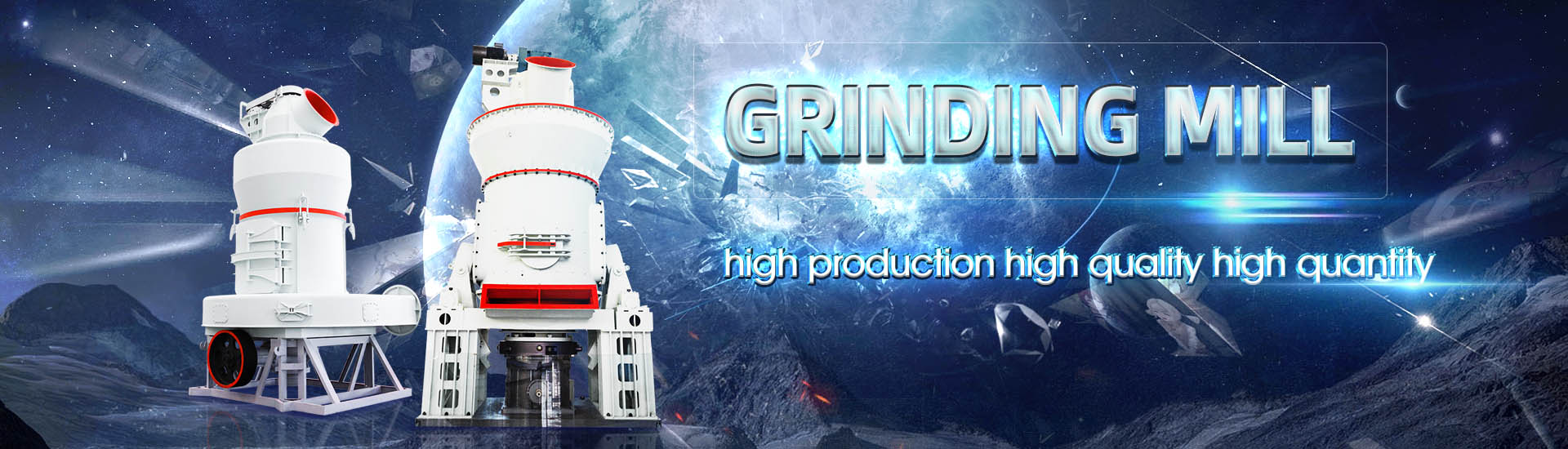
How to measure the fineness of the mill in the ore powder processing plant
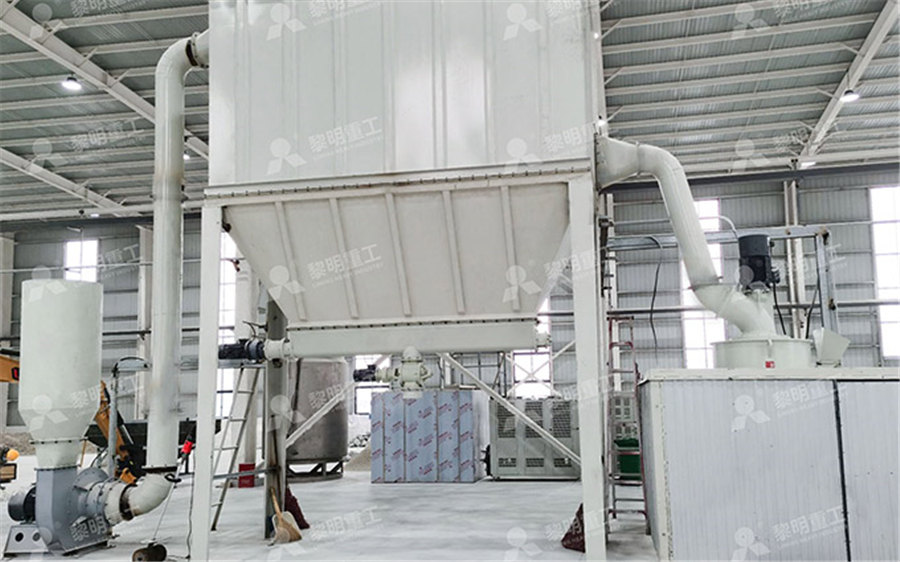
Measurement of Ore Grinding Fineness ZJH minerals
Fineness is the operating index of the grinding and classification process of the ball mill, and the fineness of the discharge and classifier overflow and coarse sand return should be measured frequently in the ore dressing plant or froth flotation plant in order to adjust the operation in timeIn the fines region, the plot should always be linear The slope of the plot gives the exponent a; KE is the intercept at x = 1 Any drooping in the upper region indicates that the balls are too A quick test procedure for the determination of milling parameters2010年4月1日 Apart from the milling of ores, milling is also used for preparing materials for some industrial applications, such as milling of quartz to fine powder (under 70 μm in diameter), Powder Milling an overview ScienceDirect Topics2017年9月1日 This paper aims to explore these observations further, focusing on the two fine grinding devices and the breakage mechanisms therein, size by size shape characteristics Fine grinding: How mill type affects particle shape characteristics
.jpg)
Optimization of mill performance by using online ball and pulp
2010年3月10日 To reach this key objective, continuous and reliable information about the mill operation is vital An innovative tool which can deliver information about inmill dynamics has sample preparation The "Art of Milling" describes the process of turning a laboratory sample into a