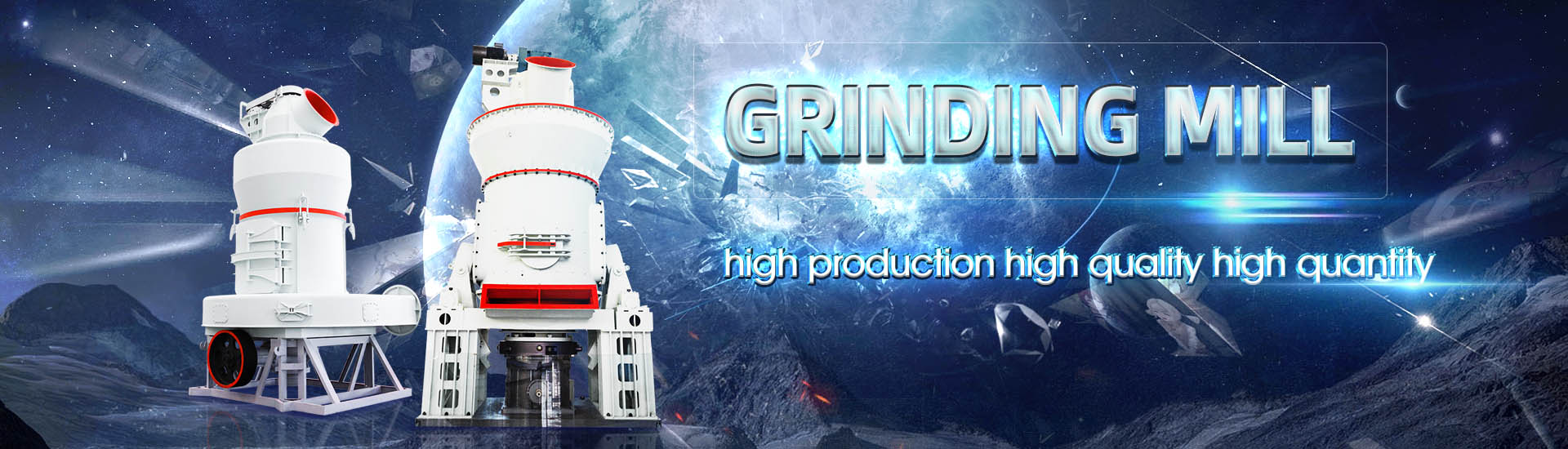
How to screen steel balls in coal mill
.jpg)
Ball Mill Steel Balls: Quality And Gradation JXSC Mineral
2024年2月19日 Let’s look at how to obtain a reasonable gradation of ball mill grinding body steel ball media and how to select ball mill steel balls Determine the steel ball gradation based on the particle size, hardness, grindability of the 2015年6月6日 Screen out the ball charge, cleaning the balls and returning then to the mill Brush the ground product from the ball screen and tray onto a square kraft paper Split the product roughly into thirdsBond Work Index Procedure and Method2023年10月27日 Grinding media play an important role in the comminution of mineral ores in these mills This work reviews the application of balls in mineral processing as a function of the A Review of the Grinding Media in Ball Mills for Mineral Processing 2017年3月4日 The process Comminution involves size reduction and sizewise classification called as screening/ separation Milling is one of the most important industrial processesSIZE REDUCTION BY GRINDING METHODS
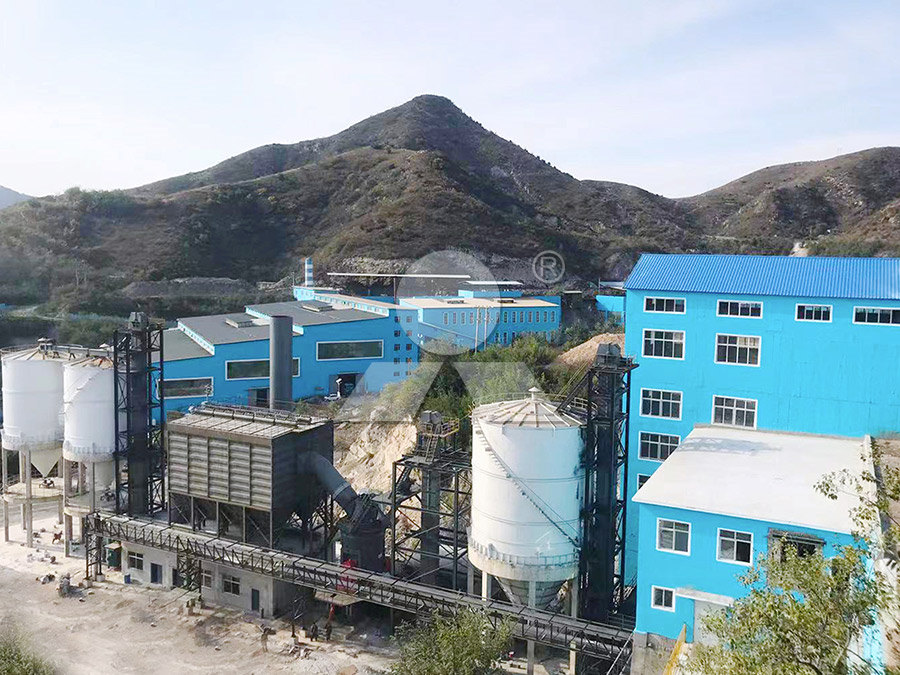
Calculate and Select Ball Mill Ball Size for Optimum
2013年8月3日 In Grinding, selecting (calculate) the correct or optimum ball size that allows for the best and optimum/ideal or target grind size to be achieved by your ball mill is an important thing for a Mineral Processing Engineer AKA Grinding in ball mills is an important technological process applied to reduce the size of particles which may have different nature and a wide diversity of physical, mechanical and chemical Grinding in Ball Mills: Modeling and Process Control Sciendo2015年6月19日 Use this online calculators for Motor Sizing and Mill sizing as well as mill capacity determinators In extracting from Nordberg Process Machinery Reference Manual I will also provide 2 Ball Mill Sizing (Design) Ball Mill Design/Power Calculation 911MetallurgistBall mills are the most common type of coal grinding mill, and are characterized by their simple design and low maintenance requirements They use steel balls to crush and grind the coal What is a Coal Grinding Mill
.jpg)
Ball Mill Success: A StepbyStep Guide to Choosing
