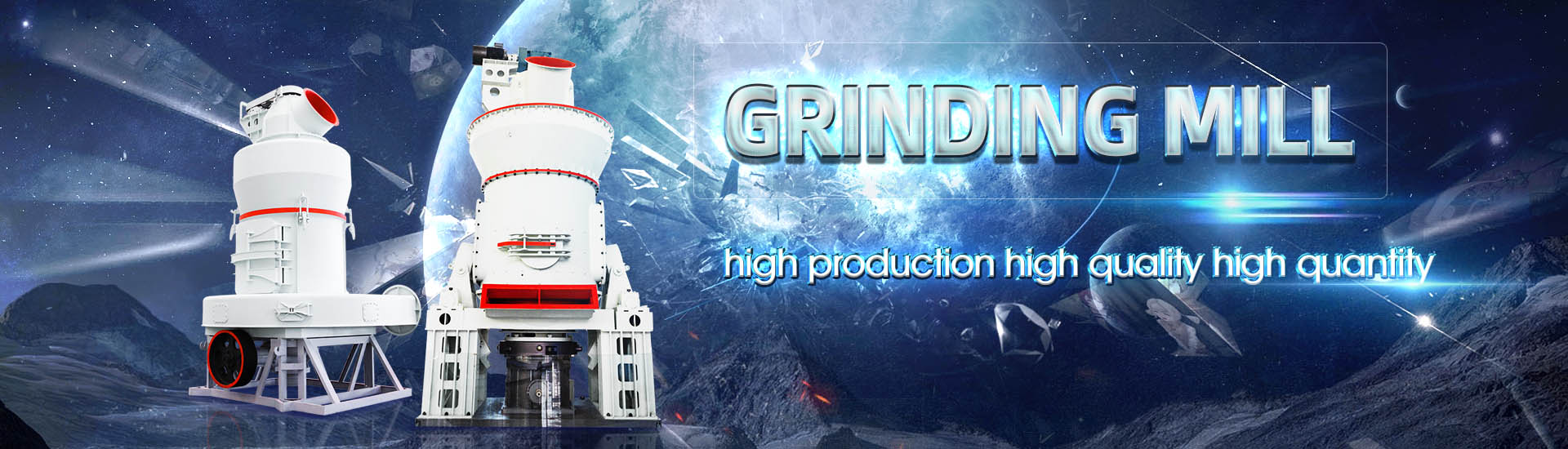
Sintered ore mill
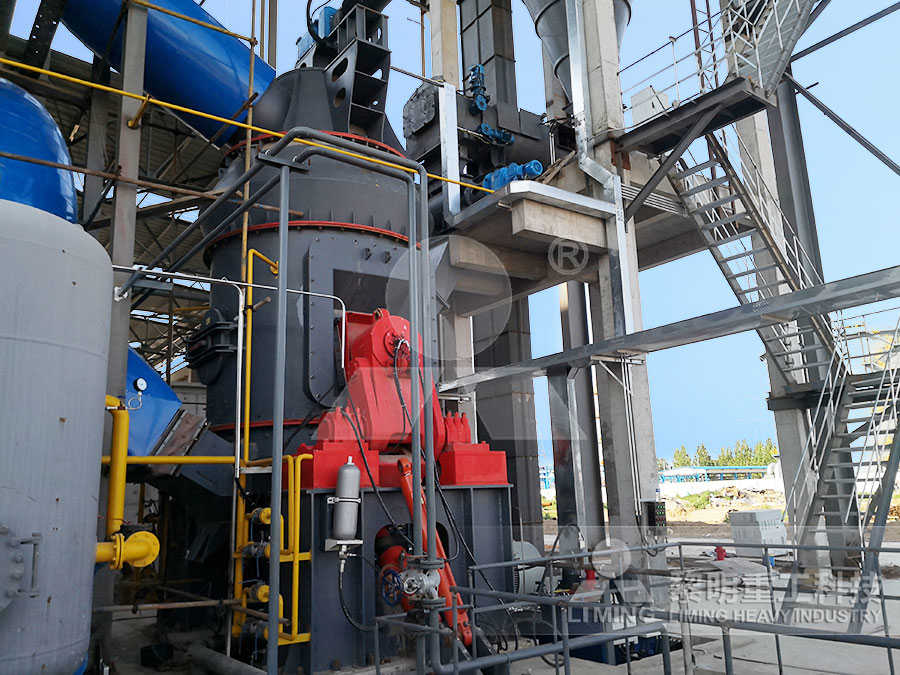
Sinter plant Wikipedia
Sinter plants agglomerate iron ore fines (dust) with other fine materials at high temperature, to create a product that can be used in a blast furnace The final product, a sinter, is a small, irregular nodule of iron mixed with small amounts of other minerals The process, called sintering, causes the constituent 展开The sintering process begins with the preparation of a sinter mixture consisting of iron ore fines, fluxes, solid fuel (called bonding agents in Japan) such as coke breeze, and return fines from Ore Sintering an overview ScienceDirect Topics2017年12月20日 Sintering is a thermal process (1300–1400°C) by which a mixture of iron ore, return fines, recycled products of the iron and steel industry (mill scale, blast furnace dusts, etc), slagforming elements, fluxes and coke Iron Ore Agglomeration Technologies IntechOpenA sinter plant is used to agglomerate iron ore to produce sinter, a product that can be used in a blast furnace According to the US Environmental Protection Agency, the sintering process Sinter plant Global Energy Monitor
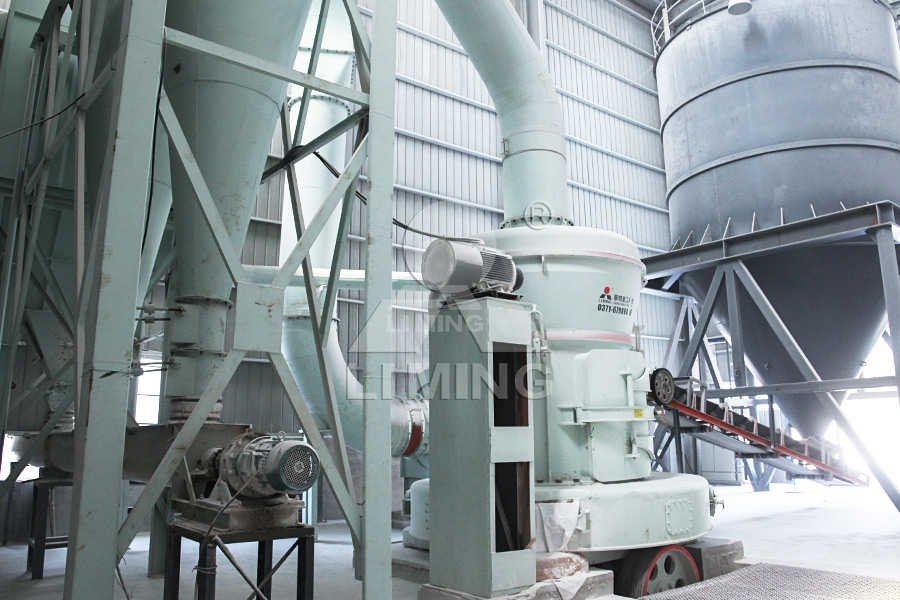
Iron Ore Sintering: Process Taylor Francis Online
2017年3月24日 Sintering is a thermal agglomeration process that is applied to a mixture of iron ore fines, recycled ironmaking products, fluxes, slagforming agents, and solid fuel (coke) The 2017年2月16日 Sintering is a thermal agglomeration process that is applied to a mixture of iron ore fines, recycled ironmaking products, fluxes, slagforming agents and solid fuel (coke)(PDF) Iron Ore Sintering: Process ResearchGateThe sinter plant turns iron ore into sinter, which is the optimal product for the blast furnace Sinter is made by burning a mix of iron ore powder, fluxes and recycled substances from the steel Raw materials Sinter plant ArcelorMittal2022年1月1日 Sintering is the most economic and widely used agglomeration process to prepare iron ore fines for blast furnace use In this chapter, the sintering process is first Iron ore sintering ScienceDirect
