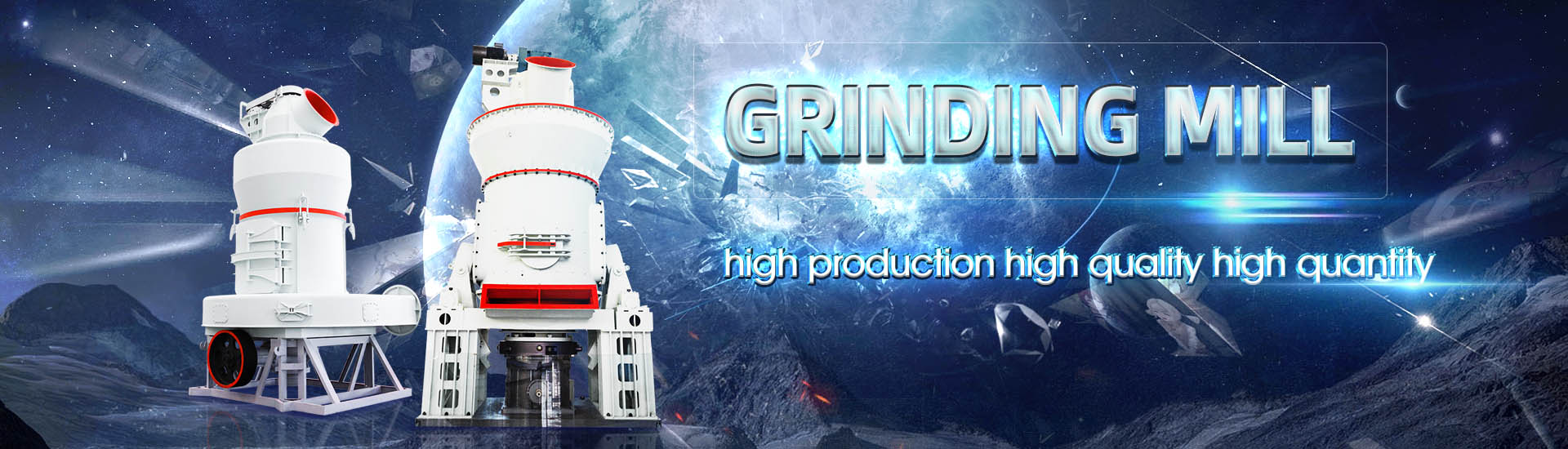
Smooth surface ore mill
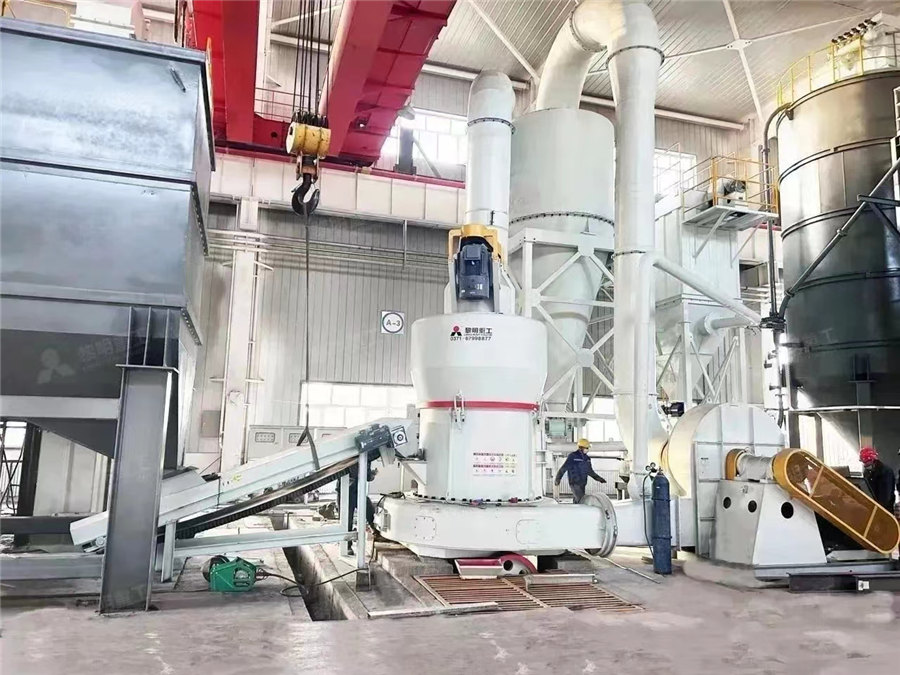
High Pressure Grinding Rolls for Minerals AusIMM
High Pressure Grinding Rolls have been used for the grinding of diamond and iron ores since about 1988 There are now about 40 machines operating worldwide in these industries This For some very fine size reduction applications, the roll surface is smooth The more roll pairs the mill has, the greater the size reduction it can achieve For instance, reducing salt feedstock to Roller mills: Precisely reducing particle size with greater efficiency2024年4月16日 By integrating computer vision techniques for realtime data extraction and employing DualSPHysics simulations for various milling scenarios, including balls only, balls with ore, and balls with slurry, we achieve a high Calibrating the Digital Twin of a Laboratory Ball Mill for 2021年7月1日 In the ore milling process, the ore particles are usually irregular polyhedrons, and the grinding media are often spherical The need for accurate simulation of this process calls DEM investigation of SAG mill with spherical grinding media and
.jpg)
Sepiolite Superfine Powder Grinding Mill SBM
2021年9月29日 Sepiolite superfine powder grinding mill is a highefficiency, energysaving, lowconsumption, and environmentally friendly industrial nonmetallic ore mill The equipment is independently developed and produced by 2016年1月1日 These mills are rapidly replacing the conventional tumbling mill for ultrafine grinding due to higher energy efficiency, low residence time in the mill with relatively sharp cut Stirred Mills – Ultrafine Grinding ScienceDirect2023年7月20日 Ore grinding is a process to further reduce and disperse the ore particle size In the mineral processing industry, ore grinding is the particle size preparation before the Ore Grinding SpringerLink2017年9月1日 The objective of this work is to assess the influence of fine grinding in ball mills and stirred mills on valuable mineral liberation and particle shape characteristics of UG2 ore, a Fine grinding: How mill type affects particle shape characteristics
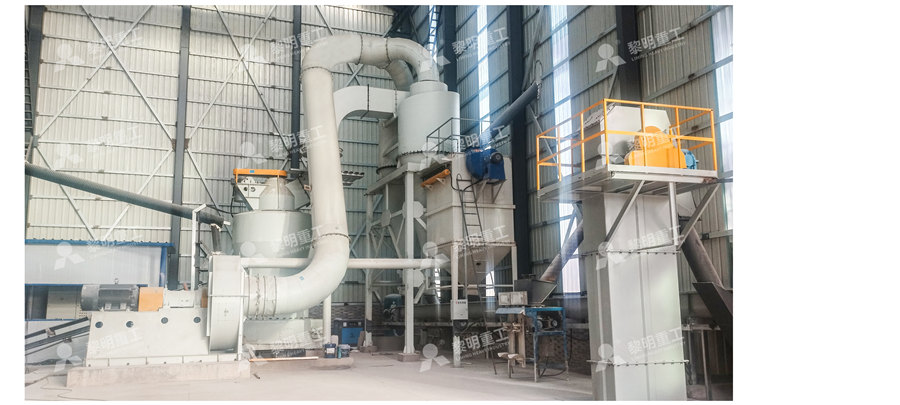
Development of a Novel Grinding Process to Iron Ore Pelletizing
2020年3月28日 Iron ore pellet production requires a fine mineral particle distribution to lead to good agglomerate densification, a smooth surface, and controlled growth in the pelletizing 2024年2月7日 In drum mills, abrasive type of wear occurs on smooth and wave liners when processing hard rock, eg, iron ore with a hardness of 1000 HV in cascade mill operations Abrasive wear is characterized by the fact that the Development MPC for the