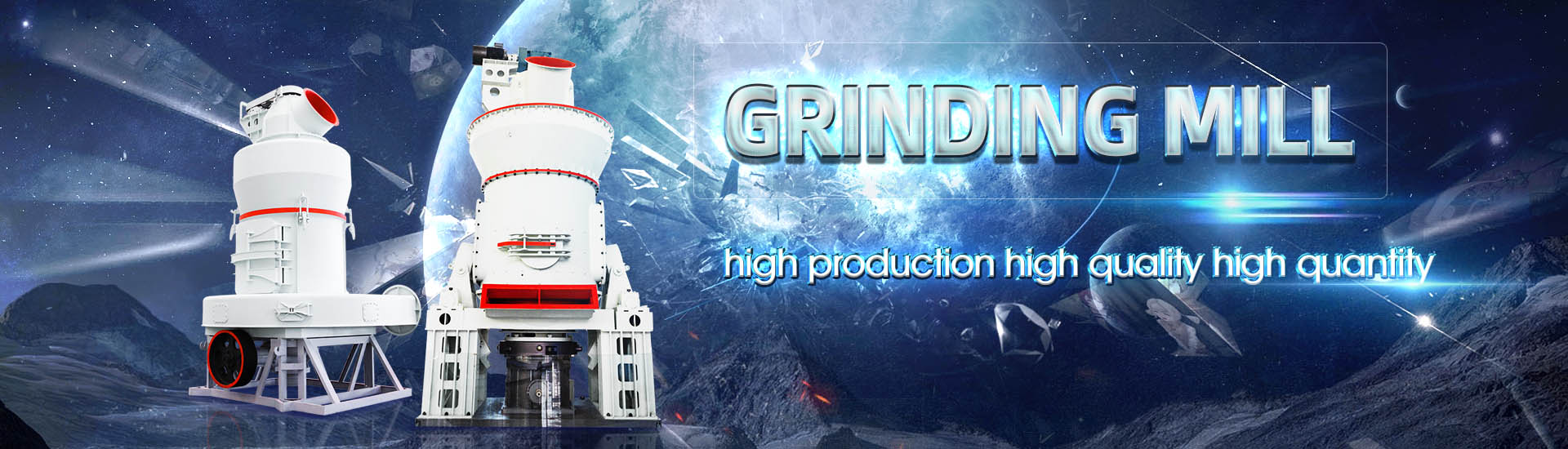
The purpose of particle ore mill in the unit
.jpg)
Mineral processing Wikipedia
Mineral processing is the process of separating commercially valuable minerals from their ores in the field of extractive metallurgy Depending on the processes used in each instance, it is often referred to as ore dressing or ore milling Beneficiation is any process that improves (benefits) the economic value of the ore by 展开2017年9月1日 The objective of this work is to assess the influence of fine grinding in ball mills and stirred mills on valuable mineral liberation and particle shape characteristics of UG2 ore, a Fine grinding: How mill type affects particle shape characteristics 2020年6月1日 The purpose of comminution in ore processing is to reduce particle size in order to improve liberation of valuable minerals and so enable separation from the undesirable Stirred media mills in the mining industry: Material grindability The IsaMill is a horizontal high speed stirred mill that operates with very high power intensities (up to 350 kW/m3) In comparison, the power intensity of a ball mill is about 20 kW/m3 The high ISAMILL FINE GRINDING TECHNOLOGY AND ITS INDUSTRIAL
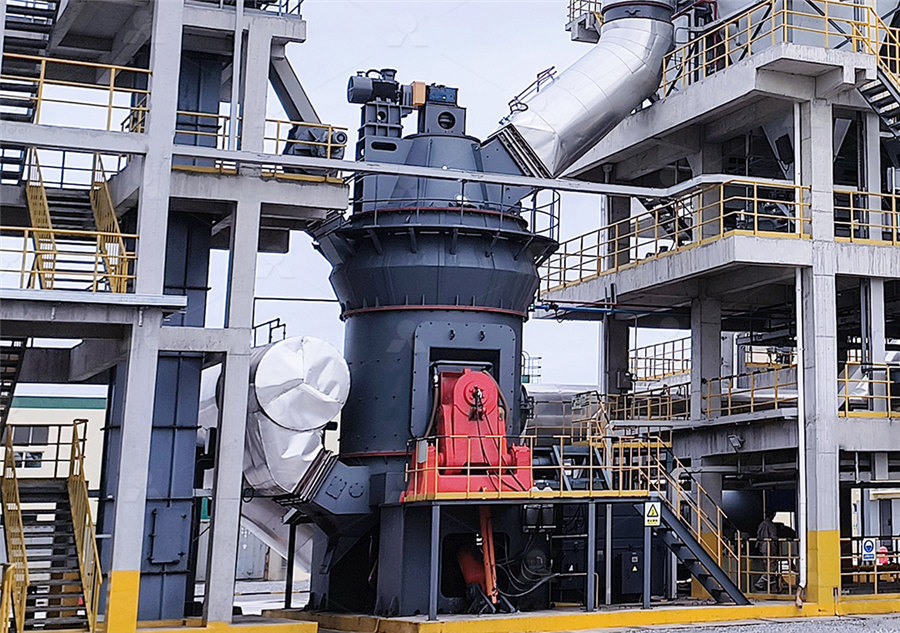
Developing a particlebased process model for unit operations of
2016年9月10日 The purpose of this paper is to develop a particlebased unit operation model for geometallurgical purposes by using wet low intensity magnetic separation (WLIMS) as a case Stirred milling was developed for fine grained ores that required an economic grind to sub 10 micron sizes The first examples were lead zinc deposits – McArthur River, George Fisher and Fine Grinding as Enabling Technology – The IsaMill2017年8月24日 In fact, the purpose of the size reduction or comminution process is threefold: (a) to liberate valuable minerals from the ore matrix, (b) to increase surface area for high reactivity Mineral Processing SpringerLink2024年1月1日 Ore grinding is a process to further reduce and disperse the ore particle size In the mineral processing industry, ore grinding is the particle size preparation before the Ore Grinding SpringerLink
.jpg)
Comminution SpringerLink
2015年2月2日 Comminution is defined as the action of reducing a material, especially a mineral ore, to minute particles or fragments [45] In the minerals industry, breakage is achieved 2017年10月1日 In this article, we present laboratory scale batch grinding and leaching profiles of a monosized gold ore sample (1700 + 850 μm) The sample was obtained from a runofmine (PDF) Determining optimum wet milling and leaching parameters Crushing, a form of comminution, one of the unit operations of mineral processing Mineral processing is the process of separating commercially valuable minerals from their ores in the field of extractive metallurgy [1] Depending on the processes used in each instance, it is often referred to as ore dressing or ore milling Beneficiation is any process that improves (benefits) the Mineral processing Wikipedia2018年8月17日 The concept of ore blending is a very relevant notion in modern high tonnage production mines It is not only essential for the prolongation of the mine life of the concerned mine but as well as a The effects of ore blending on comminution
.jpg)
Particle size distribution (PSD) of the mill feed
The dosage of a collector is an important factor that determines the efficiency of a froth flotation process The representative sample of the carbonatitic Palabora copper ore ground 45 % passing Investigation on the particle size and shape of iron ore pellet feed using ball mill and HPGR 909 areas of 500–1600 cm2 g1The concentrate must therefore be reground in order toInvestigation on the particle size and shape of iron ore pellet feed 2015年2月2日 The ball mill work index of an ore sample is calculated by Eq : $$ {W}i=\frac{491 Double contact point breakage mimics the breakage mode in jaw/cone crushers and in a mill when a particle is compressed between an impacting balls or rock and the Figure 628 shows the typical circuit configuration of a stirred mill minution SpringerLink2021年1月22日 Request PDF Impact of ball filling rate and stirrer tip speed on milling iron ore by wet stirred mill: Analysis and prediction of the particle size distribution The wet grinding of iron ore Impact of ball filling rate and stirrer tip speed on milling iron ore
.jpg)
Ore Sorting Strategies In Mineral Processing
For successful mineral processing design it’s critical to evaluate the possibility of preconcentration or waste diversion before grinding Mess up this step and you could be hit with avoidable downstream CAPEX and OPEX costs At its core, preconcentration means exploiting particle differences as early as possible so that waste material isn’t unnecessarily fed to the mill and 2021年5月15日 mediumsized SAG mill, that implies a particle size less than 05 m A mediumsized haul truck is then resolved by more than 100 particles that may disperse on the pileDigital Twins with Distributed Particle Simulation for MinetoMill Mill Diameter Mill Length Installed Power Mill Volume Power Intensity (m) (m) (kW) m3 (kW/m3) Autogenous Mill 10 45 6400 353 18 Ball Mill 5 64 2600 126 21 Regrind Ball Mill 32 48 740 39 19 Tower Mill 25 25 520 12 42 IsaMill 13 3 1120 3 280 3 3) 23/m) Ball Mill Tower Mill IsaMill (m Power Intensity Media Size No Balls / m Surface Area Fine Grinding as Enabling Technology – The IsaMill2013年3月9日 Sintering is a thermal process (carried out at 1300 deg C to 1400 deg C) by which a mixture of iron ore, return fines, recycled products of the steel plant industry (such as mill scale, blast furnace dusts, etc), slag forming elements, fluxes and coke fines are agglomerated in a sinter plant with the purpose of manufacturing a sintered product The Sintering Process of Iron Ore Fines – IspatGuru
