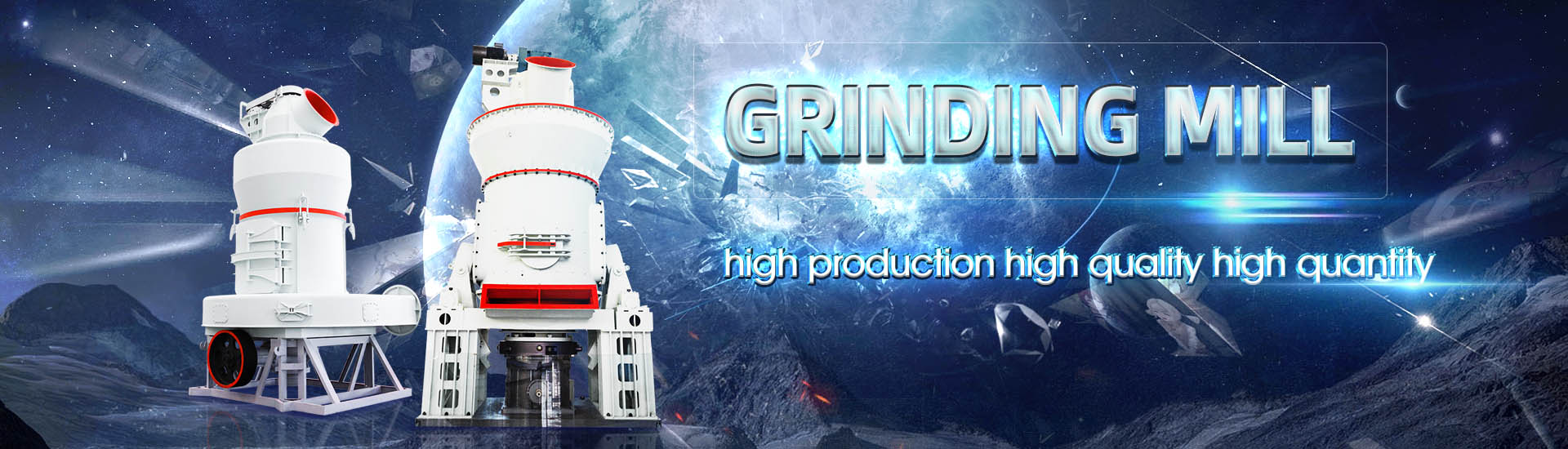
The weight and price of vertical ore mill
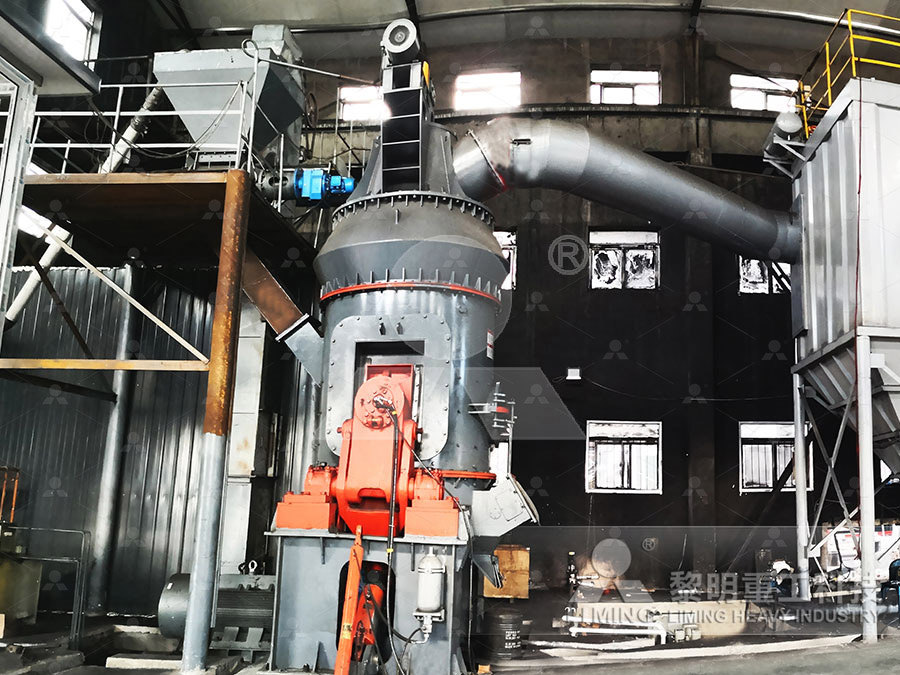
Metso Vertimills
VERTIMILL® is Metso’s gravityinduced, vertical stirred mill Its vertical configuration allows for large throughputs while maintaining a small footprint in your circuit The VERTIMILL® can bring up to 40% savings in energy consumption in some cases, and helps in reaching excellent The mechanical cost of the wet ball milling circuit is R48,328,000 compared to R59,185,000 for the dry Loesche VRM circuit (increase of 225%) The different components of the capital A Technical and Economic Comparison of Wet Milling versus Dry 2022年5月31日 The vertical roller mill (VRM) is commonly used for secondary and tertiary crushing processes in numerous industries In this study, the discrete element method (DEM) Analysis of vertical roller mill performance with changes in material 2019年4月16日 The paper demonstrates why the Loesche VerticalRollerMill (VRM) is a serious alternative to conventional grinding technologies and where the limitations of the system are(PDF) LEARNING FROM OTHER INDUSTRIES; WHY THE
.jpg)
RECENT DEVELOPMENTS IN COARSE GRINDING USING VERTICAL
Vertical stirred milling is a wellrecognized technology for the secondary, regrind and fine grinding applications and are increasingly replacing coarser ball mill applications in secondary and Therefore, the regrinding circuit of Germano second concentrator offers an interesting opportunity: a vertical mill operating in parallel with two ball mills During almost two years of operation, Comparing ball and vertical mills performance: An industrial case 2014年10月20日 This paper presents an overview of the regrind circuits in Brazil that operate with vertical mills and the results of industrial surveys at selected vertical mill circuitsRegrind of metallic ores with vertical mills: An overview 2019年4月16日 Conference: Applying a Successful Technology from the Cement Industry: Advantages of Grinding Ore in a VerticalRollerMill; At: Antalya, Türkey(PDF) LEARNING FROM OTHER INDUSTRIES; WHY THE
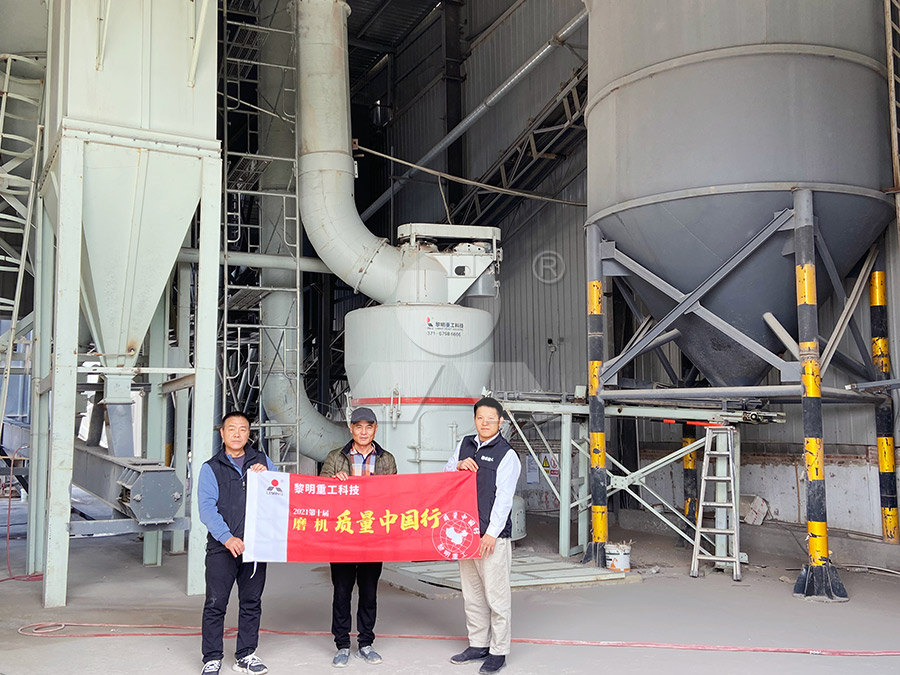
Performance Evaluation of Vertical Roller Mill in
