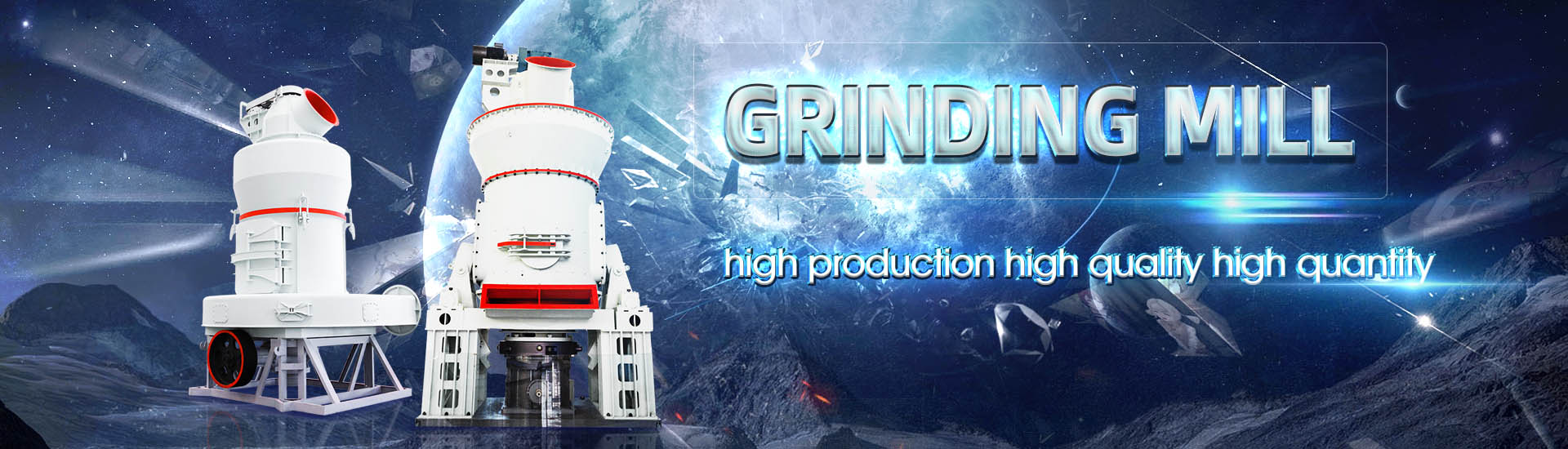
Slag cement production line process flow
.jpg)
Steel Slag—Its Production, Processing, Characteristics, and
2004年5月14日 Steel slag is a byproduct from either the conversion of iron to steel in a basic oxygen furnace, or the melting of scrap to make steel in an electric arc furnace This paper GBFS is slag from the iron production in Basic Oxygen Furnaces When this slag is actively cooled and ground, GBFS is produced, which can be utilised as a cement or concrete addition Fly ash and Blast Furnace Slag for Cement Manufacturing GOVUK2022年2月20日 Steel slag multiphased clinker technology provides an ecofriendly process to produce lowcarbon cement clinker by batching in granular steel slag without milling and extra Investigation on industrial trial production of multiphased clinker In this presentation, we review existing methods for phase identification, stoichiometry quantification, and microstructure quantification in cementitious materials and related materials We firstBlockflow diagram of primary and secondary steel

233R17: Guide to the Use of Slag Cement in Concrete and Mortar
This report addresses the use of slag cement as a separate cementitious material added along with portland cement in the production of concrete This report does not address slags derived 2023年8月25日 Utilizing treated steel slag as coarse/fine aggregate in concrete production is a highvalue solution that can alleviate the worry about resource depletion and solve the negative impact of steel slag stockpiling in slag Application of Steel Slag as an Aggregate in Concrete 4 天之前 AbstractDeveloping novel composite cement with processed ladle furnace slag Bostanci, S C 2020 “Use of waste marble dust and recycled glass for sustainable concrete Development of Newer Composite Cement with Processed Ladle 2024年11月24日 21 Mineralogical Properties of Steel Slag Steel slag's primary chemical components are CaO, SiO 2, Fe 2 O 3, Al 2 O 3, MgO, MnO, FeO, and severalSteel slag A Succinct Review on Use of Steel Slag in Mortars and Concrete
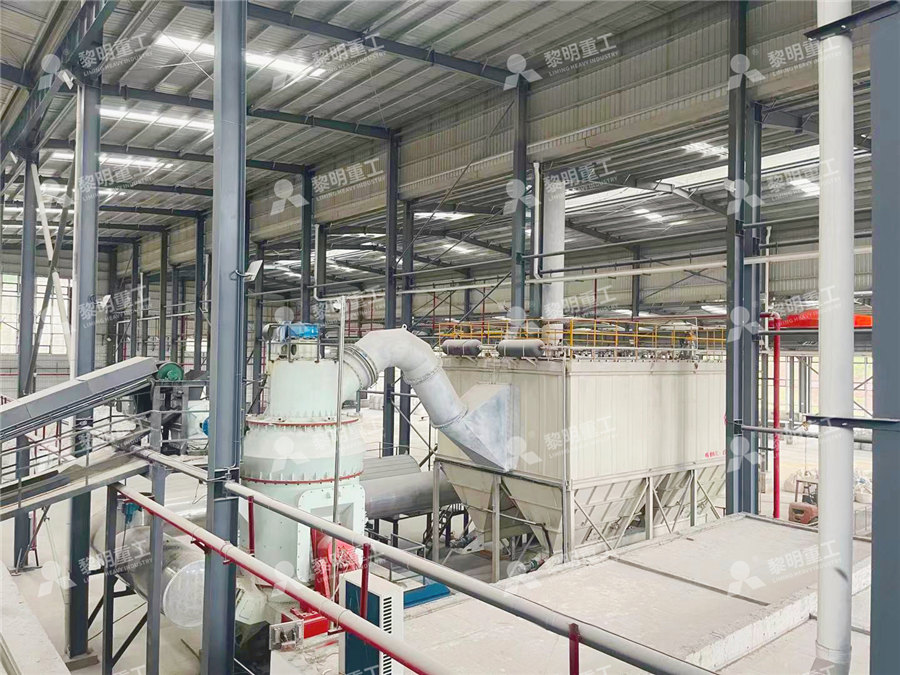
Phase evolution and performance of sodium sulfateactivated slag
This study evaluates the reaction kinetics, phase assemblage, and microstructure evolution of Na 2 SO 4activated slag cements produced with three commercial slagsAGICO is a leading cement industry equipment supplier based in China It can not only supply all kinds of slag powder grinding equipment including ball mill, vertical roller mill, and roller press, but also provide you with a complete turnkey GGBS Production Line Slag Mill for Slag Powder Stage of Cement Manufacture There are six main