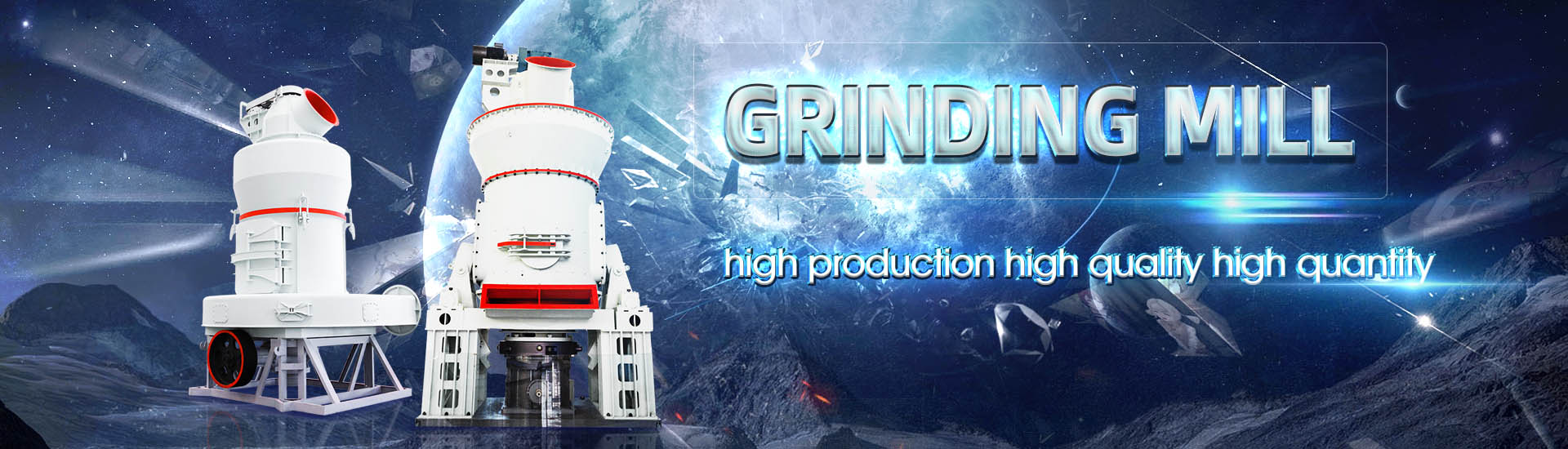
Coking coal powder making process
.jpg)
Industrial perspective of the cokemaking technologies
2019年1月1日 It is well known that the three factors which control coke strength are (1) selection of coals for coal blend, (2) adopted cokemaking technology, and (3) operating parameters 2021年12月8日 Obtaining a petroleum coking additive as a partial replacement for coking coals (for obtaining a charge in the metallurgical coke production) can be performed in delayed Technology of Producing Petroleum Coking Additives to Replace 2021年10月1日 The coking process involves mixing predetermined proportions of coking coals with different caking properties, followed by charging of the blended coal into an oven In the Effect of preheating on coking coal and metallurgical coke 2022年8月5日 Delayed coking units for processing vacuum residues are designed to operate under operating conditions that maximise liquid distillates yield and minimise coke production(PDF) Coking ResearchGate
.jpg)
Coke Making: Most Efficient Technologies for Greenhouse
2019年7月19日 Coke making is the fundamental process related to the traditional blast furnace route Coke provides the reducing actions, increases temperature through its thermal energy, 2024年1月14日 A mathematical model of the coking process in the coking chamber was constructed based on the distributed activation energy model The heat transfer process of the Heat and mass transfer analysis of coal coking process in the 2024年1月1日 Coking (coking chemistry) process is the production and energy conversion process of converting primary energy coking coal into secondary energy resources (coke, Energy Utilization in Coking Process SpringerLink%PDF16 %âãÏÓ 133 0 obj > endobj xref 133 96 00000 n 00000 n 00000 n 00000 n 00000 n 00000 n 00000 n 00000 n 00000 n 00000 n 00000 n 00000 n 00000 n 00000 n 122 Coke Production US Environmental Protection Agency
.jpg)
Study on Relationships between Coal Microstructure
2023年2月28日 The coking industry is an important basic energy and raw material industry, which connects coal, coke and steel industries and plays an important role in the industrial chain, economic construction, social 2023年1月5日 Metallurgical coal (also called "met" coal) is an important raw material used in the steelmaking process, although very small amounts of coal (relative to the amount used for electricity) are needed The coal used to make Coal to Make Coke and Steel University of Kentucky2019年1月1日 Coking coal is regarded as premium quality coal that attracts relatively higher cost and there are concerns over the limited reserves (Chukwuleke, Iiuju and Chukwujekwu, 2009) The use of coal in reduction of iron ore is associated with pollution and greenhouse gas emissions, particularly CO2 (Yilmaz and Turek, 2017)A review of ironmaking by direct reduction processes: Quality 2017年2月22日 Corex Process for Production of Iron satyendra; February 22, 2017; 1 Comment ; Corex gas, Corex process, Dome, DRI, export gas, Hot metal, Iron ore lump, MelterGasifier, non coking coal, pellets, Reduction furnace,; Corex Process for Production of Iron During the late twentieth century, several new initiatives have been taken for the development of the smelting Corex Process for Production of Iron – IspatGuru
