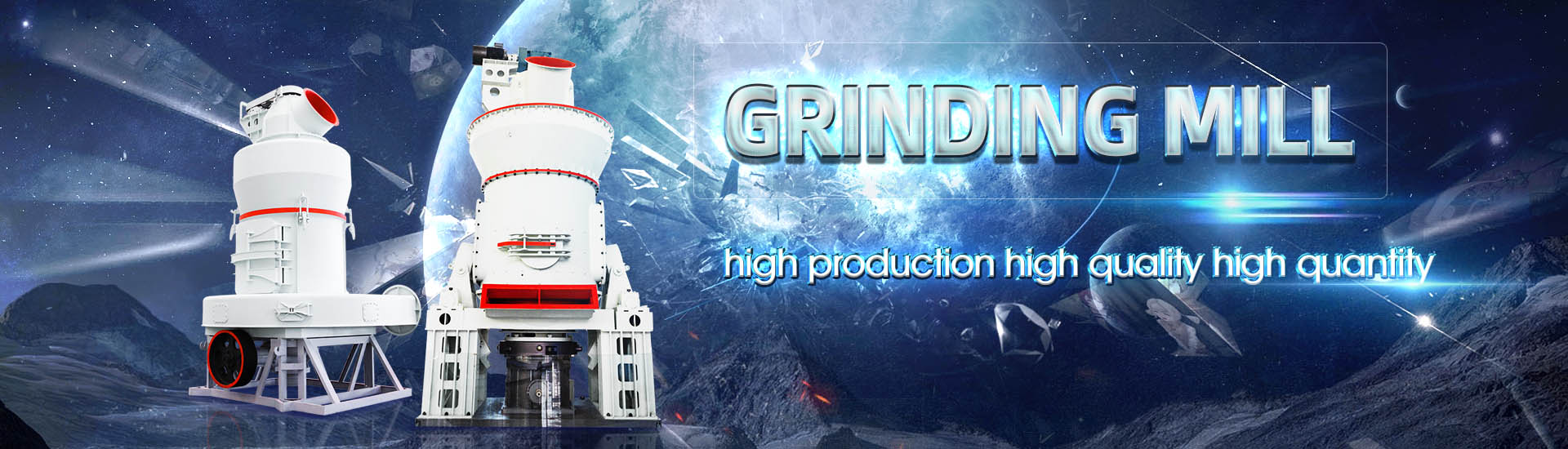
Biomass coal grinding equipment
.jpg)
Biomass Pulverizer Biomass Grinding Machine
Our energy pulverizers and biomass grinding machines are capable of grinding, crushing, and pulverizing materials to a very fine; granulated product for pelleting Stedman’s extensive line of size reduction equipment makes us a valuable Ecostan® manufactures biomass briquette pellet machines, offering biomass solutions for renewable energy Explore briquetting, pelletizing, shredding, moreEcostan® Manufacturer of Complete Biomass SolutionsFind your biomass mill easily amongst the 21 products from the leading brands (Retsch, Fritsch GmbH, Bühler, ) on DirectIndustry, the industry specialist for your professional purchasesBiomass mill All industrial manufacturersContinental Biomass Industries (CBI) engineers biomass chippers and grinders around the goals of environmental and economic efficiency CBI’s equipment is designed to keep biomass out Biomass Chippers and Grinders Terex CBI
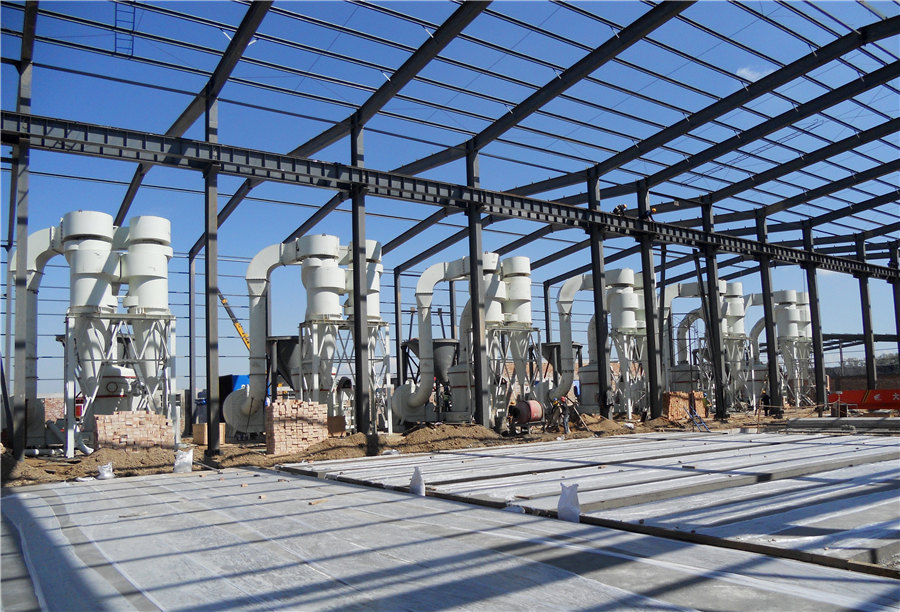
Horizontal Grinders Industrial Wood Chippers
2024年11月8日 CBI machines have been purposebuilt to outproduce, outperform, and outlast anything in the market since 1988 CBI completely reimagined the value curve by producing the ultimate material processing Cofiring technology that achieves a very high woody biomasstocoal ratio has been developed This paper presents the results of experiments on newly developed biomass pulverizers and Development of Woody Biomass High Ratio CoFiring Technology 2024年7月23日 Biomass chippers and grinders play a crucial role in preparing wood waste for energy production These machines reduce large pieces of wood and forestry residues into From Wood Waste to Green Energy: The Power of Biomass Since 1976, we have focused on manufacturing grinding equipment that turns lowgrade materials like wood waste into valuable fiber commodities like wood fuels The United States is currently the largest producer of electricity from Wood Waste Grinders for Biomass Power Plants
.jpg)
Gasification of Coal and Biomass Mixtures Solid Fuel Chemistry
