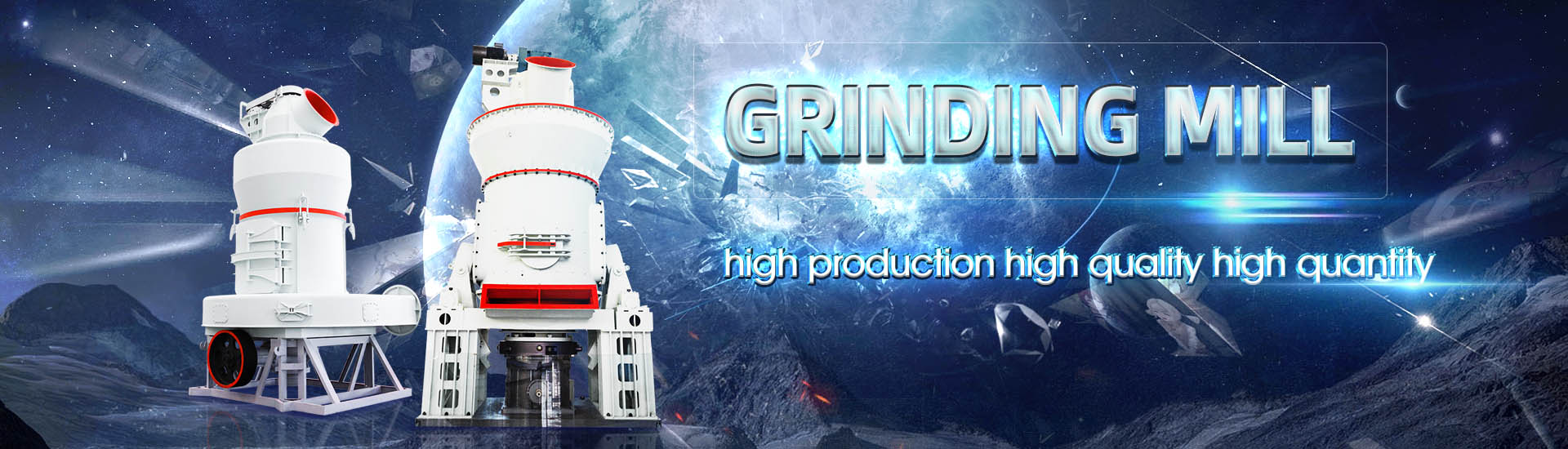
Vertical grinding mill driver
.jpg)
Vertimill® Metso
The Vertimill® is globally recognized as an energy efficient grinding mill Through a low total cost of ownership, it brings substantial improvement to the profitability of concentrators During the years, Vertimill® technology has proven to be Basically the vertical mill gearbox serves to transmit the motor couple to the grinding table Moreover, it directs the grinding forces into the mill foundation Unlike on conventional gearboxes, these two functions are completely Multiple drive for vertical mill MultiDrive Gebr PfeifferThe drive of a vertical roller mill – essentially the mill gearbox – has to fulfill two tasks: The first is to reduce the speed of the electric motor to the selected mill speed and to transmit the torque DRIVE SELECTION FOR LARGE LOESCHE VERTICAL ROLLER MILLSEnergy efficiency is an important factor of the total cost of ownership (TCO) The new "MultipleDrive" drive concept unites the benefits of a variablespeed drive with the modularity Flender MultipleDrive Gear Units for Vertical Mills
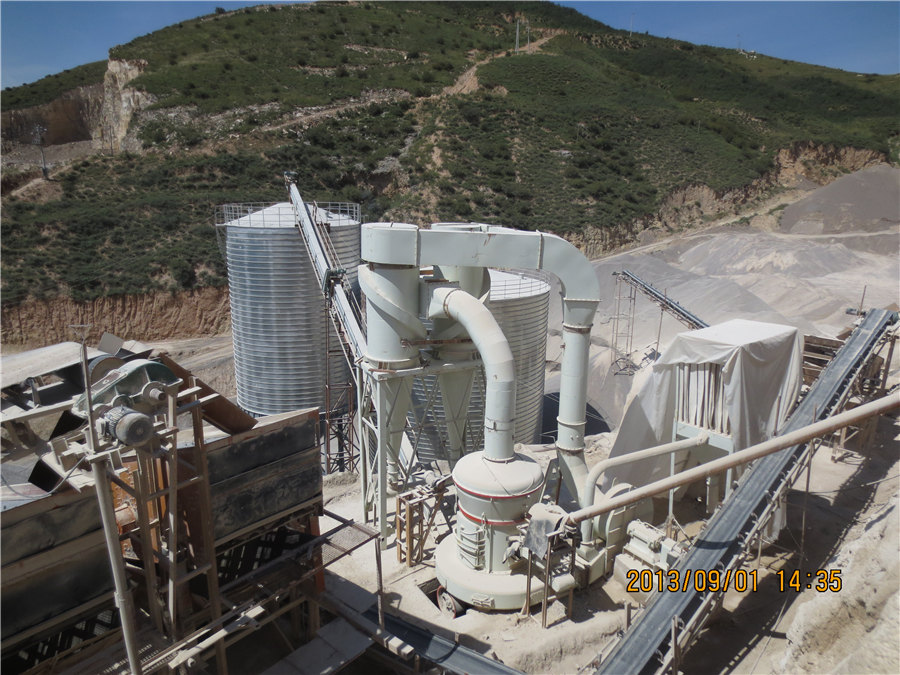
Vertical Mill Roller Drives dbsantasalo
Delivering up to 3000 kNm torque, David Brown Santasalo vertical roll mill drives provide the optimum solution for grinding applications Developed in cooperation with roller mill manufacturers, our vertical roll mill gearboxes combine strength The roller driven mill is unique compared to the other described systems Each roller unit is driven by its own motor and gearbox which fundamentally changes the grinding process An increased roller foundation is required on the level of Drive Systems for Vertical Roller MillsVERTIMILL® is Metso’s gravityinduced, vertical stirred mill Its vertical configuration allows for large throughputs while maintaining a small footprint in your circuit The VERTIMILL® can Metso VertimillsMPS vertical mill from Pfeiffer is the ideal allrounder Grinding of coal, petcoke, clay, limestone, quicklime, gypsum, and many other materials Mill drive: up to 2,000 kW: Number of grinding rollers: 3: Feed size: up to 100 mm: Feed Coal mill, gypsum mill, clay mill, etc Pfeiffer MPS mills
.jpg)
KMPS Vertical Mill Gearboxes Gear Units Products
Vertical Mill drives in the medium to high power range are used for the grinding of raw meal, clinker and slag Flender offers by far the most comprehensive drive solutions for this challenging processdrive and the “4+4” cement mills and 6roller raw mills in combination with a common parts concept covering both of the mill types, the technical and commercial risks derived from single grinding unit solutions are significantly