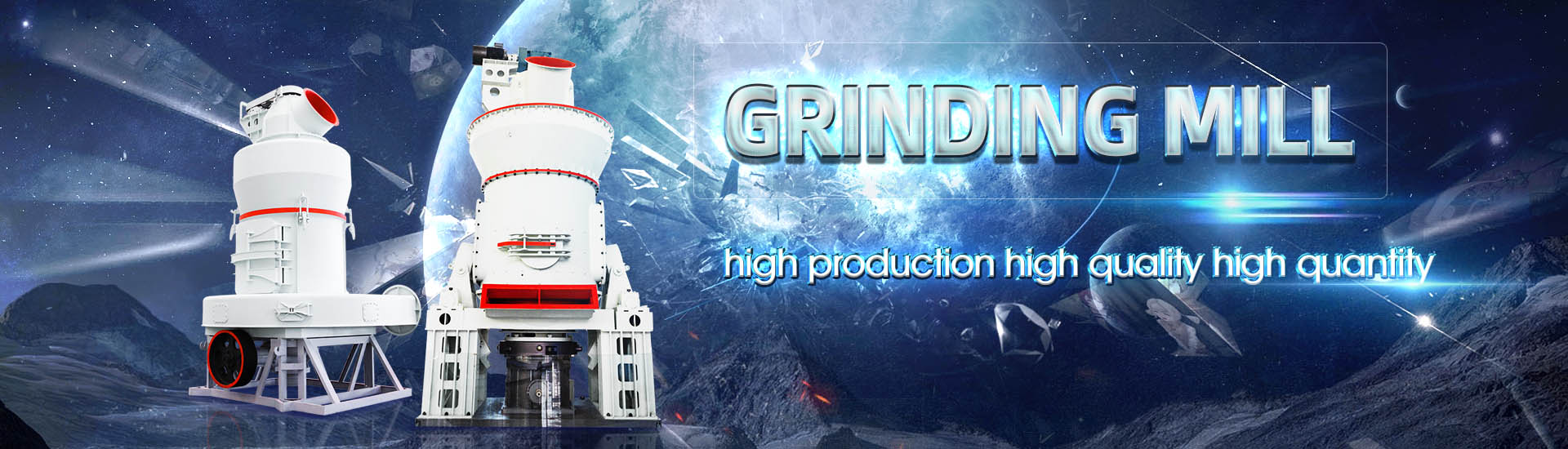
Product performance of coal mill ore mill
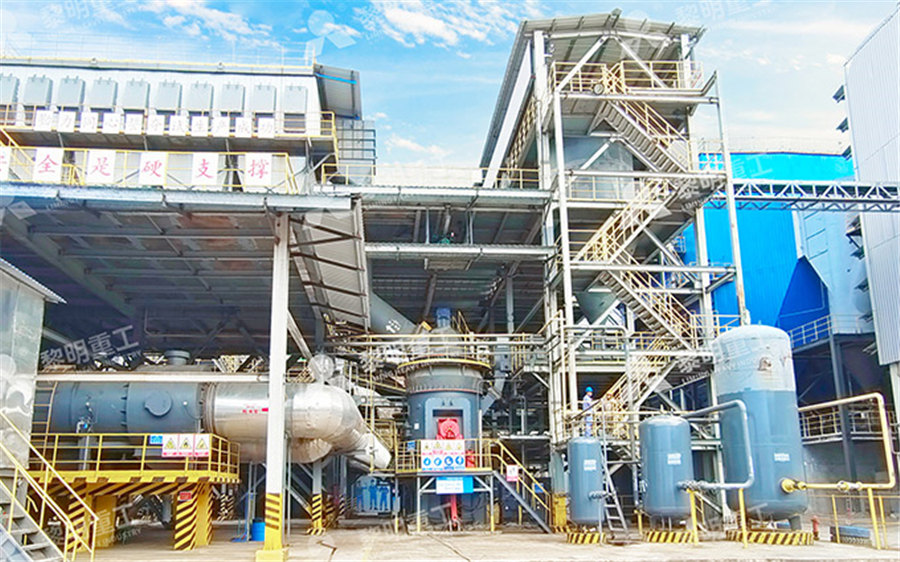
PREDICTING THE PRODUCT PARTICLE SIZE DISTRIBUTION FROM
test data also show that a finer product size is obtained when the mill operates at higher stirring speeds while using smaller grinding media Samples collected from an industrial vertical mill were2020年10月20日 In this research we try to improve the AG mill performance in terms of power draw, throughput, and product particle size distribution by setting the mill feed particle size The performance improvement of a fullscale autogenous mill by 2017年4月1日 Vertical roller mills (VRM) have found applications mostly in cement grinding operations where they were used in raw meal and finish grinding stages and in power plants Operational parameters affecting the vertical roller mill 2020年8月12日 This study shows the performance of a currently running vertical roller coal mill (VRM) in an existing coalfired power plant In a power plant, the coal mill is the critical An investigation of performance characteristics and energetic
.jpg)
Technique to Investigate Pulverizing and Abrasive Performance of
2021年11月4日 This method enables facilitated testing procedures and a more exact simulation of grinding in vertical spindle coal mills Ballrace mills and Loesche roller mills were usedMill grinding efficiency is measured at the same time as CSE through circuit samplingFunctional performance analysis combines CSE and mill grinding efficiency to provide a measureable, Functional Performance of Ball Milling Circuits A Plant AusIMMThis study explores the different product particle size of coal while applying dry and wet grinding and optimization of parameters affecting the grinding process with both methods Grinding of A statistical analysis and optimization of Indian coal grinding in a philosophy for improving boiler performance starts in optimizing the inputs, starting at the pulverizer Working in coordination, Storm Technologies and SCEG undertook a project to Combustion, Reliability, and Heat Rate Improvements through Mill
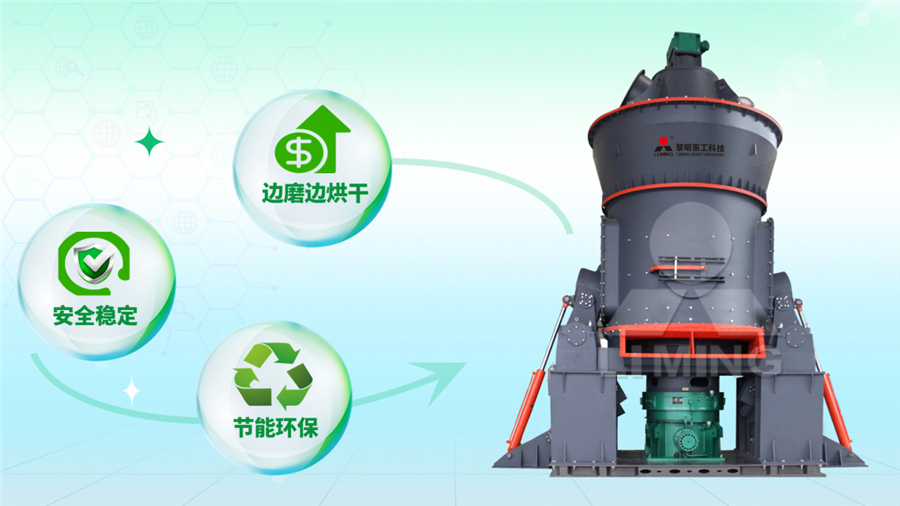
Milling Characteristics of Coal and Torrefied Biomass
