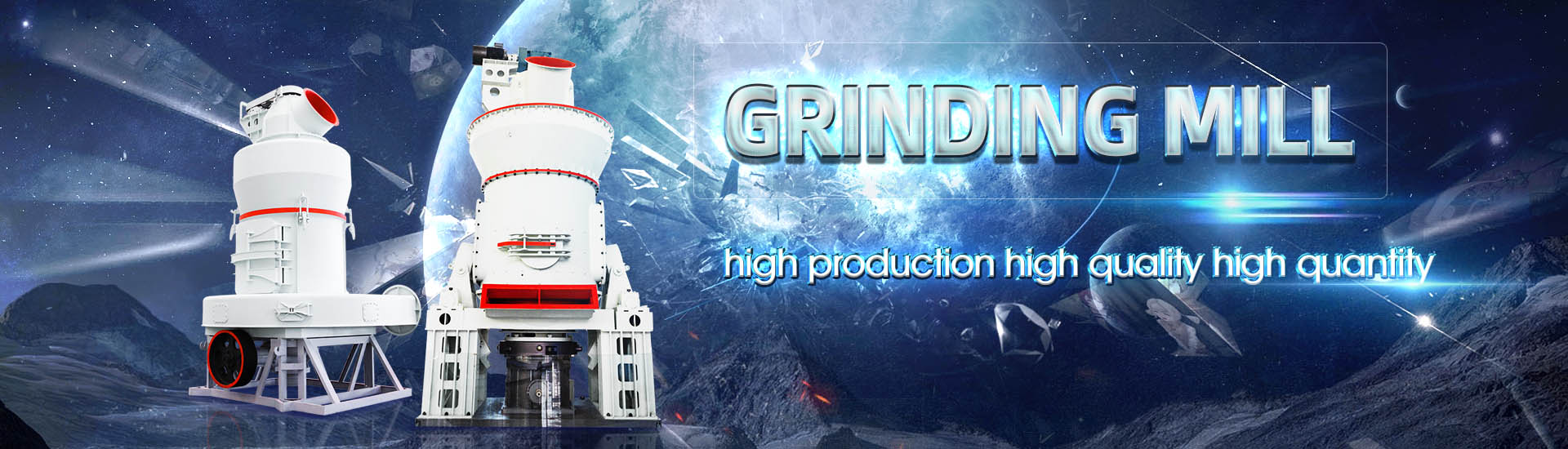
How much does a water slag iron powder making process cost
.jpg)
Optimal hot metal desulphurisation slag considering
2021年2月21日 The largest costs during the HMD process are the iron losses, iron that is skimmed off together with the slag Depending on the heat size, typically 500–4000 kg iron (05–25 wt% of the total iron) is skimmed off per 2019年10月29日 Proper management on the iron and steelmaking slag is highly demanded due to the high cost of direct disposal of the slag to landfill, which is the most adopted management approach In this article, the potential The potential utilization of slag generated from iron2005年2月1日 Environmental concerns and economic realities demand that slag production in iron and steelmaking processes can be reduced and that slag can be effectively utilized Discover the world's(PDF) Industrial uses of slag The use and reuse of iron 2023年5月15日 Steel slag is the main solid waste generated in the steelmaking process, accounting for 15 to 20% of crude steel output [1] China's crude steel output in 2021 was Comprehensive utilization of steel slag: A review ScienceDirect

The recycling and reuse of steelmaking slags — A review
2019年7月1日 Large volumes of slags are formed as byproducts during the refinement of pig iron by basic oxygen steelmaking or electric arc furnace steelmaking In order to lower the 2023年11月20日 The product can be more economical if the steel slag is reused for iron making However, the scientific community has not explored steel slag as a charge flux for iron making The recycling technique of steel slag can be A Review on Environmental Concerns and 2023年7月21日 The method has a strong processing ability and good quality of water quenched slag into slag, but due to its complex process, high electricity consumption and maintenance Comprehensive utilisation of blast furnace slag Taylor Francis 2011年10月27日 A flux, such a fluorspar (calcium fluoride) can be added to accelerate slag formation but increases the cost of the process Volume stability The final slag can have a lime/silica ratio of about 3 or 4, although this can vary substantially from one heat to the nextBasics of slag production Article on the slag industry from Global Slag
.jpg)
Iron and Steel Slag Utilization: A Comprehensive Analysis
