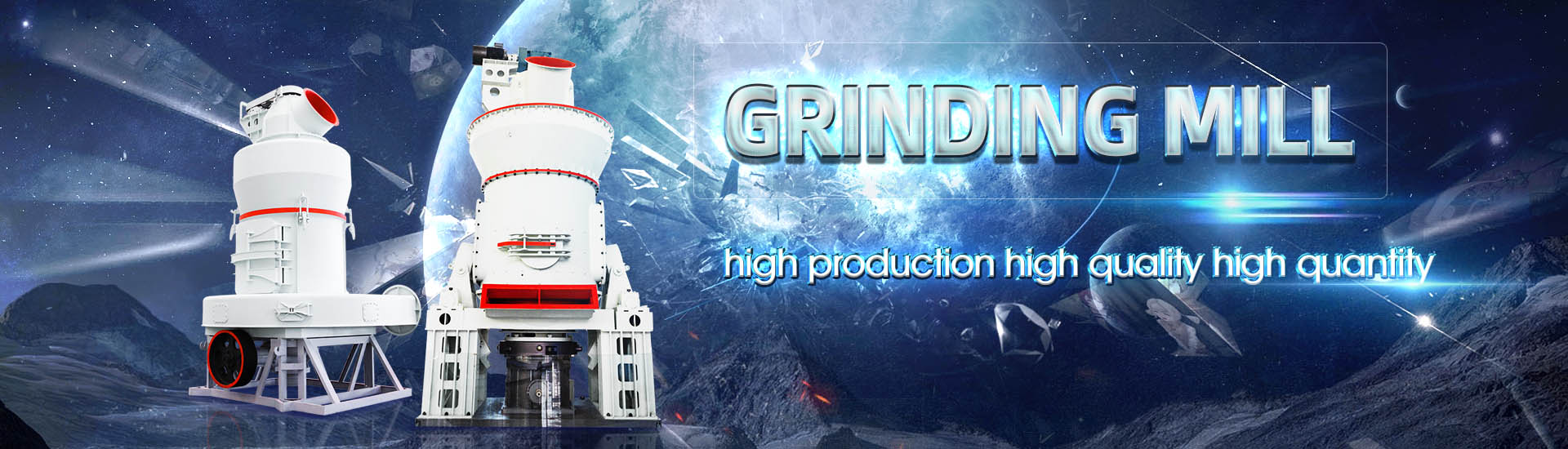
Grinding lime process flow
.jpg)
(PDF) EnergyModel and Life CycleModel for Grinding Processes
2022年5月22日 Fine and ultrafine grinding of limestone are frequently used in the pharmaceutical, chemical, construction, food, and cosmetic industries, however, research Process flow diagram for limestone processing operations Processing commences with transportation of the (raw) stone from the quarry to the processing facility, as depicted by Limestone Quarrying and Processing: A LifeCycle Inventory2017年11月28日 Grinding: The crushed limestone in the stock bin is evenly sent into the limestone grinding mill for the grinding operation The users can adjust the discharging granularity of the lime powder according to their demands Configuration and Process Flow of Limestone Milling Section 2 provides a detailed description of the production process for lime, with discussions of individual lime products, limestone inputs, and costs of production Section 3 describes the Lime Production: Industry Profile
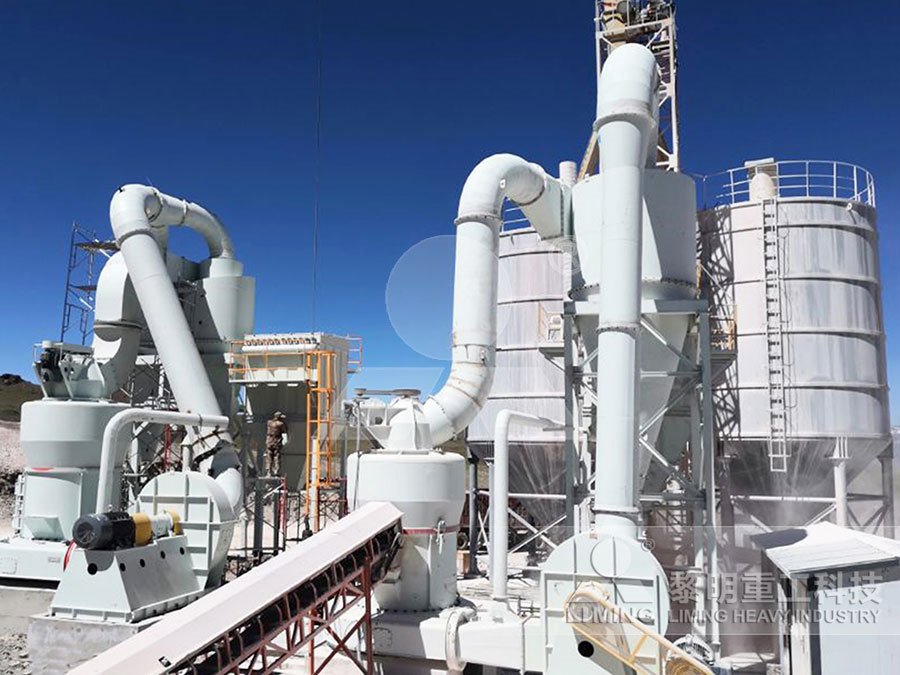
A LifeCycle Inventory of Limestone Dimension Stone Quarrying
Process flow diagram for limestone processing operations Processing commences with transportation of the (raw) stone from the quarry to the processing facility, as depicted by Screening steps similar to those in the Crushing/Sizing process (No 2) are also applied to some lime milling operations If hydrated lime is to be made, grinding equipment is employed to Industrial Process Profiles for Environmental Use: Chapter 18General process flow diagram for the manufacturing and processing of lime Lime manufacturing plants may be broadly divided into those that produce lime to be » More detailed!lime production flow diagram Grinding Mill Chinasafety, redundancies and reliable processes Christian Pfeiffer supplies engineering, mills and auxiliary equipment for limestone wet grinding plants in open and closed circuits which are EFFICIENT PROCESSES Wet limestone grinding for FGD
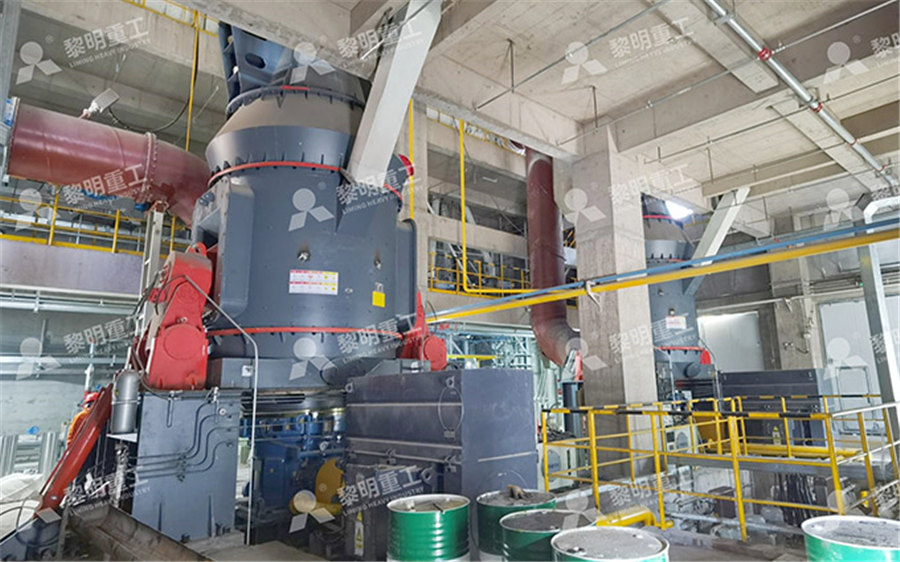