2017年9月11日 In this study, an extensive sampling study was carried out at vertical roller mill of ESCH Cement Plant in Luxemburg Samples were collected from mill inside and around the circuit to evaluate the Find your ore mill easily amongst the 42 products from the leading brands (Fritsch GmbH, Retsch, Eriez, The POITTEMILL pendulum roller mill is a vertical mill that works by compressing the material bed *Prices are pretaxOre mill, Ore grinding mill All industrial manufacturersThe rod mill is another type of grinding mill used in the copper ore mining process This machine uses steel rods as the grinding media instead of balls, which are commonly used in ball mills The rods grind the ore by tumbling within the mill, similar to the action of a rotating drumUnderstanding the SAG Mill in Copper Ore Mining ProcessVertical raw mill is one kind of raw mill, generally used to grind bulk, granular, and powder raw materials into required cement raw meal in the cement manufacturing plantVertical raw mill is an ideal grinding mill that crushing, drying, grinding, grading transfer set in one It can be widely used in cement, electric power, metallurgy, chemical industry, nonmetallic ore, and other industriesVertical raw mill Cement Plant
.jpg)
Vertical Cement Mill
Low energy, the powder consumption of vertical mill is 20%30% less than that of ball mill With the incensement of moisture of the raw material, the powder consumption will decrease obviously The vertical mill saves 30%40% of energy consumption compared to the ball mill Vertical mill has less noise than ball mill, about 2025dBRequest PDF On Sep 1, 2016, Deniz Altun and others published Operational parameters affecting the vertical roller mill performance Find, read and cite all the research you need on ResearchGateOperational parameters affecting the vertical roller mill 2019年3月3日 This study investigated a mathematical model for an industrialscale vertical roller mill(VRM) at the Ilam Cement Plant in Iran The model was calibrated using the initial survey's data, and the Modeling and simulation of vertical roller mill using population Vertical stirred mills are a fine grinding equipment that covers advantages of low rotation speed, high reliability and long life cycle The significant advantages that the vertical stirred mills have over the ball mills are smaller size, less auxiliary equipment required, more simple system and more options of processing methodsVertical Stirred Mill Mineral Processing Equipment CITIC HIC
.jpg)
vertical roller mill, vertical coal mill, vertical slag mill, superfine