This process is much quicker and requires a small area relatively • ISC process: The molten slag is poured into a steel box in which it solidifies and then subjected to water sprinkling and immersion cooling • Rapid cooling process: The molten slag is poured into a special drum in which it is cooled rapidly by sprinkling water over the slagHot dip galvanizing is the process of coating iron or steel with a layer of zinc by immersing the metal in a bath of molten zinc at a temperature of around 450 °C (842 °F) During the process, a metallurgically bonded coating is formed which protects the steel from harsh environments, whether they be external []Galvanizing process2022年2月26日 Blast furnace slag can be processed into the following materials by various processes In China, blast furnace slag is usually processed into water slag, slag gravel, expanded slag and slag beadsWater slag is the process of putting the hotmelt blast furnace slag into water for rapid cooling, which mainly includes slag pool water quenching or furnace front What is Blast Furnace Slag and How to Process It?2005年2月1日 Steelmaking slag, an important metallurgical byproduct, is composed of a large amount of valuable components, including CaO, Fe t O, MnO, and MgO, all of which are required in the steelmaking (PDF) Industrial uses of slag The use and reuse of iron and
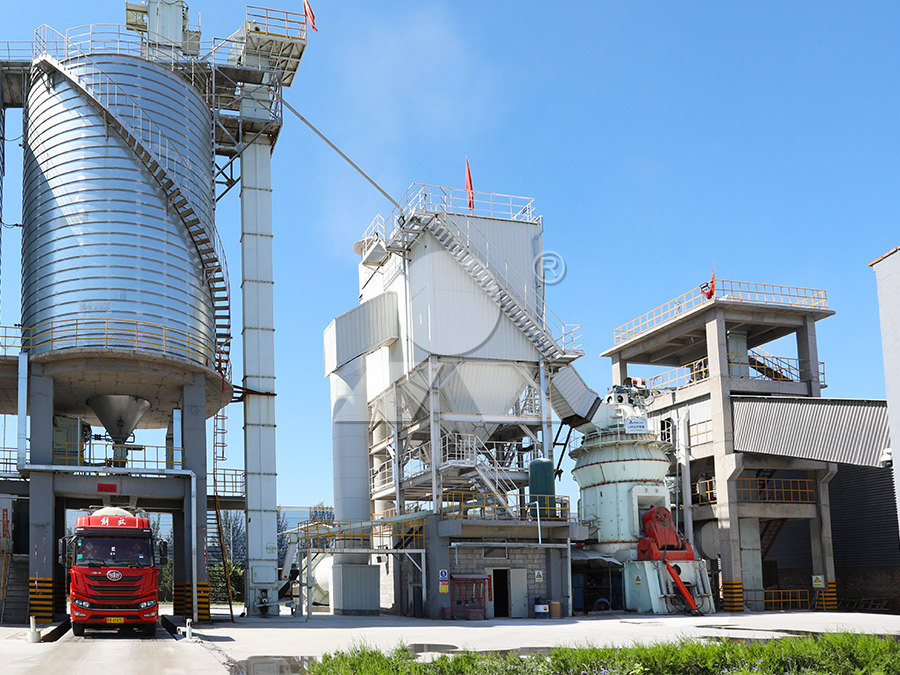
Gold Smelting Refining Process 911Metallurgist
2016年2月29日 Slag appearance is a good indicator of the process Although iron minerals have influence on color slag, it is possible to draw some conclusions according to the color For example, a blue color is symptom of copper minerals The presence of manganese minerals is note for a lavender color slag2020年12月1日 Consequently, recently, a novel synthetic method of a hydroxyapatitezeolite micro composite from BFS reported This process only required cheap chemical reagents, H 3 PO 4 and NaOH, and convenient preparation procedures This conversion process offers novel solutions to waste (Kuwahara et al, 2009)Zeolite synthesis from lowcost materials and environmental 2019年10月29日 Slag is the byproduct of iron and steelmaking processes Normally, around half to one tonne of slag would be generated for yielding one tonne of rolled iron or steel (Lobato et al 2015)It was reported that the world steel production was 19 billion tonnes in 2016, which suggested that at least around 1 billion tonnes of slag is produced during the year (Worldsteel The potential utilization of slag generated from iron and 2020年6月10日 Despite formation of Fe, there are several other processes are involved to complete the ironmaking process Most predominate transformations including MnO to Mn, SiO 2 to Si, removal of sulphur, P 2 O 5 to P and slag formation are noticed 2251 Reduction of MnO It is a multistage process occurring in the blast furnace stack regionIron and SteelMaking Process SpringerLink
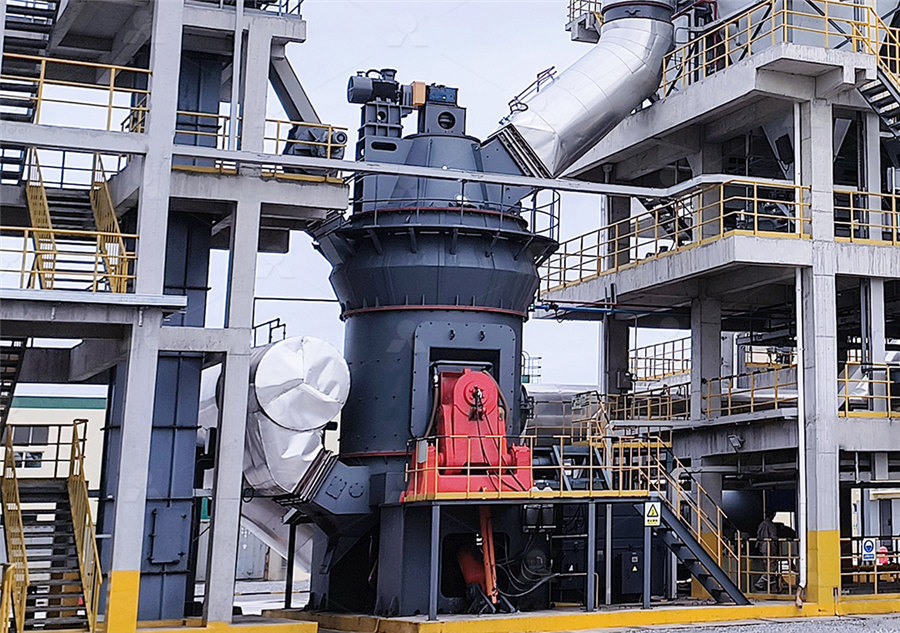
Carbon mineralization of steel and ironmaking slag: Paving the