reduced Unexpected and undesirable downtime of LATEST TECHNOLOGICAL INNOVATIONS IN GRINDING WITH THE VERTICAL ROLLER MILL2007年4月29日 New developments in drive systems for ball mills and vertical roller mills are contributing to the constant efforts to increase Cement Plant efficiency and to reduce operating costs and initial investments Besides the technical aspect of selecting a drive system, the initial cost, cost of installation, cost of commissioning as well as cost of operation are factors in the Gearbox design development for central mill drives and vertical MVR vertical mill with conventional drive: economical solution for small to medium output rates For the preparation of cement raw material, Mill drive: up to 6,000 kW: Number of grinding rollers: up to 6: Feed size: up to 120 mm: Target fineness degrees: 1,500 – 6,000 cm 2 MVR vertical roller mill with planetary gearbox Gebr Pfeiffer
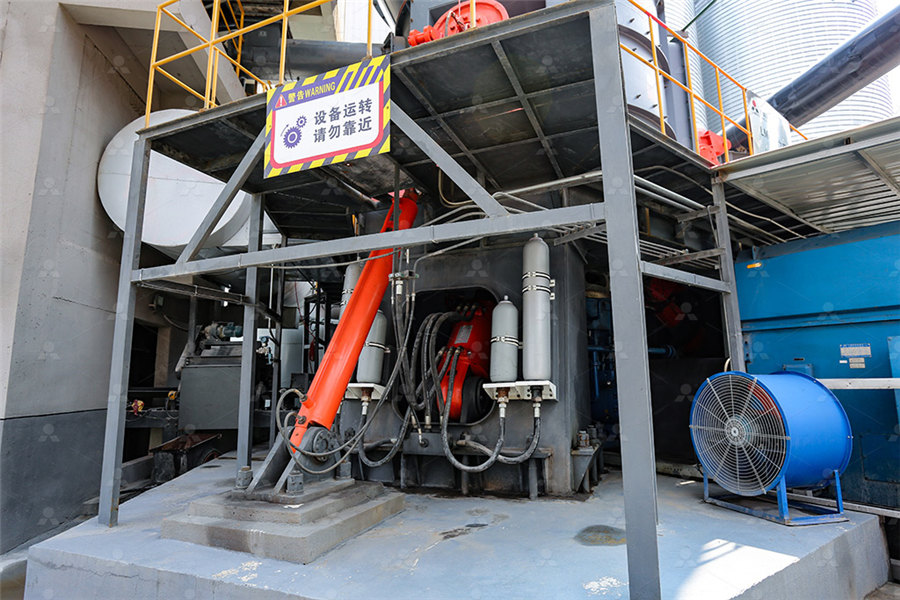
VERTICAL ROLLER MILL DRIVE GEARBOX Elecon
Roller Mils are directly driven bevelwheel planetary gears or bevel cylindrical gear units The gear unit represents an almost integral component of the mill The output flange of the gear unit is rigidly connected with the grinding table In addition to transmitting the torque ,the gear unit also has capability to take up the reaction forces from the the griding force of the mil’s rollersIncrease the energy efficiency of your vertical roller mill Reducing energy consumption is a top priority for both environmental and economic reasons But you can't afford to lose performance in your VRM Our MAAG® GEAR CEM Drive system achieves both, powering VRMs up to 14 000 kW with a compact integrated motor that reduces power loss by more than 20%MAAG® GEAR CEM DriveNote: Vertical grinding mills are used extensively within the cement industry Vertical Grinding Mill Components A vertical grinding mill consists of the following components: Electric Motor to rotate the grinding table The electric motor is often a three phase variable speed drive (VSD) induction motor, but designs varyVertical Grinding Mill (Coal Pulverizer) Explained saVReeThe intelligent design of the MultiDrive ® perfectly fits the trendsetting Pfeiffer MVR mill because with both elements together, active redundancy is ensured for the mill drive and grinding rollers Up to six independent drive units, each comprising an electric motor and gear, engage with a girth gear flanged to the neck of the grinding table transmitting their torques to the latterMultiple drive for vertical mill MultiDrive Gebr Pfeiffer
.jpg)
DRIVE SELECTION FOR LARGE LOESCHE VERTICAL ROLLER MILLS
