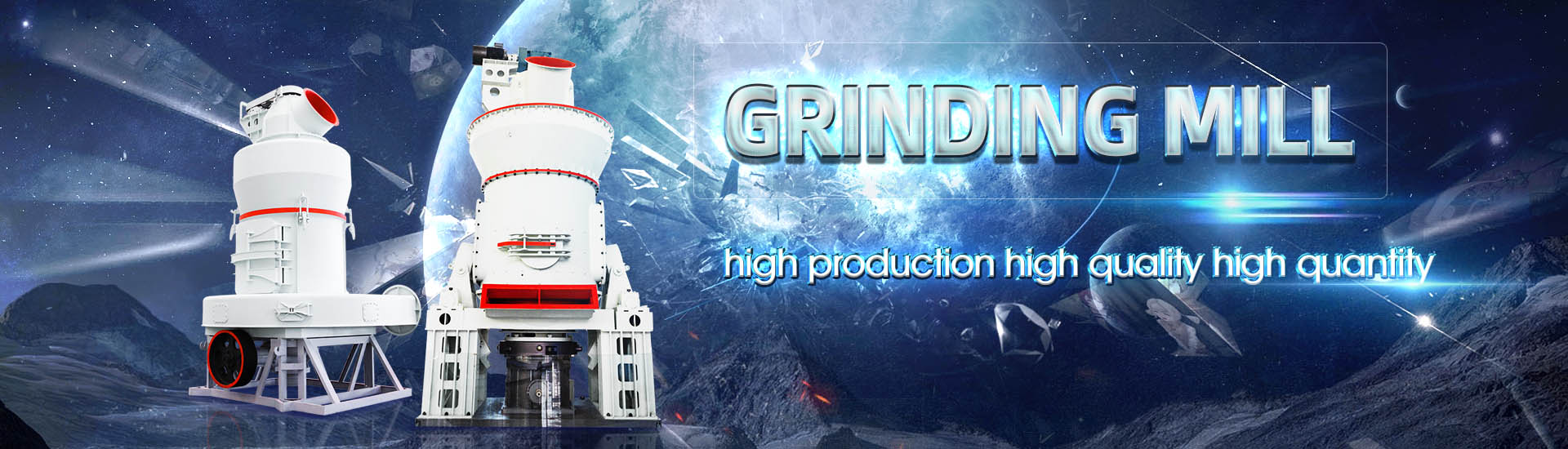
Casting pouring riser high fine vertical mill
.jpg)
THE RAUTOMEAD UPWARDS VERTICAL CONTINUOUS CASTING
Casting dies are small tubular graphite inserts, machined from high quality fine grained material These are fitted into supercooler die assemblies, comprising a casting insert, a series of 2021年11月1日 The systematic review gives an overview of various optimization software for casting processes and the importance of gating and riser optimization As the industries A systematic review on methods of optimizing riser and gating sufficient feed metal without the shrinkage pipe in the riser extending into the casting As shown in Figure 1, there are two common riser configurations: the top riser, which is typically more Feeding Risering Guidelines for Steel Castings Foundry Gate2022年5月24日 The position and quantity of risers shall be determined according to the structure of steel castings, the position of hot joints and the pouring method The size of the riser is calculated according to the empirical Process design of riser system for steel castings – ZHY
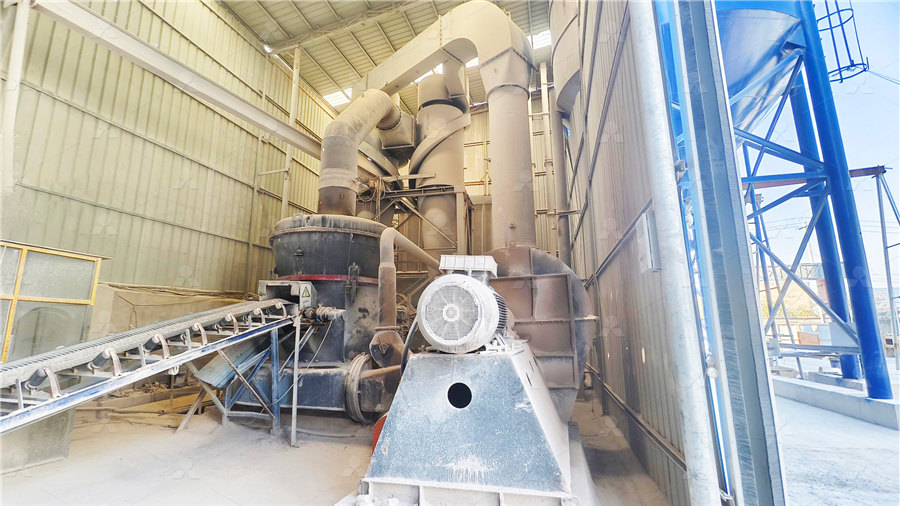
Research and Development of Gating and Riser Process
With the development of highspeed computer technology, casting CAE and casting CAD effectively improve the design efficiency and accuracy of casting process To achieve the rapid 2009年4月1日 The optimal design of a casting feeding system is considered The riser topology is systematically modified to minimize the riser volume, while simultaneously ensuring that no defect appears(PDF) Optimal riser design in sand casting process with • Provide a riser (feeder) which is a reservoir to feed molten metal to the casting as it solidifies to prevent internal and external shrinkage in the casting The riser may have to provide up to 5 MSE(324(( CASTING(and(SOLIDIFICATION(2024年2月1日 Four common metals aluminum, brass, gunmetal, and cast iron are evaluated to determine which makes the best riser In this study, we use Taguchi L9 orthogonal array Optimization and empirical studies of riser design in sand casting
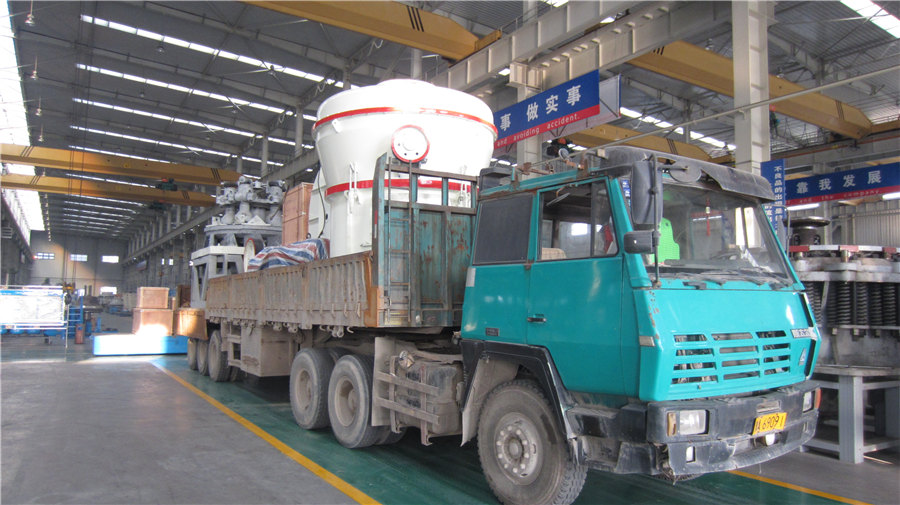
Selecting and applying risers to optimise casting
A riser (also called a feeder) attaches to the mould at the point of molten metal entry, to prevent cavities from forming due to shrinkage during solidification because the last point to solidify is outside the mould proper A combination of Pa ge 3/ 18 Runner/riser system design to make good quality castings and enhance the yield of casting in investment casting of industrial parts using casting simulation tools is very successfuloptimizing runner/riser