2023年11月24日 Coal ash mainly consists of SiO 2, Al 2 O 3, and Fe 2 O 3The SiO 2 content of the ash of various coals varies from 405 to 503%, the Al 2 O 3 content, from 129 to 324%, and the Fe 2 O 3 content, from 55 to 177% [5, 6]The concentrations of magnesium, alkalis, phosphates, and sulfates in coals are usually low The composition of plant biomass and its IEA Clean Coal Centre – Optimising fuel flow in pulverised coal and biomassfired boilers 10 1 Introduction Increasingly stringent environmental legislation and an obvious need to be economically viable mean that operators of fired power plants are constantly striving to improve ovecoal rall plant performance (Rodriguez and others, )Optimising fuel flow in pulverised coal and biomassfired boilers2020年7月15日 The elemental composition of coal and biomass provides significant parameters used in the design of almost all energy conversion systems and projects The laboratory tests to determine the elemental composition of coal and biomass is timeconsuming and costly However, limited research has suggested that there is a correlation between parameters obtained from Predictions of elemental composition of coal and biomass from 2024年3月25日 Lignocellulosic biomasses, mainly forestry and agricultural residues, are inexpensive, available and attractive to reduce the dependence of the world on fossil fuels However, before their processing in biorefineries, they must undergo a pretreatment to allow access to the desired compounds of interest (cellulose, hemicellulose, or lignin) However, the Combination of Technologies for Biomass Pretreatment: A Focus
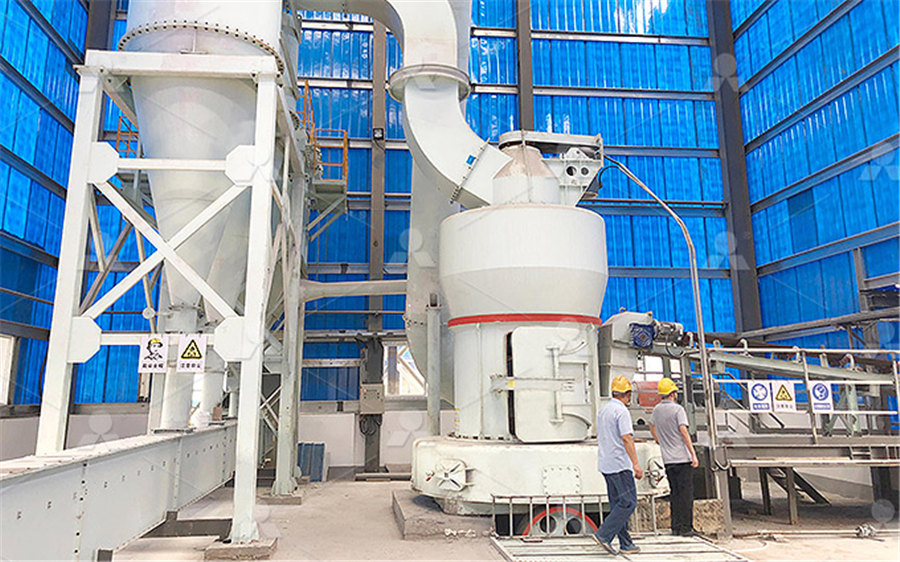
Grindability and combustion behavior of coal and torrefied biomass
biomass in coal facilities, such as that the equipment designed to burn coal should be able to easily use biomass as well, or a stable and cheap flow of biomass is needed to sustain a biomass cofiring system The costs of biomass acquisition and transportation will determine to a large extent the economic feasibility of cofiring Furthermore 2002 Coal grinding plant (LM 232 D) for grinding wood pellets for power stations 1992 Central coal grinding plant (LM 263 D) for the production of lignite (brown) coal dust 1985 Delivery of first selfinerting coal grinding plant (LM 212 D) for the steel industry 1980 Delivery of first modular coal mill (LM 263 D)Loesche Grinding Technology for the Power IndustryThe ultrafine grinding system manufactured by AGICO