stages of the cement manufacturing process Stage 1: Raw Material Extraction/Quarry The raw cement ingredients needed for cement production are limestone (calcium), sand and clay (silicon, aluminum, iron), shale, fly ash, mill scale, and bauxite The ore rocks are quarried and crushed into smaller pieces of about 6 inchesHow Cement is Made Cement Manufacturing Process2023年10月19日 Cement production line from the web Process flow of ultrafine slag grinding The process scope of the ultrafine composite mineral admixture grinding system includes the following steps: What is a ultrafine slag grinding plant? ultrafine slag
.jpg)
Projecting future carbon emissions from cement production in
2023年12月11日 Global cement emission patterns Global emissions from cement production reached 2059 Mt CO 2 in 2018, where energy and processrelated emissions account for 34% and 66% respectively Developed 2016年1月20日 In each unit's material flow structure, the flow rate and flow direction are varied In the production process, material consumption needs to be investigated at every point, and a large number of measurements are taken To analyze the material flow of a cement production line, the material flow model of each unit should be establishedAnalysis of material flow and consumption in cement production process 2022年9月21日 Global cement production has reached 39 billion tons However, the clinkerization process, which is the basis of cement production, is responsible for an approximate annual global CO2 emission of Cement and Clinker Production by Indirect Mechanosynthesis ProcessThe cyclone preheating system Phase IV: Calcination The calcination is the core phase of the cement making dry process The calcination of the preheated raw meal takes place in the rotary kiln of the cement plant The rotary kiln is a huge rotating furnace in which the raw meal is heated up to 1450 ⁰C and turned to clinkerHow Is Cement Produced in Cement Plants Cement Making Process
.jpg)
Steel slag recycling crushing and grinding production line
Process flow diagram (wet process): Wet process: The dryprocess steel slag production process does not need to consume precious water resources After the steel slag is crushed, rod milled, and magnetically separated, the slag steel can be selfgrinding to obtain grade A and B scrap steel The iron content of the slag powder can reach more 2024年1月17日 Contemporary methods of manufacturing cement can be divided into two ways: dryprocess cement production and wetprocess cement production The latter measure has been widely utilized in the cement industry; it is a common manufacturing method in which fuel and power consumption have been