representative part sample with homogeneous analytical fineness For this task RETSCH The Art of Milling Metrohm2017年9月1日 The objective of this work is to assess the influence of fine grinding in ball mills and stirred mills on valuable mineral liberation and particle shape characteristics of UG2 ore, a Fine grinding: How mill type affects particle shape characteristics media mill ATR operated in a closed loop with ATP/NG multiwheel air classifiers are ideal for this application Recommended for fineness levels below D 97 = 50 µm down to D 98 = 20 µm THE PURSUIT OF PERFECTION IN POWDER PROCESSING
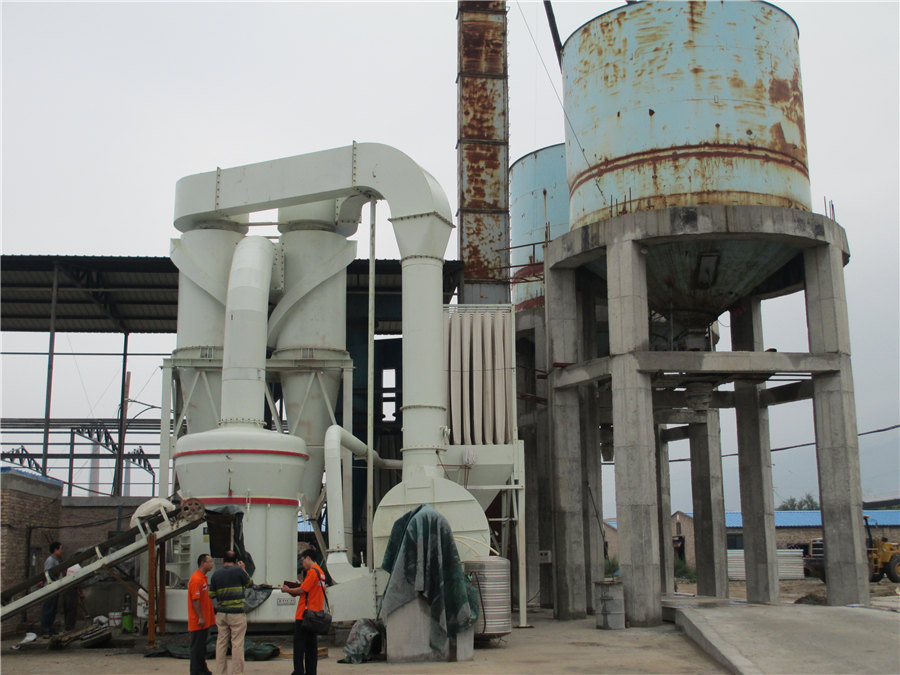
Estimation of Grinding Time for Desired Particle Size Distribution
2020年1月3日 There are many tests for determining grindability The most commonly used test is the Bond ball mill (BBM) It enables the installation of a plant scale ball mill [5] The Bond 2023年7月20日 Grinding operation quality indices mainly include four aspects (1) Grinding fineness, which is the percentage of the ore particles less than pecified size after being Ore Grinding SpringerLink2021年6月29日 Nowadays, ball mills are widely used in cement plants to grind clinker and gypsum to produce cement The research focuses on the mill speed as well as air classifier speed effect on the two Effects of Mill Speed and Air Classifier Speed on 2016年3月21日 Pulp Densities Pulp densities indicate by means of a tabulation the percentages of solids (or liquidtosolid ratio) in a sample of pulp This figure is valuable in two ways—directly, because for each unit process and operation in Common Basic Formulas for Mineral Processing
