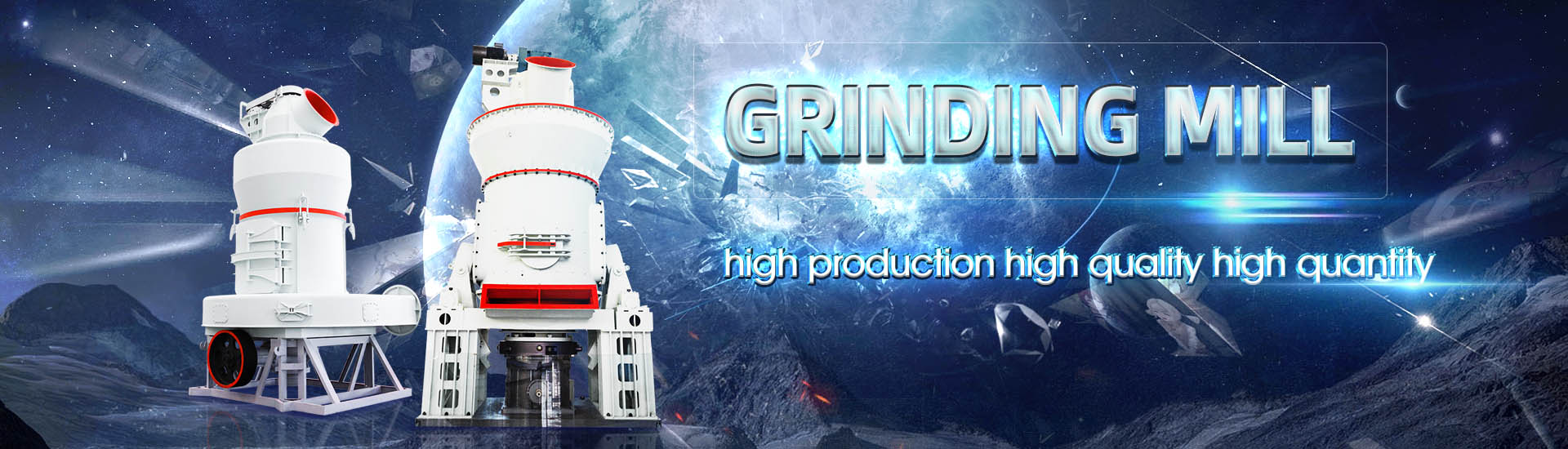
Cement burning process diagram
.jpg)
Manufacture of Cement Materials and Manufacturing
The burning process is carried out in the rotary kiln while the raw materials are rotated at 12rpm at its longitudinal axis The rotary kiln is made up of steel Five different processes are used in the portland cement industry to accomplish the pyroprocessing step: the wet process, the dry process (long dry process), the semidry 116 Portland Cement Manufacturing US Environmental Process flow diagram for the cement manufacturing process, showing electricity and heat consumption or inputs [39] The paper presented herein investigates the effects of using supplementaryProcess flow diagram for the cement manufacturing 1971年8月17日 A diagram of the process, which encompasses production of both portland and masonry cement, is shown in Figure 1161 As shown in the figure, the process can be 116 Portland Cement Manufacturing US EPA
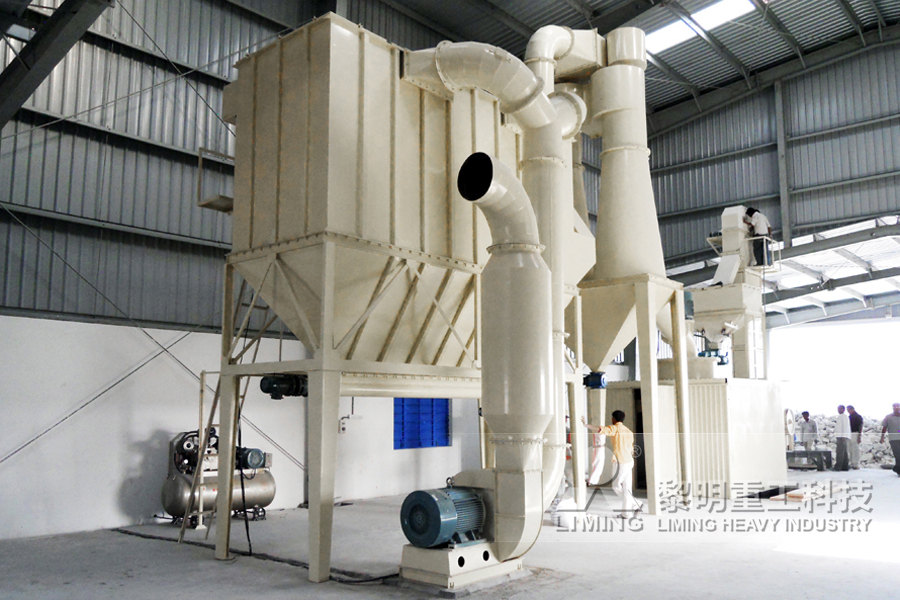
The Cement Plant Operations Handbook International Cement
The Cement Plant Operations Handbook is a concise, practical guide to cement manufacturing and is the standard reference used by plant operations personnel worldwide Providing a The clinker, base component of the Portland cement, is obtained from the grinding, homogenization and subsequent burn in high temperatures (1450ºC) inside a rotary cement Stages of the Portland cement process productionThis abstract provides a concise overview of the cement manufacturing process and its environmental implications The cement manufacturing process involves the extraction and processing of raw materials, such as limestone, clay, and (PDF) THE CEMENT MANUFACTURING PROCESSBurning: In this operation, the slurry is directly fed into a long inclined steel cylinder called a Rotary kiln In this kiln there are 3 different zones shown in fig below Cement Manufacturing Process Flow Chart (i) Drying Zones: In the wet Manufacturing of Cement By Dry and Wet Process
.jpg)
Cement Manufacturing Process INFINITY FOR
Cement Manufacturing Process by TIZITA MOGES , The first part in the diagram (Fig above) represents efficient reduction of such shorttime fluctuations Longterm fluctuations with periodical times exceeding 5hr are not reduced A schematic diagram on different stages of cement manufacturing is shown in Figure 311 The pyroprocessing stage is generally regarded as the heart of the cementmaking process Melting Points and Relative Volatilities of Everything you need to know about Kiln Burning In Fig 