2024年4月1日 In particular, the annual amounts of iron slag and steel slag globally generated were estimated to be 390 Mt and 290 Mt, respectively, in 2022 Steel and ironmaking slag contain 30–60 wt% of calcium oxide (CaO) and 3–15 wt% of magnesium oxide (MgO), suggesting high CO 2 storage capacities [19]Carbon dioxide sequestration using steel slag—modeling and experimental investigation Smitha Gopinath, Anurag Mehra, in Carbon Dioxide Sequestration in Cementitious Construction Materials, 2018 41 Introduction Steel slag is an industrial waste that is generated during the production of steel In the production of steel, oxides of metal impurities in the iron combine Steel Slag an overview ScienceDirect Topicsiron and steelmaking slag in construction and environmental treatment is facing have been discussed The article was aimed to provide an insight of proper management on iron and steelmaking slag Iron and steelmaking slag Slag is an inevitable byproduct in metal making process Iron slag (slag of blast furnace BF) and steelThe potential utilization of slag generated from ironand The iron ore production has significantly expanded in recent years, owing to increasing steel demands in developing countries However, the content of iron in ore deposits has deteriorated and lowgrade iron ore has been processed Iron Ore Pelletizing Process: An Overview IntechOpen
.jpg)
How to Smelt Iron: The 6 Steps to Iron Smelting The Crucible
Our community came together to smelt twentyfive pounds of iron Every aspect of the smelt was a team effort, from collecting magnetite sand from a local beach, to building the bloomery furnaceAlthough the Romans built furnaces with a pit into which slag could be run off, little change in ironmaking methods occurred until medieval times By the 15th century, many bloomeries used low shaft furnaces with water power to drive the bellows, and the bloom, which might weigh over 100 kilograms, was extracted through the top of the shaft The final version of this kind of bloomery Iron processing Definition, History, Steps, Uses, FactsHow Much Does A Concrete Batching Plant Cost it uses software and transmission signals to monitor and manage the entire production process Highquality equipment ranges from $20,000 to $ sand, slag powder, and additives are key raw materials When procuring these materials, we can compare multiple suppliers to select those offering How Much Does A Concrete Batching Plant Cost AGICO Cement2017年10月17日 Smelting Reduction Figure 2: The smelt reduction vessel (SRV) is the core technology component of the Hismelt process Source: RioTinto While years of ironmaking technology innovations have optimized blast furnace productivity, two alternative processes—smelting reduction and direct iron reduction— are growing in adoption The From Ore to Iron with Smelting and Direct Iron Reduction
