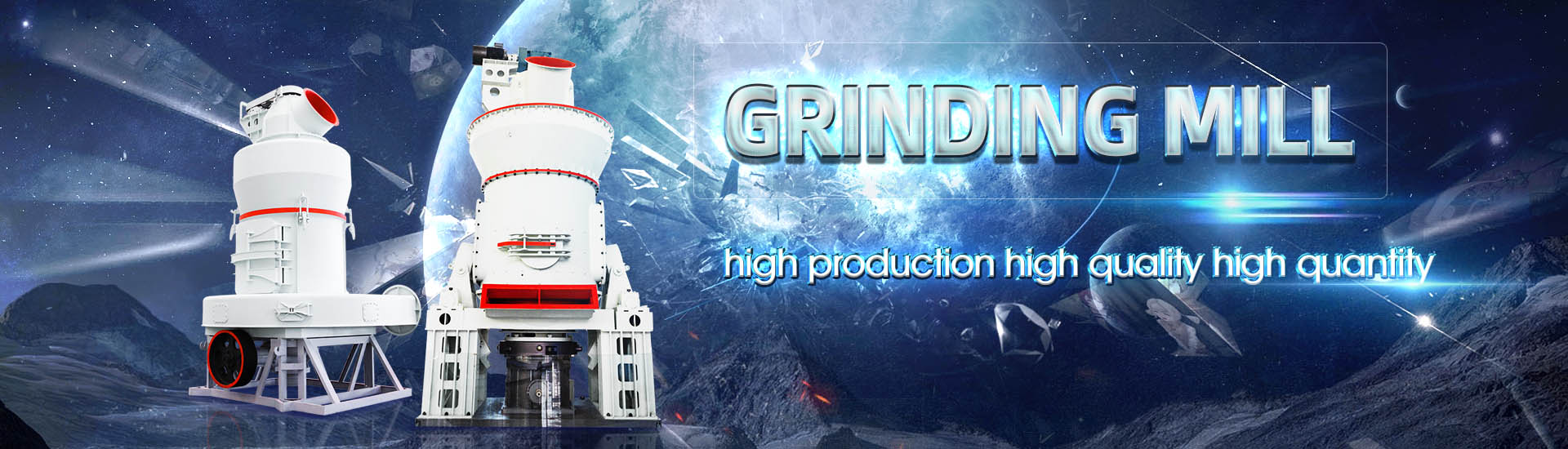
Low speed coal mill performance
.jpg)
A Comparison of Three Types of Coal Pulverizers Babcock Power
The BTM is a lowspeed mill that primarily grinds coal by impact and attrition The VRM is a medium speed mill that grinds coal by compression and, because of the low coal inventory in 2020年8月12日 To understand the performance of a vertical roller coal mill, the real operational tests have been performed considering three different coal sources Obtained results indicate thatAn investigation of performance characteristics and This paper tries to give the pulveriser mill specifications, functional, operational details and performance analysis at different operating loads Paper also mentions the measures for Pulveriser Mill Performance Analysis Optimisation in Super2011年8月1日 Three types of mills, according to speed, are available: lowspeed mills of ball/tube design; mediumspeed mills of vertical spindle design; and highspeed mills with a Mill Speed an overview ScienceDirect Topics
.jpg)
Technique to Investigate Pulverizing and Abrasive Performance of
2021年11月4日 This method enables facilitated testing procedures and a more exact simulation of grinding in vertical spindle coal mills Ballrace mills and Loesche roller mills were usedThe effect of low calorific value coal was observed on mill’s response to match the boiler energy requirements Evaluation of the current operating pulveriser data enabled the determination of Performance optimisation of vertical spindle coal pulverisersTwo types of mills generally used in power plants are low speed horizontal ball mill and medium speed vertical bowl mill While most plants have a bowl type mill, the ball type mill has a large Mathematical validation and comparison of ball tube and bowl 2020年8月12日 This study shows the performance of a currently running vertical roller coal mill (VRM) in an existing coalfired power plant In a power plant, the coal mill is the critical An investigation of performance characteristics and energetic
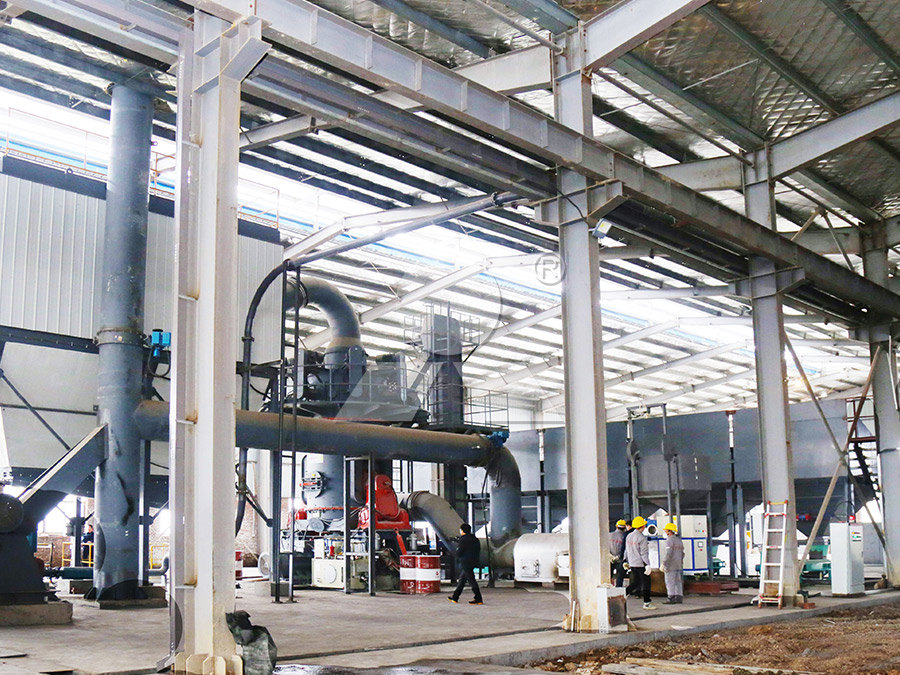
Classification performance of model coal mill classifiers with cip
