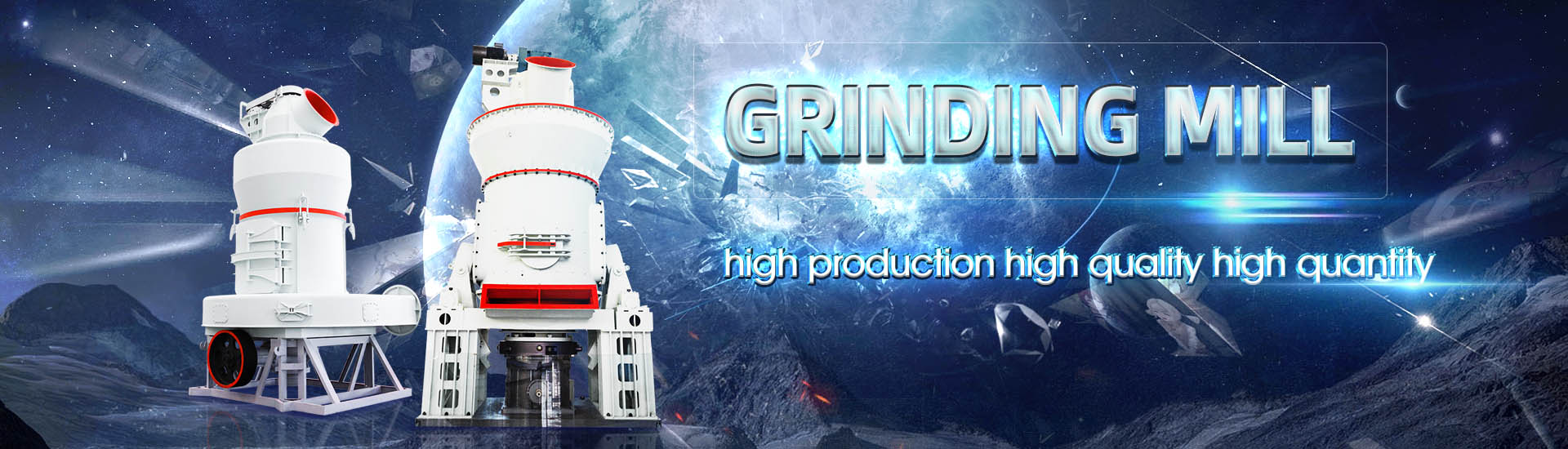
Do the secondary crushing ratio and the second stage crushing ratio mean the same thing
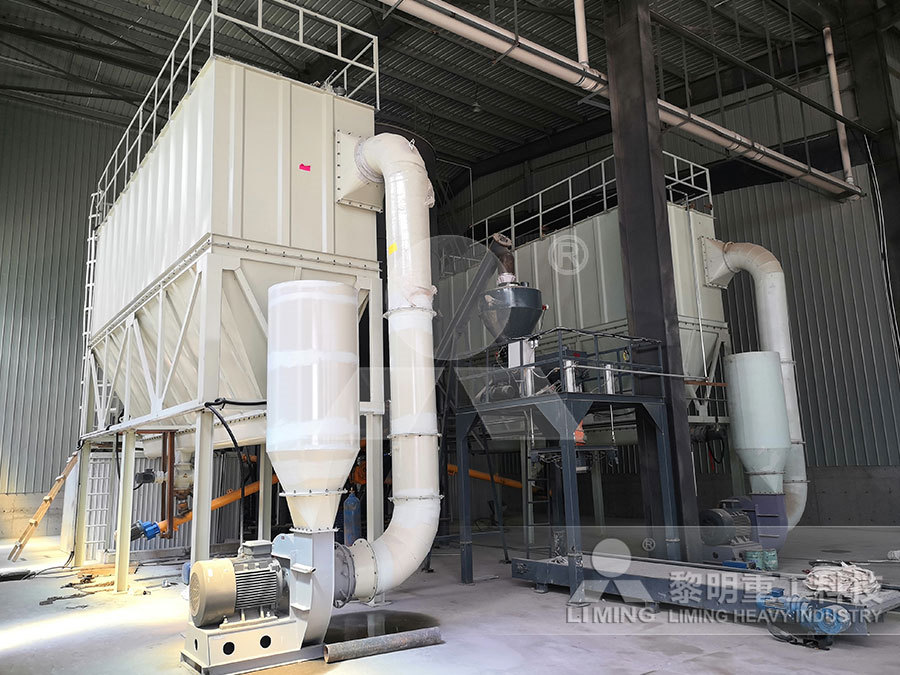
The Complete Guide to Primary Crushing, Secondary Crushing,
Primary crushing is the first stage in the comminution process and involves breaking down large rocks into smaller pieces of a size that can be handled by the downstream machinery 展开2023年2月28日 Secondary crushing is the second stage of crushing that takes place after the primary crushing The secondary crusher is the equipment that reduces the size of the Primary and Secondary Crushing: Understanding the Basics A 2024年3月25日 You can tell how good secondary crushing is by checking the size of what comes out, how much gets crushed over time, and how much power it uses Watching these Secondary Crushing 101: Everything You Need to Know JXSCThe optimum size range of 025mm cannot be achieved in a single pass through the coarse impact crusher A more efficient method is to use a secondary crushing stage, eg in the form Everything you need to know about Crushers in Cement industry
