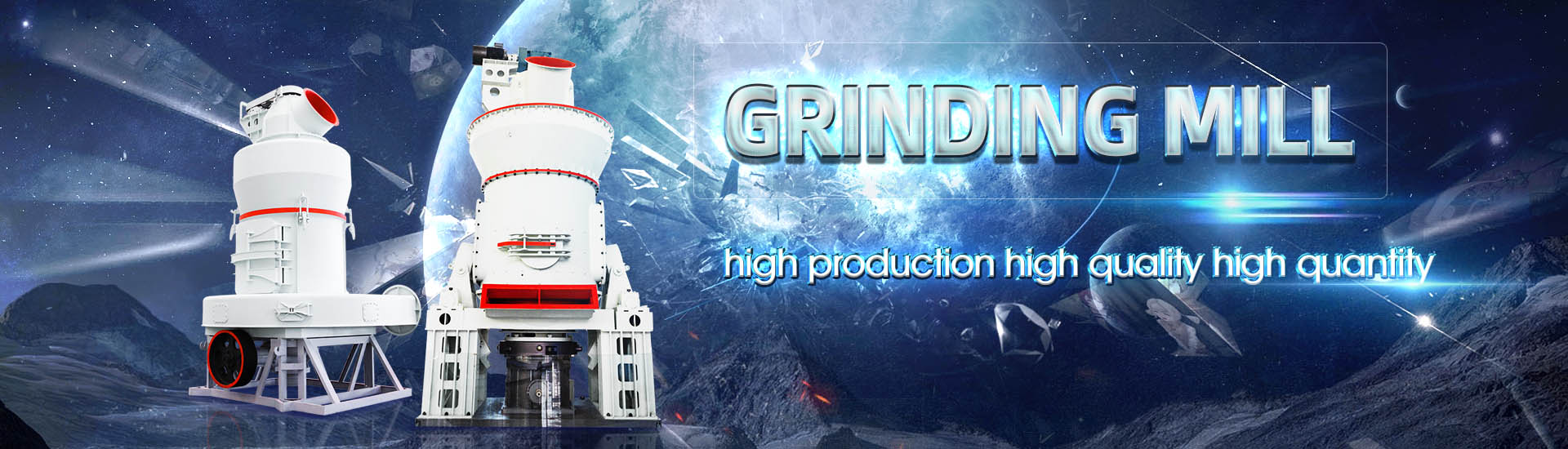
4.2*13 grinding ball consumption calculation
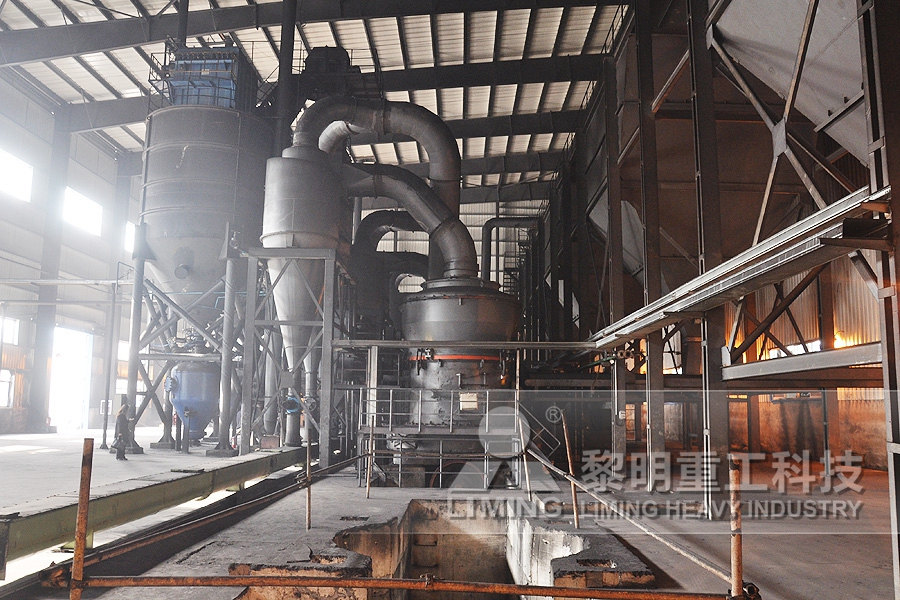
How to Measure Grinding Efficiency 911Metallurgist
2018年4月20日 In determining grinding efficiency, each stage is considered as a single stage The power per tonne for rod milling is determined from the rod mill feed rate and the power per tonne for ball milling is determined from the ball mill feed rate2020年2月26日 Measurement results of two ball mills in a real ceramic manufacturing plant showed that the proposed calculation models could achieve an accuracy of more than 96% for Calculation method and its application for energy consumption of In the present work, experiments were carried out to study the effect of wheel parameters such as grain size and grinding parameters like depth of cut and feed rate on the surface roughness and surface damage The significance of the (PDF) Methodologies for the evaluation of grinding 2004年11月1日 The Linear Wear Model, herein described, provides a theoretical framework for the best estimations of comparative grinding media wear performance (in the absence of ball Methodologies for the evaluation of grinding media consumption
.jpg)
The Power Consumption Calculation of a Ball Drum Mill
First, calculation of the power consumption of drum mills, equipped with one or several inclined intermediate diaphragms Second, determination of the power consumption required to move 2018年11月1日 Ball wear kinetics equations for three different sized balls in a grinding mill were found • Calculations of ball flux for the mill recharging were performed • Alumina ball A population balance model of ball wear in grinding mills: An 1989年1月1日 The grindingproduct size, P, in a Bond ball mill, which is given by the aperture size which passes 80% of the grinding product as a function of the aperture size of the test Calculation of energy required for grinding in a ball millThese calculations result in total embodied energy figures for steel grinding media ranging from 48 – 66 kWh/kg This is dependent on ball metallurgy, ratio of recycled steel in the feedstock and the trucking distance required to transport Energy Curve Enhancement Blog 7: Including grinding
.jpg)
ball mill calculations, grinding media filling degree, ball size, mill
