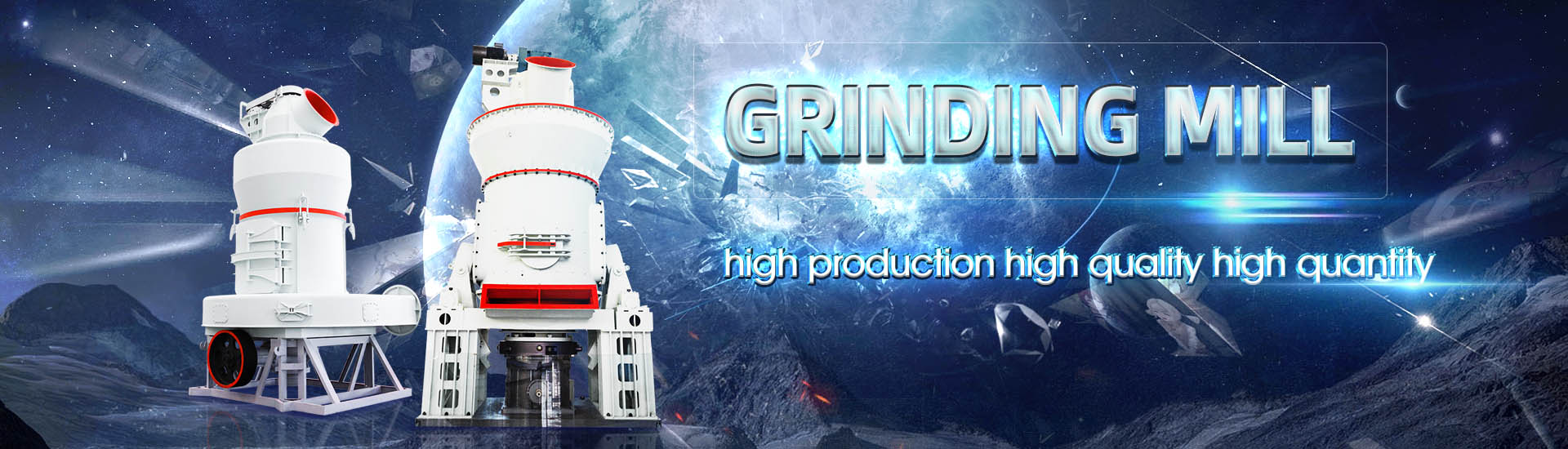
2Normal pressure value of grinding mill
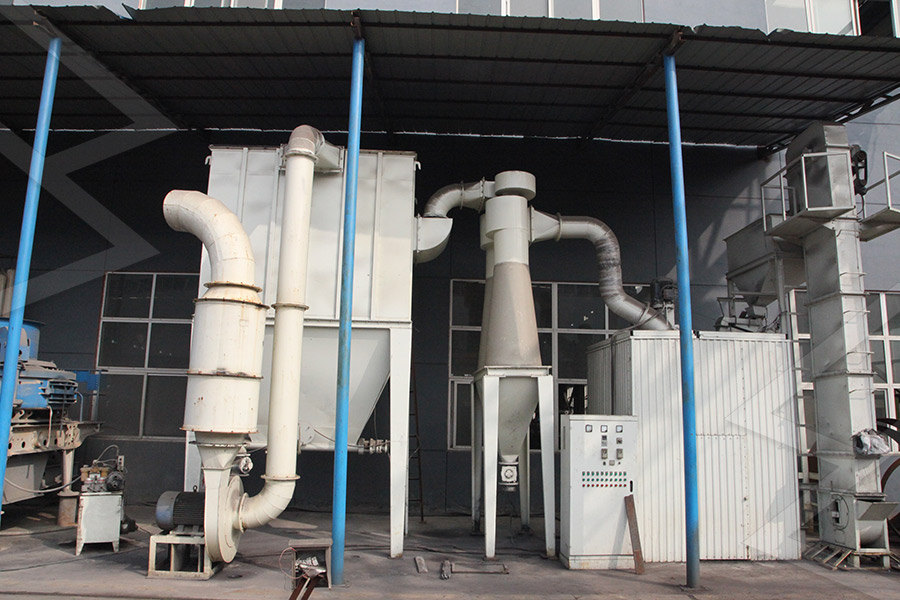
Operational parameters affecting the vertical roller mill performance
2017年4月1日 The kN/m 2 value is the pressure of the grinding roller applied onto the grinding table The value accounts for the projected area of the roller onto the grinding table The projected area consists out of the mean roller diameter multiplied with the roller width on the grinding tableControl Parameters for Loesche Vertical Mills Material grindability Grinding stock feed 50 / 100 ms: Signal detection 1 second – 10 minutes: Signal evaluation Fineness (Blaine) or residue PROCESS OPTIMISATION FOR LOESCHE GRINDING PLANTSIt discusses four mill operation conditions based on relationships between mill power, pressure loss, and process parameters For each condition, it identifies potential causes and recommends corrective actions such as adjusting feed VRM Operation SOPs PDF Mill (Grinding) Pressure2021年1月1日 Mill filling has a dominant effect on grinding mill performance (Apelt, Asprey and Thornhill, 2001), and therefore, its accurate measurement is vital for modelling grinding mill An improved method for grinding mill filling measurement and
.jpg)
Analyzing process parameters for industrial grinding circuit based
2023年9月1日 Based on the machine learning method, this study analyzed the full process parameters (ie, ball mill power, fresh ore feed rate, hydrocyclone feed pump power, Understanding the mechanical behaviour of the material and the consequent prediction of the results of a grinding stage, as well as the choice of the right equipment to perform it, are key Highpressure grinding rolls: model validation and function 2016年9月1日 Obtained results indicate that grinding pressure, primary air (PA) temperature and mill motor current have a tendency to rise by increasing coal feeding mass flow rates for all Operational parameters affecting the vertical roller mill Grinding conditions in the spiral jet mill have been extensively studied, with the consensus agreeing that particle feed rate and grinding pressure are the two mostAnalysis of holdup and grinding pressure in a spiral jet mill using
.jpg)
Parameters for the Grinding Process in Vertical Mills
