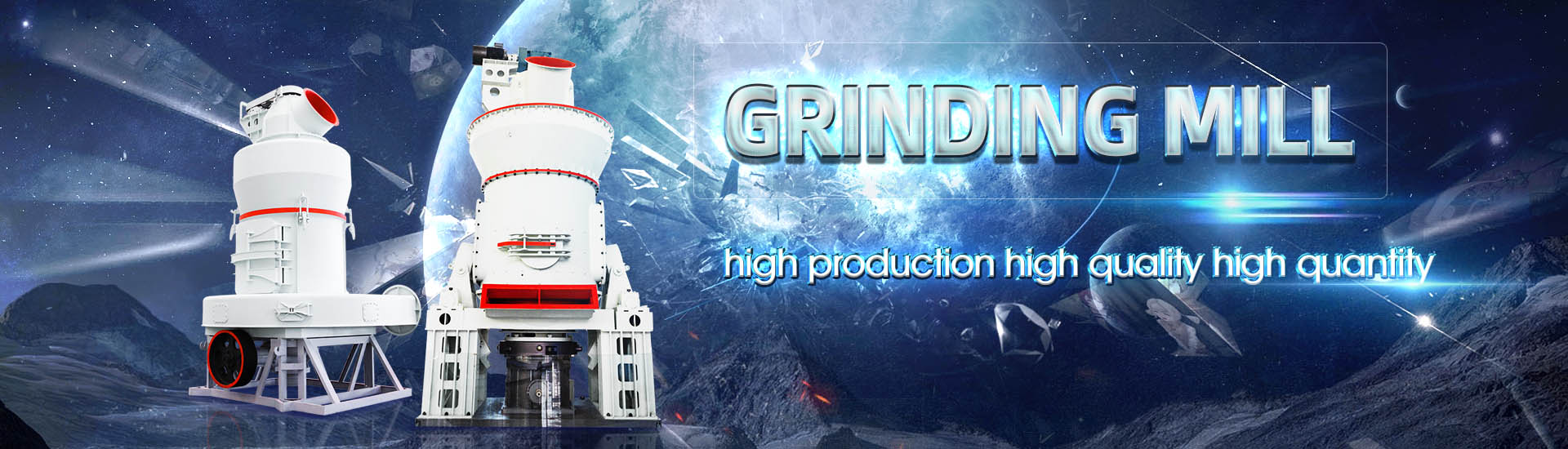
Coalfired grinding equipment
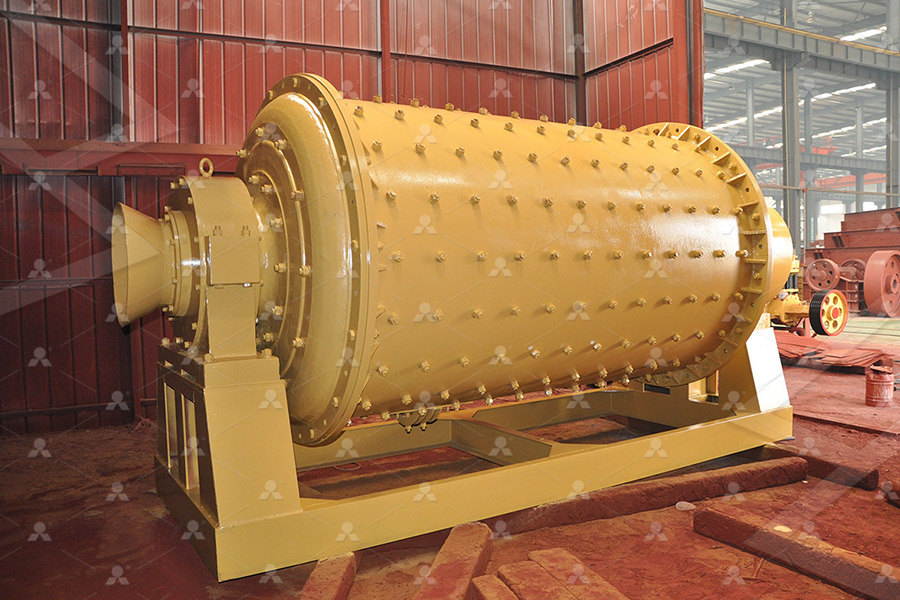
Coal Crushers Coal Pulverizers Mills Williams Crusher
Coal is crushed to desired fineness between spheres or cylindrical rollers After that, air from the boiler is heated to around 330°C (650°F) The raw coal is then fed into the pulverizer where it is ground into fine coal particles 展开From our original E/EL ballandrace type pulverizers for lower capacity applications, to the latest BW Roll Wheel™ pulverizer capable of grinding up to 230,000 pounds of coal per hour (104,300 kg/hr), we set the standard for high Reliable Coal Pulverizers and Mills » Babcock WilcoxPulverization of coal is currently the favored method of preparing coal for burning Mechanically pulverizing coal into a fine powder enables it to be burned like a gas, thus allowing more Coal Pulverizer – Power Plant Pall CorporationVertical Coal Mill is specially used for ultrafine grinding of raw coal and bituminous coal materials in cement, power plants, iron and steel plants and other fields The GRMC coal vertical mill coal grinding machine CHAENG
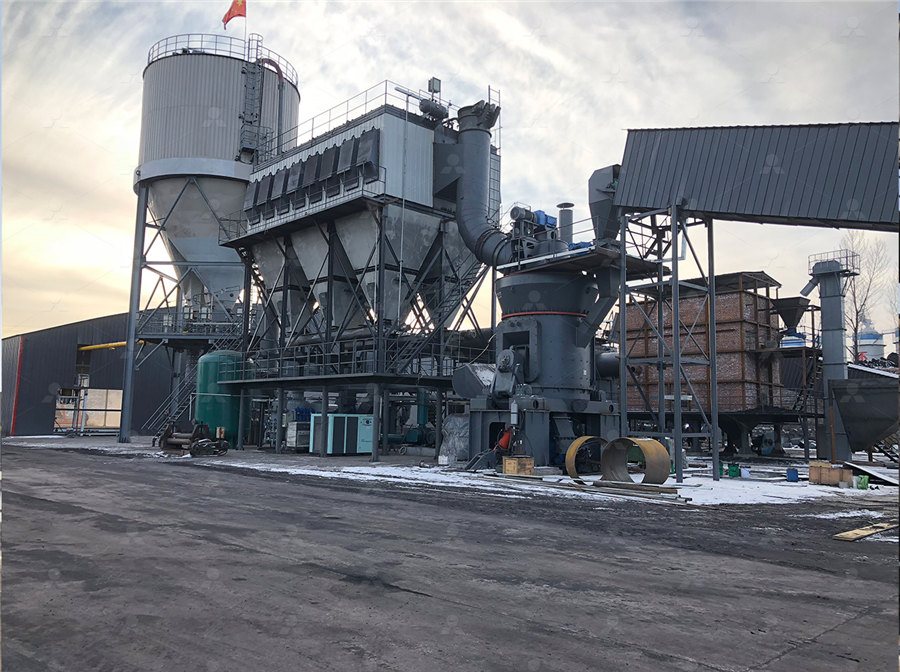
Raymond Bowl Mill designed and built for flexibility Qlar
The Raymond Bowl Mill is considered the finest vertical roller mill available for pulverizing coal The typical Raymond bowl mill system is designed to simultaneously dry, pulverize, and Grinding increases the cross sectional area of the coal and allows it to dry quicker whilst also making it easier to ignite Grinding is often referred to as ' size reduction ' Classifying occurs in order that pulverized coal reaches the Vertical Grinding Mill (Coal Pulverizer) Explained saVReeWe make many types of coal crushing equipment, like our ACC Series Rolling Ring Crusher with capacities ranging from 630–2,350 TPH We also offer hammermills, impactors, double and Coal Crushers, Shredders, Mills for Mining Power IndustriesGlobeCore provides the AVSp100, a cuttingedge coal grinding technology The fine and consistent pulverization of coal by this highperformance equipment greatly boosts output and Coal grinding machine AVSp100 GlobeCore
}@~3SRDG`IA1KP_ICWAA.jpg)
A Comparison of Three Types of Coal Pulverizers Babcock Power
