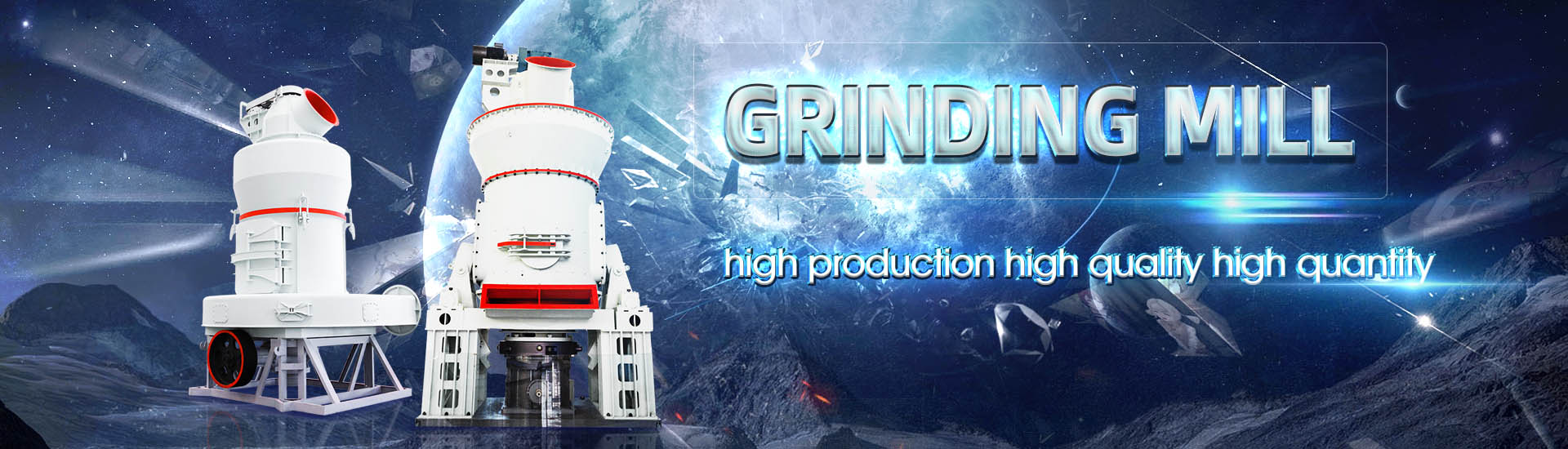
Cement burning equipment process flow chart
.jpg)
Flow chart of cement clinker burning system ResearchGate
cement clinker burning process starts from raw material entering the preheater and ends at the grate cooler after the calcined clinker is rapidly cooled The main equipmentProcess flow diagram for the cement manufacturing process, showing Process flow diagram for the The Cement Plant Operations Handbook is a concise, practical guide to cement manufacturing and is the standard reference used by plant operations personnel worldwide Providing a The Cement Plant Operations Handbook International Cement This document is the seventh edition of "The Cement Plant Operations Handbook", which provides a comprehensive guide to the entire cement production process It covers topics such as raw materials, burning, grinding, Seventh Edition Cement Hand Book PDF Cement

Stages in cement production flow chart [43] ResearchGate
The processing includes proper burning and grinding of the materials under carefully controlled conditions to form the amorphous form of silica which is important to their pozzolanic activityProcess flow diagram for the cement manufacturing process, showing electricity and heat consumption or inputs [39] The paper presented herein investigates the effects ofProcess flow diagram for the cement manufacturing Clinker burning process Clinker production is the most energyintensive stage in cement production, accounting for over 90% of total industry energy use Clinker is produced by pyroprocessing in kilnsCement Manufacturing Process INFINITY FOR Cement making process – Raw materials, clinker, cement • Cement Chemist’ LanguageCement Manufacturing
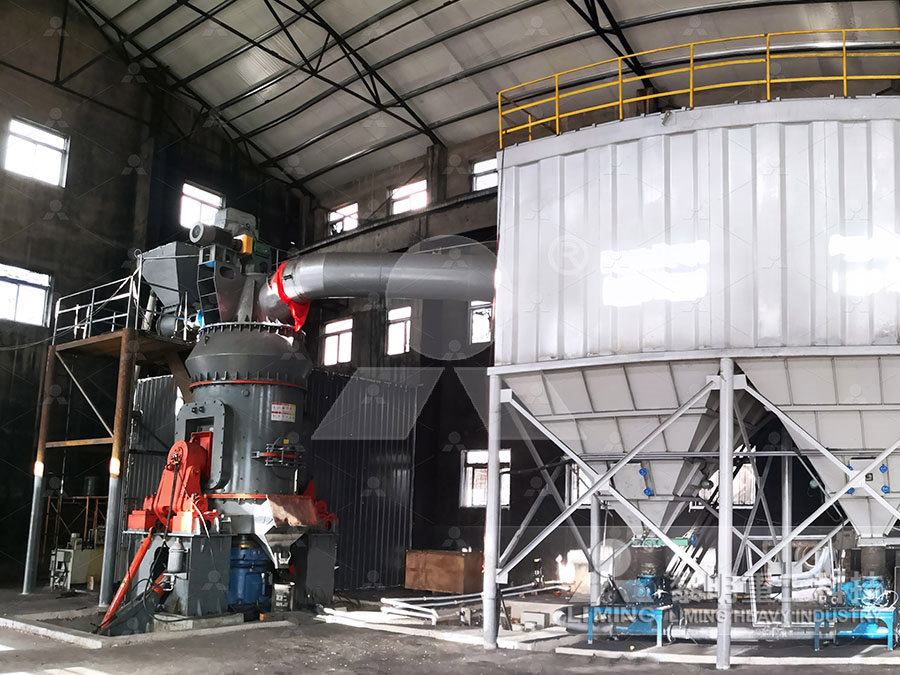
Process characteristics of clinker and cement production SINTEF
New ratebased model was developed and used to validate fullscale CAP simulations for cement plants Upcoming work: CAP optimization CEMCAP framework document: ready for use! To design the Refractory for the lining of different equipments in a cement plant, it is necessary to understand the total operational process of a cement plant in depth It is necessary to know Chapter 4 Cement Manufacturing and Process ControlBurning: In this operation, the slurry is directly fed into a long inclined steel cylinder