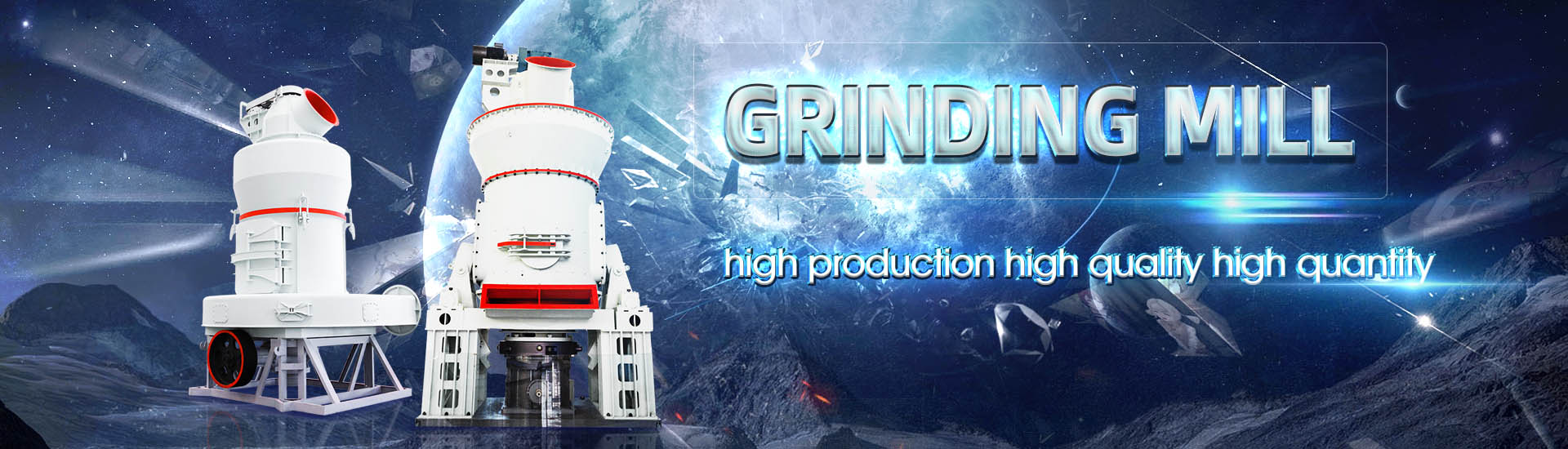
Electricity for grinding one ton of cement
.jpg)
A decision support tool for cement industry to select energy
2020年3月1日 On average, to produce one ton of cement, 34 GJ of thermal energy (in dry process) and 110 kWh of electrical energy are needed [4, 5] Furthermore, manufacturing a 2022年12月1日 The modern cement industry requires 110–120 kWh of electrical power to produce one ton of cement (Mejeoumov, 2007) Thermal energy is used mainly during the Review on energy conservation and emission reduction 2023年5月3日 Around 2% of the electrical energy produced globally is consumed during the grinding process in cement industry (IEA, 2019) For 1 ton of cement around 360 MJ of A comprehensive investigation of a grinding unit to reduce energy 2015年6月30日 On averagely, the production of a ton of cement utilizes thermal energy of 34GJ in the dry process, which in turn requires electrical energy of about 110 kWh [3, 13, 14] Energy consumption assessment in a cement production plant
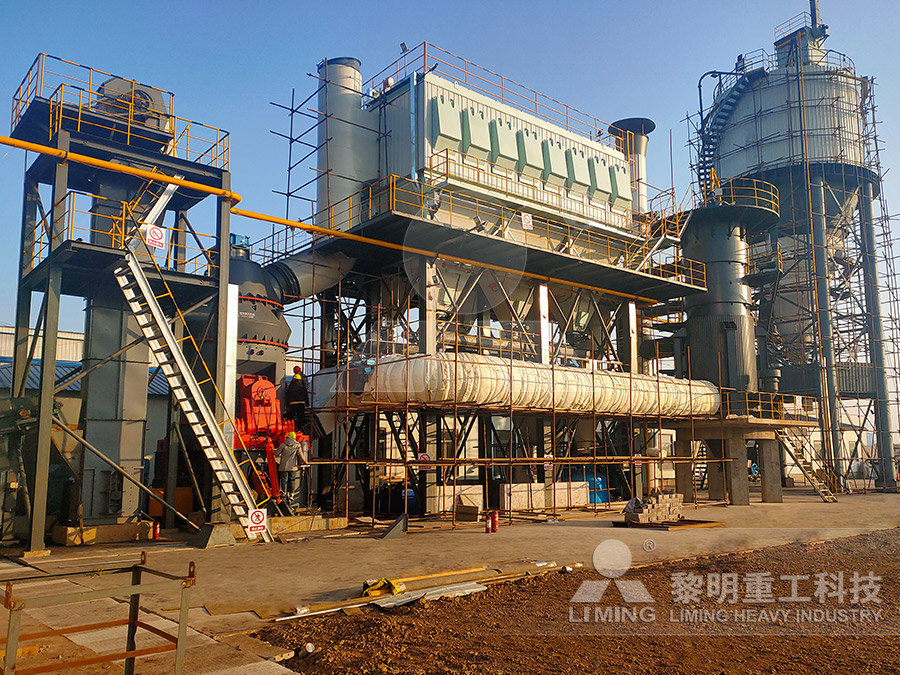
Modeling of energy consumption factors for an industrial cement
2022年5月9日 As one of the most energyintensive industries, cement plants consume around 100 kWh of electrical energy for each ton of their production This can be counted yearly as On the cement plant’s demand side, a flexible grinding approach could be used for raw meal production and cement manufacturing as powerintensive processes The management of silo POWERING THE CEMENT INDUSTRY CEMBUREAU2016年10月5日 Typical specific energy consumption is 30 kWh/t in grinding of cement Barmactype crushers found application as a pregrinder in cement grinding circuits operating with ball mills to reduce the specific energy EnergyEfficient Technologies in Cement GrindingTables 2 through 8 provide the following information for each technology: fuel and electricity savings per tonne of cement; annual operating and capital costs per tonne of cement or Energy Efficiency Improvement Opportunities for the Cement
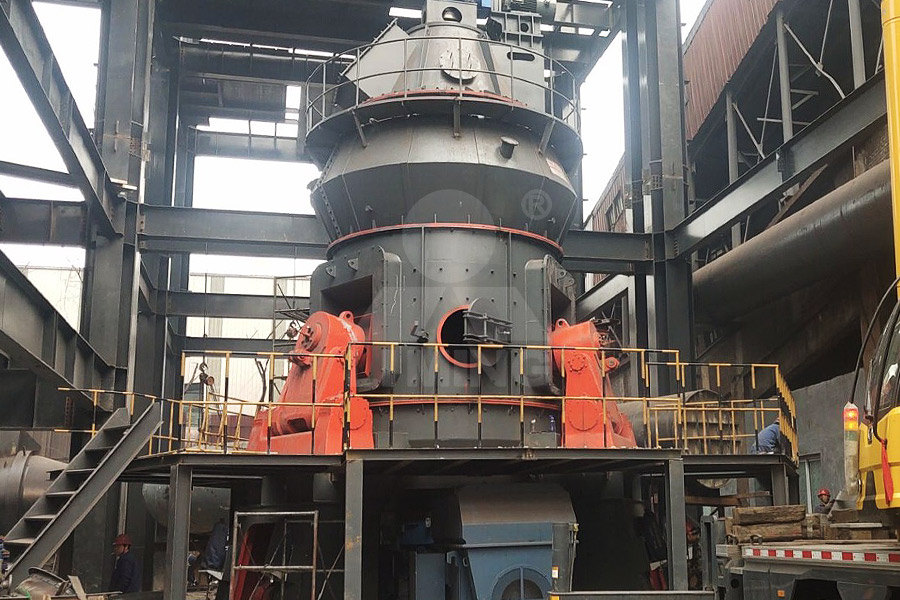
EnergyEfficient Technologies in Cement Grinding