2024年1月17日 Any machine used for grinding or crushing consumes around 30 to 40% of the energy of a factory The loading pressure, table rotation speed, moisture content, outlet temperature and pressurecommon solution to grind raw materials and cement Roller presses are used mainly in combination with a ball mill for cement grinding applications and as finished product grinding BALL MILLS Ball mill optimisation Holzinger ConsultingFluid feed pressure (kPa) 320 Fluid grinding Pressure (kPa) 300 DEM time step, µs 21 Holdup study Keeping the grinding pressure constant at 3 barg, the mass of particles in the mill is increased for each case The addition rate was set for each case, so that the required mass would be added within 001 s A periodAnalysis of holdup and grinding pressure in a spiral jet mill 2020年8月1日 The highpressure grinding roll (HPGR) is a type of roller mill that continuously produces particlebed comminution The HPGR was introduced by Schönert and first installed in the cement industry in the 1980s (Schönert, 1988, Schönert, 1985)Since then, the HPGR has been widely used in the cement industry owing to its energy savings (Camalan and Önal, Effect of the roll stud diameter on the capacity of a highpressure
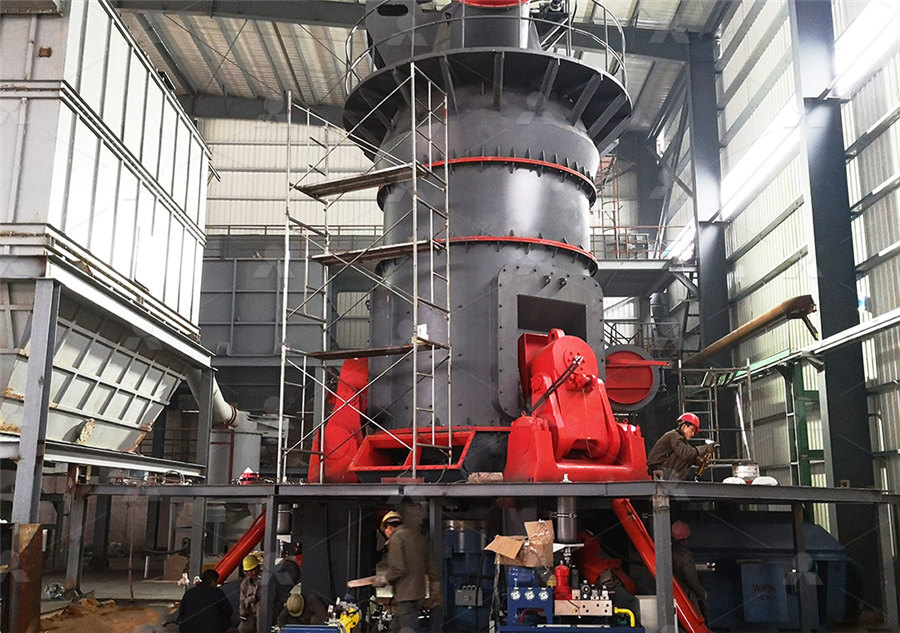
(PDF) Analysis of holdup and grinding pressure in a spiral jet mill
2021年6月7日 Analysis of holdup and grinding pressure in a spiral jet mill using CFDDEM June 2021; The European Physical Journal An average value for dissipated energy of 06 mJ is recorded for each of 2015年6月20日 The critical speed of a rotating mill is the RPM at which a grinding medium will begin to “centrifuge”, namely will start rotating with the mill and therefore cease to carry out useful work Ball mills have been successfully run at speeds between 60 and 90 percent of critical speed, but most mills operate at speeds between 65 and 79 percent of critical speedBall Mill Critical Speed 911MetallurgistAs the mill rotates, the charge moves inside the mill and extends pressure and friction on the mill Due to constant changes in the process and charge parameters, eg the engine power, filling level, charge mass, ore density, the amount of water in the charge, etc, the charge and the loading on the mill vary over time during productionStructural Analysis and Condition Monitoring of Grinding Mills: A Download scientific diagram Relationship between SAG mill power draw, bearing pressure and feed rate from publication: Supervisory Fuzzy Expert Controller for SAG Mill Grinding Circuits: Sungun Relationship between SAG mill power draw, bearing pressure and