called a Rotary kiln In this kiln there are 3 different zones shown in fig below Cement Manufacturing Process Flow Chart (i) Drying Zones: In the Manufacturing of Cement By Dry and Wet ProcessAs Clinkerization process is an endothermic (heat absorbing) process it requires burning of Suitable fuel Remember almost 40 % of the total cost spent for manufacturing cement is for fuel and power The specific heat consumption of Cement Manufacturing Process INFINITY FOR
.jpg)
Cement Manufacturing Process: Know Extraction,
2024年9月10日 Steps of Cement Manufacturing The steps involved in cement manufacturing are as follows: Quarrying: Raw materials such as limestone and clay are extracted from quarries or mines; Crushing and Grinding: The 4 天之前 The manufacture of Portland cement is a complex process and done in the following steps: grinding the raw materials, mixing them in certain proportions depending upon their purity and composition, and burning them to sintering in Manufacturing of Portland Cement – Process and Burning: In this operation, the slurry is directly fed into a long inclined steel cylinder called a Rotary kilnIn this kiln there are 3 different zones shown in fig below Cement Manufacturing Process Flow Chart (i) Drying Zones: In the wet process, the drying zone is comparatively larger than the dry process It is because the raw material in slurry form is directly fed into the kiln Manufacturing of Cement By Dry and Wet Process Expert Civiltesting – 11 Process control analysis – 12 Chromate passivation – 13 Cement quality – 14 Setting time – 15 ASTM cement types and specifications – 16 European EN 197 cement specification – 17 Composite cements (intergrinds and blends) – 18 Supersulphated cement – 19 Calcium aluminate cement (CAC) – 20 Shrinkage The Cement Plant Operations Handbook International Cement

Process flow diagram for the cement manufacturing process,
Download scientific diagram Process flow diagram for the cement manufacturing process, showing electricity and heat consumption or inputs [39] from publication: Energy Savings Associated with 2020年9月26日 Cement Manufacturing Process Cement Manufacturing Process Cement Manufacturing Process Cement is a material which is used to bind other materials together Binding means it has an effect of gluing the substances together due to cohesive