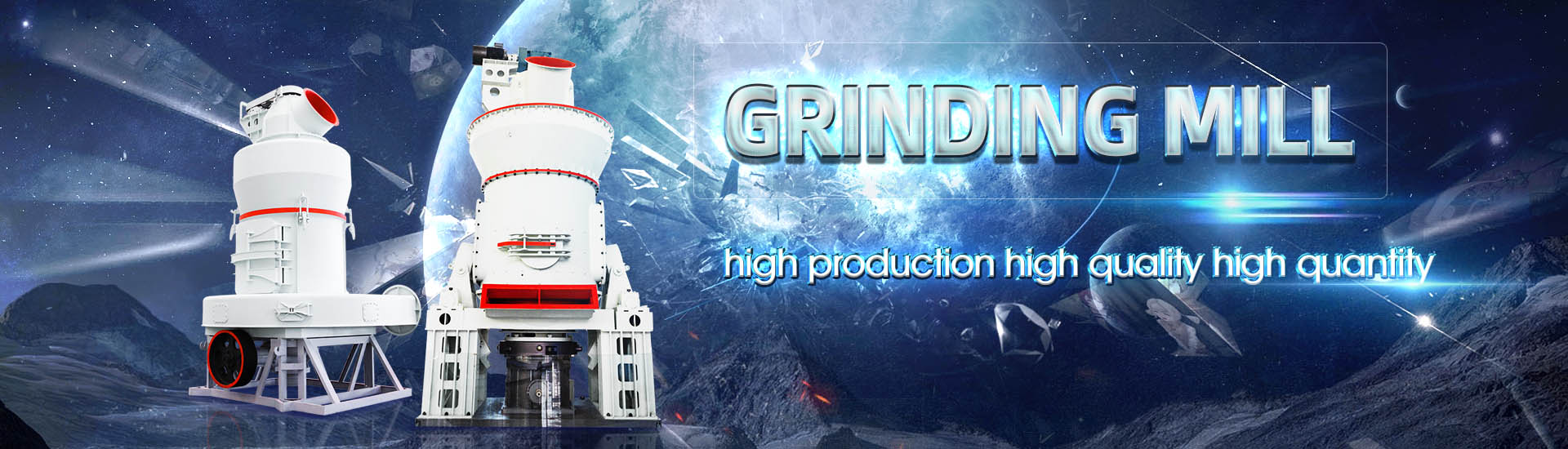
Grinding mill operation steps
.jpg)
Grinding Mills — Types, Working Principle Applications
2018年8月17日 Minerals Processing Framework (diagram) This is the stage where it all begins A rock cutting process, drilling sets the stage for the next Grinding can be achieved by several mechanisms, including: impact or compression due to sudden forces applied almost normally to the particle surface; chipping or attrition due to Grinding Mill an overview ScienceDirect TopicsGrinding is the process of removing metal by the application of abrasives which are bonded to form a rotating wheel When the moving abrasive particles contact the workpiece, they act as GRINDING MACHINES Carnegie Mellon UniversityGrinding is understood as a process of size reduction of materials to a fine powder The final grinding operation of clinker with gypsum is often termed finish grinding The terms pulverizing Grinding Operation an overview ScienceDirect Topics
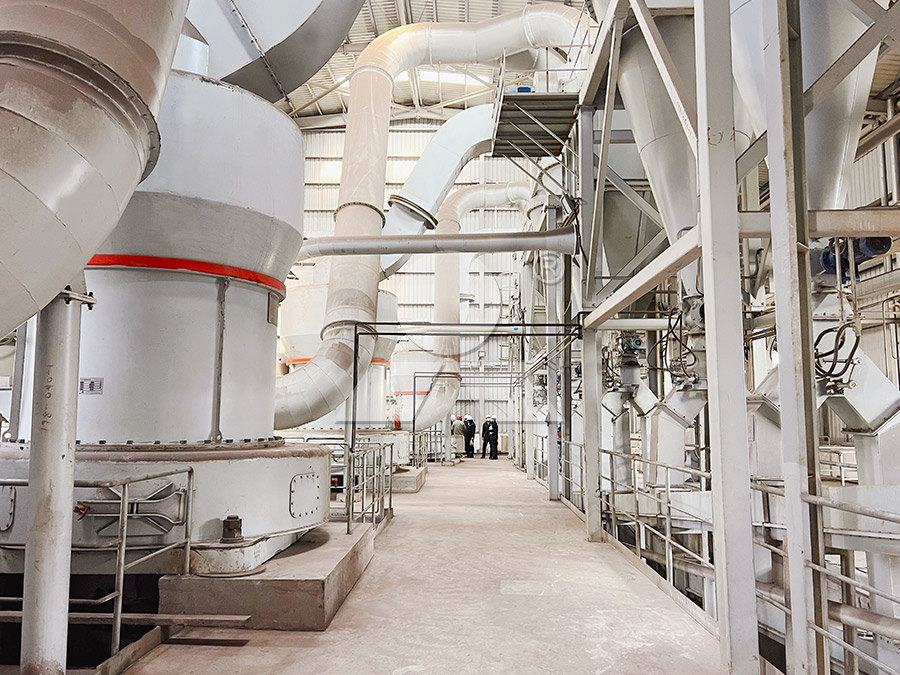
Grinding and Finishing IIT Bombay
Grinding – Ex 11 • You are grinding a steel, which has a specific grinding energy (u) of 35 Ws/mm3 • The grinding wheel rotates at 3600 rpm, has a diameter (D) of 150 mm, thickness (b) processoptimised operation of Loesche grinding systems with the main focus on efficient performance, throughput, product consistency and availability Failsafe PLC for hot gas PROCESS OPTIMISATION FOR LOESCHE GRINDING PLANTSThe principle objective for controlling grinding mill operation is to produce a product having an acceptable and constant size distribution at optimum cost To achieve this objective an attempt Grinding Mill an overview ScienceDirect TopicsGrinding is the last stage in the comminution process where particles are reduced in size by a combination of impact and abrasion, either dry, or more commonly, in suspension in water It Chapter 7 Grinding Mills Wills' Mineral Processing Technology,
.jpg)
Ball Mill Maintenance Installation Procedure
2016年10月20日 Am sure your Ball Mill is considered the finest possible grinding mill available As such you will find it is designed and constructed according to heavy duty 911 Metallurgist is a trusted resource for practical 2024年9月13日 5 Reducing and Grinding The purified grain particles are then reduced further in size through grinding This stage involves passing the grain through additional rollers that gradually reduce the particle size to produce fine The 8Step Grain Milling Process: Complete Guide 2024The document provides standard operating procedures for a ball mill It lists 18 steps for operating the ball mill, including connecting power, loading materials and grinding media, starting and stopping the mill, and unloading processed Ball Mill: Standard Operating Procedure PDF Mill The aim of the size reduction operations is to produce particles within a specified size range In the mill the grinding chamber is an oval loop of pipe 25 to 200 mm in diameter and 12 to 24 m high Feed enters through a venturi injector which is situated near the bottom of the loopSize Reduction1: Grinding – Unit Operations in Food Processing