It pulverizes coal by applying hydraulicallyloaded grinding pressure through three grin ding rollers onto a rotating bed of coal Grinding pressure can be adjusted to account for variations Introduction This article concerns itself with vertical grinding mills used for coal pulverization only (coal pulverizers), although vertical grinding mills can and are used for other purposes The 3D model in the saVRee database represents a Vertical Grinding Mill (Coal Pulverizer) ExplainedThe purpose of the coal stockyard is to ensure that there is sufficient coal reserves available to keep the power station in operation should the mine experience production problems Inside the power station, the coal is pulverised to a fine powder in giant grinding mills This is because pulverised coal burns quickly, like gasHOW ELECTRICITY IS PRODUCED AT A COALFIRED POWER 2023年1月1日 Modern coalfired central generating constant for a given size range and is independent of the rate at which material in that size range is fed to the equipment and of the presence Most coal mills are designed around achieving 100% throughput at 50–52 HGI and grinding lowHGI coals can lead to problems regarding their Advances in pulverised fuel technology: understanding coal grinding
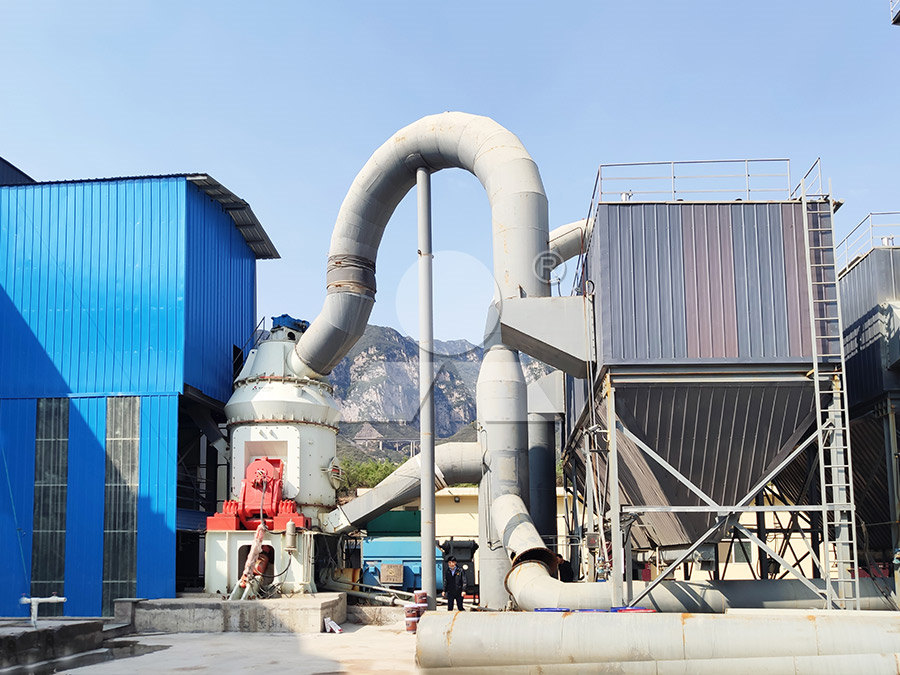
Pulverizers 101: Part I POWER Magazine
2011年8月1日 Pulverizers prepare raw fuel by grinding it to a desired fineness and mixing it with the just the right amount of air before sending the mixture to boiler burners for combustion In Part I of Vertical Coal Mill (VCM) is equipment for grinding and pulverizing coal into micron size Rotary kilns then use the powders as fuel burners The VCM has a housing section equipped with a lining The layout of the coal mill with a rotary classifier2 Babcock Wilcox Figure 1 Typical 455 MWe pulverized coalfired drum boiler — BW Carolinatype Radiant boiler (RBC) (166 bar) cycle drum boilers Examples include the 455 MWe Orlando Developments in Pulverized CoalFired Boiler TechnologyGood practice for industrial coalfired boilers 5 range of 05–50 MWth and examines: pollution control requirements; control technologies; cost implications for industrial energy from coal Currently there is no international best practice for efficient coalfuelled industrial boilers Individual manufacturers ofGood practice for industrial coalfired boilers
