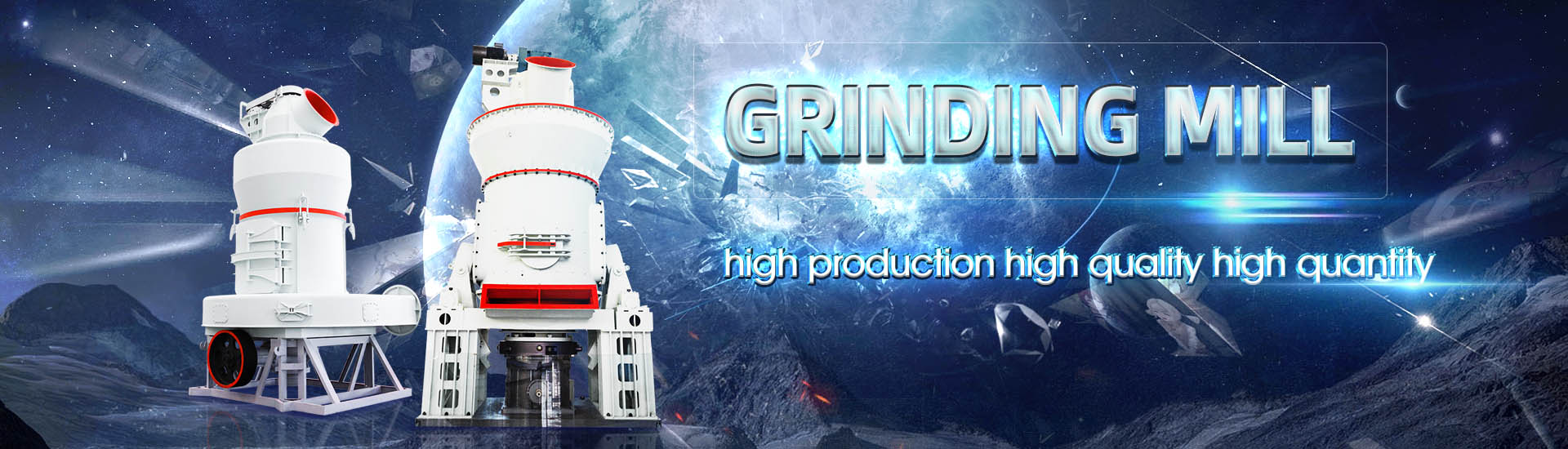
Sequence of cement limestone feeding and mixing process
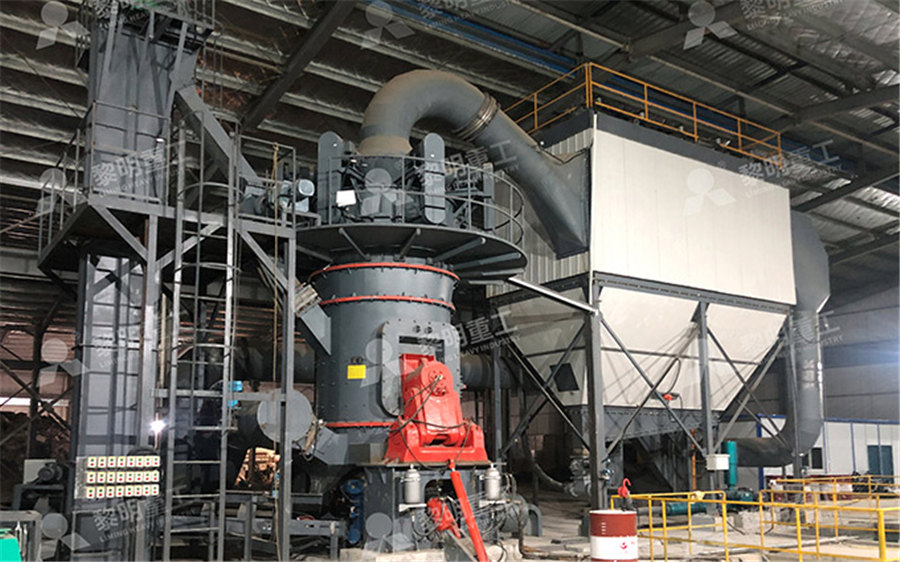
Blending in circular and longitudinal mixing piles ScienceDirect
2004年11月28日 Both circular and longitudinal piles are used for blending raw materials in the cement industry The materials are stacked in a great number of layers, and blending is obtained by reclaiming a mixture from all these layers During the last 10 years, it has become common Limestone is the most important raw material in the manufacture of cement as it provides the main ingredient CaO It is blended with other raw materials such as clay, marl, shale to prepare a HOMOGENIZATION STRATEGY IN THE CEMENT INDUSTRY PEC micrometres, producing “kiln feed” Cement Plant: The Manufacturing Process worldcementassociation 1 Limestone (CaCO3) is taken from a quarry 2 4 3 The limestone Cement Plant: The Manufacturing Process 4 5 World Cement These objectives are achieved by generating the production sequencing of the mining blocks using a sequential branchandcut algorithm The results revealed that up to 15 years, the Limestone Quarry Production Planning for Consistent Supply of
.jpg)
Manufacturing process flow 1 Quarrying and Crushing Messebo
The clinker, additive (limestone, pozzolana) and gypsum are fed by the corresponding belt weighing feeders (dosimat feeders), to a common belt conveyor then the belt conveyor feed The cement production process 1 The Quarry: The cement production process begins with the extraction of limestone and clay from the quarry 2 Crusher and PreBlending: The material is A practical guide to improving cement manufacturing processes 2022年9月27日 This paper will extensively review limestone calcined clay cement (LC3) in terms of the following three aspects: (1) history and composition of LC3 cement paste including the history of calcined clay, different types of A Review on Hydration Process and Setting Time of 2022年5月17日 The mixing process has a significant effect on the concrete properties In this study, an improved threestage mixing approach is proposed to prepare the concrete, which An experimental study on the mixing process and properties of
.jpg)
Limestone Quarrying and Processing: A LifeCycle Inventory
Process flow diagram for limestone processing operations Processing commences with transportation of the (raw) stone from the quarry to the processing facility, as depicted by 2003年6月5日 Required water:cement ratio to achieve a slump of 60 to 70 mm in concretes made with different cements Cement E contained a limestone not conforming to the EN 1971 criteriaThe Use of Limestone in Portland Cement: A State The major raw materials used in the manufacture of cement are Calcium, Silicon, Iron