system casting of centrifugal pump 2019年6月6日 Casting is the most widely used manufacturing process which involves melting of metal ores, scrap metals, carbonaceous material, alloying elements, fluxes and other additives in hot furnaces from where the liquid metal is collected by the ladle to be poured over the pouring basin, delivering the molten metal into the mould cavityCasting SpringerLinkHence, the riser solidified after the solidification of mill roller 518 Effect of pouring heads on mill roller casting The high pouring head can delay the molten metal in air before it entered to the pouring cup Due to this effect, air Design and analysis of sand casting process of mill
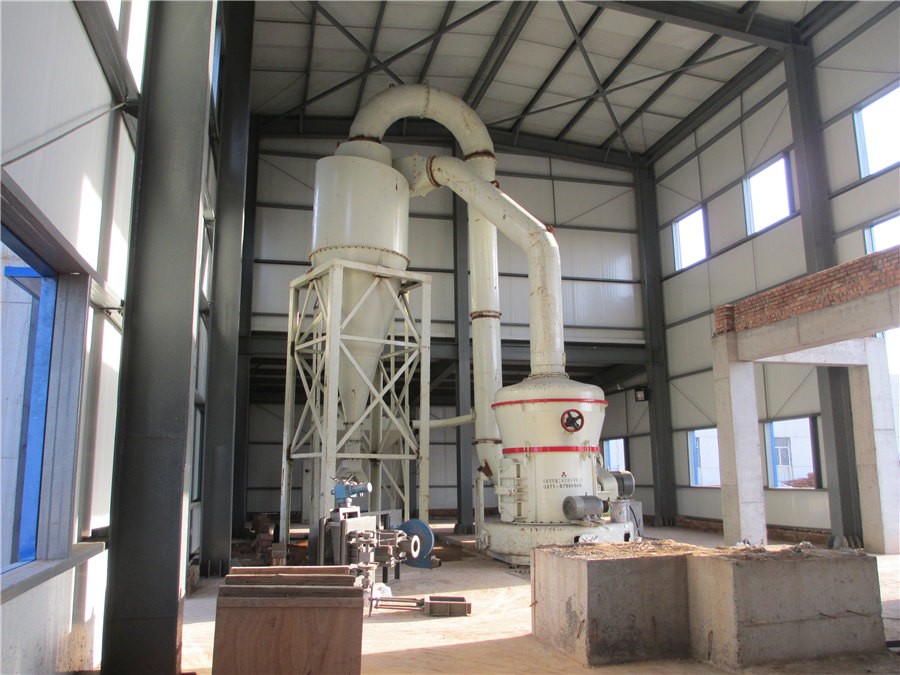
(PDF) Shrinkage, Feeding and Riser Design ResearchGate
2014年4月9日 To produce sound, high quality components, one must design the mold so liquid metal is fed to the casting while it freezes The feeding process and riser design are complicated by the high thermal 112 Casting Casting is the process of producing metal parts by pouring molten metal into the mould cavity of the required shape and allowing the metal to solidify The solidified metal piece is called as "casting" 113 Foundry It is the place where both moulding and casting is done 12 Sand Casting /Sand MouldingUNIT – I – Metal Casting Process – SMEA1401CHAENG can manufacture highquality rocker arms The rocker arm is one of the main components of the vertical roller mill Each set of rocker arm includes an upper rocker, a lower rocker, a center shaft, a bearing seat, and a bearing, mainly to transfer hydraulic pressure to the grinding roller, and turn it into the grinding force to the material bedVertical mill rocker arm CHAENG2024年9月22日 Resin Casting Resin casting involves pouring a liquid synthetic resin into a mold, which then hardens at room temperature or under heat to form solid plastic parts This process is favored for its ability to replicate fine details and achieve highquality surface finishes without the need for postprocessing Main Benefits:What is Casting: Definition, Process and Types
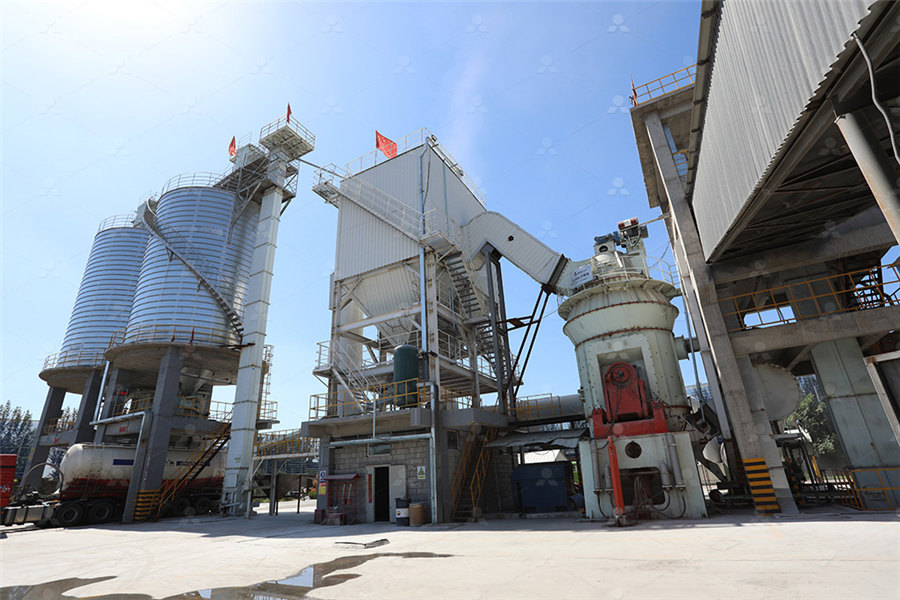
Causes of casting cracks and six kinds of common defects and
2021年5月30日 3 Improper design of the position of the casting in the mold 4 The design of pouring and riser failed to play the role of full feeding 5 The pouring temperature is too low or too high Prevention and control methods: 1 Increase the temperature of abrasive tools 2Design Riser (or Feeder): Riser design involves optimizing size, position, and shape to compensate for metal shrinkage and release gases during casting Checking Gating Design