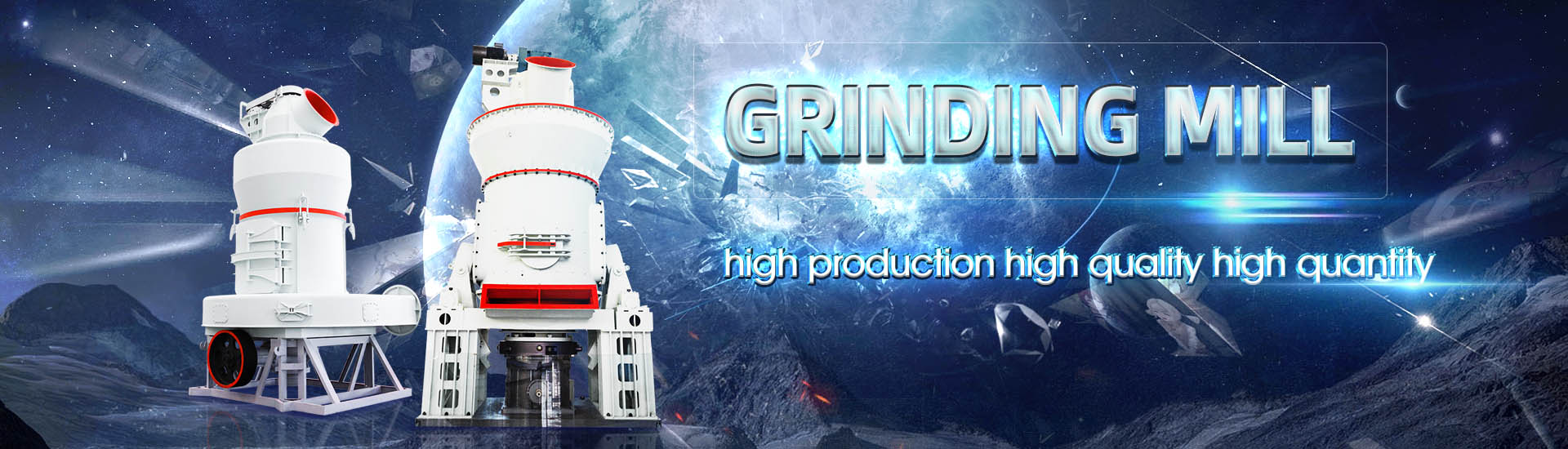
Dehydrated slag processing
.jpg)
Dry Slag Granulation: A Path to Improving the Safety and
2016年8月23日 Slag dumping and water granulation are the most commonly used slag treatment methods in the metallurgical industries In both processes, water is present (by desire for cooling and dispersion or as a result of rain accumulation) and thus equipment and Our dry slag granulation technology transforms molten slag from steel furnaces into granules using air stream, eliminating the need for water The flexibility of the process allows obtaining granules of different sizes and with different ratio Slag Dry Granulation TenovaTypical slag management methods include dumping and water granulation Electric arc furnace (EAF), ladle metallurgy furnace (LMF), argon oxygen decarburization (AOD), and blast furnace RECENT DEVELOPMENTS IN DRY SLAG GRANULATION: A PATH 2017年1月7日 The research on the activation energy of crystallization of amorphous solids in BF slag is the foundation to find out the reasonable cooling speed during dry granulation of molten slag(PDF) Process and Equipment Design for the Dry Slag
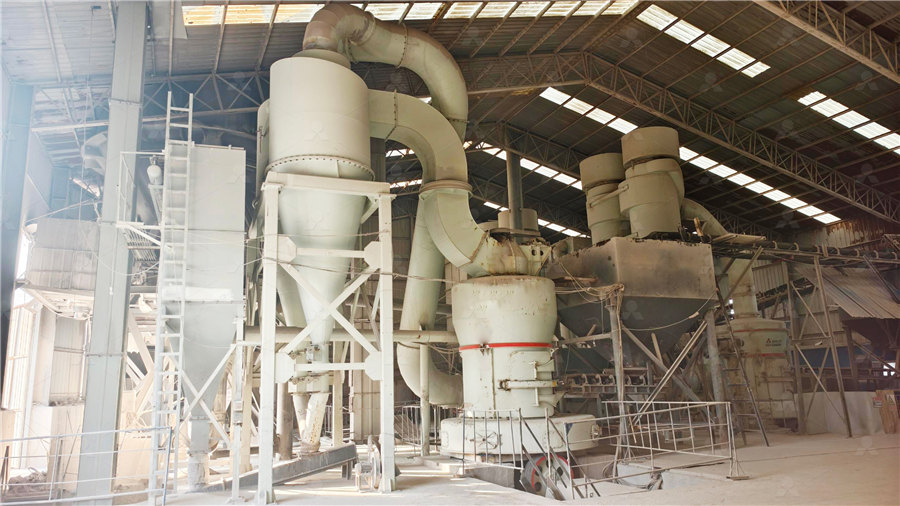
Some Fundamental Aspects of Dry Slag Granulation Process
Abstract: There is a growing interest in development of a dry slag granulation (DSG) process so as to recover the sensible and latent heats from molten slags and convert iron blast furnace Our sustainable, dry method for slag granulation derives value from waste and has the potential to transform the metal and cement industries Slag is a high volume byproduct from the metal smelting process Globally, hundreds of Dry slag granulation: producing valuable byproducts The BF slag of steel plant A was dealt with open cycle process (OCP) The granulated BF slag were almost amorphous solids as 100 % amorphous solids sample The component of the Process and Equipment Design for the Dry Slag Granulation Dry slag granulation is destined to replace conventional water granulation of molten slags in the not too distant future, creating a paradigm shift in the history of slag treatment In this dry Dry Granulation to Provide a Sustainable Option for Slag
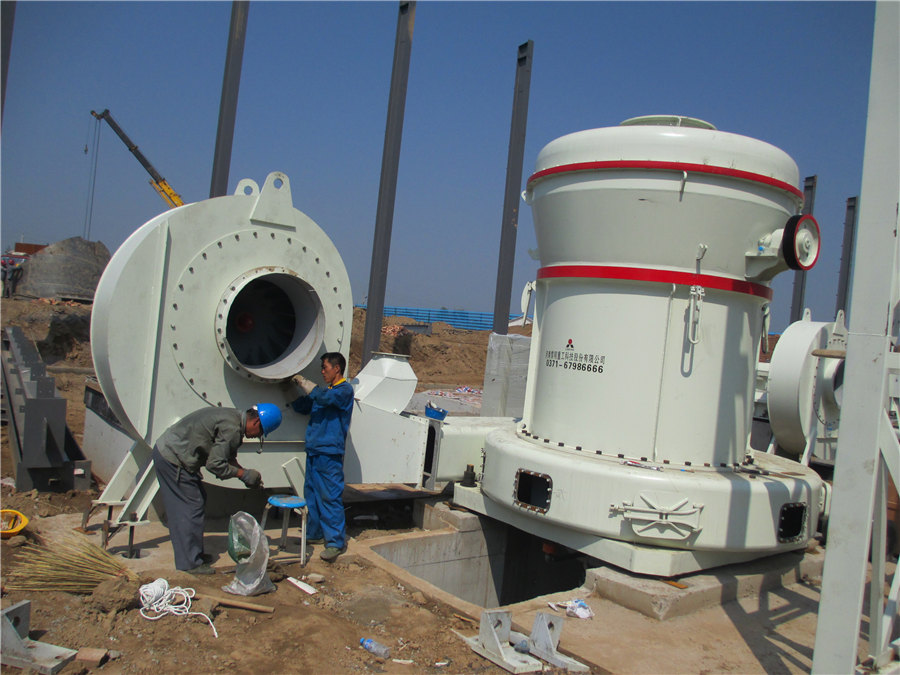
