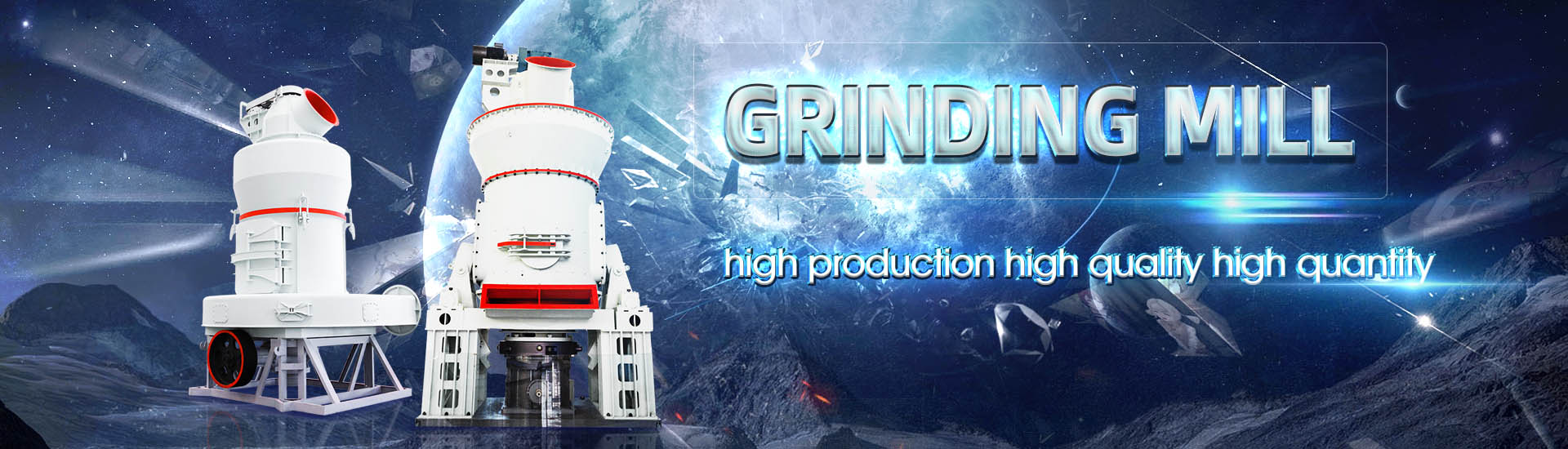
Finegrained coal raw coal mill
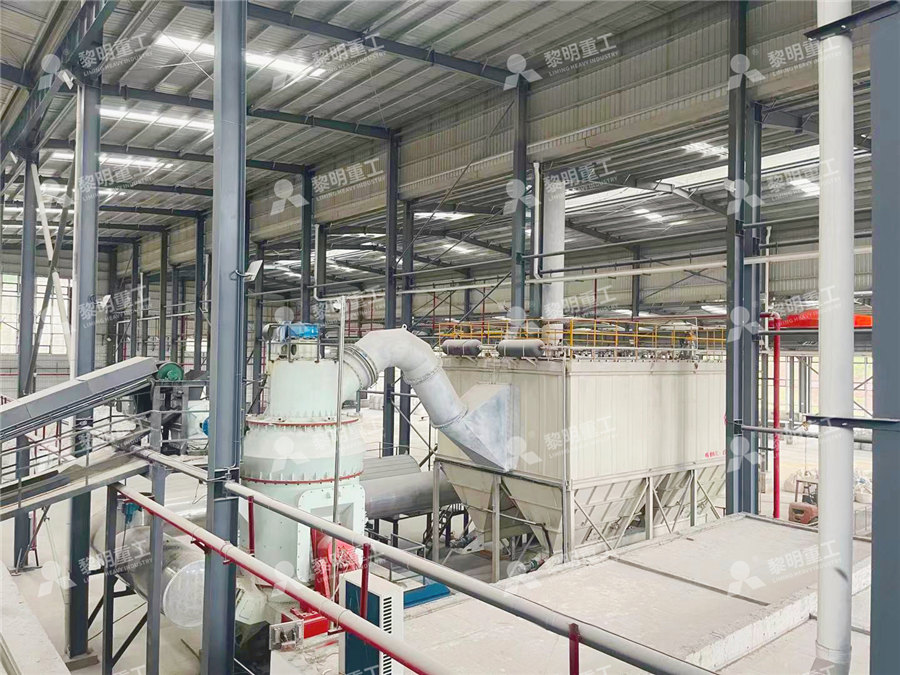
Coal Mill an overview ScienceDirect Topics
Mills are mechanical devices used to break different types of solid materials in small pieces by grinding, crushing or cutting In pulverised coalfired power plants, a pulveriser coal mill grinds 2021年8月11日 Rational combinations of research methods make it possible to develop optimal parameters for briquetting finegrained coal waste and obtain efficient fuel composites The Technological Aspects of Obtaining Fuel Composites Based on 2020年12月10日 Several techniques in the mineral processing sector have been explored to beneficiate the coal fines and ultrafines The explored beneficiating technologies include Recent developments in beneficiation of fine and ultrafine coal 2021年6月25日 This paper presents the results of studies on the briquetting of finegrained coal raw materials with environmentally friendly binders The following coal products were used as Briquetting of Fine Coal Raw Materials with Binders
.jpg)
Occurrence Characteristics of FineGrained Pyrite in Coal and Its
2022年11月14日 ABSTRACT: To explore the occurrence and distribution characteristics of finegrained pyrites in coal and the efect of pyrite particle size on flotation eficiency, coal samples 2019年12月29日 This paper presents the partial results of a study on obtaining compacted fuel from finegrained coal fractions and biomass The aim of the study was to determine the impact of selected parameters of the extrusion Research on the Production of Composite Fuel on the Significant amounts of coal waste (anthracite fines, small coke and coal, and coal slimes) have been accumulated in coalindustrial regions The reserves of finegrained coal materials are Briquetting of Fine Coal Raw Materials with Binders国内研究主要为实用概率筛分模型,潮湿细粒物料在筛面上积聚原因和黏附机理及黏附力、黏附厚度的影响因素,克服潮湿细粒原煤深度筛分堵孔、黏孔现象的设计方案,采用筛板振动、筛箱不振 细粒煤干法深度筛分技术进展及研究方向【维普期刊
.jpg)
Coal Mill an overview ScienceDirect Topics
A simple energy balance model of the coal mill is derived in (Odgaard and Mataji 2006), this model is based on a more detailed model found in (Rees and Fan 2003)In this model the coal mill is seen as one body with the mass m mThe following variables are defined: T(t) is the temperature in the coal dust flow in the mill, ṁ PA (t) is the primary air mass