is mainly used for grinding pulverized coal and cement To meet the need for further grinding and 3D printing, in 2015, our company built an ultrafine powder grinding production line of 12t/d — 20t/d The ultrafine grinding mill is the important equipment in this production lineGrinding Mill Grinding Equipment Cement Mill AGICO2020年7月20日 Grinding mills in a largescale coalfueled power plant are formed of four core parts: the coal dryer, the coal handling and transportation system, the coal sieve, and the grinding mill [56,57](PDF) Torrefied Biomass as an Alternative in CoalFueled Power
46.jpg)
Dry milling machines Qlar
Coal CokeFired Power Plants your onestop destination for weighing components and spare parts dedicated to our weighing and feeding equipmentA mill is essentially a type of grinding equipment, wherein a source material is crushed by means of headon collision with a hard ball or by shearing attrition with a rotating hard ball Currently, there is no standard grindability test for biomass Several studies used the HGI test for coal on biomass [36–41]Grinding Equipment an overview ScienceDirect Topics2021年4月20日 Cofiring coal and biomass in existing power plants facilitates influential advancement in the use of renewable energy resources and carbon emissions reductionExperimental Study and Design of Biomass CoFiring grinding, leaching, blending, pelleting, or packaging for transportation to a biorefinery Conventional Biomass Feedstocks Wood and wood pellets, corn kernels, sugar cane, and other biomass materials that are harvested after a primary crop has been collected; if not used as biomass, these materials go to waste NextGeneration Bioenergy Biomass Basics: The Facts About Bioenergy Department of Energy
.jpg)
Formulation, Pretreatment, and Densification Options to Improve Biomass
2012年6月11日 In addition, comilling wet biomass material with coal will have a significant impact on the mill heat balance 49 Backreedy et al indicated that the kinetics of biomass combustion are not thoroughly understood, and that modeling of coal/biomass blends is more complex due to gas and two particulate phases, as well as chemical reactions 50 According to 2021年11月9日 In contrast, when a conventional vertical roller mill is used, although the maximum biomass cofiring ratio