2024年8月8日 Steel Balls: Predominantly made from carbon steel, stainless steel, or alloy steel, steel balls are renowned for their high density and impact strength This makes them especially suitable for heavyduty milling tasks in cast abrasionresistant liners and partially filled with hardened steel balls Coal and preheated primary air enter one or both ends of the mill from a crusher/dryer or feeder As the mill rotates, the balls cascade and pulverize the coal by impact and attrition The pulverized coal is then conveyed by air to centrifugal classifiersA Comparison of Three Types of Coal Pulverizers Babcock PowerWhat is the difference between a ball mill and a coal pulverizer? A ball mill is a machine that grinds materials up to a consistent size using steel balls as the grinding medium A coal pulverizer is a machine that pulverizes coal to a fine powder for combustion in power generation, cement production, and other industries How does the ball How Is Coal Pulverized in a Ball Mill?They use steel balls to crush and grind the coal material, which is then discharged through a screen to separate the fine particles from the coarse ones The grinding process in ball mills is controlled by the rotating speed of the cylinder, which can be adjusted to achieve the desired particle size distributionWhat is a Coal Grinding Mill
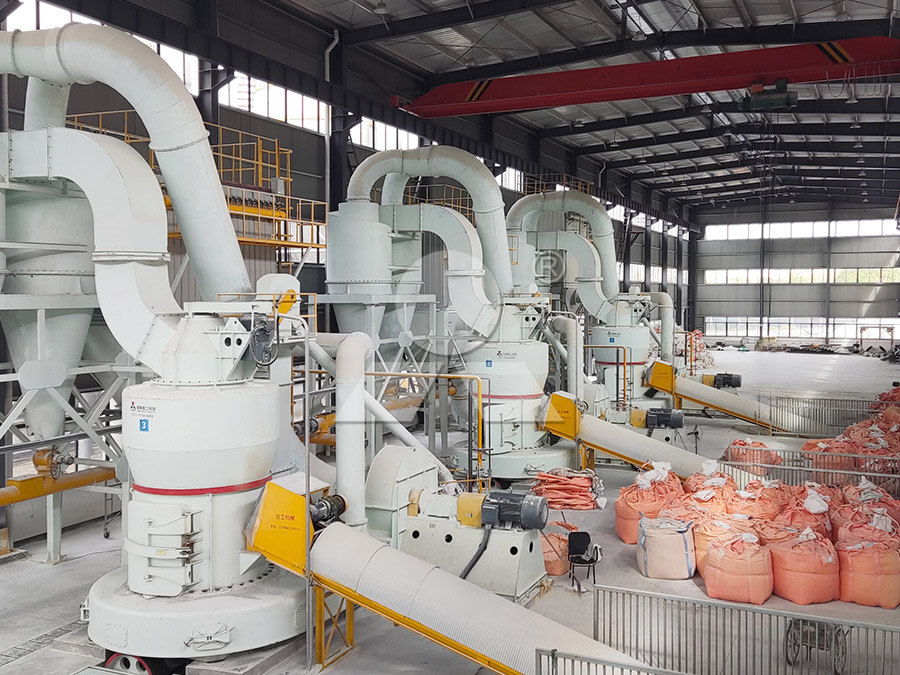
Ball Mill Design/Power Calculation 911Metallurgist
2015年6月19日 The basic parameters used in ball mill design (power calculations), rod mill or any tumbling mill sizing are; material to be ground, characteristics, Bond Work Index, bulk density, specific density, desired mill tonnage capacity DTPH, operating % solids or pulp density, feed size as F80 and maximum ‘chunk size’, product size as P80 and maximum and finally the type of 2019年8月30日 1 Calculation of ball mill capacity The production capacity of the ball mill is determined by the amount of material required to be ground, and it must have a certain margin when designing and selecting There are many factors affecting the production capacity of the ball mill, in addition to the nature of the material (grain size, hardness, density, temperature and Ball Mill Parameter Selection – Power, Rotate Speed, Steel BallCoal mill is suitable for types of coal with various hardness and humidity Coal ball mill is mainly used in coal power plant or mineral calcining system Skip and the grinding chamber is rotated to bring up the grinding media steel balls and throw them off After being ground