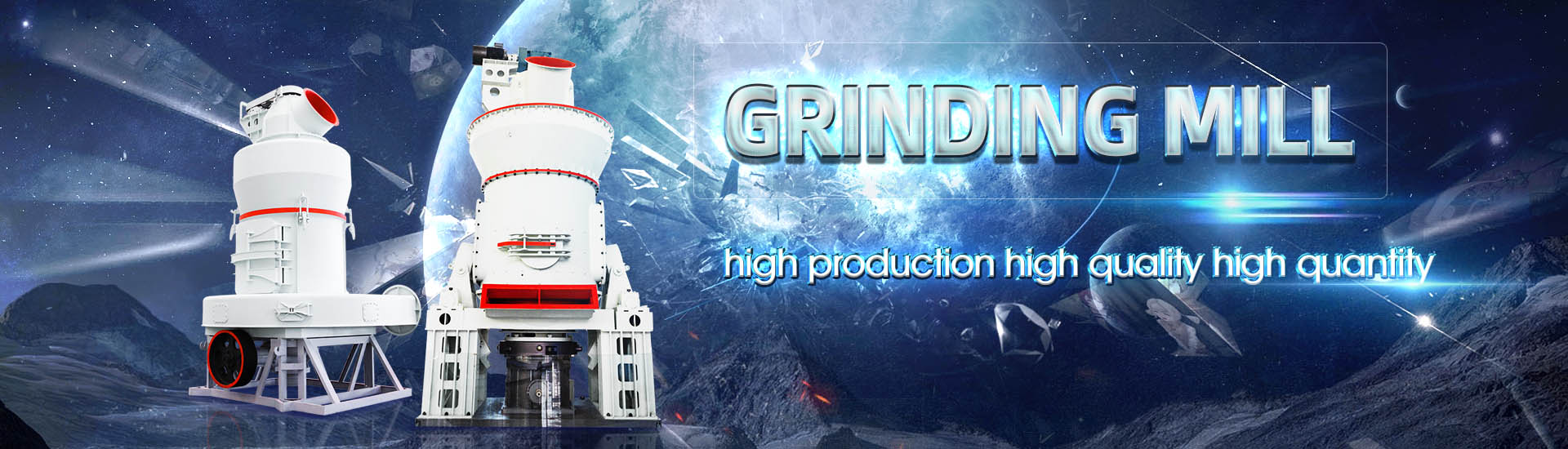
Particle diameter after grinding by vertical grinding ore grinding mill
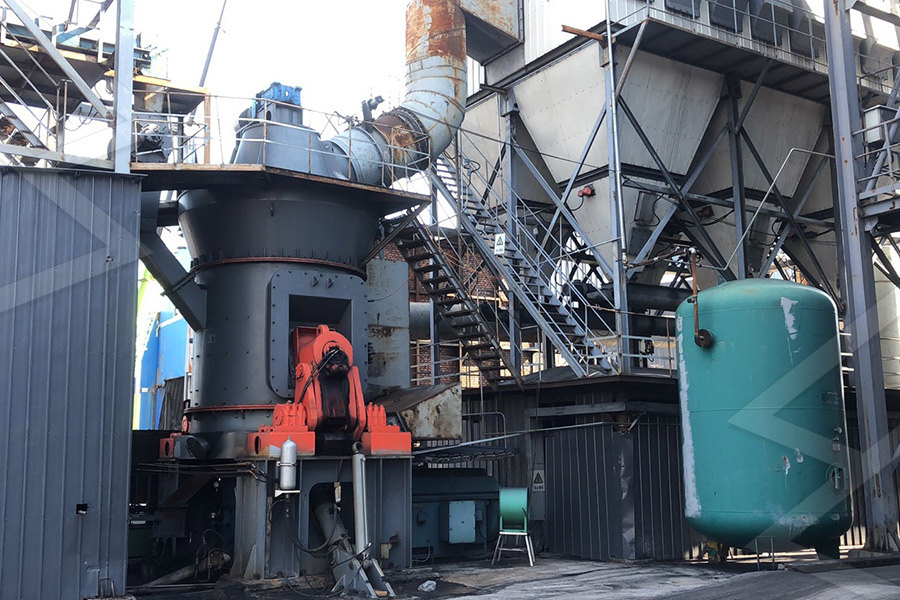
Fine grinding: How mill type affects particle shape characteristics
2017年9月1日 The objective of this work is to assess the influence of fine grinding in ball mills and stirred mills on valuable mineral liberation and particle shape characteristics of UG2 ore, a South African PGM ore2023年10月27日 From the study, the optimal media size was 40 mm for a feed size of −2 + 045 mm and 30 mm for a feed size of −045 + 015 mm Cayirli also agrees with the fact that larger A Review of the Grinding Media in Ball Mills for Mineral Processing Attrition between grinding balls and ore particles causes grinding of finer particles SAG mills are characterized by their large diameter and short length as compared to ball mills The inside of the mill is lined with lifting plates to lift the material Mill (grinding) WikipediaGrinding Mills Barry A Wills, James A Finch FRSC, FCIM, PEng, in Wills' Mineral Processing Technology (Eighth Edition), 2016 71 Introduction Grinding is the last stage in the comminution process where particles are reduced in size by a combination of impact and abrasion, either dry, or more commonly, in suspension in waterGrinding Mill an overview ScienceDirect Topics
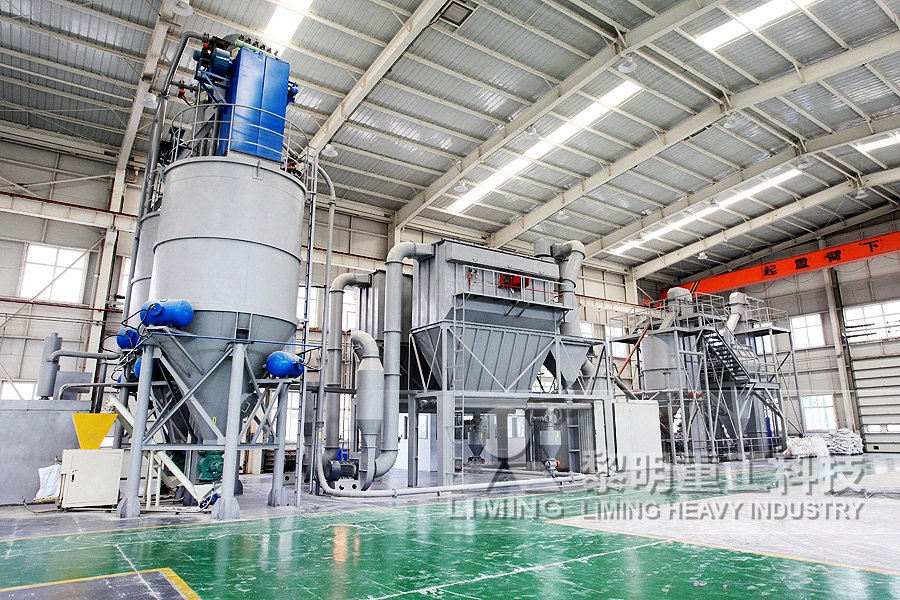
INVESTIGATION ON FLOTATION BEHAVIOR OF A COPPER SULFIDE ORE AFTER
2019年8月1日 INVESTIGATION ON FLOTATION BEHAVIOR OF A COPPER SULFIDE ORE AFTER DRY GRINDING BY LOESCHE VERTICAL ROLLER particle size, and surface which obtained from a 70 m diameter × 35 m SAG mill Request PDF On Mar 15, 2015, Mathis Reichert and others published Research of iron ore grinding in a verticalrollermill Find, read and cite all the research you need on ResearchGateResearch of iron ore grinding in a verticalrollermillCLUM series of ultrafine gypsum powder vertical grinding mills are a new type of ultrafine industrial ore grinding equipment that integrates grinding Superfine vertical grinding mill main machine and multirotor powder separator: Finished product Working Diameters (mm) 1400: 1600: 1700: Number of rollers (pieces) 3: 3: 3: Number of CLUM Ultrafine Vertical Grinding Mill2015年4月9日 Some mills are compartmentalized with each subsequent section having a smaller ball size The material can pass through to the proceeding section, but the balls cannot This ensures that the smaller particles are attacked by the smaller grinding media Ball mill is a versatile grinding mill and has a wide range of applicationsGrinding Mills and Their Types IspatGuru
.jpg)
(PDF) Performance Evaluation of Vertical Roller Mill in Cement Grinding