2021年10月28日 In this study, to evaluate the milling performance of coal and torrefied wood pellets (TPs), various blend ratios were tested using a benchscale roller mill Neutral sugar analysis was performed to evaluate the biomass DOI: 101016/jpowtec201909062 Corpus ID: ; Wet and dry grinding of coal in a laboratoryscale ball mill: Particlesize distributions @article{Bu2020WetAD, title={Wet and dry grinding of coal in a laboratoryscale ball mill: Particlesize distributions}, author={Xiangning Bu and Yuran Chen and Guangxi Ma and Yujin Sun and Chao Ni and Guangyuan Xie}, Wet and dry grinding of coal in a laboratoryscale ball mill: 2020年7月23日 Abstract The depletion of highgrade ores has forced the utilization of lowgrade ores The small liberation sizes in the lowgrade ores require fine grinding which is an energy intensive operation In the present study, lowgrade chromite ore bearing platinum group of elements (PGE) was used as an experimental material The previous study concluded the Optimization of stirred mill parameters for fine grinding of PGE 2020年5月18日 In this study, samples of bauxite whose chemical composition and Hardgrove Index values are known were ground to micronized size by a laboratory scale stirred media mill and its performance was compared with a laboratory scale ball (Bond) mill Stirred media mill decreased bauxite d50 size from 780 to 5 µm in 3 minPerformance comparison of stirred media mill and ball (BOND) mill
.jpg)
A Comparison of Three Types of Coal Pulverizers Babcock Power
pressurized seal air is also used to prevent leakage of coal dust from the mill and to protect bearings in the grinding rollers MILL SYSTEM COMPARISON AND PERFORMANCE Refer to Table I for a summary of the design features for each mill system Mill Comparisons—General The BTM is a lowspeed mill that primarily grinds coal by impact and attritionA highquality coal mill can effectively solve the fineness problem of coal powder and ensure uniform grinding of raw coal The fineness of pulverized coal has a great influence on the ignition temperature and burning time of the equipment In this way, the influence of bad raw coal on combustion efficiency can be well improved by coal millCoal Ball Mill