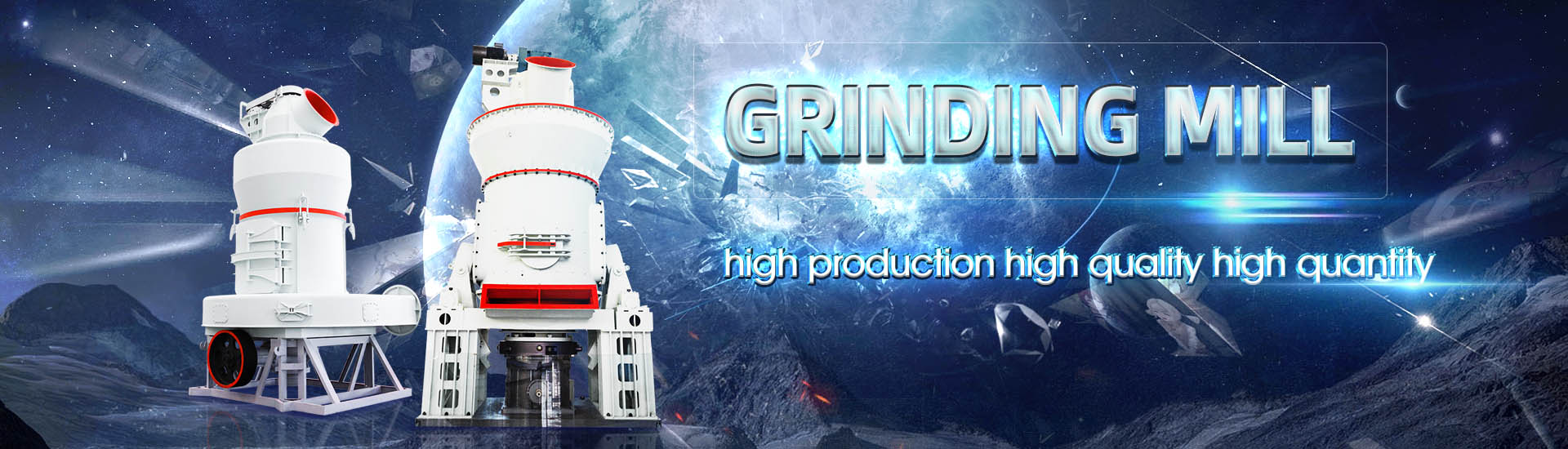
Daily 2500 clinker production line raw material vertical mill
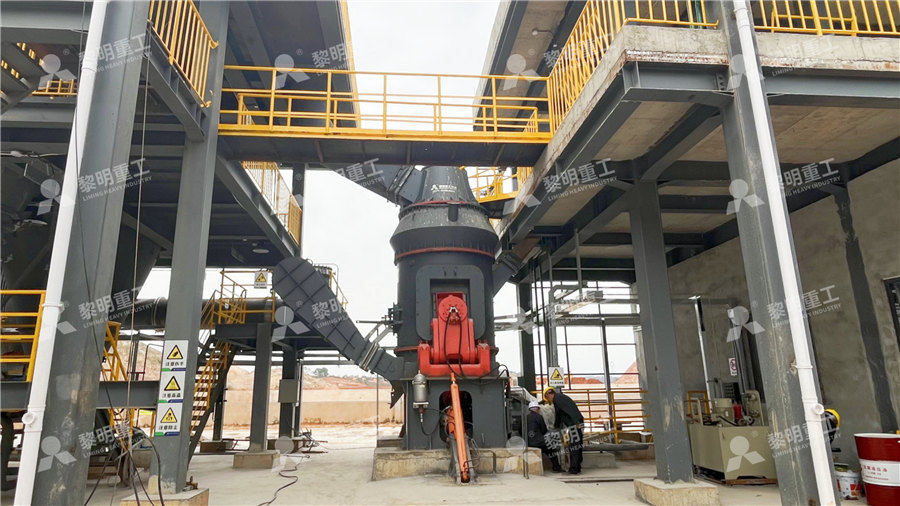
2500TPD new type dry process cement clinker production
In cement production, limestone and clay are used as main raw materials, which are crushed, proportioned and grinded into raw materials by vertical mill, then fed into cement rotary kiln to PENGFEI dry process cement plant avails of MLS3626 vertical grinding mill, designed to produce 2500 tons of cement clinker everyday Its φ4×60m rotary kiln combines preheating and decomposing system and fivestage cyclone preheater2500 Ton Dry Process Cement Plant PENGFEI GroupCompared with traditional cement production line, the 2500 t/d cement plant designed by Chaeng uses lower energy consumption equipment in the main part of energy consumption, such as vertical raw mill, vertical coal mill, vertical 2500 t/d Cement Plant Great Wall2007年9月18日 The Project is undertaken by EKON, a part of PROKONEKON Group of Companies, as an EPC Contract covering the engineering, procurement, construction (civil, Hasanoğlan Cement Factory 2500 Ton/Day Capacity Clinker
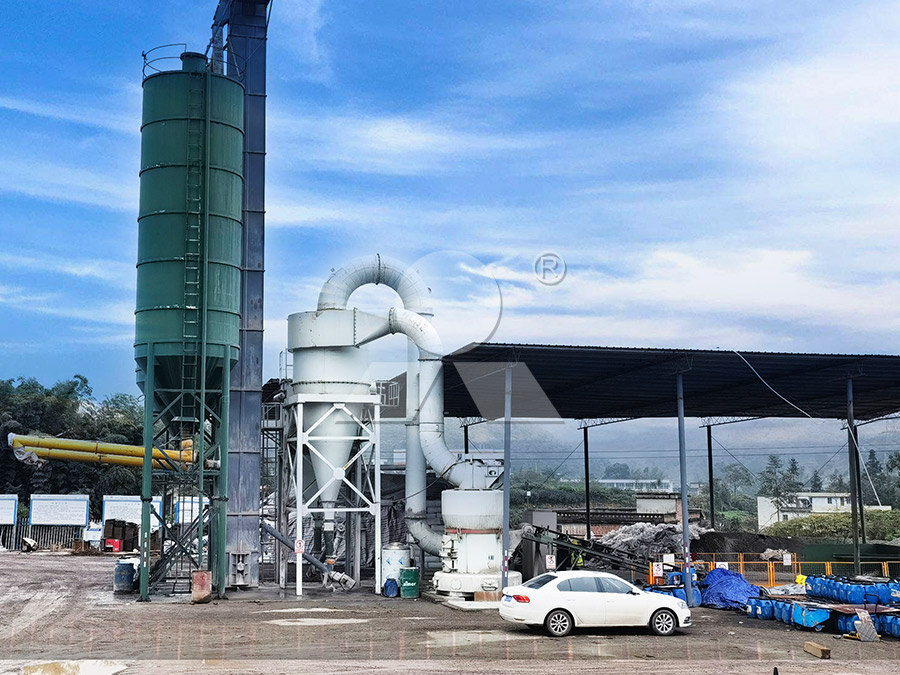
Cement Mill, Clinker Mill – SBCCOCEMENT
The feeding device of the vertical raw mill adopts rotary feeder, which has the advantages of simple airtight structure, stable operation and continuous feeding The wearresistant liner of We can design and manufacture vertical roller mills of diversified specifications and models for raw meal, cement, and slag comminuation systems in cement clinker production lines with capacity up to 10,000t/dVertical Roller Mill (VRM)SinomaLiyang Heavy Vertical roller mills are adopted in 20 cement plants (44 mills) in Japan In the vertical roller mill which is widely used in the raw material grinding process, raw materials input grinding table Vertical roller mill for raw Application p rocess materials//When grinding raw material, cement and granulated blastfurnace slag, what’s the point? Maximum through put and utmost technical availability! This is ensured by the Pfeiffer MVR PFEIFFER MILLS FOR THE CEMENT INDUSTRY
.jpg)
PROCESS OPTIMISATION FOR LOESCHE GRINDING PLANTS
vertical roller grinding mills for grinding: • Coal • Cement raw material • Clinker / granulated slag • Industrial minerals, and • Ores The core elements of these plants are the Loesche vertical Cement production line is the production line composed of a series of cement production equipment, mainly involving crushing, prehomogenization, raw material preparation and homogenization, preheating and decomposition, 2500 t/d : GRMR3841 Vertical Raw Mill : GRMC2031 Vertical Coal Mill : Φ40×60m Rotary KilnCement Production LineVertical roller