for a period of time, the coal is turned into a powdery Coal Ball Mill Grinding for Different Kinds of Pulverized Coal2019年12月19日 How to add milling balls proportionately Generally, the newly installed ball mill has a runningin process During the runningin process, the amount of steel balls is added for the first time, which accounts for 80% of the maximum ball load of the ball millHow Many Balls in a Ball Mill? JXSC Machine
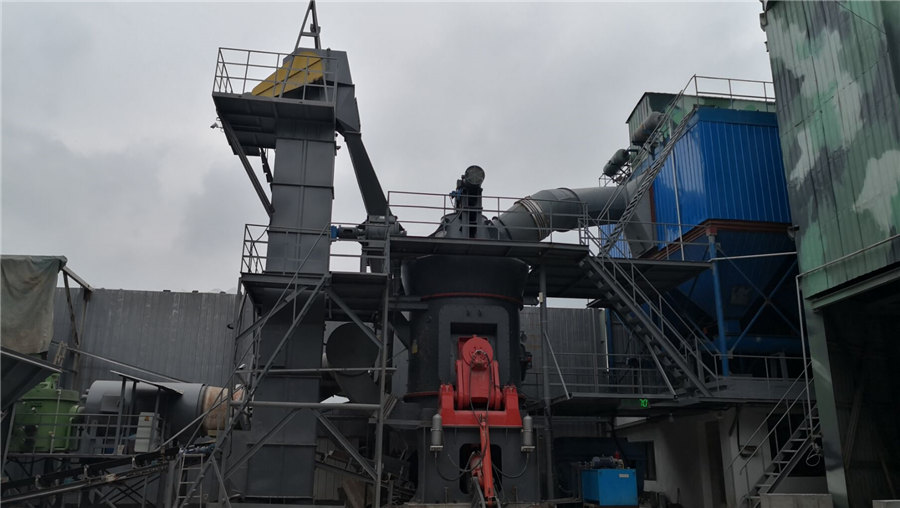
low carbon steel balls scaw KOOKS
Carbon Steel Balls Scaw baoliforkliftsco low carbon steel balls scaw igdbombayart Low Carbon Steel Ballsnsnballs Product Description Mechanical Properties Hardness for low carbon steel balls, as measured on the balls surface is Rockwell 'C'(minimum) and subject to Chat With Sales Solved: Carbon steel balls (ρ The balls introduced into the mill vary from 2 to 10 cm in diameter and the wear is from 02 to 05 kg per ton of product These figures are applicable to the grinding of cement and coal The ball wear is compensated for by introducing one or more fullsized balls to the mill at least once a dayBall Mill an overview ScienceDirect TopicsSteel balls Steel balls are one of the most widely used grinding media in cement ball mills, their diameters can range from 20mm to 150mm according to different grinding requirements In a cement ball mill, generally, φ50100mm steel balls are used in the coarse grinding chamber, φ2050mm steel balls are used in the fine grinding chamber 2Ball Mill Grinding Media Steel Balls for Ball Mills AGICO GroupA ball mill operates by rotating a cylinder with steel or ceramic balls, causing the balls to fall back into the cylinder and onto the material to be ground The rotation of the cylinder is typically between 4 to 20 revolutions per minute, depending on the diameter of the mill The larger the diameter, the slower the rotationA Comprehensive Guide to Ball Mill Manual
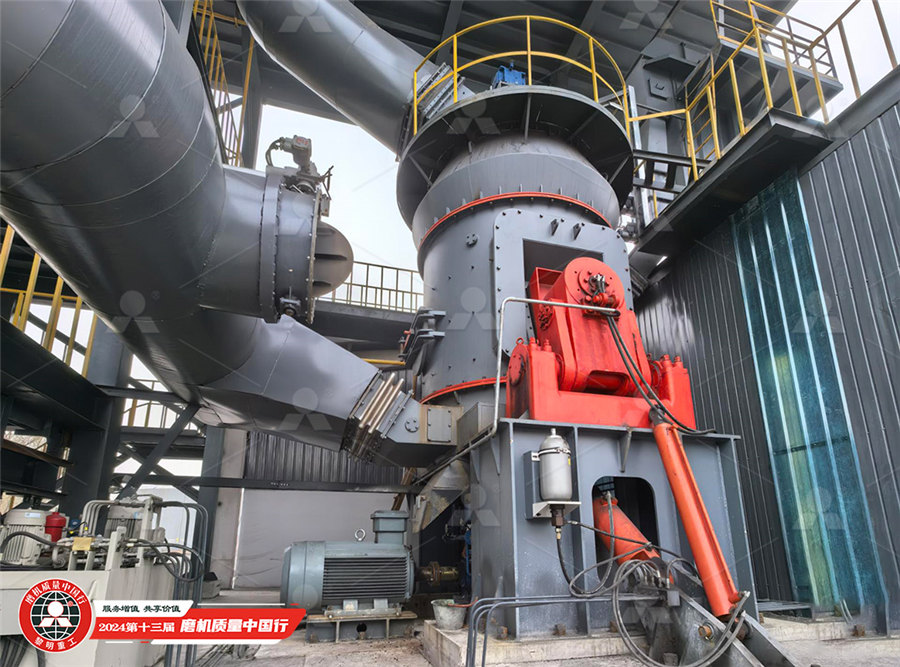
SIZE REDUCTION BY GRINDING METHODS
2017年3月4日 A stamp mill (or stamp battery or stamping mill) is a type of mill machine that cru shes material by pounding rather than grinding, either for furthe r processing or for extraction of metallic oresCoal Mill Operational parameters: Mill Load (Kw or Amps) Mill sound/filling % (in ball mills) Mill Inlet Temperature (0 C) To economize grinding media consumption, presently