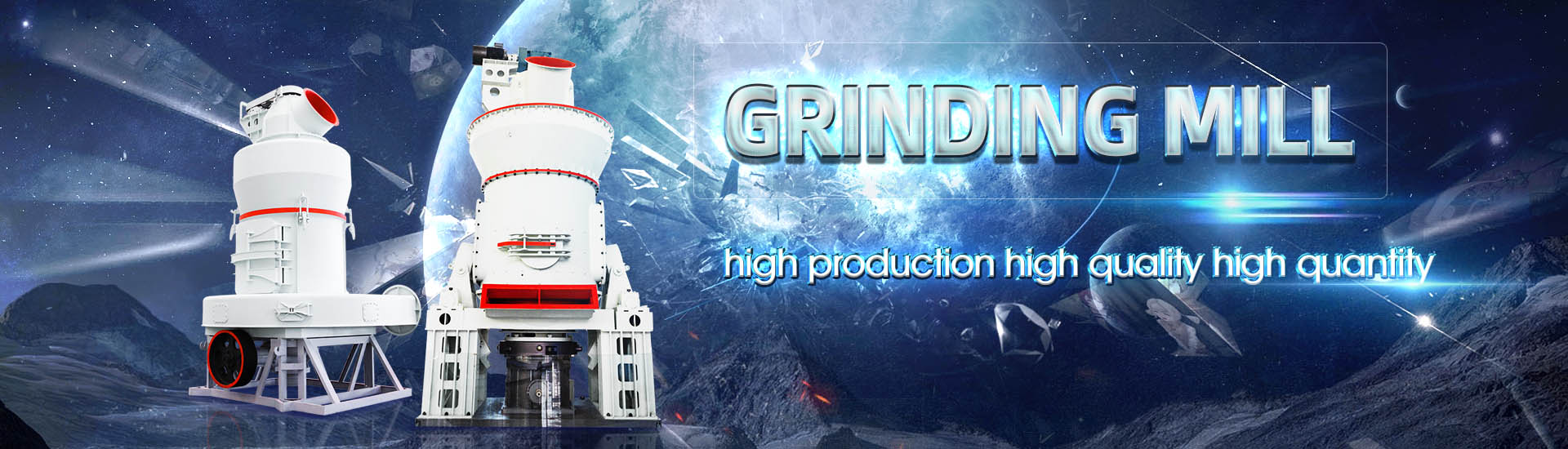
Rotary kiln black raw material
.jpg)
Rotary Kiln ONEJOON Kilns Furnaces
The rotary kiln made by ONEJOON is the optimal solution for processes and applications where high mass throughputs are to be homogeneously heattreated under high temperatures This industrial furnace is the tool of choice for the Rotary kilns are used to heat solids to the point where a chemical reaction or physical change takes place They work by holding the material to be processed at a speciied temperature for a The FEECO Rotary Kiln Handbook2023年2月25日 The transport of a load into a rotary kiln plays a decisive role in its transformation Loads may consist of raw materials (raw meal for the cement plant) and/or Rotary kiln process: An overview of physical mechanisms, models The rotary kiln is a slightly inclined steel cylinder that rests on supports (bearing rollers) with an interior lining; it is equipped with a rotating motor that induces a turning motionRotary kiln process: An overview of physical mechanisms, models
.jpg)
Mineral Raw Material for the Rotary Kiln, the Reactants and the
We showed that oil shale can replace up to 76 % of raw materials in clinker manufacturing, which is sufficient for calcination and final burning in a rotary kiln This means that oil shaleRotary Kilns—rotating industrial drying ovens—are used for a wide variety of applications including processing raw minerals and feedstocks as well as heattreating hazardous wastes Rotary Kilns ScienceDirect2017年8月1日 The rotary kiln is a pyroprocessing device used to raise the raw materials (biomass, or in this case, coconut shells) to a high temperature The kiln is a cylindrical vessel, Characterization of carbon materials and differences from The rotation of the kiln lifts the feed up the side of the kiln, and the energy required to maintain its centre of gravity above the lowest (6 o'clock) point is the main component (8090%) of the energy consumed In the case of kilns Cement Kilns: Design features of rotary kilns
.jpg)
Rotary Kiln SpringerLink
2022年11月16日 Rotary kiln is the thermal equipment for hightemperature heat treatment of solid raw materials in a rotary cylindrical kiln, also called rotary furnace, which is a continuous furnace The rotary kiln (see Fig 1 ) is mainly composed of kiln body, kiln lining, rolling ring, supporting device, transmission, discharge end hood, sealing device, dust collection chamber, Raw mineral material is preheated by high temperature exhaust gas from the kiln prior to calcining zone Hot material discharged from the calcinator is chilled through a vertical cooler X The rotary kiln calcinator is used for