flow, T PA (t) is 2021年6月25日 This paper presents the results of studies on the briquetting of finegrained coal raw materials with environmentally friendly binders The following coal products were used as test materials: anthracite fines and coal slime from coal preparation plants in the Rostov oblast Table 1 summarizes the characteristics of the coal raw materialsBriquetting of Fine Coal Raw Materials with Binders2016年5月11日 Finegrained pyrite in some Chinese coals has been investigated, with analysis by optical microscopy and a scanning electron microscope equipped with energy dispersive Xray spectrometer Finegrained pyrite in some Chinese coals ResearchGate2012年11月17日 20 131Fineness Fineness is an indicator of the quality of the pulverizer action Specifically, fineness is a measurement of the percentage of a coal sample that passes through a set of test sieves usually designated at 50, 100, and 200 mesh A 70% coal sample passing through a 200 mesh screen indicates optimum mill performance The mill wear and Coal mill pulverizer in thermal power plants PPT SlideShare
.jpg)
CANNEL COAL ORIGIN, RECOGNITION, DISTRIBUTION AND USE
bases or tops of coal seams and in most cases are thin and of limited extent Recognition and Diagnostic Features Differentiation and classification of fine grained coals requires sophisticated geoTo convert raw coal into fine coal powder, coal grinding mills are essential Coal grinding mills are specialized equipment designed to break down coal into fine particles suitable for combustion The coal grinding process involves crushing and grinding coal into small particles, which are then heated to high temperatures in a furnace, producing steam that drives a turbine to generate What is a Coal Grinding MillYou will be surprised about what has gone wrong with fire and explosion protection of your system(s) Be sure about that! Evaluation of a coal grinding system’s fire and explosion protection, including the raw coal storage and the fine coal silo storage normally can be done in one day, mostly without having to stop coal grindingBest Practices and Precautions Coal Mill Safety, Explosion and O2 + CO Percent at bag filter outlet and in fine coal bins Bag filter hopper and fine coal bin temperature (0 C) Elements of Coal Grinding System: Mill Feeding: Consists of following activities Coal Crusher: Generally, require when ball mill is used for grinding and raw coal size is on higher side(>25mm)Coal Grinding Cement Plant Optimization