online live calculators for grinding calculations, Ball mill, tube mill, critical speed, Degree of filling balls, Arm of gravity, mill net and gross power Optimization Online Training2022年3月15日 Various operational parameters, such as mill speed, the ball charge composition, charge filling, lifter type, and lifter number, significantly impact ball milling (PDF) Power consumption management and simulation of 2024年11月11日 In evaluating ore grinding energy consumption using the Bond ball mill work index, discrepancies were identified As a result, an investigation into the determination method of Hou Ying (HY) wet ball milling work index (WHY) for Gongchangling magnetite ore was conducted to determine the correlation between WHY and grinding energy consumption at varying Exploring the Link between HY Wet Ball Mill Work Index and Grinding 2011年1月1日 the Bond ball mill to realise the same grinding conditions of a 24 meter wet grinding mill However, upon close inspection of Bond’s original paper published in 1949, BondMeasurement of electrical energy consumption in a
.jpg)
4 SIZE REDUCTION
Table (41) gives some values (in units of kWhm1/2t1) Table (41): Bond’s work index for some materials Material Work index Bauxite 878 Cement clinker 1345 Clay 630 Coal 1300 Granite 1513 Gravel 1606 Limestone 1274 The Bond’s equation is:) 1 1 36 (2 1 b b i D D P W m (45) The proper units to be used are: 𝑚̇ in kgs1 and D b2013年7月15日 The sample was received crushed appropriately for the ball mill test Ball Mill Grindability Test was conducted by standard practice using 100mesh (150 pm) closing screens The ball mill work index is shown below BM Wi (kWhr/st) = 1797 ; Bond Work Index FormulaEquation 911Metallurgist2020年10月9日 consumption of the grinding process accounts for 30% to 75% of the entire operation process, 5247 4 of 13 In the formula, A The complete SABC process includes semiautogenous grinding Operation Analysis of a SAG Mill under Different Conditions Based on 2017年8月1日 e Planetary ball mill data for the calculation of specific energy transfer by the mill power consumption, ball to powder loading, reduce from 1345 m m to 134 m m in 25 h grinding period(PDF) Grinding of ClassF fly ash using planetary ball mill: A
.jpg)
Density Calculator
This free density calculator determines any of the three variables in the density equation given the other two home There are exceptions however, such as water's density increasing between 0°C and 4°C Below is a table of units in which density is commonly expressed, as well as the densities of some common materials Common Density Units2018年12月17日 Table 2 : Plant trial results for grinding aids use Additive % Dosage level Increase in productivity Savings in grinding time Savings in energy Di ethylene glycol 0102 20% ~ 20% Lignin compound 0102 15% 12% ~ 1215% Urea 0102 30% ~ 15% For commercial cement plant ball mill 12 m long, 38 m diameter, calculations performed using design Ball Mill Optimization PDF Free Download