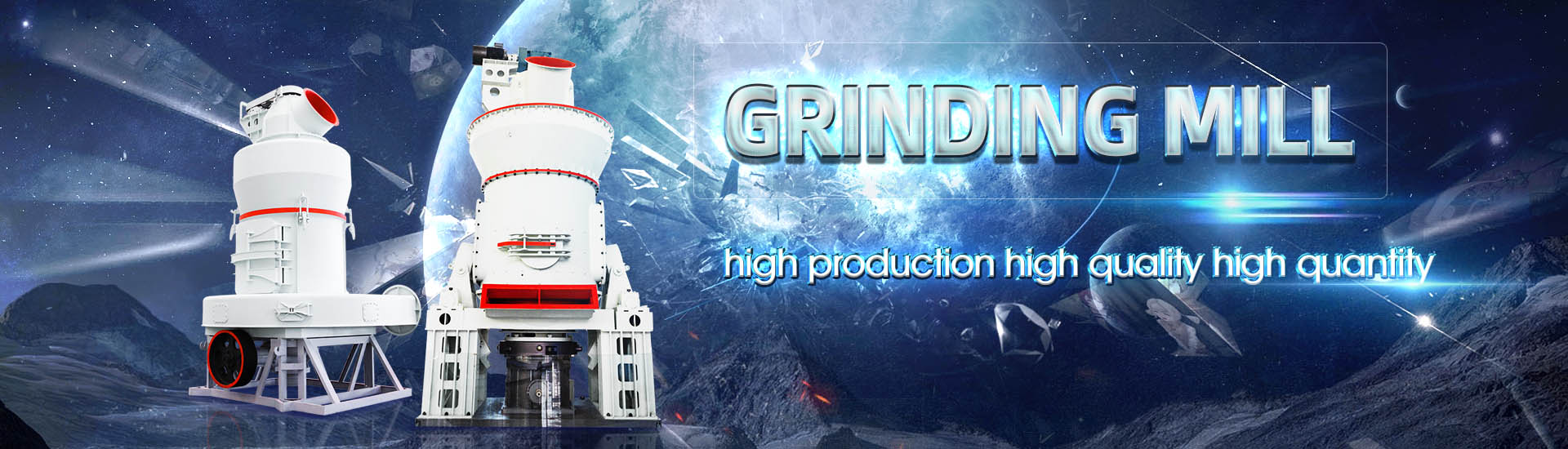
Cement mill second bin continuous forging treatment method
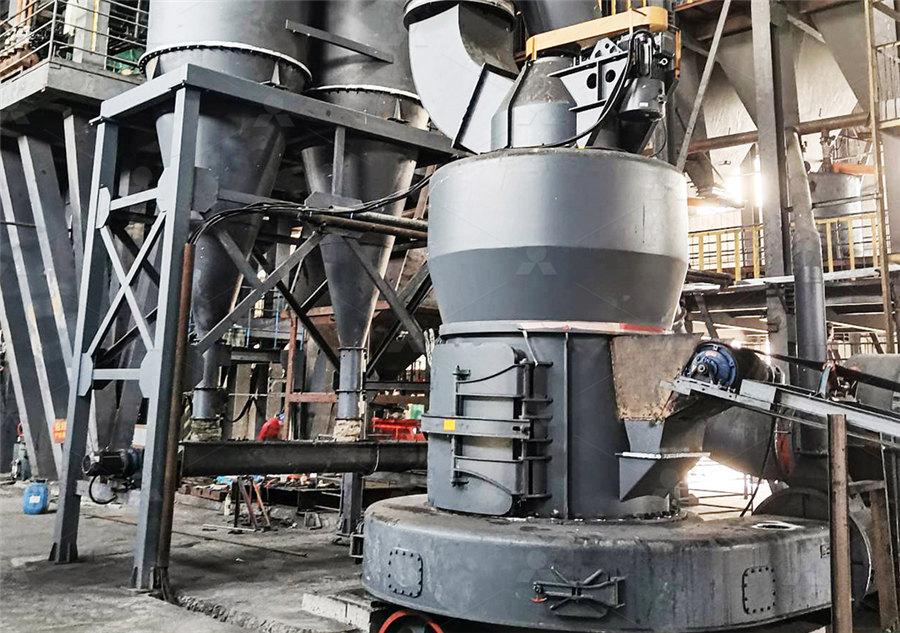
OPTIMIZATION OF CEMENT GRINDING OPERATION IN BALL MILLS
Operation and Elements of a ClosedCircuit Ball Mill System Cement ball mills typically have two grinding chambers The first chamber is filled with larger diameter grinding media andlined The first practical trials in Asia with cement grinding using Loesche mills showed poor running behaviour of the mill owing to unsatisfactory formation of the grinding bed The application of 2 µm 5 µm Loesche2012年6月1日 The paper presents an overview of the current methodology and practice in modeling and control of the grinding process in industrial ball mills Basic kinetic and energy Grinding in Ball Mills: Modeling and Process Control ResearchGate2004年12月1日 This paper compares and investigates the effect of process optimization and use of grinding aid on the operational capacity and blaine of final product in two cement mill Optimization of continuous ball mills used for finishgrinding of
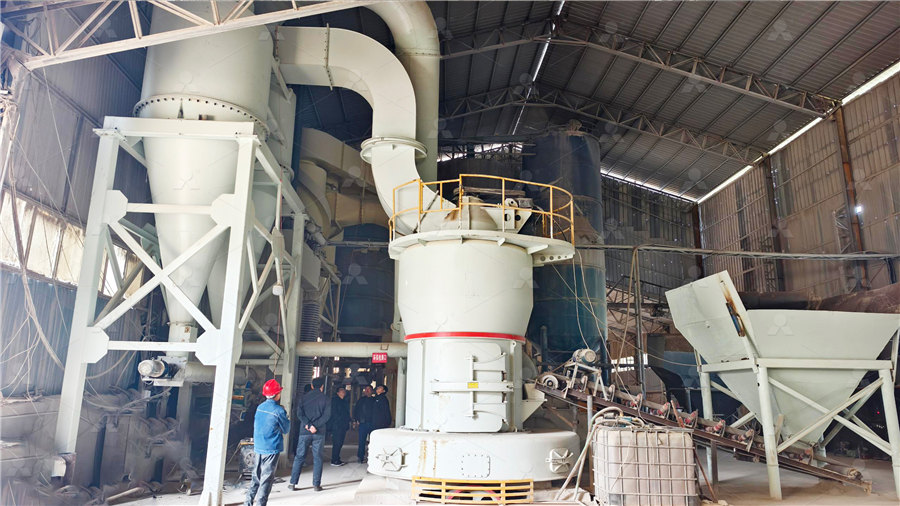
Energy and cement quality optimization of a cement grinding circuit
2018年7月1日 This study aimed at optimizing both the energy efficiency and the quality of the end product by modifying the existing flowsheet of the cement grinding circuit As a general 2020年3月1日 Batch grinding kinetics with assumptions is applied to continuous milling • The grinding performance or the size reduction is related to milling conditions • The scaleup effect A scaleup and design basis of continuous tube mills in cement 1987年8月1日 Cement manufacturing process is now operated with the aid of various control systems, such as raw meal composition control, kiln control and mill control Those systems Optimization of Cement Manufacturing Process ScienceDirectAbstract Based on a dynamical model of the grinding process in closed circuit mills, efficient efforts have been made to optimize PID controllers of cement milling The process simulation OPTIMIZING THE CONTROL SYSTEM OF CEMENT MILLING:
.jpg)
Optimization of Cement Grinding Operation in Ball Mills PEC