is limited by the equipment specifications, operating conditions, and the grindability of the feedstock (biomass/coal), the capital costs of installing new equipment are reduced 12,13 Therefore, most power plants that comill coal with biomass use existing Milling Characteristics of Coal and Torrefied Biomass Blends in a Browse our selection of highquality industrial wood waste grinder equipment today We offer grinders, rebuilt motors, motorized Biomass Power; Coal Conversion to Biomass Fuels; Super HiInertia Earning The Trust Of Customers Worldwide Rawlings Stationary Electric Wood Grinding System We specialize in the design and manufacturing Wood Waste Grinder Equipment Rawlings ManufacturingHowever, biomass in bulk has a lower calorific value than the same volume of coal, so efficient, highcapacity ship unloaders, loaders, conveyors and storage and reclaiming systems are needed to maintain power demands, along with raw material biomass processing equipment for reliable streams of feedstockBiomass handling and processing Bruks Siwertell
.jpg)
Sustainable transition towards biomassbased cement
2022年7月1日 For instance, Teixeira et al [38] conducted a comparative lifecycle analysis of biomassbased ash and coal fly ash and found that replacing 60% of concrete with biomass flyash provides the best environmental performance [38] Technological advancement of combustion, grinding, and carbon capture equipmentWall Fired Pulverized Coal Boilers Cement / Lime Kiln Direct Injection Cement Kiln Precalciner Biomass and Alternative Fuels Jeffrey Rader has experience in the processing and handling of the following biomass and alternative energy fuels, including: wood chips, waste wood / CD Material, Bark / Hog Fuel, Sawdust, Straw,Biomass Material Handling Systems Equipment JB The use of biomass as a renewable energy source is currently a reality, mainly due to the role it can play in replacing fossil energy sources Within this possibility, coal substitution in the production of electric energy presents itself as a strong alternative with high potential, mostly due to the possibility of contributing to the decarbonization of energy production while, at the same Torrefied Biomass as an Alternative in CoalFueled Power 2021年10月28日 CO2 emissions from coal power generation could be reduced by maximizing the amount of torrefied biomass that can be used in pulverizedcoalfired power plants In this study, to evaluate the milling performance of Milling Characteristics of Coal and Torrefied Biomass