1, a schematic of the cement burning process is shown together with its cyclone preheater; including some important operational variables 9781424447077/09/$2500 ©2009 IEEEThese Rotary Cement kiln Process Download Scientific DiagramDownload scientific diagram Flow chart of cement clinker burning system from publication: Technical Route to Achieve UltraLow Emission of Nitrogen Oxides with Predictive Model of Nitrogen Flow chart of cement clinker burning system ResearchGate
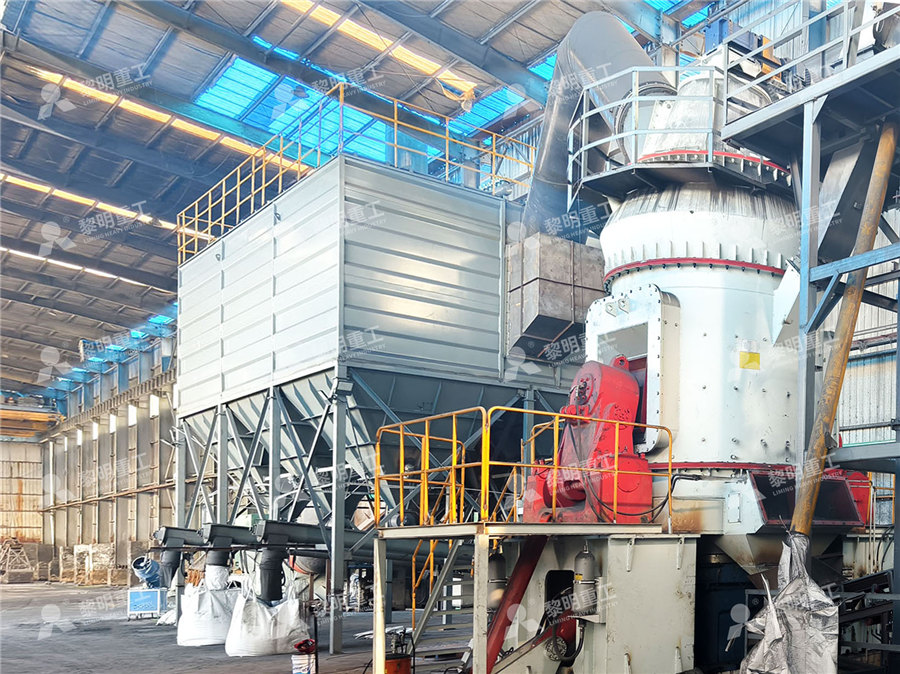
Cement manufacturing process PPT Free Download SlideShare
2014年6月10日 Evolution of the cement Process • Wet process easiest to control chemistry better for moist raw materials • Wet process high fuel requirements fuel needed to evaporate 30+% slurry water • Dry process kilns less fuel requirements • Preheater/Precalciner further enhance fuel efficiency allow for high production ratesDownload scientific diagram Process flow diagram for the cement manufacturing process, showing electricity and heat consumption or inputs [39] from publication: Energy Savings Associated with Process flow diagram for the cement manufacturing process, The production process of cement is not very complex but has many steps to be able to go from raw limestock rocks to a quality cement The steps are the following Figure 1 : Cement production process block diagram 2 Cement production step by Cement Production Demystified: StepbyStep Process and 2012年8月30日 Cement Manufacturing Process Phase IV: Kiln Phase Kiln is a huge rotating furnace also called as the heart of cement making process Here, raw material is heated up to 1450 ⁰C This temperature begins a chemical reaction so called decarbonation In this reaction material (like limestone) releases the carbon dioxideCement Manufacturing Process Engineering Intro
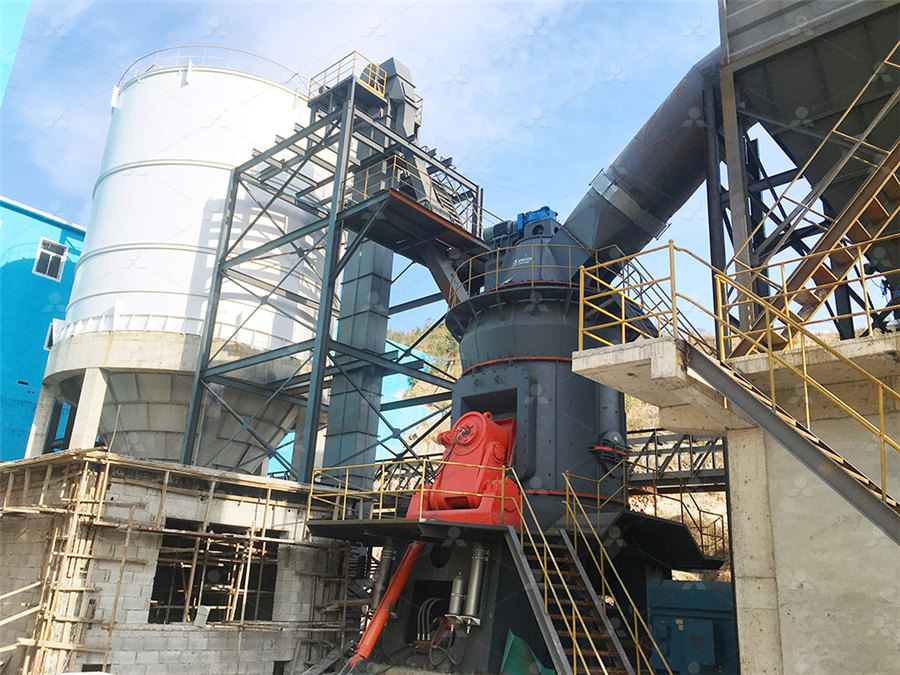
Cement Manufacturing Process: Know Extraction, Processing
2024年9月10日 Learn about the Cement Manufacturing Process including dry and wet processes and know the major differences between them, advantages, It then enters the precalciner, where a partial calcination process takes place Burning and Clinkerization: The preheated and precalcined slurry is introduced into a rotary kiln, As the perflow diagram of the wet process of cement manufacturing, the rotary kiln is an essential and important component of a cement manufacturing factory 6 It is made of a thick steel cylinder of diameter anything from 3 meters to 8 meters, lined with refractory materials, mounted on roller bearings, and capable