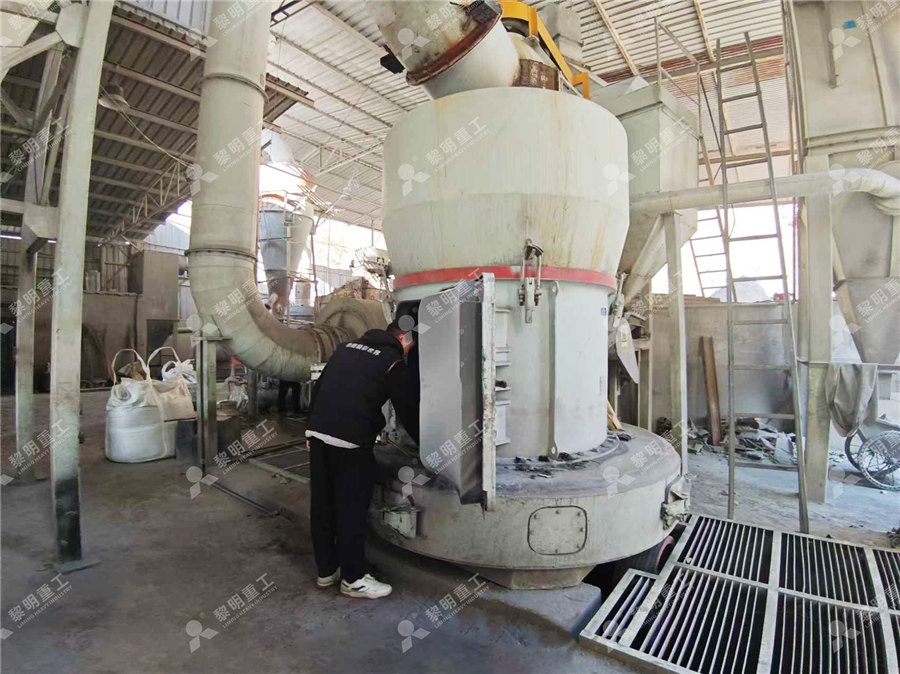
Primary Crusher vs Secondary Crusher: Understanding Their
2023年2月28日 While primary crushers are responsible for breaking down larger rocks and stones into smaller particles, secondary crushers are used to further refine these particles into 2019年9月2日 In the quarry, crushing is handled in four potential stages: primary, secondary, tertiary and quaternary The reduction of aggregate is spread over these stages to better PQ University Lesson 7: Crushing Secondary Breaking2021年4月12日 Secondary crushing (or intermediate crushing) accepts the material from the primary crushing stage and reduces it even further, whether for final product sizing or in Downstream Crushing Options for Secondary, Tertiary and2021年1月10日 Secondary crushing, as you can imagine, is the second stage of material processing following its initial reduction At this stage, material will flow through perhaps a What Is Primary, Secondary, and Tertiary Crushing?