2016年10月5日 In this chapter an introduction of widely applied energyefficient grinding technologies in cement grinding and description of the operating principles of the related equip‐ ments and comparisons over each other in 2022年11月17日 Moreover, the electricity per ton of cement by country in 2018, which was directly collected from the International Energy Agency 79, was used to further compare the energy consumption and Modernizing cement manufacturing in China leads to substantial 2024年1月9日 The cement production process emits approximately 09 tons of CO 2 per ton of cement (Hasanbeigi et al 2010), accounting for about 5–8% of global CO 2 emissions and ranking as the secondlargest CO 2 emissions source (Mikulčić et al 2016; Kajaste and Hurme 2016)According to the Intergovernmental Panel on Climate Change (IPCC) report, the cement Carbon emissions mitigation methods for cement industry2020年3月1日 Manufacturing cement requires energy intensive processes; and consumes almost 15% of the total demand for energy in industry [3]On average, to produce one ton of cement, 34 GJ of thermal energy (in dry process) and 110 kWh of electrical energy are needed [4, 5]Furthermore, manufacturing a ton of cement releases 073–099 tons of CO2 [6] which A decision support tool for cement industry to select energy
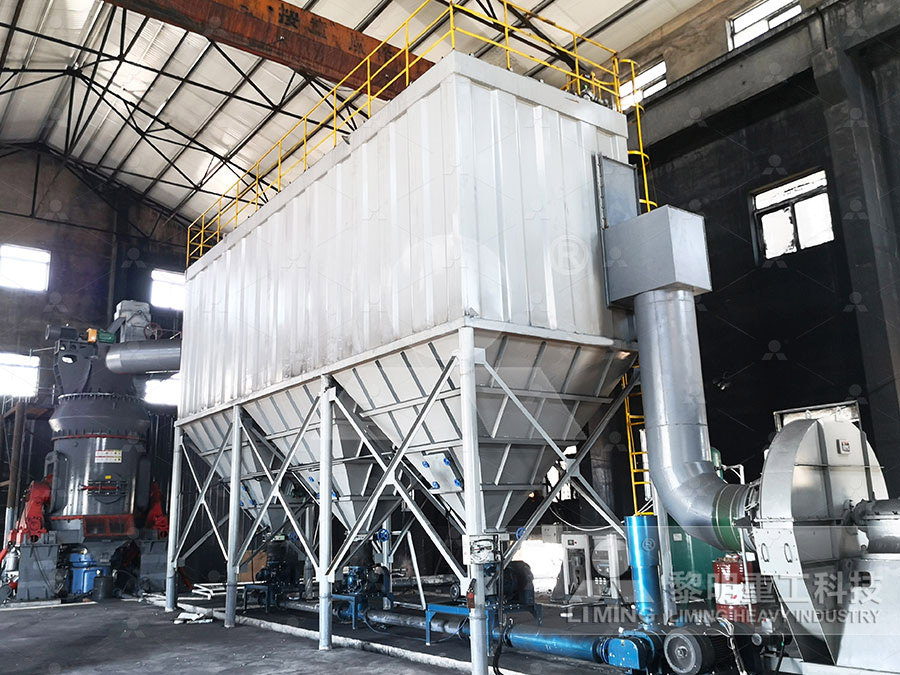
POWERING THE CEMENT INDUSTRY CEMBUREAU
CEMENT SECTOR POWERING THE CEMENT INDUSTRY Cement is an energyintensive industry, but currently, electricity accounts for circa 12% within the energy mix, while the rest is various fuels Total electricity consumption in a dry process is split into equal parts between raw material preparation and clinker production (25% each), then 43% for2021年11月15日 Production of one ton of Ordinary Portland Cement (OPC) results in nearly 700–900 kg of CO 2 equivalent emissions calculated the electricity use in a cement production process as 71 kWh/ton of PO cement and they indicated that electricity use in the grinding process varies with the grinding capacity of clinker, gypsum A review of the effectiveness of Life Cycle Assessment for gauging Improving Thermal and Electric Energy Efficiency at Cement Plants: International Best Practice iii LIST OF FIGURES Basic Layout of Cement Grinding Using Horomill ® 28 Figure 15: Energy Savings (41 billion tons in 2016) Cement accounts for at least 5 percent of anthropogenic emissions of greenhouse gases, IMPROVING THERMAL AND ELECTRIC ENERGY EFFICIENCY AT CEMENT 2023年11月1日 The production of cement is one of the largest CO 2emitting industries, accounting for approximately 8% of global CO 2 emissions (Andrew, 2017)Because the majority of these emissions arise from the decarbonation reaction of CaCO 3 and not from fuel combustion (ie, processrelated emissions), there is consensus that carbon capture and storage (CCS) Decarbonization of cement production by electrification