.jpg)
Coal Mill Safety: A Critical Aspect of Power Plant Operations Coal
You will be surprised about what has gone wrong with fire and explosion protection of your system(s) Be sure about that! Evaluation of a coal grinding system’s fire and explosion protection, including the raw coal storage and the fine coal silo storage normally can be done in one day, mostly without having to stop coal grindingThe ball mill is a traditional coal pulverizer machine, which has been widely used since it was invented In the cement plant, the new dry process cement manufacturing requires the moisture content of coal powder to be 05% ~ 15%, while that of raw coal is 15% ~ 40%Coal Mill in Cement PlantYou will be surprised about what has gone wrong with fire and explosion protection of your system(s) Be sure about that! Evaluation of a coal grinding system’s fire and explosion protection, including the raw coal storage and the fine coal silo storage normally can be done in one day, mostly without having to stop coal grindingOptimisation of coal mill systems, with fire and explosion Coal mill is an important component of the thermal power pla nt It is used to grind and dry the moisturized raw coal and transport the pulverized coal ± air mixture to the boiler Poor dynamic performance of coal mill will lead to decrease in the overall efficiency of the power plant, slow load take up rate and fr equent shut downModeling and Control of Coal Mill
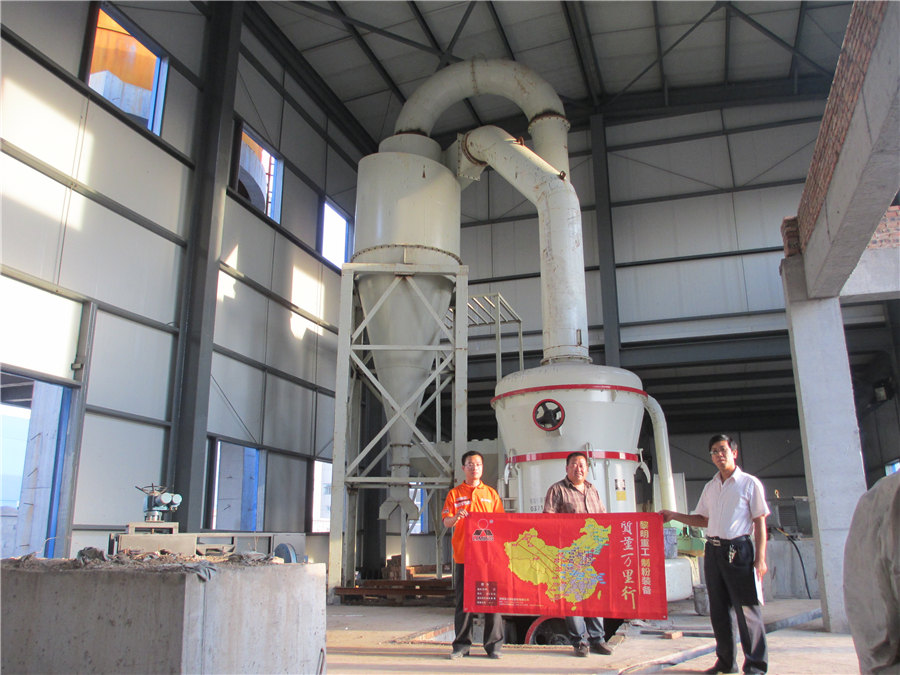
The Use of Granulation to Reduce Dusting and Manage of Fine Coal
Granulation of brown coal dust and finegrained brown coal is usually carried out at the place of production of these wastes – on the mining and processing plants Most often granulating materials are [Naumov et al 2013]: • grained coal with the addition of biomass Then coal and lignite dust as well as coking dust,2019年12月29日 Raw materials used in the research were: Finegrained coal (flotation concentrates), biomass (hydrolytic lignocellulose), and a wide spectrum of organic and mineral binders and their compositionsResearch on the Production of Composite Fuel on the Basis of Fine Our ATOX® Coal Mill has large rollers with great grinding capability of virtually all