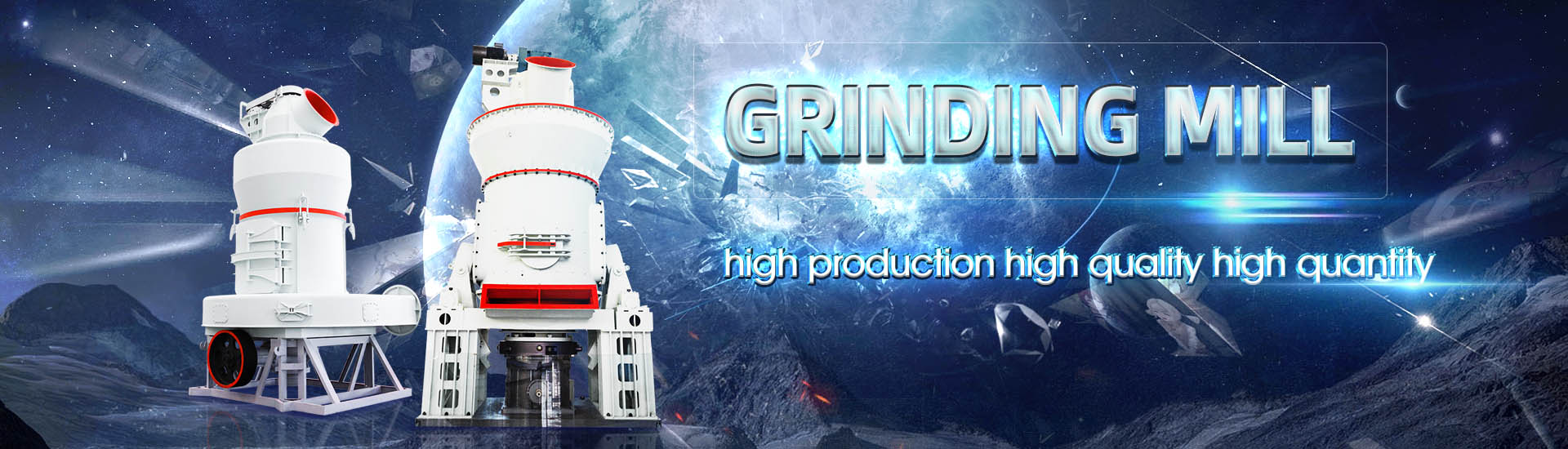
How to determine the size of an ore grinding mill
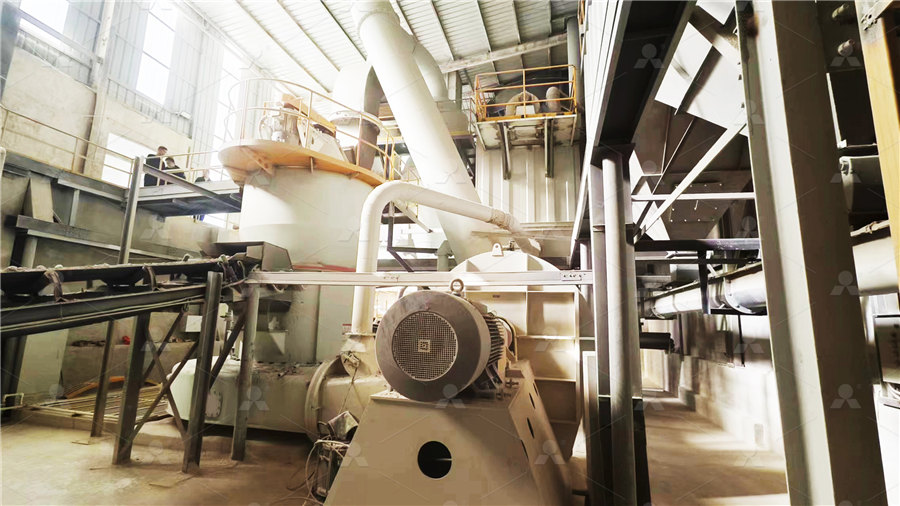
Ball Mill Design/Power Calculation 911Metallurgist
2015年6月19日 Use this online calculators for Motor Sizing and Mill sizing as well as mill capacity determinators In extracting from Nordberg Process Machinery Reference Manual I will also provide 2 Ball Mill Sizing (Design) 2013年8月3日 In Grinding, selecting (calculate) the correct or optimum ball size that allows for the best and optimum/ideal or target grind size to be achieved by yourCalculate and Select Ball Mill Ball Size for Optimum The size of the largest lumps in the mill feed is principally determined by limits set by the mill feed trunnion diameter and by the type and size of conveying equipment used for handling and of Primary Grinding Mills: Selection, Sizing And Current Practices2023年2月15日 Take all the ore samples from a ball mill (usually take new ore and returned sand samples, then match the samples in proportion) for sieving analysis Divide them into several particle sizes, such as 1812, 1210, 108, 8 Method of Steel Grinding Ball Proportioning and Example

AMIT 135: Lesson 6 Grinding Circuit – Mining Mill
Size Grinding Mills Fundamental to all mill sizing is determining the necessary specific power consumption for the grinding stage (primary, secondary, tertiary etc) It can be established (in falling scale of accuracy) in one of the following Overall, ball size and shape are important factors to consider when choosing a mill for ore grinding However, other factors such as mill design and the type of ore being processed also Factors affecting ores grinding performance in ball mills2023年7月20日 According to the different grinding medium, the grinding mill is divided into three types: (1) ball mill – it is used widely, and almost all materials can be triturated by ball mill; (2) Ore Grinding SpringerLink2023年10月27日 The grinding media impart the forces required for size reduction and determine the category of tumbling mills: autogenous, rod mills and ball mills Autogenous and semi A Review of the Grinding Media in Ball Mills for Mineral Processing