Grinding Process in SAG The high reflectivity needed may require a smoother starting surface prepared by surface grinding the coil before rolling The surface is too smooth to be measurable by common surface roughness instruments and gloss measurement is the best available technique No 4 finish is produced by polishing the surface with abrasivesMill Finishes ASSDA2023年11月2日 Proper programming techniques are similarly essential A stepover between 50 to 75% of the tool diameter usually delivers a smooth surface Always climb mill, and always offset the cutter from centreline, Achieving the best possible surface finish with face
.jpg)
Stainless Steel General Information Surface Finishes Polishing
A smooth surface is less susceptible to an accumulation of deposits and stainless, which often become focal points for localised corrosion A semidull finish with a uniform grain generally applied to the supplied surface of the mill finish stainless steel No pregrinding is involved, This ultrasmooth surface is less likely to harbour airborne contaminants or moisturethan any other mill finish, and it is easy to clean 5 Surface Uniform non reflective matt surface, can be based on either 2B or 2R mill finishes 1M or 2M Patterned Can be based on either '1' or '2' ex mill finishes* One side patterned onlyChapter 08 Stainless Steel SurfacesSCS is Smooth, Clean Surface, a steel cleaning process that makes hot rolled sheet, plate or coils clean, rust resistant and ready for fabrication or painting It offers fabricators cost and quality savings in laser cutting, welding, painting and tube pipe production at much lower cost than stainless or cold rolledSCS Smooth Clean Surface Prime Fabrication Steel in Sheet, 2023年9月7日 Difficulties and Solutions to Realize Surface Mirror Effect Achieving a mirrorlike surface finish can be challenging due to several factors, including material properties, part geometry, and the chosen surface treatment method Here are some common challenges and solutions to attain a mirror finish: 1 Surface Imperfections:The Ultimate Guide to Achieving Mirror Surface Finishes
.jpg)
Surface Roughness Explained Ra Roughness Chart Get It Made
2022年6月27日 A surface roughness chart can show different types of surface finish with Ra roughness values ranging from 125 μm Ra (very rough) to 04 μm Ra (very smooth) Asmachined Leaving a product with an asmachined finish will ensure the tightest dimensional tolerances, up to ± 005 mm or better2019年9月13日 The surface of the 2Q finish is smooth and free of scale Again, surface roughness is defined by manufacturers Being very similar to the 2H, the applications are almost the same, including but