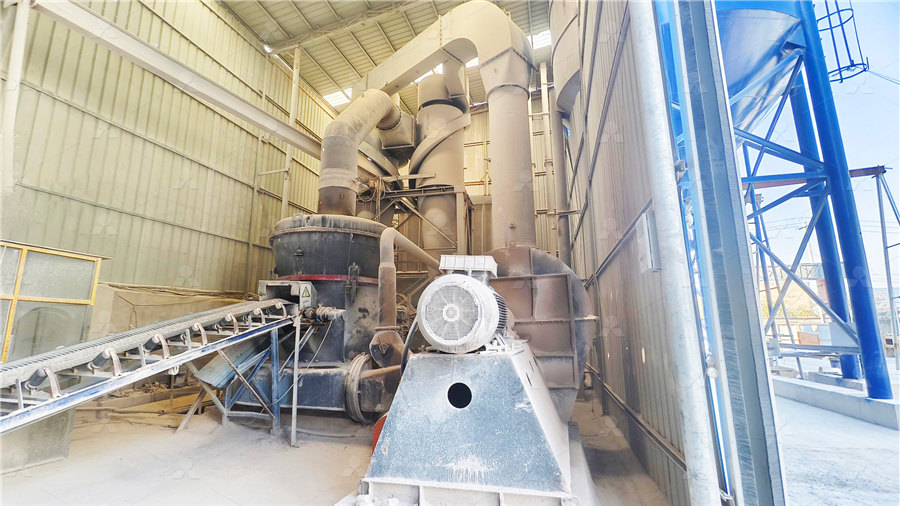
Mill (grinding) Wikipedia
A mill is a device, often a structure, machine or kitchen appliance, that breaks solid materials into smaller pieces by grinding, crushing, or cutting Such comminution is an important unit operation in many processesThere are many different types of mills and many types of materials processed in them Historically mills were powered by hand or by animals (eg, via a hand crank), 2016年6月6日 SAG Mill Operation In order to initiate the design of any mill, including autogenous and semiautogenous types, the operating conditions must be defined This includes the basic parameters of: A Mill Charge Charge Weight/Volume/Percent Filling Ore Specific Gravity Percent Rock or Ore Charge Percent Ball Charge (if semiautogenous)SAG Mill Grinding Circuit Design 911Metallurgist2023年10月20日 A ball mill is a crucial piece of equipment used for grinding and blending materials, commonly utilized in mineral processing, ceramics, and pyrotechnics industries Understanding the principles of operation and best practices for efficient and safe operation is essential for achieving optimal performance and minimizing prehensive Guide on Operating a Ball Mill MiningpediaThe principle objective for controlling grinding mill operation is to produce a product having an acceptable and constant size distribution at optimum cost waste was then dried to a 10% moisture content from a 40% initial moisture content before it underwent the pyrolysis stepGrinding Mill an overview ScienceDirect Topics
CFB石灰石脱硫剂制备——磨机公众号12.8 推送案例(8)51.jpg)
What is Grinding Process How It Works Different Types of Grinding
2022年11月28日 Grinding is a type of finishing process in mechanical processing, with less machining and high precision It is widely used in the machinery manufacturing industry The heattreated and quenched carbon tool steel and carburized and quenched steel parts often have a large number of regularly arranged grinding cracks on the surface that is basically 2024年7月21日 2 Grinding Operation Grinding can only be performed after completing the machine startup and pregrinding preparation operations Balance the grinding wheel before dressing it Pay attention to adjusting the mechanical zero point to ensure the correctness of each axis coordinateGrinding Machine Safety: Essential Tips for