DRY PROCESSING AND HIGH QUALITY APPLICATIONS FOR STEEL
Based on proper slag processing, possible slag applications that are not completely implemented in the actual state of the art for slag processing/handling are introduced The implementation of this integrated concept in the industry requires a joint effort by steel makers, processing specialists and construction aggregate application and marketing departmentsPDF On Oct 1, 2012, Sharif Jahanshahi and others published Current status and future direction of CSIRO's dry slag granulation process with waste heat recovery Find, read and cite all the (PDF) Current status and future direction of CSIRO's Slags generated in metallurgical industry are high volume byproducts or wastes containing a large amount of heat In blast furnace ironmaking, for example, for every tonne of hot metal produced, about 300 kg of slag is generated The cooling of molten slag to ambient temperature can release up to 18 GJ/t of thermal energy Blast furnace slags are currently either water [PDF] CFD modelling of dry slag granulation using a novel Our dry slag granulation technology transforms molten slag from steel furnaces into granules using air stream, eliminating the need for water The flexibility of the process allows obtaining granules of different sizes and with different ratio between crystalline and amorphous phases to respond at the request of the final userThis innovative process integrates seamlessly into Slag Dry Granulation Tenova
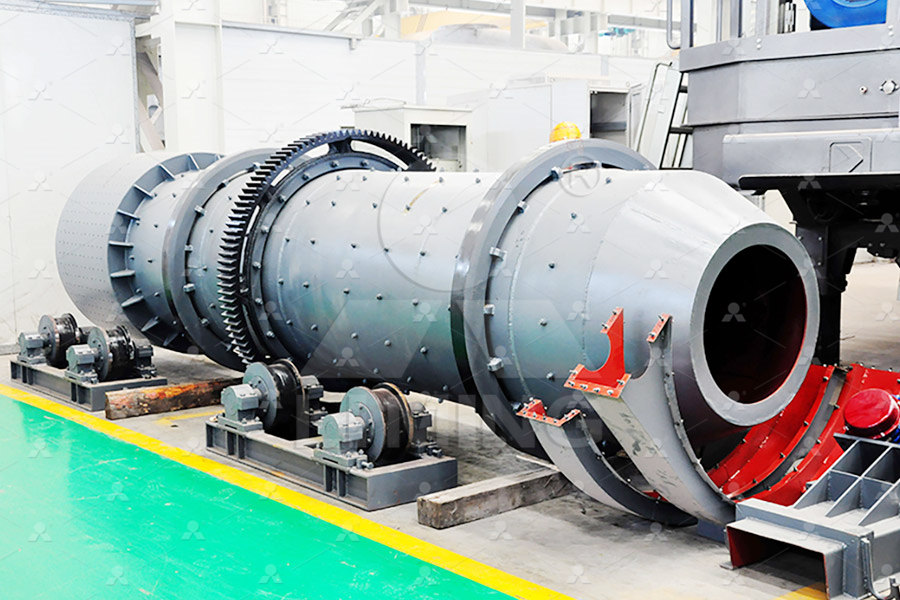
Dry processing of steel slags with Loesche mills for
2018年1月1日 Mobile plants developed by THE STANDARD are particularly generated for the processing of slag landfills and for the crushing of complex material in interim storage facilities of metallurgical plants2023年7月13日 This work proposes an environmentally safe and economically feasible method of waste coppernickel production slag utilization (Kola MiningMetallurgical Company, Nornickel, Kola Peninsula, Russia) This process involves the decomposition of slag by diluted solutions of sulfuric acid (7–10 wt% H2SO4) with a transfer in a solution of more than 70% silicon, 77% Deep Processing of Dump Slag from the CopperNickel Industry2017年9月1日 Molten slag from pyrometallurgical