.jpg)
Simplifying the crushing process Pit Quarry
2019年5月10日 Reduction ratios become an important consideration in secondary crushing Knowing just how fine you need a final output to be, along with the feed requirements of your 2016年2月29日 The term “secondary crushing” has become well established and familiar through long usage; it applies to the crushing stage, either single or multiple, which follows immediately after the primary crusher, taking all or a portion of the product of the primary crushing stage as its feedThe term should not be used, as it sometimes is, to designate a particular Secondary Crushing Equipment 911Metallurgist2019年8月14日 Optimisation of secondary crushing stage The milling circuit include two identical lines of single stage SAG milling Each low aspect ratio after precrushing indicate that the same P80 Optimisation of secondary crushing stage before 2021年4月12日 This is where downstream crushing with secondary, tertiary and quaternary stages comes in Secondary Crushing Secondary crushing (or intermediate crushing) accepts the material from the primary crushing stage Downstream Crushing Options for Secondary,
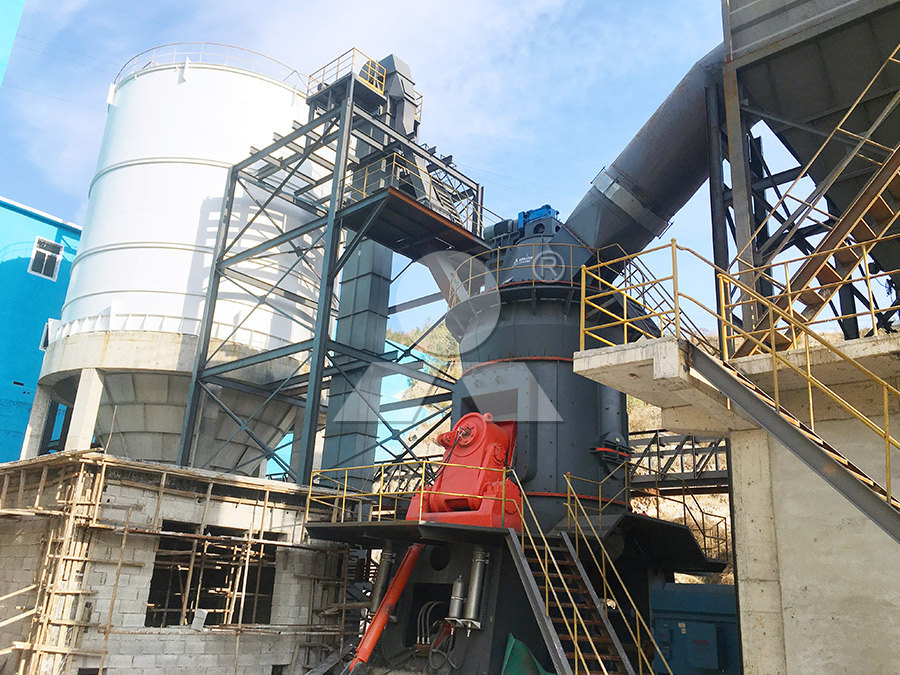
AMIT 135: Lesson 5 Crushing – Mining Mill Operator Training
This means that the number of crushing stages can be reduced depending on the feed size accepted by primary grinding stage Image of a “Classical” 3stage ore crushing prior to rod mill [image: (13551)] Diagram of Typical 12 stage ore crushing prior to AGSAG mill [image: (13552)] Calculation of Reduction Ratio in Crushing2015年12月26日 In mineral processing or metallurgy, the first stage of comminution is crushing Depending of the type of rock (geometallurgy) to be crushed, there are 2 largely different techniques at your disposition for crushing rocks In principle, compression crushing is used on hard and abrasive rocks by placing them between a high wearresistant plate/surfaceCrushing in Mineral Processing 911Metallurgist2024年7月17日 Crushing is a multistage process that includes primary crushing, secondary crushing, and tertiary crushing Different types of crushing equipment are used at each stage to meet various crushing requirements Primary crushing breaks down large raw materials into mediumsized pieces for easier handling in subsequent processesTypes of Crushers: Choosing the Right One for Each StageThe reduction ratio of a crushing stage can be defined as the ratio of average particle size entering to average size leaving the crusher This is also called the mean reduction ratio and 3329% TABLE 6 VALUE OF TONNAGES, SCREEN EFFICIENCIES AND SPLIT RATIOS FOR SECONDARY SCREEN INCLINED AT 21˚ RUN SCREEN SCREEN FEED OVERSIZE STUDY AND OPTIMISE THE SECONDARY AND TERTIARY CRUSHING CIRCUITS
.jpg)
Crushing and Screening AggNet
2012年10月15日 Reduction ratios are up to 3:1 This machine requires oneandaquarter horsepower per ton per hour of material crushed to make a 1in product The product from the roll crusher has almost no oversize The triple roll crusher is the same as above except that it has a reduction ratio of up to 5:12016年3月11日 Standard (Secondary) Cone Crusher (Refer to Fig 1): The Standard Cone crusher is normally applied as a secondary crusher in a multistage crushing circuit The small diameter feed distributor and the wide throat opening at the top of the liners enable the Standard Cone crusher to accommodate the larger