of rotating about its axis at a specified speedWet Process Of Cement Manufacturing With Flow ChartDownload scientific diagram Stages of the Portland cement process production from publication: Alternative Fuels Mixture in Cement Industry Kilns Employing Particle Swarm Optimization Algorithm Stages of the Portland cement process productionProcess diagram for cement production 2014 emission numbers taken from US GHGRP for Holcim Inc Genevieve Plant in Bloomsdale, MO The vast majority of US cement plants, During this process, 30–40% is derived from burning Cement Production an overview ScienceDirect Topics
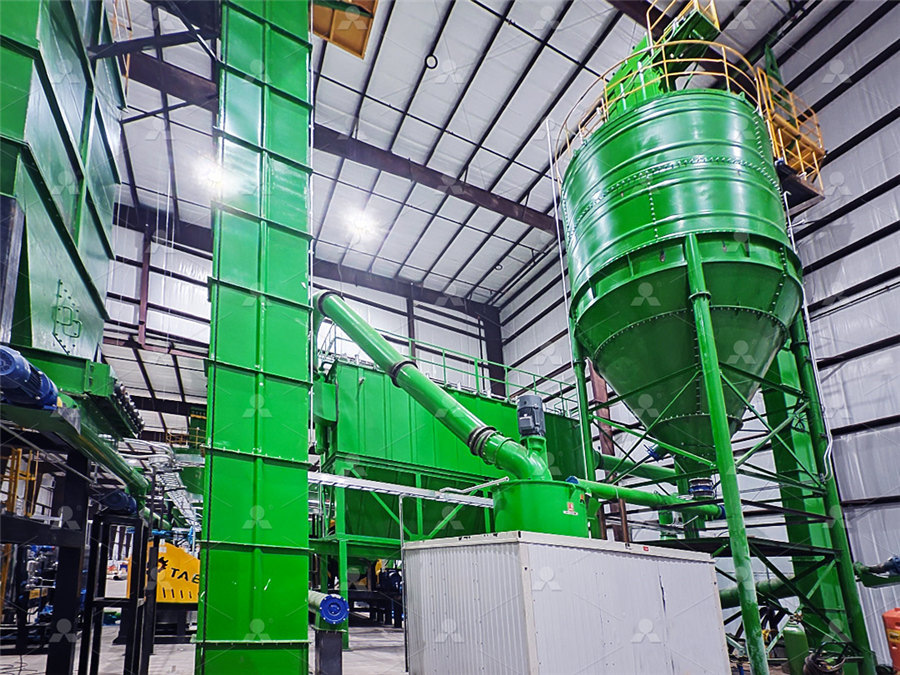
Manufacturing process Lafarge
The cement manufacturing process starts from the mining of raw materials that are used in cement manufacturing, mainly limestone and clays A limestone quarry is inside the plant area and a clays quarry is as far from the plant area Alite formation and other reactions at 1300 C1450 °C in the burning zone Cooling of the clinker Decomposition of raw materials reactions at temperatures up to about 1300 °C However, reading an article or two is perhaps not the best way to get a clear picture of a complex process like cement productionReactions in the cement kiln clinkering Understanding CementAll the cement plants set up after 1980 use the dry process for the manufacture of cement In this process, the calcareous materials such as limestone are crushed and stored in silos or storage tanks The argillaceous material such as clay is thoroughly mixed with water in a container known as the wash mill This washed clay is stored in basinsCement Manufacturing Process: How the Cement is Made?Download scientific diagram Typical cement manufacturing process flow diagram [4] from publication: Model Development for CO2 Capture in the Cement Industry Climate change has become a Typical cement manufacturing process flow diagram [4]
.jpg)
(PDF) THE CEMENT MANUFACTURING PROCESS Academia
Clinker is ground with gypsum (36%) to adjust setting time Packing marketting Wet process Dry process Dry process with preheating tower THE CEMENT MANUFACTURING PROCESS • • • • • • • Quarry Grinding Burning Grinding, Storage, Packing, Dispatch THE CEMENT MANUFACTURING PROCESS quarry dumper loader Quarry face 12019年11月30日 The process of burning is explained below (manufacture of portland cement): The raw mix or collected slurry is injected into the kiln from its upper end Burning fuel like powdered coal or oil or hot gases is forced through the lower end of the kiln so long hot flame is