1 A background to drives of vertical roller mills The drive of a vertical roller mill – essentially the mill gearbox – has to fulfill two tasks: The first is to reduce the speed of the electric motor to the selected mill speed and to transmit the torque created by the motor Secondly, the gearbox hasthe lifetime of your mill Cement grinding plant on EPC basis Reduction of capital expenditure by implementing a onemill solution with MultiDrive® as compared to a twomill solution with conventional drives For this comparison, the following cost items were considered: » Vertical roller mill(s) » Mill gearbox(es)PFEIFFER VERTICAL MILL WITH MULTIDRIVE MORE POWERThe motor drives the grinding disc to rotate through the reducer The vertical grinding mill does not have the metal impact sound of the steel balls colliding with each other and the liner in the ball mill, so the noise is low, which is 2025dB lower than that of the ball millIndustrial Vertical Grinding MillRead this indepth blog to learn about the working principle of Vertical Grinding Mill, its application, and its advantages +91 226796 9655 sales@macawberindia 130131, Hindustan Kohinoor Complex, LBS Road, Vertical Grinding Mill: How it Works, Application And
.jpg)
Vertical roller mill for raw Application p rocess materials
Recently, the vertical roller mill having great grinding performance is widely applied to the raw material grinding process However, tube mill, which has about 30% poor grinding performance as power consumption, has been still used many existing cement plant The improvement of this tube mill grinding system is highly expected DescriptionsAll the processes of grinding, drying, milling, powder screening and transporting are realized in one vertical grinding mill; no need for extra drying, screening or improving equipment The dedusting part is collected by a high concentrated pulse dustor The whole unit is compact and the construction area is about 50~60% of the ball millVSCM SERIES COARSE VERTICAL GRINDING MILL7 // Almost any plant for the grinding of cement raw material is a combination of machines specially adapted to the particular physical properties of the material to be ground As a result, our plants work efficiently without any trouble » Highly efficient grinding, drying, and separating in one unit » Outstanding production capacities exceeding 1,400 t/h in one single millPFEIFFER MILLS FOR THE CEMENT INDUSTRYOur wear parts for vertical mill grinding circuit are designed to minimize environmental impact through reduced energy consumption and waste generation, the sort of thing that has helped to drive new thinking in vertical mill technologies for the mining sector – are being responsible and customerfocusedVertical Mill Mining Magotteaux