.jpg)
Cement Industrial Process: Modeling and Optimization of the
The typical electrical energy consumption of a modern cement plant is about 110–120 kWh per ton of cement [11] Grinding is the largest electricity consumer in the cement industry It’s up to 70% of the total electrical energy in the cement industry [12] Optimizing the grinding process is important to make finer cement products,2023年5月3日 Türkiye is the largest cement producer of Europe and the second biggest cement exporter in the world The industry is responsible for more than 8% of global carbon dioxide (CO2) emissions and around 15% of the primary energy consumed worldwide In this paper, the specific energy consumption (SEC) and related emissions of a real scale cement factory currently A comprehensive investigation of a grinding unit to reduce 2015年6月30日 One ton of cement produces approximately one ton of carbon dioxide, diesel as a fuel for transportation and electricity for crushing, grinding, and screening the CDW [36]Energy consumption assessment in a cement production plant2022年5月9日 Cement production is one of the most energyintensive manufacturing industries, and the milling circuit of cement plants consumes around 4% of a year's global electrical energy productionModeling of energy consumption factors for an industrial cement
.jpg)
Effect of ester modified triethanolamine on the grinding quality of
2024年9月13日 Among them, the electricity consumption of the cement clinker grinding process accounts for 60∼70 % of the total energy consumption of cement production, but only a very low energy utilization rate is truly used for efficient grinding of clinker, generally less than 15 %, and the rest of the energy is lost in the form of heat [3]2023年1月7日 The cement industry is undeniably critical for the global economy However, they are also the largest energy consumers in the world The clinker manufacturing process causes gaseous emissions like nitrogen oxides, sulfur dioxide, carbon dioxide and particulate matter There is scope for various technologies to be used in the cement manufacturing process for Emission reduction through process integration and exploration of 2019年11月18日 Cement is one of the most widely used materials in Grinding Electricity 34833 37557 36631 31809 