mill manufacturers Vertical roller mill or VRM is a largescale grinding equipment designed for pulverizing cement raw meal, cement clinker, slag, coal, fly ash, limestone, and other hard grinding materialIt integrates grinding, drying, separation, and conveying in one machine The equipment is widely used in many industries such as cement, electric power, metallurgy VRM In Cement Plant Maximize Energy Saving CNBMSINOMA2021年1月1日 Stacking Reclaiming of Raw material: Swing type stacker Reclaimer: Limestone other raw material are stored in open area into a longitudinal storage unit called stockpile through Stacker These are then extracted transversely from the stockpile through reclaimer: 3: Raw Meal Grinding Homogenization: Grinding Mill Vertical Roller Mill Review on vertical roller mill in cement industry its
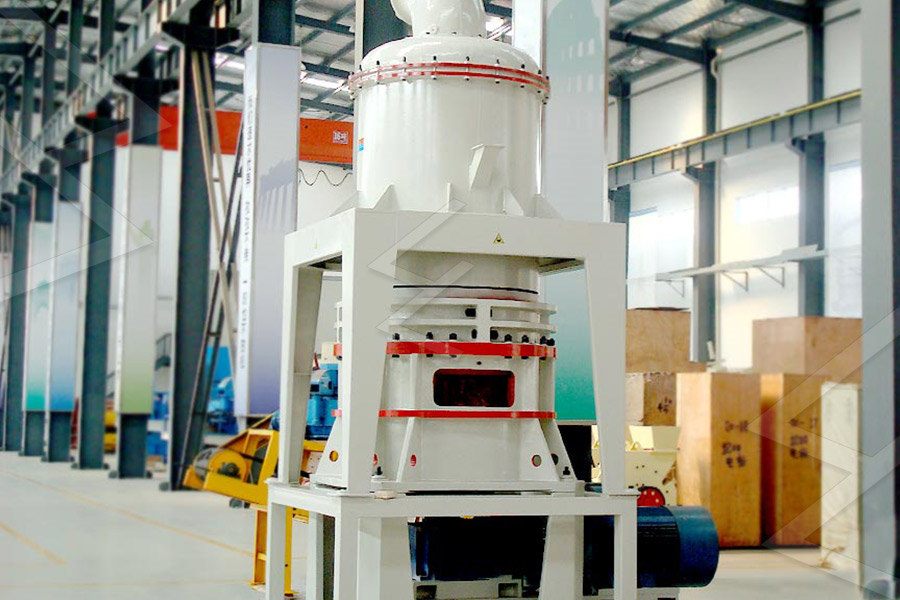
Energysaving and Efficient Vertical Roller Mill Fote Machinery
A vertical roller mill is an energysaving mill that meets market demand Raw materials: Cement raw meal, clinker (such as limestone, gypsum, sandstone, clay, etc) In July 2022, a Vietnamese customer will build a coal powder production line with an annual output of 300,000 tons To meet the needs of customers, We can design and manufacture vertical roller mills of diversified specifications and models for raw meal, cement, and slag comminuation systems in cement clinker production lines with capacity up to 10,000t/d To continuously meet the needs of grinding various materialsVertical Roller Mill (VRM)SinomaLiyang Heavy Machinery Co, LtdApplication of Vertical Roller Mill in Cement Industry Vertical roller mill (VRM) technology has become an integral part of the cement industry, offering several advantages over traditional grinding mills Today, this type of grinding machine is becoming more and more popular in both the raw material grinding process and the cement grinding Application of Vertical Roller Mill in Cement ProductionRaw Material Vertical Roller Mill xinxiang great wall machinery +09 Home; Products A 5000t/d cement production line EPC turnkey project in South Africa adopts GRMR5341 raw material vertical mill of CHAENG 2 Production Line Clinker Grinding Station Cement Grinding Plant Cement Production LineRaw Material Vertical Roller Mill
.jpg)
Raw Material Grinding Facility with Vertical Roller Mill