Abstract: The classification performance of model coal mill classifiers with different bottom incoming flow inlets was experimentally and numerically studied The flow field adjacent to two A Study on 500 MW Coal Fired Boiler Unit’s Bowl Mill Performance through Coal Sampling 168 Vol 18(2) December 2022 cprijournal specified/optimum operating conditions are met This would help to evaluate the actual mill performance vis a vis specified operating conditions 211 Servicing of Journal AssemblyA Study on 500 MW Coal Fired Boiler Unit’s Bowl Mill Performance 2009年1月1日 Coarser particles also reduce burner stability at low load Air flow distribution at the mill throat, as well as inside the mill, significantly influences the mill performance in terms of CFD Modeling of MPS Coal Mill for Improved 2020年7月2日 A comprehensive investigation was conducted to delineate the effect of ball size distribution, mill speed, and their interactions on power draw, charge motion, and balls segregation in a (PDF) Effects of Ball Size Distribution and Mill Speed and Their
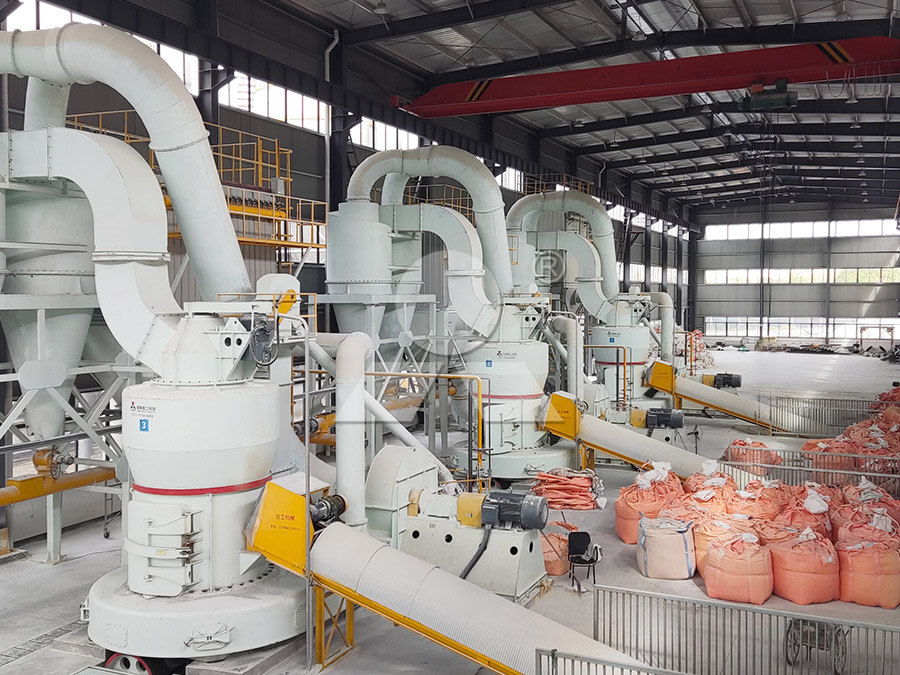
Review of control and fault diagnosis methods applied to coal
2015年8月1日 Schematic of mill control for (a) low speed mills and (b) medium speed mills The controls included are – (1) coal flow control, (2) Coal Pulverisers – Performance and Safety, IEA Coal Research, London, UK (1995), pp 5569 2020年6月29日 6 TYPES OF COAL PULVERIZER • Tube or ball mills: Lowspeed machines that grind the coal with steel balls in a rotating horizontal cylinder If the diameter of the cylinder is greater than the length of the cylinder, the mill is called a ball mill If the length of the cylinder is greater than the diameter of the cylinder, it is called a tube millclassifications and working of mills in a power plant PPTin the mining or coal processing operations Fig3 Mill fuel piping connections to furnace II COAL MILL SPECIFICATIONS PERFORMANCE ANALYSIS Typical Coal Pulveriser Mill Details in 660 MW SuperCritical [3] Unit is as given in table Table No 1 Table1 Coal mill Type Bowl Type Mediumspeed Coal mill Number of Mills 6set/ boilerPulveriser Mill Performance Analysis Optimisation in Super 2019年5月10日 • In pulverized coal combustion, the ratio of coal to carrying gas is usually in the range of y = 0506 kg/kg • Assuming a coal density rc = 15 x 103 kg/m3, and the density of the carrying gas as rg = 09 kg/m 3, the volume fraction of Monitoring Coal mill Performance PPT SlideShare