reduced to a larger extentWhat Do You Know About Wet Process Of Cement ProductionDownload scientific diagram Stages in cement production flow chart [43] from publication: A review on kiln system modeling The purpose of this study is to evaluate performance cement of Stages in cement production flow chart [43] ResearchGateSlag Vertical Mill Production Line from ZKCorp engages the advantages of simple process flow, highefficiency of grinding, great drying capacity, Blast Furnace Slag 水泥 Cement 生料 Raw Material 直径 Diameter 中径 Roller GGBS Production LineChina Henan Zhengzhou
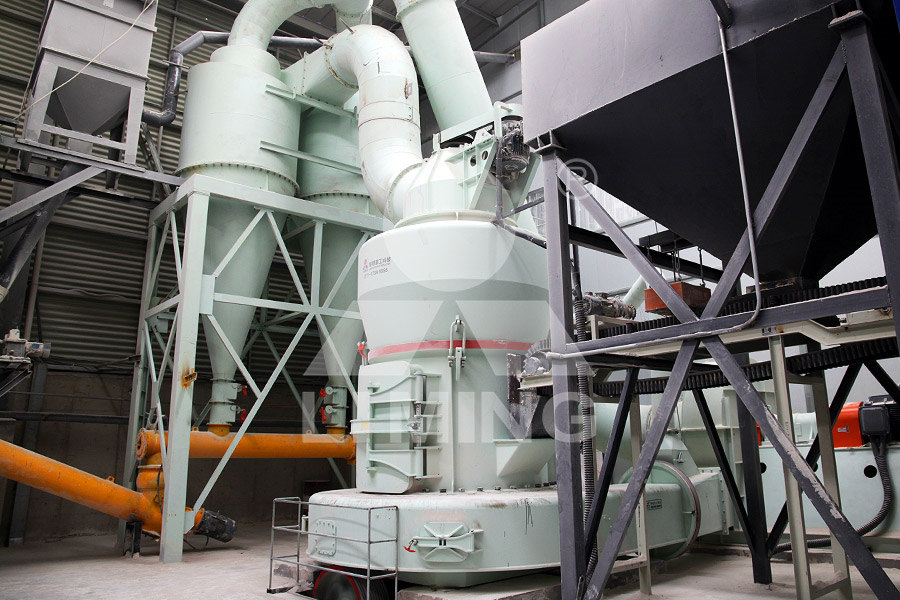
Blockflow diagram of primary and secondary steel
Download scientific diagram Blockflow diagram of primary and secondary steel slag production from publication: Sustainable ironrich cements: Raw material sources and binder types The bulk Number of problems can occur and arise within the cement production line as a result of materials compositions variations For example Viscous slag, hard burning, high early cement strength with low sulfate resistance (greater Cement Manufacturing Process INFINITY FOR 2024年10月10日 Steel slag is a byproduct of steelmaking process The producing of steel slag in China is proximately 100 million tons, but the utilization ratio of comprehensive resources is the lower This paper described the production and composition characteristics of steel slag, reviewed current situation and progress of resource utilization and stabilization of steel slag Steel slag The Research Progress of Steel Slag Utilization and Stabilization how to make blast furnace slag cement? Recently, Slag has become an important mixing material of cement, grind ability of slag is very poor In general, the slag powder is processed by the slag grinding plant in advance, and slag powder will be sent into the cement plant for making slag cement, so it is particularly important to select the appropriate slag grinding plantSlag Cement Production Line Blast Furnace Slag Cement Making
.jpg)
Cement and Clinker Production by Indirect Mechanosynthesis Process
Global cement production has reached 39 billion tons However, the clinkerization process, which is the basis of cement production, is responsible for an approximate annual global CO2 emission of 2 billion tons As part of CEMBUREAU’s 5C strategy, the European cement industry aims to achieve carbon neutrality throughout the cementconcrete value chain by 2050 This article is Download scientific diagram Process flow diagram for the cement manufacturing process, showing electricity and heat consumption or inputs [39] from publication: Energy Savings Associated with Process flow