37557 approximately 44 billion metric tons of ordinary Portland cement (OPC) Study of Energy Use and CO2 Emissions in the ResearchGateGiven 2002 production of 11,166,000 short tons of cement and 11,187,000 short tons of clinker in California, the technical potential electricity savings are about 360 GWh and fuel savings are about 78 TBtu, with a total technical potential savings for both fuels of about 20% over 2002 levels ENERGY EFFICIENCY OPPORTUNITIESTIPS TO SAVE ENERGY IN CEMENT MANUFACTURING PROCESS
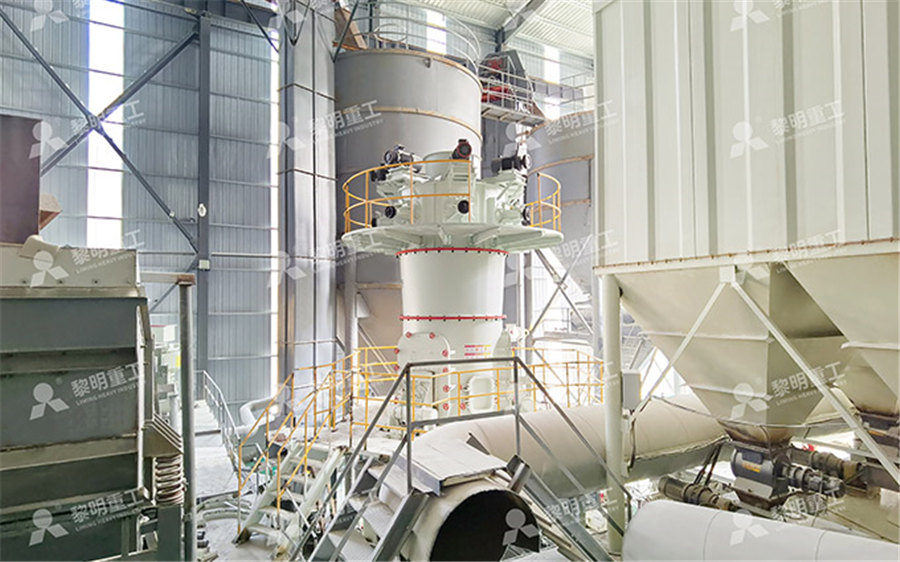
Study of Energy Use and CO Springer
2019年11月18日 Cement is one of the most widely used materials in construction This study presents a processwise evaluation of energy use and CO2 emissions for clinker, Ordinary Portland Cement (OPC) and Portland Pozzolana Cement (PPC) using the principles of lifecycle assessment Two cement plants located in India are considered as typical case studies The 2014年6月1日 China is both the largest producer of cement and the biggest emitter of CO 2 emissions in the world In 2010, the world׳s total cement production is about 33 Gt [5] and is expected to be 369–44 Gt by 2050 [1] Fig 2 shows the historical cement output from 1978 to 2010 It is observed that China has been the biggest cement producer in the world since 1985 Factorylevel measurements on CO2 emission factors of cement production Condition in one of the grinding chambers of the mill Results of Optimization The graphical analysis presented in Figure 2 represents progress of grinding along the length of the mill after optimizing the grinding process rogress of grinding is clearly visible in Desired p the graphs Figure 2: Analysis of longitudinal samplesOPTIMIZATION OF CEMENT GRINDING OPERATION IN BALL MILLS2013年7月15日 Cement industry has been always among the largest CO 2 emission sources Almost 5–7% of global CO 2 emissions are caused by cement plants, while 900 kg CO 2 is emitted to the atmosphere for producing one ton of cement In this work, global strategies and potentials toward mitigation of CO 2 emissions in cement plant have been discussed and the Global strategies and potentials to curb CO2 emissions in cement
.jpg)
EnergyEfficient Technologies in Cement Grinding