Effectiveness The effectiveness of gating system design can be verified through techniques such as waterfilled transparent molds, highspeed radiography, open molds, and contact wire sensorsUnderstanding Gating Systems in Casting: Types and Design Vertical continuous casting has been the strength of Wieland Concast's production for over a third of a century As the metal flows down into a watercooled die at the bottom of the crucible during vertical continuous casting, solidification of the alloy occurs The cast product continues smoothly downward through rollers beneath the dieHorizontal Vertical Continuous Casting Production Process2017年3月21日 10 Risering • A riser or feeder head is a vertical passage made in the cope to store the liquid metal and supply the same to the casting as it solidifies Functions: • Store sufficient liquid metal and supply the same to the Gating and riser in casting PPT SlideShare
.jpg)
Riser In Casting Types Diagram Design Riser In
The felting cost to separate the riser from casting is high Riser In Casting Design (Riser Size) Naval Research Laboratory Method The naval research method becomes important when calculating volume to the surface area becomes 2021年11月17日 Design Pouring Cup, Feeder, Riser, Runner, Ingates +86 marketing@precision but also their gating system (metal delivery system) to result in high quality products Gating system guides and How to Design the Gating System of Investment Moulding High Pressure Mould Line (HPML) Sinto® FBO III N Box Size 508x660x190/190mm Wt 4 Kgs to 36 Kgs DISA ARPA 300 Moulding Machines – 2 Lines Box Size 400x520x200 / 150mmKLRF Super Casting2024年6月27日 Sand casting is a versatile and widely used process for creating metal components with complex geometries One of the critical aspects of sand casting is the design of the gating and risering systems These systems control the flow of molten metal into the mold and ensure proper feeding during solidification, significantly impacting the quality, efficiency, and Optimizing Gating and Risering Systems in Sand Casting
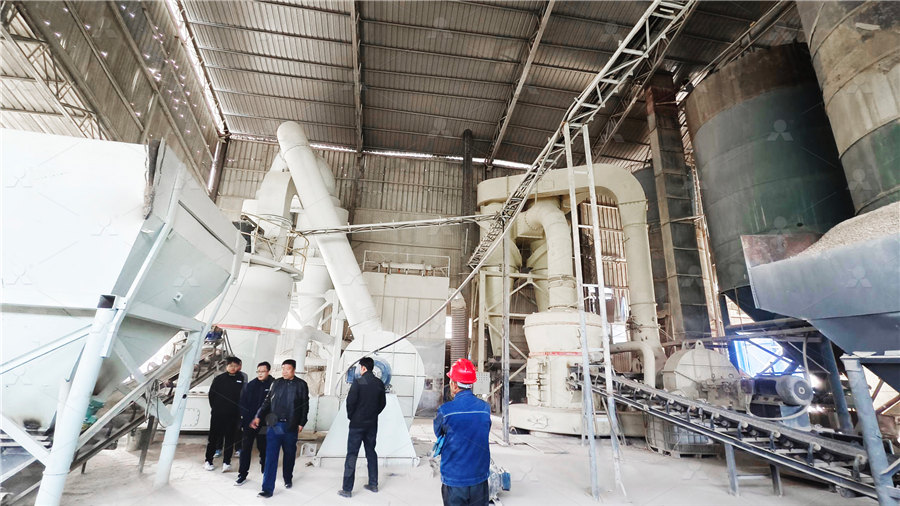
Design and analysis of sand casting process of mill roller
ber of process parameters during sand casting mill roller The aim of this research workis todesign and analyze sand casting process of mill roller Taguchi’s approach of quality engineering is to minimize the rejection rate of sand casting mill roller due to defects 2 Literature review A lot of work has been carried out by several researchers2021年8月15日 The phase transformations in solidification of steel are accompanied by shrinkage and sudden changes in the solubility of alloying