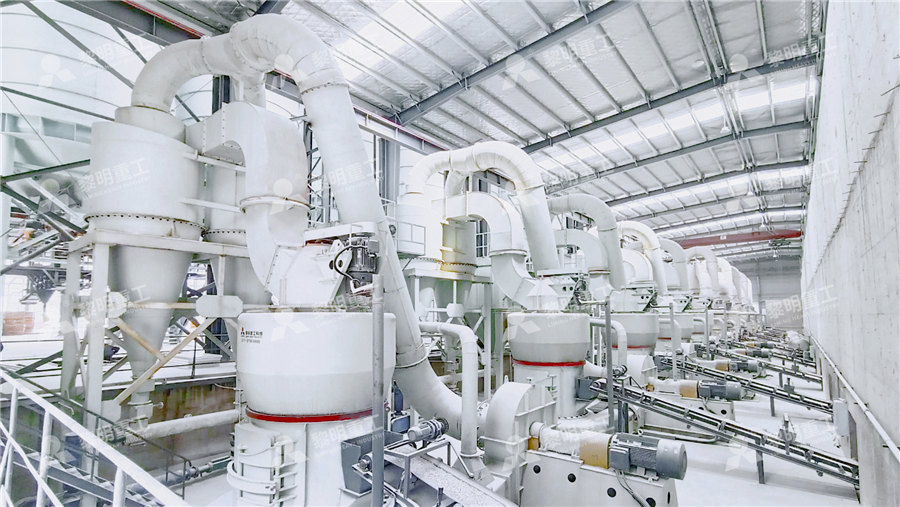
Grinding in Ball Mills: Modeling and Process Control Sciendo
55 known as the distribution function [45, 46]) describes the distribution of fragment sizes obtained after a breakage of particles of size xjThus, b1j, b2j, , bnj are the mass fractions of particles in size classes 1, 2, , n after a breakage of particles in size class j The mechanism of breakage is illustrated in [23] by a diagram shown in Fig 32021年3月26日 Ball mill grinding efficiency is influenced by many factors: ore grindability, feed size, grinding product size, ball mill diameter and length, ball mill working speed, liner type, steel ball loading system, grinding concentration, return sand ratio in closedcircuit grinding and feed rate (Ball mill) To improve the ball mill grinding efficiency, you must first understand the What Factors Will Influence Ball Mill Grinding Efficiency?The effect of relative rotational speed, the ratio of actual speed to critical speed, was found to be complex At loadings between 04 and 08, the grinding rate was a maximum at a relative rotation speed of about 08, although at lower loadings the grinding rate Ball Mill an overview ScienceDirect TopicsTable 1 Chemical composition of typical grinding media (% wt) Adapted from [24] 211 Cast Iron Cast iron can be grey cast iron or white cast iron, but white cast irons are commonly used in Grinding Media in Ball MillsA Review ResearchGate
.jpg)
AMIT 135: Lesson 7 Ball Mills Circuits – Mining Mill
In ball mills, steel balls or hard pebbles to break particle based For primary grinding, the ratio could vary between 1 ↑029 (W↓i) ↑04 / (νD) ↑025Where ν = the rotational speed of the mill Ball Bulk Density Low under LowSpeed Grinding Condition Minerals 2023, 13, steel ball consumption, and grinding a medium filling ratio of 35%, grinding concentration of 75%, Study on Grinding Behavior Characteristics under LowSpeed Grinding 2021年6月29日 Under optimum conditions of +60 mm material suitable for a 100 mm ball diameter, −60 + 20 mm material suitable for an 80 mm ball diameter, −20 mm material suitable for a 70 mm ball Effects of Mill Speed and Air Classifier Speed on Performance of 2023年11月24日 Steel grinding media are usually forged, and waterquenched Their properties are governed by their carbon content, alloying element content, and heat treatment Most commercial grinding media at present are produced from martensitic lowalloy steels The grinding media can adapt to most milling conditions and have a favourable costtowear ratioGrinding Media in Ball Mills for Mineral Processing