Manufacture Of Portland Cement Process civil learners2014年1月1日 This chapter is composed of five sections: 21 Portland cement clinker burning, 22 The phase systems important for cement chemistry, 23 The clinkering process in industrial mixes, 24 Thermochemistry of clinkering process, 25 Phase composition of PortlandPortland Cement Clinker SpringerLinkBurning: In this operation, the slurry is directly fed into a long inclined steel cylinder called a Rotary kilnIn this kiln there are 3 different zones shown in fig below Cement Manufacturing Process Flow Chart (i) Drying Zones: In the wet process, the drying zone is comparatively larger than the dry process It is because the raw material in slurry form is directly fed into the kiln Manufacturing of Cement By Dry and Wet Process Expert Civil
.jpg)
Burning process of synthesized clinkers Download
Download scientific diagram Burning process of synthesized clinkers from publication: Synthesis and Characterization of Belite Cement with High Hydraulic Reactivity and Low Environmental Impact 2024年5月14日 Cement manufacturing process is a reliable bonding material It is obtained by burning calcareous material (lime) and argillaceous material (clay) and then grinding, types of cement The cement manufacturing process was first produced by Joseph Aspidin, a mason from England As its color resembled a variety of sandstone found in Portland, he named it Portland CEMENT MANUFACTURING PROCESS ! TYPES OF CEMENT, 2020年2月15日 Most important technologies for clinker (cement) production in regard to RKS configuration, temperature ranges, and functional zones [9, 10] ∗ Escape of liquid and adsorbed water ∗∗ Dehydration of clay minerals and activation of oxides by decomposition of clay minerals ∗∗∗ The length of this zone and the cooling rate depend on the primary burner position and the Parametric Studies of Cement Production Processes John 2020 2013年1月1日 In this study the process flow diagram for the cement production was simulated using Aspen HYSYS 88 software to achieve high clinker burning, and cement grinding are the three major processes Modelling the cement process and cement clinker quality
.jpg)
Stages in cement production flow chart [43] ResearchGate