Grinding for Different Kinds of Pulverized Coalabb coal pulverizer hp 1103, ball mill pdf torrent, coal mill at power plan; bowl mill pulverizer merk essa, Long life and high Performance mills 4 planetary gear box of coal mill hp1103 SBM Crushers Performance Of Hp 1103 Mill2022年5月23日 Grinding experiments were conducted in a laboratoryscale stirred mill on a lowgrade PGE bearing chromite ore HighPressure Grinding Rolls (HPGR) product of −1 mm was used as feed material to (PDF) Modeling and application of stirred mill for the coarse
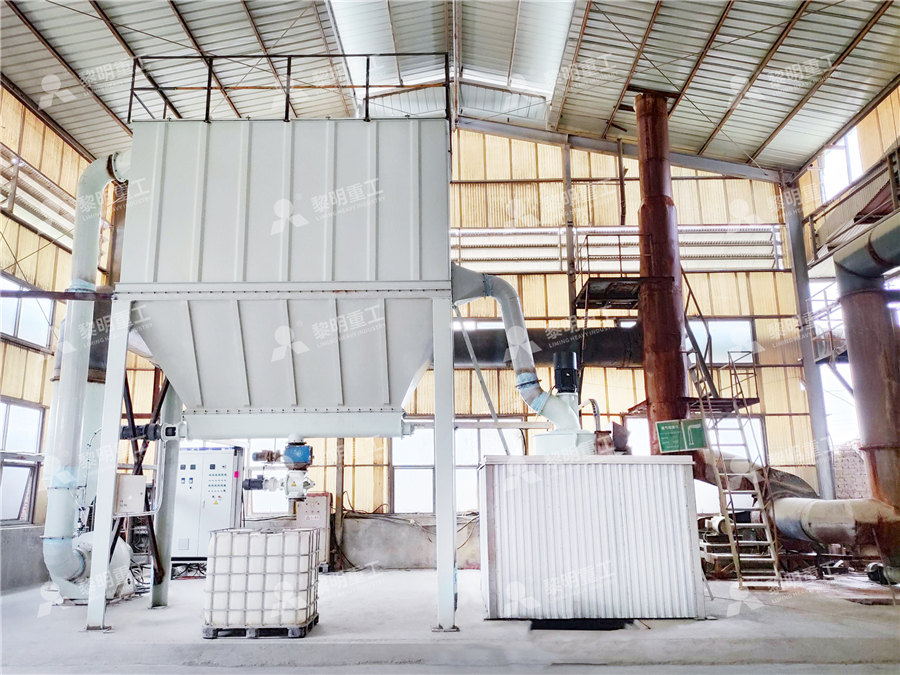
Performance optimisation of vertical spindle coal pulverisers
need improvement to achieve milloptimal performance Coal feed to the mill is important, this was observed to be a limiting constraint on mill capacity when the coal required exceed nominal load requirement KEYWORDS: Air fuel ratio; pulverised fuel distribution; classifier; elutriation; heat balance; isokinetic sampling Coal vertical roller mill adopts advanced technology, finished product has highefficiency distribution and excellent combustion performance 4 Floor space is smallest Due to its structure features, coal vertical roller mill, compared with the same specifications, can reduce floor space and floor usecost greatly than ball millCoal Vertical Roller MillMill liners are an essential component in the mineral processing industry, where they are used to protect mills from wear and tear and enhance grinding performance The design of mill liners can have a significant impact on grinding efficiency and product quality, making it essential to understand the effects of mill liner design on these factorsThe Effects of Mill Liner Design on Grinding Performance and Product 2018年2月1日 In another study to investigate ball size distribution on ball mill efficiency by Hlabangana et al [50] using the attainable region technique on a silica ore by dry milling, a threeball mix of Effect of ball and feed particle size distribution on
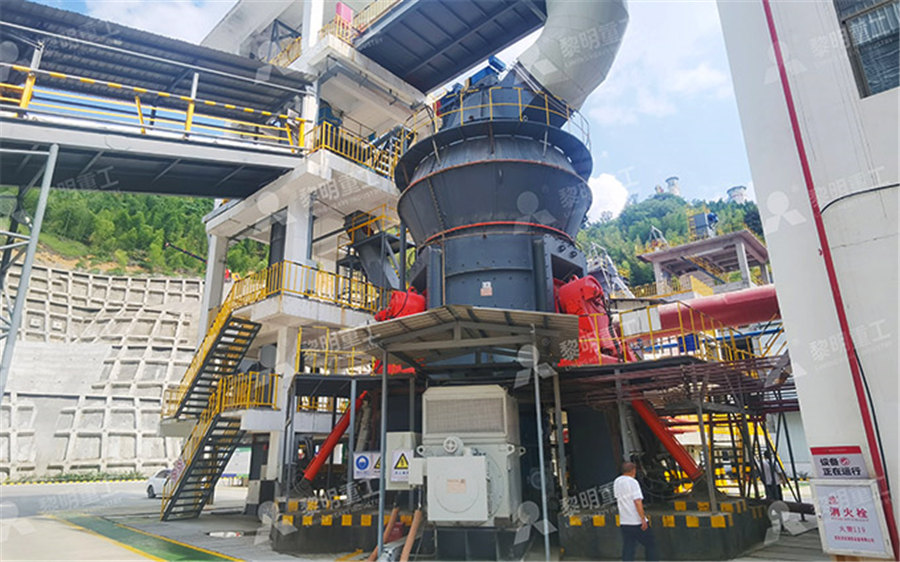
Ore mill, Ore grinding mill All industrial manufacturers