Vertical roller mills are mainly engaged in three major fields of slag, coal powder, and nonmetallic ore Divided into: vertical roller mill, vertical slag mill, vertical coal mill, and ultrafine vertical mill2014年10月20日 Rio Paracatu regrind circuit Santos Júnior et al (2011) presented some data on the Paracatu Vertical Mill circuit process, as well as its comparison to the plant's conventional ball millRegrind of metallic ores with vertical mills: An 2022年1月23日 This work concentrates on the energy consumption and grinding energy efficiency of a laboratory vertical roller mill (VRM) under various operating parametersAnalysis and Optimization of Grinding Performance of 2022年5月23日 Grinding experiments were conducted in a laboratoryscale stirred mill on a lowgrade PGE bearing chromite ore HighPressure Grinding Rolls (HPGR) product of −1 mm was used as feed material to (PDF) Modeling and application of stirred mill for the coarse
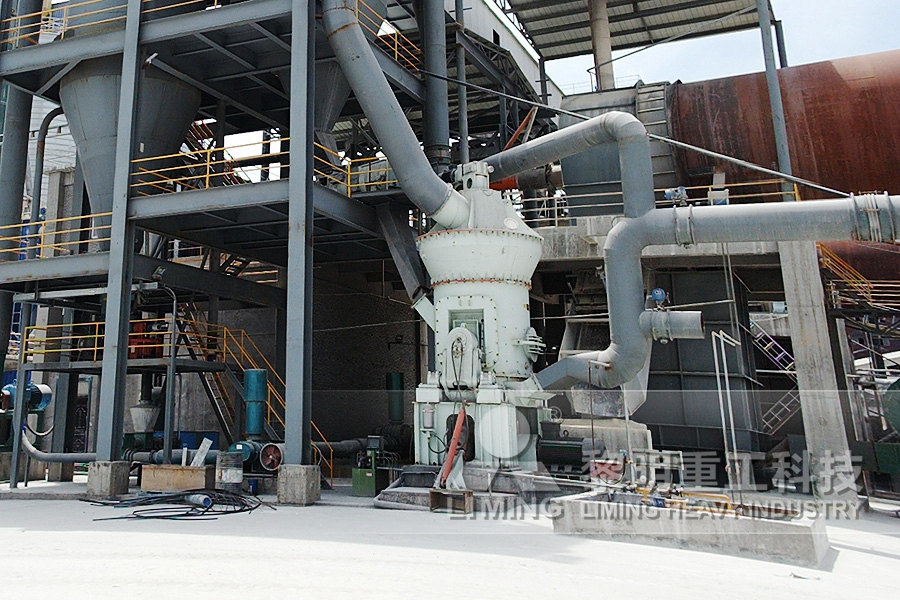
Predicting the effect of operating and design variables in
2021年7月1日 Vertical stirred mills may be classified according to the speed of the stirrer in two groups: gravityinduced or fluidized mills [[1], [2], [3]]In the gravityinduced mills, the stirrer, generally of the screw type, turns so that the grinding charge exhibits an ascending convective motion at the center, descending from the edges of the screw and close to the mill shell, owing 2015年6月19日 The basic parameters used in ball mill design (power calculations), rod mill or any tumbling mill sizing are; material to be ground, characteristics, Bond Work Index, bulk density, specific density, desired mill tonnage capacity DTPH, operating % solids or pulp density, feed size as F80 and maximum ‘chunk size’, product size as P80 and maximum and finally the type of Ball Mill Design/Power Calculation 911Metallurgist2022年5月31日 Analysis of vertical roller mill performance with changes in material properties and operating conditions (14), and the throughput refers to the weight of particles discharged from VRM per unit time, which can be obtained by postprocessing Research of iron ore grinding in a vertical rollermill Miner Eng, 73 (2015), pp Analysis of vertical roller mill performance with changes in Revised: Mill scale is one of the byproducts which produced during the processing of 11 Mar 2021 Accepted: 28 Apr 2021 ore substitution by mill scale at 3%, the rate of production increases from 2194 to 2550 Keywords mill scale; sintering process; iron ore Abstract steelIt is richEffect of Partial Replacement of Iron Ore by Mill Scale on the
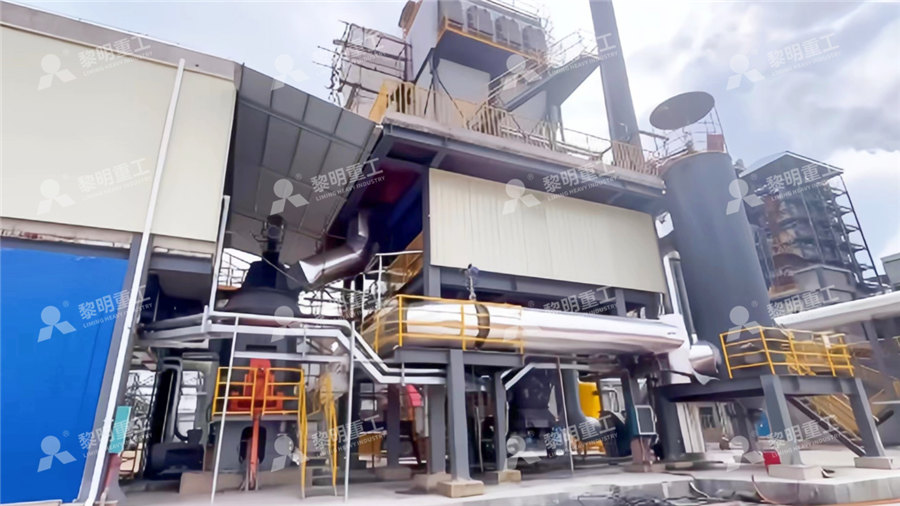
(PDF) Performance Comparison of the Vertical and Horizontal