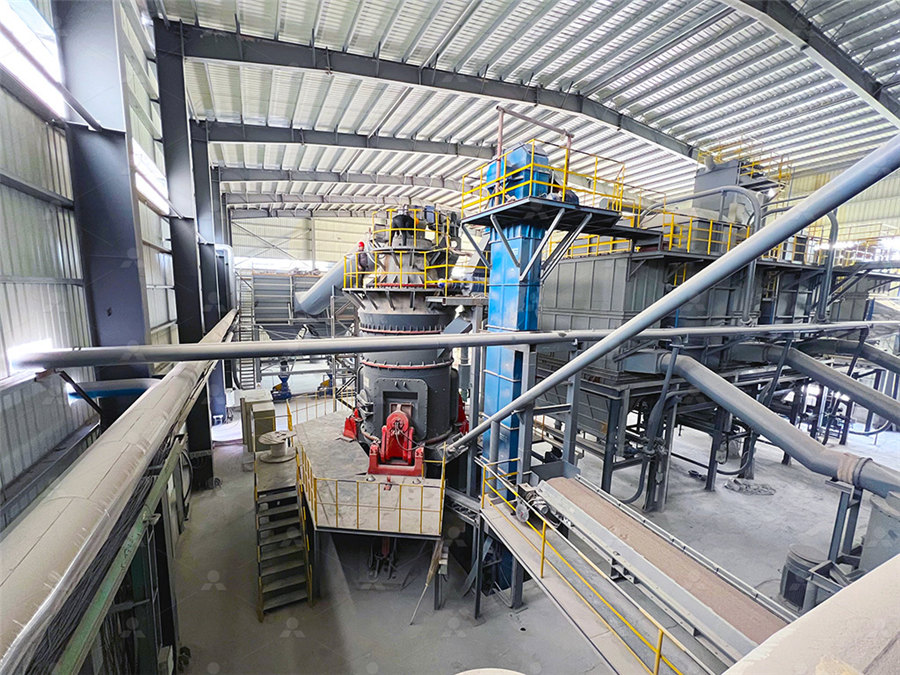
Comprehensive Overview of Hydrogen Production via
2022年10月6日 extensive (such as grinding of coal and drying or preparing a feeding coal slurry ) , ( 2 ) multi stage cleaning of raw syngas (eg, removal of particulate matter , dust, and sulphur,) andout As a result, the grinding capacity for woody biomass has exceeded the coal grinding capacity A load changing ratio of 1530%/min has also been achieved This modification to the pulverizer structure can be easily reversed, returning the pulverizer to its original configuration to allow coal grinding if required The newly developedDevelopment of Woody Biomass High Ratio CoFiring Technology 2015年2月25日 Operational results In delivery state, the mill MPS 190 was equipped with a static classifier of type SLK and designed for grinding a coal flow of 1278 kg/s with a grinding fineness of R009 = 20 per cent (residue on a screen 90 à‚µm) related to the coal parameters HGI = 55à‚°H, moisture = 9 per cent and ash content = 135 per centTop tips for switching a coalfired power plant to biomassSupplier of Radio Grab, Clamshell Grab, Biomass Pellet Plant, Biomass Machine, Wood Pellet machine, Boiler Feed System, Boiler Dozing system, Servoday Plants Equipments Limited At your Service Since 1969 Servoday Plants Equipments Limited Plot No 368283, GIDC Phase III, Dared,Wood Biomass, Rice Straw, Alfalfa Pellet, Making Plant Machinery
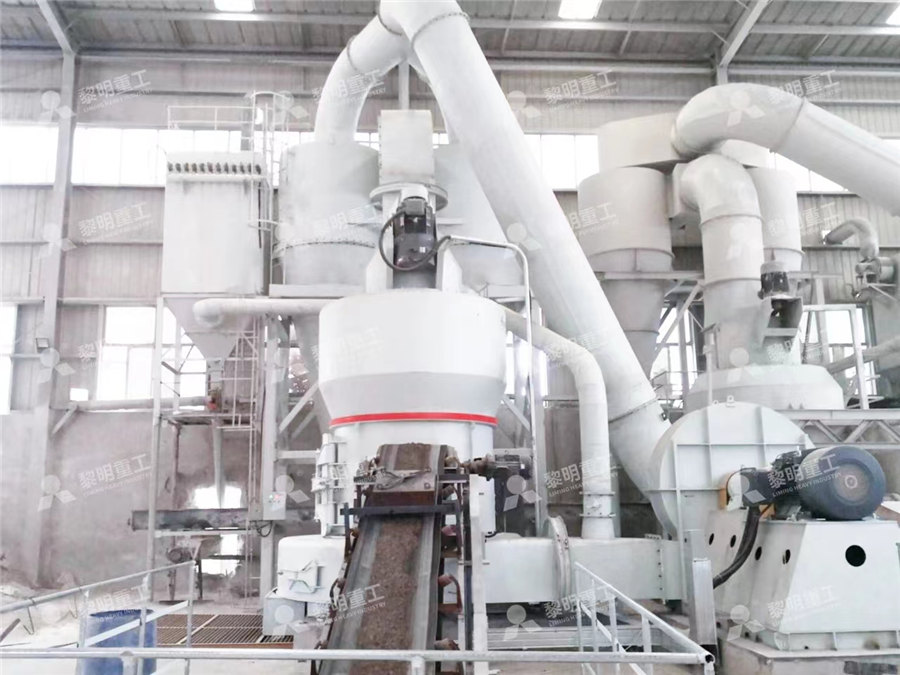
Life cycle cost assessment of biomass cofiring power plants with
2021年4月1日 Next, we describe in detail the method of delivered biomass/coal cost The relevant parameters and components of the fuel used are summarized in Table A1, Table 2, respectively Table 2 For example, new biomass grinding equipment and simple boiler modification are implemented in the direct cofiring plants However, 2020年7月2日 The energy demand for the grinding process was determined and it was shown that drying temperature, grinding system, and mainly type of biomass affects the grindability Raw material specific Impact of the Drying Temperature