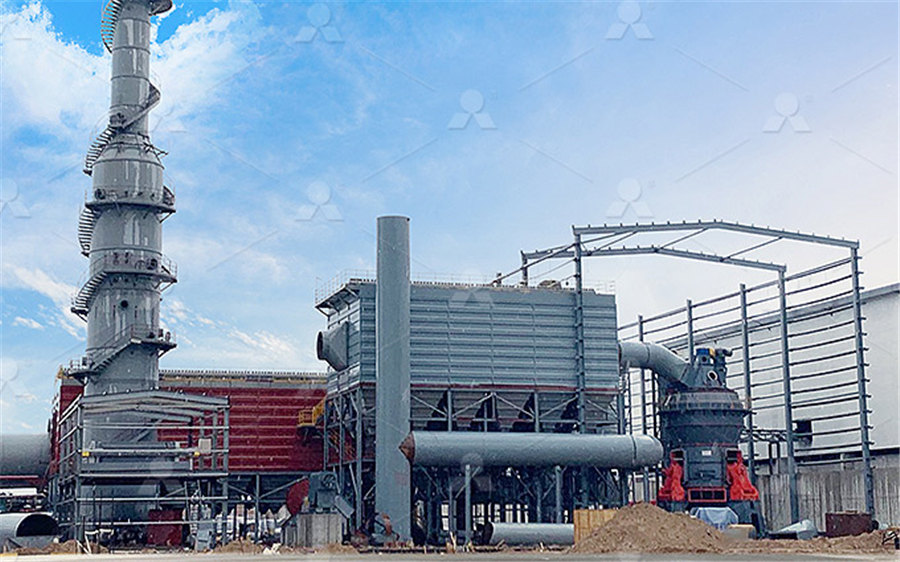
How Ball Mill Ore Feed Size Affects Tonnage Capacity
2017年7月26日 The power drawn and reduction achieved to the grinding mill feed will be maximized The grinding mill output will vary considerably with the Work Index If the feed size was 13,000 micrometers for the same grind production size, theoretical output from Fig (21) would change from about 90,000 tons per day on the 13 Work Index down to 65,000 F = 80% passing size of the feed to the grindability test (microns) P = 80% passing size of the result of the grindability test (microns) 3 Estimation of the power consumption of a grinding mill 31 STEP 3 : Estimate the power consumption of a grinding mill for a particular applicationGrinding power : step by step calculation PowderProcess2013年7月31日 An easy and fast/quick way for grinding operators to get an idea and estimate their grinds is to follow this procedure 911 Metallurgist is a trusted resource for practical insights, solutions, and support in mineral processing Quick Grind Check How to Quickly Estimate Grind 2016年7月7日 The recovery of gold by ore leaching is influenced by the size of the particles and the chemical environment The effect of particle size on the dissolution of gold is usually studied using mono Effect of Particle Size and Grinding Time on Gold Dissolution in
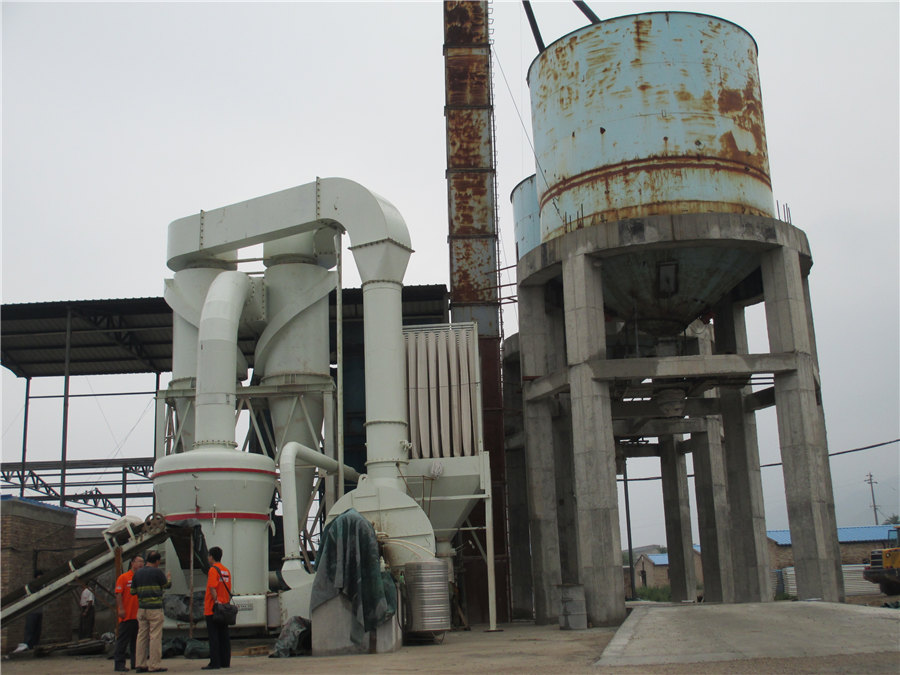
Autogenous and SAG SemiAutogenous Mill Design Calculations
2018年4月17日 Mill Sizing: After laboratory and pilot plant testing confirm the feasibility of autogenous or semiautogenous grinding, it can be used to establish the exact grinding circuit and mill sizeIn the pilot plant tests, the tare power of the pilot plant mills should be determined before and after each test run The tare power should be for the empty mill2023年10月17日 Factors for choosing a suitable ore powder grinding mill 1 Raw material characteristics: Different raw materials have different hardness, humidity