Download scientific diagram Stages in cement production flow chart [43] from publication: A review on kiln system modeling The purpose of this study is to evaluate performance cement of 2021年3月3日 Cement is produced by a hightemperature (about 1500 °C) reaction in a rotary kiln of carefully proportioned and blended ratios of lime (CaO), silica (SiO 2), alumina (Al 2 O 3), and iron oxide (Fe 2 O 3)The production of cement is a chemical process requiring an accurate blend of the previously cited four key organic oxides and the limitation of several undesirable Cement SpringerLink2017年12月5日 Methods of Manufacturing Process of Cement At present Portland Cement is manufactured by two processes, Dry Process, and Wet Process The main difference between these two methods of manufacturing of cement is that in the dry process, calcareous and argillaceous raw materials are fed into the burning kilns in a perfectly dry stateCement Manufacturing Process: What is Cement made of2013年8月30日 After 1982 all the cement manufacturing plants in India are equipped with the technologies of Dry process, since this is more energy efficient and environment friendly method of cement manufacturing In this post I am sharing with you the flow diagram of the wet process of the mixing because it is in the syllabus of the many Diploma coursesWet process Cement manufacturing Flow Diagram
.jpg)
Explain manufacturing of Portland cement with labeled diagram
The burning process is carried out in the rotary kiln while the raw materials are rotated at 12rpm at its longitudinal axis The rotary kiln is made up of steel tubes having the diameter of 2530 meter and the length differs from 90120meter2024年9月1日 Flow diagram of the cement clinker burning process (1) A dynamic modeling method for rotary kilns that combines combustion, chemical reactions, and heat transfer mechanisms is developed to estimate the rotary kiln’s dynamic calcinating statesSAMSIFF: Soft sensing the cement fCaO content with a self 2020年8月25日 A full cement production process includes the cement crushing process, raw mill process, clinker process, and cement grinding process, cement packing process, and related this process is generally known as wet Cement Production Process Cement Manufacturing An English bricklayer made the first portland cement early in the 19th century by burning powdered limestone and clay on his kitchen stove While each cement plant may differ in layout, equipment, and appearance, the general process of How Cement is Made Portland Cement Association
.jpg)
Cement Manufacturing and Process Control SpringerLink