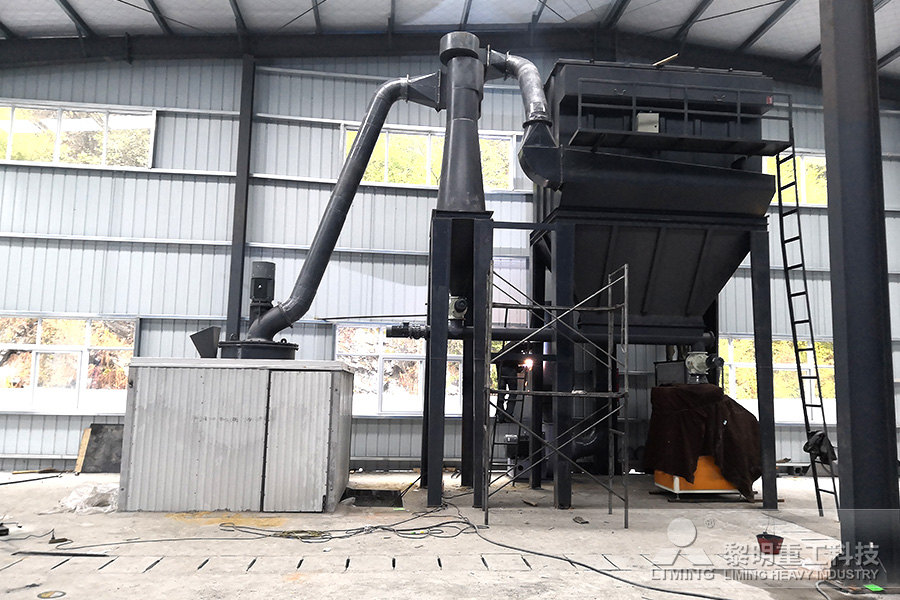
COMPARISON OF GRINDING EFFICIENCY BETWEEN BALL MILLS
COMPARISON OF GRINDING EFFICIENCY BETWEEN BALL MILLS AND VERTICAL ROLLER MILLS IN COARSE GRINDING Yakup Umucu 1, Vedat Deniz 2,Osman Mart 1 Abdi Kemal Y!ce 1, Mehmet Fahri Sara" 3 1 S leyman 2022年1月23日 This work concentrates on the energy consumption and grinding energy efficiency of a laboratory vertical roller mill (VRM) under various operating parameters For design of experiments (DOE), the response surface method (RSM) was employed with the VRM experiments to systematically investigate the influence of operating parameters on the energy Analysis and Optimization of Grinding Performance of Vertical 2015年10月23日 In this chapter an introduction of widely applied energyefficient grinding technologies in cement grinding and description of the operating principles of the related equipments and comparisons over each other in terms of grinding efficiency, specific energy consumption, production capacity and cement quality are given A case study performed on a EnergyEfficient Technologies in Cement Grinding IntechOpen2017年9月11日 PDF In this study, an extensive sampling study was carried out at vertical roller mill of ESCH Cement Plant in Luxemburg Samples were collected from Find, read and cite all the research (PDF) Performance Evaluation of Vertical Roller Mill in Cement Grinding
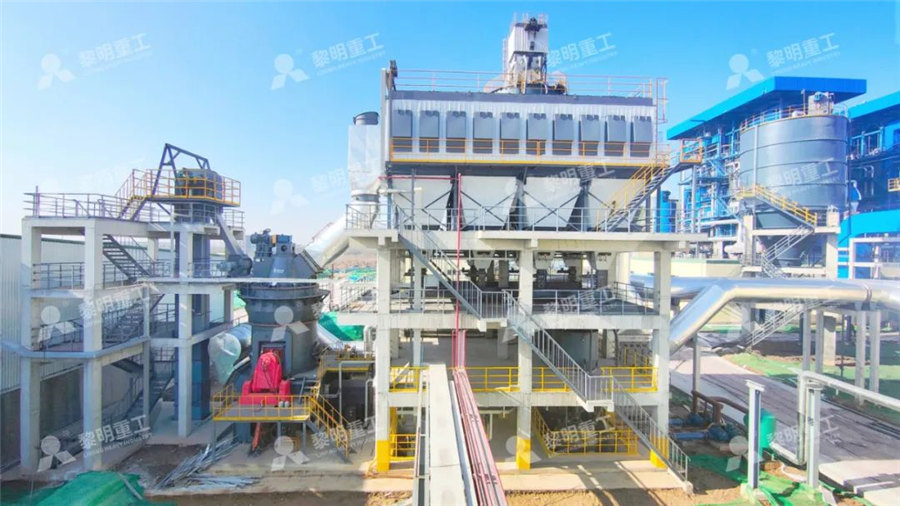
Potential of HighPressure Grinding Roll (HPGR) for Size
2022年3月16日 Potential of HighPressure Grinding Roll (HPGR) for Size Reduction of Hard Banded Iron Ore Original Article; Published: 16 March 2022; Volume 75, pages 1797–1811, (2022) The R 2value and signaltonoise ratio should be greater than 50% and 4, respectively2014年3月1日 The object of the study reported here is the grinding process in a tumbling mill where the mechanism of destruction by crushing is implemented, which is caused by the mechanism of compression loading(PDF) Analysis of ball mill grinding operation using mill power high pressure grinding roll and tumbling mill circuits SMorrell SMCC Pty Ltd, 29 Camborne Place, Chapel Hill, Qld 4069 Australia Abstract In a previous paper (Morrell, 2008a) an approach was described which enabled the specific energy of tumbling mills such as Autogenous (AG), Semiautogenous (SAG)Predicting the overall specific energy requirement of crushing, 2021年12月1日 Performance of grinding in a pin mill was evaluated while grinding of coriander seeds at 10 0 C and 50 0 C with 5, 10 and 15 rpm of conveyor screw speeds It was noted that, the amount of (PDF) Application of cryogenics in grinding of spices for value