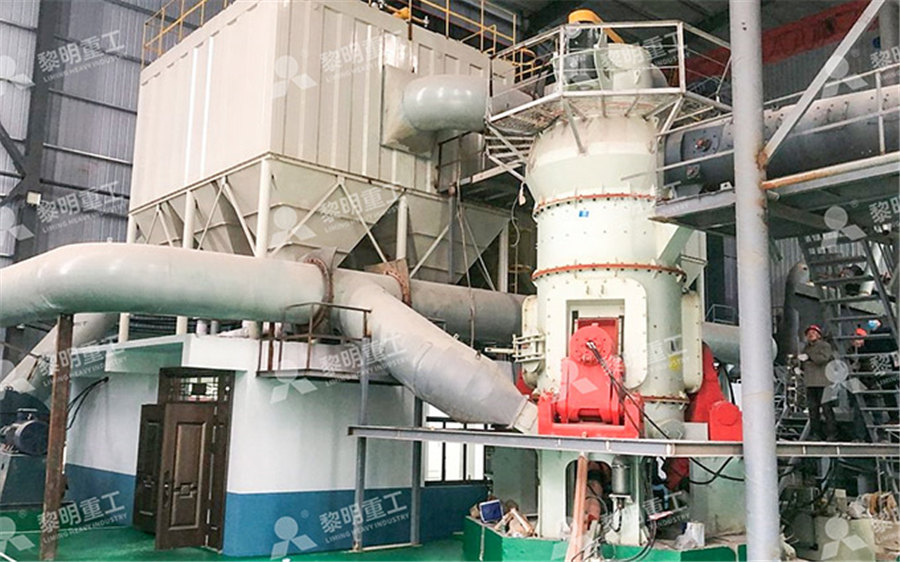
Introduction to slag analysis: How iron is made in a bloomery
2011年11月28日 Iron particles, slag and making the bloom This is where things start to get a bit tricky Killick and Gordon wrote a short but very interesting paper in 1989 that dealt with how ore particles actually get reduced to iron, and perhaps most importantly how that iron actually conglomerates at the base of the furnace22 Properties of iron/steel slag Iron/steel slag is composed mainly of CaO and SiO 2 In addition, blast furnace slag contains Al 2 O 3, MgO, and S, and steelmaking slag contains iron oxides (FeO, Fe 2 O 3), MnO, P 2 O 5, etc Steelmaking slag includes the following: slag produced in the hotmetal pretreatment processes (desiliconization Processing and Reusing Technologies for Steelmaking Slag2023年9月5日 In summary, powder metallurgy is both a technology capable of producing materials with unique properties and a process for manufacturing costeffective, highquality mechanical parts 2 The Process of Powder Metallurgy (1) Powder production This process includes the creation and mixing of the powderPowder Metallurgy: A Comprehensive Guide for Beginners2021年12月20日 The former process electrolyzes iron ore using an alkaline electrolyte as an anode and iron as the cathode precipitation at approximately 110 °C; the latter process dissolves iron ore using molten oxide electrolyte and the temperature is much Hydrogen direct reduction (HDR) in steel industry—An
.jpg)
A Comprehensive Review on the Ground Granulated
2022年7月18日 When the slag from the blast furnace is molten, it is swiftly cooled with strong water jets, which transform it into GGBS, a fine, granular and glassy substance Figure 2 depicts2015年3月2日 BOF process has limiting ability for desulphurization since the slag formed in the BOF is oxidizing (not reducing) therefore maximum value of distribution coefficient of sulphur in the process is about 10, which may be Understanding Steel Making Operations in Basic 2016年8月31日 Process of slag Generation (epagov) During the process of reducing iron ore through coke in a blast furnace, blast furnace slag is generated while steel making slag is generated in the process of Steel Slag Utilization — Overview in Indian Perspective2019年5月23日 The deposit volume of steel slag in China exceeds 400 million tons, leading to the occupation of a large area of land and serious environment pollution However, the current utilization rate of steel slag in China is only about 21%, which is far behind that ofComprehensive Utilization Technology of Steel Slag