and Aluminum These minerals are used in different form as per the availability of the minerals Table shows the raw materials for Portland cement Manufacture of Cement Materials and Manufacturing 2023年10月19日 222 Fluidity of the fresh cement paste The cement pastes with both superplasticizer and emulsifier addition were prepared by using JJ5 cement paste agitator Feeding sequence of the cement, water, superplasticizer, and emulsifier varied and coded as WSpCE, WECSp, WSpEC and WCSpE respectively, and their feeding sequences and mixing Influences and mechanisms of mixing process on properties of
.jpg)
Concrete: Batching and Mixing Concrete Technology
1 Volume batching 2 Weight batching 1 Volume Batching: In this system of batching, the materials are measured by volume The gauging of cement by volume is most inadvisable as it is difficult to secure accuracy in its measurement as the actual volume of a given weight of cement depends upon how it is filled into a gauge box and whether it is shaken downcement paste agitator Feeding sequence of the cement, water, superplasticizer, and emulsifier varied and coded as WSpCE, WECSp, WSpEC and WCSpE respectively, and their feeding sequences and mixing process are illustrated in Table S1 After the cement pastes were prepared, a simple viscometer shown in Fig Influences and mechanisms of mixing process on properties of 2022年5月17日 21 Material The ordinary Portland cement 525R (PO 525) was selected in this study in accordance with the Chinese standard []The chemical and physical properties of the cement are given in Table 1The Limestone macadam was used as coarse aggregates with a specific gravity of 270 and absorption of 05%, and it had specifications of 5–10 mm, and An experimental study on the mixing process and properties of than 1% In Messebo cement factory the exhaust gas from preheater is used to dry the raw materials from average moisture content of 4% to less than 1% in the raw meal As mentioned above there are four feeding bins in raw material proportioning station (limestone bin, Shale bin, sand stone bin and iron ore bin)Manufacturing process flow 1 Quarrying and Crushing Messebo Cement
]@S0{UDKK%G24F3JGHC.jpg)
Influence of Feeding Sequence on the Fluidity and Fluidity Time
2023年12月19日 To obtain consistent results is to ensure homogeneous mixing of the constituents In this process, the existing guidelines by China Railway Track System (CRTS) The order of feeding sequence in which cement was premixed with water and WRA and then introduced bitumen emulsion proved to have a stable CA mortar with desired fluidity4 天之前 The manufacture of Portland cement is a complex process and done in the following steps: grinding the raw materials, mixing