and adhesive action and then hardens and sets in order to become permanentCement Manufacturing Process Chemical Engineering WorldCement making process – Raw materials, clinker, cement • Cement Chemist’ LanguageCement Manufacturing2018年8月28日 After explaining the complete process of cement making, flow chart would be like that flow chart present the summary of whole process as shown below Cement making process flow chart More from my site What You Need To Know About Concrete; Types and Applications of Fly Ash in Construction;Cement Manufacturing Process The Engineering Community
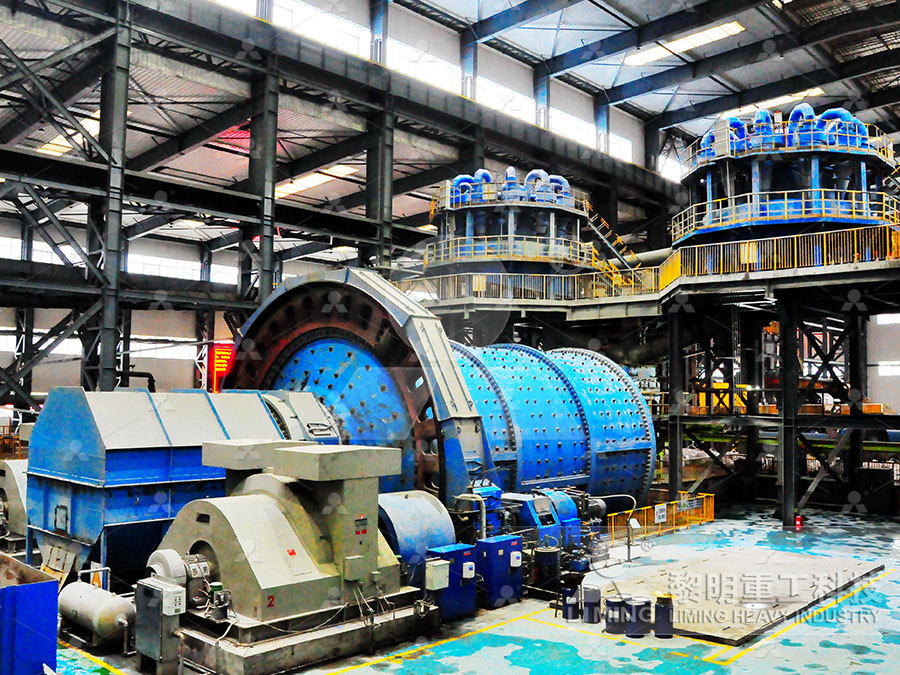
Manufacture Of Portland Cement Process Flow chart civil
2019年11月30日 Manufacture Of Portland Cement Process Flow chart – civil learners July 23, 2021 November 30, 2019 by Maruthi Baddi Burning is carried out in a rotary Kiln which is rotating at 12 rpm at its longitudinal axis rotary kiln is steel tubes having diameters in between 2530 meters and length varies from 90120 bustion and the Cement Process Pyroprocessing is the heart of the cementmaking process It is usually the major cost element and kiln performance dictates the efficiency, plant output, emissions, product quality, and plant run Everything you need to know about Kiln Burning The cement manufacturing process starts from the mining of raw materials that are used in cement manufacturing, mainly limestone and clays A limestone quarry is inside the plant area and a clays quarry is as far from the plant area Manufacturing process LafargeCement Manufacturing and Process Control 41 Cement Manufacturing: Basic Process and Operation To design the Refractory for the lining of different equipments in a cement plant, it is necessary to understand the total operational process of a cement plant in depth It is necessary to know the conditions prevailing in different equipments and theChapter 4 Cement Manufacturing and Process Control
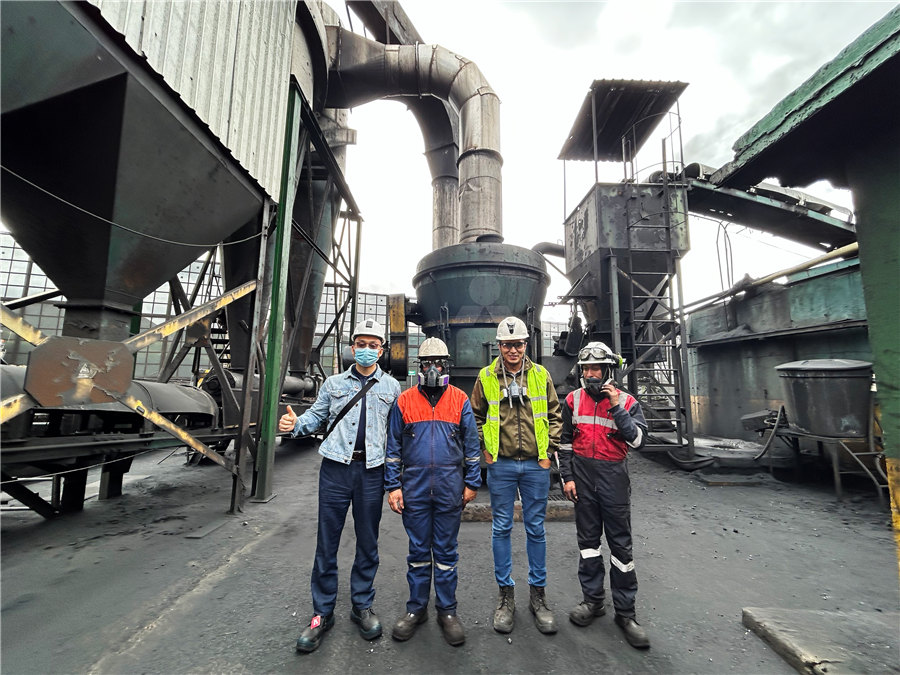
CEMENT MANUFACTURING PROCESS ! TYPES OF CEMENT, FLOW CHART