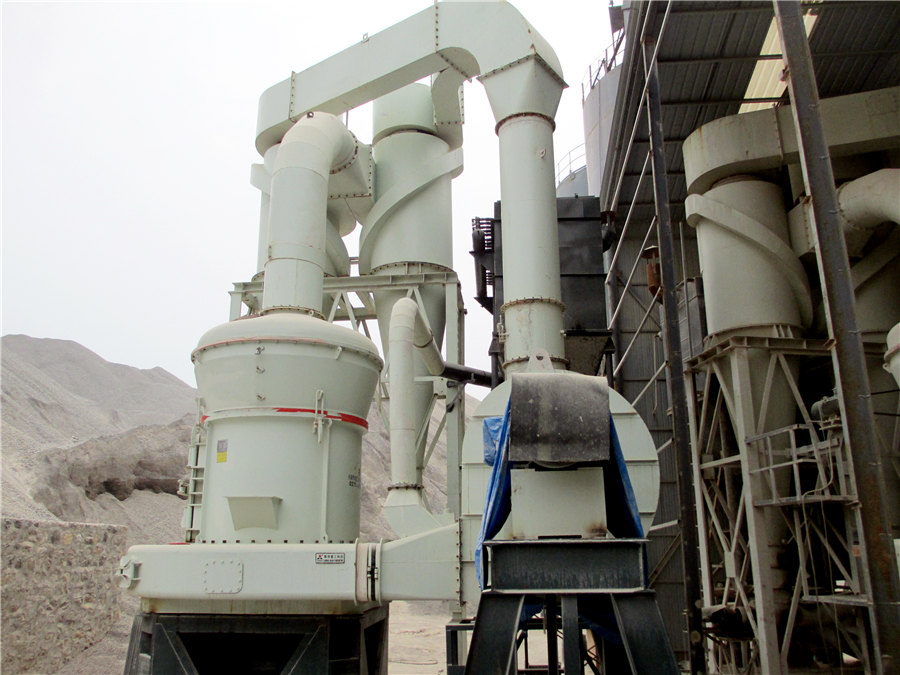
(PDF) Iron and Steel Slags ResearchGate
2017年3月5日 Normalized CaO (MgO)SiO 2 (Na 2 O,K 2 O)Al 2 O 3 (Fe 2 O 3 ) phase diagram for various types of iron and steel slags Acronyms: blast furnace slag (BFS); basic oxygen furnace slag (BOFS 2022年8月17日 How much does it cost to have a trailer sandblasted? The cost to sandblast a trailer depends on the time needed to clean it, typically around two hours So, cleaning a trailer will cost around $80 to $150 for the whole job How much is a sandblaster rental? You can opt to rent sandblasting equipment for a day, which costs about $9 to $15 per daySandblasting Cost Dustless Blasting Cost FixrSlag cement is used in virtually all concrete applications: Concrete pavements Structures and foundations Mass concrete applications, such as dams or retaining walls (SCIC #9, "Reducing Thermal Stress in Mass Concrete") Precast and prestressed concrete (SCIC #16, "Producing Precast and Prestressed Concrete with Slag Cement") Pipe and Block (SCIC #17, "Producing FAQs SCAElectrolysis of water (H 2 O) produces hydrogen and oxygen, whereas electrolysis of aluminium oxide (Al 2 O 3 decarbonising Steelmaking”, 26/04/2021 6 Losses of up to 6% will occur in high voltage transmission, depending on distance process is generated without causing emissions, and that electrode consumption does not lead to CO 2Fact sheet Electrolysis in ironmaking
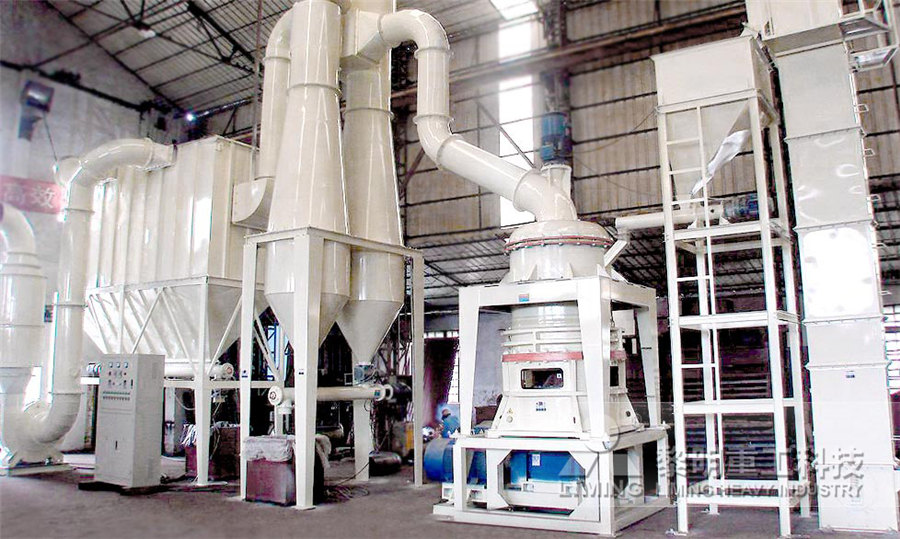
Sustainable and Comprehensive Utilization of Copper Slag: A
2023年4月21日 Annually more than 400 Mt of metallurgical slags are produced worldwide [1,2,3,4,5]From the annual Cu concentrate smelter production capacity, which is equal to around 21 Mt of copper metal in 2021, it can be estimated that more than 45 Mt of CUS were produced from primary sources assuming a slag to copper ratio of 22 [3, 4]Only 15% of the CUS Copper processing is a complicated process that begins with mining of the ore (less than 1% copper) and ends with sheets of 9999% pure copper called cathodes, which will ultimately be made into products for everyday useThe Copper Mining and Processing: Processing Copper 2017年3月22日 Powder injection: This process is similar to HMD injection processes CaO, CaC 2 and CaSi (sometimes in combination with Al) are used as reagents Sulphur concentrations below 0002% can be reached for Alkilled Sulphur removal in ironmaking and oxygen 2013年4月12日 Fig 3 Steelmaking slag Aging treatment Since the flux added to refine the steel forms a component of the steelmaking slag It is particular significance that CaO and MgO contained in the flux remain partly inactive Steelmaking Slag IspatGuru