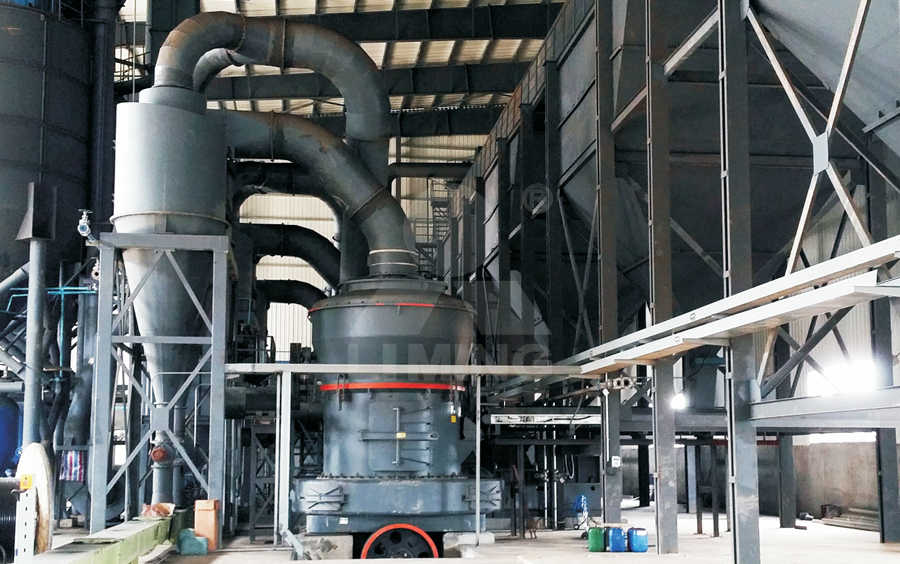
Sinter Plant Operations: Raw Materials SpringerLink
2016年9月3日 The raw materials for an integrated steelworks can be classified into four categories, which are iron ores, fluxes, fuels, and reverts The characteristics of these raw materials strongly affect the metallurgical ed and sinter productivity In this report, a new technique, adding microparticles to concentrates as a binder, was investigated A vertical wet ball mill was installed on a sepa ate granulation Improving Granulation of Sinter Materials by Using a Wet Vertical Alliance Rendezvous is one of the leading exporter and manufacturer of Mill scale, Iron Ore, and Sintered Iron Ore in Pakistan We started our operations in Karachi in 2004 Specializing in Chrome Ore and Iron Ore Our first expansion Alliance Group2017年12月20日 Until the 1950s of the last century, the oxidized iron ores that were loaded into the blast furnace had granulometries within 10 and 120 mm However, the depletion of highgrade iron ore sources has made necessary Iron Ore Agglomeration Technologies IntechOpen
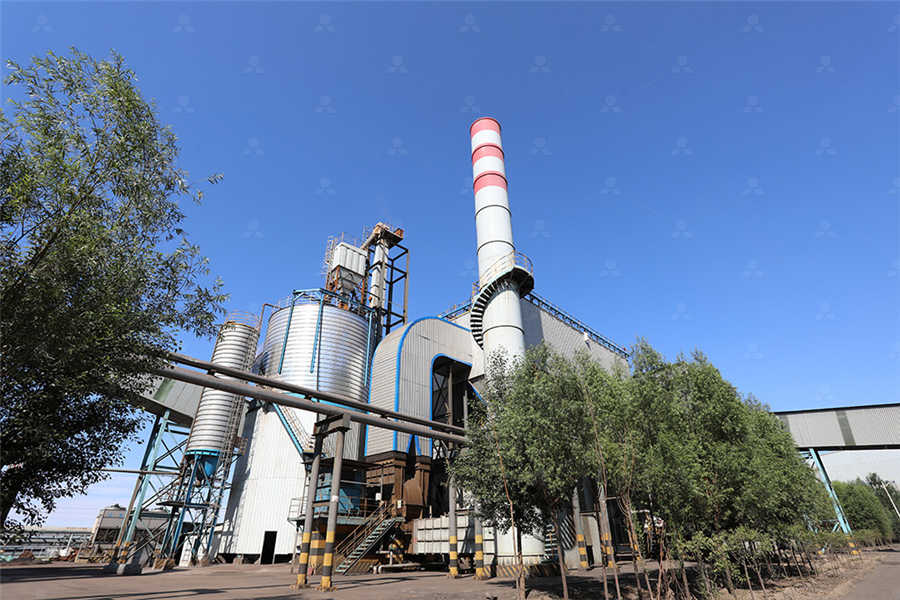
Iron Ore Processing: From Extraction to Manufacturing
2024年4月26日 The final stage in iron ore processing is ironmaking, where the iron ore is transformed into molten iron through a process called reduction The most common method of ironmaking is the blast furnace route In a blast 2013年3月9日 Sintering is a thermal process (carried out at 1300 deg C to 1400 deg C) by which a mixture of iron ore, return fines, recycled products of the steel plant industry (such as mill scale, blast furnace dusts, etc), slag forming elements, fluxes and coke fines are agglomerated