limestone, ROTARY KILN – 동원중공업(주)2017年11月29日 Development of refractory materials for the hightemperature zone of the rotary kilns used in the cement industry that is the secondlargest user of refractory materials is given in the article It is shown that the history of refractory materials used in this rotary kiln hightemperature zone commenced with aluminasilicate materials and ended with specially Evolution of Refractory Materials for Rotary Cement Kiln 2024年9月13日 It is expected that managing the rotary kiln’s calcine temperature according to the predictive model’s guidance values will allow for autonomous operation of the rotary kiln The heat produced by the burner through the combustion of coal injected with the raw material is used to generate Since SVM is a black box Operating Key Factor Analysis of a Rotary Kiln Using a MDPI
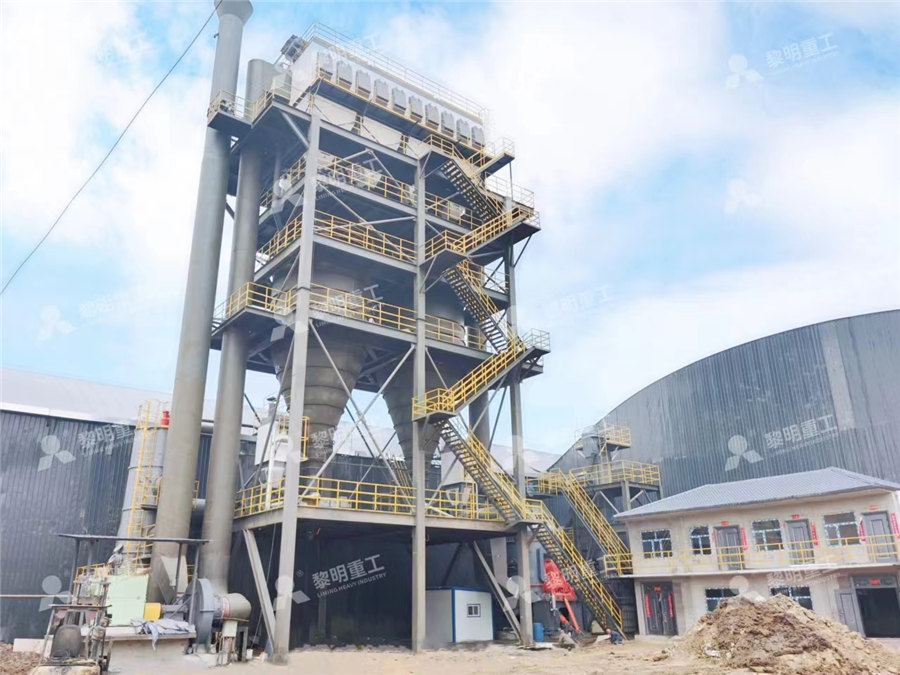
Quantitative Optimization of Cement Rotary Kiln for Heat
use rotary kilns for pyroprocessing to calcinate ores, calcinate limestone to lime for cement, and to common types of kiln; wet process kilns, long dry kiln, travelling grate preheater kiln (lepol), cyclone preheater kiln, cyclone preheater kilns with riser duct firing and, precalciner kilns Heat for Clinker ProductionThe material is heated via contact with the kiln shell FEATURES Size: Up to 15′ diameter x 75’+ heated length (up to 46m dia x 23m+ heated length) maximum capacity is dependent on process variables unique to each application; Rotary Kiln System Optimization, Rotary Kiln Rotary Kilns FEECO International Inc2017年2月14日 The rotary kiln is slightly inclined at an angle 25 degree and rotated by AC variable speed motor at a variable speed ranging from 02 rpm (revolutions per minute) to 10 rpm Due to inclination and rotary motion of the kiln, the material travels from feed end to the discharge end of the kiln in around 7 hours to 8 hoursCoal based Direct Reduction Rotary Kiln Process – IspatGuru2019年12月26日 The size of a rotary kiln is not only a function of capacity, but also of the amount of heat which can be generated inside the rotary kiln from the volatizing and/or combustion of the material The diameter and length of the rotary kiln are calculated based on the maximum feed rate, the required retention time, and what the bed profile (how full of material Rotary Kiln IspatGuru
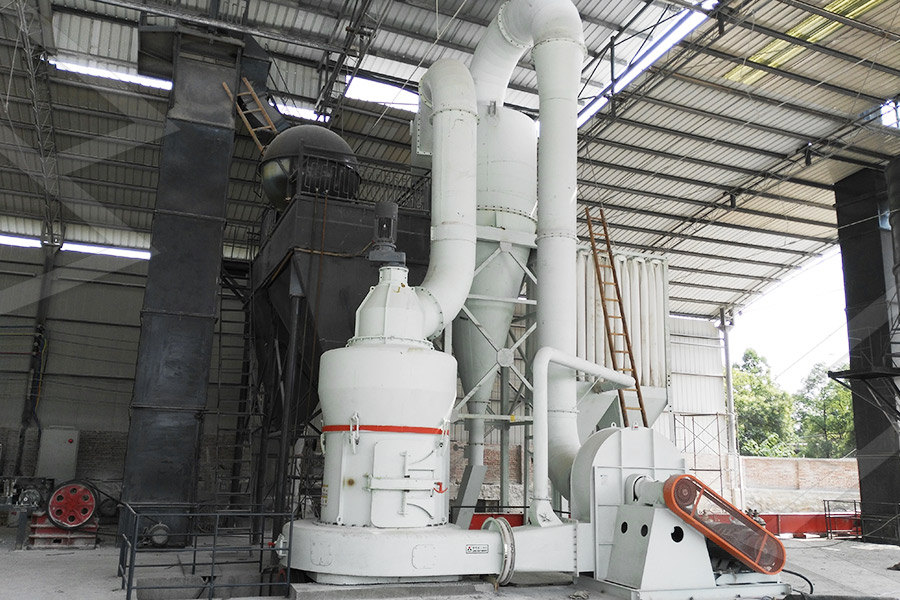
Using rotary kilns for hightemperature bulk solids processing