grinding media used are high chrome steel balls Mill shell is lined with lining plates to protect it from wear, Coal Grinding Cement Plant Optimization2023年10月4日 Mining balls, in various forms such as grinding balls, steel grinding balls, forged steel grinding balls, and rolled grinding balls, are indispensable components in the mining industryThese durable and precisely crafted spheres play a pivotal role in crushing and grinding raw materials, contributing to efficient material processing and resource extractionMining Balls: The Backbone of Material Processing2020年7月2日 A comprehensive investigation was conducted to delineate the effect of ball size distribution, mill speed, and their interactions on power draw, charge motion, and balls segregation in a (PDF) Effects of Ball Size Distribution and Mill Speed and Their
.jpg)
17 Signs of Problems with Ball Mills: Quickly Remove Hidden Troubles
2023年2月15日 Too many useless balls If there are too many useless balls, the broken ball rate will increase, and the load of the ball mill will also increase Too much largediameter steel ball would cause wear problems 2 Ways to avoid the steel balls consumption 1 Use medium with high quality and strong wear resistancea 6mesh screen until all of it bas passed the screen The combined minus 6mesh screen undersize is mixed, sampled and screenanalyzed, and its apparent specific gravity is determined by packing and shaking in a standard container, and weigh ing The apparent specific gravity ordi narily is about 60 per cent of the trueStandard Grindability Tests and Calculations 911 Metallurgist2017年4月29日 In the previous discussion the fact was established that the work done by a ball when it strikes at the end of its parabolic path is proportional to its weight and velocity; then, since the velocity may be considered as constant for all the balls in the mill, the work done by a ball is proportional to its weight Since the amount of ore crushed varies as the work done upon it, it Grinding Media Wear Rate Calculation in Ball Mill2024年10月14日 When selecting high chrome steel grinding media balls, consider the following criteria: Mill Productivity: Choose media that enhances the productivity of your grinding mill, allowing for efficient operation; Cost: Look for a balance between the performance of the grinding media and its cost, ensuring it fits within your budget; Material Properties: The grinding media Everything You Need to Know About High Chrome Steel Grinding Media Balls