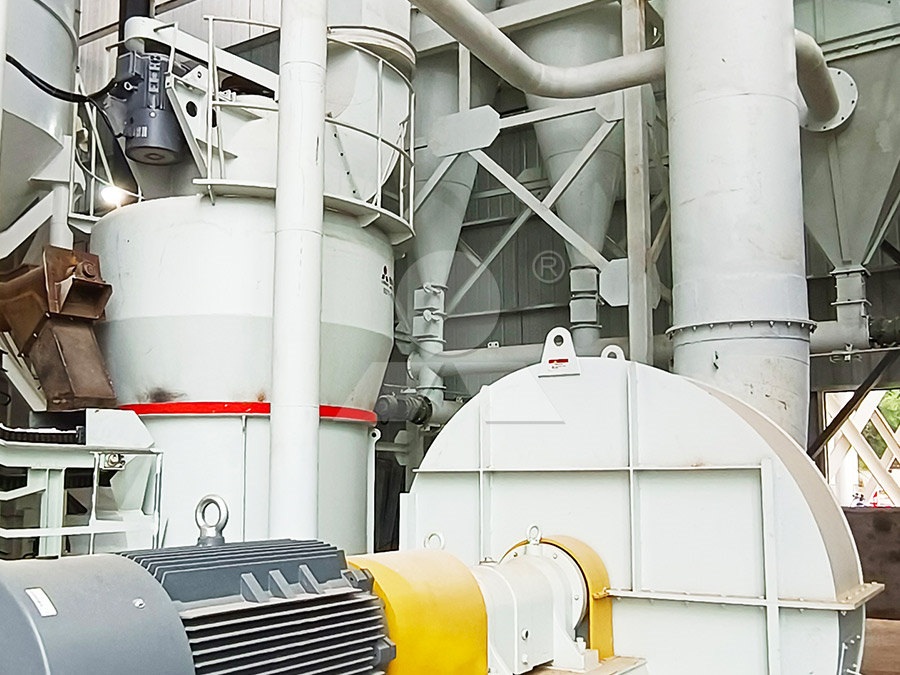
How do you calculate ball mill grinding media?
2023年6月16日 Choose the Appropriate Grinding Media Size: Select grinding media balls that are suitable for your mill and desired particle size Keep in mind factors such as ball diameter, balltomaterial ratio, and mill speed, as these can affect the grinding kinetics and efficiencyball mill employs steel balls to generate a grinding action, ie ore particle comminution via impact and abrasion with steel balls, and is a key component of beneficiation plant production Even though it has massive benefits, such as a high reduction ratio, effective breakage impact, and a wide application (Fuerstenau andEfect of grinding media on the milling eficiency of a ball mill2017年10月26日 The following are factors that have been investigated and applied in conventional ball milling in order to maximize grinding efficiency: a) Mill Geometry and Speed – Bond (1954) observed grinding efficiency to be a function of ball mill diameter, and established empirical relationships for recommended media size and mill speed that take this factor into Factors Affecting Ball Mill Grinding Efficiency2020年3月21日 Ball mill's low grinding efficiency, low processing capacity, high production energy consumption, unstable product fineness, etc are problems that many customers will encounter How to effectively improve the grinding efficiency of the ball mill is an important issue Now, let's share 10 ways to improve the grinding efficiency of the ball mill!Top 10 tips to improve the grinding efficiency of ball mill
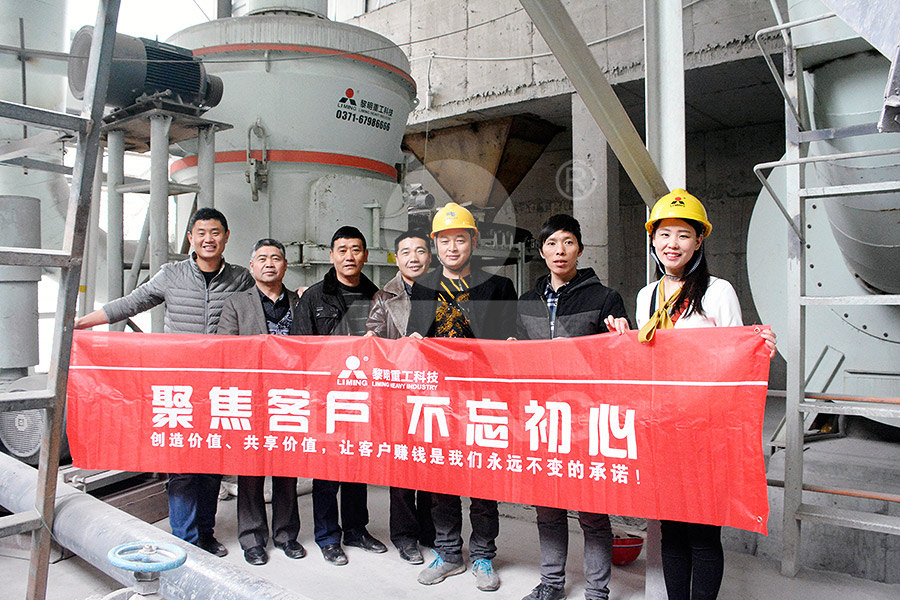
10 Ways to Improve the Grinding Efficiency of Your