2022年4月19日 Determining whether a rotary kiln is a good fit Rotary kilns are not a good fit for all applications When processing some lowsolids materials, for example, an alternative technology may be more suitable Lowcapacity needs are also generally better met through alternative technologiesThe rotary kiln is used in many solid processes, including drying, incineration, heating, cooling, humidification, calcination and reduction This widespread application can be attributed to factors such as the ability to handle varied loads, with large variations in particle size [1]The rotary kiln is a slightly inclined steel cylinder that rests on supports (bearing rollers) with an Rotary Kiln an overview ScienceDirect Topics2024年5月30日 Unreasonable raw material plans cause agglomeration and blockages 3 Impacts of ring formation Material blockages necessitate machine shutdowns for maintenance, reducing production efficiency Abnormal agglomeration friction leads to kiln lining wear, shortening rotary kiln lifespan Agglomerates falling into the cooler damage key components 4Facing Rotary Kiln Challenges? 4 Solutions to Help You!The kilns at Shoreham were typical of the "first generation" of successful kilns They were supplied as a fullyequipped package by F L Smidth (FLS), loosely based on a design by Lathbury Spackman They were numbers 3 and 4 in the FLS rotary kiln order book, the first two, of almost identical design, having been installed at Aalborg, Denmark, in 1899Cement Kilns: Early rotary kilns
.jpg)
Rotary Kiln – Shalimar Engineering
The rotary kiln is a critical component of any cement plant or lime calcination plant The raw material to be processed enters at one end of the kiln and the processed material exits at the other end Shalimar Engineering has been in the business of manufacturing rotary kilns for The main function of the rotary kiln in the minerals and materials industry is to convert raw materials (ore) into useful product materials Most or all of the kiln processes involve some chemical or physical reactions that will occur at economically Rotary Kilns ScienceDirectWith the arrival of rotary kilns in Britain in 1900, cement manufacturing processes became sharply defined according to the form in which the raw materials are fed to the kiln Raw materials were either ground with addition of water, to form a slurry containing typically 3045% water, or they were ground dry, to form a powder or "raw meal"Cement Kilns: Rotary kilnsDownload Table Mineral Raw Material for the Rotary Kiln, the Reactants and the Final Clinker Minerals from publication: Combined utilization of oil shale energy and oil shale minerals within Mineral Raw Material for the Rotary Kiln, the Reactants and the
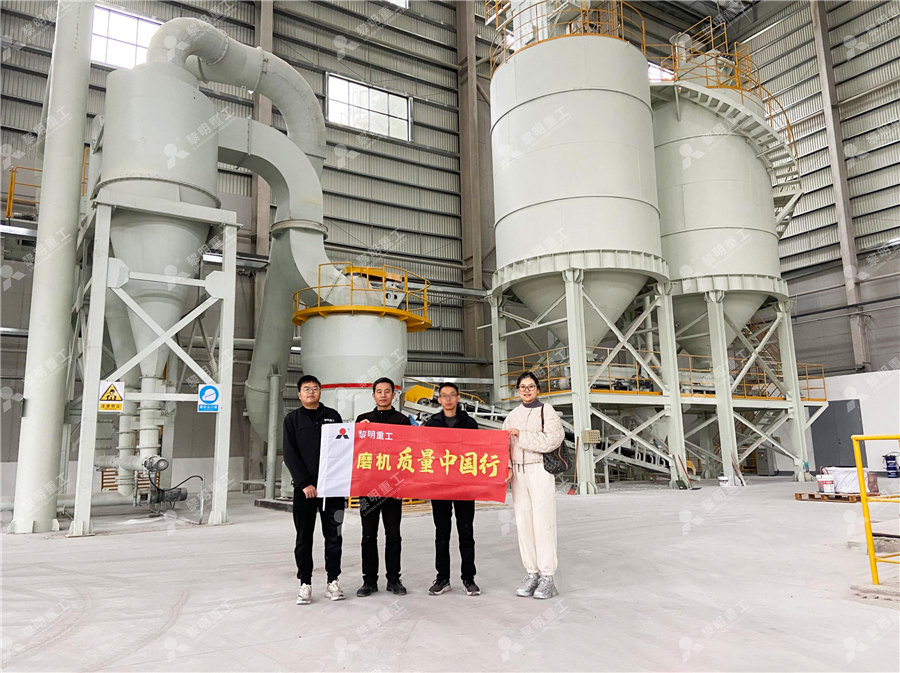
Rotary kilns – Knowledge and References – Taylor Francis