furnaces is tapped at high temperature, carrying a large amount of thermal energy But the common slag dumping and water granulation methods used for slag treatment do not permit energy recovery Furthermore, water is present in these processes and while operations are designed to minimize risks of steam explosions, RECENT DEVELOPMENTS IN DRY SLAG GRANULATION: A PATH 2016年8月23日 Abstract Slag dumping and water granulation are the most commonly used slag treatment methods in the metallurgical industries In both processes, water is present (by desire for cooling and dispersion or as a result of rain accumulation) and thus equipment and operations are designed to minimize and mitigate the risk of steam explosions resulting from the Dry Slag Granulation: A Path to Improving the Safety and Sustainability
.jpg)
Technical and economic evaluation of slag dry granulation
2012年5月7日 As a result of extensive RD in this area, the slagprocessing technologies are slowly converging around dry granulation combined with heat recovery In this paper, 2010年8月17日 Slag processing technologies, VA TECH, Melbourne, 9 10 August Fukuyama Works, NKK Japan, 1983 Blast granulation system of BOF Slag and its products, Nippon Kokan Dry granulation to provide a sustainable option for slag treatmentand iron ores However, current slag processing is far away from optimum conditions, especially for slag fines with small particle sizes, resulting in the generation of nonrecyclable ‘‘metallic’’ slag fines with insufficient iron content and great loss of iron in ‘‘nonmetallic’’ slag fines with excessive iron contentEnhancement of Iron Recovery from Steelmaking Slag Fines by 2017年9月1日 PDF Molten slag from pyrometallurgical furnaces is tapped at high temperature, carrying a large amount of thermal energy capable of processing 100 kg/min of slag(PDF) RECENT DEVELOPMENTS IN DRY SLAG
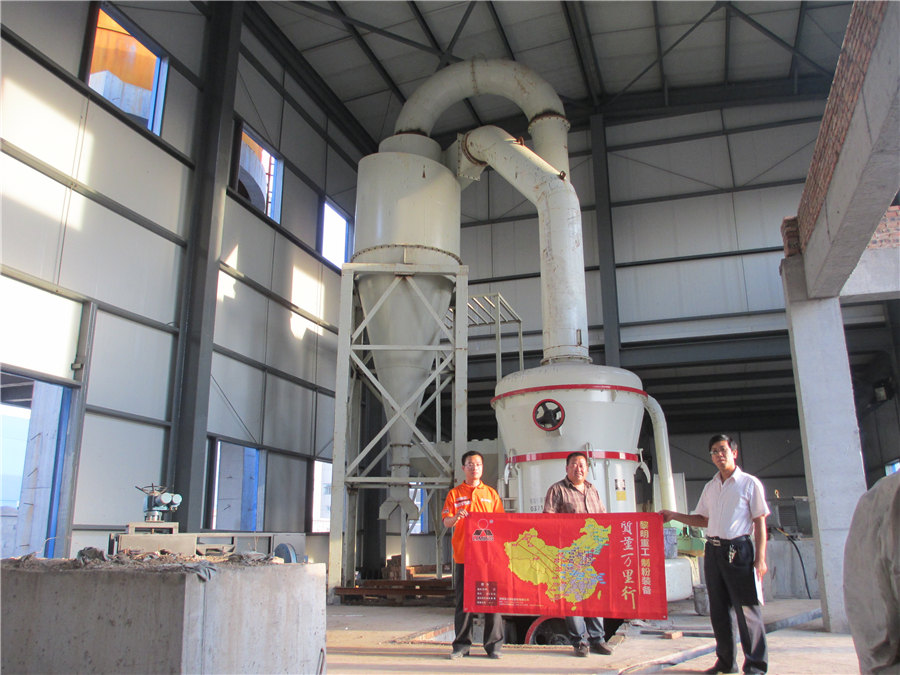
Dry Granulation to Provide a Sustainable Option for Slag Treatment