Operation and Elements of a ClosedCircuit Ball Mill System Cement ball mills typically have two grinding chambers The first chamber is filled with larger diameter grinding media and lined 2024年2月4日 Deterioration and unpredictable service performance can result from damage to continuous, reinforcing RP/C fibers Forging materials outperform composites in almost all physical and mechanical property areas, which is the basis for achieving good comprehensive performance of large forgings after heat treatment Aug 22, 2024What is Forging? The Complete Guide to Forging2004年12月1日 During the last decade, semifinishgrinding plants have been used more and more for the energy efficient grinding of highquality cement In 1999, it was found that by decreasing the ball charge Optimization of continuous ball mills used for finishgrinding of The principal raw materials for cement manufacturing are: Limestone; Silica and alumina from basalt , shale or sand; Iron from iron ore or steel mill scale Sand stone; Pumice (volcanic ash for Portland Pozzolana cement ) Gypsum Cement Manufacturing Process INFINITY FOR
.jpg)
Cement mill Wikipedia
A cement mill (or finish mill in North American usage [1]) In a twochamber mill, the media in the second chamber are typically in the range 15–40 mm, although media down to 5 mm are sometimes encountered As a general rule, the size of media has to match the size of material being ground: A cement mill is an important component of the cement manufacturing process in a cement plant The cement ball mill is designed to grind materials in either a dry or wet mode, and it finds widespread usage across different production industries, including cement, silicate products, refractory materials, chemical fertilizers, ferrous and nonferrous metal beneficiation, and glass High Efficiency and Large Output Cement Ball Mill YingYong Previous Post Next Post Contents1 COAL PREPARATION AND FIRING11 INTRODUCTION12 2COAL RESERVES13 CHARACTERISATION OF COALS BY CHEMICAL131 31 Major components132 32 Minor Components14 4CHARACTERISATION BY PHYSICAL AND MECHANICAL PROPERTIES141 41 Coal Storage142 42 Variation of Physical and COAL PREPARATION AND FIRING INFINITY FOR CEMENT EQUIPMENT2021年8月28日 Distribution of dust emissions at bag filters in the cement mill section no1 (mill filterpoint A and separator filterpoint B, Figure 1) of the analyzed cement plant(PDF) Dust Emission Monitoring in Cement Plant Mills: A