types of raw coal The rollers work harmoniously with a highlyefficient separator and feed sluice to consistently and reliably deliver coal meal to your desired fineness and moisture levelATOX® Coal Mill FLSmidth Cement2020年4月7日 Because the amount of raw coal and coal powder stored in the mill c annot be measured, there is no a ctual reference data in the model identification process So, t he dynamic characteristic of rawModeling of Coal Mill System Used for Fault Simulation
.jpg)
coal grinding machine CHAENG
Vertical Coal Mill is specially used for ultrafine grinding of raw coal and bituminous coal materials in cement, power plants, iron and steel plants and other fields The GRMC coal vertical mill produced by CHAENG adopts special structural design and production process, which is energysaving and environmentally friendly2014年10月1日 The amenability of beneficiating a fine hard coal from HwaSun coal mine using column flotation has been studied using a CoalPro flotation column developed by Canadian Process Technologies (CPT) After initial testwork using a batch flotation cell to determine the optimal flotation conditions, tests were carried out to compare its performance with the columnFine coal beneficiation by column flotation ScienceDirectYou will be surprised about what has gone wrong with fire and explosion protection of your system(s) Be sure about that! Evaluation of a coal grinding system’s fire and explosion protection, including the raw coal storage and the fine coal silo storage normally can be done in one day, mostly without having to stop coal grindingSafe operation of coal grinding systems: Raw coal yard 2019年12月29日 This paper presents the partial results of a study on obtaining compacted fuel from finegrained coal fractions and biomass The aim of the study was to determine the impact of selected parameters of the extrusion process and the applied binder (mechanical durability and density of the products) The fuels were formulated using the extrusion process Raw materials Research on the Production of Composite Fuel on the Basis of Fine
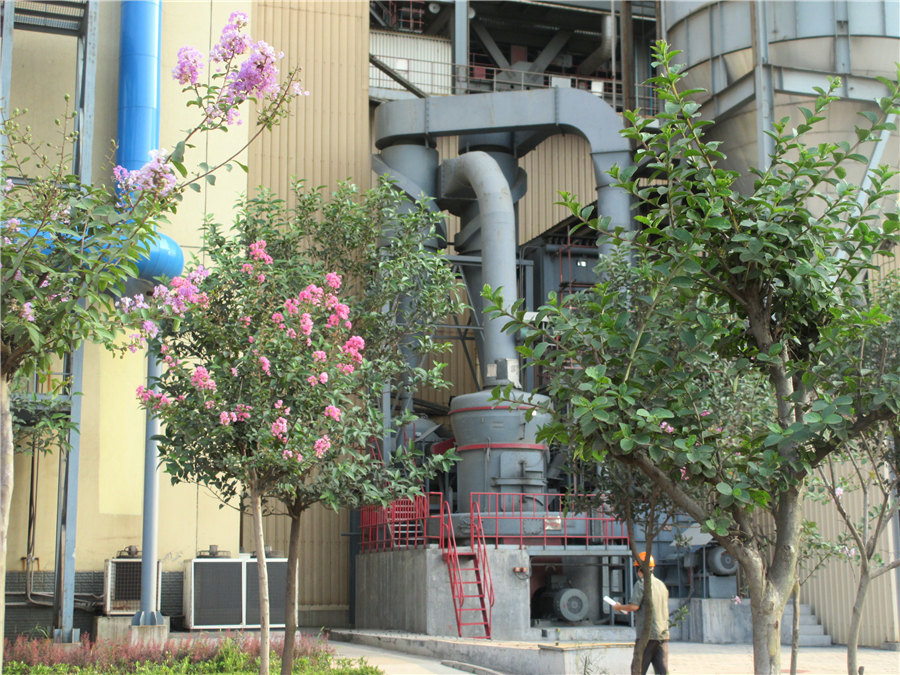
Vertical Grinding Mill (Coal Pulverizer) Explained