2019年8月27日 The major raw materials used as a source of CaO for cement manufacturing are limestone, chalk, marl, etc These raw materials by virtue of their natural occurrence contains other mineral impurities eg, MgO, SiO 2, Al 2 O 3, Fe 2 O 3, alkali compounds, and sulfidesThese impurities play an important role to influence the cement manufacturing 5 CEMENT –HISTORY In India, Portland cement was first manufactured in 1904 near Madras, by the South India Industrial LtdBut this venture failed Between 1912 and 1913, the Indian Cement Co Ltd, was established at Porbander (Gujarat) and by 1914 this Company was able to deliver about1000 tons of Portland cement By 1918 three factories were established1 Manufacturing Process of Cement Indus UniversityDownload scientific diagram Rotary klin used in burning process of cement manufacturing Portland Cement, Civil and Paper ResearchGate, the professional network for scientistsRotary klin used in burning process of cement manufacturing Download scientific diagram Cement manufacturing process flow diagram from publication: A healthbased life cycle impact assessment (LCIA) for cement manufacturing: a comparative study of China Cement manufacturing process flow diagram ResearchGate
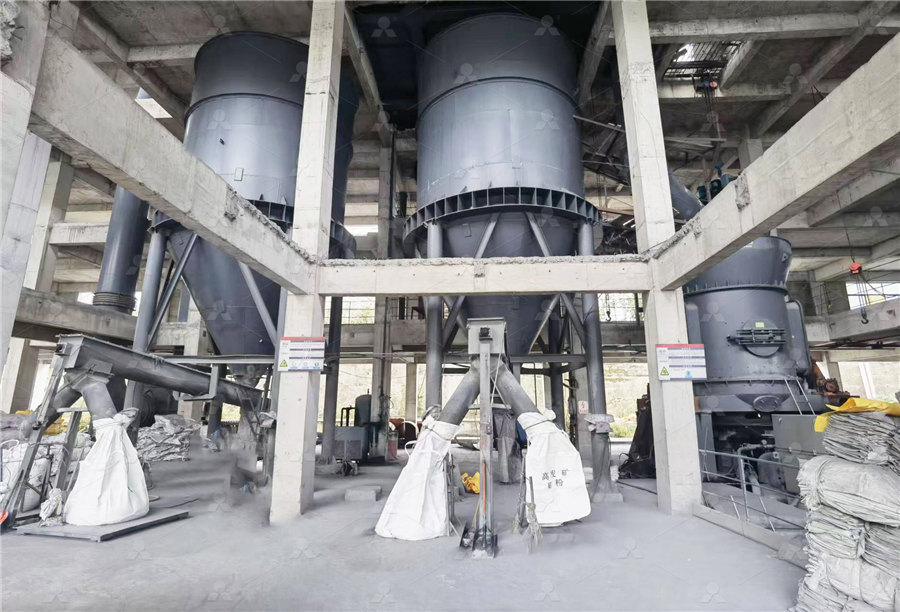
CEMENT PRODUCTION AND QUALITY CONTROL A Cement manufacturing Process
The whole process of cement manufacturing in Messebo Cement plant which consists of two separate Cement Production lines can be summarized into the following processes ;as can be seen in the process and Quality flow diagram below; 1 Quarrying and Crushing 2 Raw material the raw meal which is ready for burning process is stored and 2023年1月1日 The heating process in the cement kiln requires intense energy to heat the clinker and compensate for the heating loss Studies illustrate a significant loss of energy (> 50 %) in cement kilns, as shown in Fig 2 [4]Thus, there is a need for optimal design and efficient operation of the cement kiln to minimise this energy lossA comprehensive review on Advanced Process Control of cement Continuous high temperature process in the cement industry: Calcination and cement clinker burning Calcination of raw material CaCO 3 => CaO + CO 2 Process emissions of raw material: = 054 t CO 2 /t clinker Endotherm reaction at 950 °C ca 1700 MJ/t clinker ≈ 50% of energy Cement clinker burning at 1450 °C formation of hydraulicProcess characteristics of clinker and cement production SINTEF2018年8月28日 Cement Manufacturing Process Cement is the basic ingredient of construction and the most widely used construction material It is a very critical ingredient, because only cement has the ability of enhancing viscosity of concrete which in returns provides the better locking of sand and gravels together in a concrete mixCement Manufacturing Process The Engineering Community