diagram for the cement manufacturing process, Cement Manufacturing and Process Control 41 Cement Manufacturing: Basic Process and Operation To design the Refractory for the lining of different equipments in a cement plant, it is necessary to understand the total operational process of a cement plant in depth It is necessary to know the conditions prevailing in different equipments and theChapter 4 Cement Manufacturing and Process Control2015年8月1日 Cement production, which is highly dependent on the availability of natural resources, will face severe resource constraints in the future This is especially true for the cement industry in ChinaAnalysis of material flow and consumption in cement production process
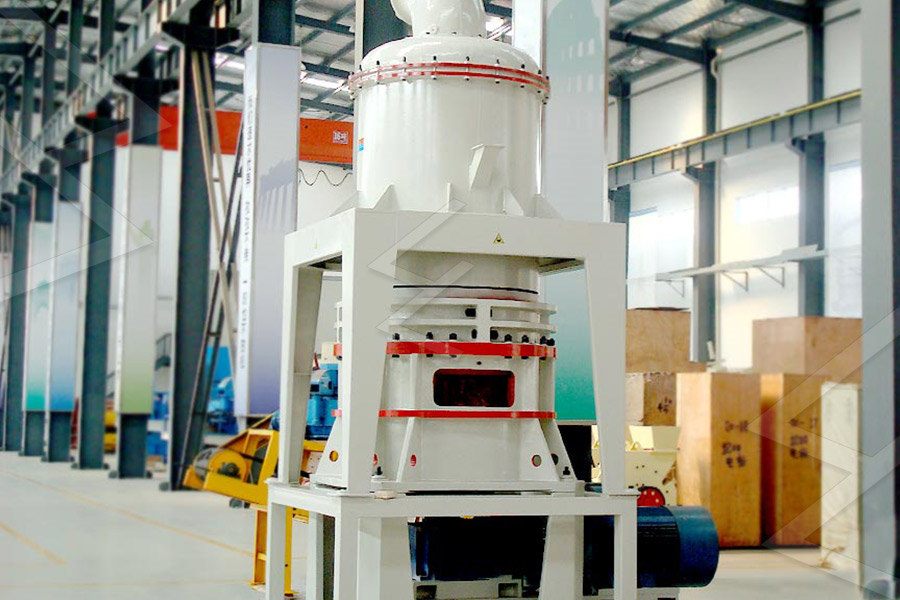
Cement Production Line,Cement Machine,Rotary KilnJiangsu
The general introduction of the technology used in the slag powder/steel slag powder production line with annual capacit The 2500 Tons/Day Dry Process Cement Plant Process Flow of 2500Tons/Day Dry Process Cement 4876m rotary kiln 2 Output: 5000t/d dry process cement production line 3 Inclination: 4% 4 Rota2014年6月10日 Evolution of the cement Process • Wet process easiest to control chemistry better for moist raw materials • Wet process high fuel requirements fuel needed to evaporate 30+% slurry water • Dry process Cement manufacturing process PPT Free DownloadThe cement manufacturing process starts from the mining of raw materials that are used in cement manufacturing, mainly limestone and clays A limestone quarry is inside the plant area and a clays quarry is as far from the plant area Manufacturing process LafargeThe use of fossil fuels such as coal, natural gas, and oil is common in cement production, both as a fuel for the kiln and as a source of heat for other parts of the process which leads to CO2 emitted by combustionHowever chemical reactions happening in the kiln (calcination) are also responsible for up to 60% of the total of emissions of the cement production process [PCA]Cement Production Demystified: StepbyStep Process and
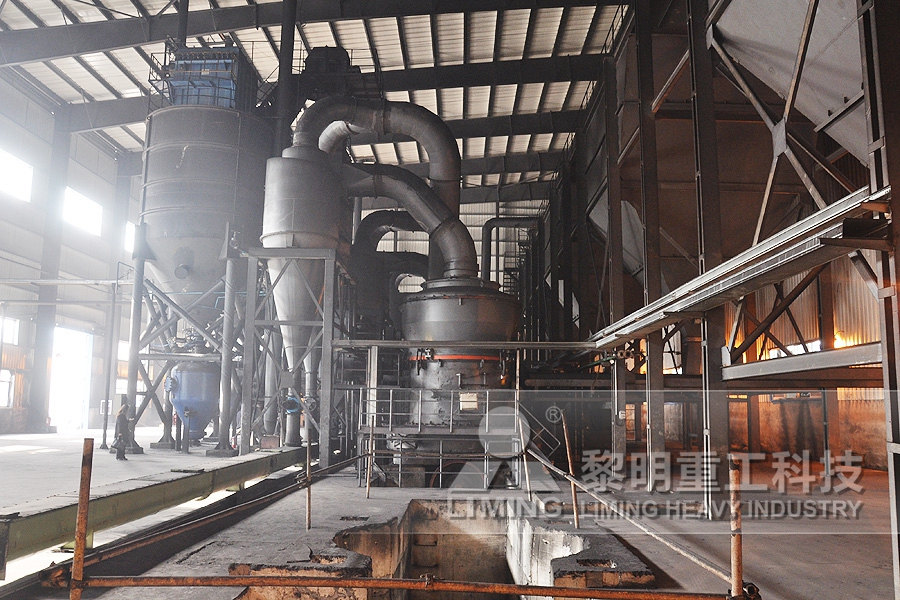
Application technology of calcium carbide slag: a case study ZKG
Since 2007, new dry process production lines with calcium carbide slag have developed rapidly, including at the Xinjiang Tianye cement plant, Inner Mongolia, the Yili Jidong cement plant, the Yili Qingsong Nangang cement plant, Jinni Group’s new dryprocess cement second plant, etc, mostly at the 2500 t/d or 3000 t/d production scaleWith 65 years of dedicated experience in cement equipment and fertilizer research, development, and manufacturing, we are your expert and reliable partner for