and grinding and crushing properties, and the corresponding ore powder grinding mill needs to be selected to meet the processing requirements 2 Production capacity: Determine the required processing How to choose a suitable ore powder grinding mill?Another type is Ball Mills, which utilize steel balls placed inside rotating cylinders to grind the ore The size of these balls determines how finely ground the ore will become The rod mill is another type of grinding mill used in the copper ore mining process This machine uses steel rods as the grinding media instead of balls, Understanding the SAG Mill in Copper Ore Mining Processore This is typically followed by grinding, which reduces the size of the ore to be further refined, and the valuable particles separated Or, in the case of industrial minerals, used as is Grinding is often done in steps: a primary mill grinds the largesized ore and then a secondary mill grinds the ore from a small size to the desired sizeThree factors that determine the wear life and performance of mill
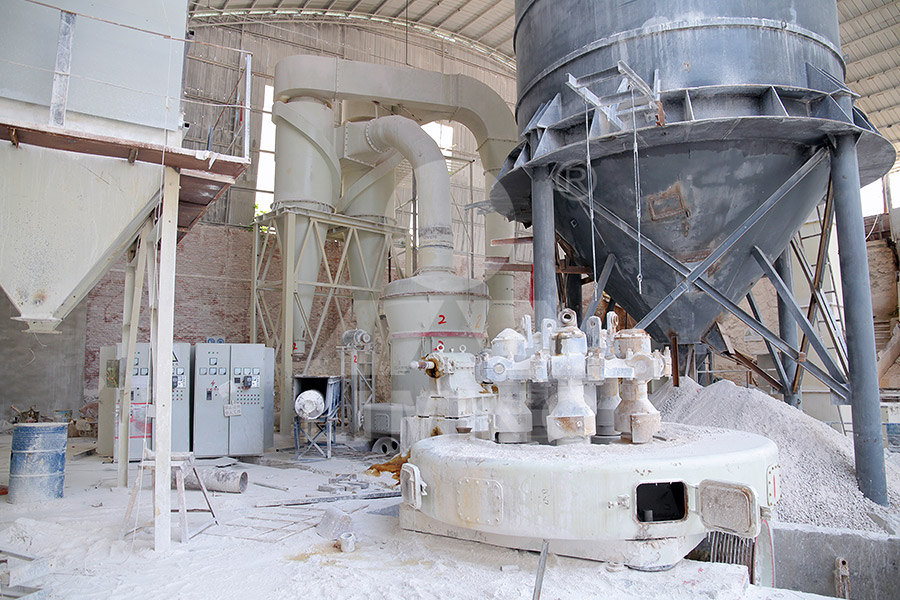
Calculate Ball Mill Grinding Capacity 911Metallurgist
2015年10月15日 Learn how to calculate the grinding capacity of your ball mill with 911 Metallurgist This guide provides essential formulas, insights, and tips to optimize your milling process and enhance production efficiency2020年1月3日 Iron ores obtained from different sources differ in their chemical and physical properties These variations make the process of grinding a difficult task The work carried out in this context focuses on three different samples of iron ore, viz, high silica high alumina, low silica high alumina, and low silica low alumina The grinding process for all the three iron ores is Estimation of Grinding Time for Desired Particle Size Distribution Ball mills are progressively used to grind the ores for particle size reduction and to liberate valuable minerals from the ores The grinding of ore is a highly energyintensive process [1–4] In this process, the size of the particle obtained depends