elements, resulting in negative side effects as micro and Optimization of Shrinkage Porosity in Grinding Media Balls by Casting Design of pouring system for high manganese steel castings (traditional casting) (1) Shrinkage rate of high manganese steel wire: 24%~32% for small parts, 20%~25% for large parts Under sand casting conditions, the general casting linear shrinkage rate (scale reduction) is selected from 25% to 27%, and different castings have different linear shrinkage rates in Production Technology of High Manganese Steel Castings2018年1月1日 In this present work, the grinding balls from high chromium white cast iron (ASTM A532) were produced by using sand moldgravity casting The simulation casting process was conducted before Simulation for grinding balls production using sand moldgravity casting
.jpg)
METAL CASTING PROCESSES PPT Free Download SlideShare
2019年7月18日 2 Steps in Casting Process • Melting the metal • Pouring it into a previously made mould which will give the shape for the part • Allowing the molten metal to cool Solidify in the mould • Removing the solidified component from the mould, cleaning it subjecting it to further treatment • The solidified piece of metal, which is taken out of the mould is called Casting2024年9月6日 Enhancing Casting Quality with Effective Riser Design: Optimizing the design and placement of risers is paramount to achieving successful casting outcomes Factors such as size, shape, location, and material selection for risers play a crucial role in maximizing their effectiveness in compensating for shrinkage and ensuring highquality castingsRisers in Casting: Functions and Mechanisms Knowledge2009年4月1日 The dimensions of the gating and riser systems are strongly related to both the quality and cost of casting In terms of the riser, which is relatively simple and focuses mainly on material (PDF) Optimal riser design in sand casting process 2019年12月1日 The quality characteristics of the mill roller in sand casting has been affected by casting defects caused by in proper process parameter usage and intern affects its proper function that lead to Design and analysis of sand casting process of mill
.jpg)
Sand Casting Process, Defects, Design
Mold In sand casting, the primary piece of equipment is the mold, which contains several components The mold is divided into two halves the cope (upper half) and the drag (bottom half), which meet along a parting lineBoth mold halves are contained inside a box, called a flask, which itself is divided along this parting line2024年2月1日 Sand casting is a crucial manufacturing step in creating a quality product that will meet the demands of the