CFB石灰石脱硫剂制备64.jpg)
Comprehensive utilisation of blast furnace slag Taylor Francis
2023年7月21日 Introduction China is the world's largest steel producer, with the China Iron and Steel Association estimating that the country's crude steel production in 2022 will be 935 million tonnes [Citation 1]Steel slag mainly refers to the blast furnace slag and converter slag produced in the process of iron making and steel making, and with the increase of steel production, the Direct reduction processes can be divided roughly into two categories: gasbased and coalbased In both cases, the objective of the process is to remove the oxygen contained in various forms of iron ore (sized ore, concentrates, pellets, mill scale, furnace dust, etc) in order to convert the ore to metallic iron, without melting it (below 1,200 °C (2,190 °F))Direct reduced iron WikipediaSlag processing George C Wang, in The Utilization of Slag in Civil Infrastructure Construction, 2016 53 Blast furnace slag processing Iron blast furnace slag results from the fusion of iron ore, fluxing materials, and coke; the reduction reactions; and the separation of iron from the ore As indicated in Chapter 2, the term blast furnace slag is used often to refer to iron blast furnace Blast Furnace Slag an overview ScienceDirect TopicsChoosing powder metallurgy materials means you must consider a handful of different factors, including desired part performance, market availability, and more While all of these factors play a role in the decisionmaking process, many manufacturers only want to ask one question: “How much does it cost?” Cost is an understandably big part of your decision, and it’s best to Powder Metallurgy Cost by Materials Horizon Technology
.jpg)
LECTURE NOTES ON IRON MAKING SUBJECT CODE: PCMT 4307
2 An introduction to modern iron making, R H Tupkary, Khanna Publishers (2004) Course Outcomes After completing this course, the student should be able to: 1 Describe the physical and chemical processes that take place during iron making 2 Analyse the effect of change in process parameters in iron making 32019年1月1日 All content in this area was uploaded by Somnath Kumar on Jan 29, 2019Recent trends in slag management utilization in the steel Chemical Reactions during Cement Manufacturing Process The reactions that take place (after evaporation of free water) between the reactants in the kilning phase of cement making process are as follows: Clay Decomposition: Si 2 Al 2 O 5 (OH) 2 → 2 SiO 2 + Al 2 O 3 + 2 H 2 O (vapor) KAlSi3O8 (orthoclase) + 05 SO 2 + 025 O 2 → 3 SiO 2 + 0 How Cement is Made Cement Manufacturing Process