.jpg)
Operation Analysis of a SAG Mill under Different
2020年10月9日 This method simulates the particles size, mill power, and qualified particles quality of crushed particle, which reveal the grinding strength and energy consumption of the SAG millThe process of comminution is the crushing and grinding of a material / ore to reduce it to smaller or finer particles The comminution process reduces particle sizes by breaking, crushing, or grinding of ore, rock, coal, or other materials Comminution Multotec2011年1月31日 The influence of grinding conditions on the production of fine particles and the width of the particle size distribution produced during ball mill grinding was investigatedInfluence of dry and wet grinding conditions on fineness and 2021年9月5日 where dε is the infinitesimal specific energy (energy per unit mass) required to reduce by dx the size of a particle with size xC is a constant related to material type, and m is a constant indicating the order of the process This equation denotes that the specific energy consumption increases as the particle size decreases Particle size distribution (PSD) is Modeling of Bauxite Ore Wet Milling for the Improvement of
.jpg)
Simulating the Impact of Ore Competence Variability on Process
2019年9月24日 There are numerous examples in the literature, some of which are quantifying the effect of Mine to Mill Grundstrom et al, 2001;Hart et al, 2001;Scott et al, 2002;Burger et al, 2006;Jankovic et al 2022年1月23日 The crushing area may also include equipment for separation by particle size such as vibrating screens or rollerscreens; both having openings of a known size for proper size separation Preparing the RunofMine (ROM) bauxite for the grinding mill circuit must be completed in order to efficiently size the grinding mill circuitPhysical Bauxite Processing: Crushing and Grinding of Bauxite2023年7月10日 For particle breakage in the grinding mill, direct contact between the media and the particle should be maintained Aside from that, the media must apply sufficient stress intensity to the particle Because stirred mills have a higher media volumetric loading than tumbling mills, they use less energy, which results in higher stress intensity and stress number per unit EnergyEfficient Advanced Ultrafine Grinding of Particles Using 2019年4月1日 The aim of this study is to apply process mineralogy as a practical tool for further understanding and predicting the flotation kinetics of the copper sulfide minerals(PDF) Process mineralogy as a key factor affecting the flotation
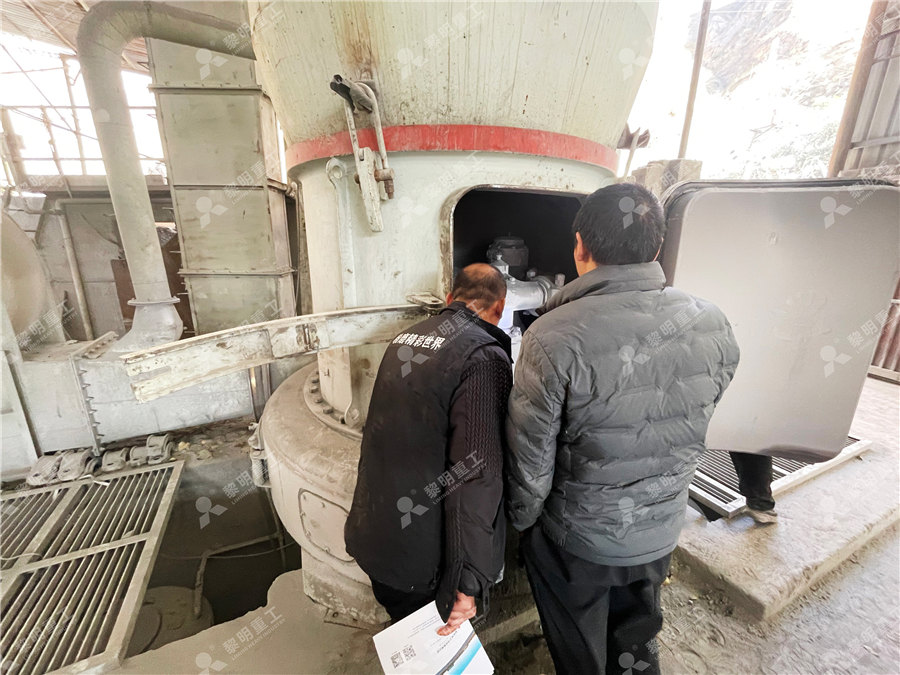
Flotation: The Past, Present and Future of Mineral Processing?