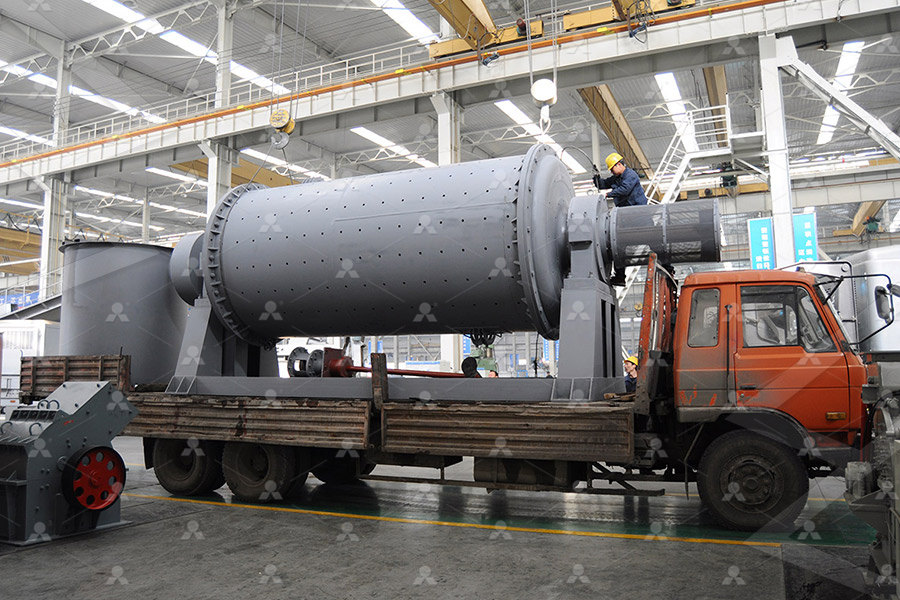
Simulating the Impact of Ore Competence Variability
2019年9月24日 The Extended Drop Weight Test (ExDWT) improves understanding concerning sources of variation in ore competence through the value chain This technique measures and describes the variability in ore Media Attributions; Metal deposits are mined in a variety of different ways depending on their depth, shape, size and grade Relatively large deposits that are quite close to surface and somewhat regular in shape are mined using openpit mine methods (Figure 815 in Section 81)Creating a giant hole in the ground is generally cheaper than making an underground 82: Mining and Ore Processing Geosciences LibreTexts2015年4月7日 Grinding balls in the operation of crushing in Ball mill, the ore milling quality and fineness directly related to the purity of the mineral aggregate When the plant capacity with changes is in the grade of ore dressing, the great relationship with the nature of the ore and the means can improve concentrate gradeImprove the Fineness of the Mineral Aggregate in the Ball Mill 2024年10月28日 The ball mill is a common grinding equipment in mineral processing in mines The fineness of the ball mill directly affects the pass rate of the product, so it is very important to master the method of adjusting the finenessThis article will introduce you to several common methods for adjusting the fineness of ball millsHow to adjust the fineness of the mine ball mill
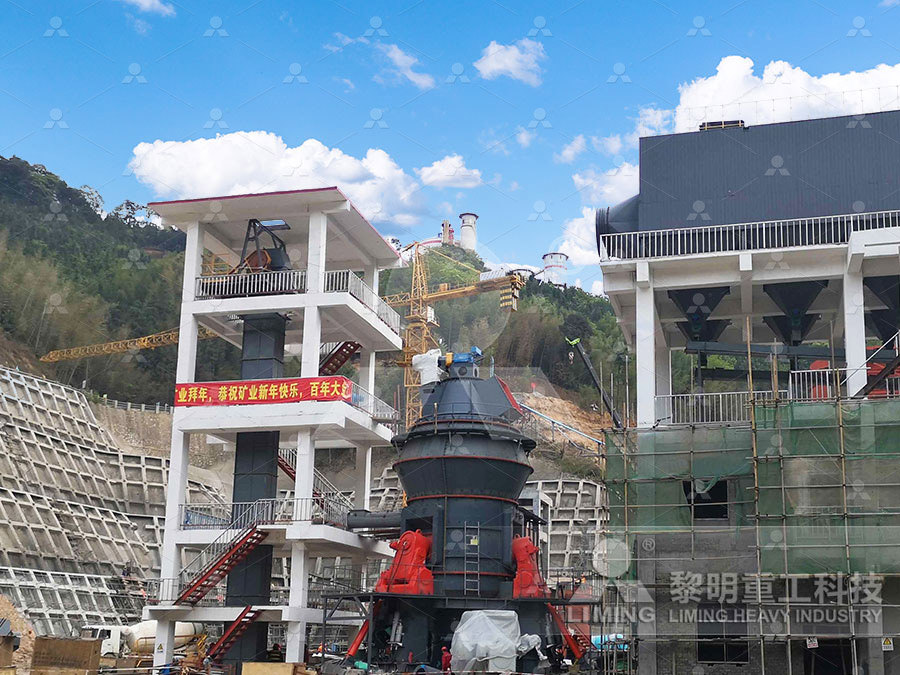
How to choose a suitable ore powder grinding mill?