The raw material is fed into the top of the kiln and moves down the tube counter current to the flow of gases and toward the flameend of the rotary kiln, where it is dried, calcined, and enters into the sintering zone The process typically begins with a 2022年10月26日 A rotary kiln is a unique facility with widespread applications not only in the process industry, such as buildingmaterial production, but also in the energy sector There is a lack of a more comprehensive review of this facility and its perspectives in the literature This paper gives a semisystematic review of current research Main trends and solutions close to Rotary Kiln, a Unit on the Border of the Process and EnergyRotary kilns (sometimes called calciners or rotary furnaces) are used for thermal treatment processes such as calcination, sintering, pyrolysis and firing, as well as for oxidation and reductionThese treatments can be applied to powders, granulates, suspensions and green bodiesA rotary kiln consists of a cylindrical, rotating body mounted between stationary The Rotary Kiln Experts for Trials and Production IBUtec2015年11月29日 Feed material atau material umpannya berupa limbah debu pabrik baja (EAF dust) yang mengandung seng oksida dan kemudian dicampur dengan karbon dan fluks untuk selanjutnya dibakar didalam rotary kilnWAELZ ROTARY KILN: Teknologi, Proses dan
.jpg)
116 Portland Cement Manufacturing US Environmental
4 Reaction, of the oxides in the burning zone of the rotary kiln, to form cement clinker at temperatures of approximately 1510°C (2750°F) Rotary kilns are long, cylindrical, slightly inclined furnaces that are lined with refractory to protect the steel shell and retain heat within the kiln The raw material mix enters the kiln at the elevatedThe mass flow speed of the material along a rotary kiln is not constant However, in an approximate way, the time of permanence of the material within the kiln can be obtained by the following Model of Mass and Energy Transfer in a Clinker Rotary Kiln2016年10月25日 Request PDF Material and energy flows in rotary kilnelectric furnace smelting of ferronickel alloy with energy saving An energy saving strategy with two energy saving measures has been Material and energy flows in rotary kilnelectric furnace smelting Rotary kiln bauxite is the key raw material of the monolithic refractory products Due to the competitive price and stable quality, DEC has been regularly supplying rotary kiln bauxite to many reputed European refractory manufacturers for years DEC has various grades, such as DRKB85, DRKB86, Rotary Kiln Bauxite DEC Material

PERHITUNGAN NERACA MASSA, NERACA PANAS DAN EFISIENSI PADA ROTARY KILN