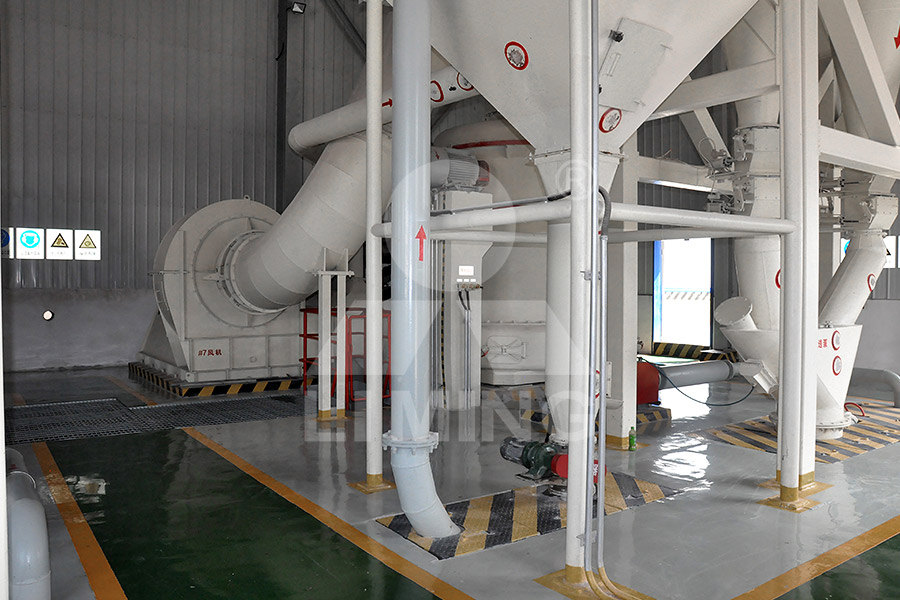
A novel selflearning fuzzy predictive control method for the cement
2023年4月1日 The quality and ratio of clinker, the fineness of cement are key factors affecting the strength of cement In order to realize the target tracking control of cement strength, a selflearning fuzzy predictive control algorithm is proposed to calculate the adjustment variables of cement grinding process Considering the serious hysteresis of cement strength detection, the 2022年12月13日 A Review on Pollution Treatment in Cement etc, is inevitable due to the continuous increment of population and Based on the predictions, cemen t consumption will r each up to 5800 mill ionA Review on Pollution Treatment in Cement Industrial Areas: storage bin Cement mill storage bin dispatch Raw mill ESP Clinker Cement gas solid Temperature and residence time during cement production Characteristics Value Temperature at main burner >1450°C: material >1800°C: flame temperature Residence time at main burner >1215 sec > 1200°C >56 sec > 1800°C Temperature at precalciner > 850°C Cement Kiln CoProcessing (High Temperature Treatment)in the NonMetallic (Mineral) Industry: Cement Production (All Sizes) Table 13: Limiting values for the pollutants of kiln Source Pollutant Limit value Monitoring Cement kilns Total PM Sum of NO and NO 2 expressed as NO 2 800 mg/m3 Continuous* 50 mg/m3 Continuous* Mercury 005 mg/m3 Periodic PCDD/PCDF 310 ng TEQ/m PeriodicOPTIMIZING THE PERFORMANCE OF FILTER BAGHOUSES AT PORTLAND CEMENT RAW MILL
.jpg)
Reducing Residual Stress in 7050 Aluminum Alloy Die
2008年7月1日 Residual stress and deflection magnitudes plotted as a function of quench type for 7050 forgings heat treated according to Table 2 The asterisk " * refers to the forging numberLearn about the raw mill in cement plants and the basic raw materials Longitudinal stacking method is also termed as “Chevron Method” to improve mix proportion is ground in Raw mill at 110 – 118TPH (Ball mill) to achieve Raw Mill in Cement Plant Cement Manufacturing 2023年4月1日 The quality and ratio of clinker, the fineness of cement are key factors affecting the strength of cement In order to realize the target tracking control of cement strength, a selflearning fuzzy predictive control algorithm