.jpg)
Semi Autogenous Grinding Mill ScienceDirect Topics
Concentrators vary similarly A new large concentrator unit typically consists of a semiautogenous grinding mill, high pressure grinding rolls, two ball mills, and a flotation circuit It can treat up to 170 000 tonnes of ore per day (Sartain, 2010) Larger concentrators consist of multiples of this basic concentrating unit2017年2月28日 High Pressure Grinding Rolls The value o btained from Eqn 8 provides information (1 991) modi ed the ball mill gr inding k inetics equat ion in A Review of the Modeling of High Pressure Grinding Rolls2009年5月1日 High Pressure Grinding Rolls (HPGR) circuits have the potential to reduce these emissions by up to 328 Megatonnes/year, or 443% when compared to the Semiautogenous/ball mill circuit alternativesPredicting the overall specific energy requirement of crushing, A 15 mio t/a cement plant is having a closed circuit ball mill for cement grinding: The mill has been operating with satisfactory performance interms of system availability and output, however power consumption was on higher side 31 System Description Mill Rated capacity 150 t/h OPC at 2800 blaine I chamber linersPROCESS DIAGNOSTIC STUDIES FOR CEMENT MILL

Numerical and analytical estimation of rolling force and torque in
2023年12月14日 Where: F is the axial force along x (N/mm) R is the roll radius (mm) θ is the angle varying from α (entry section) to 0 (exit section) (rad) s is the roll pressure (N/mm 2) t is the friction stress (N/mm 2) + sign is for the exit section − sing is for the entry section It is possible to note that all quantities are normalized along the strip width2022年12月30日 Structured grinding wheel has obvious advantages in reducing grinding force, and the structural parameters of grinding wheel have important influence on the reduction of grinding force In order to determine the influence law of structural parameters on grinding force, the following theoretical modeling and experimental research work are carried out in this Theoretical modeling and experimental study on grinding force of A PilotScale