not limited to: Automotive applications; Machines and instruments; Surgical instruments; Mechanically Polished Brushed Stainless Steel FinishesStainless Steel Finishes Explained EN ASTM FractoryWhat is Mill Finish Aluminum? Mill finish aluminum refers to the original, unpolished state of the metal that has not been treated or finished in any way This form of the metal is largely untouched, with the surface often appearing somewhat dull Mill finish aluminum has not undergone any further processing after being produced from raw aluminum through an extrusion processWhat is Mill Finish Aluminum, and How Does it Compare? Gabrian2011年10月20日 Consequently, the gaskets required a very smooth surface finish By comparison, traditional solid or perforated steel core head gaskets with composition facings or graphite gaskets typically required a finish in the 54 to 113 Ra (60 to 125 RMS) range As gasket technology has evolved, surface finish requirements at the OEM level have eased a bitSmooth Moves: Today’s Surfaces Often Demand Different Finishes
.jpg)
Machining Surface Finish: Chart Guide Moseys
Machining surface finish influences the quality, durability and performance of manufactured parts and components For instance, when manufactured products possess smooth surfaces, they resist wear and tear better than finished parts Rod Mill The rod mill is loaded with steel bars as grinding media and comprises five parts: cylinder shell, feeding system, discharge system, main bearing, and transmission system It is suitable for both dry and wet grinding to meet customer needs Materials with a Moh's Hardness of 5512 can all be handled by our millOre Grinding Mill2020年7月14日 Legend Grit #: The size of the abrasive particles used in sanding or grinding Higher numbers correspond to finer abrasives ISO #: The International Organization for Standardization (ISO) number that specifies the Surface Roughness vs Surface Finish RA RMS2024年1月11日 This blog post will delve deep into surface grinding, highlighting its importance, techniques, and applications in modern manufacturing +1(213) 398 9420 +86 ; The grinding process removes excess material and achieves smooth surface finishes, essential in applications requiring finely finished surfacesSurface Grinding: A Guide to the Process and Precision okdor
.jpg)
Mill Smooth Files McMasterCarr