market Four common metals aluminum, brass, gunmetal, and cast iron are evaluated to determine which makes the best riser In this study, we use Taguchi L9 orthogonal array design of experiment (DOE) analysis to the melting and vent hole Optimization and empirical studies of riser design in sand casting 2016年1月21日 This can result in cavities in the casting Risers prevent this by feeding molten metal to the casting as it solidifies The design of the risers, including the size and the number, is determined entirely by the casting requirements The risers must have sufficient capacity to supply the volume of molten metal needed to compensate for shrinkageRisers and runners Haworth Castings2020年3月31日 Computed tomography scans (CT) shows that parabolic sprue casting (PSC) and conicalhelix sprue casting (CHSC) reduced overall casting defects by 56% and 995% respectively when compared to Gating System Design Solutions for Casting Defects from Pouring

Steel Ingot Teeming SpringerLink
2023年7月15日 The pouring speed is usually 02–04 m/min, and the high limit is used for small steel ingots The pouring speed of top pouring is 1–2 m/min, and the maximum pouring speed (semikilled steel) is up to 7 m/min Demolding Time After pouring, the steel ingot cannot be demolded until the internal is fully solidified2022年9月5日 The dimensions of the gating and riser systems are strongly related to both the quality and cost of casting In terms of the riser, which is relatively simple and focuses mainly on material spending, singleobjective optimization algorithms, such as the genetic algorithm (GA) and evolutionary topology algorithm, have been successfully applied to determine the Optimal Design of the Gating and Riser System for Complex Casting 2018年9月24日 In this paper, the sand casting process was evaluated using ProCAST simulating software and practical experience for manufacturing of the high chromium stainless steel outlet diaphragms used in iron ore ball mill In the simulation practice, the effects of feeding and gating designs on the liquid flow, heat transfer and solidification phenomenon were Simulation of casting process: case study on the gating and G0667X 9" x 48" 3 HP HighPrecision VariableSpeed Vertical Mill A highperformance and precisioncontrolled Grizzly mill The G0667X 9" x 48" 3 HP HighPrecision VariableSpeed Vertical Mill is used to remove material from 9" x 48" 3 HP High Precision VariableSpeed Vertical
.jpg)
Sand Casting Process: A StepbyStep Guide Bunty LLC