Examination of a Novel High Pressure Grinding Roll / Stirred Mill Comminution Circuit for HardRock Mining Applications by Jeffrey Adam Drozdiak BASc, The University of British Columbia, 2006 A THESIS SUBMITTED IN PARTIAL FULFILLMENT OF THE REQUIREMENTS FOR THE DEGREE OF MASTER OF APPLIED SCIENCE in The A PilotScale Examination of a Novel High Pressure Grinding Roll 2023年7月1日 The establishment and numerical analysis of grinding force prediction models have consistently been a research hotspot Modeling methods are mainly divided into two categories: empirical and theoretical modeling 5 At the early stage, due to randomized grain characteristics on the grinding wheel surface, theoretical research on grinding force has Analysis of grinding mechanics and improved grinding force
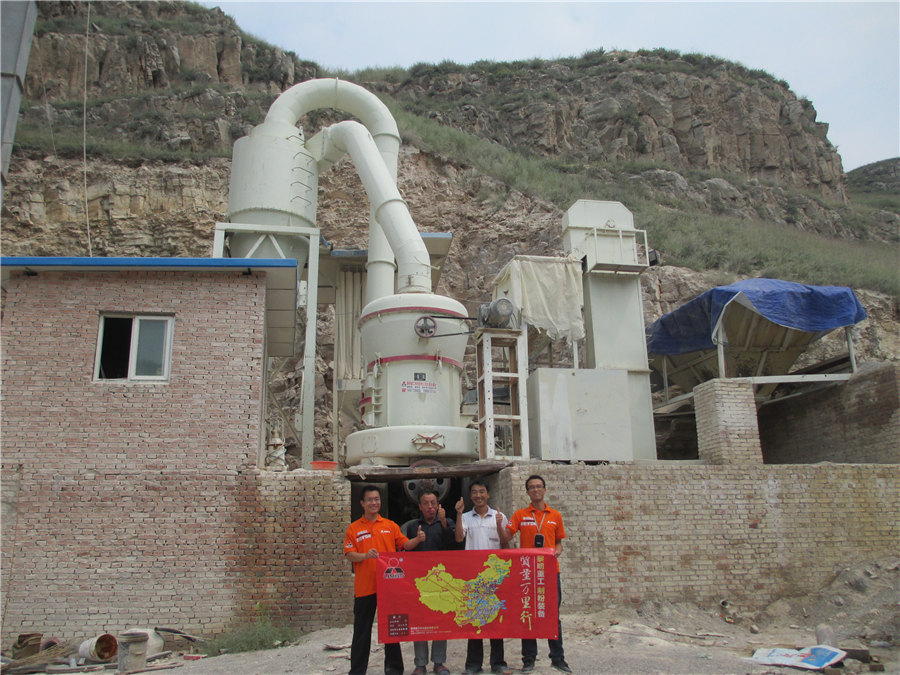
(PDF) MPS mills for coal grinding ResearchGate
2014年1月1日 Two mill systems are employed for most coal grinding applications in the cement industry These are, on the one hand, vertical roller mills (VRM) that have achieved a share of almost 90% and, on 2015年4月9日 Grinding Mills and Their Types satyendra; April 9, 2015; 12 Comments ; autogenous grinding, ball mill, grinding mills, hammer mill, rod mill, roller mill, SAG,; Grinding Mills and Their Types In various fields of the process industry, reduction of size of different materials is a basic unit operationGrinding Mills and Their Types – IspatGuru2013年8月3日 In Grinding, selecting (calculate) the correct or optimum ball size that allows for the best and optimum/ideal or target grind size to be achieved by your ball mill is an important thing for a Mineral Processing Engineer AKA Metallurgist to do Often, the ball used in ball mills is oversize “just in case” Well, this safety factor can cost you much in recovery and/or mill liner Calculate and Select Ball Mill Ball Size for Optimum GrindingMEAM VALUE OF SHP TONS/M2 (TONS/FT2) 1ST 2ND 3RD 4TH 5TH 12 ROLLER 2582 2367 2690 2958 240 220 250 275 15 ROLLER 2582 2367 2475 2690 pressure To compromise with mill performance due to power constrain PERFORMANCE OF INDIVIDUAL MILLSMILL DESIGN MILL OPERATION
.jpg)
Ball Mill Design/Power Calculation 911Metallurgist