Backendoftheline (BEOL) Semiconductor Engineering
2024年6月20日 Description The backendoftheline (BEOL) is second major stage of the semiconductor manufacturing process where the interconnects are formed within a device Interconnects, the tiny wiring schemes in devices, are becoming more compact at each node, causing a resistancecapacitance (RC) delay in chips In the BEOL, there are many process 2012年6月1日 As the cylinder starts to rotate, the grinding balls inside the cylinder crush and grind the feed material, generating mechanical energy that aids in breaking bonds, activating the catalyst, and Grinding in Ball Mills: Modeling and Process ControlGrinding is the common collective name for machining processes that utilize hard, abrasive particles as the cutting medium The grinding process of shaping materials is probably the oldest in existence, dating from the time prehistoric humans found that they could sharpen their tools by rubbing them against gritty rocksGrinding Processes SpringerLink2024年3月1日 The main influencing factors for grinding damage include abrasive grit size, grinding depth, workpiece feed speed, and wheel speed According to the research of Sabia et al [13], the grinding subsurface damage depth (SSD) of glass ceramics is proportional to 5 times the average abrasive grit sizeMa et al [14] found that the SSD of fused silica is 4–6 times the Optimization of grinding process for hard and brittle materials
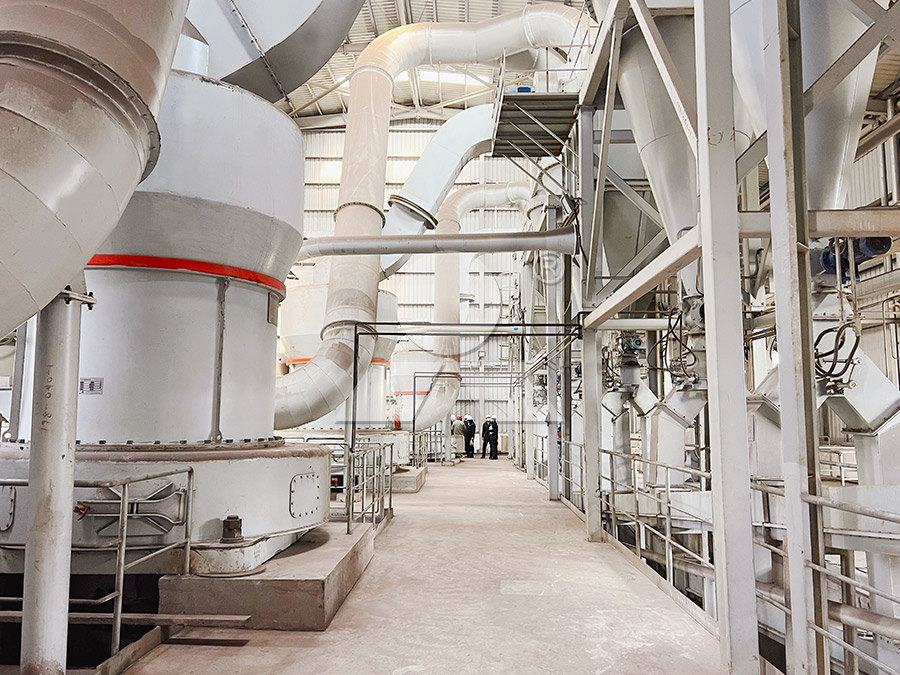
Grinding Parameters SpringerLink
2019年1月1日 'Grinding Parameters' published in 'CIRP Encyclopedia of Production Engineering' In general the material removal rate can be calculated by the actuating cross section A w, which is the cross section between tool and workpiece orthogonal to the feed directionA general overview on the process parameters and the calculation of the material removal rate Download scientific diagram Flow chart of grinding procedure from publication: Grinding Wheel Loading Evaluation by Using Acoustic Emission Signals and