in a sinter plant with the purpose of manufacturing a sintered product The Sintering Process of Iron Ore Fines – IspatGuru53 Ironmaking 焼結鉱 Sintered ore Blast furnace Foundry iron blooming/billeting Recuperating furnace鉄鋼製造プロセス Iron and Steelmaking FlowThe sinter plant turns iron ore into sinter, which is the optimal product for the blast furnace Sinter is made by burning a mix of iron ore powder, fluxes and recycled substances from the steel plant to create an opengrained, consistent substance The sinter is then crushed, cooled and screened for dust Sometimes, iron ore is supplied in the form of iron ore pelletsRaw materials Sinter plant ArcelorMittal
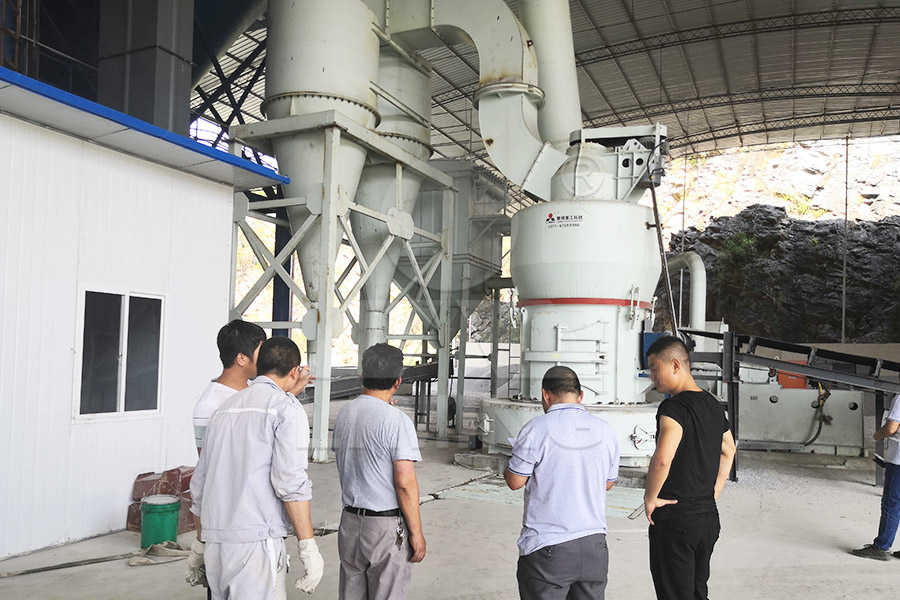
Comparison of physical properties of oxidative sintered pellets
2015年8月1日 The physical properties of oxidative sintered pellets produced from typical South African UG2 ore are compared with the physical properties of pellets produced with conventional South African 2019年12月24日 Energy Resources, Its Role and Use in Metallurgical Industries RC Gupta, in Treatise on Process Metallurgy: Industrial Processes, 2014 423132 Sinter Making The iron ore fines (− 10 mm) are agglomerated using Dwight Lloyed sintering machine The iron ore fines and coke breeze fines mix with moisture is fed on the sinter bed which is ignited by a gas Sintered Ore an overview ScienceDirect Topics2021年5月3日 Gold is extracted from gold ores According to the World Gold Council, approximately 190,000 tons of gold has been mined since 1950 The highquality ores have been gradually depleted since then [1]However, the demand for gold for industrial use has increased owing to the growing demand for electronic products, such as computers and smartphones [2], Utilizing gold mine tailings to produce sintered bricks2015年1月1日 Like other sintering processes, iron ore sintering converts iron ore fines of often − 8 mm sizing into