Files do not include a handle but do have a tang that fits into a handle Length does not include the tang Single Cut — Surface has one set of diagonal teeth and is often used with light pressure to slowly remove material and sharpen toolcutting surfaces For technical drawings and 3D models, click on a part number2020年6月22日 Sandblasting will make the surface smooth, but its too harsh for your cast iron pan to handle and the chance of damaging the pan is high Don't remove the seasoning first Some websites recommend using easy off or lye to remove seasoning This is a completely unnecessary stepCast Iron Smooth vs Rough: The Ultimate Guide2023年7月26日 Roughness Also known as surface roughness, it refers to imperfections in surface geometry Since surface finish and roughness is the feature of surface finish that is most frequently described, measured, and computed, many people use the term “Surface Finish” to refer to roughnessSurface Finish and Roughness in Machining – Ultimate Guide 2021年11月8日 Illite ore industrial grinding mill machine can grind illite into powder up to 3000 mesh Illite has the characteristics of smooth, bright, soft, good insulation because of its small particle size, large specific surface area, and unique Zeng bond structure, illite powder can be used as a lowcost adsorbent in Illite Ore Industrial Grinding Mill Machine SBM Ultrafine
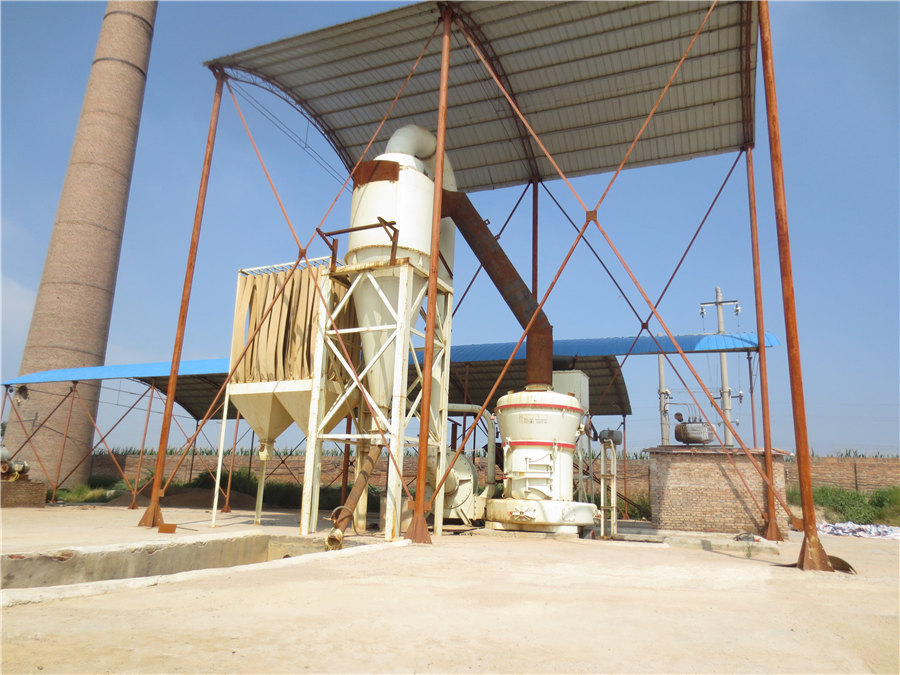
Surface Finishing for CNC Milling: A Complete Guide FacFox Docs
2023年3月16日 Surface finishing is an important aspect of CNC machining that can enhance the quality and performance of your parts In this post, we will introduce some of the types and benefits of surface finishing for CNC milling What is surface finishing? Surface finishing is the process of applying a coating, treatment, or texture to the []2021年5月6日 To ensure a good surface finish, use a special wiper insert that has a modified nose radius with larger corners to wipe the surface smooth This will allow you to cut at a faster feed rate 7 Use the Right Technique Creating a chip that is thicktothin is what you want Your technique plays a vital role in getting smooth surface finishes10 Tips for Better Surface Finish For Your CNC Machining PartsThis ultrasmooth surface is less likely to harbour airborne contaminants or moisturethan any other mill finish, and it is easy to clean 5 Surface Uniform non reflective matt surface, can be based on either 2B or 2R mill finishes 1M or 2M Patterned Can be based on either '1' or '2' ex mill finishes* One side patterned onlyChapter 08 Stainless Steel Surfaces IMOA2016年8月9日 I thought it was because a perfectly flat/smooth surface was not possible with modern materials on metal so it was better to mill the face to achieve a consistent surface? Quote; Link to comment Share on other sites More sharing options stage1350 Posted August 10, 2016 stage1350Why are putter faces milled and not just smooth flat
.jpg)
How to make a very smooth surface on the mill?