2023年10月17日 Ultrafine powder mill (threering / fourring mediumspeed micropowder mill) feed particle size ≤25 mm, production capacity 0545 t/h, production fineness 1503500 mesh,it is a highefficiency and lowconsumption ultrafine powder processing equipment that successfully replaces the traditional jet mill and complex process ball mill grinding and powder selection, 2022年1月1日 The size of grinding media is the primary factor that affects the overall milling efficiency of a ball mill (eg power consumption and particle size breakage)Effect of grinding media on the milling efficiency of a ball mill2012年6月1日 The feed material is typically composed of the BFRs and the catalyst, both in powder form As the cylinder starts to rotate, the grinding balls inside the cylinder crush and grind the feed Grinding in Ball Mills: Modeling and Process Control2018年6月1日 A number of researchers (Deniz, 2012; Bwalya et al, 2014; Petrakis et al, 2016) carried out studies about the effect of feed particle size and grinding media size on the grinding kinetics of different oresKhumalo et al, 2006 postulated that generally larger sized grinding media would break larger particles quicker but a finer product would be obtained by use of Effect of ball and feed particle size distribution on the milling
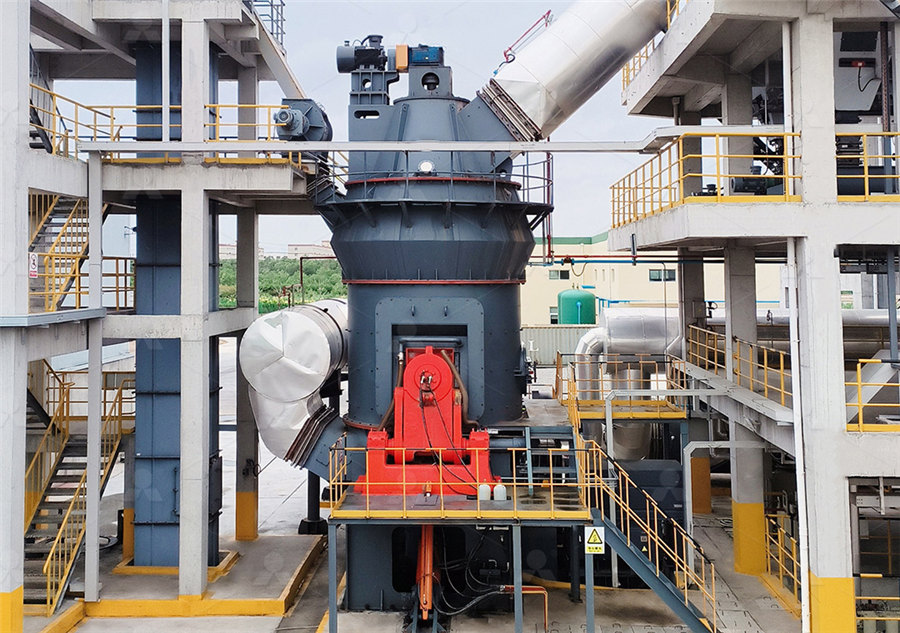
Pulverizer Fineness and Capacity Enhancements at Danskammer
RPM is programmed to follow mill coal flow to obtain a desired fineness vs mill load rela tionship; manual override with manual control of classifier speed from the control room is also provided; instrumentation for monitoring drive assembly oil bath temperature and oil2021年1月1日 India is the world's second largest producer of cement and produces more than 8 per cent of global capacity Due to the rapidly growing demand in various sectors such as defense, housing, commercial and industrial construction, government initiative such as smart cities PMAY, cement production in India is expected to touch 550–600 million tones per Review on vertical roller mill in cement industry its performance 2023年5月27日 The bentonite raw material stays in the mill for only 23 minutes, which can quickly measure and correct the chemical composition and fineness of the finished powder to ensure the quality of the finished product Raymond How to Dry, Grind and Granulate Your Bentonite Clay?2017年8月1日 In a coalfired power plant, one of the main equipment is the coal mill, whose effectiveness influences mainly the whole power plant performance (Shah, Vuthaluru, and Vuthaluru 2009) Optimisation of coal fineness in pulverisedfuel boilers
.jpg)
Understanding the effects of liner wear on SAG mill performance