Digital Image Processing In the Flow chart of grinding procedure Download Scientific DiagramThe process can also optimize the flow coefficient or improve the high and low cycle fatigue strength of certain pieces Process Abrasive Flow Machining works by the back and forth flow under pressure of an abrasive laden, viscoelastic compound or abrasive media, through a holding fixture and over the area to be polished, deburred and radiusedAbrasive Flow Machining Systems Winbro Flow GrindingDownload scientific diagram Process flow chart of preparation of pellets from publication: Pelletisation Behavior of Fluxed Iron Ore Pellets of Varying Basicities Made with Waste Fines The Process flow chart of preparation of pellets ResearchGate
.jpg)
Effect of Moisture Content on the Grinding Process and Powder
2018年6月1日 Moisture content is also a critical parameter in the grinding process as it significantly impacts various aspects, including grinding time, particle size, and power requirements (Jung et al, 2018)Another alternative process that is beginning to emerge in the United States is the parallel flow regenerative (PR) lime kiln This process combines 2 advantages First, optimum heating conditions for lime calcining are achieved by concurrent flow of the charge material and combustion gases Second, the multiple1117 Lime Manufacturing US EPA2021年8月21日 In the forming grinding of a cemented carbide microdrill, edge burrs are generated To explore the formation of the edge burrs, the grinding parameters, such as feed rate, grinding depth, wheel service time, and wheel rotation, are analyzed experimentally Results show that the burrs on the microdrill edge are caused by material plastic flow and cumulative effect The effects of grinding process parameters of a cemented 2024年6月8日 To investigate the effect of microscale grinding on the quality of ITO conductive glass, this paper conducted microscale grinding experiments on ITO conductive glass The influence of process parameters on machining quality was analyzed using microgrinding force, surface roughness, and sheet resistance as indicators Meanwhile, sodalime glass was set as Experimental investigations into the effect of process parameters