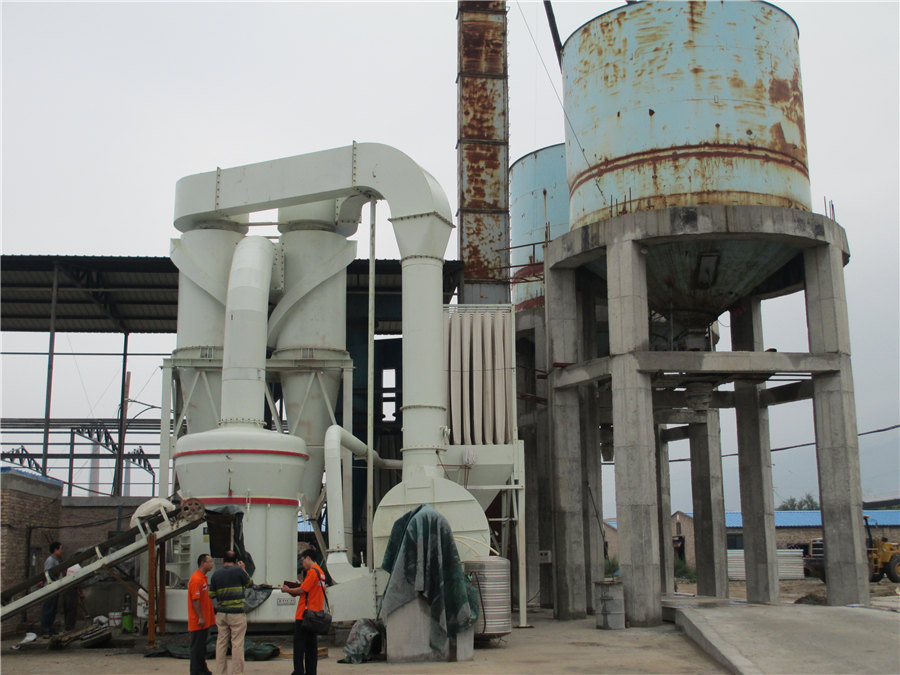
Effects of Mill Speed and Air Classifier Speed on Performance of
2021年6月29日 The aim of this work was to observe the impact of the milling technique employed by the DESI 11 disintegrator on the properties of fly ash This type of mill is a highspeed pin mill with two 2019年5月8日 Basic and detailed discussion on Coal Mill (Raymond) and Air Fans Performance in a 7075% for bituminous coal, and 8085% for anthracite • Heat input per burner is assumed to be to 75 MW for a low slagging coal and 40 MW for a system static pressure, fan speed, efficiency and brake horsepower required to drive the TPS Coal Mills and Fan Performance PPT SlideShareMonitoring and diagnosis of coal mill systems are critical to the security operation of power plants The traditional datadriven fault diagnosis methods often result in low fault recognition rate The structure of MPS mediumspeed coal mill systembeen actively developing mill system technology to achieve better coal fineness, increased capacity, greater reliability, and longer wear life The effort has improved the design of low, medium, and high speed pulverizers, all three of which are supplied by RPICOAL PULVERIZER DESIGN UPGRADES TO MEET THE DEMANDS OF LOW
.jpg)
Coal Mill in Thermal Power Plant: Enhancing Efficiency and
3 Precise Control and Automation: Bellian Machinery's coal mills feature advanced control systems that enable precise control over various operational parameters Operators can adjust grinding variables, such as coal flow and mill rotation speed, in realtime to achieve the desired coal fineness and optimize mill performanceKey words: Coal mill classifier, Cut size, Nonswirling inlet, Particle image velocimetry, Impeller rotational speed 摘要: The classification performance of model coal mill classifiers with different bottom incoming flow inlets was experimentally and numerically studiedThe flow field adjacent to two neighboring impeller blades was measured using the particle image velocimetry