2010年6月13日 I need an even smoother surface than a face mill can provide My face mill can make a mostly shiny surface, but still leaves tiny grooves that you can't feel, but can see I also noticed a larger groove spacing approx 1" apart, maybe from me turning the hand wheels on the stage in a not perfectly even mannerSo far, you’ve probably gotten the idea that maybe you should always climb mill After all, it leaves a better surface finish, requires less energy, and is less likely to deflect the cutter Conversely, manual machinists are often taught never to climb mill because it’s dangerous to do on a machine that has backlashClimb Milling vs Conventional Milling (Sneaky CNC Tricks)Mill File: Rectangular, Smooth Cut, 10 in Lg without Tang, rectangular files run in diagonal rows and one direction to sharpen edges and produce smooth surface finishes Tapered files get steadily narrower from the heel to the point for filing in Rectangular, Smooth Cut, Mill File 1NFN71NFN7 Grainger2022年8月4日 Surface finishes rely heavily on the manufacturing process, and exceptionally smooth surface finishes typically require further processing, such as grinding or polishing Because more processing would incur greater costs, the engineer or designer must avoid imposing unduly low roughness requirementsA Complete Guide to Understand Surface Roughness in
.jpg)
Stainless steel and carbon steel surface finishes Montanstahl
Our profiles in their standard mill finish can be classified under surface class Sa 3 of the EN (ISO) 85011 Cold worked profiles from Montanstahl have processrelated a very smooth surface and are already with the standard mill finish suitable for a wide range of aesthetic applications2023年4月27日 Milling and Turning: These standard machining processes create a uniform surface texture and can achieve specific surface roughness values depending on tool selection and cutting parameters Grinding: This process uses an abrasive wheel to remove material and achieve a smooth, highprecision surface finishA Guide to CNC Machining Surface Finishes Kwan Fung Precision2017年9月19日 The smooth face has always done a very respectable job sinking big nails, and has whacked in its share of finish nails as well The ability to do so without leaving a pulverized piece of trim in its wake makes the smooth face my hammer of choice For me, Smooth Face comes out on top Opinions may vary Trust meMilled Face vs Smooth Face Hammer Smackdown!Steel mill finish refers to the untreated surface of steel products directly from the steel mill It is the result of the rolling or extrusion process used to shape the steel Steel with a mill finish usually has a slightly rough texture, small imperfections, and a grayish appearanceUnderstanding Mill Finish: Everything You Need to Know
.jpg)
Keeping it Smooth: Optimizing Surface Roughness in