them in certain proportions depending upon their purity and composition, and burning them to sintering in a kiln at a temperature of about 1350 to 1500 ⁰C During this process, these materials partially fuse to form nodular shaped clinker by Manufacturing of Portland Cement – Process and Materials2015年4月14日 Below is a sample band 9 answer to a process task 1 question on concrete production Source: Cambridge English IELTS Past Papers Question– The diagrams below show the stages and equipment used in the cementmaking process, and how cement is used to produce concrete for building purposes AnswerIELTS Task 1 Process Cement and Concrete ProductionThe more complicated the limestone structure, the more sampling and testing required to ensure the delivery of quality limestone to the process In these conditions, the number of core holes will have to increase to define the areas of quality limestone and the geologic structures, and to determine the “mineability” of the depositLimestone Sampling and Testing – Cement and Lime Mines
.jpg)
Cement Manufacturing Process: Know Extraction,
2024年9月10日 Steps of Cement Manufacturing The steps involved in cement manufacturing are as follows: Quarrying: Raw materials such as limestone and clay are extracted from quarries or mines; Crushing and Grinding: The CEMENT PRODUCTION AND QUALITY CONTROL A Cement manufacturing Process Source:civilengineeringforumme The whole process of cement manufacturing in Messebo Cement plant which consists of two separate Cement Production lines can be summarized into the following processes ;as can be seen in the process and Quality flow diagram below; 1CEMENT PRODUCTION AND QUALITY CONTROL A Cement manufacturing ProcessExtraction and Preparation of Raw Materials The main raw materials (limestone, clay chalk or basalt) are quarried from natural rocks They are crushed and transferred to preblending storage where other substances (such as sand, iron ore, bauxite, shale, slag, fly ash) are added to get the desired chemical compositionCement Clinker Manufacturing Process with ReactionsThe cement production process 1 The Quarry: The cement production process begins with the extraction of limestone and clay from the quarry 2 Crusher and PreBlending: The material is then crushed to reduce particle sizes and blended to reduce variability in composition 3 Raw Mill and Kiln: Raw materials and additives areA practical guide to improving cement manufacturing processes
.jpg)
(PDF) An Insight into the Chemistry of Cement—A Review