and Grinding Technique on Biomass 2019年1月1日 Torrefaction is a thermal pretreatment process carried out in an inert environment within the temperature range of 200–300 °C to increase the energy density of lignocellulosic biomass to produce solid biofuel with similar fuel properties as coal [1]Lignocellulosic biomass is mainly composed of hemicellulose, cellulose, lignin, and minor inorganic compounds (Ash)Process simulation of an integrated biomass torrefaction and 2016年10月4日 The firing and cofiring of biomass in pulverized coal fired power plants around the world is expected to increase in the coming years Torrefaction may prove to be a suitable way of upgrading Torrefied Biomass Pellets—Comparing Grindability in Different
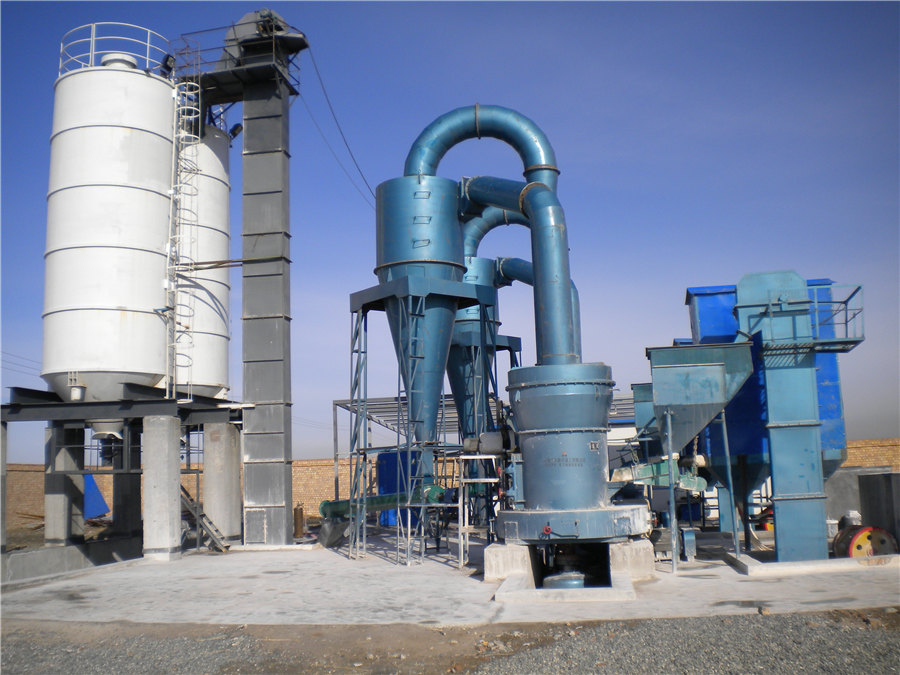
Grindability and combustion behavior of coal and torrefied biomass
2015年9月1日 However, raw biomass, as a potential energy source, also has certain drawbacks, stemming from to its own nature These include its heterogeneity and low energy density (García et al, 2013)Biomass is harder to grind due to its fibrous nature and so it is difficult to reduce to small homogeneous particles, which results in a low combustion efficiency (Bridgeman et al, action properties, storage and grinding conditions, substantial worsening of slagging and contaminating properties According to the results of studying the combustion of the mixtures of annualcycle biomass with highash brown coal 3B (heatbased percentage of biomass — 262 and 562%) at the UralVTI combustion facility [7], the actual NEW TECHNOLOGIES OF PULVERIZED COAL COMBUSTIONThis study also compares the energy consumption involved in preprocessing biomass In the case of grinding energies for both StageI and StageII processes, corn stover and switchgrass consumed Drying, Grinding and Pelletization Studies on Raw 2019年11月1日 Torrefaction changes the chemical compositions of biomass significantly and shifts the fuel properties away from biomass towards coal Under some the energy requirement for grinding torrefied biomass is 10 the amount of available biomass, biomass premium, logistics equipment, biomass moisture content, drying technology Biomass torrefaction: properties, applications, challenges, and
.jpg)
Milling Characteristics of Coal and Torrefied Biomass Blends in a