on the energy consumption of the ball mill The major challenge encountered in theEstimation of Grinding Time for Desired Particle Size Distribution2019年8月14日 Ball mill is a common grinding equipment in concentrator : hm@gmail Toggle navigation Home because it is necessary to grind the ore to a suitable selected particle size before extract highgrade concentrate from the ore It is not easy to determine the absolute value of the critical speedAt present, The Ultimate Guide to Ball Mills Miningpedia
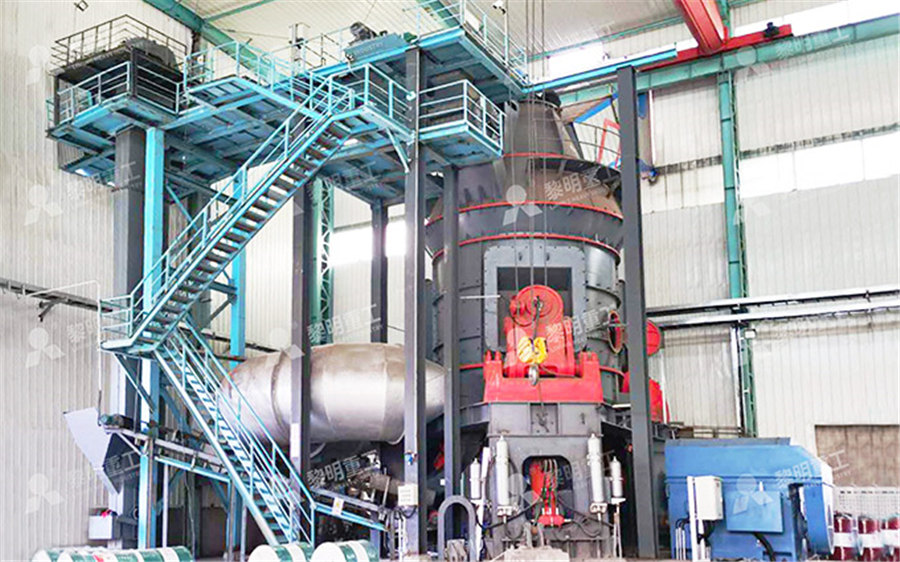
Ball Mill Success: A StepbyStep Guide to Choosing
2024年8月8日 Unlock the secrets to ball mill efficiency with our comprehensive guide on choosing the right grinding media Learn how material composition, size, shape, hardness, and cost impact your milling process and outcomes Perfect 2023年7月20日 (2) Various working parameters of grinding mill, including fraction of critical speed for grinding mill, filling rate for grinding mill, grinding concentration, grinding cycle load, etc (3) And grinding material properties, including ore grindability, feeding particle size, etc Huge energy and steel consumption in ore grinding process greatly affect the subsequent separation Ore Grinding SpringerLink2018年2月1日 In another study to investigate ball size distribution on ball mill efficiency by Hlabangana et al [50] using the attainable region technique on a silica ore by dry milling, a threeball mix of Effect of ball and feed particle size distribution on the milling A mill is a device, often a structure, machine or kitchen appliance, that breaks solid materials into smaller pieces by grinding, crushing, or cutting Such comminution is an important unit operation in many processesThere are many different types of mills and many types of materials processed in them Historically mills were powered by hand or by animals (eg, via a hand crank), Mill (grinding) Wikipedia
.jpg)
Common Basic Formulas for Mineral Processing Calculations