The mill also has vertical arrangement VXP Mill is a product of FLSmidth company and is vertically oriented stirred media mill The mill is often used in flotation concentrate regrind and precious metals tailings retreatment where the feed size is typically 200 µm [11,12] HIG Mill is a recently developed technology by MetsoOutotech company2019年9月24日 The Extended Drop Weight Test (ExDWT) improves understanding concerning sources of variation in ore competence through the value chain This technique measures and describes the variability in ore Simulating the Impact of Ore Competence Variability on Process 2010年12月1日 Vertical Integration and Macroeconomic Growth: in 2007 wit h a production of 11 6 mill ion t ons of iron ore and consumer prices 2000–2010 steel(PDF) Vertical Integration and Macroeconomic Growth: the Pilot test work was carried out by Mazzinghy et al (2015) on a batch ball mill and pilot scale vertical mill to assess the energy efficiency factor The results shows that the scaling factor of 135 was required to adjust the ball mill energyspecific breakage rates to match the breakage rates in a vertical mill The vertical millRECENT DEVELOPMENTS IN COARSE GRINDING USING VERTICAL
.jpg)
Vertical Coal Mill for Coal Grinding in Cement Plant
Vertical coal grinding mill integrates crushing, drying, grinding, powder selection and conveying; It has simple system and compact structure Vertical coal mill covers an floor area about 50% of the coal ball mill with the same VRM has been widely researched in processing of cement (Ito et al 1997;Jorgensen 2005;Wang et al 2009, Ghalandari et al 2021), coal (Tontu 2020), iron ore (Reichert et al 2015), zinc ore (van Technical specifications of vertical roller coal millRequest PDF On Mar 15, 2015, Mathis Reichert and others published Research of iron ore grinding in a verticalrollermill Find, read and cite all the research you need on ResearchGateResearch of iron ore grinding in a verticalrollermillThe Pfeiffer pilot mill used in this study is a semiindustrial vertical roller mill of type MVR with a table diameter of 400 mm The mill can be equipped with different classifiers for specific applications The process layout of the plant (Figure 2) corresponds to that of an industrial plantVertical Roller Mills used for the comminution of mineral ores
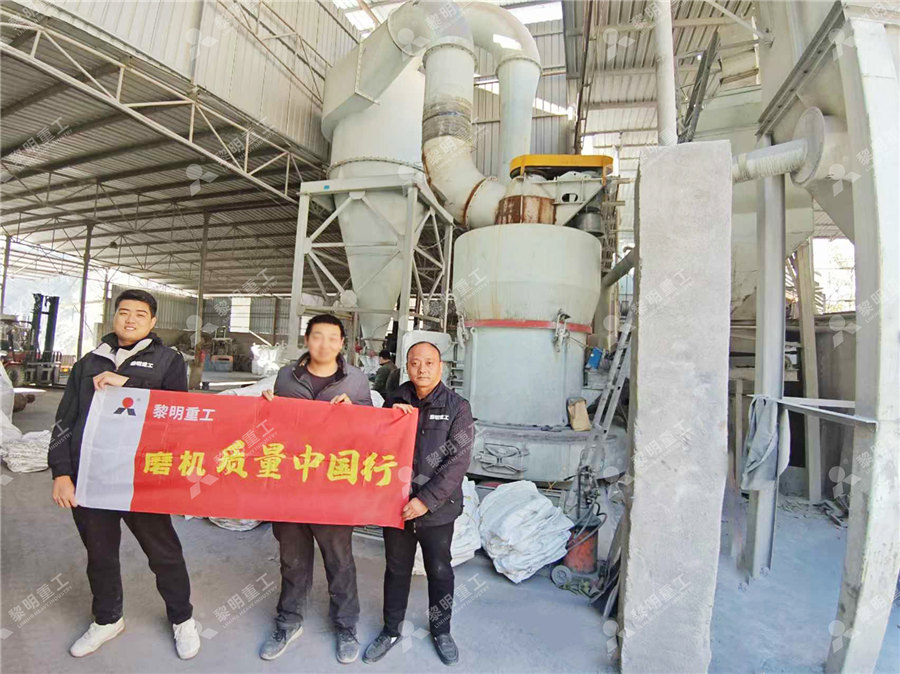
Comparing ball and vertical mills performance: An industrial case study