2016年10月5日 In this chapter an introduction of widely applied energyefficient grinding technologies in cement grinding and description of the operating principles of the related equip‐ ments and comparisons over each other in terms of grinding efficiency, specific energy consumption, production capacity and cement quality are given A case study per‐ formed on a Electricity Supply Ref Appendix C on page 96 for electrical details in single line diagram The power demand of the proposed plant is estimated at around 55 MW The Table 3f illustrates the power requirement for producing one tonne of EVERYTHING YOU NEED TO KNOW ABOUT cement plants operating in Egypt, 11 plants were analyzed These 11 plants have a share of 25% of the total energy consumption of the cement sector in Egypt, which is quite a representative sample During the data quality control one of the 11 plants was identified as an outlier The plant was contacted to verify the data but did not replyBenchmarking Report for the Cement Sector UNIDO2024年2月2日 Inputs encompass raw materials, electricity, and fuel, which provide the physical the cement manufacturing industry, one of the major foundation utilising VRM for cement grinding could potentially reduce the electrical energy consumption by 30% This will allow the company to surpass best practice energy use Benchmarking of Energy Consumption and CO2 Emissions in Cement
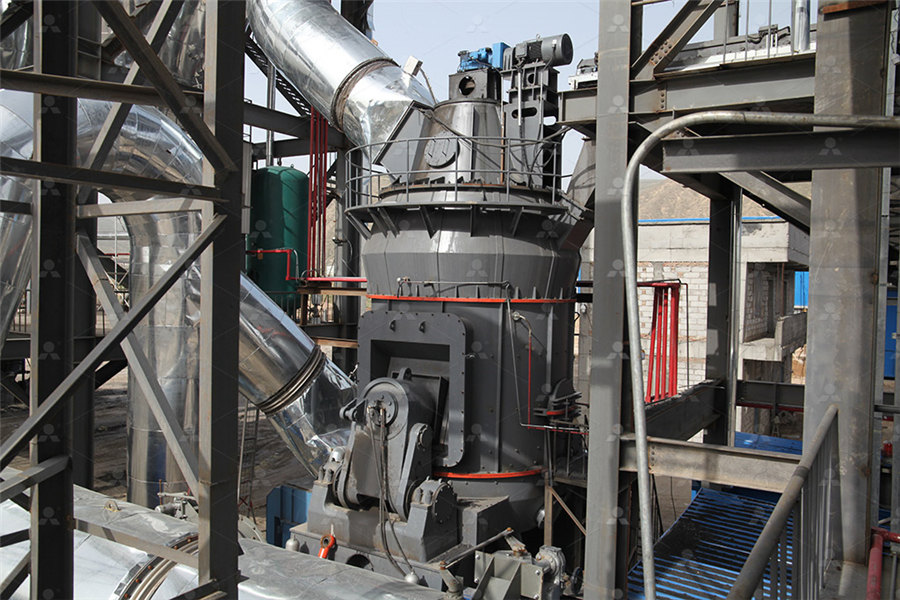
Coal for cement: Present and future trends
2016年3月1日 Next, in November 2014, Titan Cement ordered a Gebr Pfeiffer SE type MPS 2800 BK vertical roller mill for coal grinding, to be set up at line 1 at its Beni Suef plant In January 2015, Suez Cement, Italcementi’s Egyptian arm, said that it would spend US$84m during the year to convert its Helwan and Tourah 2 cement plants to use coal2023年1月1日 This chapter seeks to explore the relevance of coal in the production of cement, arguably one of the basic materials older cement production facilities can result in CO 2 emissions of about 1000 kg CO 2 per ton cement are also being investigated to reduce the specific electricity consumption of grinding mills and/or improve Coal utilization in the cement and concrete industries2020年6月24日 The configuration of the existing cement production unit of Emami Cement Limited, Baloda Bazaar, Chhattisgarh was used for this study, having a clinker production of about 32,00,000 tons per year and 30,00,000 tons per year for cement This investigation aimed at the utilization of waste heat through the concept of energy conservationThermal energy consumption and its conservation for a cement CEMENT SECTOR POWERING THE CEMENT INDUSTRY Cement is an energyintensive industry, but currently, electricity accounts for circa 12% within the energy mix, while the rest is various fuels Total electricity consumption in a dry process is split into equal parts between raw material preparation and clinker production (25% each), then 43% forPOWERING THE CEMENT INDUSTRY CEMBUREAU