2024年5月14日 Cement manufacturing process is a reliable bonding material It is obtained by burning calcareous material (lime) and argillaceous material (clay) and then grinding, types of cement The cement manufacturing process was first produced by Joseph Aspidin, a mason from England As its color resembled a variety of sandstone found in Portland, he named it Portland Without recirculation the mixing of secondary air and fuel is inadequate and reducing burning conditions and CO can be present at 4~5% oxygen at the kiln inlet Production of clinker in a reducing atmosphere in a cement kiln can seriously degrade the quality of clinker and the cement produced from the clinkerCement Kiln Process Chemistry CombustionThe cement production process 1 The Quarry: The cement production process begins with the extraction of limestone and clay from the quarry 2 Crusher and PreBlending: The material is then crushed to reduce particle sizes and blended to reduce variability in composition 3 Raw Mill and Kiln: Raw materials and additives areA practical guide to improving cement manufacturing processes 1Cement Manufacturer’s Handbook Book by Kurt E Peray This unique handbook contains the most essential engineering formulas used in the cement manufacturing process All formulas are presented in both English and metric systems of units Examples are given to familiarize the reader with the usefulness of these formulasINFINITY FOR CEMENT EQUIPMENT
.jpg)
PROCESS INSTRUMENTATION ANALYTICS Cement
• Accurate control of the burning process to minimize fuel consumption Cement Siemens has extensive and indepth experience of the cement industry’s needs Our process instrumentation and analytics portfolio gives you the precision, integration and automation you need to deliver the best production efficiency,CEMENT PRODUCTION AND QUALITY CONTROL A Cement manufacturing Process Source:civilengineeringforumme The whole process of cement manufacturing in Messebo Cement plant which consists of two separate Cement Production lines can be summarized into the following processes ;as can be seen in the process and Quality flow diagram below; 1CEMENT PRODUCTION AND QUALITY CONTROL A Cement manufacturing Process2020年8月25日 Cement equipment refers to all equipment in the cement plant, such as cement mill, cement crusher, cement kiln, cement silo, cement preheater, etc Today we will focus on the cement production process analytics What is Cement Production Process Cement Manufacturing 2021年3月9日 In this study the process flow diagram for the cement production was simulated using Aspen HYSYS 88 software to achieve high energy optimization and optimum cement flow rate by varying the flow rate of calcium Simulation and Optimization of an Integrated Process