larger agglomerates, namely, sinter, between 5 and 50 mm particle size, which possess the physical and metallurgical characteristics and gas permeability required for efficient blast furnace operationAs shown in Figure 141, iron ore sintering is carried out in three Iron ore sintering ScienceDirect

Alliance Group
Alliance Rendezvous is one of the leading exporter and manufacturer of Mill scale, Iron Ore, and Sintered Iron Ore in Pakistan We started our operations in Karachi in 2004 Specializing in Chrome Ore and Iron Ore Our first expansion was in 2013 when we opened our second corporate office in Oman as Oman Global Zaman SPC2022年1月1日 Like other sintering processes, iron ore sintering converts iron ore fines of often −8 mm in size into larger agglomerates, namely sinter, between 5 and 50 mm in particle size, which possess the physical and metallurgical characteristics as well as gas permeability required for efficient blast furnace operationIron ore sintering ScienceDirect2022年11月24日 In order to reduce the sintering allocation scheme and lower the cost of allocation, two semilignite ores with similar properties and large price differences were selected for blending to achieve the purpose of Sintering Properties and Regression Analysis of 2011年2月1日 Request PDF Utilising of the oiled rolling mills scale in iron ore sintering process Up to 5% of steel is lost with the scale at hot rolling operation This waste contains 69–72% of iron in Utilising of the oiled rolling mills scale in iron ore sintering
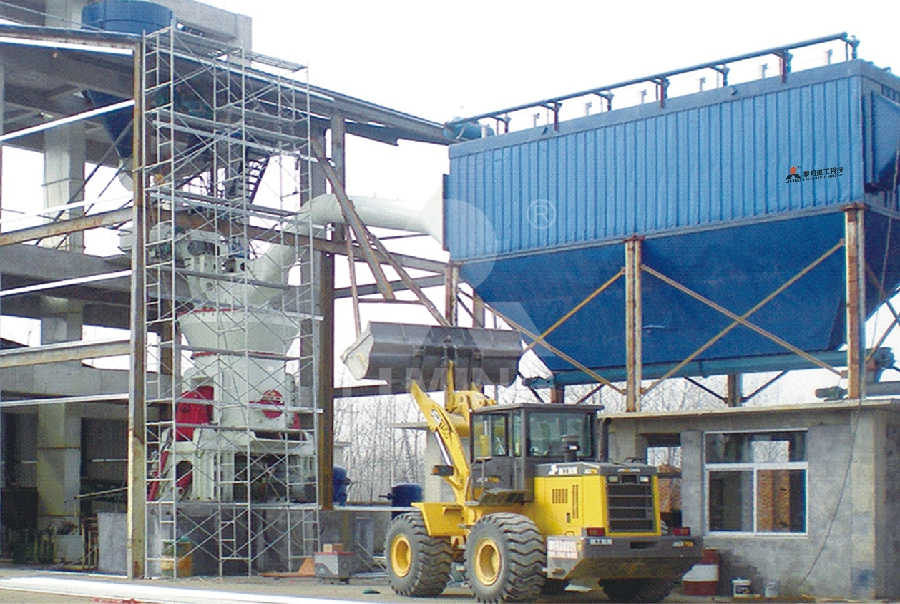
Sinter Plant Perantech
The sintering process requires various raw materials such as fine ores, fluxes, mill tailings, and return fines At the end of the sintering machine's pallet car line is a hot sinter crusher, which reduces the sintered ore into pieces of less than 150 mm Since the crusher processes material at a temperature of over 800°C, 烧结铁sintered iron是用粉末冶金方法制得的铁或铁基材料。 