Find your ore mill easily amongst the 42 products from the leading brands (Fritsch GmbH FRITSCH Planetary Ball Mills – highperformance allrounder in routine laboratory work The Planetary Micro Mill PULVERISETTE 7 premium line with 2 grinding stations is designed for Find the product, subcontractor or service provider you The coal vertical mill, also referred to as the vertical roller coal mill, is an advanced equipment developed by our company It combines modern technology with our extensive experience in powder manufacturing This coal pulverizer HighEfficiency Vertical Coal Mill Enhancing Coal Good Product Performance Better process performance of the tower mill with superior process adjustment performance, including grinding concentration, feed position, feed rate, residence time in the mill, HP Bowl Coal Mill Tower Mill Grinding: Revolutionizing Efficiency and PerformanceRequest PDF On Mar 15, 2015, Mathis Reichert and others published Research of iron ore grinding in a verticalrollermill Find, read and cite all the research you need on ResearchGateResearch of iron ore grinding in a verticalrollermill
.jpg)
Comparing Vertical Roller Mill Performance on Two Different Precious
2018年4月16日 Request PDF Comparing Vertical Roller Mill Performance on Two Different Precious Metal Ores The vertical roller mill (VRM) is a comminution device in which crushing, grinding and I219 obtained for fully worn lifters The solid upper parts of the curves are the ‘normal’ fillingload curves, which are applicable during operation as theMILLING CURVES AS A TOOL FOR CHARACTERISING SAG MILL PERFORMANCE2022年1月23日 This work concentrates on the energy consumption and grinding energy efficiency of a laboratory vertical roller mill (VRM) under various operating parameters For design of experiments (DOE), the response surface method (RSM) was employed with the VRM experiments to systematically investigate the influence of operating parameters on the energy Analysis and Optimization of Grinding Performance of Vertical 2017年4月1日 DOI: 101016/JMINENG201608015 Corpus ID: ; Operational parameters affecting the vertical roller mill performance @article{Altun2017OperationalPA, title={Operational parameters affecting the vertical roller mill performance}, author={Deniz Altun and Hakan Benzer and Namık A Aydogan and Carsten Gerold}, journal={Minerals Operational parameters affecting the vertical roller mill performance