techniqueClassification performance of model coal mill classifiers with cipspindle coal pulverising mill’s performance to facilitate optimal plant performance The effect of low calorific value coal was observed on mill’s response to match the boiler energy requirements 731 Grinding table speed Performance optimisation of vertical spindle coal pulverisersPoor dynamic performance of coal mill will lead to decrease in the overall efficiency of the power plant, slow load take up rate and frequent shut down IRJET DESIGN, TESTING AND ANALYSIS OF SPHERICAL AND AERODYNAMIC HELMET IN OPEN CIRCUIT LOW SPEED WIND TUNNEL IRJET Journal(PDF) Modeling and Control of Coal Mill Academia
制粉-10.25公众号.jpg)
Modeling of Coal Mill System Used for Fault Simulation
2020年4月7日 MPS mediumspeed coal mill is a rolltype mediumspeed coal mill designed and manufactured by Ba bcock, Germany The mill is characterized by low power consumption, smooth2019年12月1日 The classification performance of model coal mill classifiers with different bottom incoming flow inlets was experimentally and numerically studiedClassification performance of model coal mill classifiers with Rotational speed: 150 rpm 735 rpm Output: 400 kg/h 250,000 kg/h Motor power: 22 kW 1,600 kW The main body of the rod mill is a lowspeed rotating cylinder horizontally mounted on two large bearings The rod mill is driven by the motor through the reducer and Lowspeed mill, Lowspeed chopper All industrial manufacturers2020年3月1日 The classification performance of the air classifier in a vertical coal mill determines the size of pulverized coal particles Thus, the classification performance will influence the ignition, burning, and burnout of the coal particle, and NO x formation in the furnace as well [[1], [2], [3], [4]]The first generation of the coal mill classifier used static guide vanes to Classification performance of model coal mill classifiers with
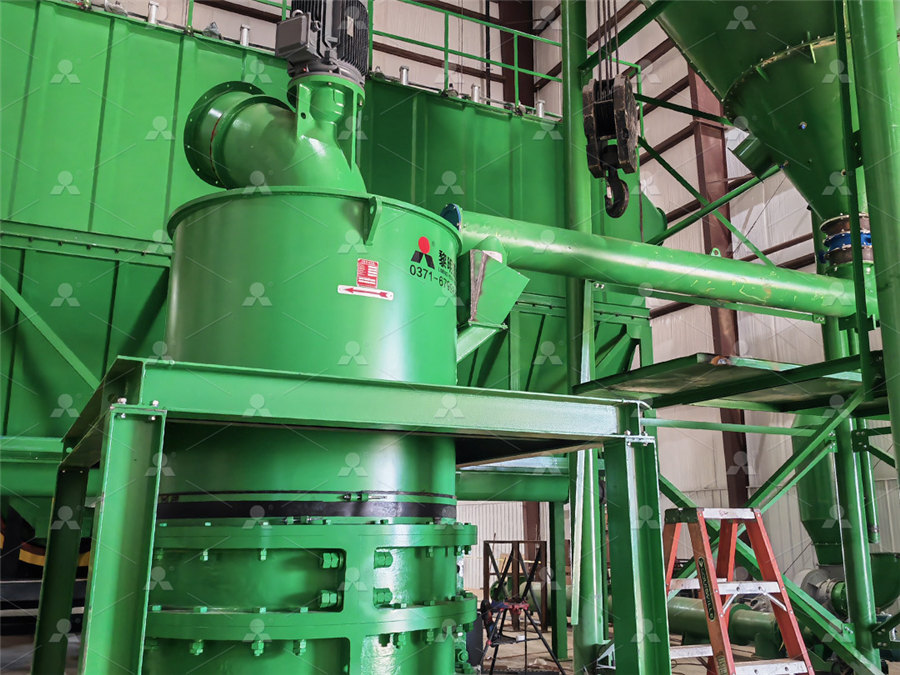
Coal Pulverizer Design Upgrades to Meet the Demands of Low