主要用作冶炼特种钢、精密合金、磁性材料等的添加剂或原料,也可作特殊用途的铁制品。 新闻 贴吧 知道 网盘 图片 视频 地图 文库 资讯 采购 百科烧结铁 百度百科2016年6月30日 Secondly, any Fe 2 O 3 which forms through oxidation of the FeO and Fe 3 O 4 in the mill scale only begins to convert to Fe 3 O 4 above ∼1150°C (see Figures 1 and 2) and so no appreciable Effect of Addition of Mill Scale on Sintering of Iron Ores2020年10月1日 Iron ore sinter plants are energyintensive components of integrated iron and steel production (see Table 1), where the iron ore fines (5 mm) lump sinter cakes with greater gas permeability, which are the most important burden materials for iron making in blast furnaces (BFs) [7]The main process is shown in Fig 2 and described in Recent progress in sustainable and energyefficient technologies
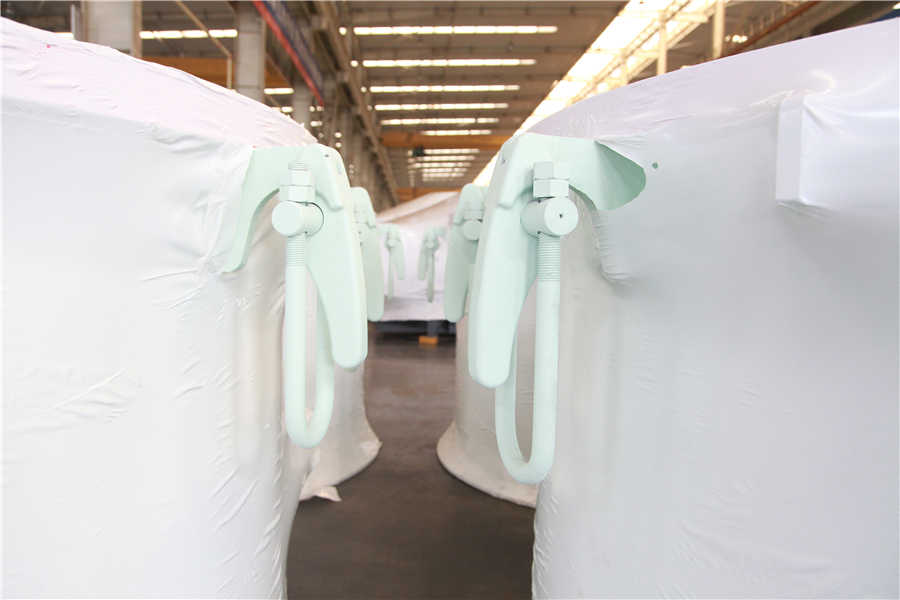
sintered ore Traduction française – Linguee
De très nombreux exemples de phrases traduites contenant "sintered ore" – Dictionnaire françaisanglais et moteur de recherche de traductions françaises Consulter Linguee; Proposer comme the percentage of sintered fines used in a blast furnace tends to vary from mill to mill eurlexropa eurlexropa2017年2月16日 PDF Sintering is a thermal agglomeration process that is applied to a mixture of iron ore fines, recycled ironmaking products, fluxes, slagforming formed by the mix to be sintered, (PDF) Iron Ore Sintering: Process ResearchGateDownload Table Chemical analysis of manganese ores and sinter/wt% from publication: Optimum condition for smelting high carbon ferromanganese In the present study, pilot plant experimental Chemical analysis of manganese ores and sinter/wt 2019年2月20日 Three types of solid oxygen materials (sintered return ore, scale briquette and fine mill scale) were carefully investigated as hot metal pretreatment agents, evaluating their desiliconisation Desiliconisation and Dephosphorisation Behaviours of