2015年6月19日 The basic parameters used in ball mill design (power calculations), rod mill or any tumbling mill sizing are; material to be ground, characteristics, Bond Work Index, bulk density, specific density, desired mill tonnage capacity DTPH, operating % solids or pulp density, feed size as F80 and maximum ‘chunk size’, product size as P80 and maximum and finally the type of 2018年4月17日 Mill Sizing: After laboratory and pilot plant testing confirm the feasibility of autogenous or semiautogenous grinding, it can be used to establish the exact grinding circuit and mill sizeIn the pilot plant tests, the tare power of the pilot plant mills should be determined before and after each test run The tare power should be for the empty millAutogenous and SAG SemiAutogenous Mill Design Calculations2015年3月1日 The model explicitly incorporates mill design data (mill diameter, grinding table diameter, air classifier geometry) and operational conditions (coal feed rate, air flow rate, air temperature, air pressure, hydraulic loading on spider, mill rotational speed), and directly outputs the mill power draw and coal size distributionsModelling of vertical spindle mills Part 2: Integrated models for E CONVENTIONAL AND HIGH PRESSURE GRINDING ROLLS CRUSHING ON THE BALL MILL GRINDING KINETICS OF AN IRON ORE Kianoush BARANI, Hossein BALOCHI Department of Mining Engineering, Lorestan University, Khorramabad, Iran, Abstract: The effect of using conventional and high pressure grinding rolls (HPGR) crushing on the ballA COMPARATIVE STUDY ON THE EFFECT OF USING
.jpg)
Grinding Mills Common Types 911Metallurgist
2016年11月7日 In Fig 13 is shown a large ball mill, designed for the dry grinding of limestone, dolomite, quartz, refractory and similar materials; this type of mill being made in a series of sizes having diameters ranging from about 26 2008年5月1日 The d50 seems to relate to theapplied air pressure as a power law equation expressed as following:d50 = aP b ; as P 0The avalue and bvalue have been found to correlate to the feed sizeFine grinding of brittle minerals and materials by 2023年12月4日 A vertical roller mill (VRM) is a grinding equipment used for the size reduction of minerals, is the purely elastic rolling resistance moment and \(M{r,\lim }\) is the limiting rolling moment value \(K{r}\) The rolling point shall predict the location of highpressure zone in Numerical Investigation of Vertical Roller Mill Operation Using CONVENTIONAL AND HIGH PRESSURE GRINDING ROLLS CRUSHING ON THE BALL MILL GRINDING KINETICS OF AN IRON ORE Kianoush BARANI, Hossein BALOCHI Department of Mining Engineering, Lorestan University, Khorramabad, Iran, Abstract: The effect of using conventional and high pressure grinding rolls (HPGR) crushing on the ballA COMPARATIVE STUDY ON THE EFFECT OF USING