2015年9月7日 It is also crucial that the user has knowledge about the process, and potential changes in the plant that can cause process drift For example, liner wear can greatly affect SAG mill performance 2013年3月1日 This is referred to as the classifier cut size Generally, the plant operator can control the classifier cut size, and thus the comminuted product fineness by adjusting the classifier rotor speed Cements ground in the vertical roller mill fulfil the quality Analytical fineness The required analytical fineness of the sample material depends on the analytical method or further processing and can vary greatly Most methods require a fineness in the size range from 20 µm to 2 mm As product properties (eg extraction, filtration or absorption capacity) are often influenced by the parThe Art of Milling Metrohm2019年11月13日 The rapid construction activity in Malaysia has increased the demand of concrete One of the key ingredients in concrete is cement The production of cement emits carbon dioxide (CO 2 ) which is (PDF) The influence of cement fineness on the structural
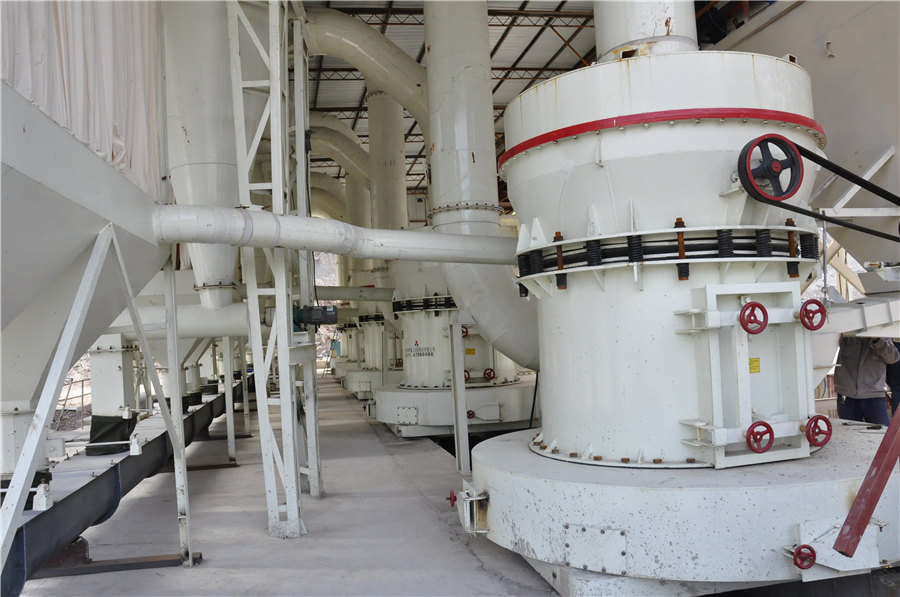
Solids and powder milling Size reduction
1 Principles of milling bulk solids Milling is the action of reducing the size of particles thanks to a mechanical action The mechanical action is submitting the particles to a stress, under the stress, some cracks will appear and subsequently the particle will be broken in different parts2019年4月22日 There are a lot of problems that most mineral processing plant meet when operating the ball mill, such as low grinding efficiency, low processing capacity, high energy consumption, unstable Ten Ways to Improve the Grinding Efficiency of Your Ball Millmineral processing, art of treating crude ores and mineral products in order to separate the valuable minerals from the waste rock, or gangue It is the first process that most ores undergo after mining in order to provide a more Mineral processing Metallurgy, Crushing Grinding 2015年8月3日 Crushing is the first step of mineral processing where the ore/rocks from the mine site is fed into the mechanical equipment in order to reduce as the efficiency decreases rapidly with fineness(PDF) Overview of Mineral Processing Methods
.jpg)
Quantifying Dry Milling in Pharmaceutical Processing:
2014年9月21日 The choice of these methods (dry/wet) depends on the end use of the product 2 One of the most important applications of particle size reduction is improving the dissolution rate of Biopharmaceutics Classification System II Shape of particles made by grinding is one of the important measures for determining the utilizations of industrial minerals namely barite, calcite, and talc particles, particularly at production