Operators2023年11月22日 Shoulder milling removes material from the side of a workpiece (the “shoulder” or “sidewall”) with different cutting tools, like end mills, to make flat, 90degree angles, like steps 6 Side Milling A side milling cutter or end 15 Types of Milling Operations XometryGrinding Mills: Ball Mill Rod Mill Design PartsCommon types of grinding mills include Ball Mills and Rod Mills This includes all rotating mills with heavy grinding media loads This article focuses on ball and rod mills excluding SAG and AG Grinding Mills 911Metallurgist

Grinding considerations when pelleting livestock feeds
roller mill during its normal expected life will be 10 to 20 times more expensive than the machine cost alone It is therefore very important to make sure the equipment selected is carefully matched to the specific grinding task to ensure most efficient operation For hammermills, the diameter (tip2024年8月8日 We encourage readers to leverage the outlined stepbystep guide to navigate the complexities of grinding media selection By thoroughly assessing milling requirements, comparing the attributes of different media types, and conducting trial tests, you can make informed decisions that optimize your milling operationsBall Mill Success: A StepbyStep Guide to Choosing the Right Grinding 2024年5月17日 A SAG (SemiAutogenous Grinding) mill is a giant rotating cylinder filled with grinding media and the ore being reduced As the mill rotates, the grinding media lifts and the impact crushes the feed material SAG mill control refers to the practice of managing the mill load, which is the amount of material inside the mill at any given timeA guide to SAG Mill management2022年10月11日 Maize Milling Processes and Terms explained Like any other industry, maize milling has its unique processes and terminology Here’s a simple explanation of how a maize mill works and the processes that can take place during the production of maize meal and bran, depending on the setup and size of the milling operation, and the type of maize meal required Maize milling process and terms explained – Roff Milling
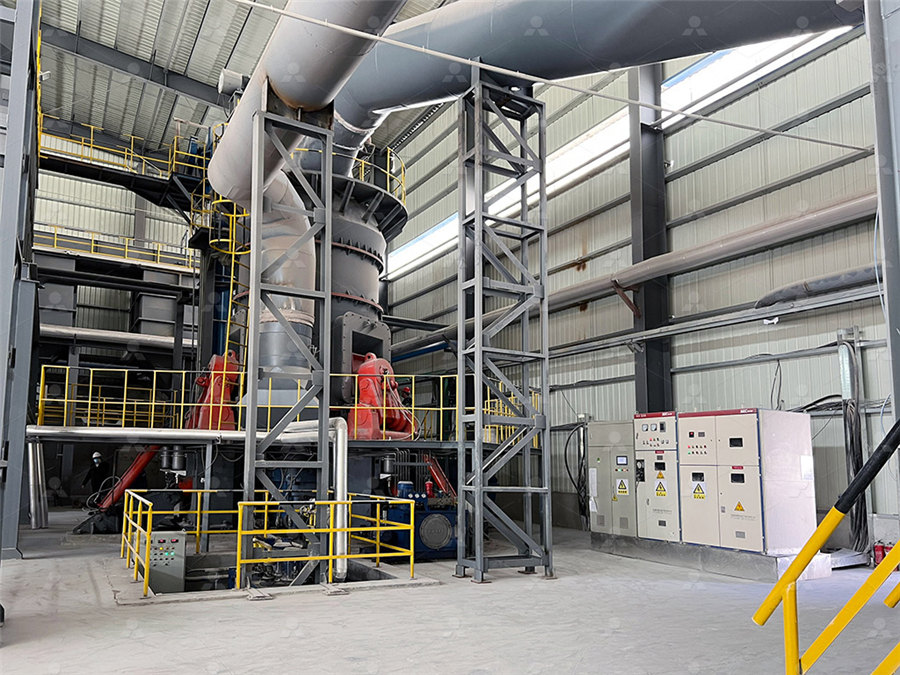
What is Milling: Definition, Process Operations
2023年7月10日 Common postprocessing steps are deburring, cleaning, grinding, surface treatment, etc What are the Different Types of Milling Operations? This leads to a highly efficient mill operation Slab Mill: Slab mill cutter is used for machining planes It is also known as a 2022年3月30日 The final step is to choose a ball mill diameter, length and speed that will draw the installed power when loaded with the mill’s maximum allowable ball load The maximum ball load needs to be chosen in conjunction with the equipment supplier as it is related to