2023年5月19日 PERHITUNGAN NERACA MASSA, NERACA PANAS DAN EFISIENSI PADA ROTARY KILN UNIT KERJA RKC 3 PT SEMEN INDONESIA (PERSERO) is one of the factories that produce cem ent as raw material for construction conversion taking place in rotary kilns and provides a broader examination of kiln applications 2 Solid load transport à The transport of a load into a rotary kiln plays a decisive role in its transformation Loads may consist of raw materials (raw meal for the cement plant) and/or waste (alternative fuels) In general, the load is introducedRotary kiln process: An overview of physical mechanisms, models Roller Hearth Kiln Specification Fuel: electricity, natural gas Heating element: upper and lower silicon carbon rods Transmission mode: helical gear segmented frequency conversion speed regulation Application: lithium battery cathode and anode materials, rare earth, building ceramics, magnetic material raw materials, etcRoller Hearth Kiln for Lithium Battery Materials SinteringFunctionality of Rotary Kilns Rotary kilns serve a significant role in processing raw materials into final products Here's how they function: Rotation: The shell’s rotation enables the material to tumble and mix, promoting even heating Temperature Control: Temperatures in the rotary kiln can reach extraordinarily high levels, necessary for initiating chemical reactions or phase Rotary Kilns: Working Principles History StudySmarter
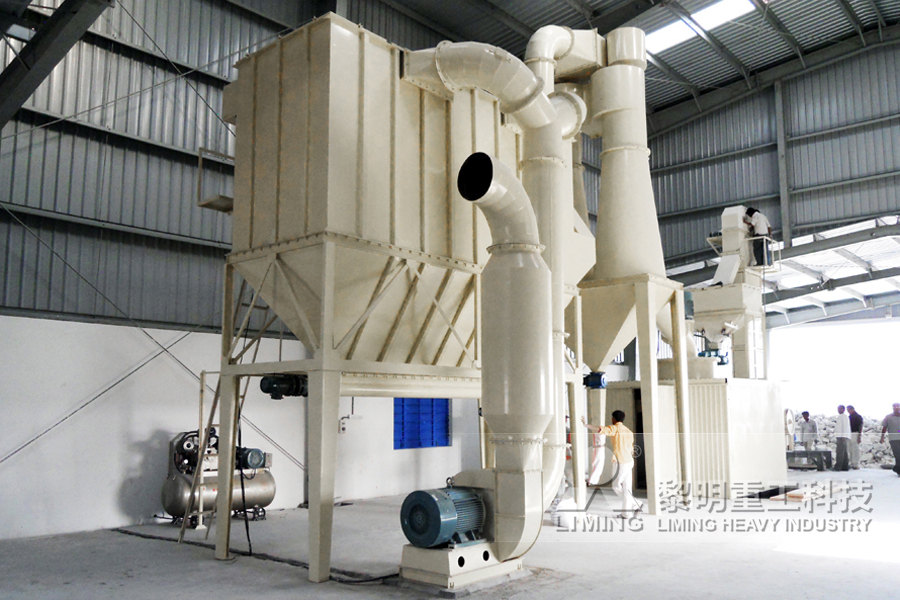
Cement Rotary Kiln CIC HMC
Cement Rotary Kiln 1 Application and Operating Principle The rotary kiln is the central equipment for cement clinkering system in the new large dry processing cement production, which can be used with unistream or twinstream preheater, calcining combustor 90%~ 95% of the raw material which has been precalcined has been fed into the slow rotating and inclining 2021年10月10日 The quarry is the primary source of raw material for the rotary kiln in cement production The consistency of material feed chemistry, in which the quarry plays a key role, is crucial for (PDF) Improving Kiln Feed Chemistry and Overburden Wasting The invention relates to a technique method for producing lithium iron phosphate material in a vacuum rotary kiln The invention relates to the industrial manufacturing of lithium ion battery cathode material, which is characterized in that: a continuous vacuum rotary kiln is adopted to sinter and produce lithium iron phosphate material, which realizes dynamic A Method for producing lithium iron phosphate material 2023年2月25日 The angle of repose is an intrinsic characteristic of a given material; it depends principally on: particle size, rotational speed of the kiln (Fig 2), and surface condition of the kiln wallMore specifically, this angle characterizes the flow properties of “solid particles” in the kiln; it is often assumed to be constant but may vary along the length of the kiln, in correlation with Rotary kiln process: An overview of physical mechanisms, models