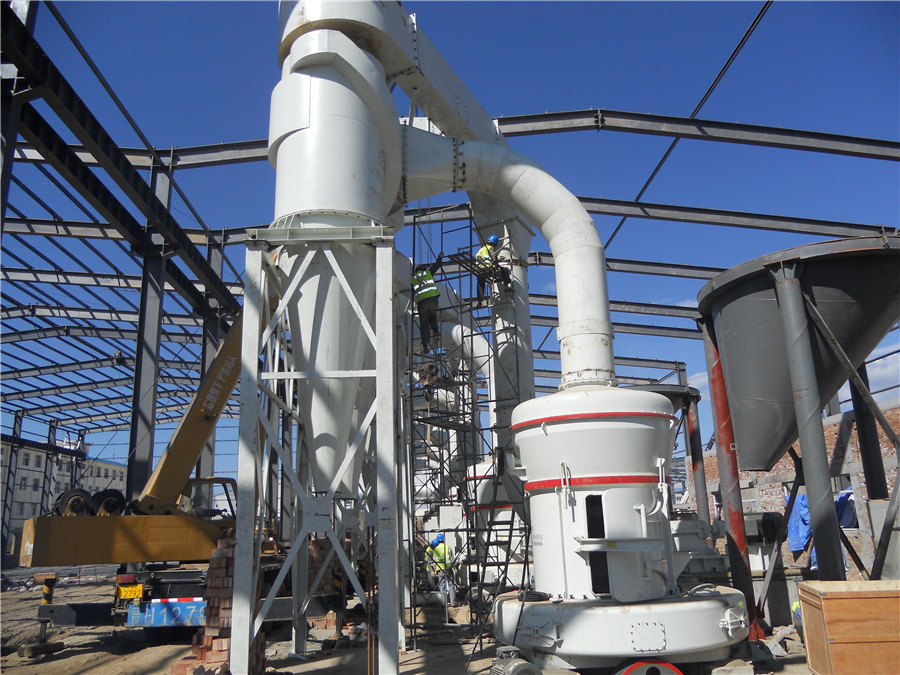
Cement Production Process PPT SlideShare
2015年9月17日 6 00 Limestone Quarry and Crushing plant The major raw material for cement production is limestone The limestone most suitable for cement production must have some ingredients in specified quantities ie, 1971年8月17日 116 Portland Cement Manufacturing 1161 Process Description17 Portland cement is a fine powder, gray or white in color, that consists of a mixture of hydraulic cement materials comprising primarily calcium silicates, aluminates and aluminoferrites More than 30 raw materials are known to be used in the manufacture of portland cement, and these116 Portland Cement Manufacturing US EPAIn the cement produciton line,it contains 8 parts:raw materials,raw material preparation,crushing and prehomogenization,raw material homogenization,preheater and calciner,the burning of concrete clinker,grinding and concrete packging 4What is the main equipments in the cement production line? Rotary kiln is the main equipment for cement plantSupply Cement Production Line Process Flow Chart and MachineAn English bricklayer made the first portland cement early in the 19th century by burning powdered limestone and clay on his kitchen stove With this crude method, Joseph Aspdin of Leeds laid the foundation for an industry that annually processes literally mountains of limestone, clay, cement rock, and other materials into a powder so fine, it will pass through a sieveHow Cement is Made Portland Cement Association
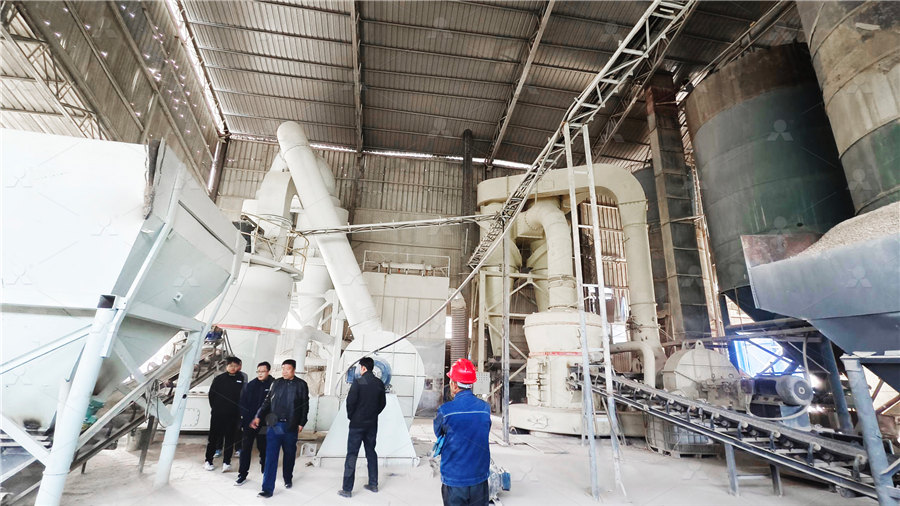
PPT Engineering Materials Cement PowerPoint Presentation, free
2019年10月23日 Engineering Materials Cement Contents • Introduction • Classification of cements • Portland Cement • Raw materials of Portland cement • Cement Manufacturing Process • Flow chart of Portland Cement manufacturing process • Cement Manufacturing Video • Mixing and Crushing • Dry Process • Wet Process • Burning Process • View of complete setup • 2013年8月30日 After 1982 all the cement manufacturing plants in India are equipped with the technologies of Dry process, since this is more energy efficient and environment friendly method of cement manufacturing In this post I am sharing with you