feed produced by the Primary crusherCrushing Plant Flowsheet DesignLayout 911Metallurgist2017年3月4日 second crushing stage sizes and small ratio of the stone powder pr because in tertiary crushing process combination of primary and secondary crushing were used according to the specific SIZE REDUCTION BY CRUSHING METHODS ResearchGateAll crushers have a limited reduction ratio meaning that size reduction will take place in stages 32 Operation stages: The operating stages in minerals processing have remained the same for SIZE REDUCTION BY CRUSHING METHODS By ResearchGate
.jpg)
Primary vs Secondary Crushers: Understanding the
2023年2月28日 Primary crushers typically have a larger crushing ratio, meaning that they can reduce large rocks or ores to a more manageable size in a single pass Secondary crushers, however, have a smaller crushing ratio, meaning In this study, the effects of three different choke feed level (1/1, 1/2, and 1/4) and four different effective reduction ratios (25, 5, 10, and 20) depend on the capacity of the crusher of the The flowchart of crushing process with onestage 80% passing reduction ratio which are defined as follows: As the crushing is performed in stages, crushing may be divided into primary, secondary, tertiary and quaternary stages based on the particle size Correspondingly, the crushers can be classified into five groups according to the size of the product they producecrushing جامعة الموصل2020年9月20日 The 2S crushing consisted of primary and secondary crushers as Jaw and HSI (horizontal shaft impactor), respectively, while 3S crushing was composed of primary, secondary and tertiary crushers as (PDF) COMPARISON OF SECONDARY CRUSHING OPERATIONS
.jpg)
Modeling and Improving the Efficiency of Crushing Equipment
2023年6月30日 Crushing is the first and most important stage in the preparation of raw materials for further processing The quality of the following processing stages (crushing, flotation,2019年9月2日 Cone crushers are used in secondary, tertiary and quaternary stages With proper chokefeed, conespeed and reductionratio settings, cone crushers will efficiently produce material that is high quality and cubical in nature In secondary stages, a standardhead cone is usually specifiedPQ University Lesson 7: Crushing Secondary BreakingFriends who know the stone production line should all know that in order to make the sand and stone grading more reasonable and the product grain shape more beautiful, most of the stones are coarsely crushed and then subjected to secondary crushing processing Therefore, the second stage of stone crushing equipment Selection is very important []What Equipment is used for the Second Stage Crushing of Sand 2015年4月3日 The reduction ratio is the ratio of the crusher feed size to product size The sizes are usually defined as the 80 % passing size of the cumulative size distribution Types of crushers Crushers are classified into three types based upon the Crushers and Their Types IspatGuru
.jpg)
Nordkalk’s new GP500S secondary crusher doubles the crushing ratio