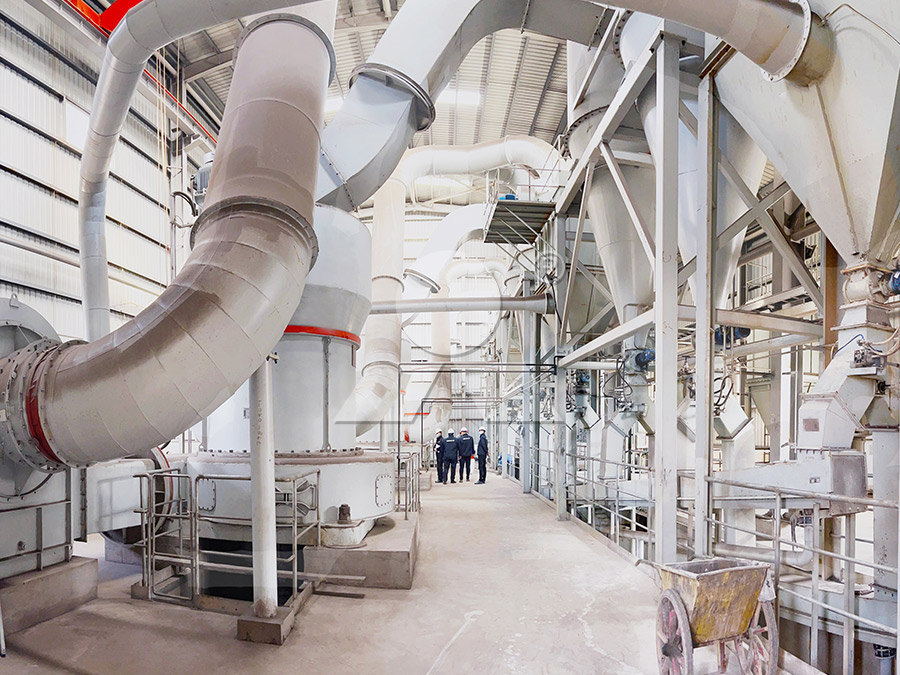
(PDF) Grinding Media in Ball MillsA Review ResearchGate
2023年4月23日 coal and cement HCCI is ferrous based alloyed with 1135 wt% chrom ium and 1875 wt% carbon of cement clinkers was higher with cylpebs grinding media than with steel balls in a ball millThe amount and ball size distribution in this charge, as well as the frequency with which new balls are added to the mill, have significant effects on the mill capacity and the milling efficiency Small balls are effective in grinding fine particles in THE OPTIMAL BALL DIAMETER IN A MILL2024年1月11日 With a ball mill 1 To pulverize crushed coals in a ball mill, you start by feeding the mill with crushed coal Then the grinding media crushes and grinds the coal in the rotating chamber 2 Airflow carries the pulverized coal How to Process Coal into Pulverized Coal in 5 Steps?We specialize in the production of cast grinding balls, ball mill forging steel balls, wearresistant steel balls, grinding steel balls, forged steel balls, and forging balls Our grinding balls are mainly used in mining, power plants, cement, chemical, Grinding Ball Ball Mill Balls For Sale Ball Mill Media
.jpg)
How to Load Steel Balls into Ball Mills LinkedIn
2024年1月16日 Open the Ball Mill:Depending on the design of the mill, open the hatch or access door to the mill chamber Load the Balls:Use a scoop or funnel to introduce the steel balls into the millBegin 2019年11月7日 Comprehensive treatment,we should have a test on the 300 MV unit steel ball coal mill pulverizing systemAt the same time,analyze the main operating parameters before modificationTransform the Optimization and transformation of 300MV units steel ball coal mill 2015年10月15日 A) Total Apparent Volumetric Charge Filling – including balls and excess slurry on top of the ball charge, plus the interstitial voids in between the balls – expressed as a percentage of the net internal mill volume (inside liners) B) Overflow Discharge Mills operating at low ball fillings – slurry may accumulate on top of the ball charge; causing, the Total Charge Calculate Ball Mill Grinding Capacity 911Metallurgist2012年6月1日 The feed material is typically composed of the BFRs and the catalyst, both in powder form As the cylinder starts to rotate, the grinding balls inside the cylinder crush and grind the feed Grinding in Ball Mills: Modeling and Process Control