Dry slag granulation could provide an ideal solution for the abovementioned shortcomings of the existing slag processes In this new approach, molten slag is atomised under centrifugal forces exertedSteel slag is a typeof solid waste emitted from the steel making process It includes electric furnace slag, converter slag, and openhearth furnace slag, with emissions account for around 15% to 20% of crude steel production According to DRY MAGNETIC SEPARATION TECHNOLOGY FOR THE RECOVERY * Technical contribution to the 71º Congresso Anual da ABM – Internacional and to the 16º ENEMET Encontro Nacional de Estudantes de Engenharia Metalúrgica, de Materiais e de Minas, part of theRECENT DEVELOPMENTS IN DRY SLAG GRANULATION: A PATH 2019年2月22日 CSIRO has been working on a dry granulation process, integrated with heat recovery, since 2002 It involves a rotary disc that atomizes molten slag to produce liquid droplets, which are rapidly quenched to become solid granules The hot granules are fed to a countercurrent moving packed bed heat exchanger, where they are further cooled and finally Design and Operation of Dry Slag Granulation Pilot Plant
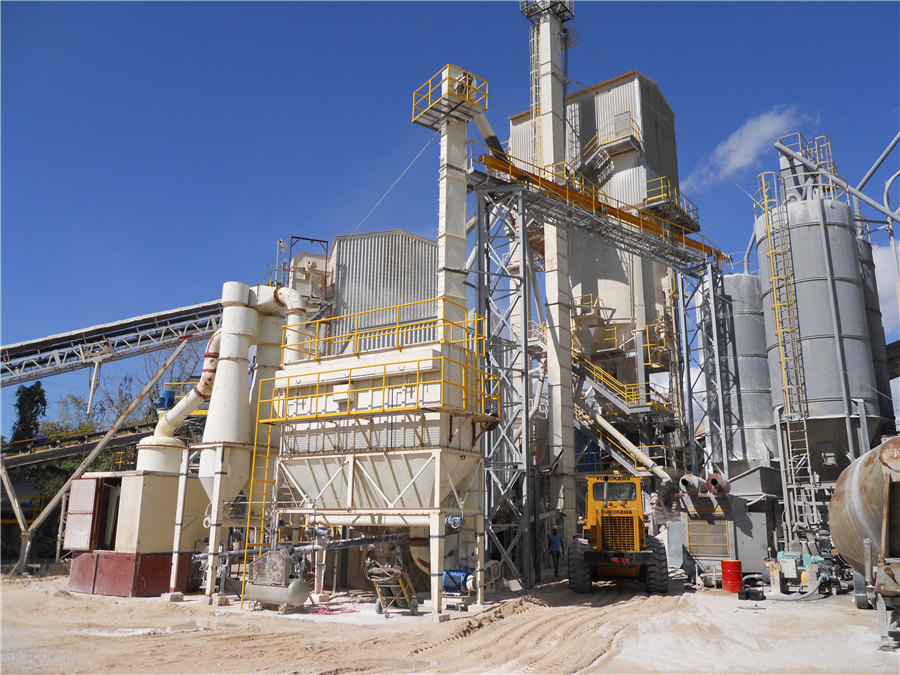
Dry / Wet Slag Cooling Conveyor General Kinematics
General Kinematics Dry Slag Cooling Conveyor eliminates popcorn slag, slag pans, and apron conveyors With GK’s Dry Slag System, slag is conveyed, cooled indirectly, and transformed into a semisolid pancake slag The patented indirect cooling trough technology of the Dry Slag Cooling Conveyor means slag can immediately be containerized or discharged to a quench slag, atomised iron, pyrrhotite removal from base metal sulphide concentrate, dense media (magnetite and ferrosilicon), recovery in coal wash plants, diamond processing, etc Metso (former Sala int Svedala etc) produced its first electromagnetic separators already in the 1890’sFor dry and wet processing Low Intensity Magnetic Separators 2016年7月28日 Steelmaking slags are usually processed for iron recovery by dry magnetic separation The recovered ironrich products are recycled back into the ironmaking and steelmaking processes to replace highcost steel scrap and iron ores However, current slag processing is far away from optimum conditions, especially for slag fines with small particle Enhancement of Iron Recovery from Steelmaking Slag Fines by Blast furnace slag is well known as byproduct of hot metal production in integrated steel and iron mills About 300 million tons of this slag is produced, based on a worldwide production of approximately 1100 million tons of hot metal per year State of the art systems cool down the liquid blast furnace slag rapidly by using lots of waterDry Slag Granulation Montanuniversität Leoben