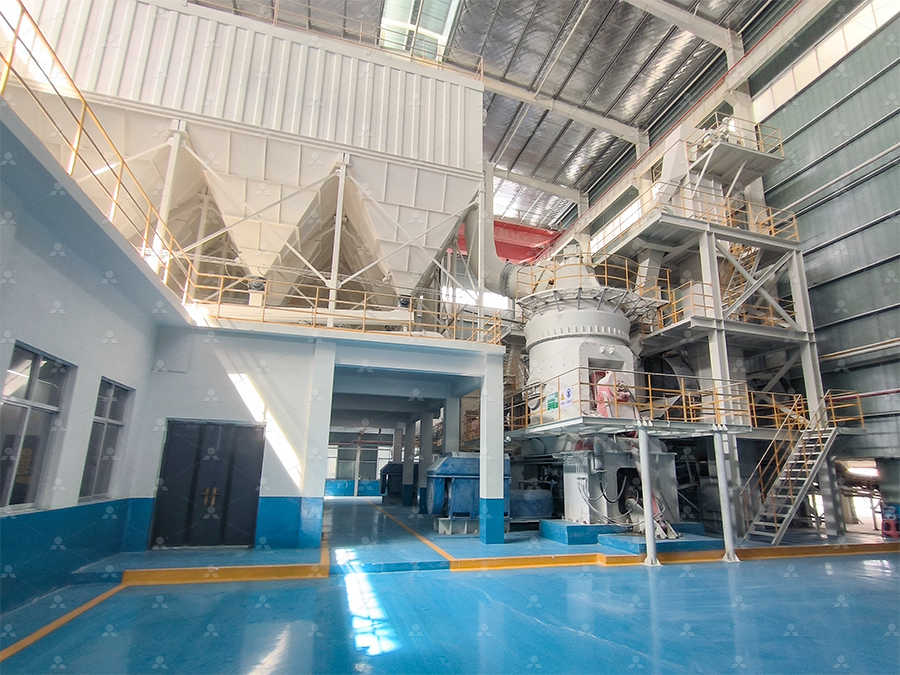
FACTORS AFFECTING THE REDUCIBILITY OF SINTERED CHROMITE
Sintered pellets have shown a superiority over lumpy ore and briquettes made of the same (ores vs pellets), grinding method (ball mill grinding vs pressure grinding) and oxidation degree (weathered ore) of chromite raw materials on reducibility 2 EXPERIMENTAL WORK The chromite reduction test project st arted with the development of the 2022年2月28日 The present work proposes a novel process to sinter porous iron ore (porosity ~23–24%) with enhanced productivity and quality The iron ore is preprocessed in the presence of calcined lime for the temporary closure of pores, which further prevents water absorption during the granulation process in drum in the presence of water The calcined lime coated iron ore A Novel Sintering Process for Porous Iron Ore Sintering with Cross section of a sintering tool and the sintered part Sintering is generally considered successful when the process reduces porosity and enhances properties such as strength, electrical conductivity, translucency and thermal conductivityIn some special cases, sintering is carefully applied to enhance the strength of a material while preserving porosity (eg in filters or Sintering Wikipedia2018年7月11日 Until the 1950s of the last century, the oxidized iron ores that were loaded into the blast furnace had granulometries within 10 and 120 mm However, the depletion of highgrade iron ore sources Iron Ore Agglomeration Technologies Provisional chapter Iron Ore
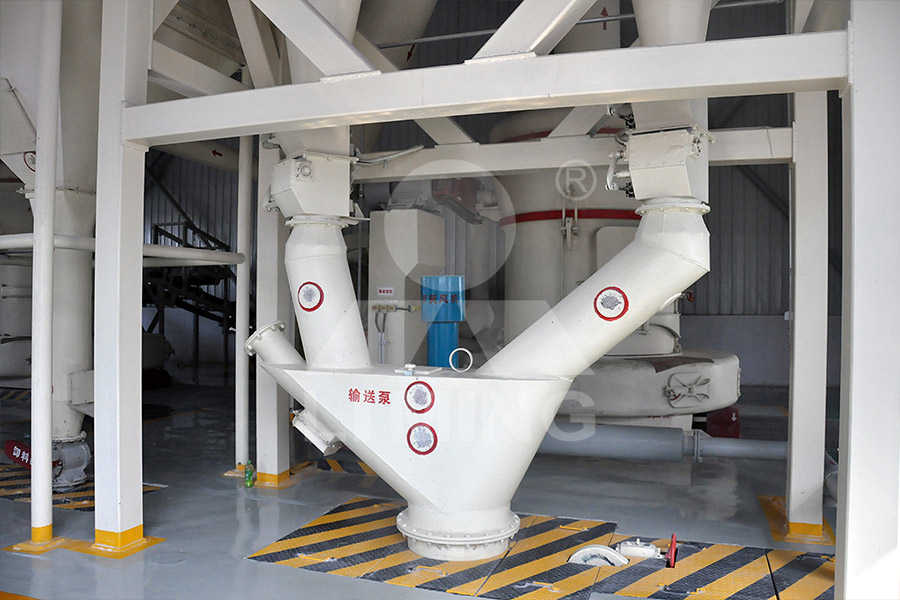
How a Steel Plant Used Sinter Feed Analysis to Get More Out of Iron Ore