Sand casting is one of the oldest and most widelyused methods of metal casting, dating back to around, and even before, 10,000 BC The process employs sand for the main mold material, as this material can be shaped and compacted to Continuous casting is a refinement of the casting process for the continuous, highvolume production of metal sections where the metal is poured to produce the casting Riser: This can be advantageous because finegrained castings The Casting Process Explained Bernier MetalsRiser Contact (Gate Contact) The connecting passage between a riser and a casting See Casting, Riser Riser, Blind A riser that does not break through the top of the cope and is entirely surrounded by sand; opened to the atmosphere by means of a firecracker core Riser, OpenWhat is Aluminum Casting? Boose Aluminum Foundry2016年12月23日 Thus it results for small riser size and high casting yield • 3 It is very important to note that volume feed capacity riser • The casting is usually a finegrained casting with a very fine quot;lost waxamp;quot; casting Pouring The mold is preheated in a furnace to approximately 1000°C (1832°F) and the molten Casting process PPT Free Download SlideShare
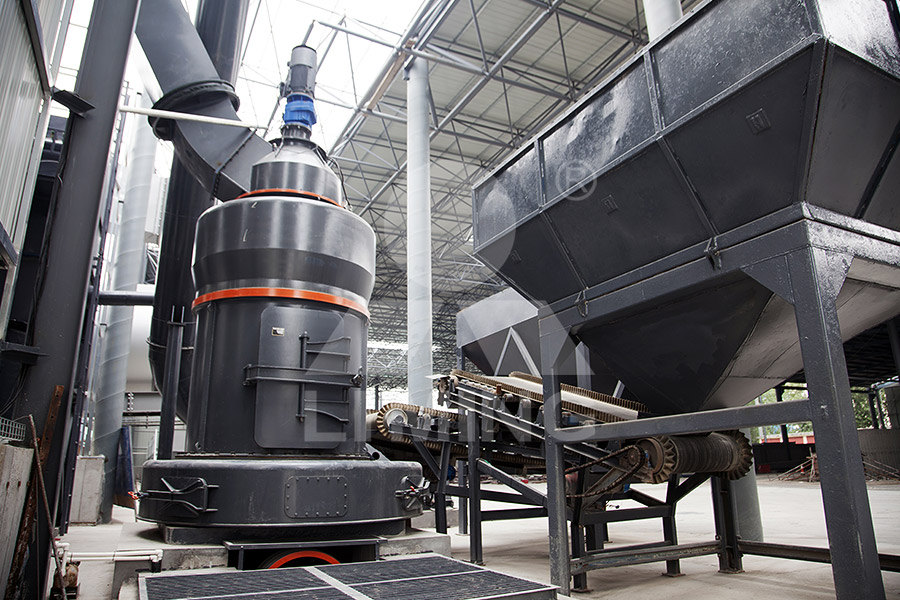
Sprue in casting refers toa)Gate b)Runnerc)Riser d)Vertical
Explanation:Sprue is an important component in casting, which is used to facilitate the flow of molten metal into the mold cavity It is a vertical passage that connects the pouring basin or cup to the runner system of the mold The sprue is responsible for carrying the molten metal from the pouring basin to the runner system and then to the mold cavityThe following are the key 2022年10月25日 (a) Front view of the Pareto front, (b) left view of the Pareto front, (c) top view of the Pareto front, and (d) Pareto front obtained by NSGA IIOptimal Design of the Gating and Riser System for Complex Casting 2023年11月9日 CLEAN STEEL CASTINGS AT ULTRALOW POURING TEMPERATURES FOR HIGH PERFORMANCE The Process involves a rotary treatment process that stirs the metal in the ladle whilst passing a curtain of fine Argon Foundry Practice 267, ADVANCES IN THE POURING OF STEEL CASTINGS WITH A SHROUDED METAL STREAM (2019) [10] CH CLEAN STEEL CASTINGS AT ULTRALOW POURING TEMPERATURES FOR HIGH 2023年8月18日 The position of the casting in the mold is not designed properly The design of the pouring riser fails to achieve the effect of full supplementation The pouring temperature is too low or too high Prevention Methods: Increase the temperature of the grinding toolPrevent 6 Common Casting Defects with These Tips MachineMFG
.jpg)
(PDF) Metal Casting ResearchGate
2020年3月8日 Some time in diecasting we inject the molten metal with a high pressure When we apply pressure in injecting the metal it is called pressure die casting process