.jpg)
Biomasscoal Cofiring Power Plant System with a High Biomass
commonly used in pulverized coalfired boilers Although cogrinding of coal and wood pellet in a mill for cofiring has been adopted at pulverized coalfired boilers domestically, the upper limit for the wood pellet ratio in such cases is only around 5% a primary fuel Industrial coal production is increasing to meet the demand There must be more consideration of coal as it effects equipment design and of equipment as it effects fuel use flexibility Needless to say these work hand in hand, however, boiler and fuel burning equipment design must be based on a primary coal analysisLatest Equipment and Design for New Coal Fired Plants and worldwide As one of the most popular coal pulverizers in the utility industry, the MPS mill was first introduced into the US in the early 1970s Most of the first generation design with a mechanical spring grinding force loading system (Figure 2) are still operating today in coalfired power plantsCoal Pulverizer Design Upgrades to Meet the Demands of Low It pulverizes coal by applying hydraulicallyloaded grinding pressure through three grin ding rollers onto a rotating bed of coal Grinding pressure can be adjusted to account for variations in coal grindability and desired product fineness Raw coal is fed through a centrally located feed pipe to the center of the grinding tableA Comparison of Three Types of Coal Pulverizers Babcock Power
.jpg)
Fly Ash Processing Plant Cement Equipment
It is the main solid waste discharged from coalfired power plants Its annual output is large, which has great harm to the environment and human health And its particle distribution is very uneven, The fly ash ball mill is the special 2020年8月12日 This study shows the performance of a currently running vertical roller coal mill (VRM) in an existing coalfired power plant In a power plant, the coal mill is the critical equipment, whose An investigation of performance characteristics and 2020年8月21日 Although an HGI mill was used as grinding equipment in this study, the actual roller mills used in coalfired power plants are equipped with rotary classifiers The pulverized biomass passes through the