SlideShare2013年8月3日 In Grinding, selecting (calculate) the correct or optimum ball size that allows for the best and optimum/ideal or target grind size to be achieved by your ball mill is an important thing for a Mineral Processing Engineer AKA Metallurgist to do Often, the ball used in ball mills is oversize “just in case” Well, this safety factor can cost you much in recovery and/or mill liner Calculate and Select Ball Mill Ball Size for Optimum GrindingAnalysis of the efficiency of the grinding process in closed circuit ball mills Valery I Telichenko1, Rashid R Sharapov1*, Svetlana YLozovaya2 and Vladimir ISkel1 1Moscow State University of Civil Engineering, Moscow, Russia 2Belgorod State Technological University named after VG Shukhov, Belgorod, Russia Abstract Ball mills for fine grinding cement clinker and additives areAnalysis of the efficiency of the grinding process in closed circuit
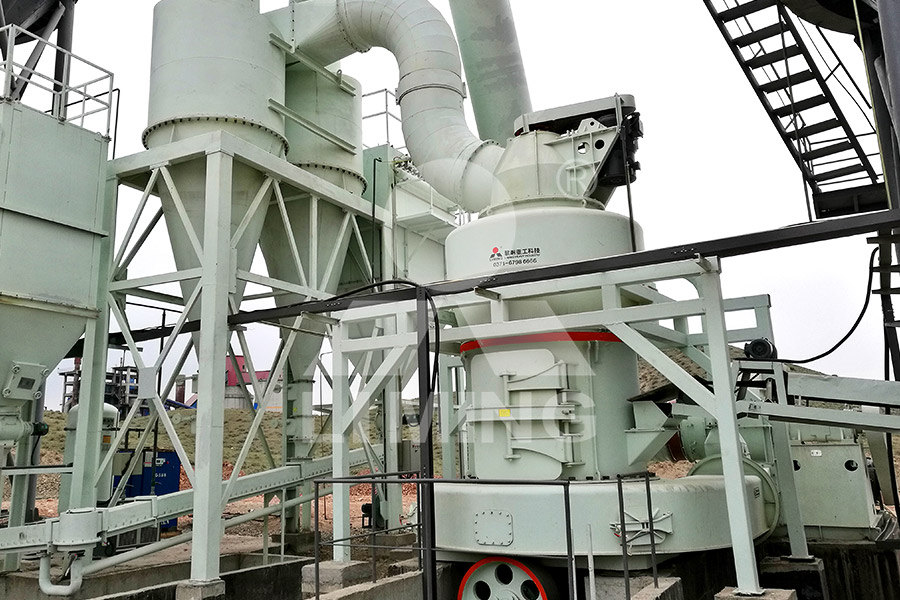
Grinding Media in Ball MillsA Review ResearchGate
Table 1 Chemical composition of typical grinding media (% wt) Adapted from [24] 211 Cast Iron Cast iron can be grey cast iron or white cast iron, but white cast irons are commonly used in 2017年4月29日 The screen analysis of the ball charge of an 8ft by 22in (24m by 558cm) Hardinge conical mill shown in Table 19 was made at the Miami Copper Co’s plant after the mill had been operating for a year with a ball load of 14,800 lb (6713 kg) which was maintained by the addition of 400 lb (181 kg) of 2in (508mm) steel balls dailyGrinding Media Wear Rate Calculation in Ball Mill2024年1月26日 In cement manufacturing industry, the grinding process is one of the most energy consuming processes Approximately 65–75 % of the total power consumption is used in grinding process Generally, ball mills are utilized for grinding the raw material into finished product (cement) in grinding unit of cement putation of charging media for a double compartment cement ball 2022年3月15日 The grinding efficiency is a function of the quality of the final product, the energy (kWh), and the power (kW), which are used to determine the energy consumption of the mill [4] (PDF) Power consumption management and simulation of
.jpg)
Bond´s work index estimation using nonstandard ball mills