coal pulverizer systems supplied by RPI originally designed for low, medium and high speed pulverization have undergone design upgrades and improvements reviews the impact on Low NOX burner performance (emissions and UBC) Since the first application using an MPS mill to process pulverized coal in Germany in the mid 1960s,2021年8月1日 Yukio et al [7] proposed a model consisting of blending, grinding and classifying processes for pulverizer control Agarawal et al [8] differentiated coal powder into ten size groups, divided the bowl mill into four zones, and developed a unified model Palizban et al [9] derived nonlinear differential mass equations of raw coal, recirculation coal and suspension coal in Coal mill model considering heat transfer effect on mass 2016年9月1日 Furthermore, VRM separator speed (rpm) is one of the key operational parameters that determines product particle size Increasing the classi er rotor speed from 60 to 80 rpm decreases the particle Operational parameters affecting the vertical roller mill performance The lowspeed coal mill is particularly suitable for grinding hard anthracite According to the data, the most important performance of the liner and its materials used in thermal power plants is high hardness Only highhardness Promotion Coal Mill Liner EB Castworld
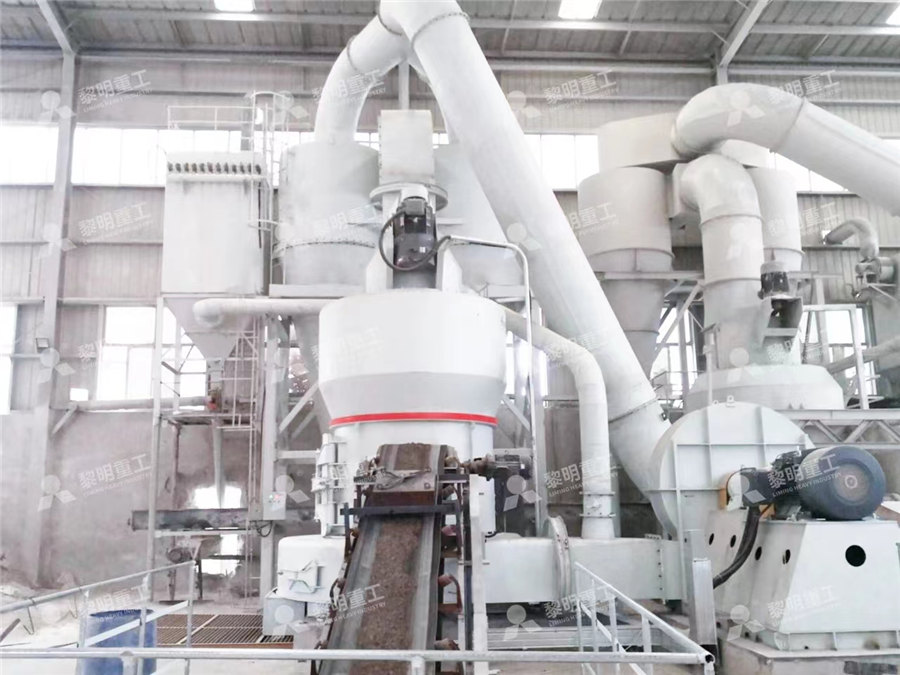
Operational parameters affecting the vertical roller mill performance
2017年4月1日 In addition to low energy consumption, an increased mineral liberation achieved by the in bed grinding principle compared to conventional tumbling mill grinding could be identified Positive effects on performance of downstream processes like flotation, leaching, etc could be provenet al 2017) In a coalfired power plant, one of the main equipment is the coal mill, whose effectiveness influences mainly the whole power plant performance (Shah, Vuthaluru, andAn investigation of performance characteristics and energetic Normally, Hardgrove Grindability Index (HGI) is used to predict mill performance The three types of coal pulveriser are generally identified by the speed of their rotation: Low speed mills are of the ball/tube design with a large steel cylinder and a charge of hardened ballsPF Power Plant Coal Tech2022年9月3日 spindle coal pulverising mill’s performance to facilitate optimal plant performance The effect of low calorific value coal was observed on mill’s response to match the boiler energy requirements 731 Grinding table speed Performance optimisation of vertical spindle coal pulverisers