classifier with a particle size larger than that of coal due to the difference in terminal velocityEffect of Biomass Carbonization on the Grinding of Coal/Biomass The purpose of coal grinding is to: Increase combustion efficiency: Finely ground coal burns more easily and efficiently than coarse coal, reducing the amount of fuel needed and increasing the operating efficiency of coalfired equipment Reduce dust emissions: Finely ground coal produces less dust than coarse coal, reducing Research on vertical crusher equipment for coal mining and
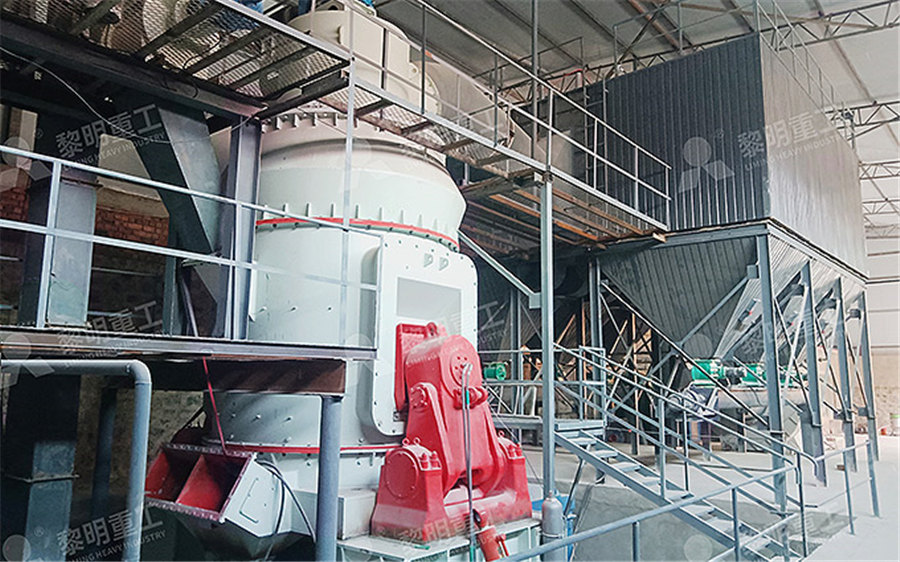
NEW TECHNOLOGIES OF PULVERIZED COAL COMBUSTION
300 mg m3 for brown coals, and higher for bituminous coals) In Russia, a great deal of experience in converting coalfired boilers to natural gas combustion has been accumulated [1] Based on the fuel supply conditions, a partial replacement of coal with alternating or joint combustion of solid and gaseous fuel is implemented in a number of 2020年8月21日 CO2 emissions from coal power generation could be reduced by maximizing the amount of torrefied biomass that can be used in pulverizedcoalfired power plants(PDF) Effect of Biomass Carbonization on the Grinding of CoalHP mediumspeed coal grinder which absorbs the structural characteristics of MPS and MBF coal grinders has the advantages of various grinders Its grinding parts have a long service life and are easy to replace And it is highly adaptable to various coalsVertical Coal Mill Power Generation Equipment Shanghai ElectricOur gravimetric feeders compensate for the variation in bulk density and feed a fixed weight of coal in response to a boiler fuel demand Gravimetric feeders have become the industry standard in coal fired power plants, reducing fuel costs through improved boiler efficiency, shortening downtimes, and reducing NOx emissionsCoal cokefired power plant equipment Qlar
.jpg)
Air Swept Coal Mill Coal Mill In Cement Plant AGICO GROUP