2020年9月15日 According to the US Geological Survey, Mineral Commodity Summaries, January 2020, “iron ore resources are estimated to be 110 billion tons of iron ore containing about 27 billion tons of iron US resources are mainly lowgrade taconitetype ores from the Lake Superior district that require beneficiation and agglomeration prior to commercial useFig8 compares the temperature of ore and gas in both types Sintered ore temperature at outlet of cooler rise approx 30 degC in circulation type Temperature difference is small enough not to affect sinter plant commercial operation Noncirculation 0 100 200 300 400 500 600 700 Cooler Inlet → Outlet Temperature (℃) Gas temperature Ore Maximizing Sinter Plant Heat Recovery英文Sintered Ores Kenichi HIGUCHI,1)* Jun OKAZAKI2) and Seiji NOMURA1) 1) Process Research Laboratories, Nippon Steel Corporation, 201 Shintomi, Futtsu, Chiba, 2938511 Japan 2) Nippon Steel Corporation Now at Nippon Steel Technology Influence of Melting Characteristics of Iron Ores on Strength of [6][7][8][9][10] [11] [12][13] Choudhar et al 7,8) studied the effect of the Al 2 O 3 content in iron ore powder on the sintered ore phase, and the results showed that the structure of the silico Chemical compositions of iron ores Download Scientific Diagram
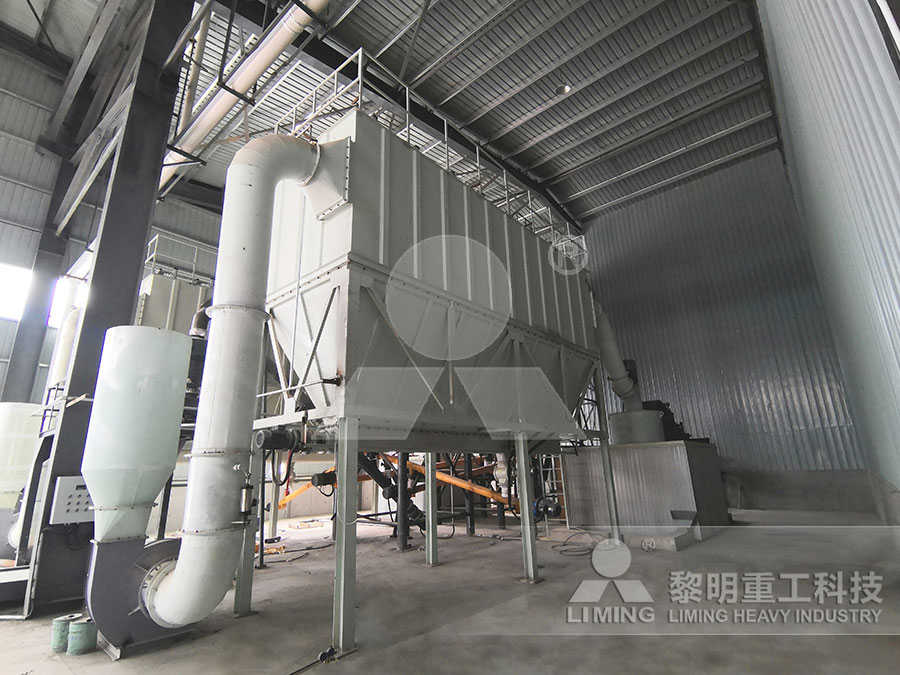
Iron ore pellets for blast furnace a technical guide
2023年1月28日 The crushing equipment is a rod mill or a ball mill Compared with fluxbased net ore or sintered ore, acid pellets have low softening and melting temperatures In addition, acid pellets are very sensitive to CaO 2022年3月1日 (eg, increasing pressure drop) With iron ore sintering, iron fines are utilizable for pig iron production The sintering process is influenced extensively by the properties of the input material and process conditions The operating setting essentially influences the properties of the sintered product [1]Model of an iron ore sinter plant with selective waste gas Manufacturing sintered ores with less Al 2O 3, SiO 2, or FeO content with superior hightemperature properties including reducibility has been explored in many plants5) However, considering the future trend of natural