2017年9月11日 PDF In this study, an extensive sampling study was carried out at vertical roller mill of ESCH Cement Plant in Luxemburg Samples were collected from Find, read and cite all the research Grinding Mills: Ball Mill Rod Mill Design PartsCommon types of grinding mills include Ball Mills and Rod Mills This includes all rotating mills with heavy grinding media loads This article focuses on ball and rod mills excluding SAG and AG mills Although their concepts are very similar, they are not discussed herePhotographs of a glass ended laboratory ball mill show Grinding Mills 911Metallurgist2023年10月27日 The ball mill is a rotating cylindrical vessel with grinding media inside, which is responsible for breaking the ore particles Grinding media play an important role in the comminution of mineral ores in these mills This work reviews the application of balls in mineral processing as a function of the materials used to manufacture them and the mass loss, as A Review of the Grinding Media in Ball Mills for Mineral 2017年9月1日 Particle shape characteristics compared after grinding in ball mill or stirred mill Ball mill; Mill diameter: mm: 219: 300: Media size (graded charge) mm: 5 (12, 19, 25, 32) Mass of UG2 ore particle shape characteristics within any particular size class are not significantly affected by grinding in an open circuit ball mill Fine grinding: How mill type affects particle shape characteristics
.jpg)
Grinding SpringerLink
2022年2月28日 Comparing dry and wet grinding curves in a ball mill in the same condition (an equal amount of materials and grinding media has been used on each pair of wetdry experiments) (Fig 17) indicated two significant differences at higher power values of wet grinding, specifically when speed exceeded 06 critical speed and for higher ω Pmax in the 2023年7月20日 Ore grinding process falls into opencircuit and closedcircuit grinding The grinding products of the former are directly processed in the next processing procedure without returning to the grinding mill After the grinding products of the latter are classified, the coarse particles are returned to the grinding mill for regrindingOre Grinding SpringerLinkResearch concluded that specific energy transferred to the ore particles is the dominant driver in fines generation (Lubjuhn, 1994; van Rijswick et al, 2023) As such, HPGRs directly transfer grinding force into the chokefed particle bed that passes through the gap between two counterrotating rolls, with the machine consumingFlowsheet of the Future: HighPressure Grinding Rolls, Vertical 2013年4月16日 A laboratory scale pintype vertical stirred mill and ceramic beads were employed for the grinding tests The effects of ball diameter (245 mm), stirring speed (200800 rpm) and ball charge Investigation of some parameters affecting the Ultrafine grinding
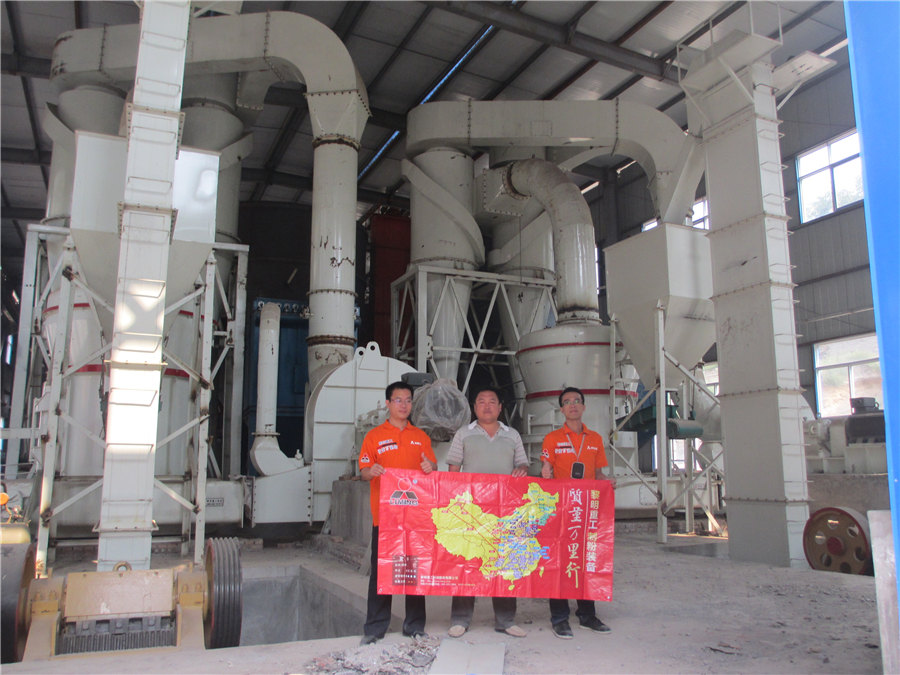