the structural integrity of the mill shell, which in turn is related to such factors as the shell thickness, steel Helping to reduce mining industry carbon emissions: A stepbystep mills for drygrinding the abovementioned grinding stock Loesche has developed and built the largest and most efficient grinding plants for its customers Loesche plants are specifically planned for the required process steps and equipped with the associated techno logy This technology comprises: • Processing plants and material storagePROCESS OPTIMISATION FOR LOESCHE GRINDING PLANTSVRM operation SOPs Free download as PDF File (pdf), Text File (txt) or read online for free The document provides standard operating procedures for grinding mills It discusses four mill operation conditions based on relationships between mill power, pressure loss, and process parameters For each condition, it identifies potential causes and recommends corrective VRM Operation SOPs PDF Mill (Grinding) Pressure
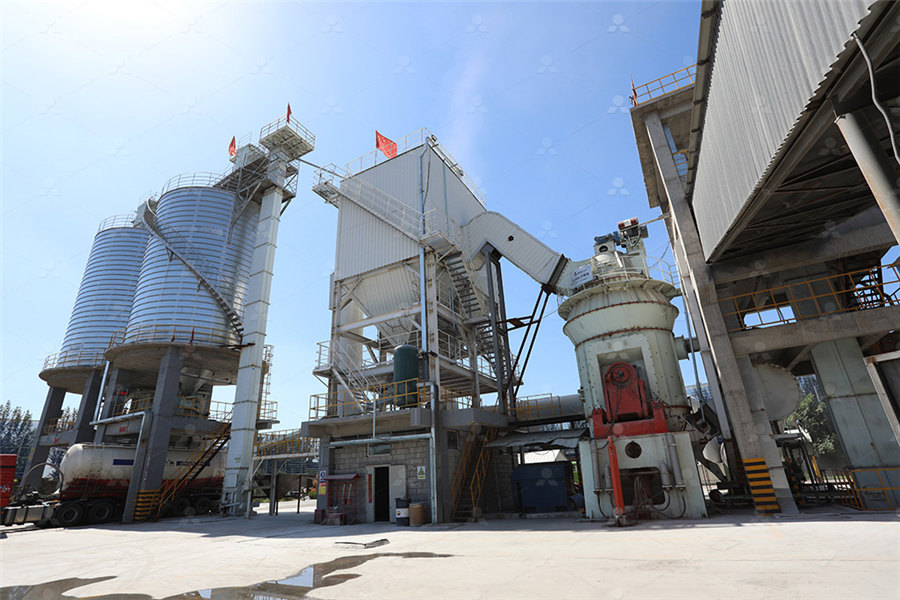
Grinding SpringerLink
2022年2月28日 The mill operation mode including continuous grinding or batch grinding or circuit 3 mineral particles continuously come out of the chamber through a pipe installed in the upper part of the mill In this step, grinding media are The operating principle of the ball mill consists of the following steps and moves there along with grinding media (balls) Fig1: Cascade Operation in Ball Mill (a) Low Speed (b It can be used for continuous operation if a sieve or Ball Mill Principle, Construction, Working, and More2024年8月23日 For instance, slower operations with a fly cutter can yield a very smooth and shiny surface Types of Face Milling Operations Based on the capability and process characteristics, there are three major types of face mill What is Face Milling? Process, Tools, and Applications2023年4月20日 In the process of grinding feldspar particles are ground into powder with a fineness requirement of 200 mesh in the mill Then we use a magnetic separator to separate ironbearing materials According to different feldspar, we choose different useful feldspar processing method, such as gravity concentration and flotationSeveral Steps And Required Equipment For Feldspar Mining And
.jpg)
Iron Ore Processing: From Extraction to Manufacturing
2024年4月26日 The choice of grinding mill depends on factors such as the desired product size, capacity requirements, and energy consumption b Autogenous and SemiAutogenous Mills: Grinding and beneficiation are crucial steps in iron ore processing as they enhance the concentration of ironbearing minerals and remove impuritiesOverview of cement clinker grinding Vipin Kant Singh, in The Science and Technology of Cement and Other Hydraulic Binders, 