Examples of movement of the media inside a ball mill 2023年10月27日 The ball mill is a rotating cylindrical vessel with grinding media inside, which is responsible for breaking the ore particles Grinding media play an important role in the comminution of mineral ores in these mills This work reviews the application of balls in mineral processing as a function of the materials used to manufacture them and the mass loss, as A Review of the Grinding Media in Ball Mills for Mineral Processing 2020年1月16日 Buzwagi Gold Mine (BGM) is operated by Acacia Mining and located in the Lake Victoria Goldfields of central Tanzania The mine commenced its operation since April 2009 and treats a sulphide copper (PDF) Optimization and performance of grinding circuits: the
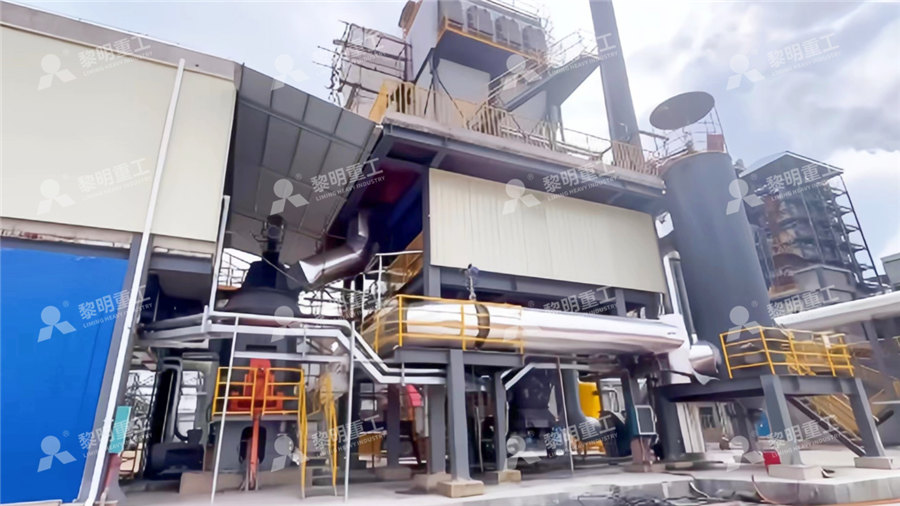
SIZE REDUCTION BY GRINDING METHODS ResearchGate
2017年3月4日 Ball mills are used for wet grinding iron ore, g old/copper ore, nickel ore and other ores, as wel l as lime/limestone for flue gas desulphurisat ion systems, coal and other raw materials Rod mill :2024年4月26日 Crushing is the initial stage in the iron ore processing journey, where large chunks of ore are broken down into smaller fragments The primary objective of crushing is to reduce the ore size for subsequent processing and improve the liberation of valuable minerals from the gangue a Jaw Crushers: Jaw crushers are commonly used for primary Iron Ore Processing: From Extraction to Manufacturing2022年3月21日 Geology, deposit types, and ore minerals There are more than 200 minerals that contain REE 7,8 The most common rareearth minerals are monazite and bastnäsite (Figure 1a–b and Table II)Monazite exists as a group of arsenates, phosphates, and silicates, but the primary REEbearing monazite is a complex phosphate 5 Bastnäsite, also known as Processing the ores of rareearth elements MRS Bulletin2023年6月18日 The fineness of any sieve or screen depends upon the width of the wire used The wire used in 10 mesh sieve will be thicker than the wire used in 60 mesh sieve A thick wire can't make a fine sieve and a thin wire can't make a thick sieve Fine sieves above 400 mesh, the particle size is described in micronsDifferent Mesh Sizes and Mesh to Micron Conversion
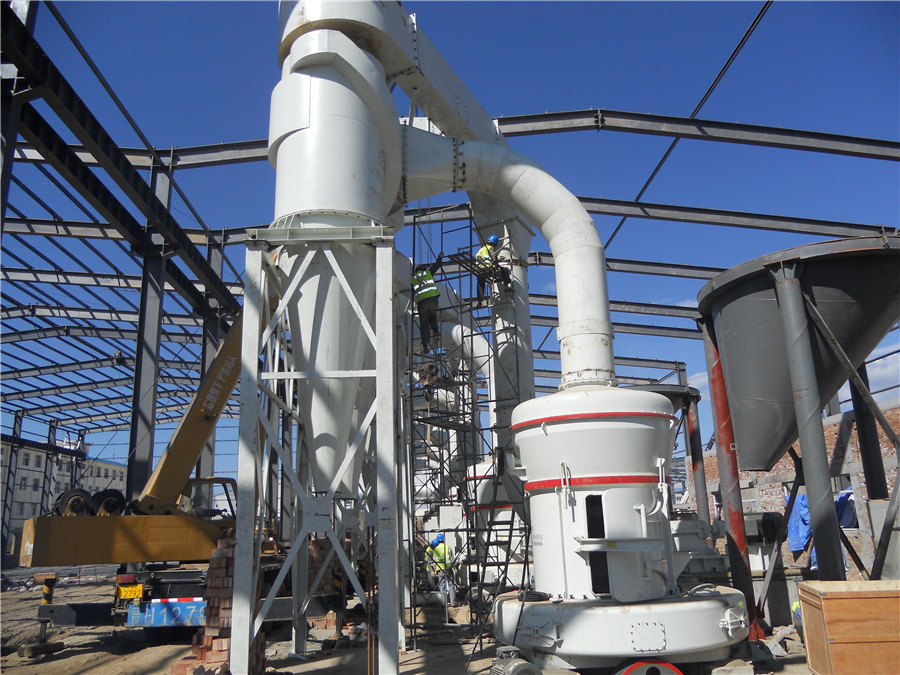
New Developments in Single Fiber Fineness and Maturity