(PDF) Grinding Media in Ball MillsA Review ResearchGate
2023年4月23日 particles better but at a lower grinding rate whilst smaller balls are unable to break large ore particles but grind smaller particles at a higher grinding rate pared with the ball mill system, the energy consumption of the vertical mill system can be reduced by 30% to 40% The vertical grinding mill does not have the metal impact sound of the steel balls colliding with each other and the liner in the ball mill, so the noise is low, which is 2025dB lower than that of the ball millIndustrial Vertical Grinding MillA wet ball mill 1 m × 1 m was chosen to grind the ore down to 200 microns A 30 % pulp was made and charged to the mill, which was then rotated at 60% of the critical speed Estimate:1 The maximum diameter of the grinding balls required at the commencement of grinding, 2 The diameter of the replacement ballGrinding Mill an overview ScienceDirect Topics2014年10月1日 In a test performed in the Loesche test center in Germany, copper slag grinding saved 229% energy in an airswept model and 344% energy in an overflow model [13,14]Copper Ore Grinding in a Mobile Vertical Roller Mill Pilot Plant
.jpg)
Study on Particle Characteristics of Cement by Vertical Roller Mill
2013年5月1日 It has been reported that vertical mills, which are widely used in mineral grinding operations, are more energysaving and environmentally friendly than the traditional ball mill, and have the 2020年8月12日 Altun et al [15] explored the influence of the parameter settings of a vertical roller mill on grinding performance and demonstrated the influence of grinding pressure values on the size and mass An investigation of performance characteristics and energetic 6 Autogenous mill: Autogenous or autogenic mills are socalled due to the selfgrinding of the ore: a rotating drum throws larger rocks of ore in a cascading motion which causes impact breakage of SIZE REDUCTION BY GRINDING METHODS By ResearchGateIt has been proven that grinding efficiency can be improved by interparticle grinding using dry grinding process the newly released surface of the ore is not affected by the surrounding In the future, vertical mill grinding technology will be more widely usedWelcome to contact us:hcmkt@hcmilling Post time: Dec042023Detailed explanation of vertical mill grinding technology
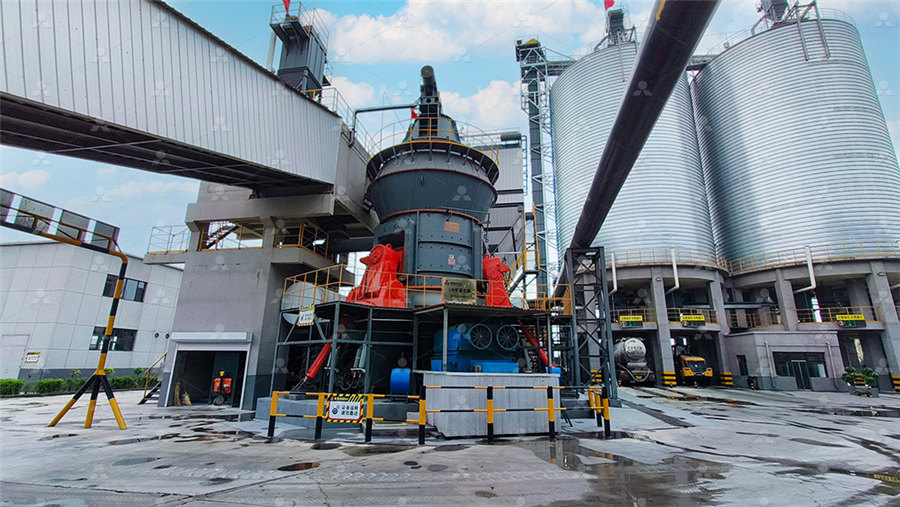
Physicochemical Problems of Mineral Processing