2019年4月1日 “Compared with the product size of 80 mm produced by our old secondary crusher from Svedala, which was installed in the 1960s, the crushing ratio of the GP500S is better by half This means that we can now feed material of some 40 mm into our fine crusher, which clearly lightens the rest of the process”Jaw box in a jaw crusher Impact Crushers Reduction ratio 10:1 Impact Crushers can be used for either primary or secondary crushing and work by creating a sudden impact force that shatters the material into smaller piecesReduction Ratios in Crushing Machinery Partnercrushing process (Fig 3a) was implemented in two crushing stages, with outlet slot dimension er = 24 mm (B) in the first stage and er = 11 mm in the second crushing stage (C, B) After the first stage of crushing, the material was sieved in order to perform our analysis of the product grain To complete sieveANALYSIS OF ENERGY CONSUMPTION OF CRUSHING 2017年1月27日 This paper presents experimental comparison of two machine crushing technologies: onestage and twostage The study was carried on a model doubletoggle jaw crusher which allows crushing forces (PDF) Analysis of Energy Consumption of Crushing

Crushing Mineral Processing 911Metallurgist
2016年1月17日 Secondary Crushing: In mineral processing, it is assumed, for the present purpose that intermediate crushing is not necessary and that the runofmine or quarried mineral has, in one pass, been reduced in size so that all is below say 6in ring size From this stage forward the utilization of the product assumes primary importance2003年1月1日 Mining is typically conducted through a set of interdependent unitoperations, which commonly include drilling, blasting, digging and hauling, in order to deliver the required ore material into (PDF) The Effects of Blasting on Crushing and Grinding2023年7月22日 The ore crushing process includes four types: ore coarse crushing, ore medium crushing, ore fine crushing, and ore superfine crushing Ore coarse crushing is a process of crushing ore blocks with a feeding particle size of 500–1500 mm to 125–400 mm The maximum crushing ratio of coarse crushing is about threeOre Crushing SpringerLinkBoth industries are interested in increasing the product quality while at the same The achieved values of are plotted in Figure 1 6a against the compression ratio the crushing stage Layout of a fourstage crushing plant for ballast production
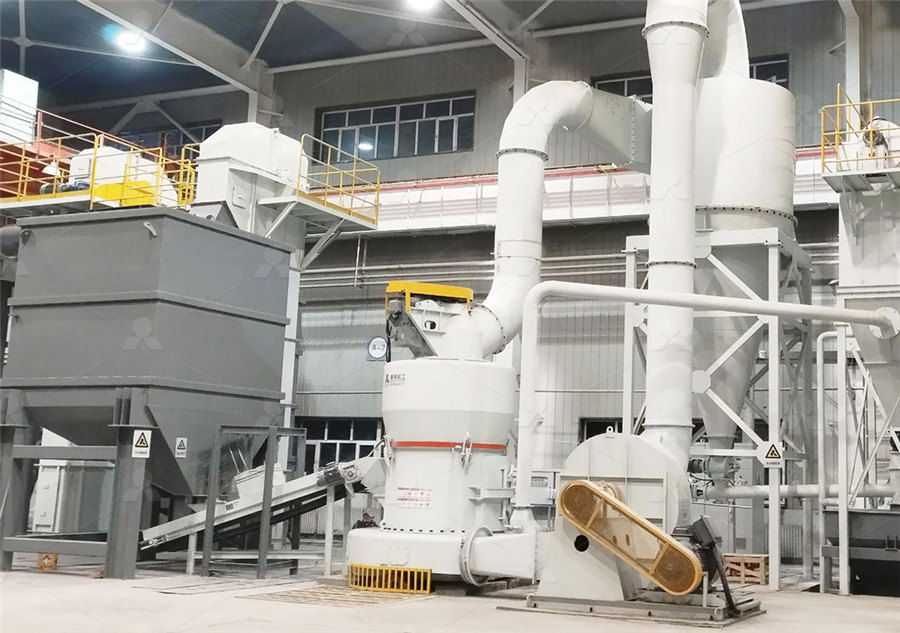
(PDF) Crushing and Screening Handbook Academia
This paper assesses a number of factors affecting the performance of the crushing plant by addressing the critical design parameters and consideration of ore characteristics, operability and maintainability Due to the fact that ore properties remain the same during milling, its control may become difficult for yield and quality of a productThe reduction ratio in crushing is the ratio of the feed size to the product size during a crushing operation It usually varies, but the reduction ratio depends on the chamber and nut adjustments However, the best particle shape is found in material about the same size as the CSS, which is the smallest discharge opening dimension on the jaw crusher Understanding the Reduction Ratio in Crushers Komplet America2024年4月17日 In conclusion, a single crusher always has a certain range of crushing ratio, for example, a jaw crusher’s crushing ratio ranges from 3 to 20 depending on its type In this way, if we want to get a better product shape by adjusting the crushing ratio, we always have to consider the overall situation of the whole crushing lineHow to adjust crushing ratio to increase the cubic shape of 2019年10月25日 32 Performance Tests To understand the effect of aggregate shape on stability and packing behaviour, two widely used tests, namely VCA drc and AoR were conducted on individual sizes of coarse aggregates VCA drc The VCA drc measures voids present in dryrodded coarse aggregates The test is useful to determine the particle packing behaviour of Understanding Effects of Crushing Mechanism on Aggregate Morphology