2023年9月18日 It is a wellknown fact that the value of the Bond work index (wi) for a given ore varies along with the grinding size In this study, a variability bysis is carried out with the Bond standard 2013年7月24日 18 Reagent Consumption Calculations; 19 LiquidSolid Relationships Specific Gravity Volume; 110 Ratio of Concentration by Assay; 111 Mill Water to Ore Ratio Requirements; 112 Resistance of Various Materials to Crushing; 113 Pulp Calculations 1131 Pulp Details by Weight 11311 Flotation; 11312 Conditioning or Dissolving; 1132 Percent Solids to Specific Gravity Conversion of Slurry2017年1月1日 The comminution circuit comprises twostage crushing and singlestage grinding in a ball mill in Highgrade northern band ore 359 72 1043 13 The power consumption was higher (72 (PDF) Performance optimization of an industrial ball mill for 1992年3月1日 Batch grinding parameters a T 063 min −1 γ 080 α 137 Λ 47 β 62 Φ 0 060 δ 01 a T 112 mm Table 2 Average input values for the fullscale mill and their corresponding interval ranges Optimization of the makeup ball charge in a grinding mill
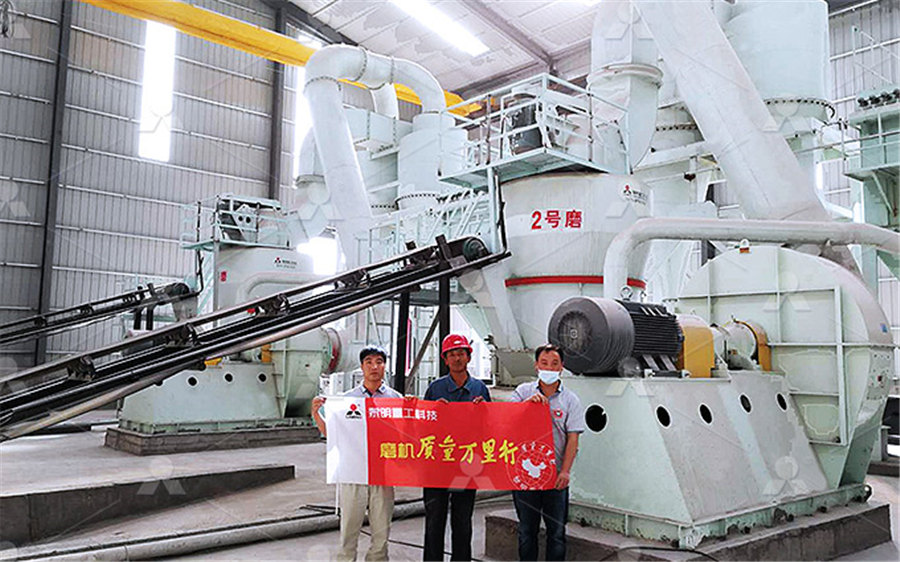
Analyzing the influence of lifter design and ball mill speed on
2023年10月30日 In the calculation of energy consumption in ball mills, classical theories mainly consider factors like the charge fill level, lifter dimensions, the number of lifters, and the rotational speed of 2019年8月30日 1 Calculation of ball mill capacity The production capacity of the ball mill is determined by the amount of material required to be ground, and it must have a certain margin when designing and selecting There are many factors affecting the production capacity of the ball mill, in addition to the nature of the material (grain size, hardness, density, temperature and Ball Mill Parameter Selection Calculation JXSC2023年4月4日 Grinding iron ores in conventional ball mills involve a considerably high consumption of metallic media, resulting in high operating costs In the case of compact itabirites, the high silica Study on Partial Replacement of Metal Grinding Ball Presented at the Ultrafine Grinding 06 (UFG 06), June 1213, for a mean energy consumption of 40 GJ/tonne cement Figure 2 Conventional clinkergrinding ball mills with a diaphragm CONVENTIONAL CLINKER GRINDING A NEW APPROACH TO
.jpg)
Efect of grinding media on the milling eficiency of a ball mill
optimize ball loading composition by varying the size of grinding media regarding ball number, total surface area, and ball weight so that the mill charge is the same in all different mixed groups 2 Methodology of Experimental Work The section that follows explains the experimental work that was done It demonstrates the quantity and lo2018年4月5日 Example Rod Mill Design Calculations Rod Mills F = 18,000 micrometers P = 1,200 micrometers Wf = 132 W = 10 x 132/√1,200 – 10 x 132/√18,000 = 283 kwh/s ton Efficiency Factors: EF1 does not apply EF2 does not apply EF3 determine after power calculations is completed EF4 Feed size is coarser than 16,000 micrometers, EF5 