resources, Influence of Ore Assimilation and Pore Formation during Sintering on Reduction Behavior of Sintered OresInfluence of Ore Assimilation and Pore Formation during Sintering 2022年1月1日 A sample of goethite iron ore sinter feed (GSF) was employed as a raw material in a sintering bed This sample partially replaced hematite sinter feed (HSF), which is currently used as raw Iron ore sintering ResearchGate

Study on Sintering Technology of Manganese Ore Fines
2024年6月20日 Methods PilotScale Sinter Pot Tests The pelletsintering process for manganese ore fines includes additional steps of raw material pretreatment and pelletizing, and it employs the technique of fuel fractionation as shown in Fig 1b First, the manganese ore fines are finely ground to − 0074mm accounted for 60% by the roll crusher (Φ200 × 125, 12 kW/h) and 2022年4月4日 In this study, compacted hematite (Fe2O3) preforms were made and sintered at various temperatures, such as 1250 °C and 1300 °C, using both conventional and microwave sintering methods The density, porosity, microhardness, cold crushing strength, microphotographs, and Xray diffraction (XRD) analysis of the sintered preforms were used to Characteristics of Conventional and Microwave Sintered Iron Ore No 5 Sinter Machine, a sintered ore production pot test of about 50 kg in scale was conducted, and the required amount of the microparticle binder addition was studied9) Based on the test result, as a pilot plant for producing and supplying iron ore microparticle binder continuously, a vertical type wettype ball mill was introduced toImproving Granulation of Sinter Materials by Using a Wet Vertical Ball Mill2015年11月23日 What largely sets New Zealand ironsands apart from typical iron ores are the levels of gangue contained within the ore, especially titanium The titanium content of the titanomagnetite is Behavior of New Zealand Ironsand During Iron Ore Sintering