Air Swept Coal Mill Working Principle First, the raw coal is fed into the feed chute by the feeding device Then, the hot air with a temperature of about 300 ℃ enters through the air intake pipe and begins to dry the raw coal while they are falling After 1996年4月10日 Exhaust gas temperature in coalfired power plants can reach approximately 120 °C to 140 °C, with the thermal energy accounting for approximately 3% to 8% of the total input energyDevelopments in Pulverized CoalFired Boiler Besides airswept coal mills, we also provide customers worldwide with slag ball mills, mining mills, cement production lines, cement grinding plants, industrial kilns, and furnaces, grinding equipment, crushing equipment, environmental Air Swept Coal Mill Cement Plant Equipment Coal Biocoal's unique properties allow it to be easily integrated into existing systems for handling storing and grinding coal, without major changes or expensive conversion to equipment Biocoal pellets are water resistant, allowing them to Biocoal Airex Energy
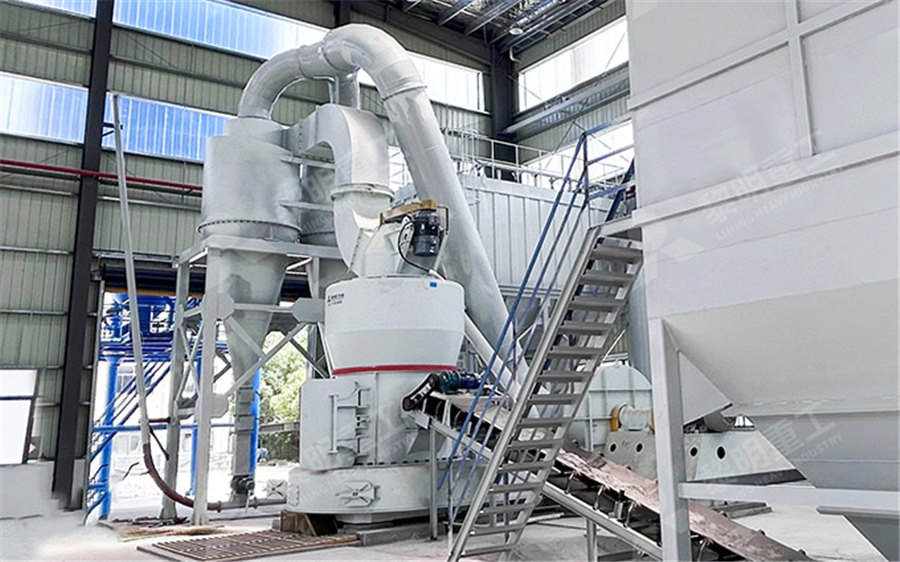
CoalFired Heating Rotary Dryer System JXSC Machine
2023年6月30日 A coalfired heating rotary dryer is a standard industrial drying equipment mainly used for heat treatment and highhumidity drying materials The coalfired rotary dryer working principle is to evaporate the moisture in the material and dry it through the thermal energy generated by burning coal The rotary dryer can dry coal, slag feed, biomass fuel, slag ore, In coal combustion, the efficiency and safety of the process are paramount Indirect firing coal grinding systems play a critical role in optimizing these aspects, especially in industrial applications such as power plants and cement manufacturing This article explores the components, advantages, and operational considerations of indirect firing cIndirect Firing Coal Grinding Systems: Enhancing Efficiency and 2012年11月17日 20 131Fineness Fineness is an indicator of the quality of the pulverizer action Specifically, fineness is a measurement of the percentage of a coal sample that passes through a set of test sieves usually designated at 50, 100, and 200 mesh A 70% coal sample passing through a 200 mesh screen indicates optimum mill performance The mill wear and Coal mill pulverizer in thermal power plants PPT SlideShare2024年2月29日 22 Process Simulation Figure 2 presents the process simulation of the pyrolysisbased cofiring system The coal and biomass grinding processes in the fuel conversion unit are simulated by Crusher model The biomass needs to be dried after grinding since the water content of the biomass entering the pyrolysis reactor is high, which could lead to a Technoeconomic Analysis of Supercritical CoalFired Power Plant