.jpg)
Grinding in Ball Mills: Modeling and Process Control Sciendo
is lined with mill liners protecting the steel body of the mill and incorporating mill lifters which help to raise the content of the mill to greater heights before it drops and cascades down [36] There are three types of grinding media that are commonly used in The Planetary Ball Mill PM 100 is a powerful benchtop model with a single grinding station and an easy catalysts, cellulose, cement clinker, ceramics, charcoal, chemical products, clay minerals, coal, coke, compost, concrete, electronic scrap, fibres, glass, gypsum 8 x 30 mm stainless steel grinding balls 5 min at 380 rpm Hardbrittle Planetary Ball Mill PM 100 RETSCH highest fineness2016年6月20日 Stroke length, rotation speed, stroke angle, and screen inclination form together parameters which affect the operation of the screen These fundamental factors have to be in proportion to each other Stroke length and material amplitude have an effect on: – how the feeder material starts to separate in the feed box and on the screen elementOre, Rock Aggregate Screening (Complete Guide)2024年1月28日 2 Liners: An abrasionresistant material such as manganese steel or rubber typically lines the inner surface of the cylindrical shell to protect it from wear due to the grinding action 3 Balls: They place steel or ceramic Ball mill: Principles, construction, working, uses, merits,
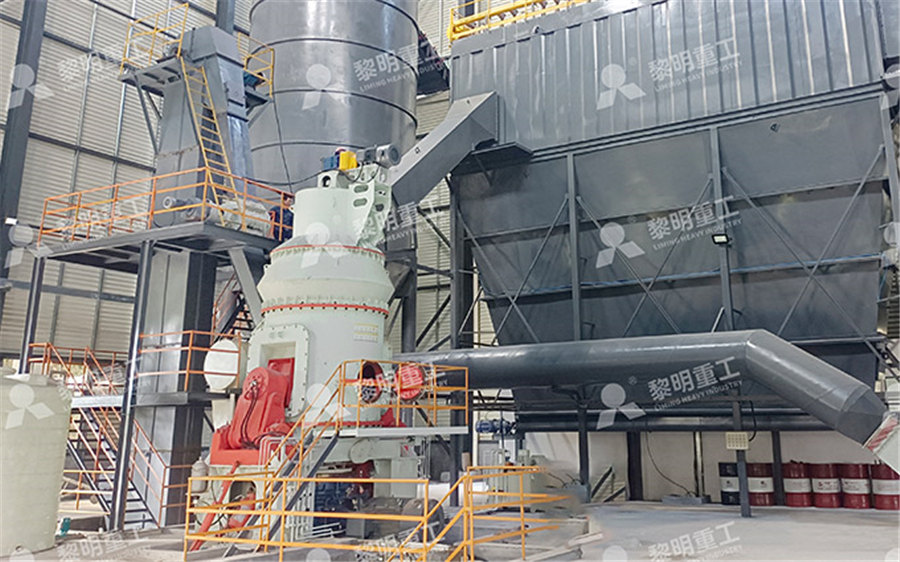
Technique to Investigate Pulverizing and Abrasive Performance of Coals
2021年11月4日 The operating costs of breaking coal particles into fine powder, to achieve optimum combustion for the boilers in a power plant, are made up of power input to carry on an energy intensive 2017年2月13日 In all ore dressing and milling Operations, including flotation, cyanidation, gravity concentration, and amalgamation, the Working Principle is to crush and grind, often with rod mill or ball mill, the ore in order to liberate the Ball Mills 911Metallurgist2015年9月6日 Although it was developed nearly 50 years ago, Bond‘s method is still useful for calculating necessary mill sizes and power consumption for ball and rod mills This paper discusses the basic development of the Bond method, the determination