Introduction This article concerns itself with vertical grinding mills used for coal pulverization only (coal pulverizers), although vertical grinding mills can and are used for other purposes The 3D model in the saVRee database represents a Analysis of fine LRC properties (a) raw coal samples, (b) particle size composition analysis, (c) phase composition analysis, (d) analysis of raw coal functional groups As shown in Fig 1 (a) and (b), the fine LRC samples have uneven distribution of each narrow particle size, mainly 025–0125 mm which is favorable for flotation, and its content accounts for 5097 % of the Sustainable strategy for highefficiency flotation of fine lowrank 2018年10月1日 Request PDF Preparation of granules made of finegrained coal fractions for gasification process The paper presents the results of tests for the production of fuel granules from finegrained Preparation of granules made of finegrained coal fractions for – Interruptions in raw coal feed – Lower feeder speeds – This occurs because a minimum airflow through the coal mill must be maintained to insure that burner line velocities are not too low to allow settling of coal in the fuel lines or burner components – Not uncommon to achieve air to fuel ratios of 3 to 5 pounds of air per pound Mill Inerting and Pulverizer/Mill Explosion Mitigation
.jpg)
Study on fluidization characteristics and drying characteristics of
2023年1月15日 Contrarily, the drying time of finegrained coal decreases and then increase with the increase of vibration amplitude Under the conditions of N = 14, f = 20 Hz, A [22] has studied the transmission of water in raw coal and its influence on the separation effect in the vibrating fluidized bed separation process2024年8月1日 (Xie et al, 2015) conducted experiments with a laboratory roller mill to investigate the effects of operating parameters such as loading force, table revolution rate, and fractional filling on the performance of the mill and found that a higher loading force, a higher revolution rate, and a lower fractional filling reduced product size and promoted the production of fine coalExperimental investigation on the preparation of macroscopic 0–1 2020年4月2日 process the raw coal to becom e as pul verise fuel before enter to primary air flow carries th e fine coal to the burn ers, Coal mill motor power (kW) 0 4171 4548 4390 4586 Analysis of the Coal Milling Operations to the Boiler Parametersfunctions to grind the raw coal to become pulverised fuel Besides that, mill system to ensure the continuously supply pulverised coal to the firing system of the boiler Each milling circuit is independent and includes: 1 Single bunker of raw coal storage with maximum 608 tonne capacity 2 Single raw coal feeders at maximum flow rate 70 t/hAnalysis of the Coal Milling Operations to the Boiler Parameters