.jpg)
An investigation of performance characteristics and energetic
2020年8月12日 To understand the performance of a vertical roller coal mill, the real operational tests have been performed considering three different coal sources Obtained results indicate that grinding pressure, primary air (PA) temperature and mill motor current have a tendency to rise by increasing coal feeding mass flow rates for all used coal2022年1月23日 This work concentrates on the energy consumption and grinding energy efficiency of a laboratory vertical roller mill (VRM) under various operating parametersAnalysis and Optimization of Grinding Performance of 2012年1月23日 PERFORMANCE OPTIMISATION OF COAL MILLS PERFORMANCE OPTIMISATION OF COAL MILLS PERFORMANCE OPTIMISATION OF COAL MILLS BOWL MILLS : INPUT: i) Mill Spring PERFORMANCE ANALYSIS OF COAL MILLSVRM has been widely researched in processing of cement (Ito et al 1997;Jorgensen 2005;Wang et al 2009, Ghalandari et al 2021), coal (Tontu 2020), iron ore (Reichert et al 2015), zinc ore (van Energetic efficiency of coal mill as a function of mill outlet
.jpg)
(PDF) LEARNING FROM OTHER INDUSTRIES; WHY THE VRM
2019年4月16日 Conference: Applying a Successful Technology from the Cement Industry: Advantages of Grinding Ore in a VerticalRollerMill; At: Antalya, Türkey2020年10月20日 Tracking the mill performance showed that the mill power consumption decreased from 949 to 663 kWh/t (a nearly 30% reduction), P 80 of the mill product decreased from 611 to 355 μm, and the mill fresh feed flow rate increased from 511 to 521 t/h by decreasing the feed ore hardness from 112 min to 58 min based on SAG power index (SPI)The performance improvement of a fullscale autogenous mill by setting 2017年9月11日 Many secondcompartment mill studies of particles sampled "through the mill" look at about 10100 plus data points longitudinally; we are looking at 300800 plus data points longitudinally (PDF) Performance Evaluation of Vertical Roller Mill in Cement Optimizing a ball mill involves several strategies, including: Optimization of Mill Design and Operating Conditions Optimizing the design and operating conditions of a ball mill can improve its performance Factors such as mill speed, ball size, and liner design can all be optimized to improve grinding efficiencyKey Factors for Ball Mill Optimization in the Mining Industry