the flow diagram of the wet process of the mixing because it is in the syllabus of the many Diploma coursesWet process Cement manufacturing Flow Diagram2013年5月11日 Categories Civil Engineering Articles, Civil Engineering Articles for Mobile, Concrete Technology, PowerPoint Presentations Tags acc cement, cement, cement concrete, cement in concrete, cement manufacture, cement manufacture process, cement manufacturers, cement manufacturers in india, Cement Manufacturing, cement manufacturing process, Cement Manufacturing Process Simplified Flow ChartCement production process , each producing one ton of Portland cement grinding at least 3 tons of materials ( including raw materials , fuel, clinker , mixed materials , gypsum ) , according to statistics , the dry process cement production line grinding operations need to consume power accounts for over 60% of the whole power plant , where raw material grinding accounted for Flow Chart Of Cement Industry { Dry Process } Blogger
.jpg)
FLOWCHART OF PROCESS USED IN MANUFACTURING OF CEMENT
In recent years, Zimbabwe has experienced an increase in high energy demand and this brings the use of coal in generating electricity Coal fired power plants produces waste products during the coal burning process which are known as coal combustion residuals which includes 3% boiler slag, 24% flue gas desulphurization material, 57% fly ash and 16% pulverized coal ashPrevious Post Contents1 EVERYTHING YOU NEED TO KNOW ABOUT KILN OPERATING AND CONTROL METHODS11 CLINKERBURNING TECHNIQUES111 Protection of Equipment and Safe operation 112 EVERYTHING YOU NEED TO KNOW ABOUT KILN Cement production has undergone a tremendous development from its beginnings some 2000 years ago While the use of cement in concrete has a very long history, the industrial production of cements started in the middle of the 19th century, first with shaft kilns, which were later on replaced by rotary kilns as standard equipment worldwideCement Production an overview ScienceDirect TopicsINFINITY FOR CEMENT EQUIPMENT Main Menu Home Page; Contact US; ATTENTION ATTENTION !!!! The clinker burning process itself is performed in a relatively small rotary kiln with an appropriate retention Fig 2046 shows a flowchart of a preheater working in conjunction with a KSVprecalciner with tempera ture data of the most Suspension preheaters with precalciner INFINITY FOR CEMENT EQUIPMENT