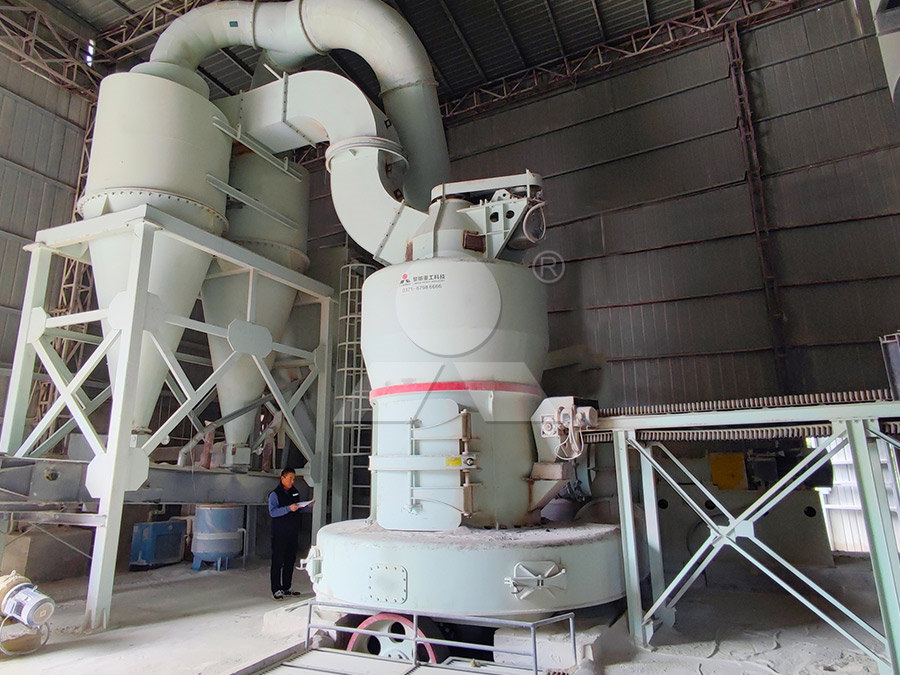
Cement Grinding Unit Process High Quality
In raw grinding, a ball mill with a high efficiency separator is used to achieve uniform particle size in raw mix for the next stages of the manufacturing process At the Cement Grinding Stage, 90 – 95% of the clinker is mixed with gypsum 2022年11月12日 Cocoa nibs are ground using a colloid mill In the process of grinding the sauce, the large particles of cocoa crumbs will become particles of only about 015mm under the highspeed shearing and friction of the colloid grinding rotor, and the efficiency is very high 3 Pressing Cocoa Liquor – Cocoa ButterCocoa Processing Flow Chart (From Bean To Powder)2020年6月21日 For instance, it was shown, that only viscosities high enough to impact the kinetic energy have an impact on the grinding process Additionally, radiometric densitometry was used to investigate grinding media transport A high correlation between tip speed and volume flow on the grinding media transport along the horizontal axis could be detectedDynamic Process Models for Fine Grinding and Dispersing2016年5月12日 Uranium Extraction Process Uranium Lime Flotation Circuit Acid leaching of high lime ores is extremely costly Ores of this type are sent to “SubA” Flotation Machines for removal of a selective lime concentrate The lime flotation concentrate would pass to a Thickener for dewatering prior to carbonate leaching to recover uraniumUranium Ore Processing Methods 911Metallurgist
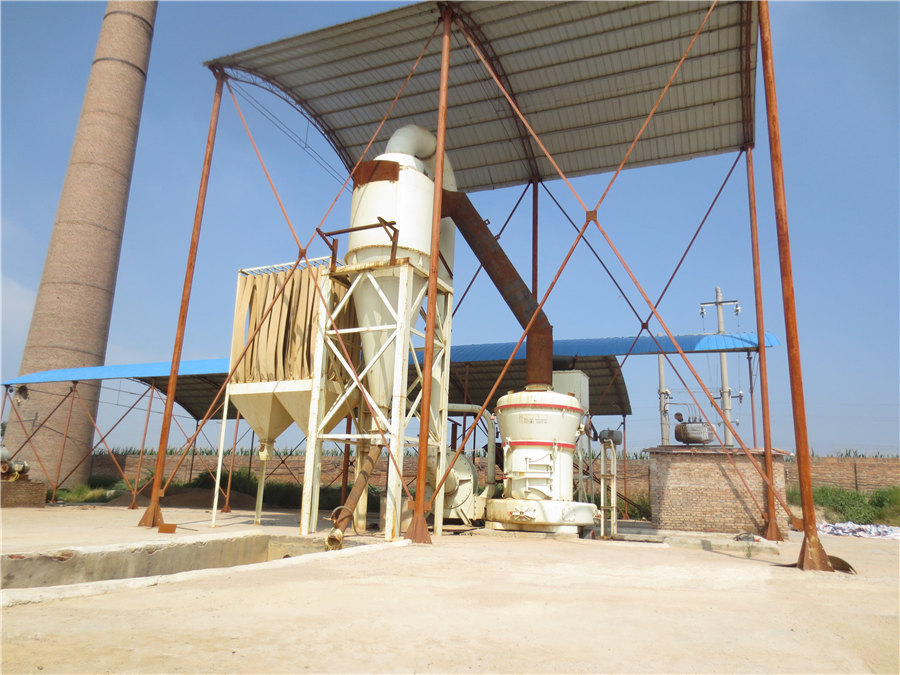
1117 Lime Manufacturing US EPA
1977年5月3日 1117 Lime Manufacturing 11171 Process Description15 Lime is the hightemperature product of the calcination of limestone Although limestone deposits are found in every state, only a small portion is pure enough for industrial lime manufacturing To be classified as limestone, the rock must contain at least 50 percent calcium