Raw Material Grinding Facility with Vertical Roller Mill Separator for 3000tpd Clinker Cement Production Line, Find Details and Price about Vertical Roller Mill Vertical Cement Mill from Raw Material Grinding Facility with Vertical Roller Mill Separator for 3000tpd Clinker Cement Production Line Jiangsu Pengfei Group Co, Ltdtion of about 1005 clinker production lines in the raw material preparation process Refer to Figure1for the electricity consumption of the raw material preparation process in differentA Survey and Analysis on Electricity Consumption of Raw Material Mill Mixing: according to the requirement of clinker, compound desired raw material for cement production line Grinding: grinding all materials into required fineness by cement mill Cement ball mill and vertical cement mill are two common types Homogenizing: homogeneous kiln feed is the precondition of clinker production, so homogenization of raw Preparation Of Cement Raw Material Cement Mill, Cement 6 – Control Parameters for Loesche Vertical Mills Variable clocking • 50 / 100 ms: Signal detection • 1 second – 10 minutes: Signal evaluation • Material grindability • Material temperature • Material moisturePROCESS OPTIMISATION FOR LOESCHE GRINDING PLANTS
.jpg)
GreatWall Vertical Mill for raw grinding
2015年4月17日 Vertical Mill for raw grinding is a type of industrial equipment used to crush or grind materials into small particles Vertical roller mills are widely used in the concrete and mining fields, and are also used to process gypsum Vertical cement mill has high grinding efficiency and low power consumption (20% – 30% less than ball mill) The granularity of the feeding material is larger(VRM cement mill is 80mm120mm, cement ball mill is less than or Vertical Cement Mill Cement Clinker Grinding The data discloses a method of collaborative treatment of sludge in cement production, using the existing new dry process cement clinker production line to produce cement clinker and collaborative treatment of sludge, the paper sludge with water content of ≥70% is directly added to the vertical mill, mixed with cement raw materials, grinding Substitution of cement raw materials: How to use paper sludge?Fig2 Schematic process flow of vertical roller mill for grinding of raw materials Vertical roller mills are adopted in 20 cement plants (44 mills) in Japan Table Effect of implementing raw material pregrinder By this production increasing, The clinker quality becomes stable CostVertical roller mill for raw Application p rocess materials

Clinker Production an overview ScienceDirect Topics
A review of the effectiveness of Life Cycle Assessment for gauging environmental impacts from cement production Oluwafemi E Ige, Collins Obiora, in Journal of Cleaner Production, 2021 223 Production of clinker The clinker production stage is where the raw material (the raw meal) converts into clinker The raw meal is fed into a rotary kiln through a preheater at about 1450 Cement Vertical roller mill (VRM) is mainly used to grind cement clinker into fine powder during cement production This vertical cement mill is widely used in the grinding