Step#3 Reasonable filling rate of steel ball Step#4 Reasonable size and proportion of steel ball Step#5 Refill steel ball accurately Step#6 Appropriate grinding density Step#7 Optimize the grinding process Step#8 Improve the 2013年8月3日 In Grinding, selecting (calculate) the correct or optimum ball size that allows for the best and optimum/ideal or target grind size to be achieved by your ball mill is an important thing for a Mineral Processing Engineer AKA Calculate and Select Ball Mill Ball Size for Optimum Emery wheel is the important tool in the mechanical workout, and it relies on wedding agent that the abrasive material of loose granule shape is combinedOwing to receives bigger surging force during wheel grinding, and need high speed rotating, thereby its intensity is to ensure safety and the prerequisite of effectively using; Steel ball is the vitals of modern mechanical industrial Ceramic binder for steel ball grinding wheel Google Patentsball mill employs steel balls to generate a grinding action, ie ore particle comminution via impact and abrasion with steel balls, and is a key component of beneficiation plant production Even though it has massive benefits, such as a high reduction ratio, effective breakage impact, and a wide application (Fuerstenau andEffect of grinding media on the milling efficiency of a ball mill Srce
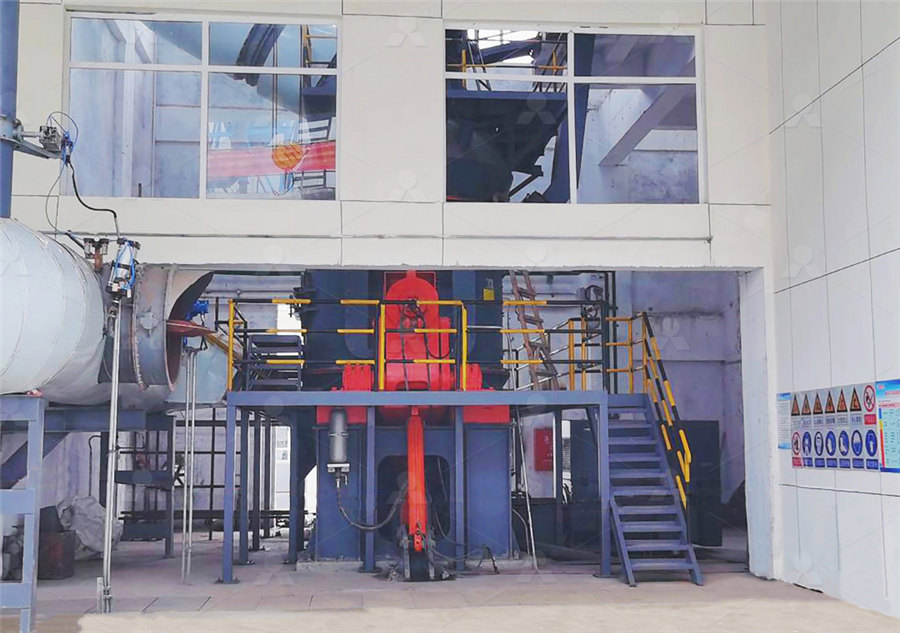
Comparative Study on Improving the Ball Mill Process Parameters
2021年2月19日 The grinding balls are made of steel with a 20 mm diameter In this study, (2 Liters) has the value of SN ratio as (12915) and ball mill speed with (105 RPM) has the value of SN ratio as (13386) furhter showing moderate effect on the signaltonoise ratio2019年11月9日 As shown in Fig 3, the cylindrical grinding experimental setup consisted of a rotary axis developed by Dewar et al [] mounted on the bed of a Blohm Planomat 408 CNC grinding machineAluminum oxide Radiac WRA60J5W grinding wheels were used to grind precision ground AISI 1045 steel workpieces (Table 1)A 51% concentrated CIMTECH 310 Investigation of the effect of speed ratio on workpiece surface 2024年1月31日 Ceramic ball milling has demonstrated remarkable energysaving efficiency in industrial applications However, there is a pressing need to enhance the grinding efficiency for coarse particles This paper introduces a novel method of combining media primarily using ceramic balls supplemented with an appropriate proportion of steel balls Three grinding media Enhancing the Grinding Efficiency of