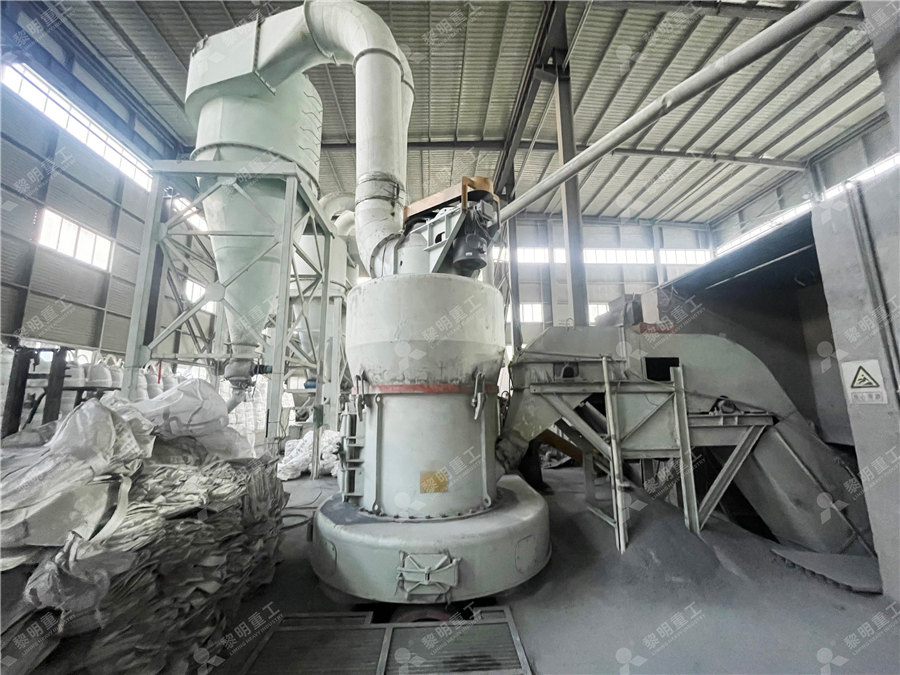
Dry Granulation to Provide a Sustainable Option for Slag
Compared with conventional wet granulation, the dry slag granulation process offers a more sustainable approach for processing molten slags through saving water, reducing pollution, as well as recovering waste heat to reduce energy consumption, hence GHG emissionsx000D FORMAL CITATION:Xie, D, Jahanshahi, S and Norgate, T, 2010These conventional slag processes, however, have some major short comings, from no heat recovery, air pollution, to consumption of a large amount of water Dry slag granulation using a spinning disc is emerging as an attractive alternative for slag processing TheCFD SIMULATION OF FREE SURFACE FLOW AND HEAT TRANSFER OF LIQUID SLAG First CSRP Annual Conference, Melbourne, 2122 November 2007 2 900 rpm, 2 mm drop, 1400oC 900 1000 1100 1200 1300 1400 01 23 Time, s Temp, o C 0 20 40 60 80 100 Solid % Solid % Surface Centre Heat Recovery from Slag through Dry Granulation ResearchGate2020年7月4日 The world’s leading countries develop dry slag granulation units that are capable of producing solid slag granules and recovering the sensible heat of slag The main element of such units is a granulation chamber where molten slag is atomized and solidified In this chamber, up to 30% of the sensible heat of the molten slag is extracted To recover more heat, the solid Heat Transfer in Fluidized Beds in a Dry Slag Granulation Unit
.jpg)
Some fundamental aspects of the dry slag granulation process
PDF On May 27, 2012, Sharif Jahanshahi and others published Some fundamental aspects of the dry slag granulation is expected to be replaced by dry postprocessing technologies due to the 2024年2月7日 This study demonstrates that the strength of the dehydrated cement pasteslag composite cementitious material is superior, with higher strengths observed at 7 days and 28 days compared to the original Portland cement paste Notably, in contrast to Portland cement, Mechanical properties and hydration behavior of dehydrated 2009年4月3日 