.jpg)
Coking Coal IspatGuru
Fig 1 Types of coal and their uses The term ‘coking coal’ is used to designate certain types of bituminous coals which, when heated at high temperatures (over 1,000 deg C) in the absence of air (carbonization), soften, liquefy, and then resolidify into a hard but porous mass known as coke, used mainly in the production of hot metal in a blast furnace2016年6月22日 Quality of coal In either coke or noncoked coal, the quality of the coal affects the quality of the steel Metallurgical coke is made from bituminous coals by a distillation process Ash deposited by the coal must be kept to a minimum, preferably below 10% of the original massHow does coke and coal play into steel making?2023年2月28日 The curvefitted FTIR spectrum (3700 cm −1 −3000 cm −1 : hydrogen bonding area, 900 cm −1 −700 cm −1 : aromatic bending, 3000 cm −1 −2815 cm −1 : aliphatic and aromatic stretching)(PDF) Study on Relationships between Coal Microstructure and 2019年1月1日 This chapter explains the technological principles behind semisoft coking coal utilization from the viewpoint of the mechanism of carbonization and reviews the development and commercialization of technologies, such as briquette blending carbonization process, coal moisture control, drycleaned and agglomerated precompaction system, formed coke The development of cokemaking technology based on the
.jpg)
Coking behavior and mechanism of direct coal liquefaction residue in
2020年11月15日 1 Introduction Direct coal liquefaction is a promising approach for producing clean liquid fuels and valuable chemicals Noticeably, direct coal liquefaction residue (DCLR) is the main byproducts which accounts over 30 wt% of raw coal [1], [2], [3], [4]One key problem in direct coal liquefaction process is the solidliquid separation methods of hydroliquefaction Process flow sheet: Illustrated in Figure Figure 321 Flow sheet of coking of coal 323 Functional role of each unit (Figure 321): (a) Coal crusher and screening: At first Bituminous coal is crushed and screened to a certain size Preheating of coal (at 150250˚C) is done to reduce coking time without loss of coal qualityLecture 32: Coke production National Institute of Technology, Briquette coal with binder and then coking Onestep process without binder Briquette coal with binderless way then coking The above four lignite coal coking process technologies, only the fourth method – the onestep process without Industrial coal coke briquette making process, 2021年1月20日 Therefore, the idea that utilization byproducts/waste for AC production came up (Fig 2), using byproducts and wastes such as coke powder, coal tar pitch, benzene residue, etc from cokemaking as raw materials for AC production which further treat wastewater and flue gas from cokemaking The process not only could utilize the cokemaking by Recirculating coking byproducts and waste for costeffective
.jpg)
Development and Problems of Fluidized Bed Ironmaking Process:
2023年10月9日 At the same time, the increasing dependence on highquality iron ore and the depletion of coking coal resources are also the limiting conditions for the continuous production of BF ironmaking [1, 2] In the traditional BF ironmaking process, sintering and coking are production processes that are extremely polluting to the environment2014年6月26日 Maximization of noncoking coal in coal blend is eloquent interest among researchers incoke making throughout the world To maximize the noncoking coals in coal blend with thescarce and expensive coking coals is an essential practice in the iron and steel industryThe fundamental aspect of the coal blending theory of low value coals to produce Efficient way to use of noncoking coals in nonrecovery cokemaking processMetallurgical coke is produced from lowash, lowsulfur coking coals in the coking process involving devolatilization and carbonization at ~ 1000–1100°C in airless ovens over 18–20 h Volatile hydrocarbon byproducts are later used to generate energy in Metallurgical Coke an overview ScienceDirect Topics2024年7月10日 What is coke fine Coke fine refers to the smallsized particles or fine granules of coke, a carbonrich material derived from coal or petroleum These fine particles are typically produced as a byproduct during the crushing, screening, and handling of larger coke pieces Coke fine sources types of them At present, coke fines primarily come from the following two Coke briquette making and the binders MAXTON
.jpg)
What Is Coking? What Happens to the Coal? Cadence
2024年8月20日 Below is an overview of what happens to the coal during the coking process 1 Metallurgical Coal Sourced and Prepared Metallurgical coal — as opposed to thermal coal, a type of coal which is used for generating electricity — contains high concentrations of carbon, which is critical to the coking process Manufacturing companies source 2016年3月30日 In book: Encyclopedia of Iron, Steel, and Their Alloys (pppp 10821108) Chapter: i) Direct Reduced Iron: Production; Publisher: CRC Press, Taylor and Francis Group, New York(PDF) i) Direct Reduced Iron: Production ResearchGate2024年1月1日 The blends of multiple coals with distinct properties were heated to temperature exceeding 1100 °C in coke oven in order to produce metallurgical coke [1], during which a multitude of chemical reactions took place [2], [3], [4]The evolution of coking properties was contingent upon the coal structure transformation during carbonization, as previously A preliminary study on the quality evaluation of coking coal from Indian lowrank coking coal (semicoking coal) with the blending of highrank imported coals and to reduce the overall cost of coke making The blending of the coals has been done in two phases Effect of blending mass ratio on the swelling index and plasticity parameters has been studied The effect of maceral content, vitrinite reflectance Caking Ability Tests for Coal Blends in Process to Utilize the Indian
.jpg)
122 Coke Production