Surface roughness, also known as surface finish or surface texture, is a critical feature that can distinguish a rough looking prototype from a polished finished product In this article, we’ll explain what surface roughness is, how it’s 2024年6月14日 I keep a 2" diameter 90 degree facemill in my shop as well as a 3" Glacern FM45 45 degree face mill The FM45 sees a lot more use for sure One last thought about face millsthey're horsepower hogs Don't try to use Face Mill Speeds and Feeds [Calculator, 45 or 90 2024年7月10日 Face milling is a key process for smooth surface and precision machining of parts, and selecting the appropriate face milling cutter and optimizing the process are crucial As a professional milling service provider, Face Milling 101: Everything You Need To Know BOYI2007年5月4日 Go in two directions Rough in x and y then finsh in x and y Do not move depth when changing direction on finish pass Flat is a relative term and you will never get a flat surface on a mill or lathe like you get from grinding and lapping Which makes think you can take a piece of fine sandpaper on a surface plate and hand dress the ridges offFacing and getting a FLAT surface
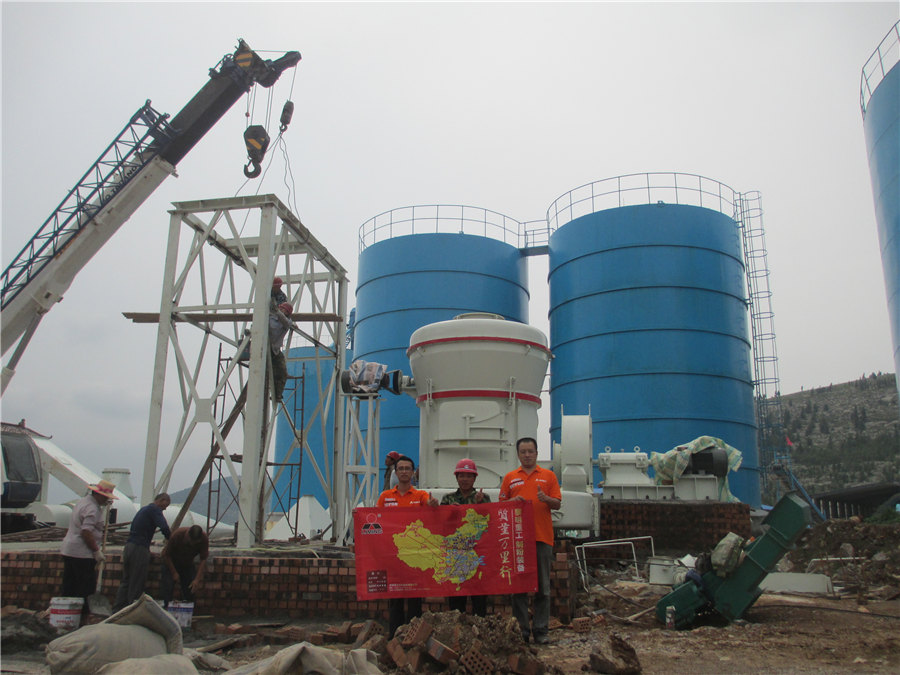
Smooth clean surface Wikipedia
Smooth clean surface (SCS) is a process applied to hot rolled sheet metal and coils to remove nearly all mill scale and clean the steel surface The SCS process feeds hot rolled sheet steel, either as individual blanks or as a continuous strip that is 2020年12月1日 In simple terms, qualifying the surface is the process of removing microscopic errors on the workpiece’s surface to make the surface as uniform as possible When this task can be done, it is always a good practice for machinists However, if you’re working with a die cast material or a forging, qualifying the surface may not be an optionThe Facing Operation In Machining, Explained Winndeavor2023年3月20日 Metal surface finishing offers a range of benefits, depending on the type of finish used Some common advantages include the following: Enhanced Appearance: Many types of metal finishing processes can improve the look of components and add aesthetic appealFinishes such as anodizing and powder coating are especially effective, as they can give metals a Get the Perfect Finish: A Guide to Metal Surface Finishing2020年2月18日 An "upcut end mill" removes the chips in an upward direction, which creates clean pockets at the cost of a slightly rougher top surface, like tearing out some of the plywood veneer on the top surface, but leaving a clean bottom surface as it mills through it If a smooth bottom to a pocket is the goal, upcut is generally the ideal C End Mill Comparison Guide MatterHackers
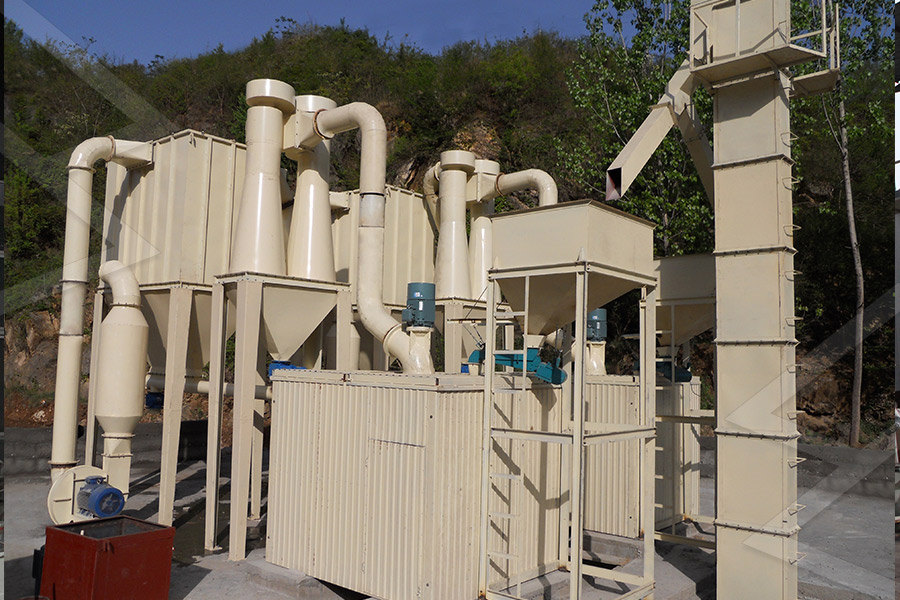
Development of hematite ore pellet utilizing mill scale and iron ore
2018年1月1日 Development of hematite ore pellet utilizing mill scale and iron ore slime combination as additive January 2018 Journal of Mining and Metallurgy Section B Metallurgy 54(00):88Surface Finishing Treatment After milling, surface finishing and treatment are crucial to enhance the final product’s appearance, durability, and functionality How to achieve desired surface finishes To get the desired surface finish on aluminum parts, one must use a mix of precision milling techniques and apply postmilling finishesThe Ultimate Guide to Aluminum Milling: Tips, Tricks, and