2023 91 Introduction Grinding is understood as a process of size reduction of materials to a fine powder The final grinding operation of clinker with gypsum is often termed finish grinding The terms pulverizing and milling are basically synonymous with Grinding Operation an overview ScienceDirect TopicsGrinding costs are driven by energy and steel (media, liners, etc) consumption; grinding is the most energyintensive operation in mineral processing On a survey of the energy consumed in a number of Canadian copper concentrators it was shown that the average energy consumption in kWh t −1 was 22 for crushing, 116 for grinding, and 26 for flotation ( Joe, 1979 )Grinding Mill an overview ScienceDirect TopicsThe Autogenous Mill, also known as AG Mill, is a type of grinding mill used in the mining industry This machine uses ore and rock itself as grinding media to perform its job Unlike other types of mills that use steel balls or rods for grinding materials, the Autogenous Mill relies on the material being ground to break itself into smaller piecesUnderstanding the SAG Mill in Copper Ore Mining Process
.jpg)
Machining 101: What is Grinding? Modern Machine Shop
2021年7月3日 Precision grinding is a middleground between metal removal and part size control, and serves as the basis for creep feed grinding, slot grinding and highefficiency deep grinding In ultraprecision grinding, little to no actual cutting occurs, but sliding action from very fine grains rubs the workpiece surface to a high finishUnderstanding the operational principles and factors that influence mill performance is crucial for optimizing mill operations and achieving the desired particle size for downstream processes By considering these factors, mining companies can enhance the productivity and costeffectiveness of their grinding mill operationsUnderstanding the operation of grinding mills in the mining and Ball Mill Grinding Machines: Exploring the Working Principle, Types, Parts, Applications, Advantages, and Recent Developments Ball mill grinding machines are widely used in various industries for the comminution of materials into fine Ball Mill Grinding Machines: Working Principle, Types, 4 Key Steps in the Operation of a Grinding Mill 1 Introduction of Material The material to be ground is introduced into the grinding mill This can be done through a hopper or directly into the grinding chamber, depending on the design of the mill 2 Interaction with Grinding MediaHow Does a Grinding Mill Work? 4 Key Steps Explained
.jpg)
Grinding in Ball Mills: Modeling and Process Control