of cement raw meal, cement clinker, slag, raw coal and other raw materialsVertical Cement Mill Great Wall1 Grinding Limestone: The primary function of a vertical raw mill is to grind limestone, the main raw material in cement production, into a fine powder This powder, known as lime, is a key ingredient in the production of clinker 2 Raw Material Preparation: Before being fed into the kiln, raw materials must be ground to a specific particle sizeThe vertical raw mill: A key component in cement productionRaw material ball mill, also called raw meal ball mill, is important grinding equipment in cement production process After being crushed, the raw meal enters the raw material mill The raw meal is grinded into fine powder by the motion and squeezing of steel balls The raw material mill manufactured by Great Wall Machinery can meet the raw material supply of 250~2500t dRaw material mill Great Wall
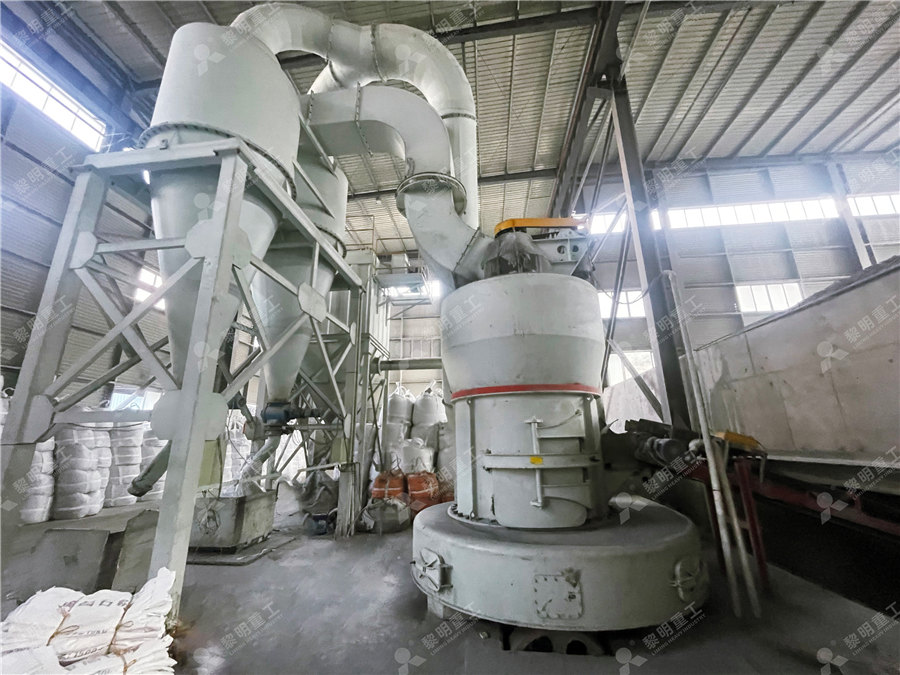
Modeling and simulation of vertical roller mill using population
enter the circuit through two apron feeders The raw materials are crushed in a hammer crusher to D 95 of 80mm The raw materials are mixed in a certain proportion and fed into a vertical roller mill (LOESCHE mill) The vertical roller mill grinds the marital to D 85 of 90µm The ground product is calcined in a preheater to 850900℃GRMK series is mainly used to grind cement clinker into fine powder during cement production,This cement mill widely used in the grinding of raw cement, slag, cement clinker, raw coal and other raw materials GRMSseries GGBS Vertical Roller Mill Great WallWhat Is Cement Vertical Mill The cement vertical mill is a type of grinding equipment that merges fine crushing, drying, grinding, and powder separating into a single, which simplifies the production process and has many irreplaceable Cement Vertical Mill Vertical Grinding MillDominica Clinker Project Vertical roller mill for raw material (LGM4018, 2500t/d) Anhui Fengyang Zhongdu Clinker Project Vertical roller mill for raw material (LGM5426, 6000t/d) Why Choose CITIC HIC's Vertical Roller Mill We have Vertical Roller Mills Cement Processing Equipment
.jpg)
Vertical Cement Mill
Process introduction The GRMK cement vertical roller mill of CHAENG adopts a new generation of cement grinding technology, which integrates grinding, drying and powder selecting functions It can save 30% of power per ton compared with traditional ball mill At the same time, it has many advantages, such as less auxiliary equipment, multiple functions, small occupied area and little LM Series Vertical Roller Mill is used to pulverize materials, material can be pulverized into 80400Mesh with this mill Feed particle size: 070mm Production capacity: 4300 tons / hour Applicable materials: limestone, coal, feldspar, calcite, fluorite, talc, iron ore, copper ore, phosphate rock, graphite, quartz, slag, etc Online Chat InquiryLM Vertical Roller Mill, Vertical Mill ManufacturerCement Kiln In Cement Plant AGICO offers different types of cement kilns from 105000t/d with steady running, high efficiency and large output We adopt the most advanced calcination technology so that the production investment of clinker is small and the income is highClinker Production Clinker Manufacturing Cement 2021年2月24日 Whatever their origin, each sediment is suitable for a beneficial reuse as silicoaluminous raw material for clinker production The characteristics of the raw sediments can lead to specific Optimizing the clinker production by using an automation model in raw
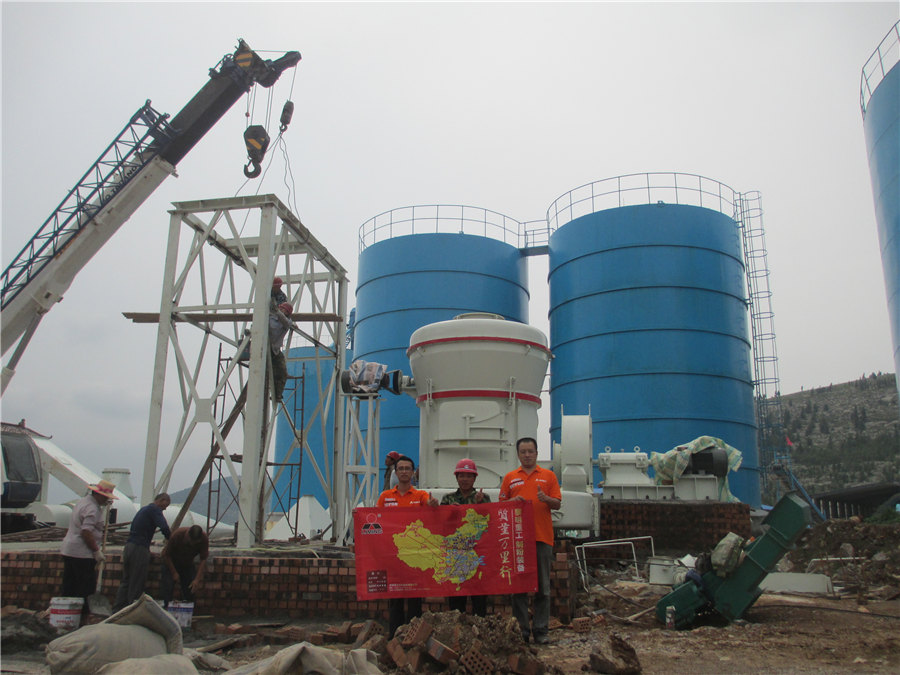
A Survey and Analysis on Electricity Consumption of Raw Material Mill
2021年1月22日 In the whole process of cement production, the electricity consumption of a raw material mill accounts for about 24% of the total Based on the statistics of the electricity consumption of the raw material mill system of 1005 production lines in China between 2014 and 2019, it is found that the average electricity consumption of the raw material preparation 2 Henan Meng Electric Group Cement Co, LTD(Lingchuan branch) 3200 t/d production line Φ42×13m cement mill 3 Sichuan Jiahua Co,LTD 1500t/d cement production line 30×11m twocabin cement mill 4 Xinjiang Hetian Luxin Building Materials Co, LTD 1200t/d cement clinker production line Φ32×13m threecabin superfine grinding millCement Mill Great Wall56 Raw material grinding and waste gas treatment A vertical mill will be used for raw materials grinding Capacity:2500~3000 t/d: 1042: 1: 8500: 8: 2500TPD new type dry process cement clinker production line; Next: No; Related products3000tpd cement production lineJiangsu Pengfei Group Co,LtdVertical Coal Mill, also known as coal mill, for superfine grinding of raw coal, soft coal specifically for cement, power plant, steel mill and other fields Its special design structure and production process creates the higher production Vertical Coal Mill Great Wall
.jpg)
Cement Mill, Clinker Mill – SBCCOCEMENT
Vertical Roller Mill for Cement Raw Material; Cement Mill, Clinker Mill; Slag Mill; Coal Grinding Mill; Ball Mill; ”]We provide various types of Cement Mill, Clinker Mills, which are designed for use in grinding mill production lines with output levels of 2500t/d, 3200t/d The feeding device of the vertical raw mill adopts rotary Our bestinclass OK™ Mill is a globally successful vertical roller mill solution for grinding raw material, cement and slag Its cuttingedge design features consistently deliver the