.jpg)
Everything you need to know about Energy Efficiency Improvements
The electricity savings of a new finish grinding mill when replacing a ball mill is estimated at 30 kilowatthour/metric ton cement High efficiency classifiers A recent development in efficient grinding technologies is the use of highefficiency classifiers or separatorsCement is one of the most widely varies from 35 to 45 GJ/ton of cement and the electric energy varies from 92 to 141 kWh the clinker and electricity used for grinding and CO 2 emission for clinker, OPC and PPC ResearchGateIn cement industry about 110 kWh of electrical energy is consumed to produce one ton of cement and about 26% of the total electrical power is used during farine productionThe use of electrical energy in cement production2021年7月28日 Figure details the electrical energy demand of the cement process as about 2% for raw material extraction, 25% for raw material preparation, 25% for clinker production plus an additional 3% for fuel grinding, Indian Cement Sector CMA
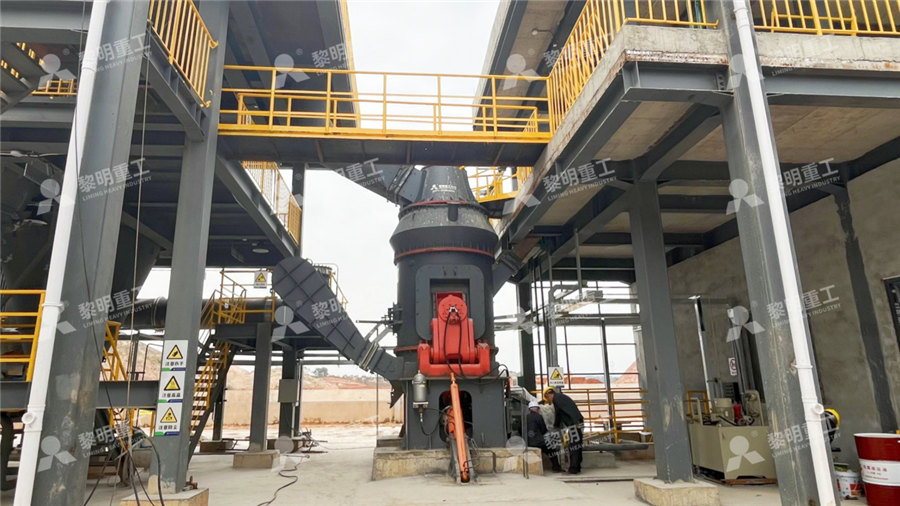
Is Coal Needed for Cement Production? A
2024年8月31日 Historical Use of Coal in Cement Production 1 The Role of Coal in Traditional Cement Kilns Historically, coal has been a primary energy source for cement production Cement kilns, which are used to heat raw materials to 2014年5月1日 Cement production in the world is about 36 billion ton per year [4] About 2% of the electricity produced in the whole world is used during the grinding process of raw materials [5] Total electrical energy consumption for cement production is about 110 kWh/t of cement, roughly two thirds of this energy is used for particle size reduction [6]Analysis of the parameters affecting energy consumption of a rotary 2020年10月1日 Depending on the technology used, extraction uses between 12 and 15 kWh per ton of mineral extracted, and crushing steps consume around 20–25 kWh per ton of raw materials and 50 to 60 kWh per ton of cement Overall, each ton of cement produced can use up 80 to 100 kWh of electrical energy (029–036 GJ)The