Parameters for the Grinding Process in Vertical Mills Using
2024年1月17日 The loading pressure, a value of 3 439 kWh/tons, equations were derived to estimate the grinding energy of the vertical roller mill by using the size and pistondie test data2022年3月30日 All industries are facing increasing pressure to ensure that carbon emissions are reduced to help achieve the socalled 15 °C future This has led to most of the major mining companies committing to significant reductions in their operational carbon footprint – in many cases by up to 30–40% in the next 10–15 years and to place themselves in a netzero scope Helping to reduce mining industry carbon emissions: A stepby 2022年3月1日 High Pressure Grinding Rolls (HPGR) circuits have the potential to reduce the Mining Industry’s CO2 emissions by up to 345 megatonnes/year, or 435% when compared to the established Autogenous Helping to reduce mining industry carbon emissions: A stepby 2021年2月15日 Grinding is an important process used for manufacturing fine particles in the chemical, pharmaceutical, ceramic, cosmetic, paint, paper, plastic, food, fine chemical and mining industries (Benz et al, 1996, Midoux et al, 1999, Chamayou and Dodds, 2007)The focus of the present study is grinding in a spiral air jet mill, also referred to as a fluid energy mill (Andrews, Analysis of grinding in a spiral jet mill Part 1: Batch grinding
.jpg)
Prediction and optimization of tower mill grinding power
High pressure grinding roll Wet screening +3 mm3 mm Wet permanent cylinder magnetic separator Tower mill Tailings Overflow outlet Fig 1 Tower mill grinding after rough separation process of highpressure grinding roll products in an iron mine Table 1 Particle size analysis results Size fraction (mm) Yield (%) Passing cumulative yield (%)2023年5月23日 Ultrasonic vibration–assisted grinding is an effective method for improving the surface quality of brittle and hard materials The grinding force is one of the key factors affecting the surface quality of the machined surface, and this has been investigated both experimentally and theoretically However, the influence of process parameters on grinding forces during Modeling of grinding force in longitudinal ultrasonic vibration