carbonate2016年11月10日 Let us apply these ideas to the derivation of an equation for the rate of grinding in a mill It follows that if, as appears reasonable, the change of specific surface S cm²/cm³, within a mill depends upon the diameter of the mill, upon the ball diameter and upon the mean diameter of the particle, D, d and b respectively, upon the density of the balls and the pulp, q and σ Grinding Process 911Metallurgist2022年6月24日 Grinding is a manufacturing process which significantly contributes in producing high precision and durable components required in numerous applications such as aerospace, Li C, Zhang Q, Wang S, et al Useful fluid flow and flow rate in grinding: an experimental verification Int J Adv Manufacturing Tech 2015; 81(5): 785–794A comprehensive review on the grinding process: Advancements 4 T INTRODUCTION This is a guide to handheld grinding The information is mainly of a practical nature, intended for operators and others professionally involved with these toolsPocket Guide to Grinding Technique Atlas Copco
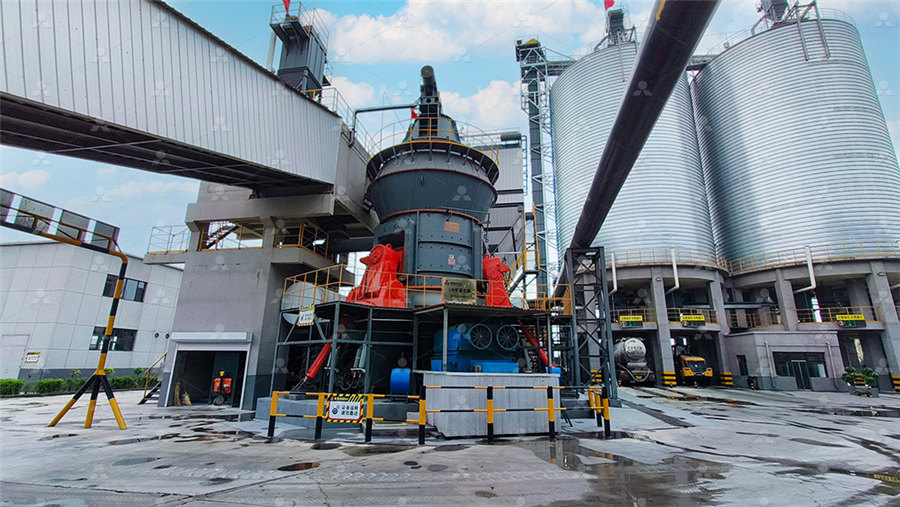
What is the process flow of rock grinding production line?
2024年1月2日 Grinding rocks into powder, the general process includes crushing, grinding, etc The specific grinding process is as follows: 1 Crushing: The stone is evenly sent to the jaw crusher through the vibrating feeder for crushing to obtain stone with smaller particle size, and then sent to the silo through the bucket elevator; 22023年11月1日 To fabricate the similar ultraprecision surface, like tooth surface of high precision grade gear, the precision grinding process was employed to machine a top surface of the stainless steel bulk The surface roughness of the ground surface was around 0239 μm 0227 μm, and 0231 μm at the inlet, middle and outlet regions respectivelyMachinability and mechanism of abrasive flow machining ultra The grinding of ore is a highly energyintensive process [1–4] In this process, the size of the particle obtained depends on the energy consumption of the ball mill The