does Rod Mill Design Calculations 911Metallurgist2023年7月1日 The effect of ball load composition, by varying the grinding media size distribution (eg alternatively by mixing four groups of 195, 38 mm; 195, 50 mm; 38, 50 mm and 195, 38, 50 mm), on the Exploring the effects of a new lifter design and ball mill speed on 2016年1月1日 For open circuit grinding [34,35], there is no disagreement with the calculation of the circulating load and classification efficiency, both of which 2 can be characterized relatively accurately(PDF) Analysis of the efficiency of the grinding process in closed
.jpg)
Study on Partial Replacement of Metal Grinding Ball with Pebbles
2023年4月4日 In addition to the direct consumption of energy from grinding, steel balls have an embodied energy (mining, smelting, and transport), which may increase the circuit’s specific energy by 34 kWh/t, adding to the consumption during the grinding itself because of wear [8] Some ore processing plants have a high grinding media consumption, as is2022年2月24日 The study reveals that the lowest specific energy consumption is achieved when the relative rotational speed of the mill is between 081 and 087; the weighted average diameter of the balls ranges Improving the efficiency of the coal grinding process in ball drum 3 Flame Momentum Calculation 8 4 Kiln Performance Efficiency 11 5 Heat Transfer 13 8 Useful Formulae in Kiln Design Operation 18 9 Cyclone Efficiency PC vessel retention time Calculations 19 10 Grinding Mill Investigation 25 11 Tromp Curve Calculation and Significance 27 13 Ball Mill Study Data 105 14 Ball Mill Formulas 111CEMENT FORMULAE HANDBOOK Green Business Centrethe grinding process intensification Specific energy consumption for the grinding dropped down to 30% Current methods of power consumption calculation of a mill drive do not allow determining the power consumption for ball drum mills with a crosslongitudinal motion of the grinding media A new calculationThe Power Consumption Calculation of a Ball Drum Mill
.jpg)
Analyzing the influence of lifter design and ball mill speed on
2023年10月30日 1 Introduction Ball mills are the most common type of fine grinding equipment They are used in the chemical and pharmaceutical industries and the mineral processing industry for the production of cement []These mills consume enormous amounts of electrical energy (50–60%); consequently, the cost of comminution accounts for roughly 60% of the overall 2023年4月24日 Grinding is the final stage of comminution, which reduces particle size to micron size level The size reduction is achieved by attrition, abrasion, and impact between the ore itself