EMJ explores the sustainability of a timehonored beneficiation technique By Carly Leonida, European Editor As we look to the future, the mining industry faces a myriad of challenges While demand for metals like copper, cobalt, lithium and iron ore is projected to reach record highs by 2050, ore grades are decreasing, orebodies are becoming more complex, and fewer tier 1 2017年9月1日 Moreover, particle shape analysis of South African platinum group mineral ore called UG2 milled in a laboratory ball mill and stirred mill was conducted by using AutoSEMEDS [35]Fine grinding: How mill type affects particle shape ResearchGate2022年1月1日 The size of grinding media is the primary factor that affects the overall milling efficiency of a ball mill (eg power consumption and particle size breakage)Effect of grinding media on the milling efficiency of a ball millIn the mill, the mixture of medium, ore, and water, known as the mill charge, is intimately mixed, the medium comminuting the particles by any of the above methods Apart from laboratory testing, grinding in mineral processing is a continuous process, material being fed at a controlled rate into one end of the mill and discharging at the other end after a suitable dwell (residence) timeGrinding Mill an overview ScienceDirect Topics
.jpg)
Factors affecting the performance of crushing plant
2014年1月1日 Conference: Proceedings of the 23rd International Mining Congress and Exhibition of Turkey IMCET 2013; At: Kemer, Antalya, Turkey, April 1619, 2013, pp 293301underflow Obviously, a very large particle has a very small possibility of reporting to the overflow, but it does have a possibility, even if it is very low Since the feed stream contains millions of individual particles, if there is a possibility of a million to one, then one particle in a million (of that size) will “go the wrong way”Introduction to Cyclones AusIMMDefinition and Overview of Gold Ore Mill A gold ore mill is a facility where the raw mined goldbearing ore is crushed into fine particles through various mechanical means These particles are then further processed to extract the valuable metal within them Gold ore mills have evolved over time to improve efficiency and increase recovery ratesUnlocking the Secrets of Gold Ore Mill: A Comprehensive Guide2019年12月23日 Comminution is the action of reducing o f material (or ore) to smaller average particle sizes This process is utilized in the mining industry to liberate valuable mineral s from the worthlessDEVELOPMENT OF A HORIZONTAL SHAFT HAMMER MILL CHAPTER