is proposed to calculate the adjustment variables of cement grinding process Considering the serious hysteresis of cement strength detection, the A novel selflearning fuzzy predictive control method for the cement Data –Southeast Cement Plant –with inline mill Souteast Cement Plant with inline mill15010050 0 50 100 150 200 250 300 350 2/9/2010 7:12 2/9 FTIR is the reference method but other methods will likely be added as •Portland Cement MACT requires continuous monitoring by October 2013 •There may be some changes in monitoring Continuous Emissions Monitoring in Support of the Cement MACT
.jpg)
(PDF) Minimizing waste using lean manufacturing: A case in cement
2017年4月1日 As an integral part of the infrastructure ecosystem, cement industries play a vital role in Indonesia's development (Amrina Lubis, 2017)This function is becoming more crucial as the Indonesian Mill liners act as a protective shield, absorbing the impact of the grinding media and materials By providing wear protection to critical components, such as the mill shell and the grinding media, mill liners significantly extend the life of the mill, reducing the frequency of replacements and maintenance shutdownsBridging the Gap: Mill Liners in Cement Manufacturing2023年4月23日 Comminution is a very important and resultdetermining step in mineral processing This is because further downstream processes in the beneficiation chain depend entirely on it(PDF) Grinding Media in Ball MillsA Review ResearchGate2022年11月1日 In the context of fullscale continuous cement ball milling, there is no exact rule for ball selection; rather, the cement industry designs the mixture of ball sizes and BSD on the basis of their experience along with recommendations from the mill machine suppliers (eg, FLSmidth, 2012, FLSmidth, 2014) and (empirical) Bond’s approach (Bond, 1958), in which top Impact of ball size distribution, compartment configuration, and
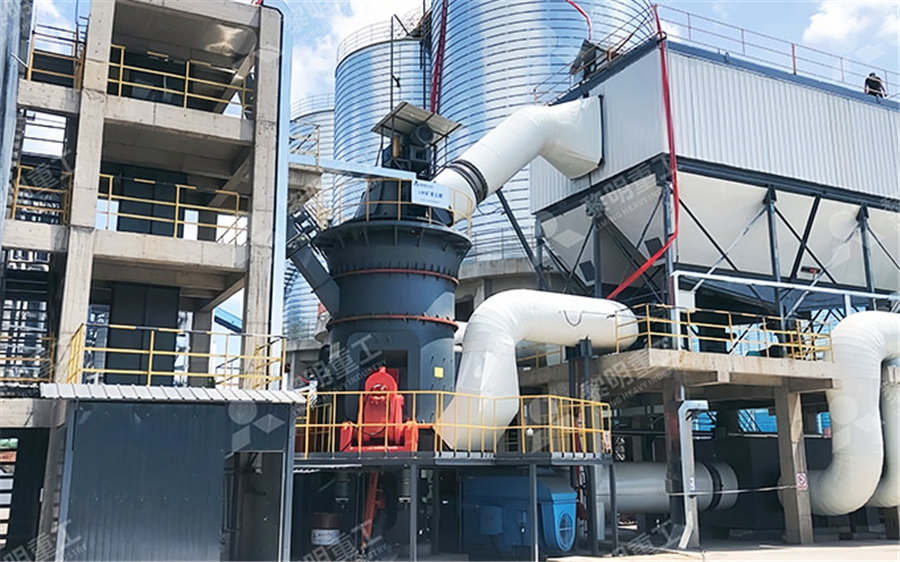
(PDF) Laser shock forginga novel in situ method designed