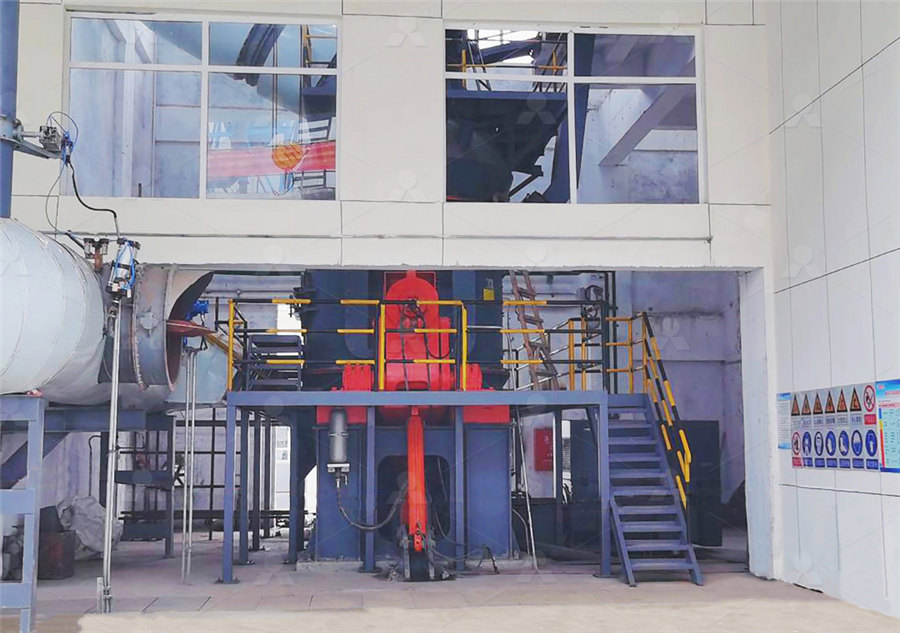
Cement grinding Vertical roller mills VS ball mills
For ball mills grinding OPC to a fineness of up to around 3600 cm2/g (Blaine) grinding aid is usually not required; it may not even be feasible considering the cost of grinding aid However, a vertical roller mill for cement grinding generally requires the use of grinding aid to achieve the most efficient operation with a stable grinding bed It is suitable for replacements of existing vertical mill drives CONCLUSION With the trend towards large single VRMs for raw material and cement grinding the reliability of the drive systems are only becoming more critical Many competing drive technologies have been developed with the focus of increasing reliabilityDrive Systems for Vertical Roller MillsWhether grinding raw coal, clinker, cement and/or slag, we have a VRM solution to suit your grinding needs What’s more, our online condition monitoring services enable you to adopt a proactive maintenance strategy for your OK™ and ATOX® mills that eliminates unexpected downtime and ensures continuous high performanceVertical roller mills FLSmidth CementDelivering up to 3000 kNm torque, David Brown Santasalo vertical roll mill drives provide the optimum solution for grinding applications Developed in cooperation with roller mill manufacturers, our vertical roll mill gearboxes combine strength Vertical Mill Roller Drives dbsantasalo
.jpg)
OK™ Raw and Cement Mill
The OK™ Mill was originally designed for cement grinding In 2017 we released the OK™ vertical roller mill for raw materials grinding The OK™ Mill’s modular design comes with unique flexibility, showcasing parts commonality, where Availability meets Performance – Vertical Mill Drive with high capacity and redundancy MultipleDrive for Vertical Mills At the same time the grinding result is improved The concept: two, three, four, five or even six independent drive units drive a common girth gearFlender MultipleDrive Gear Units for Vertical Millspage 05 2 vertical mills introduction page 07 3 principles of vertical grinding systems page 07 31 vertical mill components page 07 32 how does a vertical mill work? page 08 4 a new generation of grinding additives: maga/vm and mape/vm page 08 41 mill output increase page 09 42 quality and water demand optimisation page 09 5Technical Notebook CEMENT ADDITIVES FOR VERTICAL MILLSDrives for large vertical roller mills ditives (types and proportion of mill feed) For the grinding of granulated blast furnace slag (GBFS) a 20 % bigger motor is necessaryDrives for large vertical roller mills ResearchGate
.jpg)
Introducing the Vertical Roller Mill with Driven Rollers: An