sulfide, ammonia, and nitrogen Liquid products include water, tar, and crude light oil The coking process produces approximately 338,000 L of coke oven gas (COG) per megagram of coal charged (10,800 standard cubic feet of COG per ton) During the coking cycle, volatile matter driven from the coal mass passes upward through cast2014年6月26日 Maximization of noncoking coal in coal blend is eloquent interest among researchers incoke making throughout the world To maximize the noncoking coals in coal blend with thescarce and expensive coking coals is an essential practice in the iron and steel industryThe fundamental aspect of the coal blending theory of low value coals to produce Efficient way to use of noncoking coals in nonrecovery cokemaking processProcesses 2023, 11, 724 2 of 16 and carboxyl groups break down and release gases such as carbon dioxide and water in the temperature range of 200–400 C Secondly, depolymerization reactions Quality during Coking Process ResearchGate2024年3月19日 Abstract The hot strength and mechanical strength of metallurgical coke are the critical parameters for efficient blast furnace operation Therefore, producing the desired qualities of coke like coke strength after reaction, coke reactivity index, and coke M10/M40 is essential for optimizing the cost and productivity of hot metal Hence, the intrinsic property of coal is LowCost Ironmaking: Metallurgical Coal Prospective
.jpg)
The Role of Coke in Steel Making Process Cabaro Group
2024年3月25日 Fundamental to this process is the production of steel making process coke, a refined carbonrich product derived from coal While contemporary methods evolve, coking remains pivotal for its role in fueling and purifying the raw materials Coke serves multiple purposes in steel manufacture, particularly in the traditional blast furnace methodCoking coal is an essential part of the steel manufacturing process It forms the foundation for the manufacture of highgrade steel products Coking coal is one of the most important components of steelmaking When it comes to producing highquality coking coal for steelmakers around the world, no one can do it as well as we doCharacteristics of Coking Coal in South Africa National CoalRaw coke Eighteenthcentury coke blast furnaces in Shropshire, England Metallurgical coal or coking coal [1] is a grade of coal that can be used to produce goodquality cokeCoke is an essential fuel and reactant in the blast furnace process for primary steelmaking [2] [3] [4] The demand for metallurgical coal is highly coupled to the demand for steelMetallurgical coal Wikipedia2014年6月26日 In the form of coke, it provides physical support for the ferrous materials (burden) in the blast furnace, as well as providing a source of heat and the reducing environment necessary for the Efficient way to use of noncoking coals in nonrecovery coke making
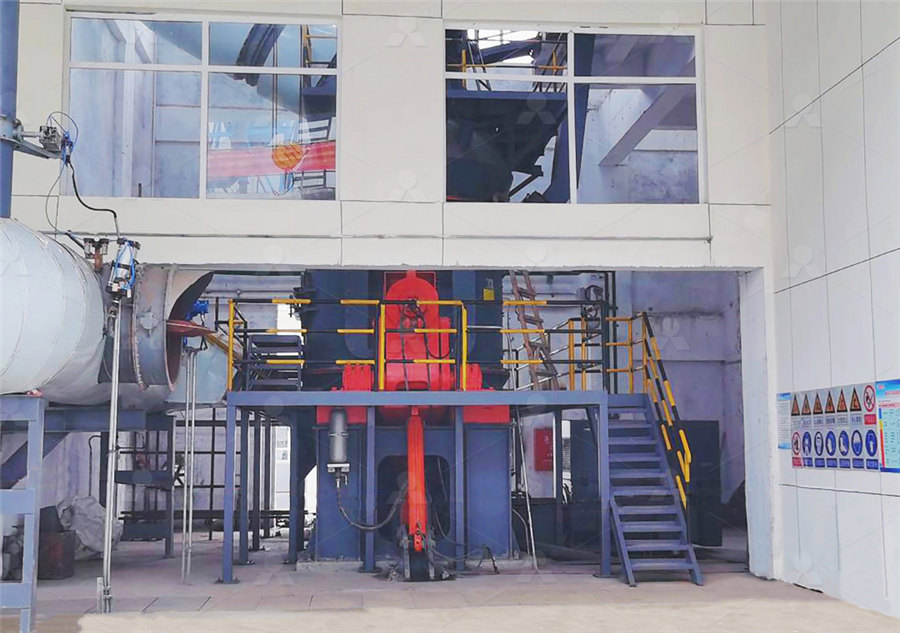
Effect of Particle Size Distribution and Degree of Saturation on Coal
2015年7月1日 Cokemaking technology utilises two systems for charging the coke oven chambers with coal—a stampcharged system (stampcharging) and a gravity charged system (top charging)All coals, regardless of whether they are caking or coking coals, leave a solid carbonaceous residue at the end of the carbonization process Chars, if heattreated to extreme temperatures, eg ≥2500 °C, Chapter 4 treats coke 23 Carbonization and coking of coal Cambridge 2021年10月1日 The moisture content of the charged coal is also a very important factor Controlling and maintain a low