2023年1月19日 This paper presents a novel hybrid insitu additive manufacturing (AM) method —Laser Shock Forging (LSF), which combines laser shock peening (LSP) with laser melting deposition (LMD)2023年8月1日 This method is based on Newton's second law and a contact model that calculates the change over time between each particle and the particle It has been increasingly employed in recent decades to explore hopper discharge behaviours, eg the mass discharge rate [ 8 , 9 ], particle flow patterns [ 10 ], and internal bulk stresses [ [11] , [12] , [13] ]The segregation of cement clinker particles in a millfeeding 2023年3月14日 The quality and ratio of clinker, the fineness of cement are key factors affecting the strength of cement In order to realize the target tracking control of cement strength, a selflearning fuzzy A novel selflearning fuzzy predictive control method for the cement 2022年12月25日 Soil samples collected from palm oil mill effluentpolluted soil were studied to determine the effect of POME on soil bacteria and enzymes during different seasonsTreatment Palm Oil Mill Effluent (POME) Using Continuous
制粉项目-2023.11.17.jpg)
OPTIMIZATION OF CEMENT GRINDING OPERATION IN BALL MILLS
Operation and Elements of a ClosedCircuit Ball Mill System Cement ball mills typically have two grinding chambers The first chamber is filled with larger diameter grinding media andlined with lifting liners The first chamber coarsegrinds the feed material and prepares it for the second chamber The second chamber is the fine grinding This mill at this time produces two types of cement namely Ordinary Portland Cement (OPC) and Pozzolana Portland Cement (PPC) OPC comprises 90%clinker, 5%additive (limestone) and 5 %( gypsum) PPC comprises 70% of clinker, 2529%% pozzolana and 5%gypsum The design capacity of the mill is 120t/h for OPC cement But currentlyManufacturing process flow 1 Quarrying and Crushing Messebo Cement2008年12月1日 The drying shrinkage of cement mortar containing steel mill scrape (Fe 2 O 3 > 94%) and steel slag aggregate (Fe 2 O 3 = 89%) is lower than that of conventional cement mortar [AlOtaibi 2008 Recycling steel mill scale as fine aggregate in cement mortars3 Factors affecting ball mill performance 4 Ball mill improvements case examples 5 Conclusions question time Introduction Cement manufacture is energy intensive o Cement manufacture consumes typically 3,100 – 3,400 MJ of fuel/t clinker 90 130 kWh / t cement in a modern plant, more for older or less efficient plants;Improvements in New Existing Cement Grinding Mills by Tim
.jpg)