.jpg)
Pulverizer Plant OM Aspects
Low Speed Medium Speed High Speed 17 to 20 Rev/min 30 to 100 Rev/min 500 to 1000 Rev/min Tube and ball mill Bowl Mill, Ball and Race mill Beater Mill, Impact Mill 13 BOWL MILL Factors affecting Mill performance Moisture in the coal• Minimal coal spillage • No rumbling • Recommended fineness •75% passing 200 mesh • Bright and attached burner flames • Low LOI (Direct impact of pulverizer performance) • Balanced airflow in fuel lines • Balanced fuel flow to burners Fuel Fineness testing is a measure of performancePerformance Driven Maintenance of Coal Pulverizers2015年5月7日 Gao et al [5] established a dynamic model for a medium speed coal mill based on mass and energy balance and predicted the dynamic performance of a coal mill Review of Control and Fault Diagnosis Methods Applied to Coal 2024年5月1日 The coal mill is a machine that breaks and grinds coal into pulverized coal It is the core equipment of pulverizing system Coal mills are categorized according to speed as low, medium and high speed mills The low and mediumspeed coal mills are the most popular due to their economy [25] The modeling object is ZGM type mediumspeed roller Dual fault warning method for coal mill based on ScienceDirect
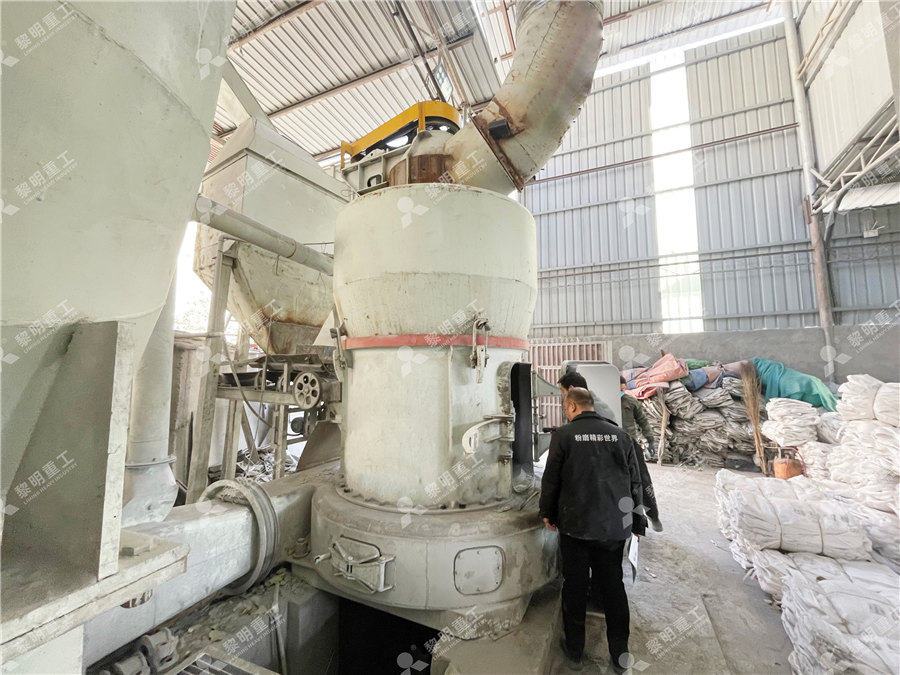
Combustion, Reliability, and Heat Rate Improvements through Mill
through Mill Performance and Applying the Essentials By: Oscie Brown, PE, SCANA (SCEG) Low NOx burners Wateree was designed with no significant margin in coal mill capacity, in addition, the original fuel specification was significantly higher in heating value (13,000 Btu 2017年10月26日 The following are factors that have been investigated and applied in conventional ball milling in order to maximize grinding efficiency: a) Mill Geometry and Speed – Bond (1954) observed grinding efficiency to be a Factors Affecting Ball Mill Grinding Efficiency2017年8月1日 The simulation results show that compared with single hidden layer, double hidden layers BP neural network can improve the performance of the network, so as to improve the prediction accuracy