moisture content can reduce heat consumption, shorten the coking time, and lower waste water production [12, 15, 18, 19]More importantly, the more moisture in coal, the lower its caking ability [8, 20, 21]During the heating process of wet coal in the coke Effect of preheating on coking coal and metallurgical coke 2024年5月22日 Lump charcoal, which is made by burning pieces of wood until all the impurities are gone and only the coal remains, is an excellent choice for outdoor grilling It's expensive to buy lump charcoal at the store, but making How to Make Charcoal (with Pictures) wikiHow
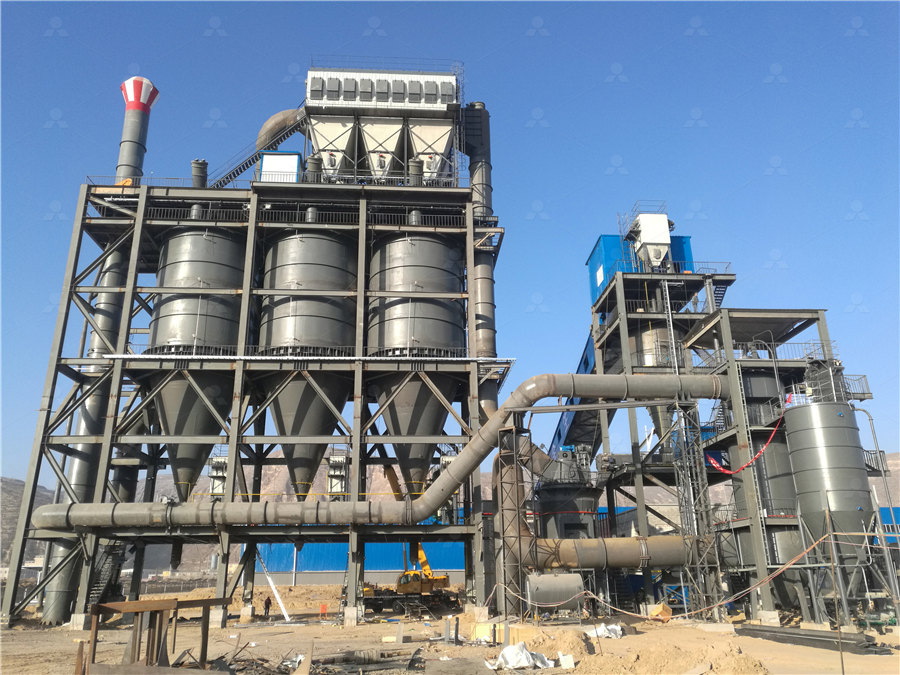
Coking coal: Impact assessment for supply security Europa
transformation in coke ovens of coking coal into coke for use in blast furnaces accounted for 89% of the EU's total coking coal consumption in 2020 (Figure 6) 95% of EU's consumption of coking coal is associated with the iron steel industry Byproducts of the coking process are used in several applications,2020年8月21日 Hard coking coals like anthracite have better coking properties than semisoft coking coals, allowing them to garner a higher price Australian HCC is regarded as the industry benchmark While PCI coal is not often classified as coking coal, it still is used as a source of energy in the steelmaking process and can partially replace coke in some blast furnacesWhat You Should Know About Metallurgical Coal ThoughtCo2022年8月23日 Since coking coal is scarce [2,3], noncoking coal and charcoal can be used as alternative energy sources for the direct reduction process involving an iron extraction route that does not require (PDF) An Overview of the ReductionSmelting Process of Iron 2021年1月20日 Therefore, the idea that utilization byproducts/waste for AC production came up (Fig 2), using byproducts and wastes such as coke powder, coal tar pitch, benzene residue, etc from cokemaking as raw materials for AC production which further treat wastewater and flue gas from cokemaking The process not only could utilize the cokemaking by Recirculating coking byproducts and waste for costeffective
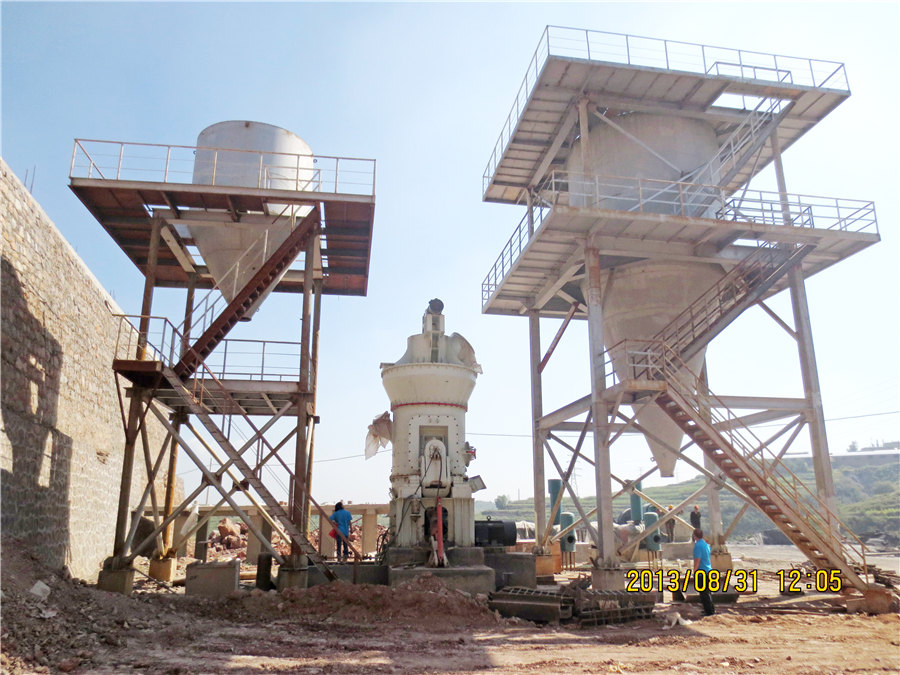
Smelting Reduction Processes SpringerLink
2020年3月3日 Direct use of noncoking coal, higher availability and lower costs than coking coal; 10% coke is often used to ensure hearth permeability, 3 Minimum coal consumption and high gas utilization, 4 After fluidized bed reduction, fine DRI is hot Coking is the process of heating coal in the absence of oxygen to a temperature above 600 °C (1,112 °F) to drive off the volatile components of the raw coal, leaving behind a hard, strong, porous material with a high carbon content called cokeCoke is predominantly carbon Its porous structure provides a high surface area, allowing it to burn more rapidly, much like how a Coking Wikipedia2023年4月5日 26 Iron ore reductionsmelting process using noncoking coals/charcoal as reductants The use of noncoking coal as an alternative energy source for sponge iron production instead of the conventional metallurgical coke cannot be overemphasized due to the problematic nature that is common to coke making processRecent Trends in the Technologies of the Direct Reduction and