the average maturity and fineness of a laydown of cotton but also the distribution of fineness and maturity throughout the spinning process Introduction Cotton fiber fineness can be defined in various ways Lord (1) lists five measures that may be used: perimeter, diameter, area of cross section, mass per unit length, and specific fiber surface2020年12月3日 In Eq (), dE is the specific energy for grinding (kwh/t), k is the grinding constant, and dx/x n is the variations of particle size during grindingThe main missing factor in most comminution A process mineralogy approach to study the efficiency of 2021年7月12日 Over the years, alternative procedures to the Bond grindability test have been proposed aiming to avoid the need for the standard mill or to reduce and simplify the grinding procedure Some of them use the standard A Review of Alternative Procedures to the Bond Ball 2017年8月18日 To measure the dispersion (or measure the particle size) of a material, a fineness of grind gauge, also known as a grindometer, is usedCONTENTS0:49 ElcometeHow to measure dispersion using Elcometer Fineness of Grind
.jpg)
EnergyEfficient Technologies in Cement Grinding IntechOpen
2015年10月23日 In this chapter an introduction of widely applied energyefficient grinding technologies in cement grinding and description of the operating principles of the related equipments and comparisons over each other in terms of grinding efficiency, specific energy consumption, production capacity and cement quality are given A case study performed on a 2018年10月1日 The standard JK impact breakage testing method has been extended to measure ore breakage variability may be the normal situation for processing an ore WJ, 1983 Breakage characteristics of ores for ball mill modelling In: Proceedings AusIMM, vol 286, June, pp 31–39 Google Scholar Pauw and Maré, 1988Quantifying variability of ore breakage by impact ScienceDirect2016年8月1日 The following paper presents and analyses methods of monitoring the key performance factors of a vertical spindle mill that is suited for implementation on older power stations, ie the quantity Mass flow and particle size monitoring of pulverised fuel vertical When iron ore is extracted from a mine, it must undergo several processing stages Six steps to process iron ore 1 Screening We recommend that you begin by screening the iron ore to separate fine particles below the crusher’s CSS before the crushing stageThe six main steps of iron ore processing Multotec
.jpg)
What is the role of a mill in a coalfired power plant?
2023年11月30日 In a coalfired power plant, a mill or pulverizer plays a crucial role in the process of converting raw coal into a form that can be burned efficiently and used to generate electricitythe mill settings, eg hopper load, mill speed and separator adjustment Therefore, a cost effective operation of the mill requires well defined grinding quality and particle size limits Simple as this task sounds, it is difficult to realize in practice due to the above mentioned variabilityPowerGen 2008, Orlando, USA Online measurement of coal fineness