of the model and provide basis for the followup maintenance of coal mill, which has certain practical engineering significanceModeling of a medium speed coal mill Semantic Scholar2021年8月1日 310 The low lubricating oil pressur e of the coal mill caused the trip of the coal mill Cause analysis : ( 1 ) Insufficient output of oil pump ( 2 ) The filter screen is seriously Fault analysis and optimization technology of HP bowl type medium speed
.jpg)
Bowl Mill Coal Pulverizer COAL HANDLING PLANTS
Therefore the name “Bowl Mill” has been adopted to refer to this piece of equipment Components of Bowl Mill Coal Pulverizer Gearbox It is driven by an electric motor, is directly connected to the bowl hub A planetary gear arrangement provides the proper reduction between the motor and the bowl hub to obtain the desired bowl speedFigure 7) with sufficient coal/air mill exit temperature (14009, was expected to eliminate a number of past fuel system deficiencies such as: Low mill product fineness Little mill turndown capability Utilization of maximum available primary air at all mill loads (to avoid mill roller skidding) Abnormally high coal pipe (excessive coal pipe wearWorldProven Coal Pulverizer Technology Debuts in the US2021年11月4日 (BCURAroll) mill—high stress wear tester, the drysand rubber wheel low stress scratch ing abrasion tester, the Yancey, Geer and Pr ice (YGP) abrasion te ster, the hammer impact Figure 1Technique to Investigate Pulverizing and Abrasive Performance of Coals Air swept coal mill is low speed ball mill with rotation speed 1525rpm Structure Air swept ball mill mainly consists of feeding discharge system, hollow shaft, rotating cylinder filled with steel balls, gear ring, reliable performance, easy maintenance Wide adaptability for coal types, particularly suitable with hard anthraciteAir swept coal mill Geckointech
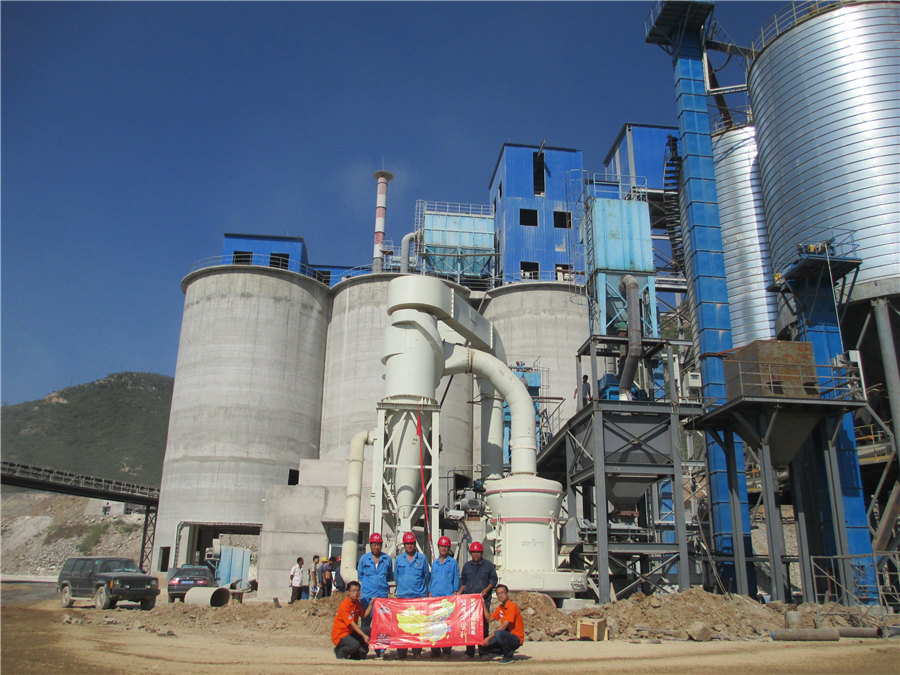
Vertical mill for coal pulverizing in power plant Geckointech
Vertical mill adopts low speed, big roller diameter, high loading force design It has the widest adaptability to coal types and variation in coal properties, big grinding surface ability, low rolling resistance, low energy consumption, stable output, etc