.jpg)
Furnaces and process equipment for Cathode Active Material ONEJOON
Roller Hearth Kiln for Cathode Active Material (CAM) A key product is the electrical heated gastight Roller Hearth Kiln with pneumatic airlock systems and an indirect cooling zone to be able to run under oxygen atmosphere for production of Cathode Active Material (CAM) with higher Nickel content like NCM622, NCM811 and NCA which will be used in EV LithiumIon BatteriesIn a modern works, the blended raw material enters the kiln via the preheater tower Here, hot gases from the kiln, and probably the cooled clinker at the far end of the kiln, are used to heat the raw meal As a result, the raw meal is already hot before it enters the kiln The dry process is much more thermally efficient than the wet processManufacturing the cement kiln Understanding Cementbatch intermittent rotary kiln with continuous carbonization–steam activation process conducted at 500 °C to 700 °C was studied The activated carbon products were characterized by FTIR, SEM–activation process in a batch intermittent rotary kiln NatureSome possible ways to recover the heat losses are introduced and discussed and they are Electricity generation, Heat recovery from kiln surface and Preheating raw material before the clinkering process Keywords: Rotary Kiln, Design Parameters, Exhaust Gas, Radiation 1Heat Balance Analysis in Cement Rotary Kiln Academia
.jpg)
Reinforcement LearningBased Supervisory Control Strategy for a Rotary
Raw material flow controller Kiln rotary motor speed controller Coal feeder Induced draft fan Air blower Feed pump Kiln electromotor Rotary Kiln , HI LO T TB Z SP BZ SP Primary air flow Setpoint of controller air press Setpoint of n Human intervention uM u1 u u3 Rotary kiln processthe raw material by up to 90% before enters the rotary kiln, where sintering during the melting phases of the kiln feed and formation of the clinker minerals takeNew Generation of Refractories for Rotary Cement Kiln2019年8月1日 The UARR has a rotating cylindrical cavity or crucible of highdensity alumina with a longitudinal length (L) of 76 mm and 31 mm in inner radius (R)To reduce reflection losses, the kiln presents a smaller aperture with a radius (R ap) of 20 mm, open to the ambient and a conical frustum with a diameter of 32 mmThe cavity is insulated with lowdensity alumina and it is A labscale rotary kiln for thermal treatment of particulate