2017年3月20日 An effect of a grinding method, that is ball mill and high pressure grinding rolls (HPGR), on the particle size, specific surface area and particle shape of an iron ore concentrate was studied2018年12月1日 The first stirred vertical mill was developed in Japan by the Japan Tower Mill Company Ltd which was later renamed to Kubota Tower Mill Corporation, KTM The Japanese Tower Mill was the first vertical grinding mill to be used in the mining industry (Stief et al, 1987) The Tower Mill® is now produced by NipponEirichPredicting the product particle size distribution from a laboratory 2023年7月10日 principal grinding methods used in mineral ore processing, reducing the particle size from 500 mm to sub15 µ m through ultrafine grinding [ 23 ] Energies 2023 , 16 , x FO R P EER RE VIEW 5 of 41(PDF) EnergyEfficient Advanced Ultrafine Grinding of Particles Figure 3: Relationship between feed size (F80) and Bond efficiency factor (Huang et al, 2019) VERTICAL POWER MILL (VPM) – PRINCIPLE OF OPERATION Declining ore grades and more complex ore bodies, as well as waste management and global net zero initiatives, lead to a clear trend for high tonnage yet energy efficient grindingRECENT DEVELOPMENTS IN COARSE GRINDING USING VERTICAL
.jpg)
Performance Evaluation of Vertical Roller Mill in Cement Grinding
FIGURE 4 Particle size distributions of collected samples (Survey 2) Bond work indices and breakage characteristics under compression were determinedVertical Shaft Impactor Mill (VSI Mill) The Vertical Shaft Impactor Mill, also known as the VSI Mill, is a unique type of grinding mill that operates on a completely different principle compared to other types of mills This type of mill uses highspeed rotors with wearresistant tips to crush and grind materials into smaller particlesUnderstanding the SAG Mill in Copper Ore Mining Process2015年3月15日 For the grinding tests, a Loesche mill LM45 (table diameter 045 m) is used (Fig 2a) This pilot scale mill is a special development for ore grinding, which is reflected by several features The mill has four rollers, which are able to stress the particle bed with grinding pressures of up to 5000 kN/m 2Research of iron ore grinding in a verticalrollermillfrom the ores The grinding of ore is a highly energyintensive process [1–4] In this process, the size of the particle obtained depends on the energy consumption of the ball mill The major challenge encountered in the process of iron ore grinding is to maintain the desired product particle size distribution (PSD) with sufficientEstimation of Grinding Time for Desired Particle Size Distribution
.jpg)
Fine grinding: How mill type affects particle shape characteristics