2022年12月23日 This review provides an indepth analysis of the complex chemistry of cement, offering valuable insights for researchers2020年2月18日 The limestone mined is used chiefly for the manufacturing of cement, lime and edible lime etc Scientific studies revealed that loss of forest cover, pollution of water, soil and air, depletion of (PDF) Environmental Hazards of Limestone Mining and2019年8月27日 The major raw materials used as a source of CaO for cement manufacturing are limestone, chalk, marl, etc These raw materials by virtue of their natural occurrence contains other mineral impurities eg, MgO, SiO 2, Al 2 O 3, Fe 2 O 3, alkali compounds, and sulfidesThese impurities play an important role to influence the cement manufacturing Cement Manufacturing and Process Control SpringerLink2023年7月10日 The cement manufacturing process involves the extraction and processing of raw materials, such as limestone, clay, and shale, which are then heated in a kiln at high temperatures to form clinkerCement Manufacturing Process and Its Environmental Impact
.jpg)
Cement Production Process Cement Manufacturing Process AGICO CEMENT
2020年8月25日 A full cement production process includes the cement crushing process, raw mill process is representative of all types of cement limestone and clay are the main raw materials of cement making, the cement raw materials will be processed into a raw meal by crushing, batching, grinding Feeding raw meal into cement kiln to The final step in cement manufacturing is the grinding of clinker into cement powder, followed by the finalization process that ensures the product meets all required specifications and standards This stage is crucial as it defines the Cement Making Guide: Steps, Impact Green 2012年8月30日 Cement Manufacturing Process Phase IV: Kiln Phase Kiln is a huge rotating furnace also called as the heart of cement making process Here, raw material is heated up to 1450 ⁰C This temperature begins a chemical Cement Manufacturing Process Engineering Intro2017年1月13日 Mixing order affects efficiency, and every mixer and mixing method has advantages and disadvantages Batching affects sequence Batching, or measuring raw ingredients before mixing by weight, volume or both, is another important factor “Sometimes, weight and proportions change based on sequencing choices made during batching,” Sequencing in Mix Design NPCA
.jpg)
PORTLAND LIMESTONE CEMENT WITH FLY ASH: FREEZETHAW
PLC is produced by intergrinding cement clinkers with limestone during the manufacturing process As limestone is softer than clinker [10], the same grinding energy results in the formation of smaller particles of limestone, in comparison to those of Burning: In this operation, the slurry is directly fed into a long inclined steel cylinder called a Rotary kilnIn this kiln there are 3 different zones shown in fig below Cement Manufacturing Process Flow Chart (i) Drying Zones: In the wet process, the drying zone is comparatively