a Magnetite SecondStage 2023年7月27日 In the ball grinding process, because the steel ball has 360° free rotation, it is suitable for falling motion and throwing motion When the rotating speed of the cylinder is low, the medium rises to a certain height along the circular track with the rotation of the cylinder, falls freely along the surface of the medium layer in the mill under Ball Grinding Process SpringerLink
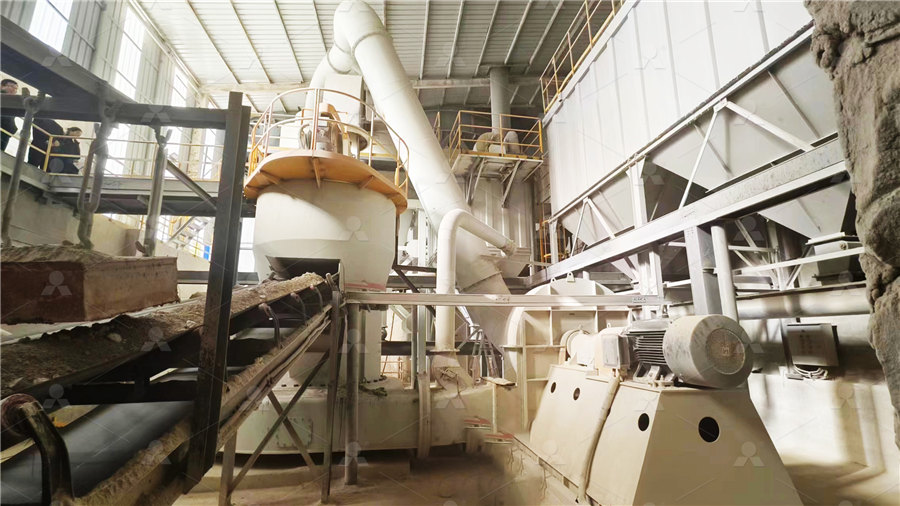
Why the ball to powder ratio (BPR) is insufficient for describing
2014年6月15日 Nevertheless, parameter factors, such as the type of ball milling, balltopowder ratio (BPR), rotation speed, grinding period, size and shape of the milling media, and process control agent (PCA 2008年7月1日 Very low speed singlegrain grinding tests were carried out for 45 steel and 20Cr alloy with 14# ZA grain The grinding groove width and depth, the grinding force ratio, specific grinding forces Grinding at Very Low Speed Request PDF ResearchGate2023年4月24日 Grinding is the final stage of comminution, which reduces particle size to micron size level The size reduction is achieved by attrition, abrasion, and impact between the ore itself and between the ore particles and grinding media []According to Swart et al [], ball mills are mostly used because of their very high size reduction ratio, although they have a very low Grinding Media in Ball MillsA Review [v1] Preprints2021年7月12日 Effect of BalltoPowder Ratio on Morphology, Structure, and Flowability of BallMilled Gray Cast Iron Powder Peer Reviewed; Published: 12 July 2021 Volume 30, pages 1679–1691, (2021) ; Cite this articleEffect of BalltoPowder Ratio on Morphology, Structure, and
.jpg)
Grinding SpringerLink
2022年2月28日 The particular rate of breakage ratio between dry and wet grinding varies from 11 Eirich Tower Mill and Metso Vertimill are two wellknown stirred mills operating at low speed In this Ozkan, A, Yekeler, M, Calkaya, M: Kinetics of fine wet grinding of zeolite in a steel ball mill in comparison to dry grinding Int J 2021年7月5日 When the ball mill rotates at a certain speed and the filling rate is large, and the grinding efficiency is low 5 Precise refill ball In production, the grinding action of the steel ball and the ore will cause the wear