Intelligent Modeling of Cement Plant Mill Unit Using Artificial
PDF On May 13, 2021, Elshan Moradkhani and others published Intelligent Modeling of Cement Plant Mill Unit Using Artificial Neural Networks and Real Data Find, read and cite all the research Previous Post Next Post Contents1 Raw Meal Beneficiation Learning Objectives2 Raw Meal Beneficiation Concepts21 Silo Concepts211 Air Fluidized Silo Systems212 Air Fluidized Silo Systems: Aeration System213 Air Fluidized Silo Systems :Operation214 AirFluidized Silo Concept: Valuation215 Air Fluidized Silo Systems: OverFlow System216 Air Fluidized Silo Raw Meal Beneficiation INFINITY FOR CEMENT EQUIPMENTArticle A DiscreteContinuous Method for Predicting Thermochemical Phenomena in a Cement Kiln and Supporting Indirect Monitoring Edoardo Copertaro1,*, Paolo Chiariotti2, Alvaro Antonio Estupinan Donoso1, Nicola Paone2, Bernhard Peters1, and Gian Marco Revel2 1 Université du Luxembourg, Faculté des Sciences, de la Technologie et de la Communication, Avenue deA DiscreteContinuous Method for Predicting Thermochemical 2021年10月14日 MVR roller mills are used for grinding cement clinker, granulated blastfurnace slag and Pozzolana Bulk materials vary considerably in terms of grindability and abrasiveness The capacities of cement production lines too vary within wide limits to suit individual requirements The system has up to six stationary grinding rollers on a rotating grinding trackMVR roller mill Indian Cement Review
.jpg)
Kiln Exhaust Gas Treatment Options
Most new cement manufacturing facilities are of the dry process design The flue gas is recirculated back to the raw mill using a precalcinator arrangement The kiln gas is used to sweep the mill of finely ground raw feed particles The Raw Mill and Coal Mill: grinding rollers, shafts, pinions, gears, bearings Kiln: kiln tires, riding rings, kiln girth gears, support rollers Forged Finish Grinding Cement PartsForgings for Cement Plants Scot Forge2021年2月15日 Currently, the treatment methods for gangue mainly focus on solid filling coal mining method and cementitious filling coal mining method (Agrawal et al 2020;Sasagawa 2018; Lu et al 2021)Cemented Backfilling Mining Technology for Gently Inclined Coal 2023年12月28日 #1 Hand Forging To give shape to a job by striking it with a hammer is called hand forging or smithing #2 Machine Forging To give the desired shape to a job with the help of a forging machine is called machine forging Press machines, rolling machines, and various kinds of power hammers are included in this category #3 Drop ForgingForging: Types, Methods, Operations, Advantages More The