vertical mill performance and to compare the operational data of the three mills The industrial data was also compared to jar mill tests results, which are monthly conducted in Samarco labs in order to predict the specific energy consumption required by the ore fed to 2016年3月21日 where R represents the ratio: % Pb in crude ore/% Cu in crude ore Formula (32) is very convenient for milling calculations on ores of this type Example: An ore contains 5% lead and 1% copper The ratio of perfect concentration for a concentrate of maximum grade and 100% recoveries of lead and copper would be:Common Basic Formulas for Mineral Processing CalculationsA compact coal mill solution for grinding virtually any type of raw coal Our ATOX® Coal Mill is a compact vertical roller mill that can grind almost any type of raw coal The coal mill utilises compression and shear force generated between the large rollers and the rotating table to crush and grind raw coal, removing the need for a separate piece of equipment for crushingRoller mill ATOX® COAL FLSmidth DorrOliver Eimco vertical A vertical roller mill, also known as a vertical grinding mill or vertical mill, is a comprehensive grinding equipment integrating crushing, drying, grinding, grading, and conveying Vertical grinding mills can be widely used in electric power, metallurgy, construction, chemical industry, and other industries to make powder, especially for materials such as cement clinker, coal Energysaving and Efficient Vertical Roller Mill Fote Machinery
.jpg)
(PDF) Recycling of mill scale in sintering process Science of
2011年1月1日 Infect only a few investigators worked on the kinetics of mill scale reduction [24][25][26][27][28][29][30]In previous studies on the use of the catalyst for iron ore or mill scale reduction Revised: Mill scale is one of the byproducts which produced during the processing of 11 Mar 2021 Accepted: 28 Apr 2021 ore substitution by mill scale at 3%, the rate of production increases from 2194 to 2550 Keywords mill scale; sintering process; iron ore Abstract steelIt is richEffect of Partial Replacement of Iron Ore by Mill Scale on the Figure 37 Size analysis for a repeat experiment performed in a vertical mill shown as a function of grinding time for a single 595 +420μm feed size 71 Figure 38 Vertical mill geometry (left) and RockyDEM simulation of the vertical millPREDICTING THE PRODUCT PARTICLE SIZE DISTRIBUTION FROM A VERTICAL 1 A piece of multipurpose grinding equipment, not only for grinding gold ore but also for gold amalgam; 2 Small investment, high output, low production costs, good benefits, well received by users, is the best equipment to replace the ball Wet Pan Mill JXSC Machinery