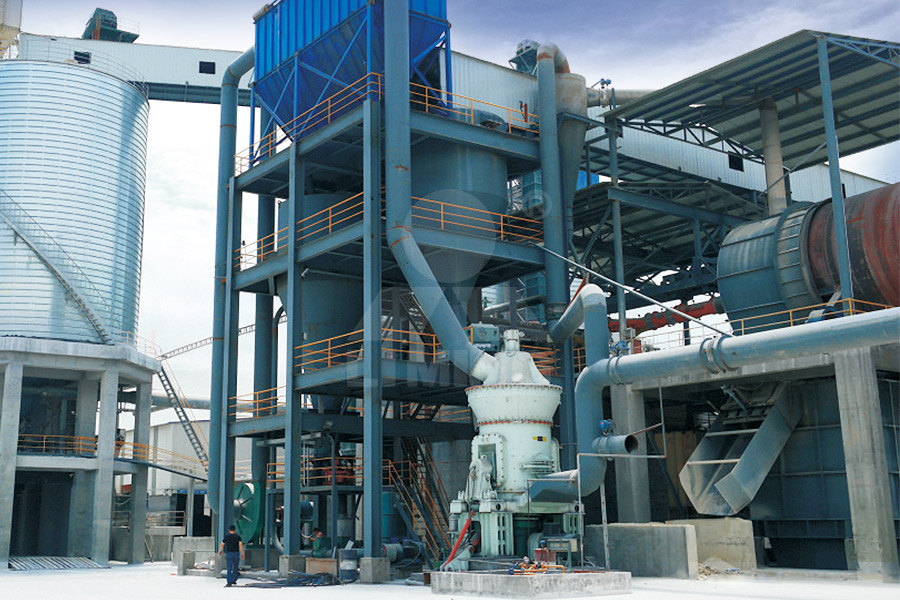
What is a Fired Equipment? Types of Fired Equipment for Oil
Coalfired equipment, Gasfired equipment, and; Oilfired equipment; Differences between Coal Fired, Gas Fired, and Oil Fired Equipment The main differences between coalfired, gasfired, and oilfired equipment lie in the type of fuel they use and the combustion characteristics associated with each fuel Here are some key distinctions:2020年4月2日 By referring to M ill which refe rs to grinding equipment in Wikipedia, the free encyclopae dia (2016), characterist ics of large scale coalfired boiler In Energy a nd Environme nt, 20 09Analysis of the Coal Milling Operations to the Boiler ParametersThere are several pieces of equipment involved in processing coal to be burned in this fashion Figure 1 is a simplified diagram detailing this equipment in a directfired coal burning system Combustion Engineering, Babcock Wilcox, and Riley Stoker Corp are major manufacturers of coal pulverizing equipmentCoal Pulverizer – Power Plant Pall CorporationPulverisers are one of the major auxiliaries in a coal fired thermal power station They are used for grinding the precrushed raw coal, so that the pulverised product at desired PF fineness can be fed directly to the furnace of the steam generator BHEL MANUFACTURE BOWL MILLS AND BALL TUBE MILLS 15 65 115 BBD 3448 BBD 4760 BBD 4772BHEL PRESENCE IN COAL MILLING EQUIPMENT
.jpg)
Fire and Explosion Prevention in Coal Pulverizing Systems
Association in their Codes 85E 1974, "Prevention of Furnace Explosions in Pulverized CoalFired Multiple In practice, the more dangerous condition is an ignition source, ie, a fire, within the coal pulverizing or conveying equipment Fires are generally caused by accumulations of powdered coal brought to temperatures above their RILEY POWER’S ATRITA® COAL PULVERIZERS RELIABLE COSTEFFECTIVE EQUIPMENT FOR LOW OR MODERATE GRINDING CAPACITY REQUIREMENTS Riley Power Inc babcockpower FEATURES / BENEFITS in its capacity range installed at coalfired plants In addition to designing andRILEY POWER’S ATRITA COAL PULVERIZERS RELIABLE COSTEFFECTIVE As the significant