larger than the dry process It is because the raw material in slurry form is directly fed into the kiln Manufacturing of Cement By Dry and Wet Process Expert Civil2024年10月15日 The initial studies of LC³ demonstrate that the mechanical properties of LC³ are comparable and even sometimes better than those of OPC Avet et al reported [6] that limestone and calcined clay could replace up to 50 % of cement in concrete productionAlthough the 3day strength of LC³ concrete is slightly lower than that of OPC concrete, the 7day strength of LC³ Improved mechanical properties and fiber dispersion of limestone In this process, the existing guidelines by China Railway Track System (CRTS) specify a proper feeding sequence of constituents, adequate mixing time, and mixing speed as the key parameters that are to be decided based on the trials [5] The performance of bitumen emulsionbased materials is highly sensitive to the type andInfluence of Feeding Sequence on the Fluidity and Fluidity Time
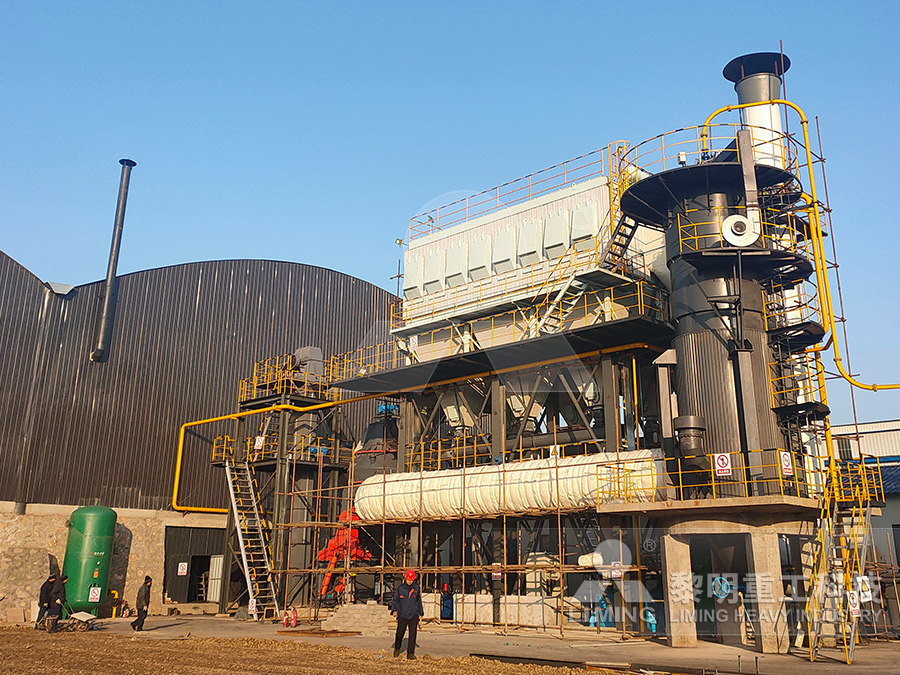
Analysis of material flow and consumption in cement production process
2015年8月1日 Cement production, which is highly dependent on the availability of natural resources, will face severe resource constraints in the future This is especially true for the cement industry in ChinaCement Manufacturing and Process Control 41 Cement Manufacturing: Basic Process and Operation To design the Refractory for the lining of different equipments in a cement plant, it is necessary to understand the total operational process of a cement plant in depth It is necessary to know the conditions prevailing in different equipments and theChapter 4 Cement Manufacturing and Process Control2021年4月24日 Mixing can differ from hand to machine mixing of concrete mix, with machine mixing being the most common However, no successful mixture can be achieved without the proper batching of all concrete materials Points to be Checked before Mixing of Concrete Materials Manual Mixing A watertight platform of at least size 3m X 3m should be availableMethods for Mixing of Concrete and Their Procedure2022年5月6日 The concrete mixing plant is divided into four parts: sand and gravel feeding, powder feeding (cement, coal ash, mineral powder, etc), water and concrete admixture feeding, conveying mixing and storage First, the Summary Of The Operation Sequence Of The Concrete
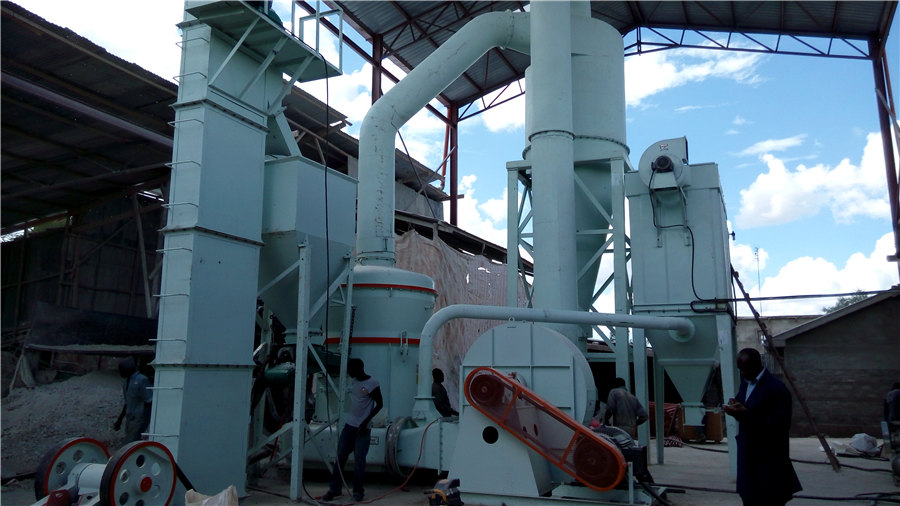
Cement manufacturing process