major challenge encountered in the process of iron ore grinding is to maintain the desired product particle size distribution (PSD) with sufficient liberation of valuable (PDF) Estimation of Grinding Time for Desired Particle Size 2021年7月6日 Before implementing the improved flowline production system, the workers could only depend on a commonsense judgment It could eventually incur procedural complexity in a manufacturing procedure, failure to manage time properly, frequent interruption of Balancing of the Production Line Process in the Manufacturing
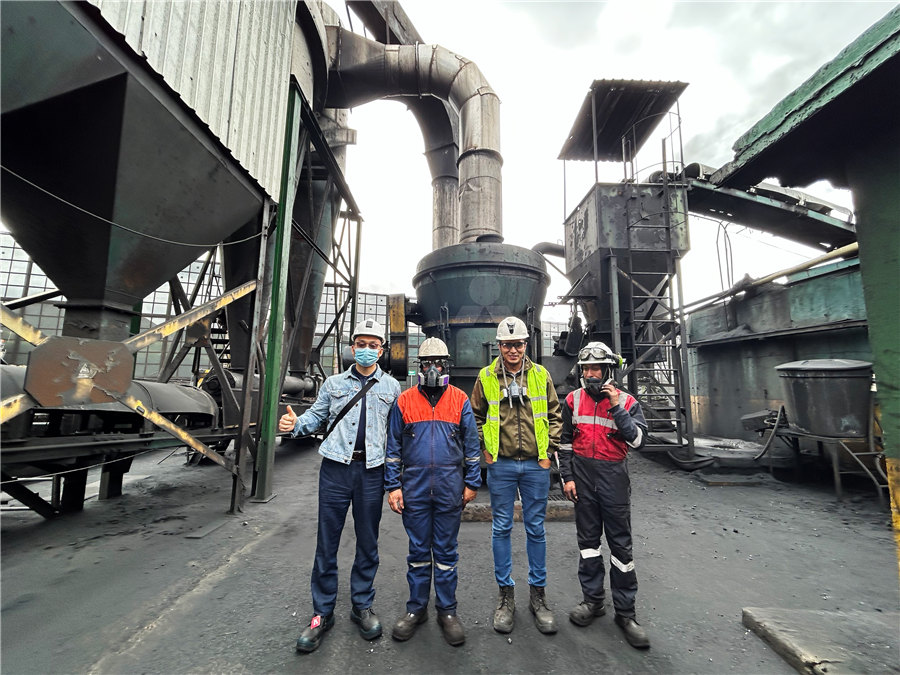
Development of an expert system for optimal design of the grinding process
2021年7月12日 The physical or empirical modeling of the grinding process and the effects of its parameters on the workpiece quality is sophisticated This is due to the extreme complexity of the process So far, no remarkable success could be made by the proposed models to achieve a reliable and effective design and control of the process This article introduces an expert 2019年6月11日 The effects of grinding (mediumcoarse) and extraction time (14–22 h) on the physicochemical and sensorial properties of cold brew coffee produced using two types of Colombian specialty coffees Effect of grinding, extraction time and type of coffee on the process auditing, capacity upgrades troubleshooting operations analysis process calculations and flow diagrams process selection and equipment sizing analysis of optimum material storage requirements development of costeffective engineering solutions commissioning info@saxuming saxumus saxuming engineered solutionsPROCESS ENGINEERING FOR THE CEMENT LIME INDUSTRIES Download scientific diagram Typical cement manufacturing process flow diagram [4] from publication: Model Development for CO2 Capture in the Cement Industry Climate change has become a Typical cement manufacturing process flow diagram [4]
.jpg)
BRPL Home Brahmani River