cement plant technology, and equipment, continually striving to enhance production processes and precision Our focus spans metal casting to riveting, welding, machining, and heat treatmentCement Fertilizer Equipment Manufacturer 65+ years Experience4 天之前 By this process, the product formed is Portland cement Related: 17 Types of cement their properties and Uses Types of Manufacturing of cement There are two processes known as “wet” and “dry” processes depending upon whether the mixing and grinding of raw materials are done in wet or dry conditionsManufacturing of Portland Cement – Process and MaterialsEnvironmental Benefits of Slag Cement Slag cement is used in nearly all types of concrete construction: pavements; structures and foundations; mass concrete (ie, dams and retaining walls); and prestressed, dry cast and precast concrete products such as pipes, pavers, and blocks Today, slag cement is the best option for a concrete producer to use for the lowest Slag Cement Heidelberg Materials
.jpg)
Process Flow of Recovering Ferrochrome from Ferrochrome Smelting Slag
2021年4月6日 After several generations of equipment production practices, Forui Machinery has designed the process flow and equipment configuration with the lowest loss 3 Good treatment effect, no secondary pollution The Ferrochrome slag treatment program has a very good effect on the treatment of ferrochrome slagHowever, in the 1950s, slag cement became available in other countries as a separate product The first granulation facility in the US to make a separate slag cement product was Sparrows Point, Maryland, in the early 1980s Recent years have seen the supply and acceptance of slag cement grow dramatically throughout the USWhy Slag Cement? SCAPerformance comparison of cement replacing materials in concrete: Limestone fillers and supplementary cementing materials – A review Daman K Panesar, Runxiao Zhang, in Construction and Building Materials, 2020 23 Slag cement Slag cement is a byproduct from the iron manufacturing industry Molten slag is produced with molten iron in blast furnaces Slag Cement an overview ScienceDirect TopicsContinuous high temperature process in the cement industry: Calcination and cement clinker burning Calcination of raw material CaCO 3 => CaO + CO 2 Process emissions of raw material: = 054 t CO 2 /t clinker Endotherm reaction at 950 °C ca 1700 MJ/t clinker ≈ 50% of energy Cement clinker burning at 1450 °C formation of hydraulicProcess characteristics of clinker and cement production SINTEF
.jpg)
Cement Making Process Cement Production