of the efficiency correction factors based on mill dimensions and feed characteristics, and the application of the Calculate Top Ball Size of Grinding Media FRED C BOND 2016年10月20日 Ball Mill GEAR GUARD A plate steel gear guard is furnished with the mill for safety in operation and to protect the gear and pinion from dirt or grit As soon as the gear and pinion have been cleaned and coated with the proper lubricant, the gear guard should be assembled and set on its foundation DISCHARGE HOUSING “Doghouse”Ball Mill Maintenance Installation Procedure 911Metallurgist
.jpg)
STEEL MILLING BALLS FOR BALL MILLS Specifications
415 The balls of the 5th group are manufactured of steel, the carbon equivalent of which shall be no less than: 075% for balls with rated diameter of 1560 mm provided that carbon weight percentage in steel shall be no less than 060%; 080% for balls with rated diameter of 70120 mm provided that carbon weight percentage inThe sizes of FTM Machinery grinding steel balls can be designed according to customer requirements Generally, the ball diameter is between 20 mm and 125 mm You can also design 10 mm, 11 mm or other diameters of steel balls Small steel balls: 40 mm or 60 mm Medium balls: 80 mm Large steel balls: 100 mm or 120 mmChoose the Best Grinding Steel Balls for Your Ball Mill Fote 2021年6月29日 Nowadays, ball mills are widely used in cement plants to grind clinker and gypsum to produce cement The research focuses on the mill speed as well as air classifier speed effect on the two Effects of Mill Speed and Air Classifier Speed on Performance of miniature vertical spindle ball mill’s mortar along with 1inch steel balls A weighted upper race is placed on the coal sample and the steel balls and the ball mill is made to rotate for 50 revolutions The crushed coal samples are then removed and sieved The quantity of the crushed coal passing through 200 mesh (75 µm) is weighed andA Study on 500 MW Coal Fired Boiler Unit’s Bowl Mill
.jpg)
What are the Components of Ball Mill Inside and How to Repair
Inside the cylinder, there are steel balls of different sizes that are used to grind the material The material is fed into the mill through a hollow trunnion at the end of the cylinder The grinding media, the balls, are then lifted by the mill’s rotation and fall back down onto the material, thus crushing it into a fine powder