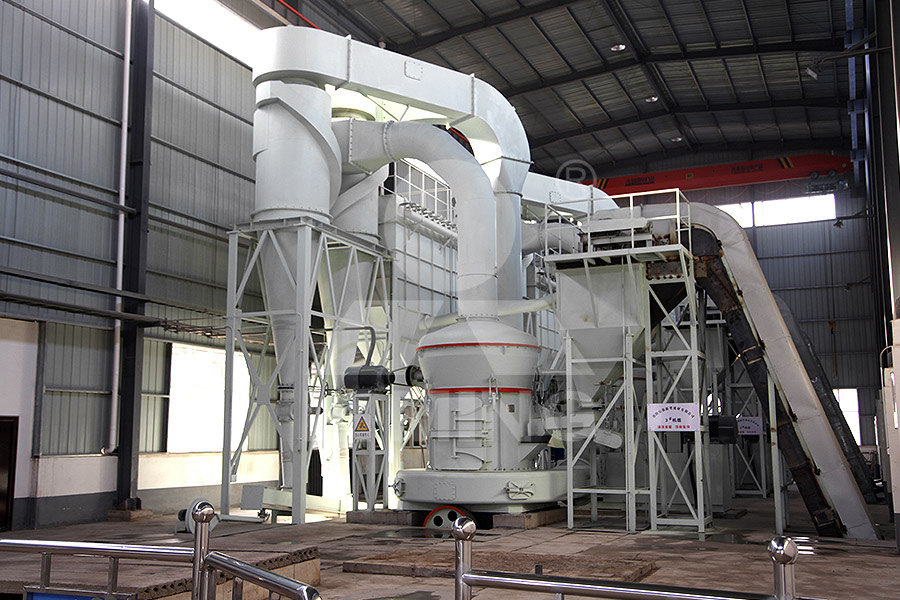
The use of tetraethyl orthosilicate silane (TEOS) for surfacetreatment
Request PDF On May 11, 2016, Yamei Cai and others published The use of tetraethyl orthosilicate silane (TEOS) for surfacetreatment of hardened cementbased materials: A comparison study with 2021年8月28日 This paper is a case study of a Portland cement plant in Romania, the experimental determinations presented mainly focusing on dust emissions in an important sector of the plant (cement mill and related facilities), with dust extraction from two chimneys in working areas (cement mill filtration system and grinder component separator filtration system), as well Dust Emission Monitoring in Cement Plant Mills: A Case Study in 2020年4月1日 Effects of combining ultrasonic microforging treatment with laser metal wire deposition on microstructural and mechanical properties in Ti–6Al–4V alloy Author links open overlay panel Han Ye a , Kun Ye a , Bugao Guo a b , Fangbing Le a , Chao Wei a , Xu Sun a , Guoyong Wang c , Yong Liu a bEffects of combining ultrasonic microforging treatment with 2012年2月9日 However, the waste gas induction point of the raw mill needs to be relocated to the rear of the fan If a tube mill was used in Scheme 1, it would not be able to use up all the kiln exit gas As a result, the mill would require hot waste gas, and this would be in conflict with the requirements of a gas precipitator for low temperature inlet gasTreating Waste Gases World Cement
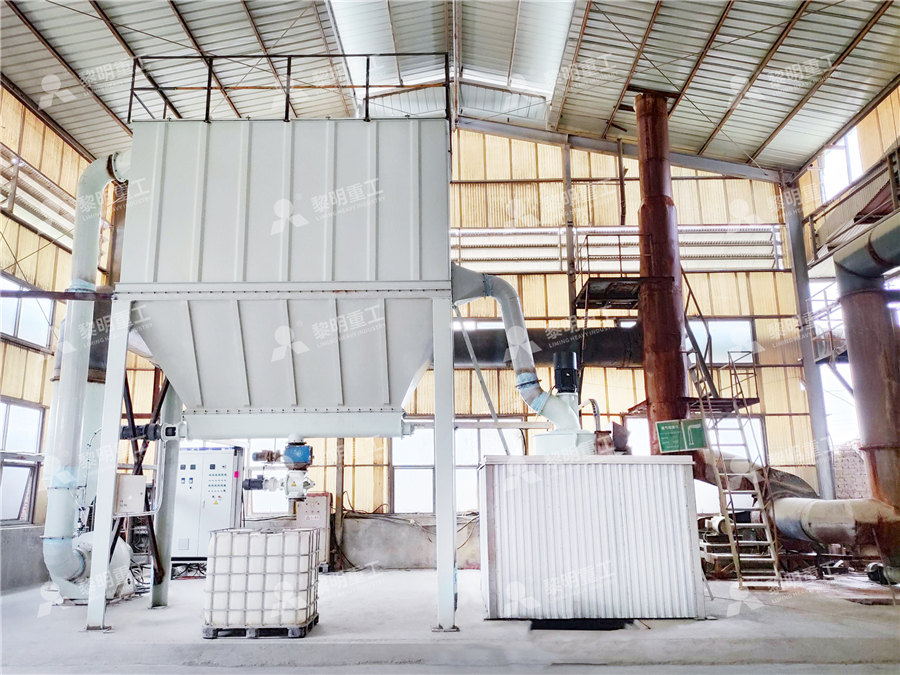
Cement Grinding Optimization PDF Mill (Grinding) Cement
Cement Grinding Optimization Free download as Word Doc (doc / docx), PDF File (pdf), Text File (txt) or read online for free 1 The document discusses optimizing cement grinding circuits It presents tools like the Bond method and population balance models that can be used to analyze and optimize cement grinding 2 It provides details on the typical cement production process