.jpg)
Performance Comparison of the Vertical and Horizontal Oriented
2023年1月31日 The mill also has vertical arrangement VXP Mill is a product of FLSmidth company and is vertically oriented stirred media mill The mill is often used in flotation concentrate regrind and precious metals tailings retreatment where the feed size is typically 200 µm [11,12] HIG Mill is a recently developed technology by MetsoOutotech companyDOI: 101016/JPOWTEC202104057 Corpus ID: ; Predicting the effect of operating and design variables in grinding in a vertical stirred mill using a mechanistic mill modelPredicting the effect of operating and design variables in grinding MSE PRO Bench Top Mini High Energy Vertical Planetary Ball Mill, 04L Size (4 x 100ml or 4 x 50 ml) Designed for holding four 50 ml size milling jars or 100 ml milling size jars (to be ordered separately) Can be placed in a glove box Should not be used in an Argon atmosphere as it can cause arcing due to a 110V voltage power supply to this equipmentPlanetary Ball Mills MSE Supplies LLCHow much does a mill weigh and how can you move it safely? A standard Bridgeportstyle vertical knee mill will weigh about 2,000 to 3,000 lbs, depending on when it was made and what options it has To move it, there should be a threaded hole on top of the ram that’s a hoist point Thread in an eye bolt and start hoisting That’s the short How Much a Mill Weighs and How to Move it (+Videos)
.jpg)
Performance Comparison of the Vertical and Horizontal Oriented
Minerals 2023, 13, 315 5 of 16 Figure 4 Pilot scale M20 and its internal structure (on the right) 22 Sampling of FullScale HIGMill and Pilot Tests of IsaMillThese lowgrade ores with complex compositions have a large number of constituent minerals and significant differences in their physical and chemical properties, which seriously affects the VERTICAL ROLLER MILL TECHNICAL DETAILS ResearchGate2018年10月1日 The impact of ore variability on process performance was observed at the OK Tedi mine in Papua New Guinea, where the variations in feed ore hardness (Bond work index 5–16 kWh/t) and in feed size distributions caused the SAG mill throughput to fluctuate between 700 and 3000 t/h (Sloan et al, 2001)Quantifying variability of ore breakage by impact ScienceDirect