2015年8月31日 With the market demand for efficient, highly flexible, and highcapacity plants for cement production, it was time to develop an innovative drive concept to cope with the demand: the world's first vertical roller mill (VRM) with driven rollers With this concept, it is the rollers of the VRM that are driven, notas is usually the casethe grinding table With the rollerdriven Mill Capacity [t/h] Mill Drive Power Output Torque Gearbox Mill Capacity Fig 1: Development of mill sizes 11 Function of the main gearbox in a vertical roller mill The main gearbox of a vertical roller mill has to perform two major tasks (see also Fig 2): 1 Transmission of the power from the main motor to the grinding table 2A New Gearbox Generation for Vertical Roller Mills Artec Machinethe lifetime of your mill Cement grinding plant on EPC basis Reduction of capital expenditure by implementing a onemill solution with MultiDrive® as compared to a twomill solution with conventional drives For this comparison, the following cost items were considered: » Vertical roller mill(s) » Mill gearbox(es)PFEIFFER VERTICAL MILL WITH MULTIDRIVE MORE POWERThe world’s most reliable stirred mill just got bigger Developed as a solution to lower capital expenditure, the Vertimill® 7000’s much larger size allows for more available power One Vertimill 7000 grinding mill, replaces the need for multiple smaller Vertimill grinding mills to achieve the same power output Key benefits:Vertimill® Metso
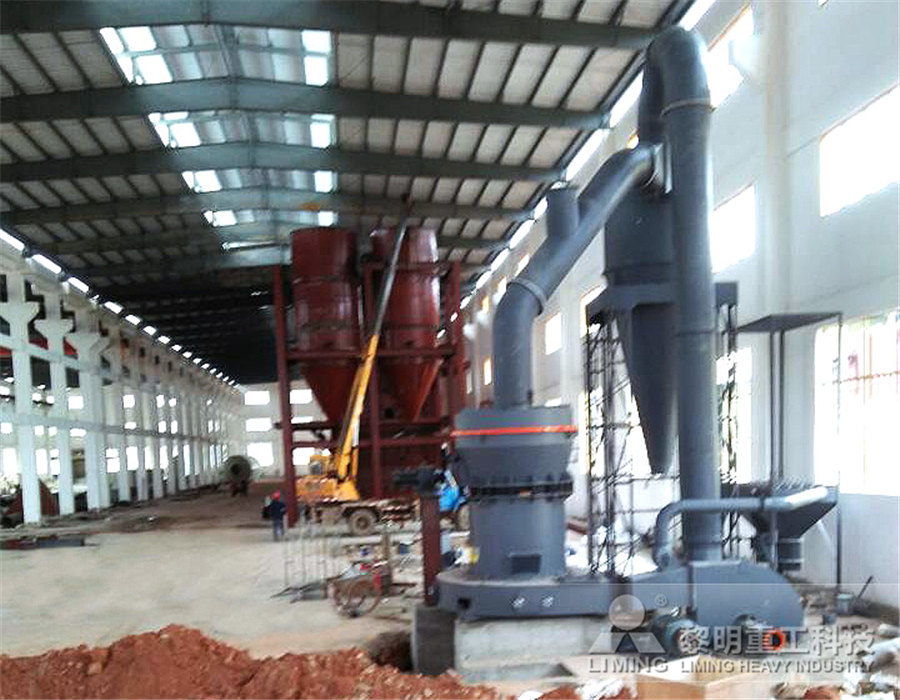
Industrial gear unit drive solution for vertical mills SEW
Vertical mill Various types of vertical mills exist to grind limestone, design and arrangement of grinding rolls in vertical mills vary depending on the manufacturer and the material to be ground Our drive solutions for vertical mills are also characterised by The hightorque drive allows the use of various grinding media, catering to a wide range of densities, while the variable speed drive ensures the mill can adjust to different process conditions, enhancing performance flexibility The vertical design also eliminates cavitation issues within the grinding zone at high speedsVertical mills for fine grinding – FLSWith our partner Gebr Pfeiffer, they are the pioneers of vertical roller mill technology for material grinding The inventors of mill drives with more than 10,000 kW, modular ready2grind systems and gypsum calcination in vertical Industrial Solution Provider Malaysia AYS EngineeringVertical design eliminates cavitation in the grinding zone at high speeds ; Hightorque drive allows the use of grinding media with a wide range of intrinsic density ; Variable speed drive allows the mill speed to vary with process conditions ; Quick, simple, safe maintenance procedure;VXPmill for fine ultra fine grinding FLSmidth