highest quality products with the greatest efficiency It OK™ Raw and Cement Mill2016年5月10日 To stabilize the vertical mill grinding table, we must do a good adjustment of dam height , which is the basis of a vertical mill grinding table, the key of vertical mill normal operation Chaeng will introduce you to describe how to establish stable abrasive bed Material thickness can be adjusted to adjust the height of dam, retaining ring material vertical mill is a How to stabilize the vertical roller mill material dam ring?【Product description】: GGBS (Slag product applications) vertical roller mill is the equipment to grind Ground Granulated Blast furnace Slag (GGBFS) into small particlesGGBS (fineness:42004500cm2/g) produced by vertical roller mills are being used to substitute clinker in conventional cement manufacturing, for which the percentage of GGBS usage is typically at 1015% and 20 GGBS Vertical Roller Mill
.jpg)
Best HLM Vertical Roller Mill Manufacturer and Factory
As the vertical roller mill works, the motor drives the reducer to rotate the dial, the raw material are delivered to the center of the dial from the air lock rotary feeder The material moves to the edge of the dial due to the effect of centrifugal force and than be ground by the force of the roChina vertical cement raw mill supplier, roller mill for cement grinding, clinker grinding mill, mill disc 13005600MM, 2 3 4 roller 11002500MM Email +86592; Home; Products Cement Plant Machinery; Rotary Kiln; Ball Mill; production line TPD: HJRM1320: 1,300:Vertical Cement Raw Mill for Cement, Clinker Grinding2 Raw materials management system – 22 Concrete problems 16 1 Raw materials – 2 Raw mix – 3 Reserves – 4 Crushing – 5 Drying – 6 Preblending – 7 Storage and handling 3 Raw milling and blending 3 Computerised Maintenance Management Systems 30 1 Raw milling – 2 Blending – 3 Kiln feed 4 Flames and fuels 38 1The Cement Plant Operations Handbook International Cement Whether grinding raw coal, clinker, cement and/or slag, we have a VRM solution to suit your grinding needs What’s more, our online condition monitoring services enable you to adopt a proactive maintenance strategy for your OK™ and ATOX® mills that eliminates unexpected downtime and ensures continuous high performanceVertical roller mills FLSmidth Cement
.jpg)
Sustainable Clinker and Cement Production by Using Alternative Fuels
The use of alternative fuels in both combustion and production processes is known as coprocessing in cement manufacturing Waste is now being used to substitute primary fuel sources like coal, petroleum, and gas in the combustion process They are usually from combustible municipal waste, refusederived fuels, biomass, or nonhazardous industrial and commercial