2016年3月21日 Concentration and Recovery Formulas These are used to compute the production of concentrate in a mill or in a particular circuit The formulas are based on assays of samples, and the results of the calculations are generally accurate— as accurate as the sampling, assaying, and crude ore (or other) tonnage on which they depend2023年2月15日 A beneficiation plant in Singapore loads balls into a ϕ 1500mm×3000mm wet grid type ball mill, determines the filling rate ϕ = 50%, and selects cast steel grinding balls δ = 45 t/m 3 The ball mill processes the mediumhard ore 1 See Table 1 for the sieving analysis results of all the ore samples from a ball mill Table 1Method of Steel Grinding Ball Proportioning and Example11 Grinding media size specification A number of researchers (Deniz, 2012; Bwalya et al, 2014; Petrakis et al, 2016) carried out studies about the effect of feed particle size and grinding media size on the grinding kinetics of different ores Khumalo et Effect of ball and feed particle size distribution on the milling 2017年9月13日 F = The size in microns (micrometers) that 80% of the feed is finer than When accurate mill ore feed rate in dry tons per hour, mill power draw in kilowatts, and mill feed and product size analyses in microns are available the Bond Equation can be used to measure the operation of comminution machines, reporting it as operating work indexHow to Calculate Grinding Mill Operating Efficiency
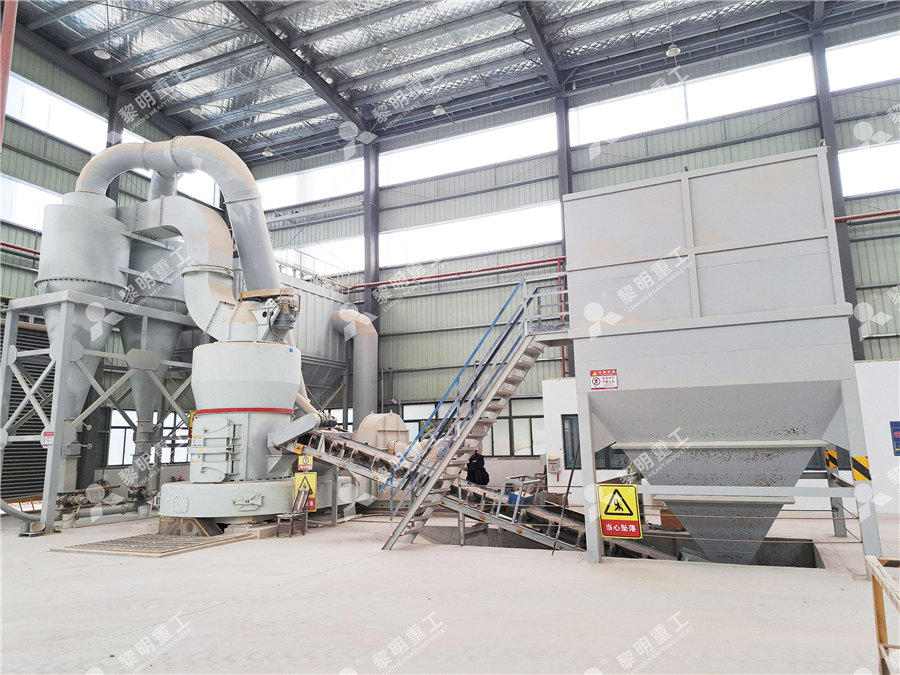
Grinding in Ball Mills: Modeling and Process Control Sciendo
Grinding in ball mills is an important technological process applied to reduce the size of particles which may have different nature and a wide diversity of physical, mechanical and chemical characteristics Typical examples are the various ores, minerals, limestone, etc The applications of ball mills are ubiquitous in mineralThe performance of grinding mills depends on many operating factors among which are the time of grinding, mill speed, grinding media–toore ratio, 150μm feed size fractions were selected to determine the nominal degree of hematite liberation from the representative HSHA, LSHA, and