interlocked slag and metallic magnesium and sized to minus 4 mesh plus 14 mesh objective – to concentrate the particles of highest metal content (lowest specific gravity) Result oPERATIoN The metal is fed onto the narrow side of a flat porous deck, sloped in two directions, and vibrated with a straight line reciprocating motionDry Separations for the Processing Industry Triple/S DynamicsAs a result of extensive RD in this area, the slagprocessing technologies are slowly converging around dry granulation combined with heat recovery In this paper, Process flow diagram of a dry slag granulation system with heat
.jpg)
Dry slag granulation with energy recovery: Pilot ResearchGate
2015年5月1日 In 2013, Paul Wurth developed a sphere injection system for slag processing [170] with a fullscale pilot plant implemented at ROGESA [172] (Fig 34)PROCESSES FOR THE DRY PROCESSING OF STEEL SLAGS WITH LOESCHE MILLS FOR METAL RECOVERY AND PRODUCTION OF SILICATE COMPOSITE MATERIAL FOR USE IN THE BUILDING MATERIALS INDUSTRY DrIng Holger Wulfert, Loesche GmbH DrIng Andreas Schiffers, CALA Aufbereitungstechnik GmbH Co KG Prof DrIng Andreas PROCESSES FOR THE DRY PROCESSING OF STEEL SLAGS WITH 2022年6月1日 In order to analyze the effect of mechanical activation on the carbonation conversion of steel slag sample compacts, the steel slag before and after mechanical activation was prepared as mixtures with 15:10 and 1:10 of watersolid ratio, compression moulded under 9 MPa, and carbonation was cured at 20 °C, 70% of relative humidity and 002 MPa of CO 2 Mechanical activation of medium basicity steel slag under dry Models for wet processing Finer material is in almost all applications preferably processed in water Also, for the wet processing there are a number of models to choose from to suit the various requirements The concurrent, CC, and counterrotation, CR, models are mostly selected for processing of ore at the feed end of the concentration circuitFor dry and wet processing Low Intensity Magnetic Separators
.jpg)
(PDF) Dry slag granulation of modified BOF slag