.jpg)
A Study on 500 MW Coal Fired Boiler Unit’s Bowl Mill
High volatile coals with less fixed carbon require less fine pulverization High volatile coals require a fineness of about 60% passing through 200 mesh For low volatile coals, 15 Mill Wear and Ash Content in Raw Coal The coal is abrasive in nature due to the presence of hard materials like pyrites, α quartz etc, Coal dust explosions are among the severe hazards in industries using coal, posing significant risks to personnel and infrastructure These explosions occur when fine coal particles become airborne and come into contact with a heat source in an enclosed environment, leading to a rapid combustion event Given the catastrophic potential of such incidents, robust measures for coal Coal Dust Explosion Protection: Ensuring Safety in industries using Download Citation On May 1, 2021, N I Buravchuk and others published Briquetting of Fine Coal Raw Materials with Binders Find, read and cite all the research you need on ResearchGateBriquetting of Fine Coal Raw Materials with Binders ResearchGate2023年5月15日 However, the separation effect of finegrained coal in compound dry separation bed is poor, especially the separation of −3mm fine particles is ineffective, while they are important for promoting the separation of +6 mm materials However, the study on the separation effect mechanism of this part of fine coal particles is still blankEffect of 3–0 mm fine coal migration characteristics on high sulfur
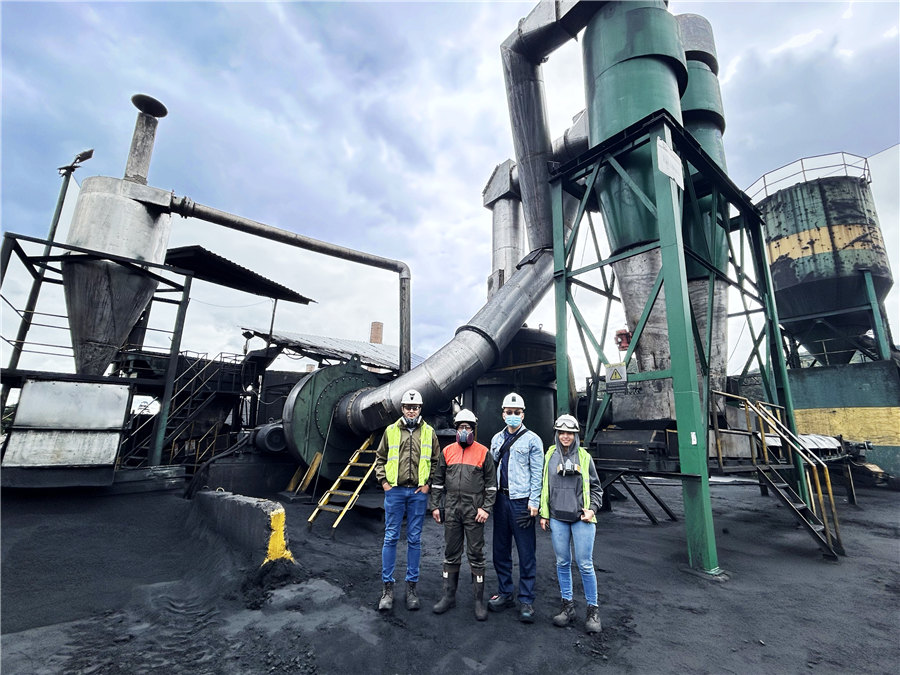
Finegrained object detection method using attention
2021年9月1日 Request PDF Finegrained object detection method using attention mechanism and its application in coalgangue detection Although the performance of object detectors is constantly improving 2024年1月11日 With a ball mill 1 To pulverize crushed coals in a ball mill, you start by feeding the mill with crushed coal Then the grinding media crushes and grinds the coal in the rotating chamber 2 Airflow carries the pulverized coal out of the ball mill 3 Next, you'll need to use the mill