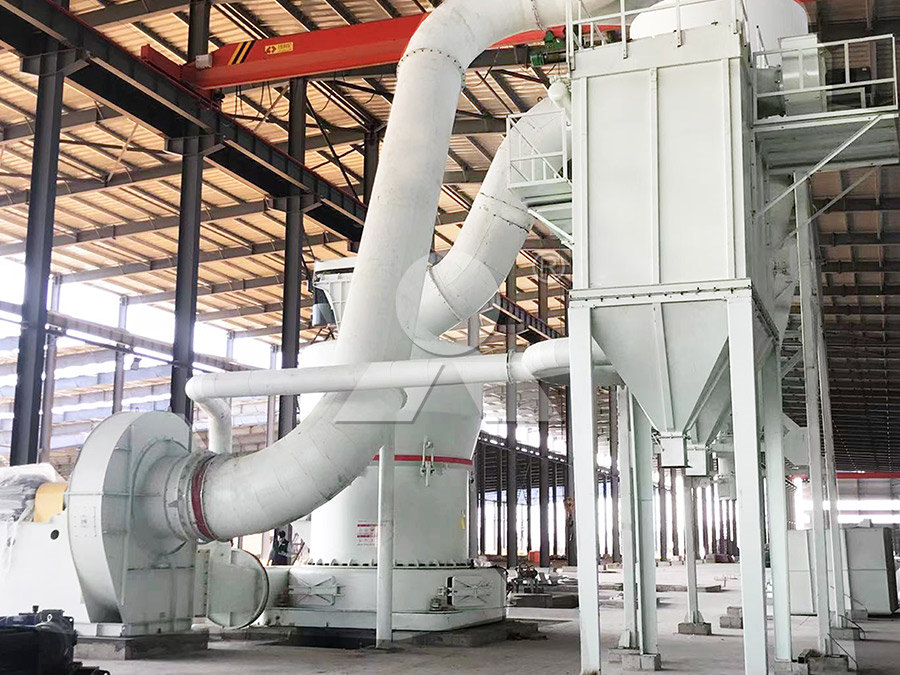
Dry process of cement – we civil engineers
2018年8月24日 Dry process These are two different processes of manufacturing cement wet process minerals are wet ground (by adding water) to form a slurry and then dried, dry process minerals are dry ground to form a powder like substanceBoth the processes are in use and have their own advantages and disadvantagesWhile in wet process grinding is easier,in dry 2018年2月27日 2 Contents • Introduction • Classification of cements • Portland Cement • Raw materials of Portland cement • Cement Manufacturing Process • Flow chart of Portland Cement manufacturing process • Cement Manufacturing Video • Mixing and Crushing • Dry Process • Wet Process • Burning Process • View of complete setup • Rotary Klin zones • Chemical Reactions Manufacture of cement Classification and hydration PPTcement plants with wet process kilns is 305006, and the sixdigit SCC for plants with dry process kilns Process flow diagram for portland cement manufacturing 1164 EMISSION FACTORS 11/21 Table 1161 4 Reaction, of the oxides in the burning zone of the rotary kiln, to form cement clinker at116 Portland Cement Manufacturing US Environmental 2021年3月3日 Cement is produced by a hightemperature (about 1500 °C) reaction in a rotary kiln of carefully proportioned and blended ratios of lime (CaO), silica (SiO 2), alumina (Al 2 O 3), and iron oxide (Fe 2 O 3)The production of cement is a chemical process requiring an accurate blend of the previously cited four key organic oxides and the limitation of several undesirable Cement SpringerLink
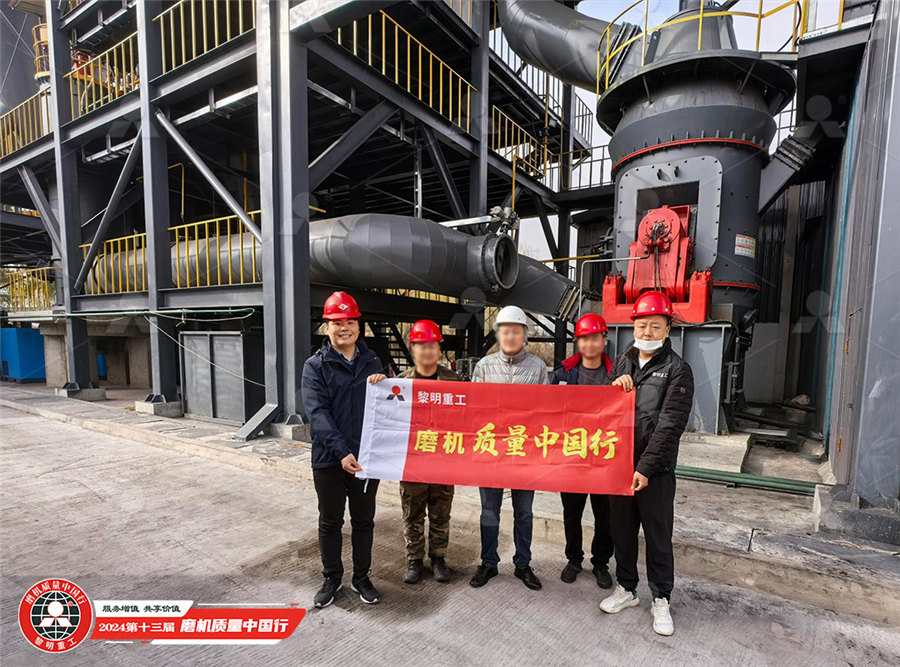
Manufacturing process flow 1 Quarrying and Crushing Messebo Cement
This mill at this time produces two types of cement namely Ordinary Portland Cement (OPC) and Pozzolana Portland Cement (PPC) OPC comprises 90%clinker, 5%additive (limestone) and 5 %( gypsum) PPC comprises 70% of clinker, 2529%% pozzolana and 5%gypsum The design capacity of the mill is 120t/h for OPC cement But currentlychemical process flow software known as DWSIM An analysis of this heat recovery model shows an increase of 1966% in the energy efficiency of the manufacturing processDesign and Simulation of a Waste Heat Recovery System for a Cement