.jpg)
Advances in screening technology in the mining sector
Fig 2 illustrates the interrelations for a screen classification process The circulating quantities are not only dependent on the screening efficiency, but also on the quantity of oversize produced by the mill At a screening efficiency of 100 % and 35 % oversize produced by the mill, the circulating load factor is already 154Download scientific diagram Particle size distributions of mill feed ( ) and discharge ( ) from publication: The physical basis of non random breakage in an ironoxide hosted copper gold ore Particle size distributions of mill feed ( ) and discharge ( )2003年11月1日 SkimAir flotation cells can also be fitted with dual outlets for the purpose of optimising mill efficiency and flash performance in combination (see Fig 1) The top discharge is of a lower pulp density (∼40–50% solids) compared to the bottom discharge (∼60–70% solids) and is sometimes bypassed to the mill dischargeThe interaction of flash flotation with closed circuit grinding2017年4月1日 Separation operation of verticalrollermill will be modelled by application of current models The model shall enable the prediction of the throughput, the particle size distributions around the verticalrollermill circuit, the specific energy consumption and in a later stage the wear to be expected in dependency of ore treatedOperational parameters affecting the vertical roller mill
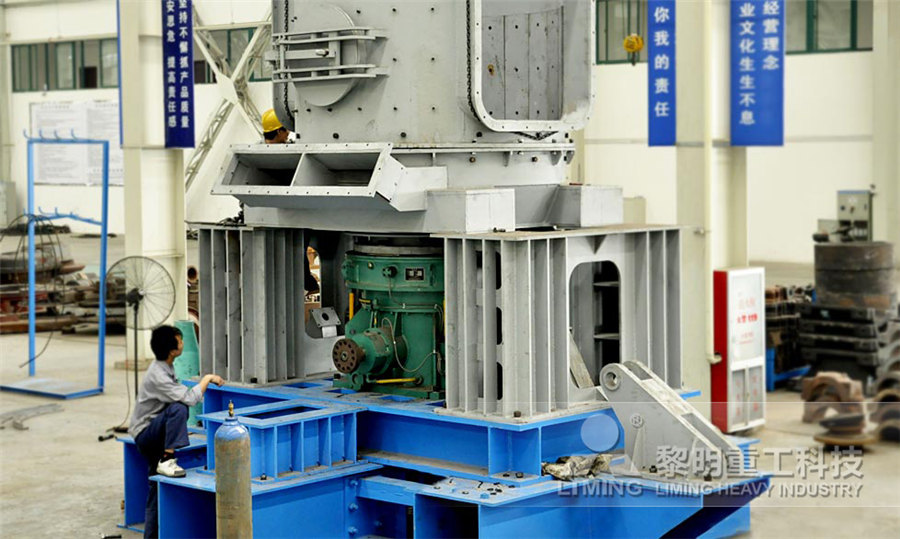
(PDF) Determining optimum wet milling and
2017年10月1日 The effect of particle size on the kinetics of gold cyanidation was investigated for a gold ore from the Abitibi region (Canada) Six size fractions representative of the plant operation were used 2013年7月15日 For any circuit, whether a crushing circuit, a rod mill, or a closed ball mill circuit, the Work Index always means the equivalent amount of energy to reduce one ton of the ore from a very large size to 100 um The sample was Bond Work Index FormulaEquation 911Metallurgist2017年10月16日 Sensorbased ore particle sorting can be used to preconcentrate ROM ore feed, SAG Mill scats and low grade or waste stockpiles Plant throughput increase, reduced operating costs and mine optimization Ore sorting the road to optimizing your operation2016年1月1日 "In the processing of UG2 platinum ore, stirred milling technologies are dominating regrind applications that require grinding the particles to P80s’ in the region of 45 µm For this application stirred mills are 30–40% more energy efficient and require a smaller foot print compared to traditional tumbling mills In this work a study was carried out using a batch pin Stirred Media Detritor Performance Assesment in the UG2 Platinum Ore
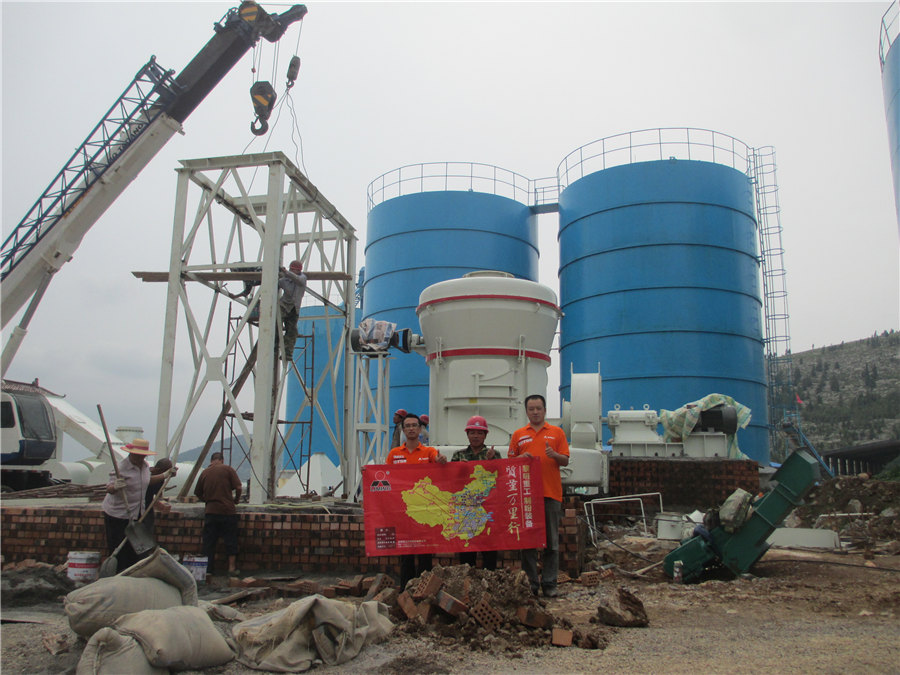
An Evaluation on the Impact of Ore Fragmented by
2022年2月17日 minerals1200258An Evaluation on the Impact of Ore Fragmented by Blasting on Mining Performancepdf2019年8月14日 • Central discharge ball mill: the inlet of medium unloading ball mill is at both ends, and the outlet is in the middle of the ball mill 4 According to the ore discharge of ball mill: • Overflow ball mill: Discharge the ore through hollow shaft • Grid ball mill: Discharge the ore through the plaid plateThe Ultimate Guide to Ball Mills Miningpedia2015年3月10日 Vertical roller mills (VRM) have been used extensively for comminuting both cement raw materials and minerals like limestone, clinker, phosphate, manganese, magnesite, feldspar and titanium These mills combine crushing, grinding, classification and drying operations in one unit and have advantages over conventional machines and literature reports that 15% Copper ore grinding in a mobile vertical roller mill pilot plant2017年8月24日 The purpose of screening is therefore splitting the feed Cone crushers work as tertiary crushers when installed in close circuit between the secondary unit and the ball mill to crush and overflow since its main goal is to decrease the ore particle to a level that allows effectively separation between gangue Mineral Processing SpringerLink
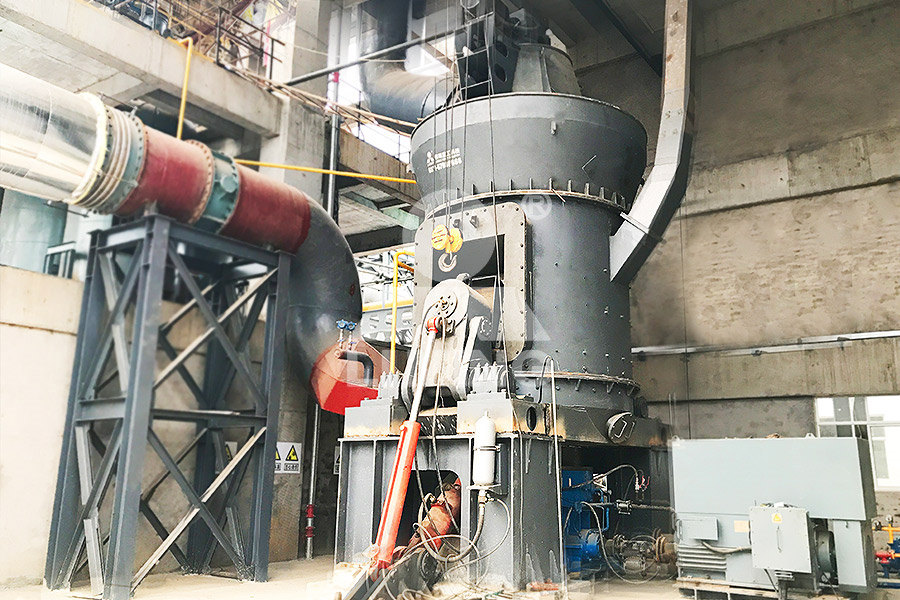
Particle Size Reduction in a Fluid Energy Mill Academia
The purpose of this paper was to develop models for the particle size distribution of the ground product in multidisc mills depending on the variable process parameters, For the type and mass of the ore used in this experiment, combined mill and classr, Fig 7 2022年1月1日 The population balance model (PBM) provides the fundamental sizemass balance equation for fully mixed batch grinding operations, and several studies highlighted its advantages for the design Effect of operating conditions on the particle size distribution and