2021年10月28日 Woody biomass cofiringbased power generation can reduce CO2 emissions from pulverized coal boilers Carbonization of woody biomass increases its calorific value and grindability, thereby One of the most attractive and easily implemented biomass energy technologies is cofiring with coal in existing coalfired boilers In biomass cofiring, biomass can substitute for up to 20% of the coal used in the boiler The biomass and coal are combusted simultaneouslyBiomass Cofiring in CoalFired Boilers National Renewable 135 74 Examples ofbiomass cofiringin pulverized coalfiredboilers 208 522 Underfeed stokers 146 741 Direct cofiringofdemolition wood waste with coal, Ge1derland Power Station Impact ofash on the flue gas cleaning equipment in biomassfiringsystems 272 851 Introduction 272 852 The impact ofcofiringon electrostatic precipitators The Handbook of Biomass Combustion and Cofiring2012年12月1日 PDF Torrefaction is a thermochemical pretreatment process at 200–300 °C in an inert condition which transforms biomass into a relatively superior Find, read and cite all the research you (PDF) A review on advances of torrefaction technologies for biomass
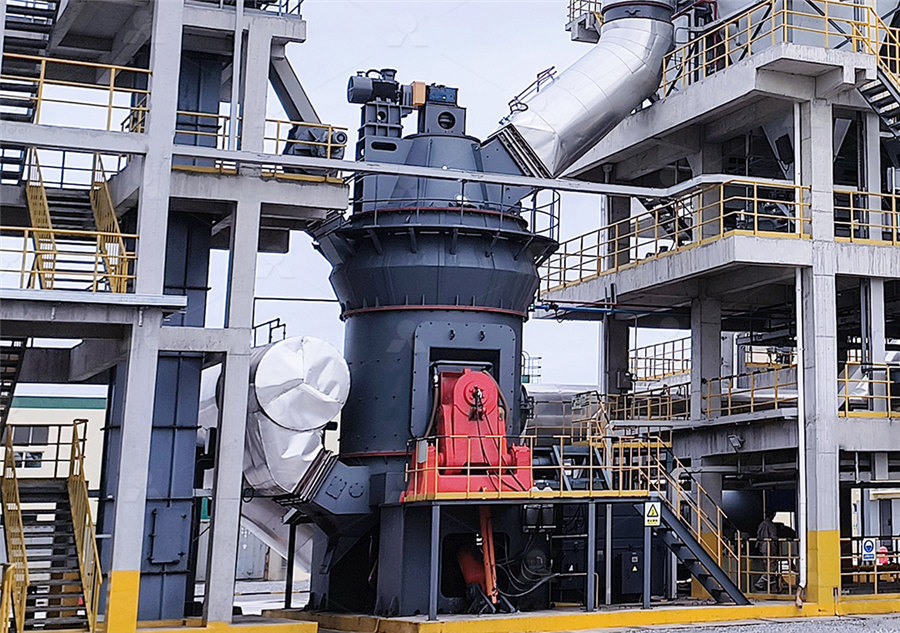
Grindability of torrefied wood chips and wood pellets
2018年12月15日 If torrefied biomass has to be used in the existing coal boilers, the grindability of torrefied biomass needs to be determined a commonly used design parameter of grinding equipment [25] The grinding of raw biomass has been 2021年5月17日 Growing concerns over climate change have prompted the quest for renewable energies to mitigate adverse impacts caused by the excessive use of fossil fuels In particular, using waste and biomass as fuel precursors is currently under active research Pyrolysis is a thermal conversion in an inert atmosphere, involving the rapid heating of feedstocks to Microwave pyrolysis of coal, biomass and plastic waste: a review 2021年1月1日 Compared to coal, biomass has higher VM content and lower FC content For example, the VM content in coal and biomass are normally in the ranges of 0550 wt% and 6788 wt%, Thus, the consumed energy of grinding biomass undergoing torrefaction can be largely reduced Download: Download highres image (638KB)Progress in biomass torrefaction: Principles, applications and