Coke dust is used as a compensatory fuel and to improve physical strength of the pellets by uniform firing of each pellet up to the core Both Lime stone and coke are ground in a definite lime to coke ratio in a ball mill by Dry grinding process The product is lime + coke powder mix of desired fineness is stored for subsequent mixing process2023年9月1日 Based on the machine learning method, this study analyzed the full process parameters (ie, ball mill power, fresh ore feed rate, hydrocyclone feed pump power, hydrocyclone pressure, mill feed water flow rate, dilution water flow rate, and sump level) for industrial grinding circuitAnalyzing process parameters for industrial grinding circuit based 2024年1月26日 This step facilitates the subsequent grinding process by preparing the chilli for optimal extraction of flavors and heat Sauce grinding: The crushed chilli are then fed into a grinding machine where they are finely Chili Sauce Manufacturing Process Flow Chart2022年2月28日 Generally, grinding process efficiency can mainly be improved by either improving the grinding behavior of the material being ground or enhancing the grinding machines Recently, the use of additives socalled grinding aids, which is applied in a small amount of 001–025 wt% related to the mass of product, has reduced these problems and been Grinding SpringerLink
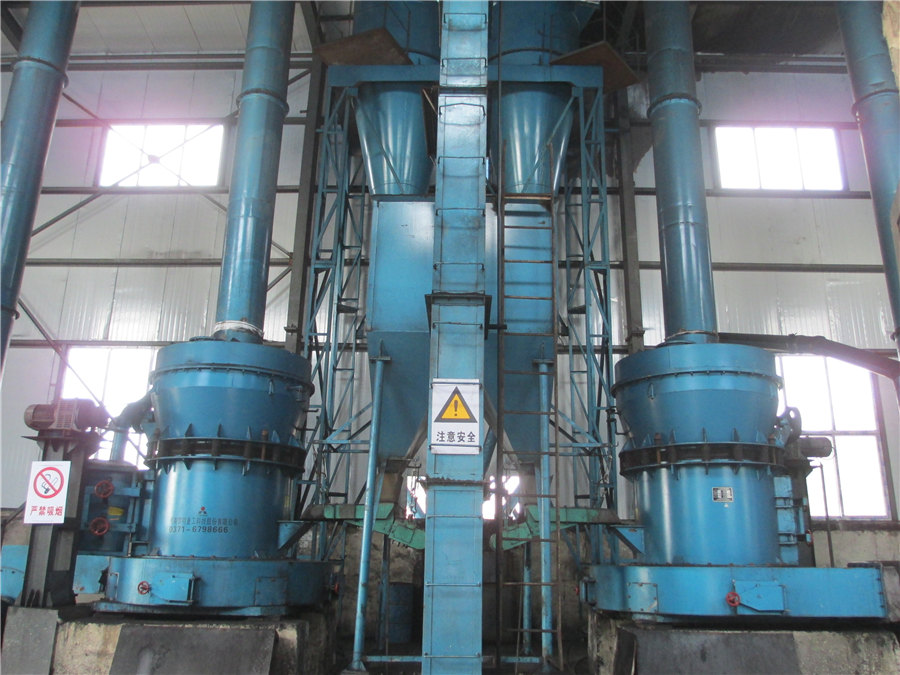
Quicklime preparation Gebr Pfeiffer
Quicklime reacts with water, generating a great amount of heat We distinguish softburnt lime, mediumburnt lime, and hardburnt lime In the construction industry, quicklime is added to mortar It can also be used as a drying or 2013年5月9日 Surface grinding is the most common process used in the manufacturing sector to produce smooth finish on flat surfaces Surface quality and metal removal rate are the two important performance (PDF) Optimization of Process Parameters in Surface Grinding 2023年8月22日 In the process of doublesided grinding, the grinding temperature, wheel wear, wheel clogging, and other problems will affect the final machining quality The use of grinding fluid is an important means to reduce grinding temperature and