.jpg)
Factors affecting ores grinding performance in ball mills
Overall, ball size and shape are important factors to consider when choosing a mill for ore grinding However, other factors such as mill design and the type of ore being processed also play a role in how well the ball milling process works Effect of media type on ore grinding performance2013年2月1日 Self similar distribution of hammer mill product size for iron ore and coal 916 SK Dey et al / Powder Technology 235 (2013) 914 – 920 Author's personal copyComminution features in an impact hammer mill ResearchGate2019年9月24日 Although ore variability is frequently debated as a major source of uncertainty in process performance, most of the current ore testing product sizes (P80) of 170 SAG mill performance, Simulating the Impact of Ore Competence Variability on Process 2016年9月1日 Altun et al 6 indicated a strong correlation coefficient between Workingpressure Classifierrotorspeed and product performance of a vertical roller coal mill, mill types in ore Operational parameters affecting the vertical roller mill performance
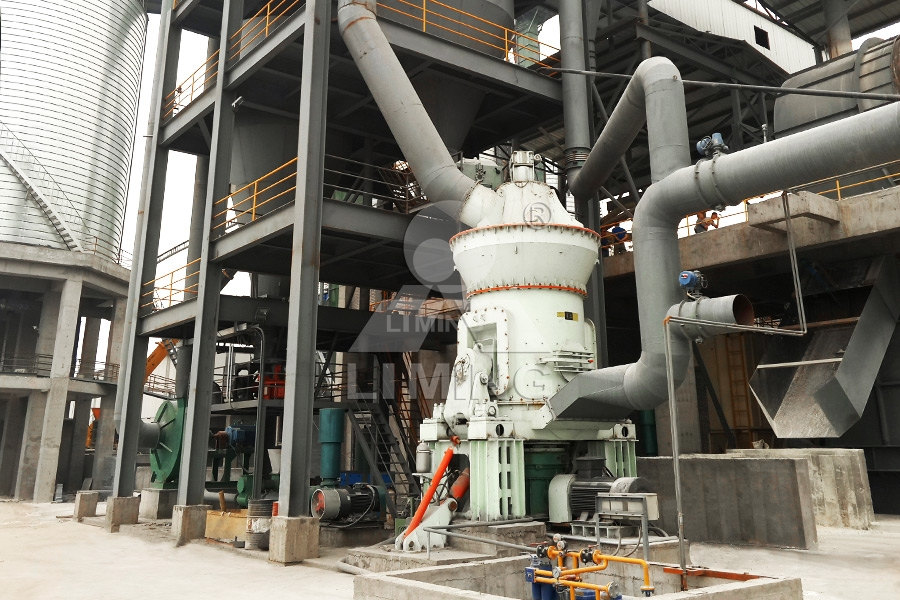
Copper ore grinding in a mobile vertical roller mill pilot plant
2015年3月10日 VRM has been widely researched in processing of cement (Ito et al 1997; Jorgensen 2005; Wang et al 2009, Ghalandari et al 2021)), coal (Tontu 2020), iron ore (Reichert et al 2015), zinc ore (van Drunick et al 2010), copper ore (Viljoen et al 2001; Altun et al 2015), gold (Erkan et al 2012; Altun et al 2017), nickel ore (Viljoen et al 2021年6月29日 This article deals with the preparation and laboratory milling of βdicalcium silicate Dicalcium silicate is the second most important calcium silicate of Portland clinker βC 2 S is usually Effects of Mill Speed and Air Classifier Speed on DOI: 101016/JMATPR202010976 Corpus ID: ; Investigate the reduction of mill scale with low grade coal through solid gas reactor @article{Shekhawat2021InvestigateTR, title={Investigate the reduction of mill