.jpg)
CLUM Series Ultrafine Vertical Roller Mill
3 Double PositionLimiting Technology Makes Operation More Stable In the CLUM series ultrafine vertical roller mill, the contact point between roller shell and millstone liner plate adopts electronic limiting technology and mechanical limiting protection technology, which can avoid the destructive impact (eg the grinding roller directly smashing the millstone) caused by machine Drive System: The drive system comprises the motor, gearbox, and clutch assembly, which provide rotational power to the mill It ensures smooth and controlled mill operation Discharge System: The discharge system includes the discharge chute, trommel screen, and trunnion, which allow the ground materials and grinding media to exit the mill while retaining oversized Ball Mill Grinding Machines: Working Principle, Types, Parts The main motor of the vertical roller mill drives the grinding plate in the grinding machine through the transmission of the reducer The grinding roller rotates around the pins under the friction of the grinding plate After the feeding screw is dropped into the center of the grinding plate,it is moved to the edge of the grinding plate by the Vertical roller mill Hengtu MachineryVertical mill Various types of vertical mills exist to grind limestone, design and arrangement of grinding rolls in vertical mills vary depending on the manufacturer and the material to be ground Our drive solutions for vertical mills are also characterized by Industrial gear unit drive solution for vertical mills SEW
.jpg)
Diamant Vertical Grinding Mill Engsko
The Vertical Grinding Mill is now CEapproved For very fine grinded coffee on our Diamant Vertical mills, we can supply the mills with special coffee stones in the size 400 mm and 500 mm Our mill in size 400 mm is available in a special version for milling oily products for example mustard – it must be dry and not wetthe lifetime of your mill Cement grinding plant on EPC basis Reduction of capital expenditure by implementing a onemill solution with MultiDrive® as compared to a twomill solution with conventional drives For this comparison, the following cost items were considered: » Vertical roller mill(s) » Mill gearbox(es)PFEIFFER VERTICAL MILL WITH MULTIDRIVE MORE POWERpressure on company’s operations The original tertiary grinding fineness was 325 mesh with 7173% passing Iron concentrate grade was 65% and the average recovery rate 87% Solution: Introduction of Metso’s Vertimill® VTM1500 vertical grinding mill at Miaogou Iron Mine to achieve the goal of the technologicalMetso Vertimills