impact of future power generation on cement demand: An Cement Grinding Ball Mill Motors”, Ghana Journal of Technology, Vol 6, No 1, pp 917 Abstract Ball mills as used in mining, cement production and allied industries consume about 40% to 56% of the total electric power supplied to the processing plant Electric power losses in ball mill operations constitute about 25% of the available power The Effects of Temperature, Vibration and Dosage on the
.jpg)
Technological Energy Efficiency Improvements in Cement Industries
2021年3月30日 A typical wellequipped plant consumes about 4 GJ of energy to produce one ton of cement, while the cement production in the world is about 36 billion tons per year It was estimated that the cement manufacturing process consumes around 7% of industrial energy consumption, which, in turn, accounts for 30–40% of the global energy consumption [ 3 ]in industries Cement industry is one of the major energy consuming industries and the optimum use of energy is at present important for our national economy The energy cost is the highest component of cost structure of cement manufacture Energy cost in Indian cement industry account for over 40 to 50 percent of the manufacturing cost of the Optimizing Electrical Energy Consumption In Cement Process 2024年9月13日 Cement is produced worldwide at an astonishing rate of about 150 t/s and is an indispensable material for social and technological development [1]Studies [2] show that for every ton of cement clinker produced, approximately one ton of CO 2 is emitted, which is actually far higher than the theoretical decarbonization content of limestoneEffect of ester modified triethanolamine on the grinding quality of 2022年5月26日 Recycled cement production The RC production process analyzed in this research corresponds to the patented method developed at IST (Bogas et al 2020) described in Sousa and Bogas ()The method is based on the magnetic separation of the cement paste from the aggregates and, resuming briefly, it comprises three stages as depicted in Fig 1: (i) Industrial production of recycled cement: energy consumption
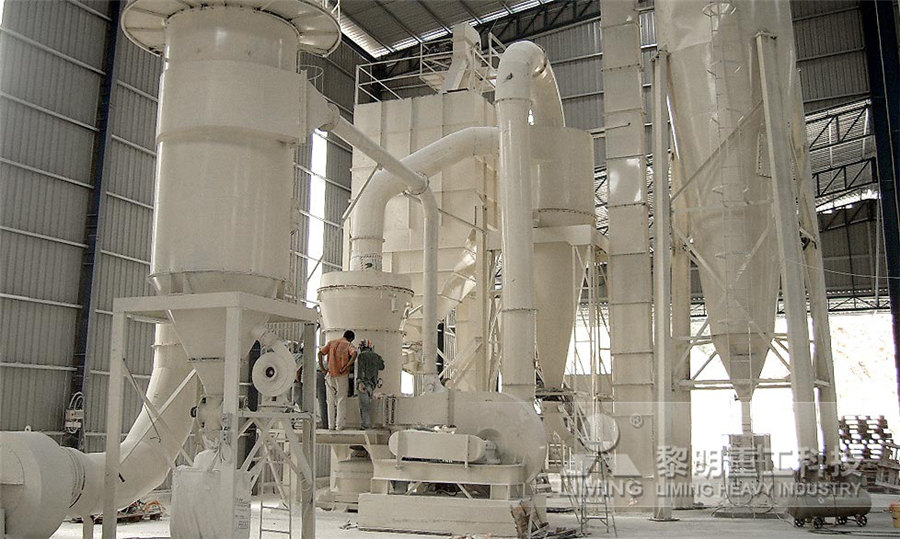
Everything you need to know about clinker/cement Grinding
Normally, grinding aids are added in a 15% concentrated solution (1:7 grinding aid to water – helps the dispersal of grinding aid in mill), at approximately 225 Lb/Ton for medium fineness and 34 Lb/Ton for high fineness cement