LSLA feed iron ore samples The crushed – 3mm iron (PDF) Estimation of Grinding Time for Desired Particle Size 2018年6月1日 A number of researchers (Deniz, 2012; Bwalya et al, 2014; Petrakis et al, 2016) carried out studies about the effect of feed particle size and grinding media size on the grinding kinetics of different oresKhumalo et al, 2006 postulated that generally larger sized grinding media would break larger particles quicker but a finer product would be obtained by use of Effect of ball and feed particle size distribution on the milling 2012年6月1日 The feed material is typically composed of the BFRs and the catalyst, both in powder form As the cylinder starts to rotate, the grinding balls inside the cylinder crush and grind the feed Grinding in Ball Mills: Modeling and Process Control
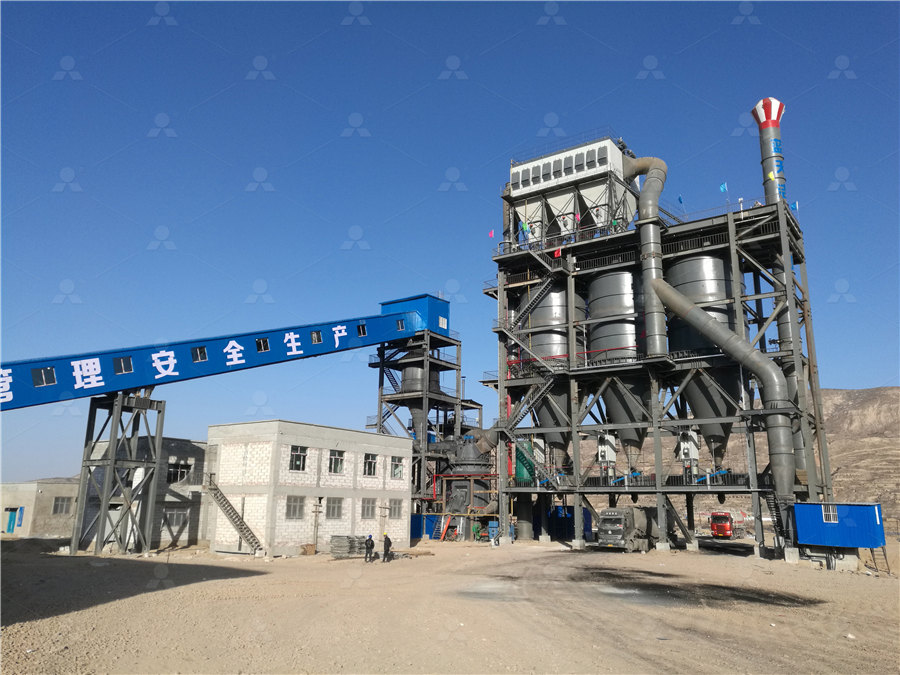
Calculate Top Ball Size of Grinding Media FRED C BOND
2015年9月6日 1 The first study was to determine if either of the two existing theories of comminution the Rittenger theory or the Kick theory were correct Bond concluded that neither was correct He developed a theory that the energy required for comminution was a function of the difference in the square root of the size of the particles in the feed and in the product of the 2015年10月14日 The majority of grinding balls are forged carbon or alloy steels Generally, they are spherical, but other shapes have been used The choice of the top (or recharge) ball size can be made using empirical equations developed by Bond (1958) or Azzaroni (1984) or by using special batchgrinding tests interpreted in the content of population balance models (Lo and Calculation of Top Grinding Media Size Ball SizingAlthough it is well known and easily experienced that the feed size distribution influences the throughput and stability of operation of a semiautogenous grinding (SAG) mill, the details are poorly understood since it is often only the input and output measurements that are used to identify unfavourable inmill conditions Load cells and power monitoring are sometimes