classifier to separate the fine coal particles from the airflowHow to Process Coal into Pulverized Coal in 5 Steps?When it is working, the raw material is loaded into the mill through the feeding equipment, and the hot air enters the mill through the air inlet pipe , coal and hot air exchange heat in the mill, the coal is crushed and ground in the mill, while the coal is crushed, the pulverized coal powder and gas are taken out together by the special induced draft fan through the discharge device of the Air Swept Coal Mill Cement Plant Machinery2022年11月11日 However, finegrained pyrites (smaller than 60 μm) are difficult to separate by the flotation method 15−17 On the one hand, the formed foam of the mixture of finegrained pyrite and coal particles during the flotation process has strong stability and low fluidity, making the pyrite difficult to separate from coal 16 On the other hand, the finegrained pyrite can form Occurrence Characteristics of FineGrained Pyrite in Coal and Its
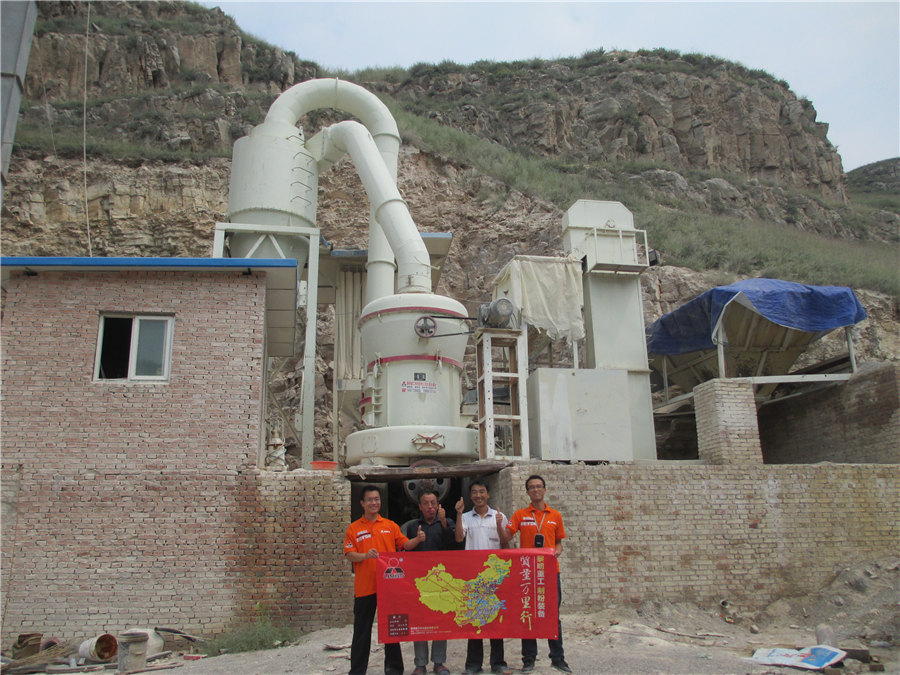
Ultrafine coal grinding and ultraclean coal preparation
2005年4月1日 The coal of low ash tail grinding removal of slime flotation experiment shows that the clean coal yield is 3547% and for complete comprehensive clean coal yield is up by 5420% compared to raw THE ISSUE OF COAL SLUDGE AND FINE COAL GRANULATION Granulation of brown coal dust and finegrained brown coal is usually carried out at the place of production of these wastes – on the mining and processing plants Most often granulating materials are [Naumov et al 2013]: • grained coal with the addition of biomassThe Use of Granulation to Reduce Dusting and Manage of Fine Coal2024年8月1日 The vertical spindle mill (VSM) is the key equipment to realize the preparation of 0–1 mm fuel used in powderedcoalfired circulating fluidized bed combustion technology (PCCFB) In this paper, a pilotscale VSM test system was set up to explore the feasibility and operating performance of coarsegrained pulverized coal preparation The effects of loading Experimental investigation on the preparation of macroscopic 0–1 2013年7月4日 Finegrained waste generated in the processing plant of a coalprocessing plant in eastern Poland (Lublin Coal Basin) was used to obtain briquettes using the roll press briquetting methodUtilization of Fine Coal Waste as a Fuel Briquettes ResearchGate