.jpg)
COMPARISON OF SECONDARY CRUSHING OPERATIONS
39% of the rotor diameter, respectively The ratios statistically found could be declared a startup These ratios are, therefore, beneficial for initial sizing related to secondary crushing Secondary impact crushers are vital tools in the aggregate and mining industries, designed specifically for the second stage of crushing After the initial reduction by a primary crusher, these machines take the coarser input material and further reduce it to the desired size, shaping the particles into a more cubical or uniform formSecondary Impact Crushers CONMACHThe first crusher in a crushing system into which material is fed Succeeding crushers in the system are referred to as secondary (second), tertiary (third) or quaternary (fourth) crushers Reduction Ratio The ratio of the top size of input material to the top size of crusher discharge material Run of Mine (ROM)Construction, Working and Maintenance of Crushers for Crushing Table 1: Energy and cost calculations by unit operation Operation Feed size Product size Work input Energy cost cm cm kwh/ton $/ton 40 24 087 Explosives ∞ 40 102 23 016 Primary crushing 102 191 61 043 Secondary crushing 191 0053 1935 135 Grinding 2043 150 Totals By far the greatest work input is in grindingThe Effects of Blasting on Crushing and Grinding Efficiency and
.jpg)
ENERGY EFFICIENCY IN COMMINUTION GETTING MORE FROM THE CRUSHING STAGE
2020年1月13日 crushing plant, the secondary crush er provides a feed to the third crushing stage at d 80 = 35 mm and the tertiary crusher(s ) provide a feed, having d 80 = 8–9 mm, for milling in a closed circuit2015年10月28日 In most cases, the fine crushing and cubicizing functions are combined in a single crushing stage The selection of a crusher for tertiary crushing calls for both practical experience and theoretical knowhow This is where producers should call in an experienced applications specialist to make sure a system is properly engineered Types of Selecting the Right Crushing Equipment AggNet2016年6月6日 Circuits above, but with feed preparation including two stages of crushing—typically referenced as precrushing Common convention generally refers to highaspect ratio mills as SAG mills (with diameter to effective grinding length ratios of 3:1 to 1:1), lowaspect ratio mills (generally, a mill with a significantly longer length than diameter) are also SAG Mill Grinding Circuit Design 911Metallurgist2015年10月29日 Hafeez et al (8) compared the effect of singlestage and twostage crushers on asphalt mixes and concluded that mixes prepared using twostage crushing have a higher RM, DM, and fatigue life (PDF) Influence of Singleand TwoStage Aggregate
.jpg)
2 Stage or 3 Stage Crushing? Trimax Machinery
2021年7月23日 Should I go for 2 stage or 3 stage crushing? That’s a question we always get asked By the way, what’s 2 stage or 3 stage crushing anyway? That’s another common question that may be asked That question is easier to answer 2 stage crushing involves just 2 crushers in a crushing plant, i,e, a primary crusher and a secondary crusher