The comparison data between the wet process cement production line and the new dry process cement production line shows that with the same rotary kiln size (diameter), the production capacity of the cement kiln which adopts the pre 2021年3月9日 In this study the process flow diagram for the cement production was simulated using Aspen HYSYS 88 software to achieve high energy optimization and optimum cement flow rate by varying the flow Simulation and Optimization of an Integrated Process Flow Sheet plants is also sold outside to cement plants Slag application also reduces the overall cost of production of cement JSPL has established Nandyal works, Andhra Pradesh Vijaynagar works, Karnataka and Dolvi works, Maharashtra of 480 MTPA 060 MTPA and 220 MTPA cement plant to produce portland slag cement (PSC) and GroundSLAG IRON AND STEEL IBM2022年5月12日 Use of slag In industrial production, slag plays an important role Some major factories refine and process slag into slag cement, slag micro powder, slag powder, slag Portland cement, and slag wool Blast furnace slag can also be used as raw materials for cast stone, glassceramic, fertilizer, enamel, ceramics, etc (1) GlassceramicSlag grinding mill micro powder production line SBM Ultrafine
.jpg)
Copper Slag Processing Production Line Flow Henan Forui
2021年12月5日 COPPER SLAG PROCESSING PRODUCTION LINE FLOW:1 Using a Crusher for Crushing, 2 Using a Mill for Grinding, 3 Screening Skip to content Main Menu Home; About; If you need equipment quotation and process flow, please feel free to Contact Us: Whatsapp: +87; : asaguo@foruimining;Download scientific diagram Typical cement manufacturing process flow diagram [4] from publication: Model Development for CO2 Capture in the Cement Industry Climate change has become a Typical cement manufacturing process flow diagram [4]Figure 7 and 8 the process flow diagram of a granulator and heat recovery system for superheated steam production is shown The process parameters shown in these figures are exemplary for a slag Process flow diagram of a dry slag granulation system for steam 2002年11月11日 Conference: Nigerian Materials Congress (NIMACON) Akure, Nigeria November 1113, 2002 At: NIMACON 2002: Engineering Materials Development Institute, Akure, Nigeria(PDF) Slag Cement Production in Nigeria ResearchGate
.jpg)
Manufacturing of Cement By Dry and Wet Process Expert Civil
Burning: In this operation, the slurry is directly fed into a long inclined steel cylinder called a Rotary kilnIn this kiln there are 3 different zones shown in fig below Cement Manufacturing Process Flow Chart (i) Drying Zones: In the wet process, the drying zone is comparatively larger than the dry process It is because the raw material in slurry form is directly fed into the kiln