used Understanding Size Effects of Semiautogenous Grinding (SAG) Mill 2005年8月5日 The article provides a stepbystep calculation procedure to determine the exact ball mill size (on the basis of the calculated power requirement) for a specific ore grinding plant applicationDetermination of work index in a common laboratory mill
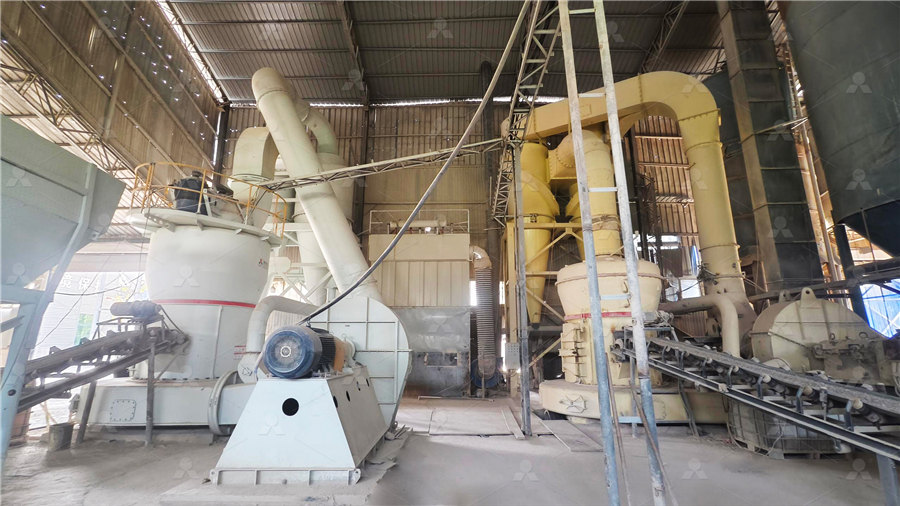
SAG Mill Testing Test Procedures to Characterize Ore Grindability
size reduction in a comminution device Because grinding theories are imperfect and ore hardness can vary with size, grindability tests are designed to best represent the size reduction of the industrial equipment analysed For that reason, it is preferable to design a primary ball mill from a rod mill work index rather than a ball mill2013年7月15日 For any circuit, whether a crushing circuit, a rod mill, or a closed ball mill circuit, the Work Index always means the equivalent amount of energy to reduce one ton of the ore from a very large size to 100 um The sample was Bond Work Index FormulaEquation 911Metallurgist2015年7月29日 As you increase the volume of the through put, the time that the ore has to react to the grinding media is lessened As you add ore to the mill you are also adding WATER and changing density which affects the slurry rheology and workings of the grinding action inside that mill This water is one of the main controls that you have over your grindEffect of Water Density on Grinding Mill 911MetallurgistThe capacity not only determines the mill equipment size, but also dictates how to operate the mill, whether continuous or batch operation is required, and whether the process can be performed inhouse or if a tolling service is a better option The required product size is an important grinding cost factor, especially for finesize grindingHammer Milling and Jet Milling Fundamentals AIChE
.jpg)
Determination of granulometrical composition of the clinker by grinding