improve machining quality At present, the research on the flow characteristics of doublesided grinding is not deep enough, resulting Analysis of grinding fluid efficiency in doublesided grinding2014年9月1日 Grinding aids (GAs) are increasingly used during cement production to reduce energy consumption and/or optimize clinker factor This paper seeks to assess the effect of such additions on Effect of clinker grinding aids on flow of cementbased materials
.jpg)
Energy Prediction Models and Distributed Analysis of the Grinding
2023年8月14日 Grinding is a critical surfacefinishing process in the manufacturing industry One of the challenging problems is that the specific grinding energy is greater than in ordinary procedures, while energy efficiency is lower However, an integrated energy model and analysis of energy distribution during grinding is still lacking To bridge this gap, the grinding time 2009年1月1日 The design outcome is a process flowsheet that specifies the required equipment and their arrangements in the beneficiation plant The iron ore beneficiation plants normally include a series Processing of Magnetite Iron Ores–Comparing Grinding Options2022年6月23日 The flow conditions of the grinding fluid during grinding are analyzed with regard to the problem of easy burns during surface profile grinding of difficulttomachine materials, nickelbased hightemperature alloys The CFD simulations were carried out to analyze the grinding fluid flow in the grinding zone during flat and circular profile grinding according to the Analysis of grinding fluid flow in hightemperature alloy surface 2020年1月3日 Iron ores obtained from different sources differ in their chemical and physical properties These variations make the process of grinding a difficult task The work carried out in this context focuses on three different samples of iron ore, viz, high silica high alumina, low silica high alumina, and low silica low alumina The grinding process for all the three iron ores is Estimation of Grinding Time for Desired Particle Size Distribution