scale with low grade coal through solid gas reactor}, author={Deepika Shekhawat and N Gautam and M K Banerjee and Amar Patnaik}, Investigate the reduction of mill scale with low grade coal through 2023年10月27日 The ball mill is a rotating cylindrical vessel with grinding media inside, which is responsible for breaking the ore particles Grinding media play an important role in the comminution of mineral ores in these mills This work reviews the application of balls in mineral processing as a function of the materials used to manufacture them and the mass loss, as A Review of the Grinding Media in Ball Mills for Mineral Processing
.jpg)
CFD Modeling of MPS Coal Mill for Improved Performance and Safety
2009年1月1日 Air flow distribution at the mill throat, as well as inside the mill, significantly influences the mill performance in terms of separation, drying, coal/air flow uniformity at the mill outlet 2023年4月23日 between the ball mill a nd rod mill showed that particles in a ba ll mill h ave a shorter residence time than in a rod mill [5 8] This is because balls offer less resistance to t he flow of (PDF) Grinding Media in Ball MillsA Review ResearchGate2019年10月1日 It is believed that the line load on particles in rod mills helps to break hard materials (Gupta and Yan, 2016) By comparison, the point load on the particles in ball mills is conducive to the Wet and dry grinding of coal in a laboratoryscale ball mill: Particle 2019年5月8日 7 Maintenance Strategy Maintenance Significant Item Inspection / Execution Task Coal Measure HGI (hard grove index), moisture content, abrasiveness and size of coal fed to mill Pulverised fuel (PF) Measure particle size distribution, PF velocity and temperature Grinding media (Balls and Rings) Measure ball diameter, ring depth profile and material TPS Coal Mills and Fan Performance PPT SlideShare
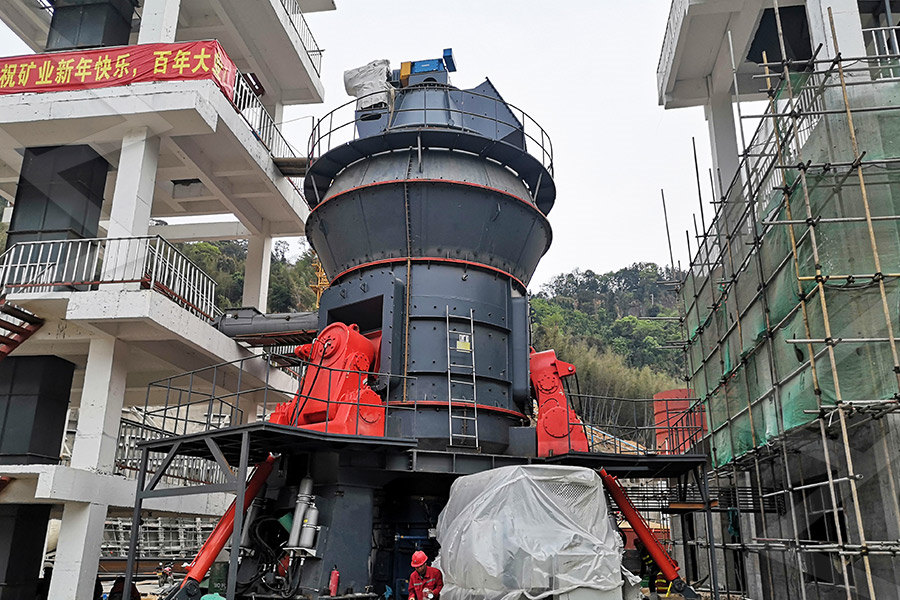
Analysis of the Coal Milling Operations to the Boiler Parameters
controller Wen, (2010) concludes that the mill performance in term of coal end product is the major factor can cause the plant performance through the combustion in the boiler furnace According to Wei, Wang, and Wu, (2007) the design mill depends on the coal in