2012年6月1日 As the cylinder starts to rotate, the grinding balls inside the cylinder crush and grind the feed material, generating mechanical energy that aids in breaking bonds, activating the catalyst, and 2014年7月15日 It is a sad fact that in many processing operations across North America and Canada mill maintenance is seen as little regular maintenance is as vital as the grinding mill machine itself, but to get the very most from it, a dedicated cleaning mill equipment is the first step There are any number of issues Mill Maintenance Plan: 3 Steps That Maximize Mill Productivity and This step involves the material being retained inside the mill for a specific time (with or without grinding balls) which is calculated by applying Bond’s work index to the process calculation This index takes into account the material ore hardness and feed size, mill speed, material recirculation, desired fineness, etcThe six main steps of iron ore processing MultotecThe milder abrasives like 32 and 38 Aluminum Oxide are best for lighter precision grinding operations on steels and semisteels, while the intermediate 57 and 19 Aluminum Oxide abrasives are used for precision and semiprecision grinding of both mild and hard steels The severity of the grinding operation also influences the choice of gradeChapter 5: Surface Grinder – Manufacturing Processes 45
.jpg)
Wet Ball Milling Method and Technology allwingrinding
This step is crucial for increasing the concentration of valuable minerals and improving the economics of the mining operation Tailings Management: Wet grinding also helps in the management of tailings, Allwin, est 1993 in China, specializes in wet grinding mill equipment for enterprises Our ISOcertified factory produces over 10k 2020年11月18日 Grinding, also called surface grinding, is a machining operation in which material is removed using a powered abrasive wheel, stone, belt, paste, sheet, compound, etc to realize fine finish tolerances and surface finishes While there are a number of ways to grind parts, grinding is a more precise method of tolerance modificationManufacturing Process: Grinding Huyett2024年11月4日 A 6week modular course is designed to give the course attendee a solid understanding of the grinding system and its auxiliary equipment The purpose of the training is to Identify and understands necessary known and unknown information towards the completed cycle of the grinding system, whether it is a ball mill, vertical mill, or crushing processGRINDING TECHNOLOGY COURSE The Cement Institute2024年1月11日 This grinding operation, fundamental in manufacturing, hinges on the precision and efficiency of the surface grinding machine and its components Now, let’s dive into the specifics: The rotating abrasive wheel, typically made of materials like aluminum oxide or silicon carbide, is key in this processSurface Grinding: A Guide to the Process and Precision okdor