2014年4月15日 PDF Molten slag is the byproduct in the steel making process which is hot and full of energy, but the energy is now totally wasted due to lack of Find, read and cite all the research you 2021年4月27日 Dehydrated slag cement fines can be rehydrated, reforming phases similar to that formed during pure hydration of clinker cement (calcium silicate hydrates, portlandite, and so on), but also other Dehydration of portland cement and slag blended cement produced during BF slag treatment, which needed to be further researched Keywords: Dry slag granulation technology, Activation energy of crystallization, Cooling speed, Process and equipment 1 Introduction Usually a large amount of blast furnace (BF) slag is produced every year and most of them is treated with water in ChinaProcess and Equipment Design for the Dry Slag Granulation 2021年6月24日 Slags are valuable byproducts of iron and steelmaking processes Their efficient reutilization and the recuperation of their thermal energy are key for improving the overall efficiency of these processes With the innovative approach presented in this work, it is possible to recover thermal heat from liquid slags The process concept consists of a slag tundish and Process Concept for the Dry Recovery of Thermal Energy of Liquid

Economic and environmental evaluation of slag dry granulation
2012年6月10日 Fuel savings of the order of POUND 2m/year could be achieved processing half the slag from a large blast furnace of capacity 10,000 t d** minus **1 of iron which is operating with about 7700 t d Hatch helped Northam Platinum Limited achieve the firstever dry slag granulation system for a platinum smelter Who We Are + What We Do + Insights + Solutions + Careers Northam Converter Dry waterfree processing, reduced cost, lower maintenance, potential for heat recovery, decoupling of primary and secondary processes, Northam Converter Dry Slag Granulation Hatch Ltd2019年2月5日 A New Look at Slag Grinding 4 th Global Slag Conference 1011 November 2008, Strasbourg, France COMFLEX ® Highly efficient and flexible comminution system 16 th ArabInternational Cement Case Study of Dry HPGR Grinding and Classification in Ore Processing2016年7月28日 Steelmaking slag fines are leftover materials generated in routine slag processing and their particle sizes are usually smaller than 125 mm The steelmaking slag fines can include Enhancement of Iron Recovery from Steelmaking Slag Fines by