and between the ore particles and grinding media []According to Swart et al [], ball mills are mostly used because of their very high size reduction ratio, although they have a very low Grinding Media in Ball MillsA Review [v1] Preprints2023年11月1日 As shown in Fig 15, the grinding unit consumption of the ceramic medium stirring mill was 317(kWh/t), When the content of −0043 mm accounted for 80% Therefore, the cost of grinding power consumption is significantly reduced by about 5016% by using the new ceramic ball stirring mill system to substitute the original twostage ball millEnergy conservation and consumption reduction in grinding online live calculators for grinding calculations, Ball mill, tube mill, critical speed, Degree of filling balls, Arm of gravity, mill net and gross powerball mill calculations, grinding media filling degree, ball size, mill
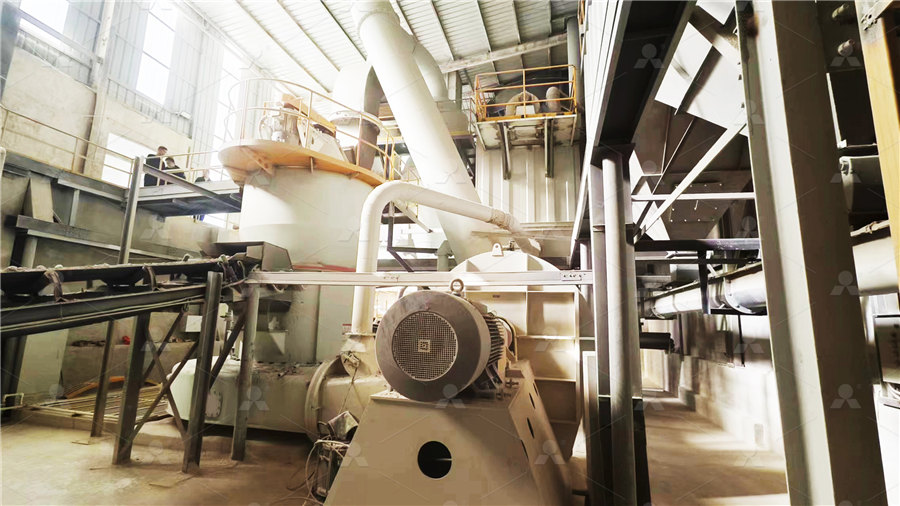
A simple calculation for residency time of grinding balls inside
2 UNCORRECTED PROOFZL Jiang et al/Wear 8669 (2001) 1–4 The weight of a ball is related to its diameter as W D ˆˇ 6 D3 (2) where ˆ is the density of the balls Combining Eq (2) with (1 2015年7月31日 These drawbacks were resolved to some extent by several researchers, who developed alternative methodologies to determine energy consumption during crushing and grinding [9][10][11][12][13][14][15]Kinetic grinding test approach to estimate the ball mill work ranging in diameters from 32 m to 48 m Design and operational parameters of the ball mills sampled are given in Table 1 Table 1 Sampled ball mill’s design and operational parameters range Operating and Design Variables Values Mill diameter 32 – 48 m 1st chamber length 315 – 425 m 2nd chamber length 518 – 1000 mCALCULATION OF THE POWER DRAW OF DRY MULTI–COMPARTMENT BALL 2016年1月1日 The wear of balls used during a grinding process is considered one of the losses that cause an increase in the operating cost allocated to the ball mill [21]A comparison of wear rates of ball mill grinding media
.jpg)
(PDF) Methodologies for the evaluation of grinding media consumption
A Review of the Grinding Media in Ball Mills for , based on pilot Drop Ball Testing (DBT) results has been proposed to incorporate breakage as a potentially significant grinding media consumption mechanism 4 (87) Balls consumption gr/ton kg/h gr/kW h 479 621 527 501 707 604 46 138 146 Sp Wear Constant, k Ed 255 295 2013年7月15日 Crushing and Grinding Calculations April 1962 Additions and spectroscopy as function of ball milling time For low milling times (24 between 29 and 133 were used as (PDF) Energy Efficient Ball Mill Circuit – Equipment Sizing