of the steel ball, leading to changes in the ratio of the steel balls of various sizes, 9 ways tell you how to improve ball mill efficiency2024年2月19日 Therefore, when choosing a steel ball, its impact must be considered first 2 The grinding force of the steel ball During the ball mill’s operation, the steel ball’s surface area is mainly relied on to make the material contact with the steel ball’s surface to improve the ball mill’s grinding efficiencyBall Mill Steel Balls: Quality And Gradation JXSC Mineral2021年8月20日 Adjusting the grinding parameters can be the easiest and fastest solution to improve a part’s surface finish Here are the key parameters and recommended actions to do it successfully Creepfeed/surface grinding: Increase wheel speed This is a good starting point However, be sure the wheel is rated to run at the new speed5 Grinding Considerations for Improving Surface Finish
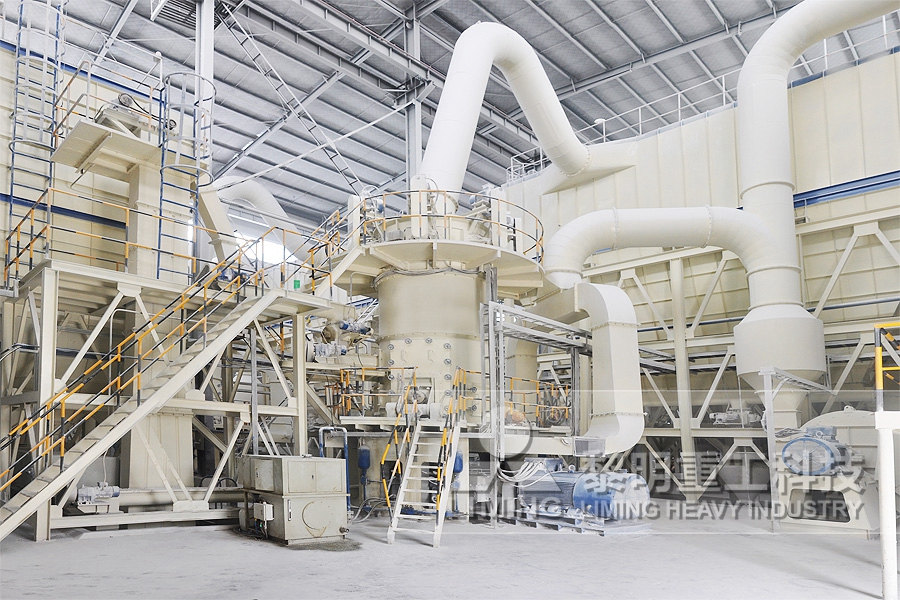
Brief Analysis of the Influence of Operational Factors on Grinding
2024年9月23日 Media Ratio: The size and specification of grinding media should be appropriately matched For instance, in ball mills, the ratio of steel balls of various diameters depends on below factors Such as ore properties, particle size, and grinding fineness Various methods exist for calculating ball ratios But there is no unified academic consensus2015年10月15日 Learn how to calculate the grinding capacity of your ball mill with 911 Metallurgist This guide provides essential formulas, insights, and tips to optimize your milling process and enhance production efficiencyCalculate Ball Mill Grinding Capacity 911Metallurgist1The chromium content is 1%3% and the hardness is HRC≥45 This kind of wearresistant steel ball is called a lowchromium alloy cast ball, and the lowchromium ball is produced by mediumfrequency electric furnace melting, metal mold, or sand castingChina Grinding Ball Manufacturers Suppliers FactoryBall milling is a mechanical process that involves the rotation of a drum containing grinding media, typically steel balls, at a high speed The materials to be milled are loaded into the drum, and as the drum rotates, the grinding media collide with the materials, causing them to Exploring ball milling theory: A comprehensive guide