Due to these characteristics, the cement composition may vary and is basically a water cement water cement were known from the past Such as lime mortar, which the Egyptians and Greeks by mixing it with volcanic ash, clay bricks and lime juice, they reached to some sort of lime water that it had The property of hardening and By applying the mortar the Romans were able to build The use of fossil fuels such as coal, natural gas, and oil is common in cement production, both as a fuel for the kiln and as a source of heat for other parts of the process which leads to CO2 emitted by combustionHowever chemical reactions happening in the kiln (calcination) are also responsible for up to 60% of the total of emissions of the cement production process [PCA]Cement Production Demystified: StepbyStep Process and 2021年8月10日 Natural cements They are made from impure limestone Raw limestone is first calcined at moderate temperatures and subsequently cooled, ground and bagged for use as cement Calcination is the process whereby calcium carbonate (limestone) is heated to produce calcium oxide and carbon dioxide according to the reaction as follows:Cement and Clay Products Technology SpringerLink2018年8月29日 In this paper, investigated was the influence of limestone in limestone Portland cement on the rheological properties of mortars Two types of limestone of different origin and chemical (PDF) Influence of limestone addition to cement on rheological
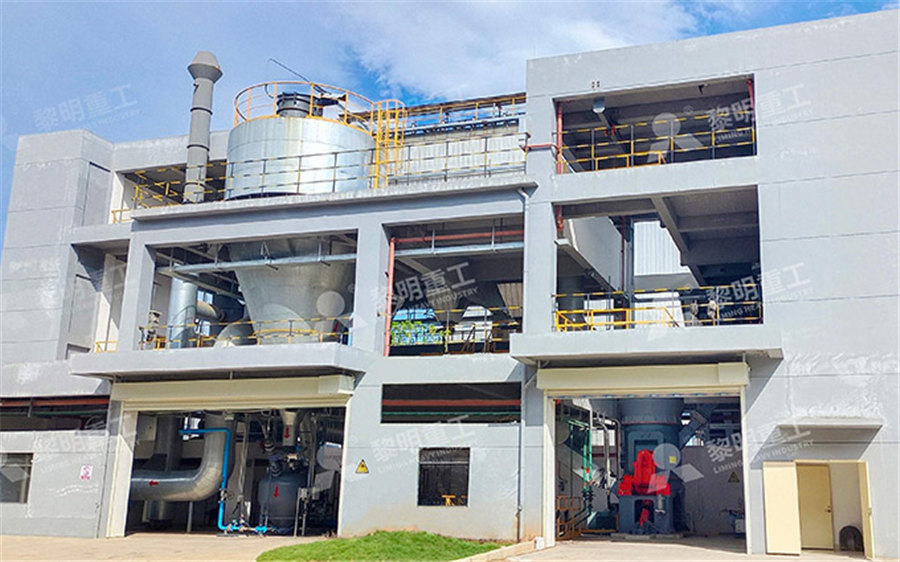
LIMESTONE SAMPLING AND TESTING CEMENT AND LIME
• These types of limestone reserves require further testing at the cement plant prior to the raw material blending process • Sampling and testing must be continuous to meet certain chemical requirements Based upon the quality of the limestone delivered to 2011年7月1日 Effective Optimization of the Control System for the Cement Raw Meal Mixing Process: II constant limestone and clay feeding, T Const,Lim and T Const,Clay and stable RM dynamics, T Const,DynEffective Optimization of the Control System for the Cement 2018年6月20日 Lastly, the importance of allowing the cement paste sample to rest during the measurement sequence was also analysed These trials were conducted on two types of Portland cements with completely The Research of Mortar Components Mixing Process2018年12月1日 a limestone replacement ratios, b finenes of limestone, c fineness of cement, d slag additions: water to binder ratio 05, e water to binder ratios: 20% limestone, f curing temperature(PDF) Modeling of Hydration, Strength Development, and Optimum
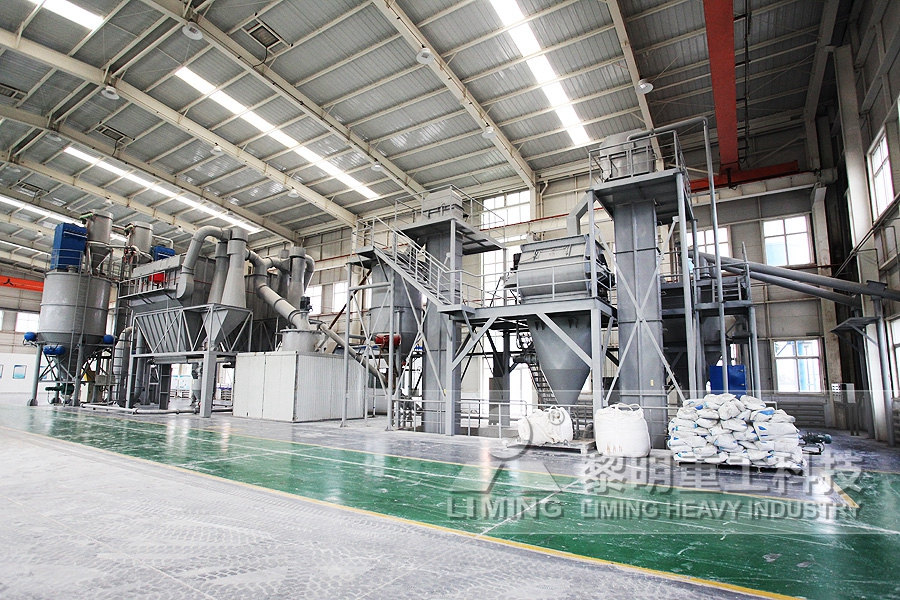
Decarbonisation pathways of the cement production process via
2024年1月15日 In the conventional cement production process, CO 2 emissions primarily result from the production of clinker, the main component of Portland cement [3]Specifically, two main sources of CO 2 emissions exist: (1) process emissions from the calcination process, where limestone (CaCO 3), a key component in the raw meal for clinker production, decomposes into