2017年9月1日 In this case, the ball mill, which produces more elongated particles, may be preferred over the stirred mill Differences in product shapes are attributed to the different grinding methods used in 2024年6月14日 The grinding process plays a crucial role in industry, allowing for the reduction of particle sizes of raw materials and substances to the required fineness—either as a finished product or for further technological processes The Influence of the Grinding Media Diameter on of 80mm The raw materials are mixed in a certain proportion and fed into a vertical roller mill (LOESCHE mill) The vertical roller mill grinds the marital to D 85 of 90µm The ground product is calcined in a preheater to 850900℃ After calcination, the materials enter to a rotary kiln and heated to 1450℃ to become clinkerModeling and simulation of vertical roller mill using population 2017年2月20日 Grinding Mill Design Morgardshammar started to design and deliver grinding mills in the beginning of the century Today the mills are computer designed and manufactured in big plants with modern machinery In order to keep manufacturing costs at a minimum level, Morgardshammar has a series of standard mill diameters up to and including 65 mGrinding Mill Design Ball Mill Manufacturer 911Metallurgist
.jpg)
SIZE REDUCTION BY GRINDING METHODS ResearchGate
2017年3月4日 After the grinding the state of the solid is A rotating drum causes friction and attrit ion between steel rods and ore particles] A SAG mill with a 44' diameter and a power of 3 5 MW APPENDIX A VERTICAL STIRRED MILL GRINDING TESTS Figure 213 Size distribution of particles after a breakage event Solid arrows represent the force applied over the particle for breakage, and dotted arrows indicate the VTM mill processing copper ore PREDICTING THE PRODUCT PARTICLE SIZE DISTRIBUTION FROM A VERTICAL 2018年8月8日 On the contrary, the predominance of the mass fraction of particles with a smaller diameter (from 1 to 8 μm) of particles after grinding in the disintegrator and vortex machine [21, 22] provides (PDF) Grinding Kinetics Adjustment of Copper Ore Grinding in 3 Double PositionLimiting Technology Makes Operation More Stable In the CLUM series ultrafine vertical roller mill, the contact point between roller shell and millstone liner plate adopts electronic limiting technology and mechanical limiting protection technology, which can avoid the destructive impact (eg the grinding roller directly smashing the millstone) caused by machine CLUM Series Ultrafine Vertical Roller Mill
.jpg)
Grinding in Ball Mills: Modeling and Process Control
2012年6月1日 As the cylinder starts to rotate, the grinding balls inside the cylinder crush and grind the feed material, generating mechanical energy that aids in breaking bonds, activating the catalyst, and breakage mechanism in stirred mills for particles larger than 1µm Recently Yue and Klein (2003) have examined breakage in successive grinding cycles and have found that a grinding limit exists where increasing grind time no longer results in particle breakage They have postulated that this grinding limit is a function of theUltra Fine Grinding A Practical Alternative to Oxidative