2020年7月24日 In grinding processes, energy consumption is a very important profitability criterion for the applied particular size reduction technology The energy consumption of grinding is the subject of Figure 1 shows the mill matrix operating on the feed five times in succession Note that some product exits in the topsize at all times For the case that P and F are known, the problem (Inverse Problem) is to find M For the case of wet grinding in a ball mill where all the top size is ground away during a small time interval, mu and Pt must Assessment of the Functionality of Selection and Breakage Rate 2023年10月1日 To determine the ball mill work index of the samples (Table 1), around 10 to 17 kg of ore was required for the particle size crushed to −335 mm (Amtech, 2006) The 700 cm 3 ore sample weight is fed to the Bond mill at a −335 mm size rangeEstimation methodology for Bond ball mill work index experiment 2021年6月18日 The material being ground also helps us determine the grit size For hard to grind materials, we would recommend a finer grit size because a smaller particle will penetrate hard materials and form a chip easier than a larger blockier one Difficult or hard to grind materials are abusive to the abrasive grain and can cause them to blunt or dullThe 7 Factors Used to Determine a Grinding Wheel Specification
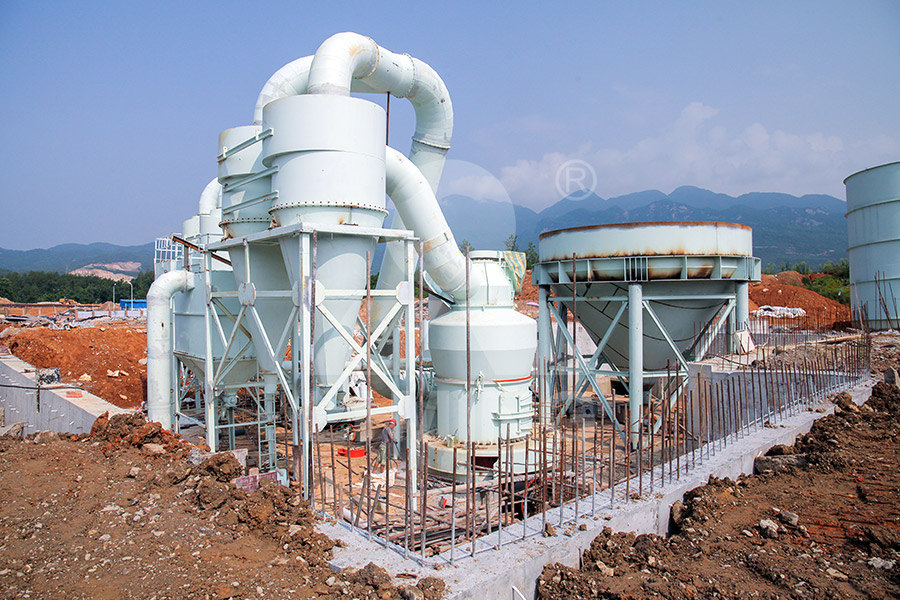
A Review of the Grinding Media in Ball Mills for Mineral
2023年10月27日 The ball mill is a rotating cylindrical vessel with grinding media inside, which is responsible for breaking the ore particles Grinding media play an important role in the comminution of mineral ores in these mills This work reviews the application of balls in mineral processing as a function of the materials used to manufacture them and the mass loss, as Grinding in ball mills is an important technological process applied to reduce the size of particles which may have different nature and a wide diversity of physical, mechanical and chemical characteristics Typical examples are the various ores, minerals, limestone, etc The applications of ball mills are ubiquitous in mineralGrinding in Ball Mills: Modeling and Process Control Sciendo