ancillary equipment of coalfired power plants, coal mills are the key to ensuring the steady operation of boilers In this study, a fault diagnosis model was proposed on the Effect of mill outlet temperature on the coal moisture contentWyoming Hanna Basin coal, Rosebud seam, having a heating value 913% below that of the original coal; analysis is shown in Figure 2 This fuel change did not affect Unit 5's load carrying capability Then during 198384, OPP D began procurement of a significantly lower cost Wyoming Powder River Basin coal for their two coalfired plants This coal,WorldProven Coal Pulverizer Technology Debuts in the US
.png)
Coal Mill Coal Fired Power Generation Shanghai Electric
Vertical Coal Mill On the basis of retaining the advantages of RP grinders, the innovative HP mediumspeed coal grinder which absorbs the structural characteristics of MPS and MBF coal grinders has the advantages of various grinders Its grinding parts have a long service life and are easy to replace Ball Grinding Mill Dual inlet dual outlet steel ball mills have advantages of high The raw material of coal powder is coal with various hardness, and it drying in the coal mill grinding process to obtain finished coal powder which can be efficiently burned Coal ball mills are widely used in the cement industry and thermal power generation industry, and are also suitable for metallurgical industry, chemical industry, sugar industry and other fieldsCoal Ball Mill Grinding for Different Kinds of Pulverized CoalIndustrial Plants For Sale Used Equipment Specials 365 MW Coal Fired Cogeneration Plant Stock #V813200 Perry has available a365 MW coal fired cogeneration plant with 3 Boilers and 2 Turbogenerators Last used in production of cane sugar Boiler #1 #2 are Riley Stoker coalfired boilers, Boiler 1 is 125 klb per hour at 900used coal processing plant equipment Welcome to TablesTo design equipment for coalfired thermal power plants or to select a nonstandard fuel, it is necessary to know a wide range of coal characteristics, including its abrasive properties [1, 2] When mining, transporting, crushing, and grinding coals for pulverized coal combustion, equipment surfaces and grinding components, which are in contact DEFINITION AND ASSESSMENT OF COAL ABRASIVITY Springer